Do you ever think about how a small change in mold design affects your entire production line? A minor adjustment might greatly impact success or failure.
Problems in mold design might greatly change the injection molding process parts, like pressure, speed and time. Important elements such as the size of the gate, layout of the runner and design for exhaust hold major importance in how the melt flows and how efficiently cavities fill up. Tackling these issues really helps to simplify production and reduce flaws.
I have seen small changes in mold design create big effects in production. Changing the gate size impacts flow. A larger gate lets the melt flow easily with lower pressure. But a smaller gate requires more pressure, risking problems like mold deformation.
The runner system is also crucial. A poorly planned runner layout causes uneven fill times in cavities. But a balanced design fills all cavities at the same time. It is like a symphony where every part should work together in harmony.
Exhaust design is often overlooked. Poor exhaust placement traps air in the cavity, requiring higher injection pressure to move the melt inside. Well-placed vents allow the melt to enter smoothly.
Each part of the mold design fits like pieces of a puzzle. Correctly aligned elements change injection molding from frustrating to perfect. Really perfect.
Gate size affects injection pressure in molding.True
The gate size directly influences the pressure needed to fill the mold cavity.
Runner system layout has no impact on melt flow.False
The runner system layout is crucial for directing and balancing melt flow.
How Does Gate Design Affect Injection Molding Efficiency?
Have you ever thought about how a simple gate’s design drastically improves injection molding efficiency?
Gate design plays a big role in how well injection molding works by affecting things like pressure, speed and time. Choosing the correct gate size and position really helps. The right number of gates also reduces defects. Proper gate placement allows for even filling.
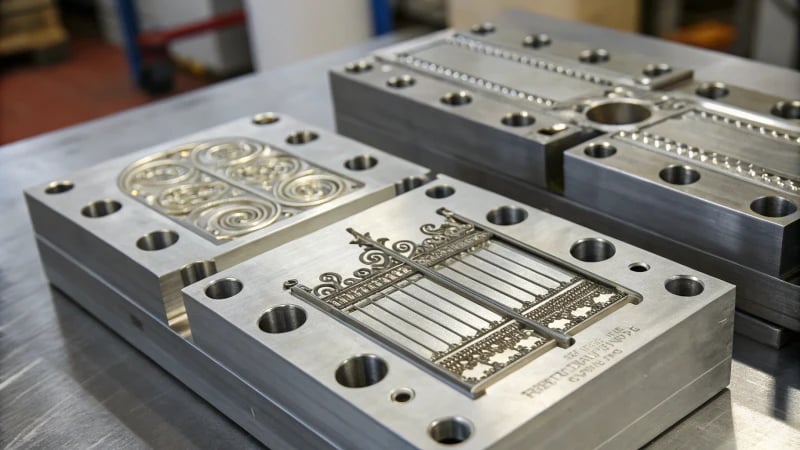
How Gate Size Affects Injection Pressure
A time in my workshop, I noticed how gate size changes everything. Bigger gates let the melt flow easily, lowering the pressure needed. Smaller gates demand higher pressure to maintain movement. It’s like adjusting a faucet – too much pressure could cause issues like mold deformation. So, choosing the right gate size is really important.
Gate Size | Injection Pressure |
---|---|
Large | Low |
Small | High |
Gate Position and Injection Speed
Gate position determines flow1, similar to placing a fan in a room. A central gate provides equal flow, much like air spreading evenly. On the other hand, an off-center gate needs adjustments to avoid problems like weld marks.
- Central Gate: Equal flow
- Offset Gate: Needs speed adjustment
Number of Gates and Injection Time
While trying different gate numbers, I saw that more gates can shorten the path of the melt, reducing injection time2 a lot. However, too many gates might complicate the design and lead to quality issues. Finding the right number of gates is like cooking; too much or too little changes everything.
Number of Gates | Injection Time |
---|---|
Few | Longer |
Many | Shorter |
Influence of Runner System Design
Designing runners feels like crafting rivers. Their size and shape affect flow greatly. Larger runners create smoother flows at lower pressures, similar to a wide river. A balanced setup ensures even filling, like water reaching every part at once.
Runner Characteristic | Effect on Process |
---|---|
Larger Size | Lower Pressure |
Balanced Layout | Stable Time |
Exhaust System Design
Exhaust systems work like pressure release valves, reducing resistance in cavities. A good setup cuts down pressure, but a poor one might lead to defects. Correct positioning keeps flow stable, which is really vital.
By refining exhaust systems alongside gate sizes3 and runner designs, we see great strides in molding efficiency.
Larger gates reduce injection pressure in molding.True
Larger gates lower resistance, allowing smoother melt flow at reduced pressures.
Central gate positions increase injection speed.False
Central gates allow balanced flow, not necessarily increased speed.
How Does the Runner System Affect Injection Molding?
Have you ever thought about how a simple plastic piece gets its form? The runner system in injection molding plays a crucial role in this process, guiding the flow with great accuracy.
The runner system in injection molding resembles a highway for molten plastic. It efficiently directs the plastic from the injection unit to the mold cavities. It manages flow, affecting both pressure and speed. This system plays a critical role in production efficiency. It also impacts part quality. Production efficiency and part quality depend on it.
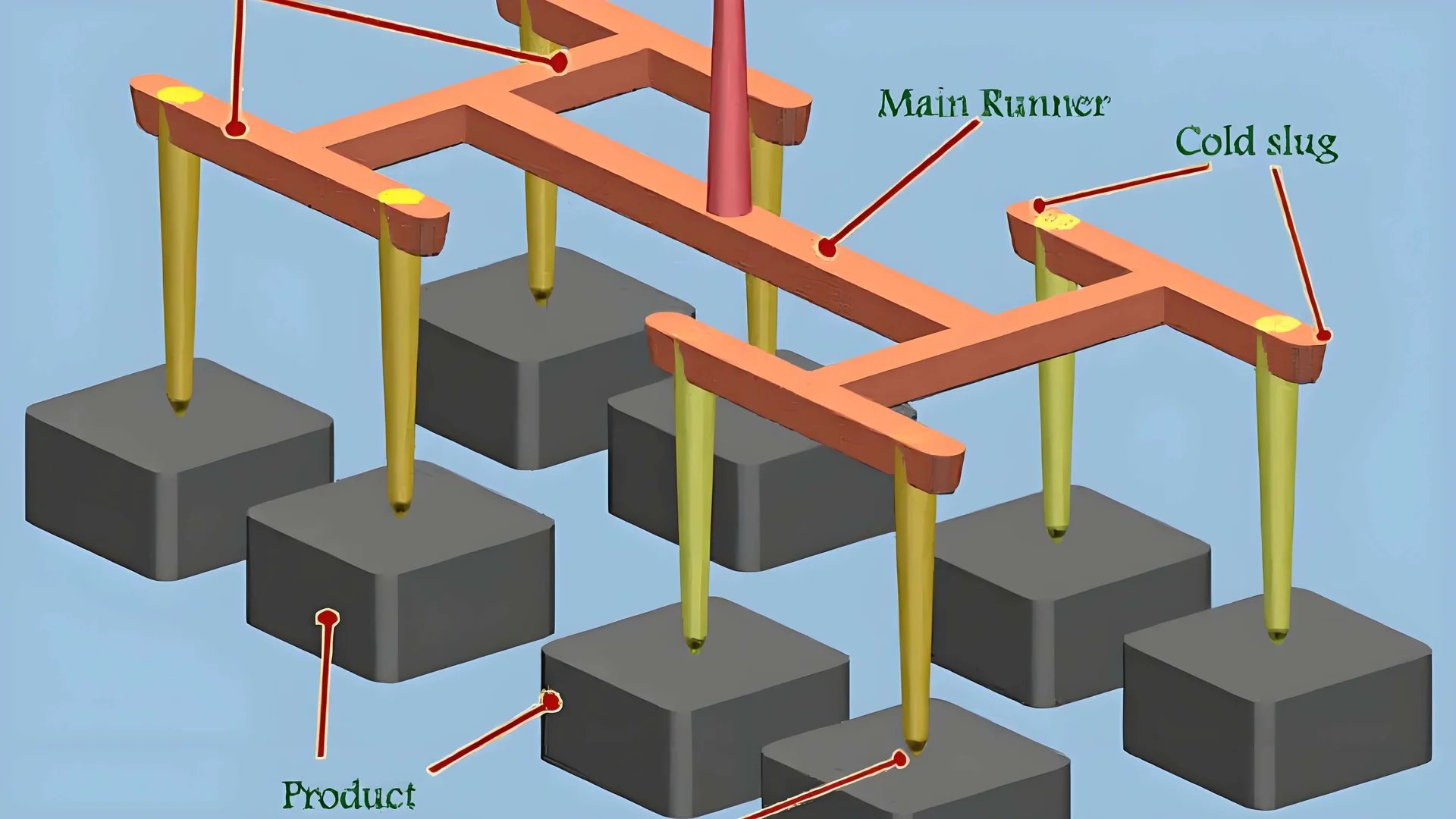
Understanding the Runner System in Injection Molding
Think of a busy city, with cars driving through a network of roads. This is like the runner system in injection molding. It guides hot, liquid plastic to its target, ensuring a steady flow. This system strongly influences the quality and efficiency of everyday products.
Runner Size and Injection Pressure
Runner size is crucial in molding. Like freeway lanes, a bigger runner allows smoother traffic, requiring less force to move the plastic. But this larger size also results in more waste and longer cooling. I once used a large runner, hoping to reduce pressure, but ended up with increased waste. The runner size matters a lot.
Runner Size | Impact on Pressure | Material Waste |
---|---|---|
Large | Low | High |
Small | High | Low |
Runner Shape and Injection Speed
Runner shape plays an important role too. Circular runners act like smooth roads, allowing for a gentle pace. But rectangular runners resemble twisty paths, needing a faster push. I experimented with different shapes while designing a mold. Finding the perfect shape was tricky but very fulfilling.
Runner Layout and Injection Time
A good layout is like well-timed traffic lights, with every part filling up simultaneously. I remember having an unbalanced layout once, leading to uneven filling. That experience taught me precision is key.
Knowing these aspects helps designers like Jacky fine-tune their plastic creations4. Runner size, shape and layout work together to improve molding processes and build successful products.
For those curious about injection molding mechanics5, studying various runner designs provides new ideas for better production and precise products.
Larger runners decrease injection pressure needed.True
Larger runners reduce flow resistance, lowering pressure requirements.
Circular runners require higher injection speeds.False
Circular runners enable smooth flow, requiring lower injection speeds.
Why Is Exhaust Design Crucial for Molding Quality?
Some plastic gadgets work perfectly, but others have small annoying problems. Exhaust design in molding usually causes this difference. Let’s find out why this matters so much.
Exhaust design plays a key role in injection molding. It lets gases escape easily. This stops problems like burn marks and incomplete fills. Correct exhaust placement improves product quality. It also increases production efficiency.
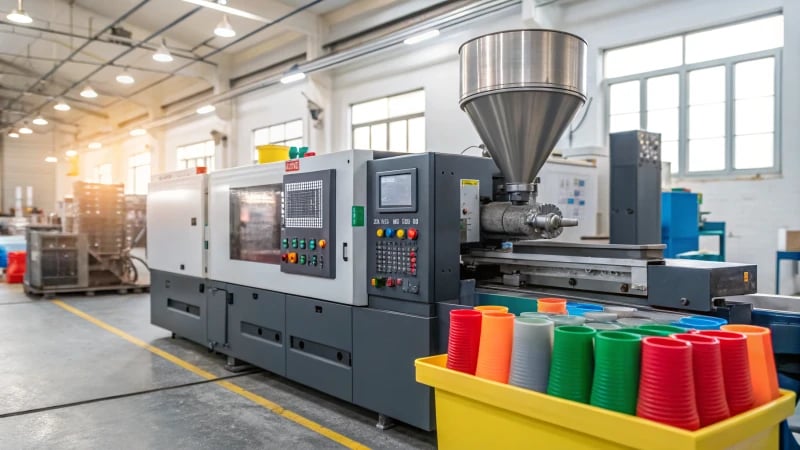
The Role of Exhaust Design in Injection Molding
I remember when I first faced a plastic piece that simply refused to come out correctly. It was during a project for smooth smartphone cases. We kept seeing ugly burn marks, and it drove us mad. That’s when I learned about the importance of good exhaust design. Allowing trapped air and gases to leave during the molding process6 reduced back pressure that causes annoying defects like burn marks or incomplete shapes. It felt like opening a window in a stuffy room, letting everything move more smoothly.
Exhaust Effect | Impact on Quality |
---|---|
Proper Ventilation | Fewer Defects |
Poor Ventilation | Burn Marks, Flash |
Impact of Exhaust Position and Method
Changing living room furniture sometimes makes everything feel great, right? It’s the same with exhaust positioning. Best exhaust ports stay at the last filling points to keep flow steady and stop turbulence. I tried various methods like grooves or vacuum pumps, resulting in huge changes in injection time. Discovering the best spot for exhaust can transform the process.
The positioning of exhausts is crucial. Ideally, exhaust ports should be located at the last filling points. This strategy ensures that the melt maintains a stable flow rate, preventing turbulence which can lead to uneven injection speeds7. Selecting appropriate exhaust methods is essential for optimizing injection time.
Exhaust Design Considerations
Exhaust and Injection Pressure
A smart exhaust lowers the need for high injection pressure, saving energy and keeping the mold safe from damage caused by too much pressure.
Exhaust Methods and Injection Time
Different methods greatly affect injection times. Natural venting might slow cycles, but advanced ways like vacuum pump exhausts increase efficiency.
For those curious about improving molding outcomes, see more on runner system designs8 that work with exhaust systems.
Understanding these parts has helped mold designers like me improve processes, bringing about better quality and productivity. Managing exhaust design has been key to solving common defects and producing high-quality products efficiently.
Exhaust design prevents burn marks in injection molding.True
Proper exhaust design allows gases to escape, preventing burn marks.
High injection pressure is needed with good exhaust design.False
Good exhaust design reduces the need for high injection pressure.
How Does Mold Design Influence Injection Time and Pressure?
Ever thought about how a simple design change might transform your injection molding process?
Mold design improvement really decreases injection time and pressure by changing gate size, position, number, runner system dimensions and exhaust settings. These changes not only help efficiency but also reduce defects. The end result is a higher quality product.
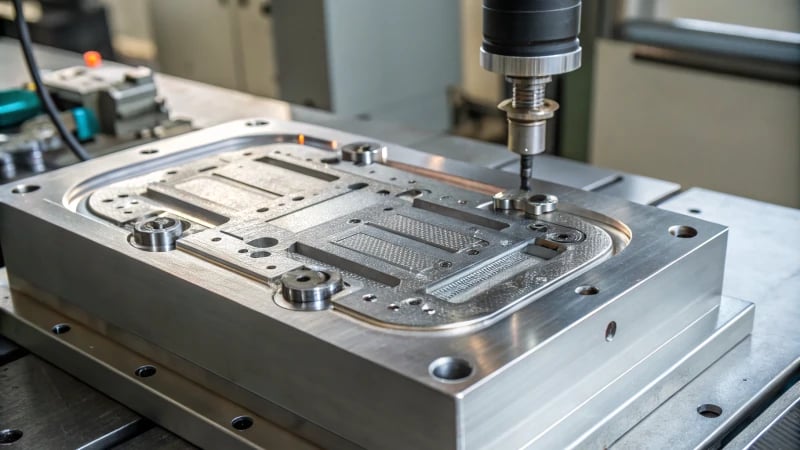
A Personal Story of Gate Design
Let me tell you about a project that showed me how important gate design is. I remember struggling with a mold that wouldn’t behave. The final products came out with frustrating deformations, and I didn’t know why. Then, I realized I had ignored gate size and position. I increased the gate size, and instantly things got better. Injection pressure went down, and the melt moved more freely. It was like completing a puzzle!
-
Gate Size: Imagine a wide open door welcoming guests easily; that’s a bigger gate in the mold world. It lowers melt resistance and needs less injection pressure. When I tried smaller gates, it felt like squeezing through a narrow path – pressure rose and risks of deformation grew.
-
Gate Position: Think of a central gate as hitting the bullseye in darts – it gives even distribution. An off-center gate is like playing pinball with the flow paths. I learned that off-center gates require careful speed control for smoothness.
-
Number of Gates: Picture having several shortcuts on your journey; that’s what more gates offer for injection time. Shorter paths mean quicker fills, but watch out for unwanted weld marks if not cautious.
Runner System Discoveries
Runners are the unseen champions of mold design – when designed properly, they make everything work smoothly.
-
Runner Size: Larger runners are like wide roads – they decrease flow resistance and save pressure. If too big, you’ll waste materials, like taking the scenic route when you need speed.
-
Runner Shape: Circular runners allow the melt to flow smoothly at lower speeds. Imagine them as the lazy rivers in your mold layout.
-
Runner Layout: Balanced layout matters – all cavities should fill at the same time, like synchronized swimmers moving in unison.
Exhaust Design Insights
The exhaust system is like air vents in a crowded room – if designed correctly, everyone breathes comfortably.
-
Exhaust Effect: Good exhausts reduce cavity air resistance. This makes melt flow easier and decreases needed injection pressure.
-
Exhaust Position: Putting them in the right place keeps melt flow stable – it’s like having windows where cool breezes come in.
-
Exhaust Method: Using techniques like exhaust grooves is like opening all windows wide – it speeds up filling and cuts injection times.
I’ve spent many hours exploring gate design influence9, runner system impacts10, and exhaust configurations11. These discoveries allowed me to better manage air resistance and improve mold flow. These hard-learned lessons have really improved product quality while reducing costs.
Larger gates reduce injection pressure in mold design.True
Larger gates decrease melt resistance, requiring less pressure.
Circular runners increase flow resistance in molding.False
Circular runners offer smoother melt flow, reducing resistance.
Conclusion
Mold design significantly influences injection molding parameters like pressure, speed, and time. Key factors include gate size, runner layout, and exhaust design, impacting efficiency and product quality.
-
Discover how the position of a gate affects the distribution speed of materials during molding. ↩
-
Understand how using multiple gates can optimize or complicate the injection time. ↩
-
Learn how different gate sizes influence the pressure required in injection molding processes. ↩
-
Learn how to optimize plastic component design for electronics to enhance functionality and aesthetics. ↩
-
Understand the fundamental principles of injection molding to enhance your production techniques and outcomes. ↩
-
Discover why effective exhaust design is key to preventing defects in molded products. ↩
-
Learn how exhaust positioning influences the flow rate and injection speed. ↩
-
Find out how runner systems complement exhaust designs to improve molding efficiency. ↩
-
Learn how strategic gate design can enhance molding efficiency and reduce defects. ↩
-
Explore how optimizing runner systems improves flow path control. ↩
-
Understand how managing air resistance enhances mold performance. ↩