Engineering plastics have revolutionized how I approach design challenges, offering unparalleled flexibility and strength.
Engineering plastics are high-performance materials that I rely on for creating industrial components with superior mechanical, thermal, and chemical resistance. In injection molding, these plastics empower me to produce intricate, reliable parts with precision.
I remember the first time I used polyamide in a project. The high tensile strength allowed me to manufacture mechanical parts that could withstand significant loads. It was a game-changer, especially in high-stress environments. Each project is a chance to explore these materials’ unique benefits further, from their outstanding molding accuracy to their impressive design flexibility. Using engineering plastics in injection molding has consistently given me the confidence that my designs will not only meet but exceed industry standards.
Engineering plastics are used in injection molding.True
Engineering plastics are commonly used in injection molding for creating complex parts.
Engineering plastics offer poor thermal resistance.False
Engineering plastics are known for their superior thermal resistance properties.
- 1. What Makes Engineering Plastics So Special?
- 2. Why Are Engineering Plastics Ideal for Injection Molding?
- 3. What Are the Advantages of Using Engineering Plastics in Manufacturing?
- 4. How Do Different Engineering Plastics Compare in Performance?
- 5. How are engineering plastics used in real-world applications?
- 6. Conclusion
What Makes Engineering Plastics So Special?
Ever wondered why engineering plastics are the unsung heroes of modern manufacturing?
Engineering plastics are notable for their outstanding mechanical strength, thermal stability, chemical resistance, and dimensional accuracy, ideal for challenging industrial uses.
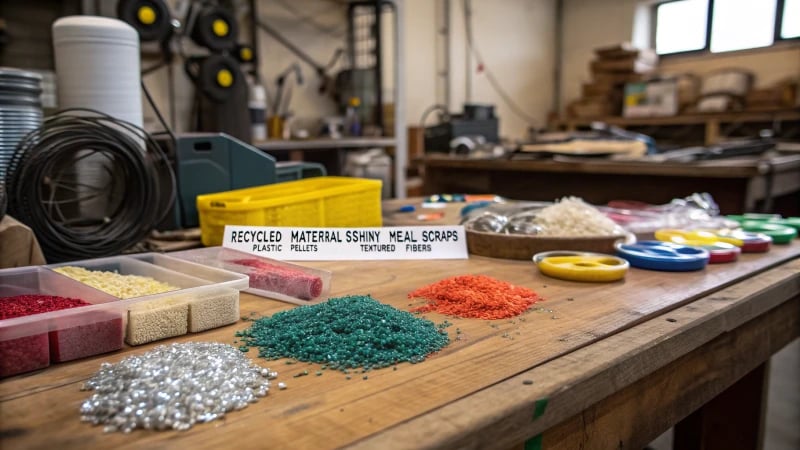
Definition and Features
I remember the first time I encountered engineering plastics in a project. I was amazed by their ability to endure harsh conditions without breaking a sweat. These materials are used for industrial parts and housings due to their high-performance nature. They can withstand mechanical stress over a wide temperature range and tough chemical environments. Here are some standout characteristics:
-
Mechanical Properties: Picture this – you’re designing a new automotive part, and you need something that can handle significant stress. Polyamide (nylon) is your best friend here. It’s strong and tough, perfect for heavy-duty applications.
-
Thermal Stability: Imagine working on a component that must endure high temperatures. Polycarbonate would be your go-to material. It retains its shape and function even when the heat is on.
-
Chemical Resistance: If you’ve ever worked in environments with harsh chemicals, you know the importance of resistance. Polysulfone can handle acids and alkalis like a pro.
-
Dimensional Stability: When precision is crucial, like in high-tech gadgets, polyphenylene ether ensures that parts remain accurate regardless of environmental shifts.
Advantages in Injection Molding
The versatility of engineering plastics shines in injection molding. Their unique properties contribute significantly to the precision and quality of the final product:
-
High Molding Accuracy: I recall a time when I needed to produce a casing for an electronic device with stringent size requirements. Engineering plastics like PC-ABS alloys provided the perfect solution, thanks to their fluidity and stability.
-
Enhanced Product Performance: During an injection molding process, the strength and resilience of polyamide can be fully utilized. This means gears or other components can bear loads effectively.
-
Design Flexibility: I love that engineering plastics allow for creative freedom. Whether it’s adjusting injection parameters or trying out complex shapes, materials like polyacetal (POM) make it possible to push design boundaries.
Common Applications
Here are some engineering plastics commonly used in injection molding along with their applications:
Plastic Type | Application | Key Benefits |
---|---|---|
Polycarbonate (PC) | Electronics & Optics | High impact resistance, optical clarity |
Polyamide (Nylon) | Automotive & Machinery | Wear resistance, self-lubricating |
In my experience, these materials offer a brilliant balance between mechanical prowess and processing ease, making them indispensable across industries. For more insights into how engineering plastics1 elevate product design and manufacturing, dive deeper into their world.
Polyamide is used for automotive mechanical parts.True
Polyamide's high strength and toughness make it ideal for automotive parts.
Polysulfone lacks resistance to chemical environments.False
Polysulfone is known for its strong resistance to acids and alkalis.
Why Are Engineering Plastics Ideal for Injection Molding?
When I first discovered engineering plastics, I was amazed by their potential in revolutionizing injection molding. Let’s explore why these materials have become a game-changer for industries everywhere.
Engineering plastics are ideal for injection molding due to their strong mechanical properties, thermal stability, and chemical resistance, enabling precise and durable product manufacturing.
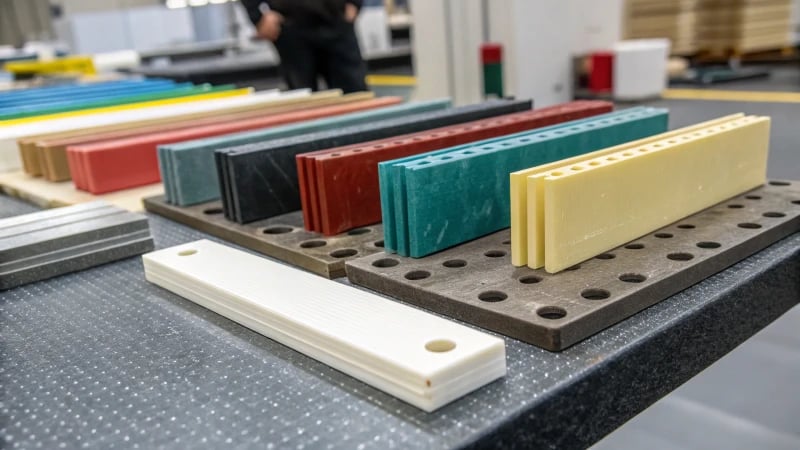
Characteristics of Engineering Plastics
I remember the first time I held a part made from engineering plastic, like polyamide. It felt like holding a piece of the future—light yet incredibly strong. These plastics are designed to endure, withstanding stress and high temperatures without breaking a sweat. Materials like nylon boast impressive tensile strength, making them perfect for demanding applications in fields like automotive and electronics.
Property | Example Material | Key Feature |
---|---|---|
Mechanical Strength | Nylon | High tensile strength |
Thermal Stability | Polycarbonate | Heat distortion resistance |
Chemical Resistance | Polysulfone | Resistant to acids and alkalis |
Advantages in Injection Molding
Working with engineering plastics has taught me the beauty of precision. Imagine crafting electronic components with PC-ABS alloys, achieving remarkable dimensional accuracy thanks to their fluidity and stability. It’s like having an artist’s brush that never fails you, creating intricate designs that meet stringent industry standards.
- Product Performance: Consider polyamide gears2—each tooth is a testament to its ability to endure wear in transmission systems. These gears are a perfect example of how engineering plastics can transform product performance.
- Design Flexibility: The adaptability of these materials allows me to experiment with mold designs, tailoring them to the unique traits of each plastic, such as the versatility of polyacetal (POM) in crafting complex shapes.
Common Engineering Plastics in Use
The versatility of engineering plastics is something I’ve come to rely on across various projects:
- Polycarbonate (PC): Its use in electronics, like computer monitor shells, is driven by its impact resistance and transparency. Each piece crafted feels like a small triumph of engineering.
- Polyamide (Nylon): In the automotive world, nylon’s durability makes it indispensable for engine parts. I’ve seen it endure countless tests, proving its reliability time and again.
These materials open a world of possibilities, allowing engineers like me to create products that not only meet but exceed expectations in quality and precision. For more insights on the application of engineering plastics3 across different sectors, you can explore case studies that showcase their transformative impact on product development.
Nylon has high tensile strength ideal for gears.True
Nylon's high tensile strength makes it suitable for wear-resistant gears.
Polycarbonate lacks thermal stability in electronics.False
Polycarbonate is known for its superior thermal stability, suitable for electronics.
What Are the Advantages of Using Engineering Plastics in Manufacturing?
Ever wondered why engineering plastics are a game-changer in manufacturing?
Engineering plastics enhance manufacturing with high mechanical strength, thermal stability, and chemical resistance, improving performance and design flexibility for demanding applications across industries.
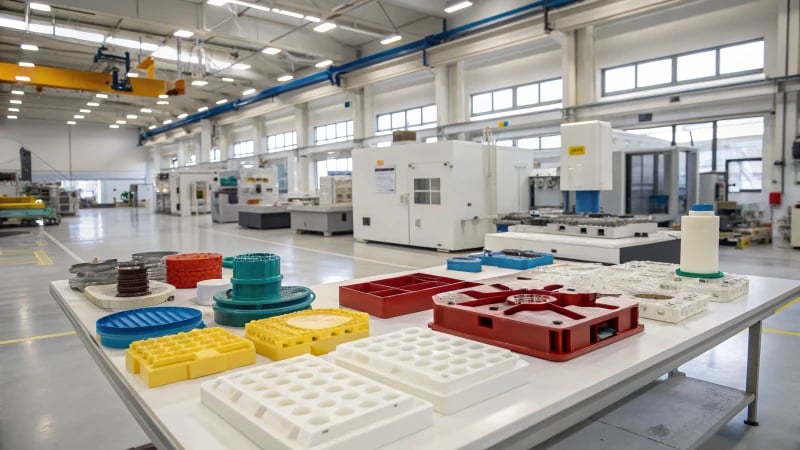
High Mechanical and Thermal Properties
When I first encountered engineering plastics like polyamide (nylon), I was amazed by their high tensile strength4. It reminded me of my early days in manufacturing, when I marveled at how these materials could withstand significant mechanical stress. It’s like watching a superhero take on intense challenges without breaking a sweat. They can endure high temperatures too, which makes them perfect for tough environments.
Property | Example Material | Application |
---|---|---|
High tensile strength | Polyamide (Nylon) | Mechanical parts like gears |
Thermal stability | Polycarbonate | Electronic device housings |
Chemical Resistance
One time, I was working on a project involving harsh chemicals. That’s when polysulfone came into play with its incredible resistance to acids and alkalis. It was like having an invisible shield against corrosion. This quality makes these plastics a fantastic alternative to metals, cutting down on weight and boosting longevity.
Precision in Injection Molding
Precision in injection molding is a thrill for anyone who loves getting things just right. For example, PC – ABS alloys5 have this uncanny ability to maintain tight dimensional tolerance, which is crucial as electronic devices keep getting smaller and more intricate.
Versatile Design Options
The flexibility in design with engineering plastics is something I can’t help but get excited about. It’s like being a kid in a candy store, except the candy is materials like polyacetal (POM), which let us mold complex shapes and structures to meet any product specification.
Case Studies: Common Applications
Polycarbonate (PC):
I remember seeing my first polycarbonate computer monitor shell and being struck by its clarity and resilience. These materials are perfect for electronics, with their transparency and impact resistance making them the go-to for items like phone back covers.
Polyamide (Nylon):
In the automotive industry, nylon is a true workhorse. Its durability and wear resistance make it ideal for engine parts and seat components. I’ve seen it perform beautifully in small transmission parts, thanks to its self-lubricating properties.
Material | Application Field | Benefits |
---|---|---|
Polycarbonate | Electronics | High impact resistance, transparency |
Polyamide | Automotive | Durability, wear resistance |
By embracing these amazing properties of engineering plastics, manufacturers can significantly boost product quality and efficiency. Whether it’s about cutting down weight or enhancing precision, these materials offer a compelling alternative to traditional options like metals or standard plastics.
Explore more about advanced manufacturing techniques6 with these innovative materials to stay ahead in the competitive landscape.
Polyamide is used for gears due to high tensile strength.True
Polyamide, or nylon, is known for its high tensile strength, ideal for gears.
Polysulfone lacks chemical resistance in harsh environments.False
Polysulfone is chemically resistant, making it suitable for harsh environments.
How Do Different Engineering Plastics Compare in Performance?
Ever wondered how engineering plastics stack up against each other in performance? Let’s dive into the fascinating world of these materials and see what makes each one special.
Engineering plastics, including polyamide, polycarbonate, and polysulfone, vary in mechanical strength, thermal stability, and chemical resistance. Selection should align with application requirements like load capacity, temperature tolerance, and environmental factors.
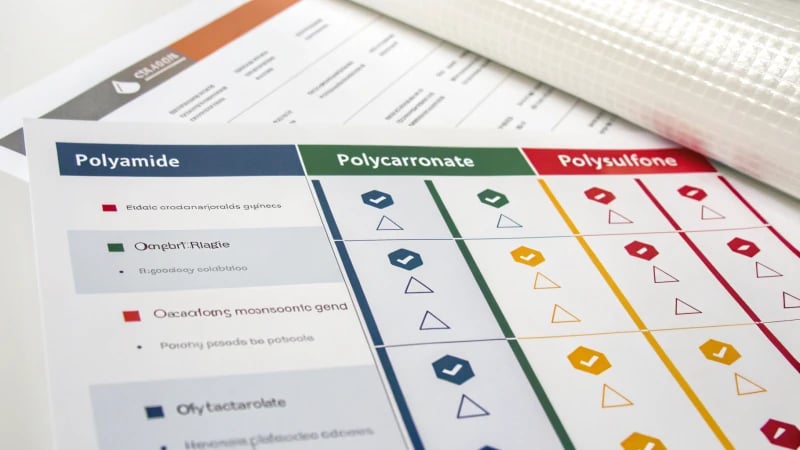
Characteristics of Engineering Plastics
I remember the first time I had to choose the right material for a project. It felt like standing in front of a buffet without knowing what any of the dishes were. That’s when I realized just how critical understanding engineering plastics is. These high-performance materials, such as polyamide (or nylon), boast impressive mechanical properties like strength and toughness. I once used nylon for mechanical parts that needed to withstand significant loads.
Property | Polyamide (Nylon) | Polycarbonate (PC) | Polysulfone |
---|---|---|---|
Mechanical Strength | High | Medium | Medium |
Thermal Stability | Moderate | High | Moderate |
Chemical Resistance | Moderate | Low | High |
Then there’s polycarbonate (PC), which I’ve seen perform beautifully in high-temperature settings thanks to its excellent thermal stability. And don’t get me started on polysulfone—its ability to resist acids and alkalis has saved my projects more than once!
Advantages in Injection Molding
Ah, injection molding. This process allows for remarkable precision. I’ve found that using engineering plastics in this method ensures high accuracy due to their fluidity and stability. Picture this: crafting precise electronic equipment shells with PC-ABS alloys7. It’s like sculpting with a material that listens to your every command.
- Accuracy: Achieving dimensional precision is crucial for miniaturized products—something I learned while designing intricate gears from polyamide.
- Performance: Enhances mechanical and thermal properties, which is especially useful when working with polyamide gears.
- Design Flexibility: It’s like having a flexible friend who adapts to your needs. I once designed a thin-walled product using polyacetal (POM), adjusting the parameters just right to nail it.
Case Studies of Engineering Plastics in Use
Reflecting on my experiences, Polycarbonate (PC) is a favorite in electronics. Its transparency and impact resistance make it perfect for monitor shells and phone covers. I’ve also marveled at its use in optics, where it shapes lenses due to its ideal refractive index and optical properties.
Polyamide (Nylon), meanwhile, shines in the automotive world. I’ve worked on engine components and seat parts using nylon because its durability is second to none. In machinery manufacturing, nylon’s self-lubricating properties make it a go-to for small transmission parts8.
Each plastic has its own unique set of traits that dictate its suitability for specific applications. When you’re knee-deep in selecting materials, consider factors like mechanical stress tolerance and environmental conditions to ensure everything performs optimally. It’s like finding the right piece in a jigsaw puzzle—when it fits, everything just clicks.
Polyamide has higher mechanical strength than polycarbonate.True
Polyamide is noted for its high mechanical strength, surpassing polycarbonate.
Polysulfone is less resistant to chemicals than polycarbonate.False
Polysulfone has high chemical resistance, while polycarbonate has low resistance.
How are engineering plastics used in real-world applications?
Ever wondered how the plastic in your gadgets or car parts holds up so well? Let me take you on a journey through the world of engineering plastics and their magic in everyday life.
Engineering plastics, valued for strength and durability, are vital in automotive, electronics, and machinery, enabling the creation of lightweight, wear-resistant components crucial for modern designs.
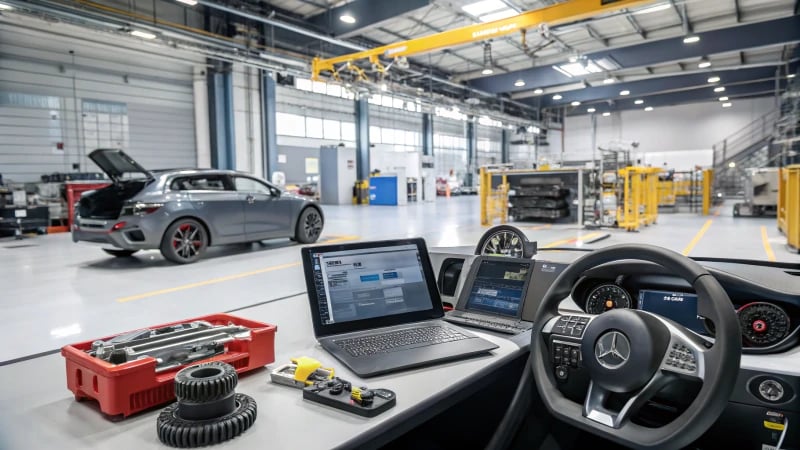
Automotive Innovations
Imagine popping the hood of your car and seeing all those intricate parts working in harmony. Engineering plastics like polyamide (nylon)9 make this possible by being the unsung heroes of engine parts and seat adjustments. I remember the first time I realized that these materials don’t just make cars lighter; they make them safer and more efficient. Their excellent mechanical properties and wear resistance mean fewer trips to the mechanic and more road trips with peace of mind.
Application | Benefits |
---|---|
Engine Components | High tensile strength and heat resistance |
Seat Adjustment Parts | Durability and precise fit |
Nylon’s self-lubricating properties are like a secret weapon against friction, ensuring that everything runs smoothly for longer.
Consumer Electronics Revolution
In our digital age, the gadgets we can’t live without are made possible thanks to materials like polycarbonate (PC)10. Its high transparency and impact resistance are key in creating sleek and durable computer monitors and phone covers. There was this one time when I dropped my phone, and it bounced rather than shattered—thanks to PC’s resilience!
- Optical Applications:
- Used in lenses and mirrors due to its favorable refractive index and optical clarity.
Machinery and Equipment Applications
When you’re designing a machine, precision is everything. Polyoxymethylene (POM)11, with its stiffness and low friction, is a go-to for precision gears and pulleys. I’ve always admired how POM keeps everything running like clockwork, even under pressure.
- Transmission Parts:
- Nylon gears benefit from its toughness, ensuring they endure wear while maintaining precision.
The dimensional stability of engineering plastics, such as polyphenylene ether (PPO)12, is vital for high-precision equipment. This stability ensures that even when environmental conditions change, performance doesn’t falter. It’s like having a best friend who’s always reliable no matter what.
The versatility of these plastics extends to injection molding, where high molding accuracy and design flexibility enable complex shapes that enhance product diversity. This adaptability is why industries continue to innovate, pushing the boundaries of design and functionality.
By leveraging these materials, industries achieve unprecedented innovation and efficiency. Whether in an automotive setting or within a high-tech gadget, engineering plastics continue to redefine what’s possible today. Every time I see a new product that seems impossible to manufacture, I’m reminded of how engineering plastics make it all possible.
These insights illustrate just a fraction of the potential applications of engineering plastics in modern industries. Each application highlights the unique properties that make these materials indispensable across sectors, reinforcing their role in technological advancements.
For more insights into specific material applications, explore relevant resources13. These resources offer a deeper understanding of how engineering plastics contribute to current technological advancements.
Nylon is used in automotive seat adjustment parts.True
Nylon's durability and precise fit make it ideal for seat adjustments.
Polycarbonate lacks impact resistance in electronics.False
Polycarbonate is known for its high impact resistance, ideal for electronics.
Conclusion
Engineering plastics are high-performance materials used in injection molding, offering mechanical strength, thermal stability, and chemical resistance for precise, durable industrial components across various applications.
-
Explore how engineering plastics are utilized across different industries and the benefits they bring to manufacturing. ↩
-
Learn how polyamide gears enhance durability and performance in mechanical systems. ↩
-
Discover real-world examples of how engineering plastics are used in various industries. ↩
-
Learn about the specific mechanical advantages of polyamide (nylon) in manufacturing applications. ↩
-
Discover why PC-ABS alloys are preferred for precision molding in electronics. ↩
-
Explore innovative manufacturing methods using engineering plastics to improve product quality. ↩
-
Discover how PC-ABS alloys enhance precision and performance in electronic equipment shells through injection molding. ↩
-
Learn about nylon’s self-lubricating properties that make it ideal for reducing wear in transmission parts. ↩
-
Explore how nylon’s mechanical properties make it ideal for automotive parts. ↩
-
Discover why polycarbonate is preferred for electronics casings. ↩
-
Learn how POM’s low friction benefits machinery components. ↩
-
Understand PPO’s role in maintaining precision in equipment. ↩
-
Gain insights into cutting-edge uses of engineering plastics. ↩