Have you ever thought about how the complex layout of channels in a mold affects how long it lasts?
The design of main and branch channels influences how long a mold lasts. These channels affect wear, thermal fatigue and stress concentration. Proper channel size, good surface smoothness and correct alignment with cooling systems are very important. These factors probably reduce wear. They really help a mold last longer.
Thinking back to my early days in mold design, I recall the first time I saw how small changes in tiny channels could change a mold’s strength. It was like a light turning on in my mind when I understood that even small things like the taper angle or how smooth a channel’s surface is could greatly affect wear. I saw molds break down because of small details like these, leading to expensive stoppages and repairs.
Through trying different methods and learning from mistakes, I discovered that aligning channels with cooling systems was very important. It was shocking to see how wisely placing channels could stop heat problems, avoiding those annoying little cracks that could harm the mold. This journey taught me how important stress distribution is in keeping a mold working longer. This understanding is now natural in my design process.
Focusing on these details, I’ve noticed that the mold not only lasts longer, but it also works better, giving the same product quality every time. It’s a small amount of time spent in design that really pays off a lot over time.
Main channel design affects mold wear and tear.True
Proper main channel design reduces wear by minimizing stress points.
Surface roughness of channels has no impact on mold life.False
Smooth surfaces reduce friction, thus extending mold service life.
How Does Channel Wear Influence Mold Longevity?
Have you ever thought about how channel wear, even though it seems minor, significantly affects the lifespan of a mold?
Channel wear greatly shortens mold life. Friction and heat rise. Mold changes shape and breaks. Optimized channel design keeps molds strong. Proper care helps molds last much longer.
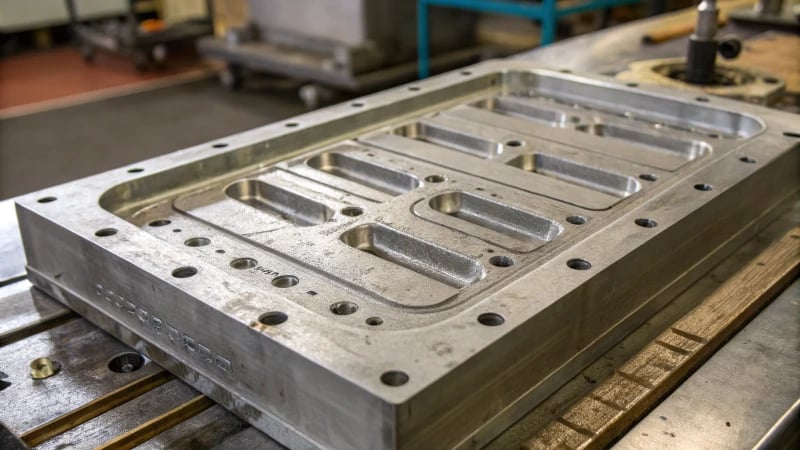
Understanding the Impact of Channel Design on Wear
The design of the main channel is crucial for reducing wear and extending mold life. An improperly designed taper angle or rough surface of the main channel can increase friction, leading to faster wear. For instance, a small taper angle in high-speed injection molding can cause excessive friction on the inner wall.
Design Aspect | Impact on Wear |
---|---|
Taper Angle | Affects friction and wear rate |
Surface Roughness | Influences particle abrasion |
The Role of Runner Design in Mold Longevity
Runner design goes beyond just connecting points; it resembles planning a rollercoaster for liquid plastic. Strange shapes or small runners create shear forces like sandpaper rubbing against the mold. I once worked on a design where unbalanced runner sizes led to more wear in certain spots. Ignoring such details often creates bigger problems.
Find out more about runner designs1 by exploring this topic.
Effects of Thermal Fatigue on Mold Life
Thermal fatigue acts like a hidden enemy to mold life. It enters through temperature changes in the channel and cavity. Long channels may not seem bad but cause heat loss, leading to thermal stress that forms tiny cracks. Think about mismatched cooling systems – too hot or too cold can harm, similar to leaving an ice cube under the hot sun.
A detailed guide on thermal management in molds2 can provide further insights.
Stress Concentration and Its Consequences
Proper alignment between the main channel and injection machine nozzle is vital. I have seen how poor alignment causes stress concentration, leading to cracks that grow with each use. It’s like bending a paperclip repeatedly – it eventually breaks.
An informative article on stress management in mold design3 could be beneficial to explore.
Tips for Mitigating Wear and Extending Mold Life
- Regular Maintenance: Frequent checks and cleaning reduce wear.
- Optimized Design: Designed channels and runners balance flow and lessen friction.
- Material Selection: Durable materials resist wear in high-stress areas.
Understanding these details helps professionals like me design molds that last longer and perform very well in plastic injection molding environments4.
Small taper angle increases friction in mold channels.True
A small taper angle causes excessive friction, accelerating wear.
Irregular runner shapes decrease mold longevity.True
Irregular runners increase shear forces, leading to faster wear.
How Does Thermal Fatigue Influence Mold Durability?
Do your molds seem older than they should? Thermal fatigue could be the reason. This issue quietly reduces their strength over time.
Thermal fatigue reduces how long molds last. Repeated heating and cooling create small cracks and bend the molds. Changing channel designs helps. Using the right materials helps too. These changes reduce damage. Molds last longer.
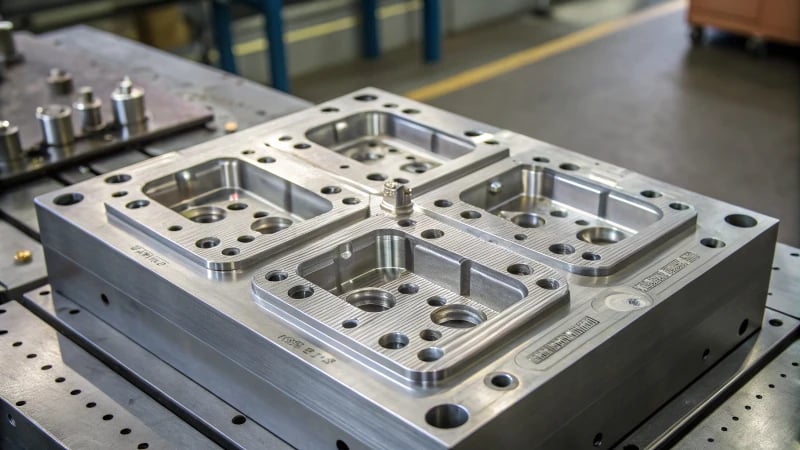
Understanding Thermal Fatigue in Molds
Thermal fatigue manifests when molds undergo continuous heating and cooling cycles5, common in processes like injection molding. This cyclical temperature change induces thermal stresses, causing microcracks and eventually compromising the mold’s structural integrity.
Channel Design Implications
One key design element is the main channel. If its length is excessive, it contributes to significant heat loss of the plastic melt, resulting in substantial temperature differences between the channel and cavity. This discrepancy not only induces thermal stress but also thermal fatigue. For example, with poorly coordinated cooling systems, local overheating6 may cause uneven thermal expansion, leading to mold material deformation.
Channel Design Factors | Impact on Mold Durability |
---|---|
Taper Angle & Surface Roughness | Affects wear degree and thermal stress |
Length of Channel | Influences heat loss and thermal fatigue |
Coordination with Cooling System | Determines thermal balance & longevity |
Runner Design Considerations
Runner designs also play a pivotal role. Long runners increase heat loss, aggravating temperature differences and causing additional thermal stress. This results in thermal fatigue in mold materials, particularly those with poor thermal stability. The layout should facilitate balanced flow to prevent local overheating, which can accelerate material aging.
Balanced runner designs ensure uniform pressure across cavities, reducing risks of deformation from uneven pressure distribution. An unbalanced design might lead to certain cavities experiencing over-pressure, exacerbating wear and thermal fatigue.
Mitigating Thermal Fatigue
Employing materials with high thermal stability can reduce the incidence of microcracks due to thermal fatigue. Additionally, maintaining an optimal channel layout that aligns with the cooling system ensures thermal equilibrium.
Engineers are encouraged to evaluate the flow balance7 within runner systems to mitigate wear and extend mold life. Utilizing computer-aided simulations can predict potential thermal stress points, aiding in proactive design adjustments.
Thermal fatigue causes microcracks in molds.True
Thermal fatigue results from repeated heating and cooling, causing microcracks.
Long runner designs decrease mold thermal stress.False
Long runners increase heat loss, aggravating thermal stress and fatigue.
Why is stress concentration a concern in mold design?
Stress concentration in mold design isn’t simply a technical issue – it’s a possible turning point for durability and performance. Controlling it is essential for your molds.
Stress concentration happens when stress spreads unevenly across a material. This often occurs at places like holes or grooves. In mold design, this problem leads to cracks. These cracks can shorten the mold’s service life. Cracks really reduce how long molds last.
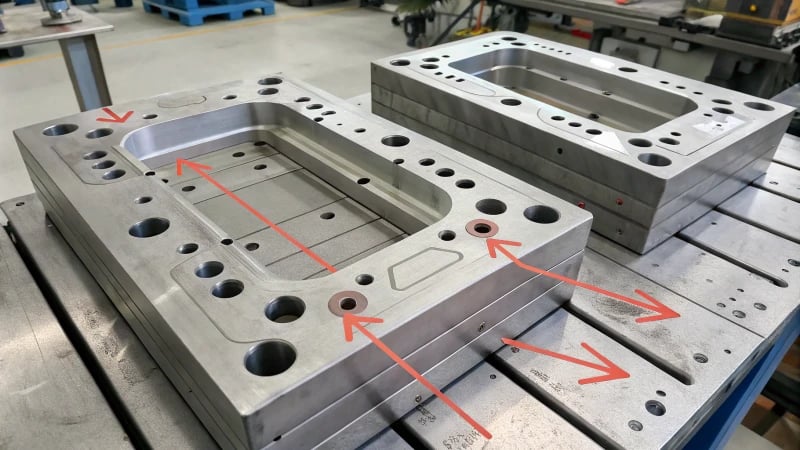
Understanding Stress Concentration
When I started learning about mold design, the term ‘stress concentration’ felt distant. Quickly, it proved vital – like finding a twist in a movie. Stress concentration means areas where stress gathers, such as around holes or sharp corners. Imagine stacking plates; a slight shake could cause them to fall. This is what stress does to molds – it turns small problems into big failures.
In mold design, it is crucial to recognize these stress spots. The channel design8, taper angles, and surface texture influence stress flow. I recall a project where we misjudged these factors, leading to cracks and a shorter mold lifespan. It cost us dearly.
Key Areas of Concern
1. Main Channel Design
Once, the taper angle in a channel caused excessive wear. Think of sandpaper scraping metal; it happens when friction rises due to wrong angles or size mismatches between the channel and nozzle.
-
Impact of Geometry: Design Element Effect on Stress Small Taper Angle Increases friction and stress Mismatched Diameters Causes uneven pressure distribution
2. Runner Design
The runner system is tricky – like a maze without a map. Irregular or unbalanced runners result in uneven flow and high shear forces. I experienced a mold where uneven runners caused severe wear, similar to finding potholes on a new road.
-
Design Challenges: Runner Feature Stress Impact Irregular Shape Increases shear forces Unbalanced Layout Leads to uneven pressure
The Role of Thermal Fatigue
Thermal fatigue sounds like science fiction, but it is a real problem. Temperature changes cause parts of the mold to expand or shrink unevenly. I saw molds with microcracks from misaligned cooling, like an unseen crack in an old mug that suddenly leaks.
Thermal stresses add up over time, causing big damage if unchecked. Properly arranged cooling systems9 help prevent uneven heating or cooling.
Managing Stress Concentration
Addressing stress concentration is truly like chess, requiring several steps ahead. Optimizing design elements, like taper angles and surface texture, manages stress flow. Advanced simulations highlight high-stress spots, allowing for better designs.
Handling these issues can prolong mold life, cut maintenance costs and improve product quality. Smart choices today lead to fewer problems later.
Small taper angles increase stress in molds.True
Small taper angles cause increased friction, leading to higher stress.
Thermal fatigue does not affect mold stress concentration.False
Temperature variations cause expansion differences, increasing stress.
How Can Runner Design Best Practices Enhance Mold Longevity?
Have you ever thought about how changing the runner design could help your mold last longer? Let’s explore the secrets to improving durability against wear and thermal strain.
Improving runner design in injection molding helps molds last longer. This happens by reducing wear and heat fatigue. Important things to consider are the right taper angle, smoothing the surface and balancing the flow. These aspects lower stress and keep the temperature even.
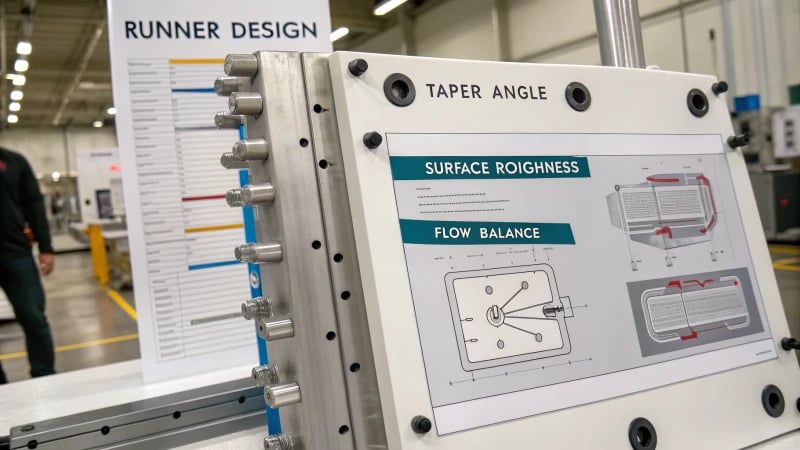
Understanding the Role of Runner Design
In injection molding, the runner design10 is very important. It affects how long molds last. The correct design lowers wear by reducing forces between the plastic and the runner walls. I found that a smooth surface with roughness around Ra = 1.6 minimizes friction and protects molds. Surface smoothness is key.
Key Factors Influencing Wear
Shape and Size
Runner shape and size impact flow dynamics. In one project, irregular shapes increased wear due to higher forces. Consistent flow rates are vital; any inconsistency causes uneven mold wear.
Taper Angle and Roughness
Proper taper angles save molds by cutting down friction. During fast injection, low wall roughness prevents wear from particles.
Factor | Ideal Specification |
---|---|
Taper Angle | Adequate to reduce friction |
Surface Roughness | Ra = 0.8 – 1.6μm |
Managing Thermal Fatigue
Length and Layout
Runner length affects heat loss during flow. Longer runners cause temperature changes, leading to stress and cracks. Good layout keeps the heat even and stops overheating.
Maintaining Flow Balance
Unequal runner times create pressure issues, which deform molds. Equal filling times lead to balanced pressure, preventing overpressure.
Learn more about runner optimization techniques11. Proper focus on this extends mold life, lowers maintenance, and really helps production efficiency.
Additional Considerations
Cooling channels in runners are essential. I saw how a good cooling system works with runners to keep proper mold temperature. Look into advanced cooling strategies12 for even better mold performance.
By adopting these practices, designers extend mold life and cut downtime, achieving greater manufacturing efficiency.
Proper runner design reduces mold wear in injection molding.True
Correctly designed runners minimize shear forces, reducing wear.
Longer runners reduce thermal stress in mold designs.False
Longer runners increase temperature differences, causing thermal stress.
Conclusion
The design of main and branch channels in molds significantly impacts their service life by influencing wear, thermal fatigue, and stress concentration, ultimately affecting performance and longevity.
-
Learn how efficient runner designs reduce wear and improve mold lifespan. ↩
-
Explore techniques to manage thermal stress in molds. ↩
-
Discover strategies to alleviate stress concentration in molds. ↩
-
Uncover key practices that enhance mold durability in injection molding. ↩
-
Explore how repeated temperature changes induce thermal stresses leading to mold wear. ↩
-
Learn about the consequences of uneven cooling on mold integrity and lifespan. ↩
-
Discover how flow balance impacts pressure distribution and wear in molds. ↩
-
Understanding how taper angles affect stress can prevent mold failure, ensuring durability. ↩
-
Proper cooling prevents thermal fatigue, extending the mold’s service life. ↩
-
Gain insights into how runner design affects injection molding efficiency and mold longevity. ↩
-
Learn techniques to ensure even cavity filling and prevent mold deformation. ↩
-
Discover innovative cooling methods to enhance mold performance and lifespan. ↩