Finding ways to cut costs without compromising quality in injection molding is a delicate balancing act. But it’s entirely doable with the right strategies.
To reduce injection molding costs, optimize mold design, choose cost-effective materials, and refine production processes for improved efficiency and reduced expenses.
Thinking back to when I first started in this industry, I remember the endless possibilities mold design presented. Choosing the right number of cavities was like playing a strategic game; it could make or break our cost efficiency. I’ve learned that simplifying mold structures by cutting unnecessary components not only saves money but also streamlines maintenance. I often found myself amazed at how reusing standard parts like ejector pins could reduce costs over time.
Then there’s material selection—a pivotal lesson in balancing performance with affordability. By picking general-purpose plastics over pricier engineering ones, when possible, I’ve slashed costs while still meeting product requirements. Building strong supplier relationships has also been a game-changer, allowing for better pricing and flexible terms. Plus, who knew recycling waste could be so rewarding? It felt like a win-win when we could reintegrate scrap back into production.
And let’s not forget process control—fine-tuning parameters like temperature and pressure to perfection means fewer defective products and less waste. It’s about squeezing every bit of efficiency out of the process. Automating parts of production with robots was another step forward; watching them work tirelessly to boost output while cutting down labor costs was like witnessing the future unfold.
For anyone diving deep into injection molding, these strategies aren’t just theoretical—they’re tested and true methods that have worked wonders in my own journey. They might just be the key to unlocking significant savings in your operations too.
Optimizing mold design reduces injection molding costs.True
Efficient mold design minimizes material usage and cycle time, reducing costs.
Using premium materials always reduces injection molding costs.False
Premium materials often increase costs, contrary to cost-reduction goals.
How Can Mold Design Optimize Cost Efficiency?
Ever wondered how a simple tweak in mold design could save you big bucks?
Mold design enhances cost efficiency through strategic cavity selection, simplifying structures, and using interchangeable parts, leading to reduced material waste and controlled production costs while maintaining quality.
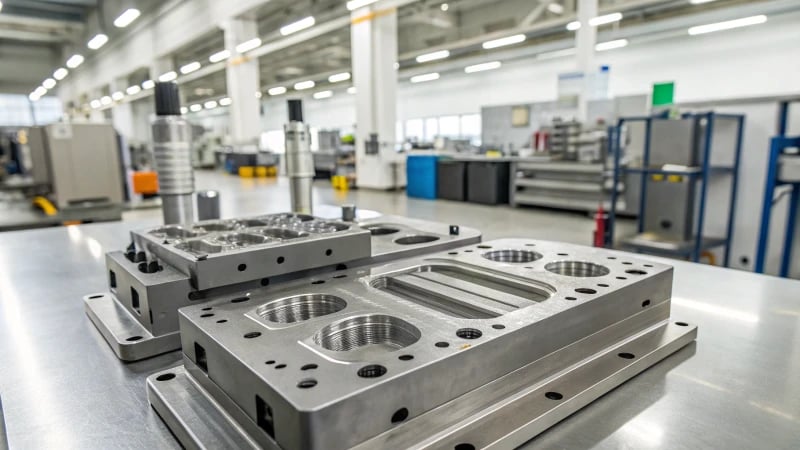
Selection of Mold Cavities
You know, when I first got into mold design, I underestimated the importance of picking the right number of cavities. It’s kind of like choosing between a single scoop or a double at an ice cream parlor, but with much bigger stakes! For instance, using a multi-cavity mold for mass-producing small items like bottle caps can lower costs by reducing injection cycles and improving output1. But for more specialized items, a single-cavity mold might just do the trick.
Streamlining Mold Structures
Streamlining mold structures is another fascinating aspect. I recall once simplifying a mold’s design by cutting out unnecessary parts, and it was like decluttering a room—suddenly everything was more efficient and easier to manage. By optimizing the gate and runner system, I managed to minimize material waste, which felt as satisfying as finally figuring out a complex puzzle.
Aspect | Optimization Strategy |
---|---|
Cavity Selection | Multi-cavity for mass production |
Structure | Simplify design; optimize gate and runner systems |
Improving Versatility and Interchangeability
Speaking of versatility, have you ever had to switch parts on a machine quickly? Standardizing components like ejector pins means you can swap parts faster than you can say "replacement." This not only saves time but also slashes costs, much like finding a universal remote for all your gadgets. Enhancing mold versatility allows for part interchangeability of standardized parts2, reducing costs associated with maintenance.
Raw Material Selection and Management
Choosing the right materials is like selecting ingredients for a recipe—it can make or break your dish. Opting for general-purpose plastics over engineering ones can be more economical if strength isn’t critical. Plus, negotiating with suppliers for better deals is like haggling at a market; it can lead to significant savings without compromising on quality.
Injection Molding Process Control
Mastering the injection molding process feels like getting the hang of using a new gadget. By fine-tuning parameters such as temperature and pressure, I’ve improved first-pass yields and cut down on defects. It’s incredibly rewarding to see the positive impact on production efficiency.
Implementing rapid mold change techniques enhances machine utilization, thereby boosting production efficiency.
Quality Control and Cost Accounting
Finally, rigorous quality control is essential—kind of like proofreading an important document to avoid embarrassing mistakes. Keeping close tabs on costs throughout production helps identify high-cost areas that need tweaking aids in identifying3, ensuring everything runs smoothly and profitably.
These strategies have truly revolutionized how I view mold design, making it a cornerstone for cost efficiency in manufacturing.
Multi-cavity molds reduce production costs.True
Multi-cavity molds increase output by reducing injection cycles, lowering costs.
Standardizing mold components increases maintenance costs.False
Standardization reduces maintenance costs by allowing quick, cost-effective replacements.
How Does Choosing Raw Materials Affect Manufacturing Costs?
Ever wondered how the simple choice of materials can save big bucks in manufacturing?
Choosing the right raw materials is crucial for reducing manufacturing costs, enhancing efficiency, and maintaining product quality. Cost-effective and suitable materials lead to savings without compromising performance.
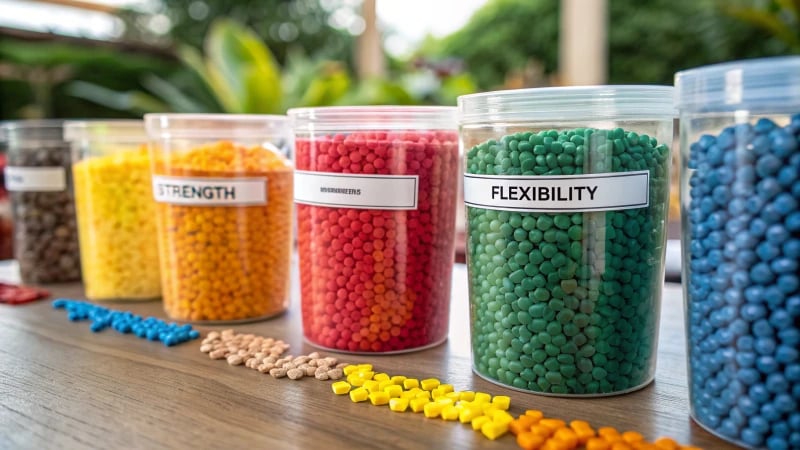
The Impact of Material Costs on Manufacturing
When selecting raw materials, cost-effectiveness is paramount. I remember the time I was working on a project to design plastic bottle caps, and I had to decide between using general-purpose plastics like PP or more expensive engineering plastics. It was like trying to decide between a budget-friendly meal at home or splurging at a fancy restaurant. I chose the former and realized that these materials were not only cheaper but perfectly suited for the job, helping me keep costs down without compromising quality. It’s all about understanding where you can afford to economize while still meeting the product’s performance needs.
Material Type | Application Example | Cost Consideration |
---|---|---|
General-purpose | Plastic bottle caps | Lower cost |
Engineering plastics | High-performance parts | Higher cost |
Optimizing Material Procurement
I’ve learned that building strong relationships with suppliers is key. It’s like having a good friend who always gives you a discount because they value your loyalty. By negotiating long-term contracts, I’ve secured better prices and terms. Bulk purchasing also lowers costs per unit, though it’s crucial to manage inventory wisely to avoid wastage. Who wants to deal with expired materials cluttering up the workspace?
- Bulk Purchasing: Reduces price per unit.
- Long-term Contracts: Secures favorable terms.
- Inventory Control: Prevents backlogs and expiry.
Inventory management4 is essential in this process.
Recycling and Waste Management
One of my proudest achievements was setting up a recycling system for marginal waste during production. By reprocessing these materials, not only did I reduce consumption but also aligned our operations with sustainable practices. It’s like giving a second life to something that would otherwise be discarded, contributing to both cost efficiency and environmental responsibility.
- Crushing and Reprocessing: Converts waste back into usable material.
- Quality Assurance: Ensures recycled materials maintain product standards.
This approach enhances cost efficiency5.
Influence on Injection Molding
Material choice significantly impacts injection molding efficiency. I once faced challenges with defect rates, but by choosing easy-to-mold materials and fine-tuning the injection parameters like temperature and pressure, I improved our qualification rate dramatically. It was like tuning a musical instrument until it played just right. Plus, simplifying mold designs by minimizing complexity reduced maintenance costs significantly.
- Temperature Control: Ensures optimal melt flow.
- Pressure Regulation: Prevents defects and scrap.
Precision in process parameters is essential for optimal production outcomes6.
By choosing versatile components for molds, I ensured they were easier to maintain and replace, much like having universal tools in your toolbox that fit multiple uses. This approach not only cut down costs but also kept production lines running efficiently through cost-effective maintenance7.
General-purpose plastics are more cost-effective than engineering plastics.True
General-purpose plastics like PP and PE are cheaper, suitable for non-strength applications.
Bulk purchasing always leads to cost savings in manufacturing.False
While bulk purchasing lowers unit costs, it requires effective inventory management to avoid waste.
How can process control enhance production efficiency?
Imagine cutting down production waste and boosting quality with just a few strategic tweaks. Sounds like magic, right?
Process control improves production efficiency by optimizing mold design, managing raw materials, and refining injection molding. This minimizes waste, enhances product quality, and maintains consistency, ultimately increasing productivity.
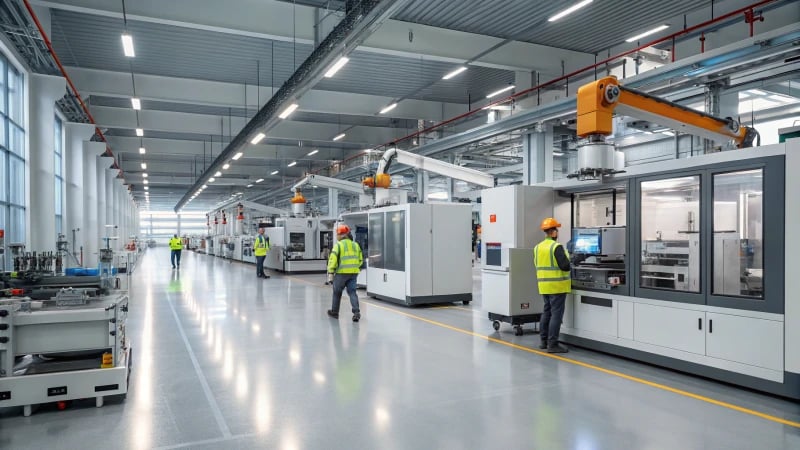
The Role of Mold Design in Process Control
Incorporating efficient process control begins with mold design. A reasonable selection8 of mold cavities can drastically impact cost and production time. Multi-cavity molds are ideal for mass-producing small items like plastic bottle caps, reducing both mold and cycle costs per product.
I remember the first time I simplified a mold structure; it was like removing unnecessary gears from a clock. By minimizing complex parts, such as avoiding intricate slanting tops, I not only saved on manufacturing costs but also on maintenance. A focus on the gate and runner system enhances efficiency by optimizing how plastic melt fills the cavity, thereby reducing material waste.
Optimizing Raw Material Management
Choosing suitable plastic materials aligned with product performance needs is crucial. Using general-purpose plastics such as PP or PE instead of more expensive engineering plastics can lower costs while meeting functionality requirements.
Building long-term relationships with suppliers was another turning point for me. It helped us secure better prices and terms, making bulk purchasing feasible without the risk of material backlog. Plus, recycling marginal waste became a norm in our operations, allowing us to reintroduce materials into the production line and further conserve resources.
Injection Molding Process Management
Precision is everything when it comes to injection molding parameters like temperature, pressure, and speed. Proper injection temperatures enhance plastic flow, reducing defects and scrap rates. The first time I nailed the perfect injection temperature, the reduction in defects was astounding.
Efficiency took another leap with better production scheduling9. Implementing rapid mold change technology (SMED) significantly reduced machine idle times. Automation—including robotic handling and packaging—further boosts efficiency while reducing labor costs.
Establishing a robust quality control system also became a priority. Catching product issues early on meant less waste and more accurate cost accounting across all areas—from mold costs to energy expenditures.
Here’s a snapshot of the cost benefits achieved through these optimizations:
Optimization | Cost Benefit |
---|---|
Multi-cavity molds | Reduced cycle costs |
General-purpose plastics | Lower material costs |
Rapid mold change | Increased machine uptime |
Reflecting on these strategies, it’s clear that embracing process control isn’t just about keeping up—it’s about staying ahead in the game.
Multi-cavity molds reduce production cycle costs.True
Multi-cavity molds enable simultaneous production of multiple items, lowering costs.
Using engineering plastics always reduces production costs.False
Engineering plastics are often more expensive than general-purpose plastics.
How Can We Improve Quality and Reduce Scrap in Manufacturing?
Ever felt the frustration of watching precious resources turn into scrap during production? It’s a pain I know all too well.
Improving quality and reducing scrap in manufacturing involves optimizing mold design, selecting suitable materials, and refining injection molding processes, enhancing efficiency while ensuring high-quality results with minimal waste.
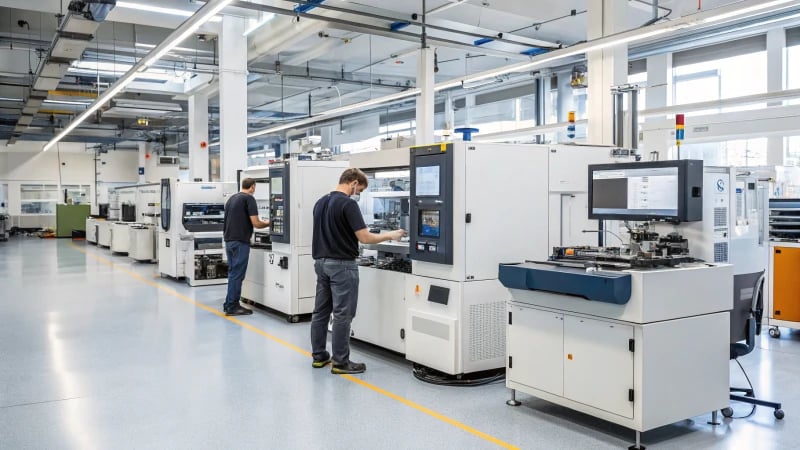
Optimizing Mold Design
I remember when I first delved into mold design, it was like cracking open a complex puzzle. Choosing the right number of mold cavities was my initial challenge. Imagine being able to produce a multitude of plastic bottle caps in one go—multi-cavity molds make this possible, saving both time and money. The thrill of finding cost-effective solutions in mold design is unmatched.
Moreover, simplifying mold structures brought its own set of revelations. I found that reducing unnecessary parts not only cut costs but also made maintenance a breeze. Designing efficient demolding mechanisms without over-complex components became my go-to strategy.
Then there was the game-changing realization about versatility and interchangeability. Standard-size components meant fewer headaches when it came to maintenance, allowing for quick replacements that were cost-efficient.
Material Selection and Management
I’ll never forget the moment I realized the impact of choosing the right materials. Opting for general-purpose plastics like PP or PE for products with moderate performance needs helped me cut costs without sacrificing quality. It’s amazing how material selection can make or break the production process.
Working closely with suppliers to optimize procurement strategies turned out to be another essential move. Establishing strong relationships not only got me better prices but also ensured that inventory management was on point—no more wastage due to expired materials.
Recycling marginal waste was an eye-opener for me, too. Seeing unqualified products get a second chance through reprocessing was both economically and environmentally satisfying.
Injection Molding Process Control
Getting injection molding parameters just right was like mastering an art form. Controlling temperature, pressure, and speed improved our one-time molding qualification rates dramatically. It was incredible to witness defects reduce as we perfected these aspects.
Boosting production efficiency became another passion of mine. Technologies like rapid mold change systems10 reduced idle times and propelled productivity forward. Watching robots handle product placement streamlined operations in ways I hadn’t imagined.
Lastly, setting up a robust quality control system was pivotal. It allowed me to detect issues early, reducing scrap and optimizing costs across all facets of production. Cost accounting became my ally in identifying high-cost areas ripe for optimization.
Technique | Benefit |
---|---|
Mold Design Optimization | Cost Reduction |
Material Selection | Enhanced Quality |
Process Control | Efficiency Boost |
These strategies are more than just techniques—they’re lifelines that drive manufacturing excellence and keep us ahead in the industry. Explore more on process improvements11 to stay competitive.
Using multi-cavity molds reduces production costs.True
Multi-cavity molds enable efficient production, lowering manufacturing costs.
General-purpose plastics compromise product quality.False
Plastics like PP or PE cut costs without compromising moderate performance needs.
Conclusion
Effective cost reduction in injection molding involves optimizing mold design, selecting affordable materials, refining production processes, and implementing robust quality control to enhance efficiency without sacrificing quality.
-
Explores how multi-cavity molds enhance production efficiency by reducing cycle times and costs. ↩
-
Highlights the cost benefits of using interchangeable parts in mold design. ↩
-
Shows how detailed cost tracking helps identify areas for financial optimization. ↩
-
Learn how effective inventory management can prevent material wastage and financial loss. ↩
-
Explore how recycling practices improve cost efficiency and sustainability in manufacturing. ↩
-
Understand why precise process parameters are crucial for quality production outcomes. ↩
-
Find out how versatile mold components contribute to reduced maintenance costs. ↩
-
Learn how choosing the right number of mold cavities can optimize production costs and efficiency. ↩
-
Explore effective scheduling methods to minimize equipment idle times and enhance production efficiency. ↩
-
Understand how these systems can enhance efficiency by minimizing downtime. ↩
-
Discover comprehensive strategies for optimizing manufacturing processes to improve efficiency and reduce waste. ↩