In the bustling world of manufacturing, high-speed injection molding technology is creating a buzz, transforming how we produce goods.
High-speed injection molding technology significantly boosts production efficiency and product quality by reducing molding cycles and enhancing automation. However, it presents challenges such as high equipment costs and technical skill requirements, demanding careful management and strategic planning.
But don’t just take my word for it! Let’s dive deeper into how this technology reshapes manufacturing, revealing insights that can give you a competitive edge.
High-speed injection molding shortens molding cycles by 40%.True
Traditional cycles are 10 seconds, reduced to 6 seconds, a 40% decrease.
- 1. How Does High-Speed Injection Molding Improve Production Efficiency?
- 2. What Impact Does High-Speed Injection Molding Have on Product Quality?
- 3. Why Is Mold Design Critical in High-Speed Injection Molding?
- 4. What Are the Financial and Talent Challenges in Adopting High-Speed Injection Molding?
- 5. Conclusion
How Does High-Speed Injection Molding Improve Production Efficiency?
In the competitive manufacturing landscape, high-speed injection molding is a game-changer, enhancing production efficiency like never before.
High-speed injection molding improves production efficiency through shorter molding cycles and enhanced automation, resulting in increased output and reduced errors.
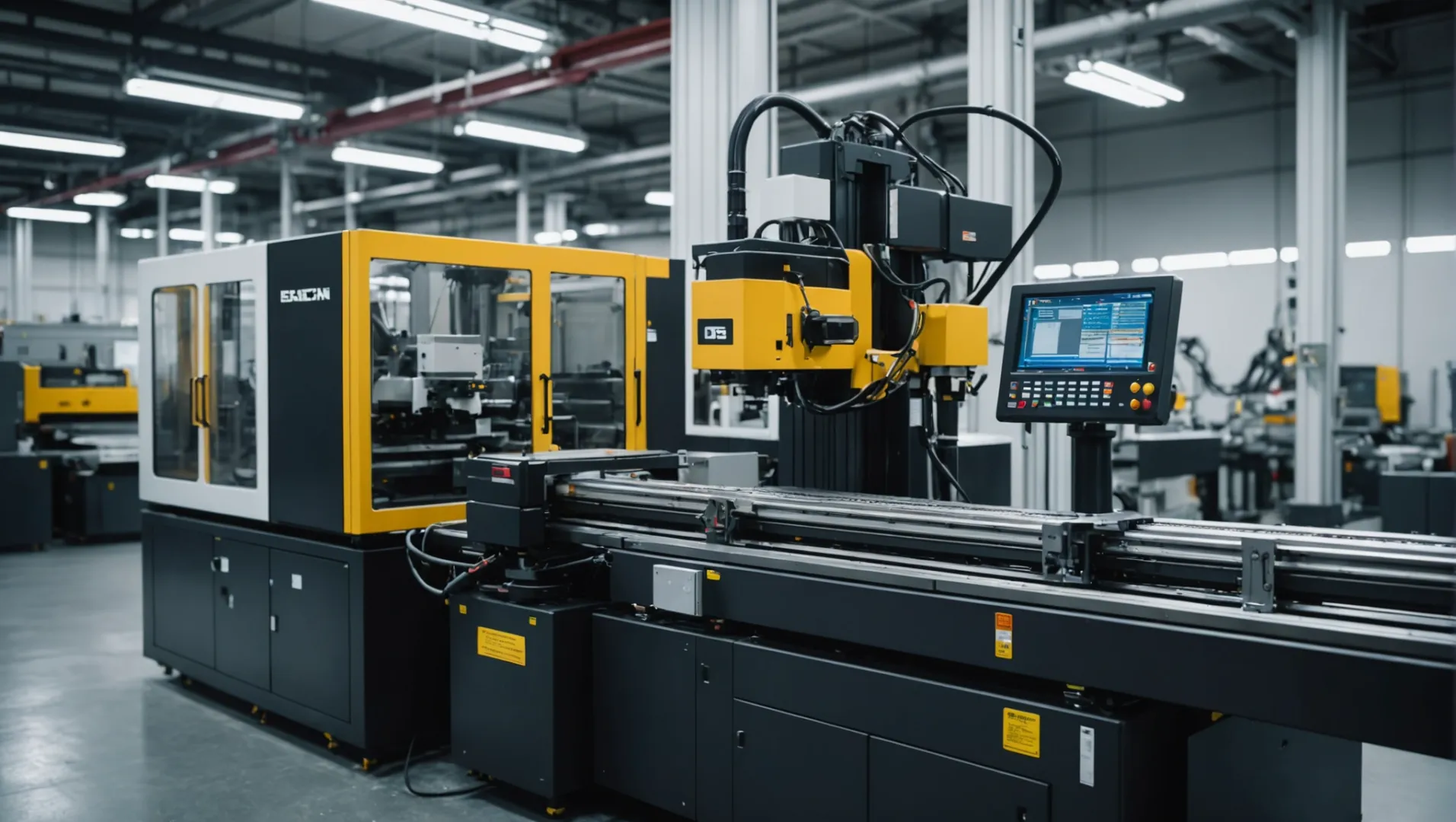
Shortened Molding Cycles
One of the most significant benefits of high-speed injection molding is the drastic reduction in molding cycles. Traditional injection molding machines may require around 10 seconds to complete a cycle. In contrast, high-speed machines achieve this in approximately 6 seconds due to technologies such as three-axis linkage. This decrease in time significantly boosts production rates, enabling companies to meet high market demands efficiently. For large-scale manufacturers, this means producing more units within the same timeframe, directly impacting both productivity and profitability.
Enhanced Automation and Reduced Errors
High-speed injection molding systems often incorporate advanced automation, which reduces the need for manual intervention. This results in a lower man-machine ratio and decreased labor intensity. Automated processes replace manual tasks such as product handling and removal, leading to consistent production quality and a reduced rate of errors caused by human factors. The result is a more stable and reliable production process.
Case Studies: Efficiency Gains in Action
Consider a company utilizing high-speed injection molding for manufacturing electronic components. By reducing the cycle time from 10 seconds to 6 seconds and automating various stages of production, they increased their output by over 30%. This not only improved their market competitiveness but also enhanced their economic performance.
Aspect | Traditional Molding | High-Speed Molding |
---|---|---|
Cycle Time | 10 seconds | 6 seconds |
Output Increase | – | 30% |
Error Rate | Higher | Lower |
Energy Efficiency Improvements
The integration of energy-efficient systems in high-speed injection molding also contributes to improved production efficiency. These machines often employ hybrid or fully electric drive systems with servo motors, significantly reducing energy consumption compared to traditional hydraulic systems. Such improvements not only decrease operational costs but also align with sustainable manufacturing practices.
To explore more on how energy efficiency is achieved, check out these energy-saving technologies in molding1.
By understanding the intricacies of high-speed injection molding2, manufacturers can optimize their operations and maintain a competitive edge in the industry.
High-speed molding reduces cycle time by 4 seconds.True
High-speed injection molding cuts cycle times from 10 to 6 seconds.
Automation in high-speed molding increases error rates.False
Automation reduces errors by minimizing human intervention in processes.
What Impact Does High-Speed Injection Molding Have on Product Quality?
High-speed injection molding is revolutionizing product quality with its precise control over production parameters and enhanced automation.
High-speed injection molding enhances product quality by improving dimensional accuracy and reducing defects such as bubbles and weld marks. It ensures consistent quality through advanced control systems, making it ideal for industries with stringent standards like electronics and medical devices.
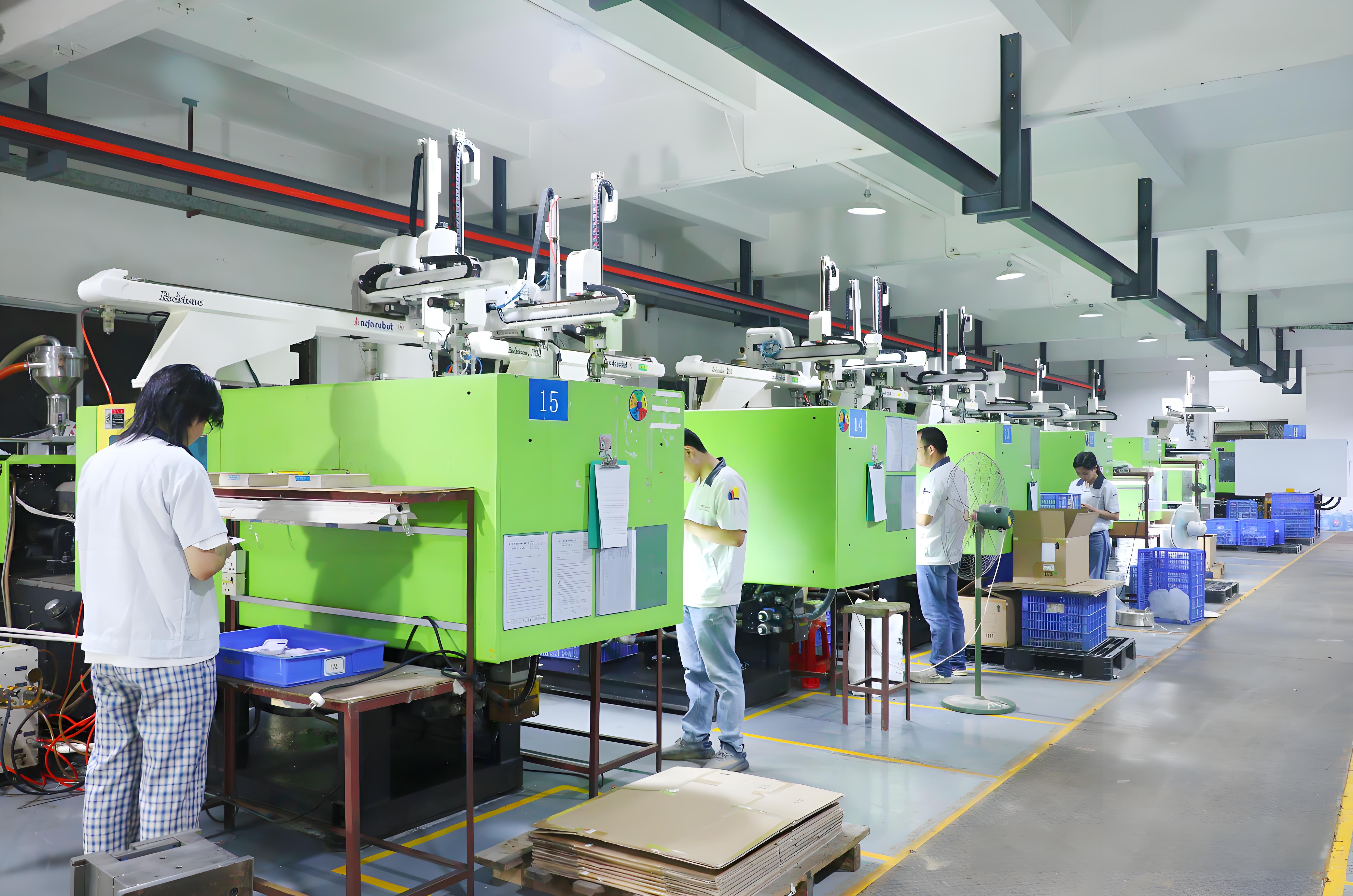
High-Speed Injection Molding
Enhanced Dimensional Accuracy
One of the most significant impacts of high-speed injection molding on product quality is its ability to achieve high dimensional accuracy. Advanced control systems in these machines meticulously regulate parameters such as temperature, pressure, and flow rate. This precision reduces variability in the molding process, resulting in products with tighter tolerances. For industries such as electronics manufacturing3 or medical device production, where precision is paramount, this technology ensures adherence to strict quality standards.
Reduction in Defects
The high-speed nature of this molding process allows the melt to fill the cavity quickly and evenly, minimizing internal stresses that can lead to defects like bubbles or weld lines. The swift filling reduces the likelihood of temperature gradients within the mold, which often cause these imperfections. Consequently, products exhibit enhanced structural integrity and aesthetic appeal, critical for consumer electronics and automotive parts.
Consistency and Stability
High-speed injection molding also provides consistency and stability in production. The ability of these machines to respond swiftly to changes in the molding process—thanks to their high-speed acceleration capabilities—ensures uniform product quality. This aspect is especially vital for complex-shaped products where maintaining consistency across batches is challenging.
Case Study: Application in the Medical Sector
Consider a scenario in the medical industry, where components like syringes or surgical instruments require not only high precision but also consistency across millions of units. High-speed injection molding is leveraged here to maintain exacting standards, significantly reducing the risk of defective products reaching end-users.
Feature | Benefit |
---|---|
Dimensional Accuracy | Tighter tolerances, better fit |
Defect Reduction | Fewer bubbles, weld marks |
Consistent Quality | Uniformity across batches |
Challenges in Material Selection
While the benefits are clear, challenges such as selecting appropriate materials can arise. The rapid filling speeds demand materials with excellent fluidity and thermal stability, often necessitating special high-performance plastics. This requirement can increase material costs but is crucial for maintaining product quality standards during high-speed processes.
Explore more about material compatibility4 in high-speed injection molding to understand how different materials can affect product outcomes and what solutions exist to mitigate these issues.
High-speed injection molding reduces product defects.True
It minimizes defects like bubbles and weld marks by quick cavity filling.
Material costs are lower in high-speed injection molding.False
Rapid filling speeds require costly high-performance plastics for quality.
Why Is Mold Design Critical in High-Speed Injection Molding?
Mold design plays a pivotal role in the success of high-speed injection molding, influencing efficiency, product quality, and cost-effectiveness.
Mold design in high-speed injection molding is crucial due to its impact on production efficiency, product quality, and operational costs. Optimized mold structures ensure rapid and even melt distribution and cooling, while material selection enhances durability under high pressures.
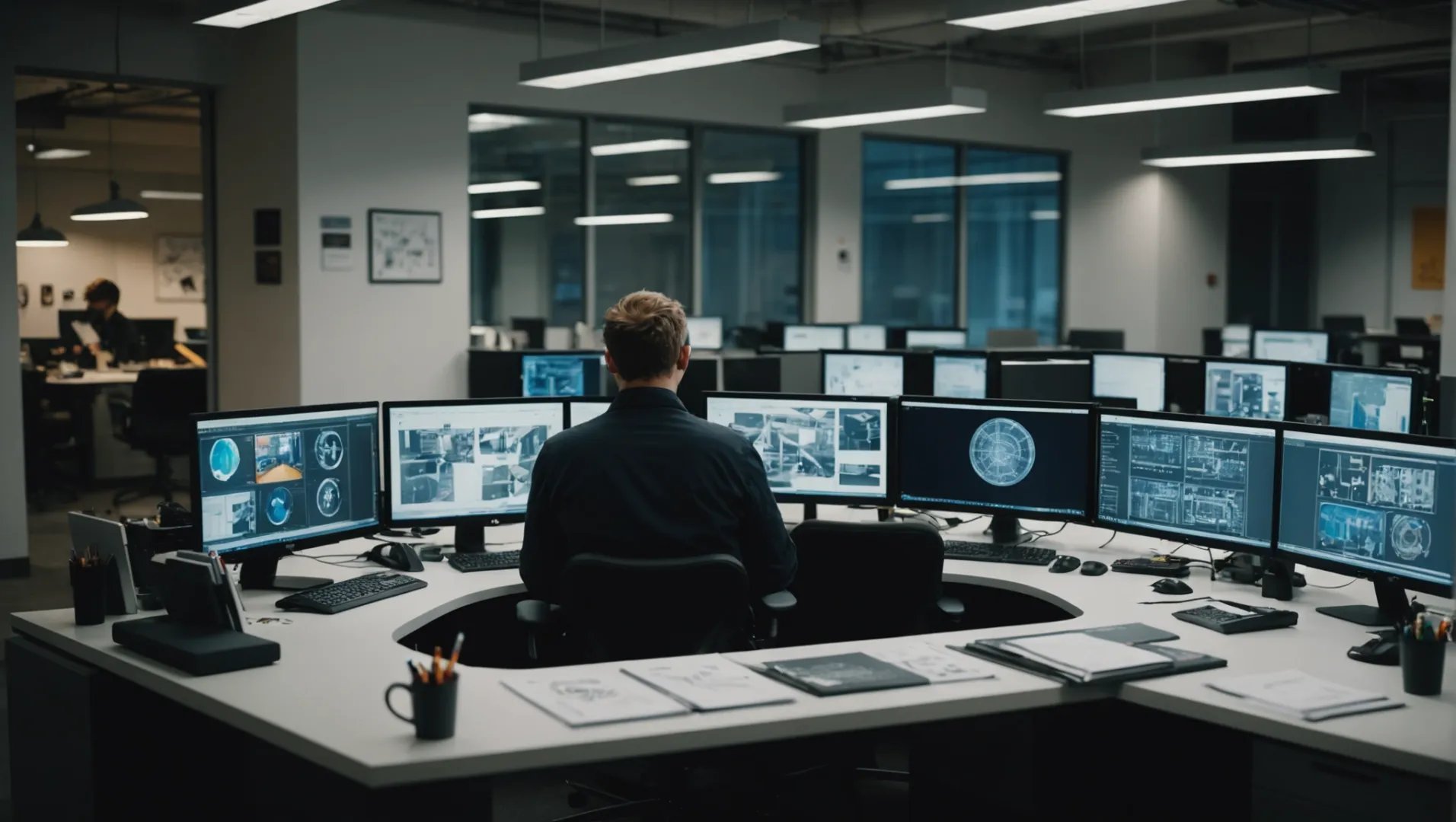
High-Speed Injection Molding Mold Design
The Role of Mold Structure Optimization
In high-speed injection molding, optimizing the mold structure is not just beneficial but essential. The layout of the mold cavity, the design of the gates, and the cooling system must all work harmoniously to facilitate quick and uniform melt filling. This process minimizes potential defects such as air bubbles and weld marks. For instance, a well-designed gate system reduces shear stress during injection, which is critical for maintaining the integrity of delicate components like electronic parts.
-
Mold Cavity Layout: A strategic cavity layout can drastically reduce cycle times. By designing cavities that allow for simultaneous filling, manufacturers can achieve higher efficiency. This is particularly advantageous in industries requiring mass production, such as consumer electronics.
-
Advanced Cooling Systems: Efficient cooling systems are integral to reducing cycle times. They ensure that products solidify quickly and uniformly, which is crucial for maintaining dimensional accuracy and reducing warpage.
Importance of Mold Material Selection
High-speed injection molding imposes significant demands on the mold materials. The selected materials must endure elevated pressures and temperatures while maintaining their structural integrity over numerous cycles.
-
Durability and Wear Resistance: Molds made from high-strength steel or those treated with surface coatings are preferred for their ability to withstand repetitive use without degradation. This is essential to ensure consistent quality over time.
-
Thermal Conductivity: Materials with good thermal conductivity help in dissipating heat quickly, which is vital for maintaining a rapid production cycle. This reduces cooling time and contributes to overall energy efficiency.
Challenges in Mold Design for High-Speed Injection Molding
Despite the advantages, mold design in high-speed injection molding presents several challenges that require strategic solutions.
-
Complexity and Cost: The initial design and manufacturing of molds can be expensive. Companies must balance the upfront investment with potential long-term savings in production costs.
-
Precision Engineering: High-speed processes demand precise engineering to avoid issues such as flashing or short shots. This requires advanced CAD/CAM systems and skilled engineers who can translate complex designs into functional molds.
Moreover, companies often need to conduct trials5 to ensure that chosen materials and designs meet production requirements efficiently. Exploring new materials6 that offer better performance at lower costs remains an ongoing pursuit in the industry.
Optimized mold design reduces cycle times significantly.True
Strategic cavity layouts and cooling systems enhance production speed.
Material selection has no impact on mold durability.False
High-strength materials ensure molds withstand high pressures and temperatures.
What Are the Financial and Talent Challenges in Adopting High-Speed Injection Molding?
High-speed injection molding offers transformative benefits, yet financial burdens and talent shortages pose significant adoption hurdles.
Adopting high-speed injection molding involves high upfront costs and maintenance expenses, alongside a scarcity of skilled technicians. These challenges necessitate strategic investments and comprehensive training programs to ensure successful implementation and operational efficiency.
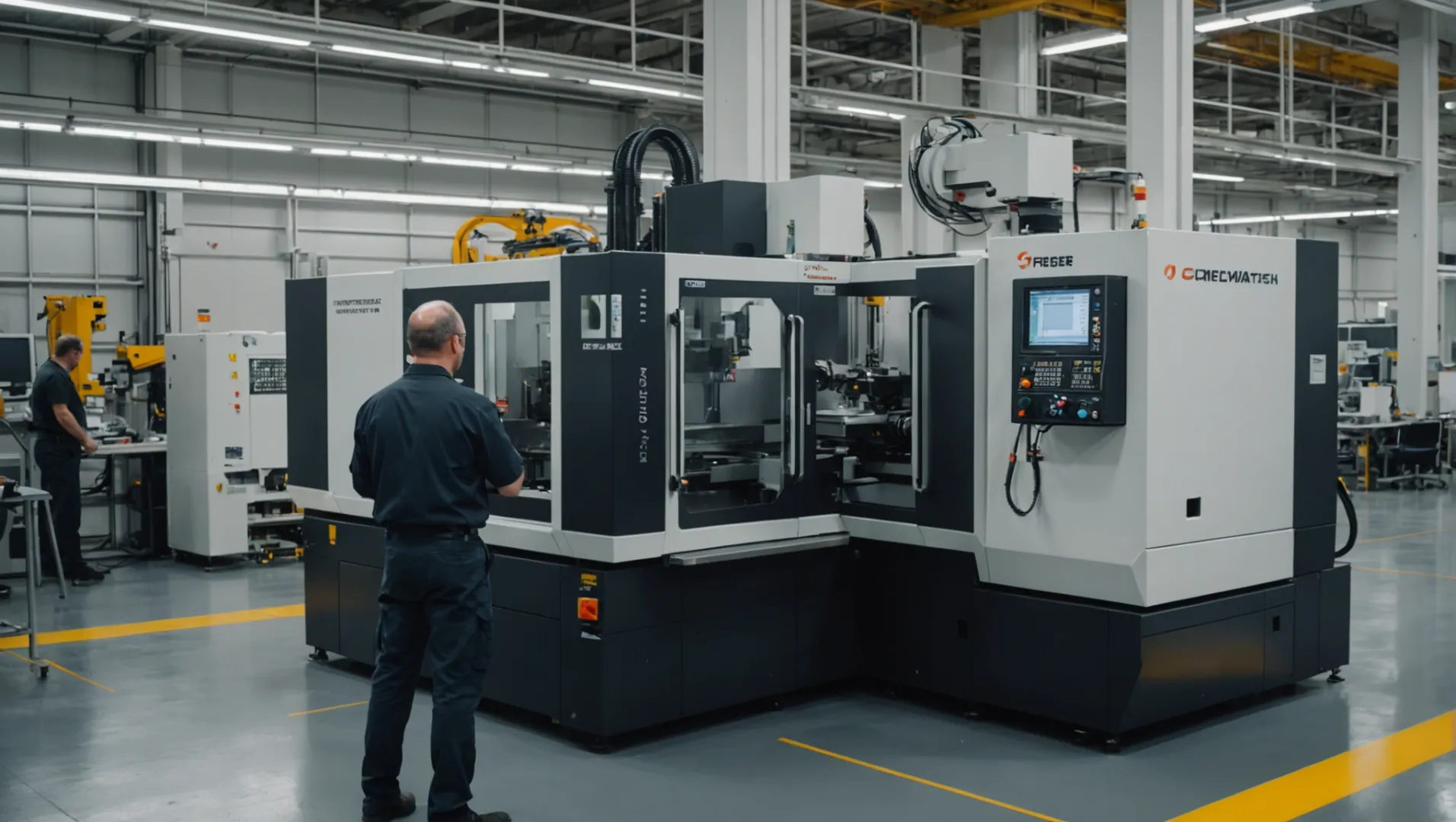
High Initial Investment
One of the foremost challenges faced by companies considering high-speed injection molding technology is the substantial initial investment required. The cost of acquiring high-speed injection machines, alongside the necessary automation equipment and molds, can be prohibitive. For small to medium-sized enterprises, this financial burden can limit their ability to adopt this advanced technology.
Additionally, upgrading existing equipment to accommodate high-speed processes demands further capital outlay, potentially affecting a company’s cash flow. The decision to invest in such technology must weigh the long-term benefits against these immediate financial constraints.
Increased Maintenance Costs
The complexity of high-speed injection molding machinery means that maintenance costs are inevitably higher compared to traditional methods. These machines have intricate designs and incorporate advanced technologies that require specialized attention. Enterprises need to factor in not just the cost of regular upkeep but also the availability of professional technicians7 who are capable of performing these tasks effectively.
Without proper maintenance, companies risk operational downtimes, which can further increase costs and impact production schedules.
Shortage of Skilled Technical Talents
Another significant challenge is the shortage of skilled professionals well-versed in high-speed injection molding operations. These processes demand a comprehensive understanding of injection molding techniques, mechanical principles, and automated control systems. Currently, there is a considerable gap between the demand for such expertise and the availability of qualified individuals in the job market.
Difficulty in Training Programs
Training existing employees to handle the complexities of high-speed injection molding is no small feat. Companies must develop detailed training programs that cover equipment operation, parameter settings, and troubleshooting skills. This is crucial to prevent production inefficiencies and ensure that operations run smoothly.
Investing in continuous learning and development programs becomes essential for companies aiming to maintain a competitive edge. A structured training plan not only improves employee competency but also enhances overall organizational productivity.
Conclusion: Balancing Investment and Capability
While the financial and talent-related challenges associated with adopting high-speed injection molding technology are significant, they are not insurmountable. Companies that strategize effectively—by allocating resources wisely and investing in talent development—stand to gain substantial advantages from the enhanced production efficiency and product quality offered by this cutting-edge technology.
High-speed injection molding requires high initial investment.True
The technology involves costly machines and automation equipment.
Skilled technicians are readily available for high-speed injection molding.False
There is a significant shortage of skilled professionals in this field.
Conclusion
High-speed injection molding offers remarkable benefits but requires careful planning and skilled personnel. Companies that navigate these challenges effectively will thrive in a competitive landscape.
-
Discover cutting-edge energy-saving methods for efficient production.: Insulating the Barrel · 100% Electric Machines · Use a Variable Speed Drive · Calculating Life Cycle Costs · Use the Correct Machine for the Product. ↩
-
Explore the comprehensive benefits of adopting high-speed injection molding.: Benefits Of Injection molding · High efficiency and quick output. · Labor costs are low · Design versatility · Production with a high output. ↩
-
Precision is crucial for electronics manufacturing quality control.: With precision manufacturing, companies are able to create consistent quality, which helps them avoid the risks of throwing away incorrectly designed parts, … ↩
-
Material compatibility impacts product quality in high-speed molding.: If two materials come in contact with one another and cause a chemical reaction, they’re incompatible and cannot be used together in multi- … ↩
-
Trials help verify mold designs before full-scale production, ensuring quality and efficiency.: Therefore, before modifying the mold, a mold trial and evaluation are usually performed to optimize the mold design and process parameters. ↩
-
Discover innovative materials that enhance mold durability and performance.: Manufacturers recently began using plant-based materials in their injection molding to create plastics that are less harmful to the environment. ↩
-
Find expert-led training programs for technicians to ensure operational efficiency.: The American Injection Molding (AIM) Institute is a world leader in education and training for the plastic injection molding industry. ↩