I recall the first time I saw an injection molding machine working – it seemed like magic!
When a mold cavity is not filled completely, defects appear. These defects include short shots and rough surfaces. The look and function of the molded items suffer. It’s like trying to finish a jigsaw puzzle without all the pieces. This happens when mold filling is insufficient. Product quality gets hurt.
During my early days at the mold factory, I discovered the importance of fully filling molds. Products appeared with rough surfaces, clearly showing incomplete filling. This often led to items that seemed unfinished, with edges that should have remained smooth turning jagged instead. It’s like attempting a perfect soufflé but ending up with a collapsed one – it’s just not right.
Such defects are not only about looks. They also weaken the structure, leaving products likely to crack under stress. One time, a client faced breaking plastic brackets. The problem? Incomplete filling created weak spots unable to handle pressure. Solving these issues needed careful changes to the molding process, making sure every corner of the mold received enough material. Every corner needed filling.
Insufficient mold filling causes short shots in products.True
Short shots occur when the mold cavity is not fully filled, leading to incomplete products.
Surface roughness improves with insufficient mold filling.False
Insufficient filling leads to surface defects, worsening the product's finish.
What Causes Insufficient Mold Filling in Injection Molding?
Imagine this꞉ you’re working on a big project and suddenly, the quality of your injection-molded parts is not good. Very frustrating, isn’t it?
Low injection pressure often causes insufficient mold filling in injection molding. Limited material supply is another reason. Sometimes, improper machine settings also contribute. Problems in mold design may be a factor too. Solving these issues greatly improves product quality. Quality really matters.
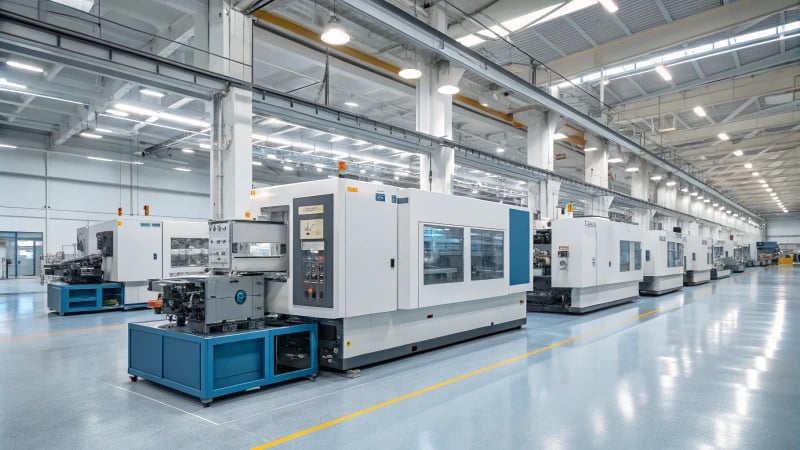
Causes of Insufficient Mold Filling
I’ve been in situations where unexpected defects appear in products, leaving me puzzled about their cause. It feels like baking a cake but missing the baking powder; something important is absent.
Low Injection Pressure
Low injection pressure is a common problem. Think of trying to spread icing on a cake that is too stiff. If the pressure is not correct, the material does not reach every part of the mold cavity1. By adjusting the pressure, like adding a little more milk to that frosting, you reach better results. But be cautious – excessive pressure can create problems like flash.
Inadequate Material Supply
Inadequate material supply is another issue. Imagine running out of flour while making cookies; you can’t fill the mold without enough material. A steady and adequate supply into the injection machine is crucial to prevent "short shots." Important. Very important.
Cause | Effect |
---|---|
Low Injection Pressure | Short shots and incomplete filling |
Inadequate Material Supply | Incomplete product shape |
Improper Machine Settings | Poor surface finish and dimensional deviation |
Mold Design Issues | Uneven density and reduced mechanical strength |
Improper Machine Settings
Improper machine settings resemble setting your oven too low for baking; even with all the right ingredients, it won’t work out well. Incorrect temperature or timing might lead to premature cooling and incomplete filling. Regularly checking these settings is as vital as double-checking a recipe.
Mold Design Issues
Mold design problems are like picking a cake pan that’s too small; it just doesn’t function properly. Thin walls or complex shapes in mold design need careful attention to allow proper material flow. Improving design with simulation tools or consulting design experts2 avoids these mistakes.
-
Appearance Effects:
- Short Shot Phenomenon: Creates surfaces that appear incomplete.
- Increased Surface Roughness: Causes flow marks or ripples.
- Dimension Deviation: Leads to products that are undersized.
-
Performance Effects:
- Decrease in Mechanical Properties: Makes products prone to stress cracks.
- Uneven Density: Affects thermal and acoustic qualities.
By understanding these factors, I put strategies into action to avoid insufficient mold filling, probably achieving high-quality production consistently.
Low injection pressure causes short shots.True
Low pressure fails to fill the mold completely, leading to short shots.
Proper machine settings have no impact on mold filling.False
Incorrect settings can cause premature cooling, affecting mold filling.
How does the short shot phenomenon affect product appearance?
Have you ever thought about how a small mistake in injection molding changes your carefully crafted product into an eyesore?
Short shot phenomenon causes surfaces to remain unfinished. The textures often turn out rough and the sizes deviate in injection-molded products. This compromises both their look and how they work. Surfaces stay incomplete.
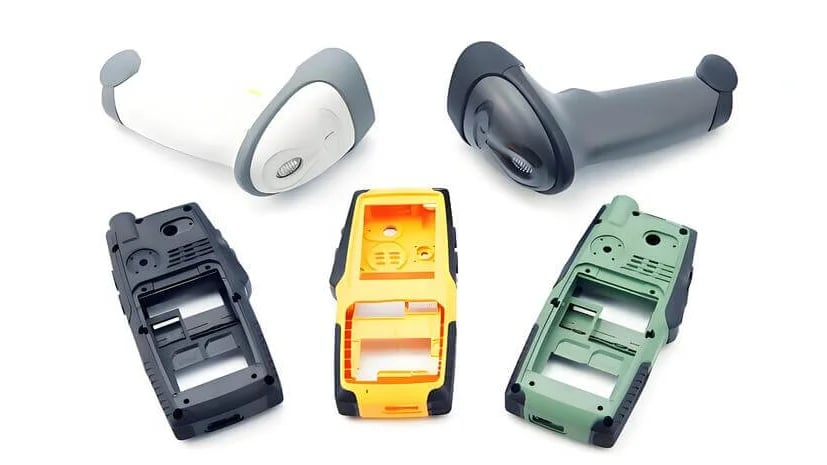
Incomplete Product Surfaces
Picture spending hours crafting a design, only to see the final item looking like it’s missing parts. Short shot problems cause this. When the mold does not fill sufficiently3, products appear unfinished, like a thin plastic shell not fully formed. Frustration hit hard when our slender handles looked like Swiss cheese. It’s a usual trouble with complex shapes. It really tests patience.
Increased Surface Roughness
Imagine expecting a shiny, smooth finish but getting an item that feels like sandpaper. Roughness occurs when plastic flow becomes uneven from incomplete filling. Visualize a clear container meant to sparkle, but instead, it feels dull and rough. It’s a tough reality, especially after promising a flawless product.
Product Type | Effect of Short Shot | Visual Impact |
---|---|---|
Slender Handles | Incomplete Formation | Unfinished Look |
Transparent Containers | Surface Roughness | Diminished Clarity |
Dimensional Deviations
Size issues arise too. If short shots happen, nothing fits correctly due to dimensional deviations. I’ve struggled with plastic gears that refused to align. This isn’t just about looks; it impacts functionality as well. Think of buckles that won’t buckle! Yes, these deviations can harm a product.
Broader Implications on Appearance
Mistakes affect more than just a product’s look – they can tarnish a brand’s image. For designers like Jacky and me, understanding these problems is vital. Designs must not only be visually pleasing but also functional. No one wants a product that falls short of its promise.
For more understanding, studying injection molding techniques4 can show ways to improve material flow.
Short shots cause incomplete product surfaces.True
Short shots occur when molds are not fully filled, leading to incomplete surfaces.
Short shots improve the transparency of plastic items.False
Short shots increase surface roughness, reducing transparency and gloss in plastics.
How Does Insufficient Filling Impact Mechanical Properties?
Have you ever thought about how a small space might weaken a plastic piece?
Not enough filling in injection molding weakens mechanical properties. It causes incomplete structures and uneven density. Strength reduces. Toughness lowers. Product reliability worsens.
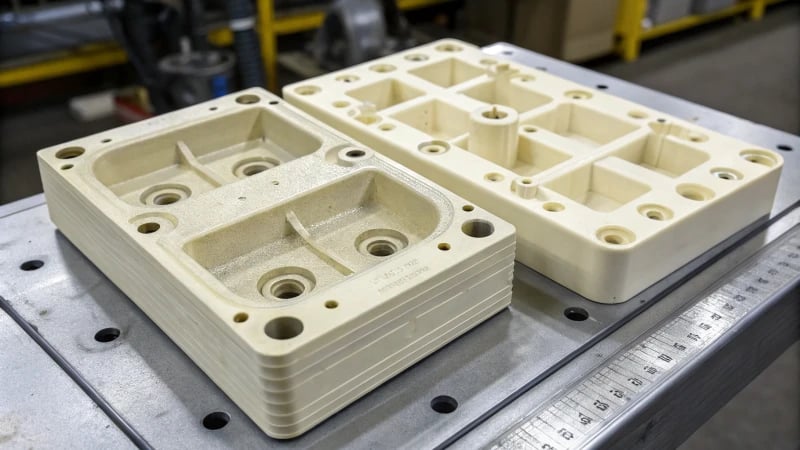
Appearance Problems
When molds are insufficiently filled, the appearance of products can suffer. Short shots occur when the mold doesn’t get all the material it needs, leaving some parts undone. This is especially sad for detailed designs where every part counts. Imagine putting effort into a design only to see rough spots or marks on it – like waves on a peaceful sea.
Appearance Issue | Effect |
---|---|
Short shot phenomenon | Visibly incomplete product areas |
Increased roughness | Unstable flow creates surface defects |
Loss in Strength
The mechanical properties of products are often compromised by insufficient filling. Strength and toughness are reduced as unfilled sections create weak points in the structure. This can lead to cracking or breakage under stress, such as bending or impact. Picture a plastic clip5 that can’t do its job because of these weak spots.
- Strength and Durability: Weak spots that might break
- Density Spread: Uneven spread affects how it works
Uneven Density and Its Impact
Uneven density causes more issues. It’s like trying to balance on a seesaw with a shaky weight. Dense areas have different heat and sound properties than empty ones. For things like insulation containers6, this difference can be a big problem, hurting how they work in ways you might not want to think about.
Performance Issue | Resulting Problem |
---|---|
Uneven density | Alters thermal/acoustic properties |
Short shots lead to incomplete product areas.True
Short shots occur when molds are not fully filled, causing visible incompleteness.
Uneven density improves product thermal properties.False
Uneven density negatively affects thermal properties by creating inconsistent material distribution.
How Can I Ensure Complete Mold Filling?
Look closely at an injection molded product. Notice that some edges seem as if a piece is absent. Is it puzzling?
Proper mold filling requires adjusting injection speed and pressure accurately. Molds need precise designs to work properly. Optimal material temperature is vital. Good venting allows air to escape. These steps stop issues like short shots and uneven density. Quality and looks in the final product depend on these processes. Quality is key.
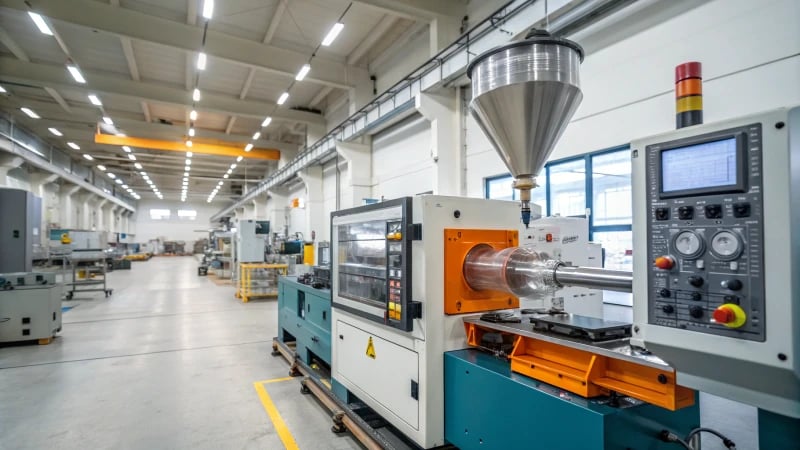
Optimize Injection Speed and Pressure
Adjusting injection speed and pressure is like tuning a musical instrument. Too much speed causes defects like short shots because the plastic doesn’t cool evenly. On the other hand, low pressure might let material leak out of the mold. It’s all about finding the balance. It’s vital that the material fills every part of the mold perfectly.
- Injection Speed: Optimize injection speed7 to ensure complete filling without defects.
- Pressure Control: Balance pressure to prevent flash and ensure full cavity filling.
Proper Mold Design
Designing a mold is like planning a city. Gates and runners act like roads, allowing smooth flow. A poorly placed gate is like a roadblock during rush hour; nothing moves smoothly. The runner system must work well so every part of the mold receives enough material.
Aspect | Description |
---|---|
Gate Placement | Reduces flow path length for better material flow |
Runner System | Ensures even distribution of material |
Maintain Material Temperature
Temperature control is both science and art. If it’s too low, plastic might harden early, leading to incomplete filling. Consistent temperature is crucial as it allows the material to flow smoothly into every mold corner, achieving the perfect surface finish.
- Temperature Control: Maintain consistent temperature8 throughout to reduce surface roughness and dimension deviation.
Proper Venting
Vents allow the mold to breathe. Without vents, trapped air creates flaws—think of tiny bubbles on plastic items. Well-placed vents let air escape, guaranteeing a smooth finish each time.
By addressing these factors, product designers can ensure their creations meet both aesthetic and functional standards expected by clients. Consulting resources such as CAD software guides can further optimize designs for large-scale production.
High injection speed minimizes cooling defects.True
High speed reduces cooling rates, preventing defects like short shots.
Low pressure increases the risk of flash in molds.False
Low pressure actually prevents flash by reducing excess material flow.
Conclusion
Insufficient mold filling in injection molding leads to defects like short shots, rough surfaces, and reduced mechanical properties, compromising both the appearance and functionality of products.
-
Explore how mold cavity design impacts product quality in injection molding. ↩
-
Discover how expert consultation can enhance mold design. ↩
-
Discover how insufficient mold filling leads to incomplete product surfaces and affects aesthetics. ↩
-
Explore methods to prevent short shots and ensure complete mold filling for better product quality. ↩
-
Learn about short shot phenomena and how they affect the integrity of molded products. ↩
-
Explore how uneven density affects the performance of insulation containers. ↩
-
Learn how adjusting speed and pressure prevents defects like short shots. ↩
-
Explore methods for maintaining consistent material temperature during molding. ↩