All Posts
blog & article
read our latest newsletter
Whether you’re curious about material selection, product design, mold design, mold making and injection molding, feel free to ask us anything. Our team is ready to provide the guidance and insights you need.
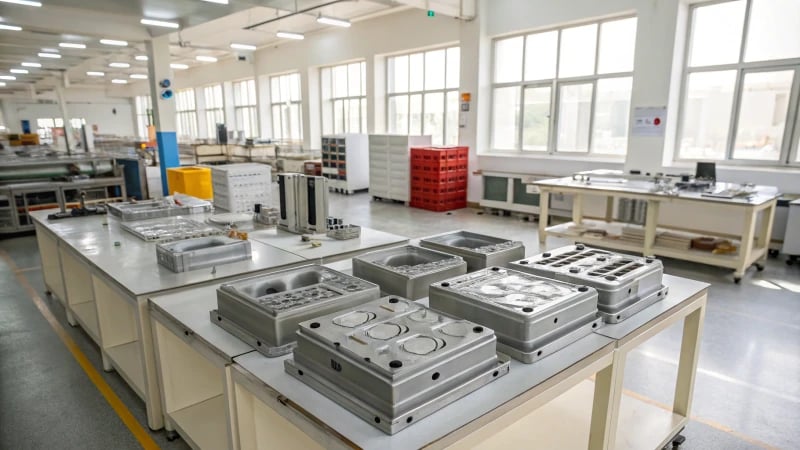
What Are the Best Strategies for Finding High-Quality Plastic Molds?
Finding high-quality plastic molds requires clear product specifications, evaluating manufacturers' strengths, reviewing design plans, understanding manufacturing processes, and ensuring reliable after-sales support for optimal outcomes.
MANUFACTURING
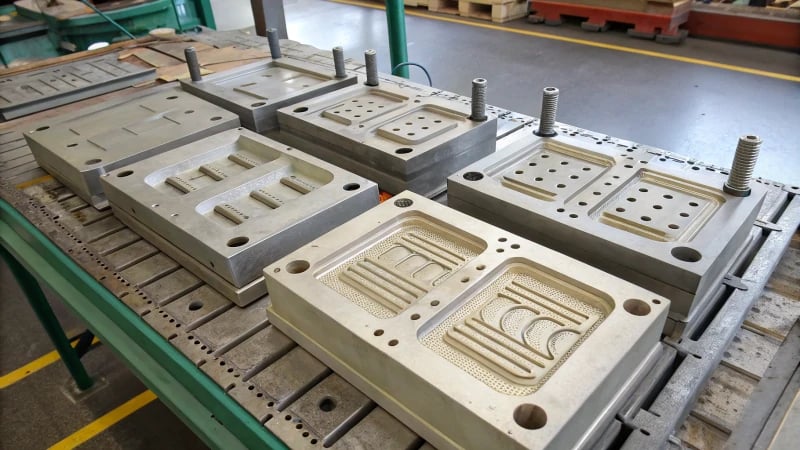
What Factors Should You Consider When Choosing a Cooling Channel Layout in Mold Design?
Choosing the right cooling channel layout in mold design is crucial for optimizing cooling efficiency, product quality, and minimizing defects. Factors like product shape, wall thickness, and precision requirements significantly influence this decision.
DESIGN
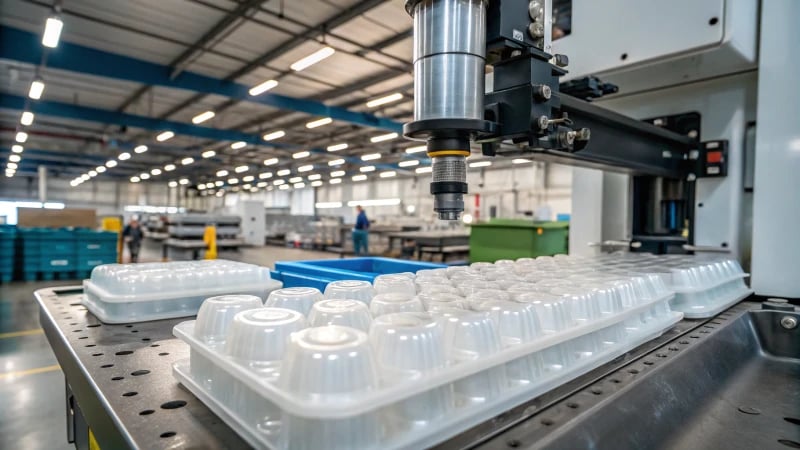
Is Acquiring a Plastic Molding Business a Smart Investment?
Investing in a plastic molding business can be lucrative due to stable demand and technological advancements, but challenges like raw material price volatility and environmental regulations must be carefully considered.
DEVELOPMENT
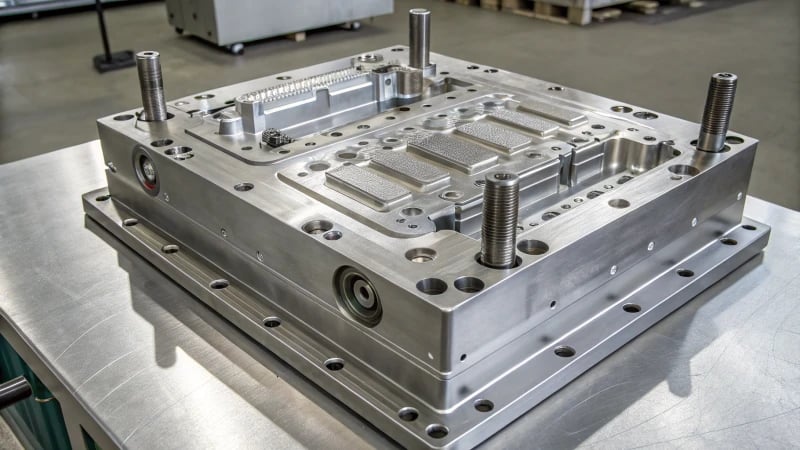
What Makes Plastic Moldable? Discover Its Key Properties!
This article explores the key properties of plastics that make them moldable, including thermoplasticity, fluidity, processability, and repeatability. It highlights their significance in manufacturing various products across industries.
Materials Recommendations
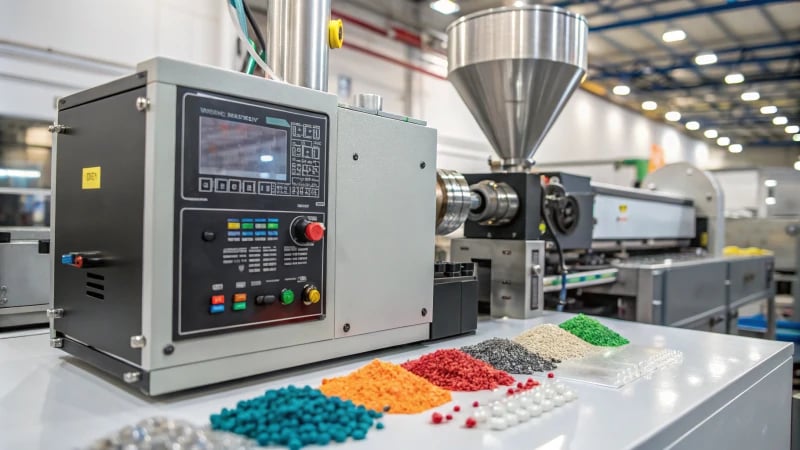
What Are the Best Methods to Determine the Adjustment Sequence of Injection Molding Process Parameters?
This guide explores the best methods for determining the adjustment sequence of injection molding process parameters, focusing on temperature, pressure, speed, and cooling time to enhance product quality and efficiency.
OPTIMIZATION
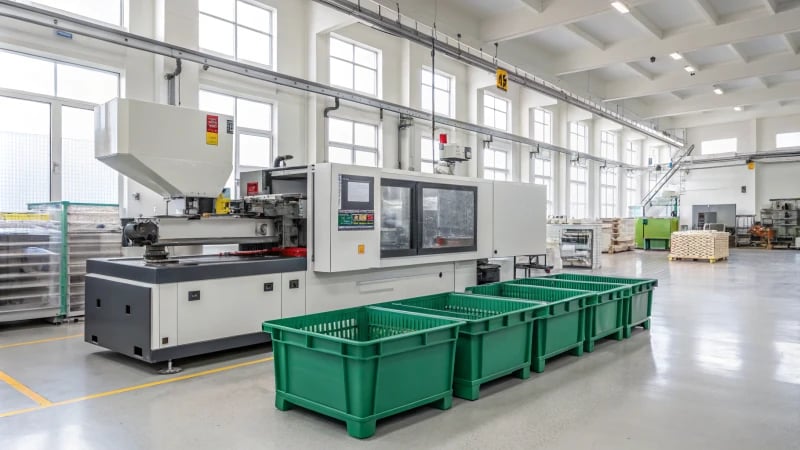
What is Plastic Injection Molding and How Does It Work?
Plastic injection molding is a vital manufacturing process that melts plastic and injects it into molds, producing precise and efficient products across various industries. This article explores its advantages, challenges, and applications.
DEVELOPMENT
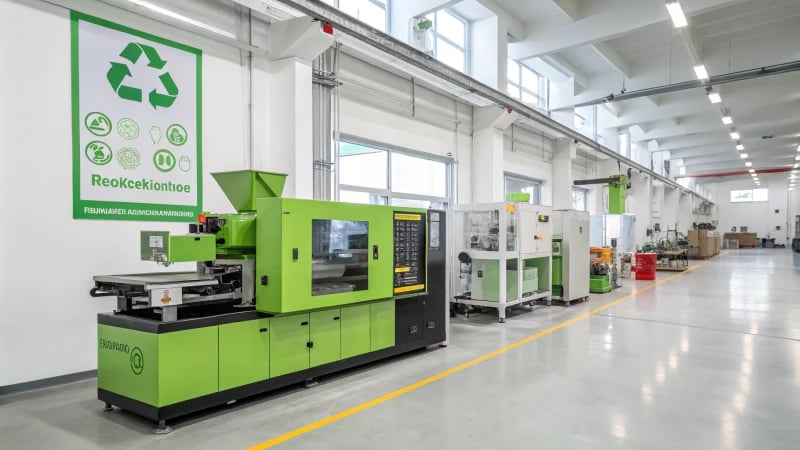
What Are the Key Advantages of Injection Molding?
Injection molding is a highly efficient manufacturing process that offers numerous advantages, including high production efficiency, design flexibility, low costs, and excellent product quality, making it ideal for large-scale production.
DEVELOPMENT
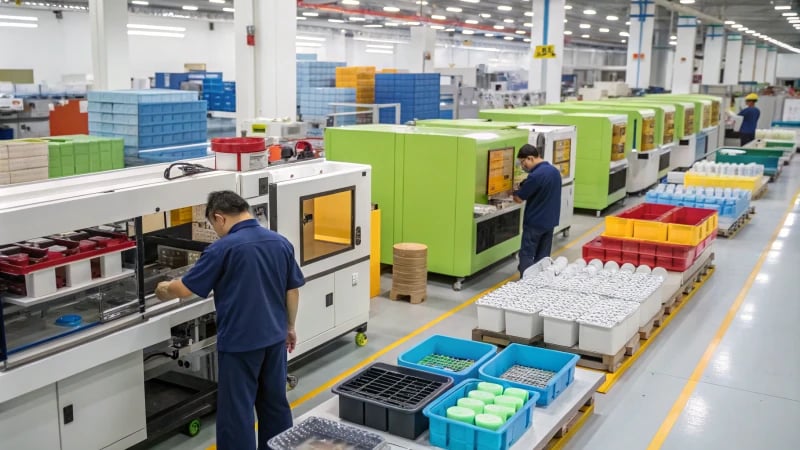
What Are Plastic Molding Services and How Can They Benefit Your Business?
Plastic molding services, including injection, extrusion, blow, and compression molding, enhance manufacturing efficiency and reduce costs. Proper mold design and material selection are crucial for product quality and operational success.
DEVELOPMENT
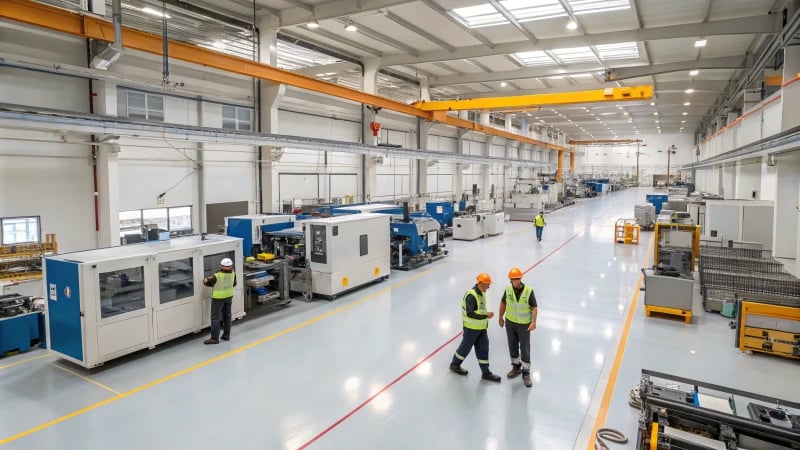
How Are Plastic Products Manufactured? Discover the Process!
This article explores the intricate process of plastic product manufacturing, detailing key stages such as design, material selection, molding techniques, post-processing, and quality control to ensure high-quality outcomes.
MANUFACTURING
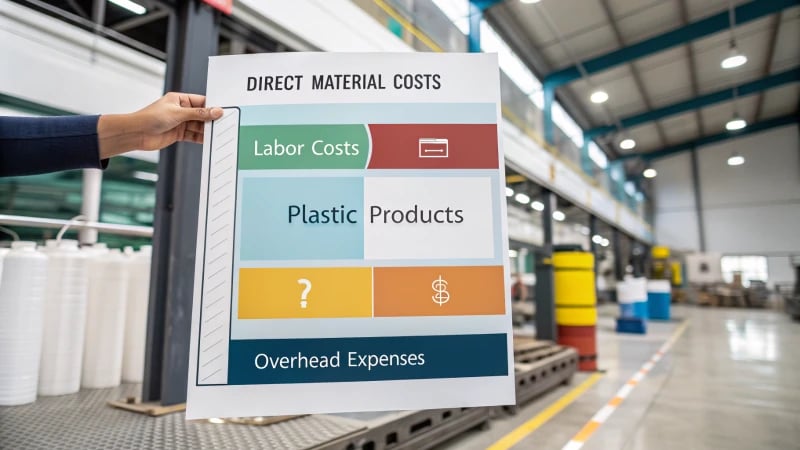
What Are the Steps to Accurately Calculate the Manufacturing Cost of a Plastic Product?
Calculating the manufacturing cost of plastic products involves understanding direct material, labor, and overhead costs. This structured approach aids in pricing strategies and informed decision-making for product designers.
Price Evaluation
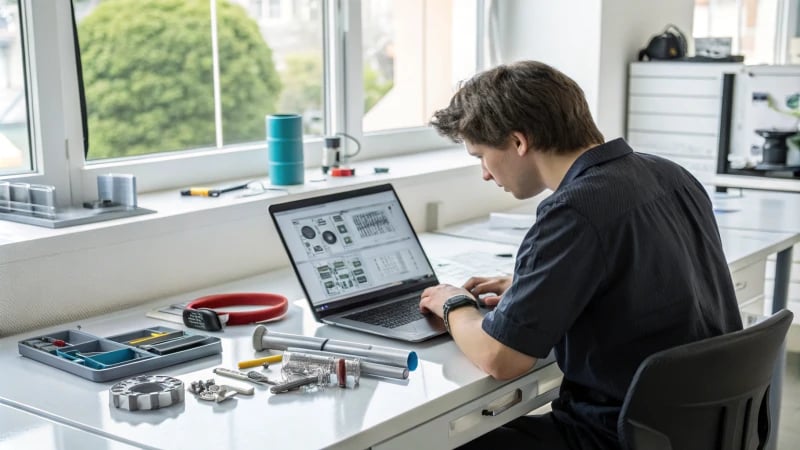
What are the Best Ways to Find Your Ideal Injection Mold Manufacturer Online?
Finding the right injection mold manufacturer online can be overwhelming. Utilize search engines, B2B platforms, industry associations, and networking to streamline your search and ensure quality partnerships.
Find Suppliers
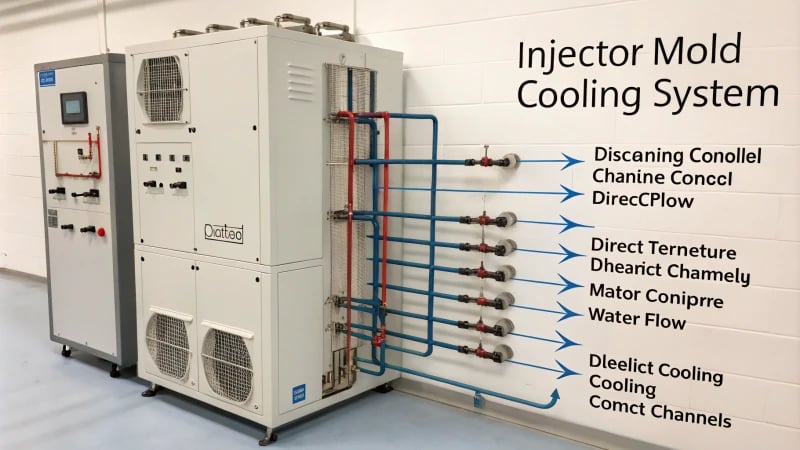
What Are the Best Strategies for Designing an Injection Mold Cooling System?
This blog post explores effective strategies for designing injection mold cooling systems, emphasizing the importance of cooling methods, layout planning, channel sizing, flow rate control, and sealing designs to enhance product quality and efficiency.
OPTIMIZATION
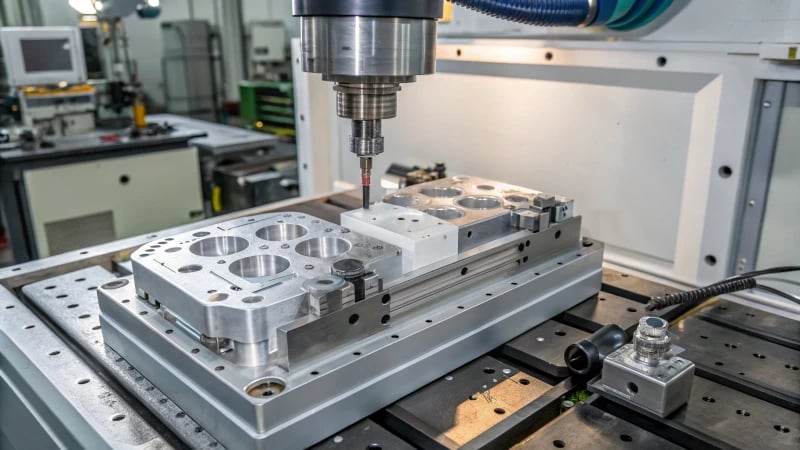
What is the Precision Level of Injection Molding?
Injection molding achieves high precision with dimensional tolerances of ±0.01 to ±0.5mm, influenced by mold design, process parameters, and material properties, crucial for industries like automotive and electronics.
DEVELOPMENT
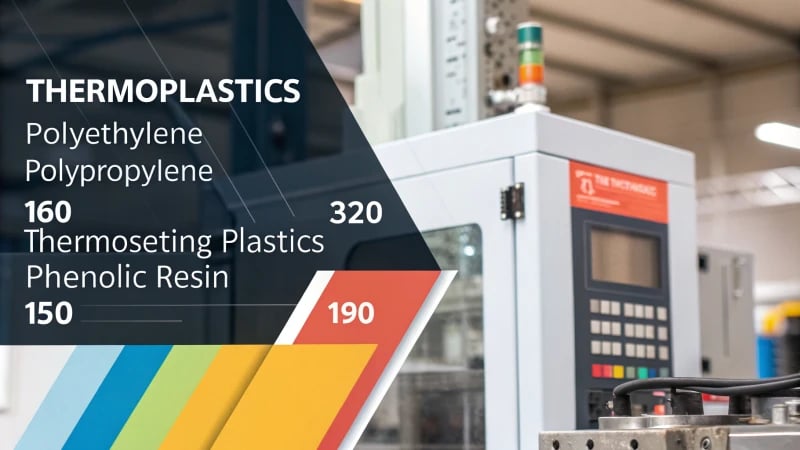
What Is the Best Temperature for Molding Plastic?
Discover the optimal temperatures for molding various plastics, including thermoplastics and thermosetting types. Learn how temperature control impacts product quality and essential practices for successful plastic molding.
OPTIMIZATION
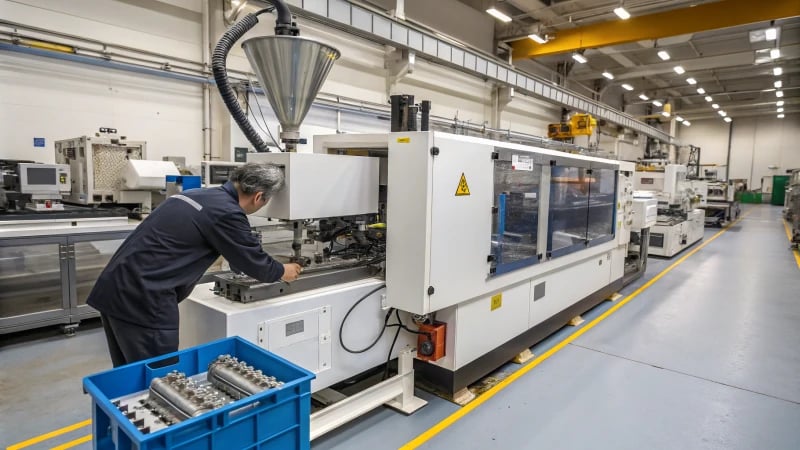
What Factors Influence the Output of an Injection Molding Machine?
The output of an injection molding machine is influenced by various factors including performance parameters, mold design, and raw material characteristics. Optimizing these elements enhances production efficiency and product quality.
DEVELOPMENT
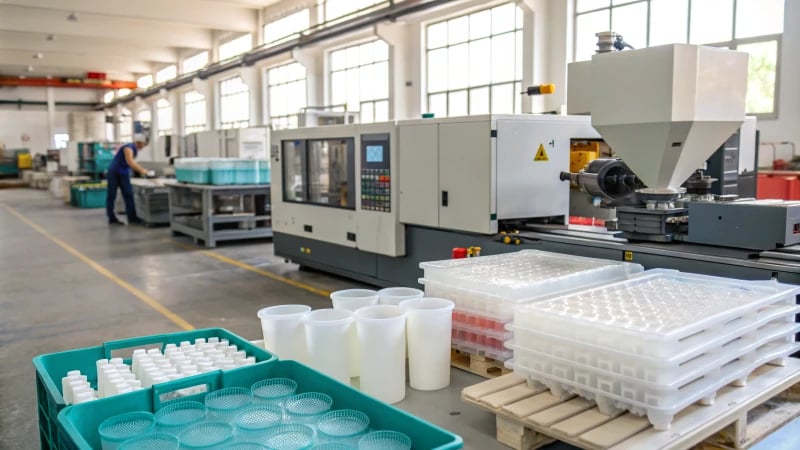
What Are the Key Factors That Influence the Injection Molding Process?
This blog post delves into the critical factors influencing the injection molding process, including raw material selection, mold quality, process parameters, and quality monitoring techniques to enhance production efficiency and product quality.
OPTIMIZATION
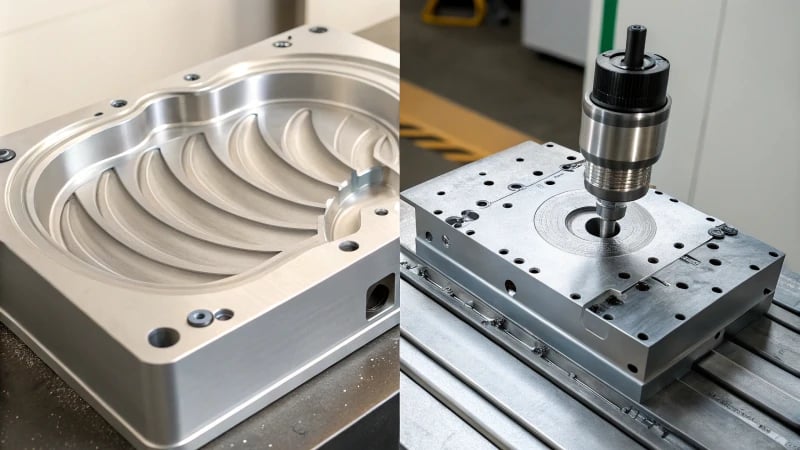
What Are the Key Differences Between a Mold and a Die?
Molds and dies are essential manufacturing tools that shape materials like plastics and metals. Understanding their differences in function, structure, and quality control is crucial for efficient production.
MANUFACTURING
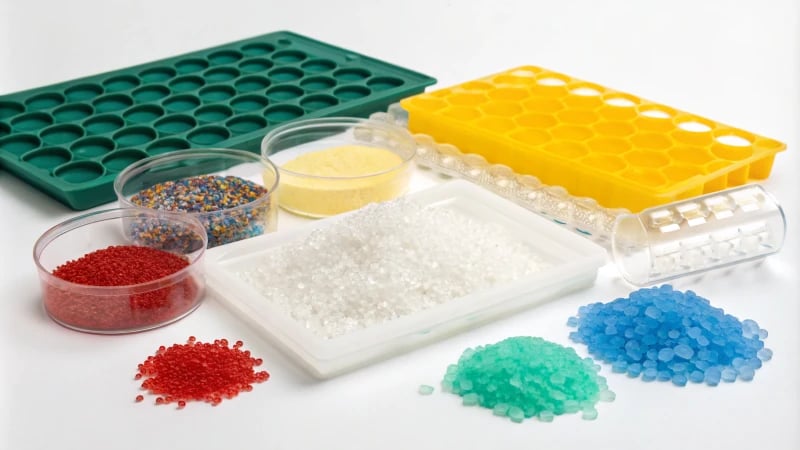
What is the Strongest Injection Molded Plastic You Should Consider?
This article explores the strongest injection molded plastics, including Polyamide, Polycarbonate, Polyoxymethylene, and Polyphenylene Ether. Each material's unique properties make them ideal for various applications in automotive and electronics industries.
Materials Recommendations
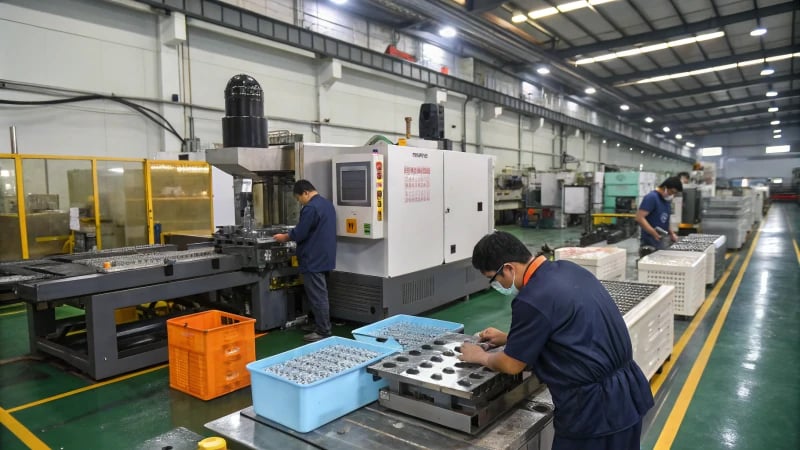
What Are the Key Steps in the Plastic Injection Mold Manufacturing Process?
This article delves into the essential steps of plastic injection mold manufacturing, covering mold design, material selection, processing technologies, cooling systems, and quality control practices to ensure high-quality production.
MANUFACTURING
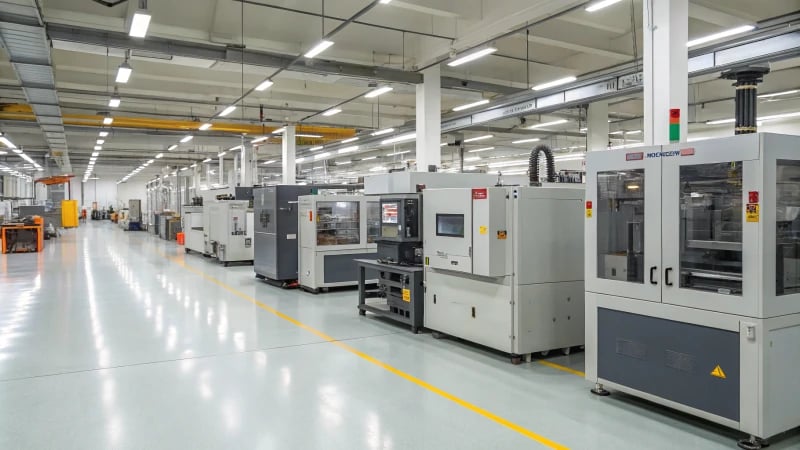
What Are the Most Common Types of Injection Molding Machines?
This article explores the various types of injection molding machines, including hydraulic, electric, and pneumatic options. It highlights their classifications by appearance, power source, plasticization methods, and clamping techniques to aid in selecting the right machine for manufacturing needs.
DEVELOPMENT
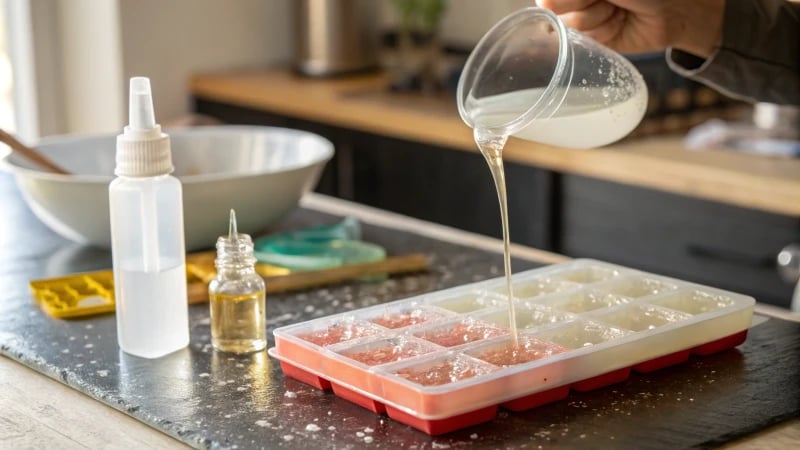
What Are the Best Ways to Prevent Resin from Sticking to Molds?
Preventing resin from sticking to molds is essential for smooth crafting. Utilize mold release agents like silicone oil, wax, and PTFE, optimize curing conditions, and consider internal release agents for better results.
OPTIMIZATION
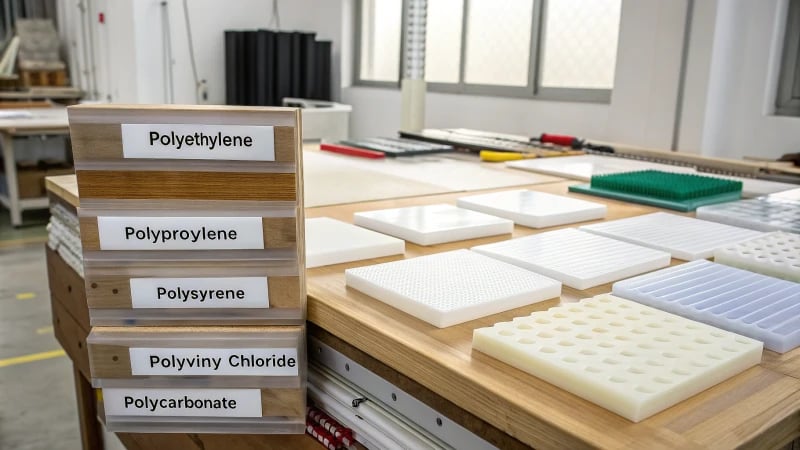
What Is the Best Type of Plastic for Molding: A Comprehensive Guide?
Choosing the right plastic for molding is crucial for product success. This guide explores various plastics, their properties, applications, and how to select the best material for your project.
Materials Recommendations
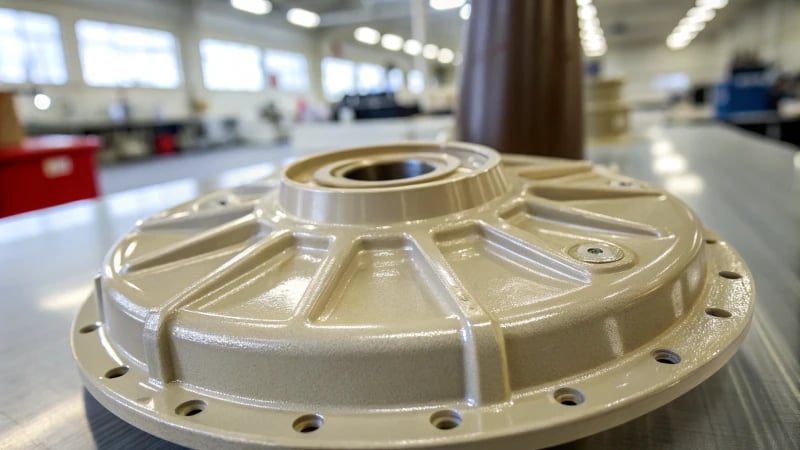
What Are the Best Techniques for Creating High-Quality Injection Molded Parts?
Creating high-quality injection molded parts requires careful attention to raw material selection, mold design, process parameter control, and rigorous quality monitoring. Each step is crucial for optimal results.
DEVELOPMENT
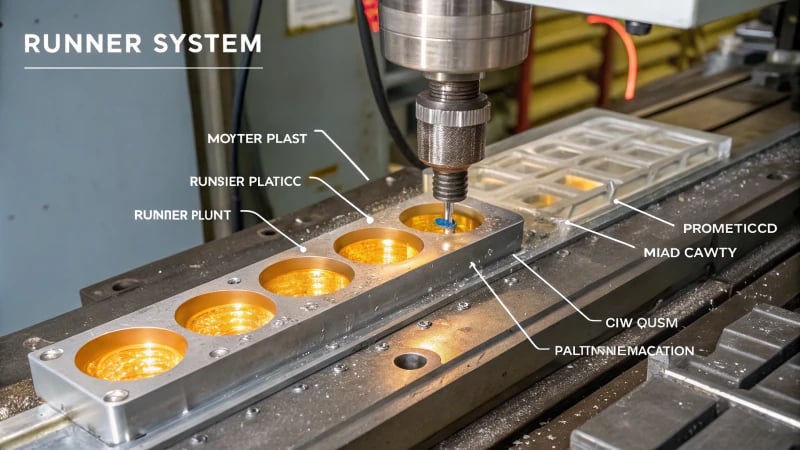
What Role Does the Runner Play in Plastic Molding?
The runner system in plastic molding is crucial for transporting molten plastic from the injection machine to the mold cavity. Its design impacts production efficiency, product quality, and waste reduction.
DEVELOPMENT
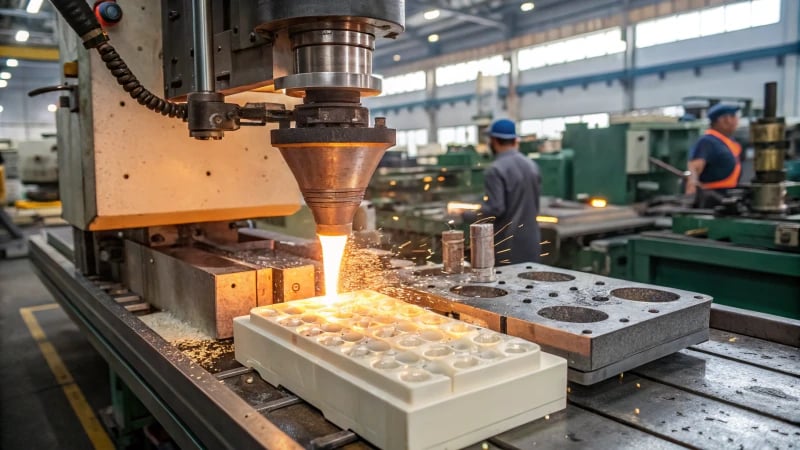
How Do Injection Molding Machines Create Plastic Boxes?
This article delves into the injection molding process for creating plastic boxes, covering machine operation, mold design considerations, process parameters, and strategies for improving production efficiency.
MANUFACTURING
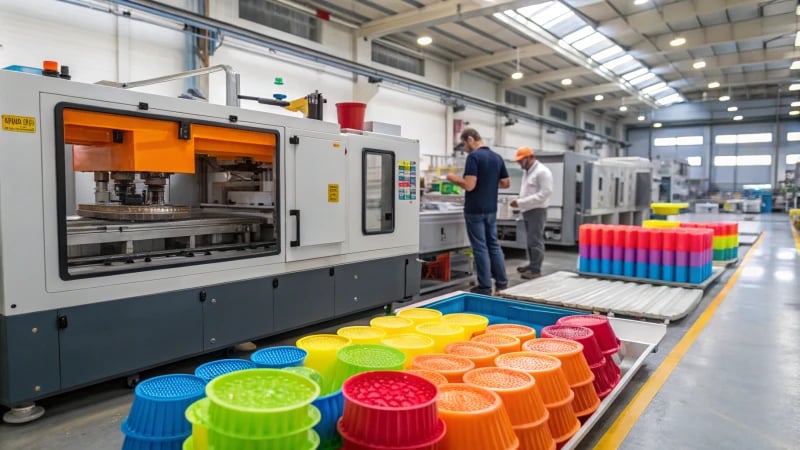
What Is Plastic Molding and Why Is It Important?
Plastic molding is a crucial manufacturing process that shapes plastic materials into various forms using techniques like injection, extrusion, and blow molding. It enhances efficiency, reduces waste, and supports diverse industries.
DEVELOPMENT
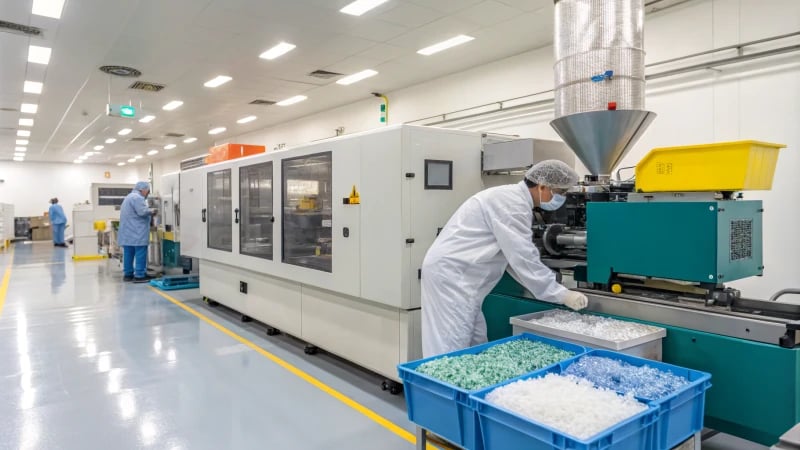
What Are the Benefits of Plastic Molding Services?
Plastic molding services offer numerous benefits, including efficiency, cost-effectiveness, design flexibility, and strict quality control. These advantages make them ideal for various manufacturing needs and enhance product quality.
DEVELOPMENT
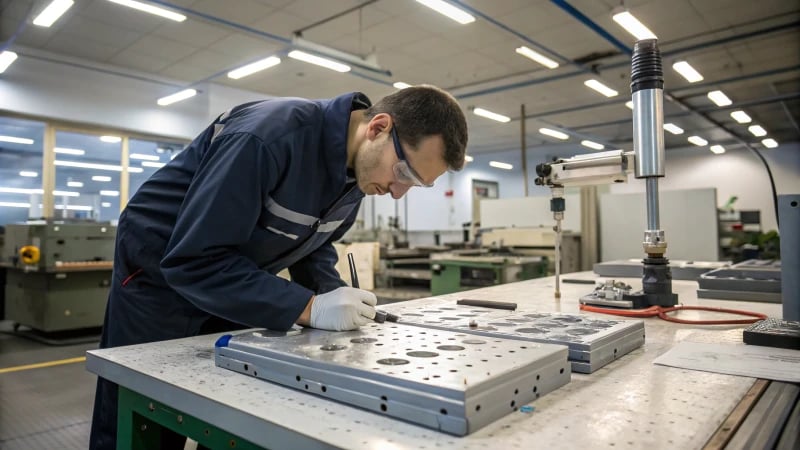
What Are the Best Techniques for Making a Hard Plastic Mold?
This article explores the essential techniques for creating hard plastic molds, covering design, material selection, processing, assembly, trial production, and maintenance to ensure high-quality results.
DEVELOPMENT
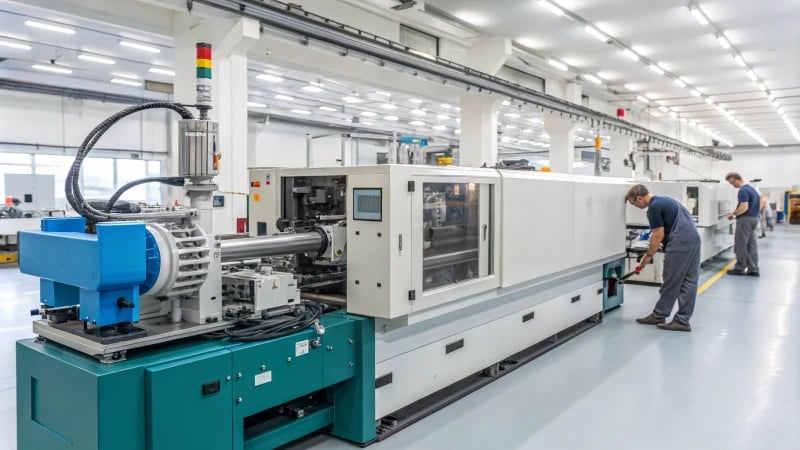
What is Tool Life in Injection Molding and Why Does It Matter?
Tool life in injection molding refers to the duration molds and components last before needing replacement. Factors like material quality, design complexity, and process parameters significantly influence tool longevity and production efficiency.
DEVELOPMENT
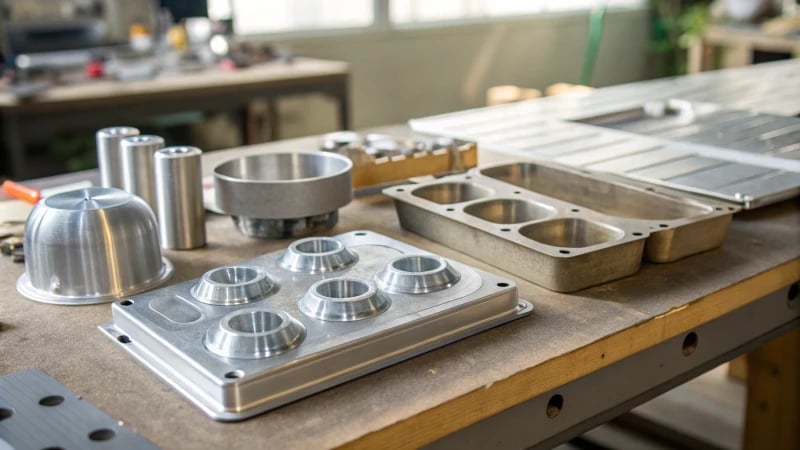
What is the Best Material for Your Mold and How to Choose It?
Choosing the right material for mold making involves considering factors like batch size, precision requirements, complexity, performance characteristics, and cost. Advanced materials enhance durability and efficiency in production.
Materials Recommendations