Tackling the challenge of injection molding high-temperature parts can feel daunting, but focusing on key design elements can make all the difference.
Successful injection molding of high-temperature parts requires selecting heat-resistant materials, designing for thermal expansion management, and implementing efficient heat dissipation to maintain integrity and functionality.
Once you’ve got a handle on the basics, delving into specific design strategies can really elevate your results. Picture this: I’m in my workshop, experimenting with different materials and designs. Through trial and error, I’ve learned that choosing the right material, like PPS or PEEK, isn’t just about heat tolerance—it’s about matching the coefficient of thermal expansion with any metal components to prevent stress and damage. Let’s explore how these insights and more can help you craft high-quality high-temperature parts.
Material selection is crucial for high-temperature parts.True
Choosing materials that withstand high temperatures ensures part durability.
Heat dissipation is irrelevant in injection molding.False
Effective heat dissipation prevents part deformation and maintains integrity.
- 1. How Do Material Properties Influence High-Temperature Injection Molding?
- 2. How Can I Design Durable High-Temperature Parts?
- 3. Why Is Heat Dissipation Crucial in High-Temperature Injection Molding?
- 4. How does mold design impact high-temperature applications?
- 5. What are the key strategies to overcome high-temperature injection molding challenges?
- 6. Conclusion
How Do Material Properties Influence High-Temperature Injection Molding?
Ever wondered how choosing the right material can make or break your injection molded parts in high-heat environments?
Material properties such as high-temperature tolerance, thermal stability, and mechanical strength are vital for high-temperature injection molding, ensuring components maintain durability and functionality under intense thermal stress.
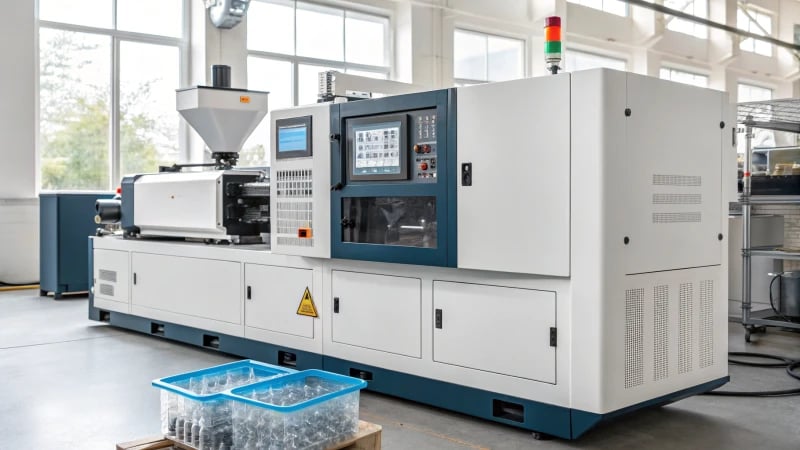
Factors Related to Material Selection
Reflecting on my journey in the mold industry, I’ve learned that selecting the right material is akin to finding the perfect pair of shoes for a marathon. It’s not just about comfort; it’s about ensuring peak performance under pressure.
High Temperature Tolerance: Selecting materials like polyphenylene sulfide (PPS) or polyetheretherketone (PEEK) is crucial for maintaining mechanical properties at elevated temperatures. For instance, during a project, I opted for PPS when dealing with components hovering around 200℃. Its ability to maintain integrity was a game-changer. On another occasion, when faced with even higher temperatures, I turned to PEEK. Its resilience above 250℃ saved the day.
Material | Maximum Temperature | Properties |
---|---|---|
PPS | 200℃ | Mechanical stability at moderate temperatures |
PEEK | 250℃+ | Suitable for extreme temperatures |
Thermal Stability: Materials like polyimide (PI) are preferred due to their stable chemical structure at high temperatures, preventing decomposition and aging. I recall working with PI for its unmatched stability at high temps, preventing any premature aging of parts.
Coefficient of Thermal Expansion Matching: When combining high-temperature components with others, matching the thermal expansion coefficients is critical to prevent stress and connection issues. Imagine piecing together a puzzle where each part expands differently; chaos would ensue! By matching these coefficients, especially when integrating metal inserts, I avoided unnecessary stress and potential failures. For example, designing injection molded parts1 with metal inserts requires selecting plastics with similar thermal expansion rates.
High-Temperature Mechanical Properties
When crafting components like engine surrounds, the Strength and Stiffness at elevated temperatures become non-negotiable. Liquid crystal polymers (LCPs) often come to my rescue here, ensuring parts withstand operational stresses without faltering.
Toughness and Fatigue Resistance: In automotive applications, materials must withstand thermal cycles and dynamic loads. A wise choice of materials can dramatically minimize premature failures in components like turbocharger system parts, ensuring longevity and reliability.
Structural Design Considerations
The design of these structures is where art meets science.
Wall Thickness Design: Maintaining uniformity prevents thermal stress. During one project, I meticulously kept thicknesses between 1.5 and 5 mm, allowing for optimal heat conduction and minimizing deformation risks.
Reinforcement Rib Design: To enhance strength without excess weight, ribs should not exceed 60% of the wall thickness. Incorporating reinforcement rib design is like adding a backbone to these parts—bolstering strength without unnecessary weight. Moderate rib heights and appropriate demoulding slopes enhance efficiency.
Connection Structure Design: High-temperature connections require careful consideration of thermal expansion effects. By using metal inserts or special methods2, I’ve improved connection reliability in many designs.
These factors underline the essence of material selection tailored for high-temperature conditions to ensure that injection molded parts are not only reliable but also built to last.
PPS is suitable for temperatures above 250℃.False
PPS is ideal for temperatures up to 200℃, not above 250℃.
Uniform wall thickness reduces thermal stress.True
Consistent wall thickness minimizes deformation and stress from heat.
How Can I Design Durable High-Temperature Parts?
Imagine a world where your designs not only survive but thrive in scorching conditions. That’s the challenge and thrill of crafting high-temperature components.
To design durable high-temperature parts, choose heat-tolerant materials, ensure uniform wall thickness, enable efficient heat dissipation, and optimize mold design for enhanced durability and performance.
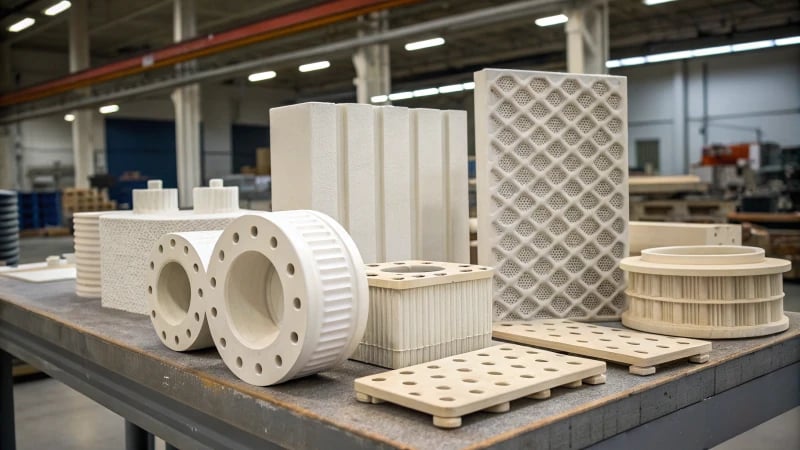
Material Selection Considerations
Let me take you back to a project where I had to design parts that could withstand intense heat. It was like choosing a partner for a long-term relationship; the material needed to be just right. I gravitated towards polyphenylene sulfide (PPS) and polyetheretherketone (PEEK) because of their high temperature tolerance3. These materials don’t just melt under pressure—literally.
Material | Max Temperature (℃) | Key Properties |
---|---|---|
PPS | 200 | Mechanical stability |
PEEK | 250+ | Extreme heat resistance |
I learned the hard way that matching the coefficient of thermal expansion is crucial to avoid stress or loosening during temperature swings. Once, I used a plastic with a wildly different expansion rate than the metal it was paired with—it wasn’t pretty. Now, I ensure the plastic’s expansion is as close to the metal’s as possible.
Structural Design Strategies
Wall Thickness and Reinforcement
I recall a mentor once telling me, "Uniformity is your best friend," and it stuck with me. Uniform wall thickness minimizes thermal stress, preventing those annoying cracks and deformations. If you absolutely must vary the thickness, think gentle transitions—like arcs or bevels—to keep stress at bay.
Reinforcement ribs have saved me more times than I can count. They boost strength without packing on the pounds, but keep rib thickness under 60% of the main wall thickness.
Undercuts and Connections
Designing undercuts was like solving a puzzle. I had to consider the material’s elasticity and shrinkage at high temperatures to ensure reliability. Metal inserts or specialized connectors became my go-to for stabilizing joints that might falter in the heat.
Heat Dissipation Techniques
The art of heat dissipation is fascinating. For me, using natural convection like heat fins feels like harnessing a superpower. However, when more muscle is needed, forced convection via fans or heat sinks gets the job done.
Method | Application Example |
---|---|
Natural Convection | High-temperature electronic housings |
Forced Convection | Automotive engine intake manifolds |
Mold Design Considerations
Every time I design a mold, it feels like I’m crafting a masterpiece. The placement of gates can make or break material flow during injection molding. Proper gate positioning prevents defects such as weld marks and trapped air, crucial for the final product4.
Cooling systems are like the unsung heroes of mold design. They need to be efficient to maintain production pace and part quality. Strategic channels and effective cooling media are key to shortening cooling times while keeping part quality intact.
By considering these strategies, I’ve consistently enhanced the durability and functionality of parts in high-temperature applications. It’s all about finding that perfect balance between strength, stability, and efficiency.
PPS can withstand temperatures up to 200℃.True
PPS maintains mechanical stability at temperatures up to 200℃.
Rib thickness should exceed main wall thickness for strength.False
Rib thickness should not exceed 60% of the main wall thickness.
Why Is Heat Dissipation Crucial in High-Temperature Injection Molding?
Ever wondered why some things just can’t take the heat while others thrive? In high-temperature injection molding, it’s all about managing that intense heat to perfection.
Efficient heat dissipation in high-temperature injection molding prevents defects, enhances component strength, and extends the lifespan of parts. It relies on effective cooling systems and proper material selection for optimal results.
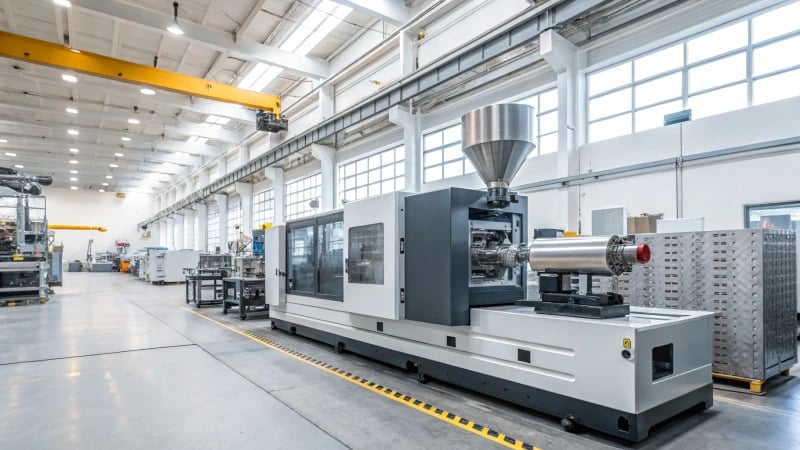
Understanding Heat Dissipation in Injection Molding
I’ve always been fascinated by how things are made, especially with injection molding. Picture this: you’ve got molten plastic at sky-high temperatures being forced into a mold. Now, if this plastic doesn’t cool down evenly, you’re looking at some serious issues like warping or sinking, which nobody wants.
Factors Related to Material Selection
When I first started diving into material selection, it felt like choosing a favorite ice cream flavor—so many options, but each with its own perks. Materials like polyphenylene sulfide (PPS) and polyetheretherketone (PEEK) are like the superhero duo of high-temp molding. They stand strong under heat, ensuring components are not just tough but also long-lasting. It’s crucial to match thermal expansion coefficients when you’re pairing these materials with others; otherwise, you might end up with loose or cracked parts due to thermal cycling.
Material | Temperature Range | Key Properties |
---|---|---|
PPS | 180-200℃ | High strength |
PEEK | Above 250℃ | Extreme heat resistance |
Key Points of Structural Design
Ah, the art of design—where uniform wall thickness is king! I remember the first time I learned about using reinforcement ribs; it was a game-changer. They boost rigidity without weighing things down, keeping everything stable under stress. And for those tricky undercuts or connections, choosing materials with the right elasticity is essential to maintain reliable connections even when things heat up.
Heat Dissipation Design Considerations
Selecting the right heat dissipation method can feel like solving a puzzle. Natural convection is great for some scenarios, while others might need forced methods. Think of it like choosing between a gentle breeze or a full-blown fan.
Method | Application | Benefits |
---|---|---|
Natural | High-temp electronic equipment | Simple, cost-effective |
Forced | Components with high dissipation needs | Efficient heat removal |
Mold Design Related Factors
The mold’s cooling system plays a crucial role here. It needs to be designed to handle the heat efficiently, which in turn reduces cycle times and boosts production efficiency. Using multi-point gates can significantly improve melt flow and prevent defects like weld marks.
By understanding these factors, I’ve learned that designing components that meet both functional and aesthetic needs in demanding environments is entirely possible. Properly designed molds and materials ensure that injection molded parts perform reliably over time, even in tough conditions like those found in the automotive and aerospace industries.
Learn more about optimizing mold design5 by considering factors such as gate size and cooling channel configuration for improved efficiency.
Heat dissipation prevents warping in injection molded parts.True
Uniform cooling is essential to maintain structural integrity and prevent warping.
PPS is unsuitable for high-temperature injection molding.False
PPS is preferred for its high strength and temperature tolerance.
How does mold design impact high-temperature applications?
Ever wondered how the secret to handling high temperatures lies in the tiny details of mold design?
Mold design is vital for high-temperature applications, affecting material selection, structural stability, and cooling. Proper design prevents defects, ensures durability, and enhances production efficiency.
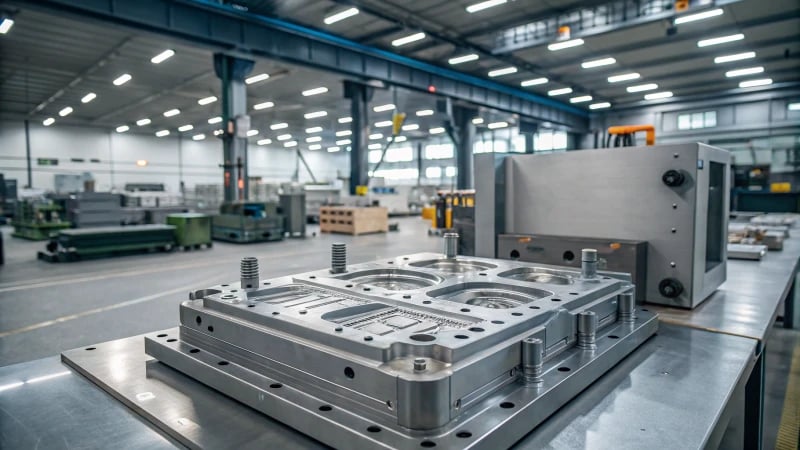
Material Selection Considerations
Choosing the right material for high-temperature applications feels like picking the perfect outfit for a scorching day—comfort and durability are key. Polyphenylene Sulfide (PPS) works wonders at 180-200℃, just like your trusty summer tee, while Polyetheretherketone (PEEK) steps up when things heat above 250℃, much like switching to breathable linen. These materials keep their cool under heat stress, vital for maintaining performance in temperature-sensitive scenarios.
Material | Temperature Range | Key Properties |
---|---|---|
PPS | 180-200℃ | High mechanical stability |
PEEK | Above 250℃ | Extreme heat resistance |
Structural Design for Stability
In my early days as a designer, I learned that uniform wall thickness is crucial. It’s like building a sandcastle; uneven walls can crumble under pressure. Ideally, thickness should range from 1.5 to 5 mm, with smooth transitions to minimize stress, ensuring everything stands strong under the heat.
Cooling System Design
Efficient cooling systems are like the air conditioning of mold design. Back in my first project, we used water to cool things down evenly—this reduced cycle times and made production smoother than a summer breeze. Consider cooling system improvements6 to manage heat effectively.
Gate Design and Placement
Imagine pouring syrup; it needs the right flow. Gate design is similar. Correct placement ensures smooth filling, minimizing defects like weld marks. Multi-point or latent gates enhance melt flow, crucial for intricate shapes.
Importance of Thermal Expansion Matching
Once, I worked on a project where mismatched materials led to stress cracks—it was a costly lesson. Matching thermal expansion coefficients reduces these risks, especially with metal inserts. Explore more about thermal expansion issues7 and learn how to manage them effectively.
Heat Dissipation Strategies
Selecting suitable heat dissipation methods is like choosing between a fan or a breeze on a hot day. Options include natural convection or forced methods like fans or heat sinks. Designing effective channels is key for maintaining temperature balance without compromising integrity or escalating costs. For comprehensive guidance on heat dissipation design8, explore advanced strategies to optimize your molds for high-temperature conditions.
PPS can handle temperatures above 250℃.False
Polyphenylene Sulfide (PPS) is suitable for temperatures around 180-200℃.
Uniform wall thickness reduces thermal stress.True
Even wall thickness prevents deformation by reducing thermal stress in mold design.
What are the key strategies to overcome high-temperature injection molding challenges?
Navigating the fiery world of high-temperature injection molding can be daunting, but with the right strategies, it’s a path to perfection.
To overcome high-temperature injection molding challenges, focus on selecting appropriate materials, designing robust structures, optimizing heat dissipation, and creating precise molds to ensure high-quality products.
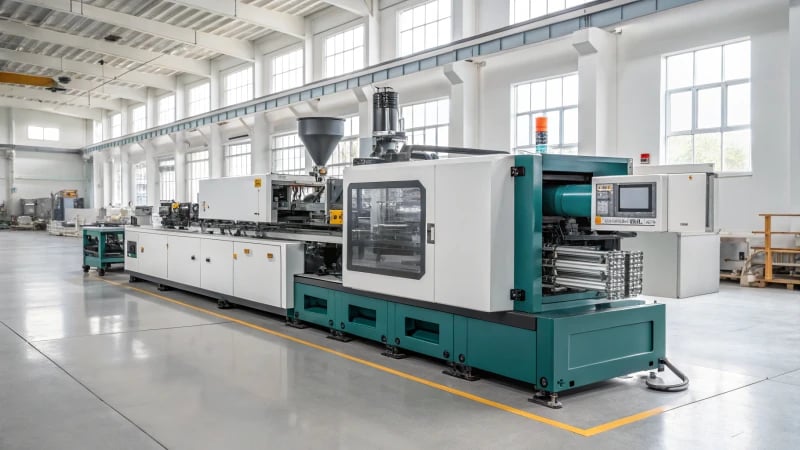
I remember my early days in the mold industry when I first encountered the complexities of high-temperature injection molding. It felt like trying to tame a dragon with a plastic sword—each step revealing new challenges. But as I learned, each obstacle was an opportunity to refine my craft.
Material Selection for High-Temperature Molding
Choosing the right material is like finding a trustworthy partner. I often think back to a project where we used polyphenylene sulfide (PPS) for components exposed to temperatures around 180-200℃. It was like building armor for our products, ensuring they remained resilient. When the heat cranked up beyond 250℃, polyetheretherketone (PEEK) became our go-to, with its ability to withstand extreme conditions akin to a superhero withstanding fire.
Table: Material Properties
Material | Max Temp (°C) | Key Feature |
---|---|---|
PPS | 200 | Mechanical Stability |
PEEK | 250+ | High Thermal Resistance |
Structural Design Considerations
When it comes to design, it’s all about balance. I once worked on a project where uneven wall thickness led to catastrophic thermal stress—it was like watching a beautiful sculpture crack under pressure. To prevent such heartbreak, I’ve learned that uniform wall thickness and clever reinforcement ribs are essential. They provide strength without unnecessary bulk, much like a well-crafted bridge.
Heat Dissipation Strategies
Efficient heat dissipation is the unsung hero in maintaining component efficiency. I recall the satisfaction of seeing a complex part work flawlessly after we implemented natural convection methods with fins—watching those fins do their job was like witnessing magic unfold. For tougher cases, forced methods like cooling pipes became our secret weapon.
Cooling Techniques Table
Technique | Description |
---|---|
Natural Convection | Uses fins to disperse heat |
Forced Convection | Involves fans for active cooling |
Mold Design Specifics
The nuances of mold design are where art meets science. I can still feel the thrill of optimizing gate designs for smooth material flow—imagine a river flowing perfectly without obstructions. Proper gate and cooling system designs are the keys to reducing cycle time and enhancing quality, ensuring that each piece emerges flawless, ready for its role in the real world.
By refining these elements, manufacturers like us can navigate the fiery challenges of high-temperature injection molding and consistently produce top-quality components. Each success in overcoming these challenges isn’t just about improving a process; it’s about crafting a legacy of excellence in our field.
PEEK can withstand temperatures over 250°C.True
PEEK is known for its high thermal resistance, tolerating over 250°C.
Natural convection uses fans for cooling.False
Natural convection disperses heat using fins, not fans.
Conclusion
Key design considerations for successful injection molding of high-temperature parts include material selection, structural integrity, heat dissipation strategies, and optimized mold design to ensure durability and performance.
-
Learn how matching thermal expansion coefficients prevents stress and connection issues in molded parts. ↩
-
Discover special methods to enhance connection stability in high-temperature environments. ↩
-
Explore materials with high-temperature resistance, understanding their specific benefits and applications in various industries. ↩
-
Discover effective gate design strategies to optimize molding processes for high-temperature materials. ↩
-
Explore this link for strategies on improving mold design efficiency in high-temperature environments. ↩
-
Learn innovative strategies to enhance cooling efficiency in mold designs, reducing cycle times and improving part quality. ↩
-
Gain insights into selecting materials with compatible thermal expansion rates to prevent stress-related damages. ↩
-
Explore advanced techniques for designing heat dissipation systems that enhance component performance and longevity. ↩