Discovering the mysteries of injection molding really changes how you approach manufacturing. Believe me, I’ve experienced it!
To determine the adjustment sequence of injection molding process parameters, consider barrel and mold temperature, material drying, injection speed, pressure, holding pressure, and cooling time. Adjustments should align with material properties and product requirements for improved quality and efficiency.
During my time in the mold industry, I found that mastering injection molding depends on adjusting parameters well. True mastery goes beyond numbers. It involves finding the balance where quality and efficiency meet. Over the years, I have refined my method of changing temperature, pressure, speed and cooling time systematically. This guide shares those insights with you. I hope it increases your manufacturing abilities as it did for me.
Temperature significantly impacts injection molding quality.True
Temperature adjustments are crucial for optimizing the injection molding process, affecting material flow and final product characteristics.
Cooling time has no effect on injection molding efficiency.False
Cooling time is a critical factor in injection molding that directly influences cycle time and product quality.
- 1. What Are the Key Temperature Parameters in Injection Molding?
- 2. How Do Material Properties Influence Parameter Adjustments?
- 3. How Does Injection Speed Impact the Quality of My Products?
- 4. Why Is Cooling Time Critical in the Injection Molding Process?
- 5. How Can You Optimize Holding Pressure for Better Results?
- 6. How Can You Effectively Validate Injection Molding Parameters?
- 7. Conclusion
What Are the Key Temperature Parameters in Injection Molding?
Have you ever thought about how the right temperature settings could ruin or perfect an injection-molded product? Let’s explore the important temperature factors. These factors probably influence production speed and quality. I will share insights from my experience in this interesting field.
In injection molding, key temperature parameters include barrel temperature (180-220°C for PP), mold temperature (60-80°C for precision parts), and drying temperature for materials like nylon (80-90°C for 4-6 hours). Adjusting injection speed and pressure to these temperatures is crucial for quality.
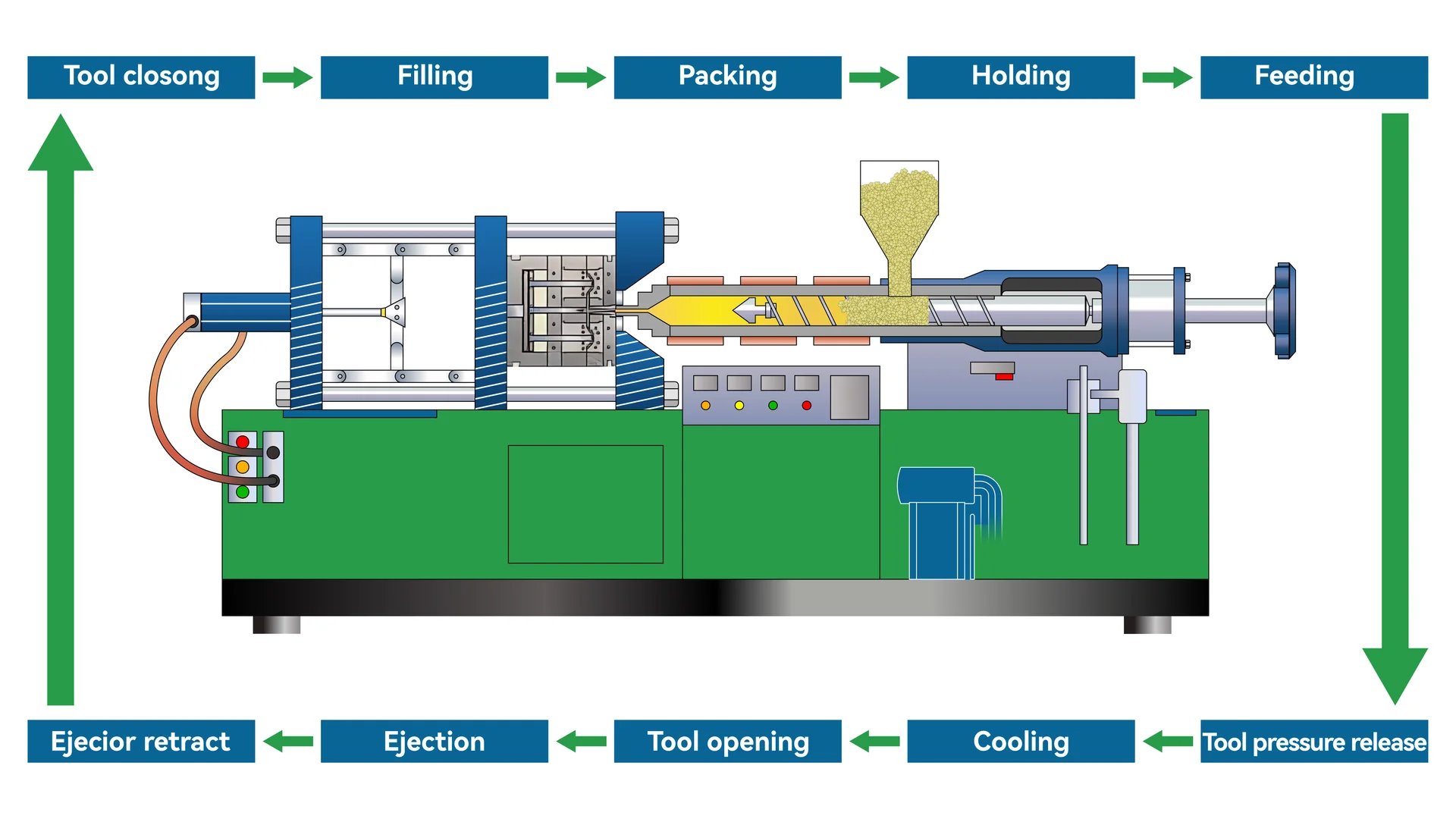
Understanding Barrel Temperature
The barrel temperature is critical in the injection molding process, as it determines how effectively the plastic material melts.
For instance, the barrel temperature for polypropylene (PP) materials typically ranges from 180 to 220°C. This range ensures that the material reaches a state suitable for injection, providing optimal fluidity.
Material | Barrel Temperature (°C) |
---|---|
Polypropylene | 180 – 220 |
Nylon | 200 – 250 |
When designing products with high surface quality requirements, such as precision electronic parts, the mold temperature may need to be set higher (60 – 80°C) to achieve uniform cooling.
Mold Temperature Considerations
Mold temperature directly affects the final product quality. Higher temperatures can enhance fluidity and ensure better filling of intricate molds, which is crucial for maintaining dimensional accuracy.
For example, a mold temperature of around 70°C might be ideal for achieving a smooth surface finish on complex designs. If you’re looking to dive deeper into the impact of mold temperature on product quality, check out mold temperature effects1.
Material Drying Parameters
For certain plastic materials, especially those that absorb moisture like nylon (PA), drying is an essential pre-treatment.
- Drying Temperature: Generally set between 80 and 90°C.
- Drying Time: Typically lasts for about 4 to 6 hours.
The purpose of this drying process is to eliminate moisture content that could lead to defects during injection, such as bubbles or silver streaks. To learn more about moisture control in plastics, see moisture management in plastics.
Adjusting Injection Parameters
Once the temperature parameters are set, attention shifts to injection speed and pressure:
- Injection Speed: This should be tailored based on product wall thickness and complexity. For thin-walled products, a higher speed (30 – 50mm/s) is often recommended initially.
- Injection Pressure: Should be adjusted following speed setting, particularly in relation to product fill. For instance, a flow length ratio of about 100:1 may require pressures around 100 – 120MPa initially.
Holding Pressure and Time
After establishing initial injection parameters, the next step involves optimizing holding pressure:
- Holding Pressure: Often set between 60 – 80MPa for thicker walls (5 – 8mm).
- Holding Time: Typically lasts around 10 – 15 seconds.
This adjustment is vital to prevent shrink marks and ensure that products maintain their intended dimensions after cooling. Explore more about optimizing holding pressure in injection molding at holding pressure optimization.
Cooling Time Assessment
Cooling time is another critical parameter that must be fine-tuned according to product wall thickness:
- For 10mm thickness: Approximately 30 – 40 seconds.
- For 3mm thickness: Around 10 – 15 seconds.
Proper cooling prevents deformation and ensures that products meet quality standards. To gain insights into cooling techniques, visit cooling techniques in molding.
Iterative Validation and Fine-Tuning
The final step in ensuring optimal temperature settings involves repeated validation through trial production. Monitoring overall quality metrics allows for gradual adjustments to stabilize production parameters effectively. Each parameter impacts the others, necessitating careful analysis and fine-tuning until desired outcomes are achieved.
Barrel temperature for polypropylene is 180-220°C.True
This range is essential for melting polypropylene effectively during injection molding.
Mold temperatures above 80°C guarantee better product quality.False
Higher mold temperatures enhance fluidity and filling, but not all cases require this setting.
How Do Material Properties Influence Parameter Adjustments?
Do you ever think about how the core nature of materials affects changes in manufacturing settings? This is an interesting journey. I have grown to really value it through my own experiences in the industry. It is truly fascinating.
Material properties significantly affect parameter adjustments in manufacturing, impacting temperature settings, injection speeds, and cooling times, which are crucial for optimal production quality.
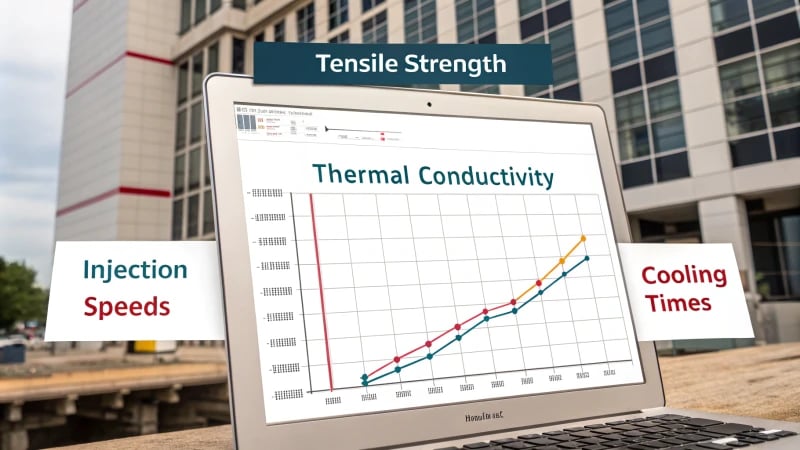
Understanding Material Properties
Material properties are not just technical specifications; they resemble the personality traits of the materials we use. Each time I begin a project, understanding these properties becomes my guiding star. It helps me improve processes effectively.
Material properties play a crucial role in the adjustments made to parameters during manufacturing processes. These properties can be mechanical, thermal, or chemical in nature and significantly influence how materials behave under various conditions.
-
Mechanical Properties: These include tensile strength, hardness, and elasticity. For instance, materials with high tensile strength may require higher injection pressures to ensure proper filling of molds. This means the designer must consider the mechanical properties to set appropriate injection pressures2 based on the material being used.
-
Thermal Properties: The melting point and heat capacity of a material dictate temperature settings during processes like injection molding. For example, polypropylene (PP) is processed at temperatures between 180 – 220°C, as it melts within this range. Knowing these thermal traits is crucial for setting temperature parameters3 that impact production quality directly.
Parameter Adjustments Based on Material Types
Different materials need specific adjustments in process parameters:
Material Type | Recommended Barrel Temp (°C) | Recommended Mold Temp (°C) | Drying Temp (°C) | Drying Time (hrs) |
---|---|---|---|---|
Polypropylene | 180 – 220 | 60 – 80 | N/A | N/A |
Nylon | 200 – 250 | 60 – 80 | 80 – 90 | 4 – 6 |
I’ve seen how nylon’s drying requirements prevent defects such as bubbles and silver wires during injection if not addressed. Therefore, the designer must adjust drying parameters4 accordingly.
Injection Speed and Pressure Adjustments
The relationship between injection speed and pressure is also influenced by material properties. When processing thin-walled products, a higher injection speed is often required:
- For thin-walled designs (2-3mm), a starting speed of 30 – 50mm/s is recommended to prevent short shots. However, materials with lower flow rates may necessitate adjustments in both speed and pressure to achieve optimal filling.
To address potential issues like flow marks or jetting, the injection speed5 should be fine-tuned based on specific material characteristics and wall thickness of the product being produced.
Importance of Cooling Parameters
Cooling time is another critical parameter that is influenced by thermal properties:
- A thicker product generally requires a longer cooling time. For instance, cooling times may vary significantly from 10-15 seconds for products with a wall thickness of 3mm to 30-40 seconds for those at 10mm thickness. Properly adjusting cooling times6 based on material properties ensures that deformation does not occur during demolding.
Continuous Validation and Fine-Tuning
Finally, once initial parameters are set, continuous validation becomes important. Observing product quality and making small adjustments based on trial run feedback is key. Each change in parameter settings—such as pressure or temperature—can affect overall product outcomes; thus understanding material traits is crucial in this process.
Material properties dictate injection speed adjustments.True
Different materials require specific injection speeds to ensure optimal filling and prevent defects during manufacturing processes.
Thicker products need shorter cooling times.False
Cooling times increase with product thickness to prevent deformation, making material properties crucial for setting these parameters accurately.
How Does Injection Speed Impact the Quality of My Products?
Have you ever thought about how the injection speed influences the quality of your product? I want to share my experiences in injection molding with you. This important factor really matters for what we create. Very important, indeed.
Injection speed significantly influences injection molding product quality, affecting surface finish, measurements, shape retention, and strength. It alters flow characteristics and filling dynamics, impacting every process aspect.
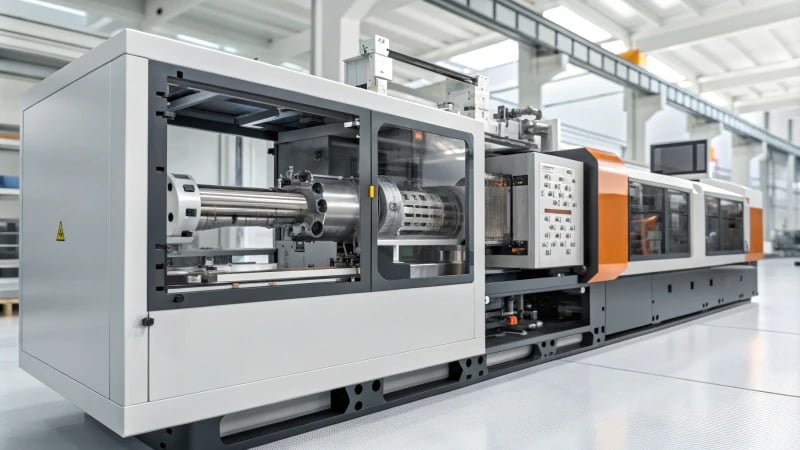
Understanding Injection Speed
Injection speed is a critical parameter in the injection molding process that significantly influences the quality of the final product. The speed at which the molten plastic is injected into the mold affects various factors including the surface finish, dimensional accuracy, and overall integrity of the molded part.
Higher injection speeds are often used for thin-walled products or those with simpler geometries. For instance, when producing a thin-walled plastic shell, I learned about ideal speeds. A speed of approximately 30-50 mm/s was recommended. Initially, I doubted the effect of numbers on final results; however, it helped prevent short shots, where the mold does not fill completely. Watching a perfect product emerge felt incredible. The right speed made a difference.
Conversely, slower injection speeds can be beneficial for complex or thicker-walled products to allow for better filling and to avoid defects such as flow marks or jetting. Slower speeds became vital for products with thick walls or complex details as it avoids defects like flow marks. It’s fascinating how understanding speed dynamics allows designers like me to raise product quality without losing efficiency.
Factors Influencing Injection Speed
Several key factors should be considered when determining the optimal injection speed:
- Wall Thickness: Thick walls need slower speeds for even flow; pouring syrup too fast doesn’t reach every corner.
- Material Properties: Different plastics have unique behaviors; for instance, polypropylene (PP) flows easily and can be injected faster than nylon (PA).
- Mold Design: A mold’s complexity can define the needed speed; slowing down for intricate designs ensures complete filling.
Factor | Influence on Injection Speed | Recommended Speed Range |
---|---|---|
Wall Thickness | Thicker = Slower | 30-50 mm/s |
Material Type | Viscosity impacts speed | PP: 30-50 mm/s, PA: 10-20 mm/s |
Mold Complexity | Complex = Slower | Adjust based on flow tests |
Observing Effects on Product Quality
Observation reveals injection speed’s impact on product quality. Common issues that may arise from inappropriate speeds include:
- Flow Marks: High injection speeds can create visible flow lines on the surface.
- Jetting: Excessive speed can cause defects due to material jetting into the mold.
To mitigate these issues, I used a simple plan:
- Begin with moderate speeds based on assessments.
- Conduct trial runs and evaluate surface quality.
- Change speed as needed based on observations.
For example, if flow marks are observed at a speed of 40 mm/s, reducing to 30 mm/s could improve surface finish greatly. This iterative process of testing and adjusting ensures that final products meet quality standards while optimizing production efficiency.
Conclusion Without a Conclusion
Adjusting injection speed is like a dance requiring careful steps. Designers like me strive to produce high-quality plastic parts by mastering this skill. If interested in optimizing your process, explore injection molding best practices7 or how material properties affect speed . Continuous learning drives success in our field.
Higher injection speeds improve surface finish in thin-walled products.True
Higher speeds can enhance the surface quality of thin-walled molded items by ensuring complete filling and reducing defects.
Slower injection speeds are better for complex mold designs.True
Complex molds require slower speeds to allow proper filling, preventing defects like flow marks and ensuring product integrity.
Why Is Cooling Time Critical in the Injection Molding Process?
Ever thought about why cooling time matters so much in injection molding? Knowing its importance truly shifts your approach to both quality and efficiency. Let’s explore why this part is very vital in manufacturing.
Cooling time in injection molding is crucial for preventing defects such as warping or shrinkage. Optimal cooling depends on wall thickness and material properties, ensuring high-quality production.
Importance of Cooling Time
Cooling is when magic happens. Molded plastic solidifies, holding its shape as it leaves the mold. I saw a part come out too soon once and it warped instantly. If cooling time is too short, the product will warp or shrink. This may lead to problems later.
Consider wall thickness. A product with walls of 10mm thick might need about 30 to 40 seconds to cool. In contrast, something 3mm thin could cool in 10 to 15 seconds. Seeing these differences really helps in grasping how design influences cooling.
Factors Affecting Cooling Time
Several things affect the best cooling time:
Wall Thickness
Thicker walls trap heat longer, needing more time to cool.
Material Properties
Each plastic cools differently. For example, polypropylene cools differently from nylon.
Mold Temperature
Higher mold temperatures delay cooling since heat transfer rates vary.
Airflow
More airflow around the mold might reduce cooling time. However, it is really crucial to manage this to avoid uneven cooling.
Impact on Production Efficiency
Optimizing cooling time is about much more than avoiding defects. It’s about increasing production efficiency. Slow cooling leads to longer cycle times and lower output. But if cooling is too quick, product quality might suffer.
Manufacturers often run trials to find the right balance. Adjusting settings based on observations during production is common. For more on improving production efficiency, see cooling optimization techniques.
Cooling Time Validation Techniques
Once we decide on preliminary cooling times, based on design and material, we need to test these settings. Here’s how:
Temperature Measurement: I use infrared thermometers to check product temperature after demolding.
Deformation Observation: I inspect for warping or surface flaws.
Trial Production Runs: Conducting trial batches helps assess quality and adjust as needed.
Combining these validation techniques with careful monitoring lets us fine-tune cooling times. This helps us achieve the best results without losing quality.
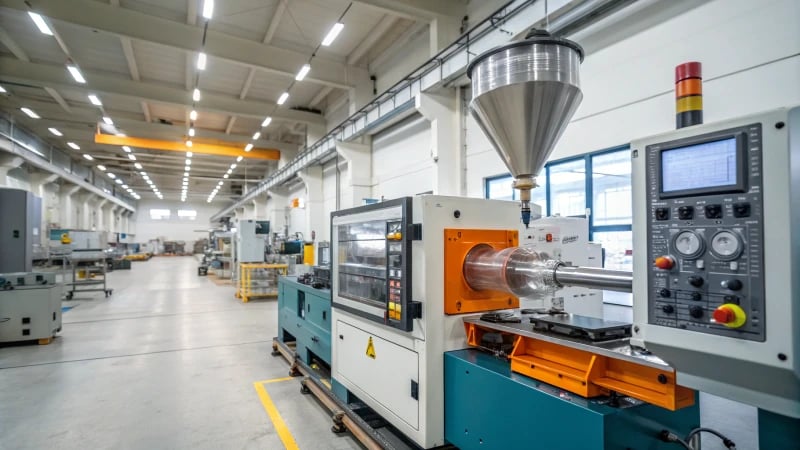
Cooling time is a crucial aspect of the injection molding process, directly influencing the quality and integrity of the molded parts. Understanding why cooling time matters involves several key parameters that need to be optimized for each specific application.
Importance of Cooling Time
Cooling time is more than a technical term; it changes the game in injection molding. Parts solidify properly when it is correct. This prevents defects like warping or shrinkage. In the beginning, I discovered that cooling time depends on many factors. Wall thickness and material properties are important examples. Precision is very crucial for that ideal finish everyone wants.
For instance, consider a product with a wall thickness of 10mm. The cooling time may take between 30 to 40 seconds, whereas a product with a wall thickness of 3mm might only require about 10 to 15 seconds.
Wall Thickness (mm) | Cooling Time (seconds) |
---|---|
3 | 10 – 15 |
10 | 30 – 40 |
This variation in cooling time highlights how different designs and material properties dictate the necessary adjustments during production.
Factors Affecting Cooling Time
Several factors contribute to determining the optimal cooling time:
- Wall Thickness: Thicker walls retain heat longer and require more time to cool.
- Material Properties: Different plastics have unique thermal properties that affect how quickly they cool. For example, polypropylene cools at a different rate compared to nylon.
- Mold Temperature: A higher mold temperature can lead to longer cooling times as the heat transfer rates are affected.
- Airflow: Enhanced airflow around the mold can reduce cooling time, but careful management is essential to avoid uneven cooling.
Impact on Production Efficiency
Optimizing cooling time is not just about preventing defects; it also significantly affects production efficiency. If cooling time is too long, it can lead to increased cycle times and lower throughput. Conversely, reducing cooling time too much may compromise product quality.
To strike the right balance, manufacturers often conduct a series of trial runs, adjusting parameters based on observations and measurements taken during production. For a deeper understanding of production efficiency, you might want to explore cooling optimization techniques8.
Cooling Time Validation Techniques
After establishing preliminary cooling times based on product design and material selection, it’s essential to validate these settings through rigorous testing. Techniques include:
- Temperature Measurement: Using infrared thermometers to check product temperatures post-demolding.
- Deformation Observation: Inspecting products for signs of warping or surface imperfections.
- Trial Production Runs: Conducting batch trials to monitor overall product quality and adjust as needed.
By combining these validation techniques with precise monitoring, manufacturers can fine-tune their cooling times to achieve optimal results without sacrificing quality. For a comprehensive guide on validation methods, see validation best practices9.
Cooling time affects the quality of molded parts.True
Insufficient cooling time can cause defects like warping or shrinkage, impacting product integrity.
Thicker walls require longer cooling times in injection molding.True
Products with greater wall thickness retain heat longer, necessitating extended cooling durations for proper solidification.
How Can You Optimize Holding Pressure for Better Results?
Do you want to improve your injection-molded products? Optimizing holding pressure is very important! Please listen as I share insights and tips from my years of experience. These tips probably help you to achieve better results.
Optimize holding pressure by adjusting time and pressure according to wall thickness and quality needs. Regularly test and monitor outcomes to refine settings, enhancing the product’s quality and performance.
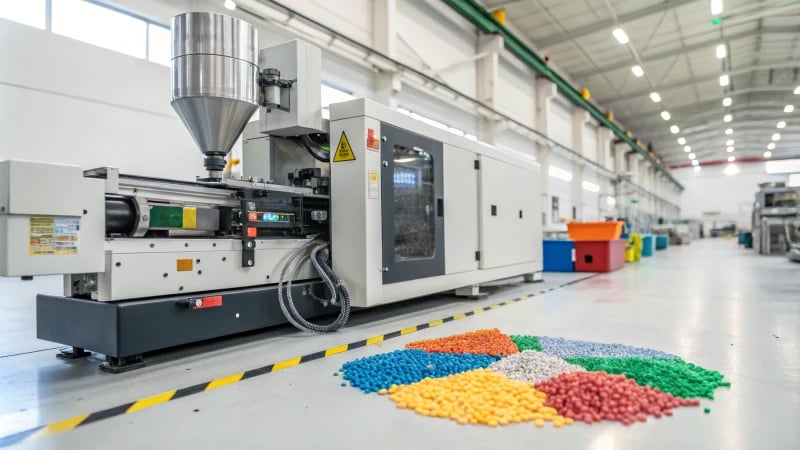
Improving Holding Pressure
To improve holding pressure in injection molding, adjust settings like holding time and pressure. Base adjustments on wall thickness and the desired product quality. Regularly check performance through repeated testing. This is very important for the best results. I recall my early days in the industry. The trial and error process showed me how important these adjustments are. Each change brought better quality. I felt excited analyzing each result. I knew I was closer to perfecting the process.
Key Parameters for Optimization
To optimize holding pressure effectively, consider the following parameters:
Parameter | Description | Example Values |
---|---|---|
Holding Pressure | The pressure applied post-injection | 60 – 80 MPa |
Holding Time | Duration for which the holding pressure is applied | 10 – 15 seconds |
Wall Thickness | Thickness of the molded part | 5 – 8 mm |
Surface Quality Needs | Desired aesthetic and functional qualities of the part | High precision requirements |
Practical Steps for Optimization
-
Initial Settings: Start by determining your initial holding pressure based on the wall thickness and desired quality. For thicker parts, increase the holding pressure incrementally to observe changes in quality.
-
Monitor Surface Quality: After each trial, check for shrink marks or other surface defects. This can help fine-tune both pressure and time settings. If defects are observed, consider increasing either the holding time or pressure.
-
Iterative Adjustments: Make adjustments based on observations. It may take several iterations to find the optimal settings that yield consistent results. Each change in one parameter can affect others, so remain flexible in your approach.
Observing Results
To validate your adjustments, keep an eye on:
- Dimensional Accuracy: Use calipers or laser measurements to assess if the product meets specifications.
- Quality Inspections: Conduct visual inspections for any surface imperfections or inconsistencies.
- Trial Production Runs: Run batches to gauge efficiency and quality before moving to full-scale production.
By optimizing holding pressure and understanding its relationship with other parameters like temperature and injection speed, you can achieve better results and enhance product quality significantly. For further details on improving performance under pressure, check out this guide on stress management techniques10.
Higher holding pressure prevents shrink marks in thick-walled parts.True
Increasing holding pressure is essential for thick-walled components to avoid defects like shrink marks during the cooling process.
Holding time does not affect the quality of molded products.False
The duration of holding pressure significantly influences product quality, as insufficient time can lead to defects and inaccuracies.
How Can You Effectively Validate Injection Molding Parameters?
Let’s explore some key strategies for checking injection molding settings. These steps help improve product quality and may also help your manufacturing process run more smoothly. Are you ready to begin?
To effectively validate injection molding parameters, focus on temperature, adjust injection speed and pressure, optimize holding pressure, accurately determine cooling times, and conduct repeated validations to ensure consistent quality.
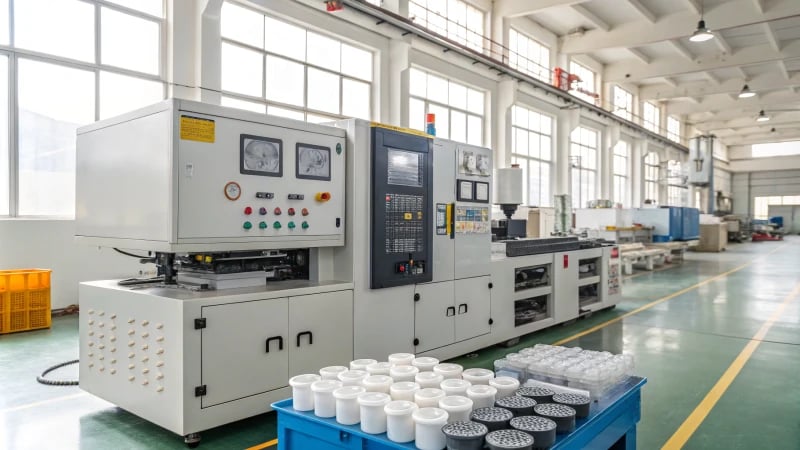
Starting from the Basic Parameters
The validation starts by identifying key basic parameters that guide the molding process. Among these, temperature settings feel like the heartbeat of injection molding to me.
-
Barrel Temperature: Imagine molding a product with polypropylene (PP). The barrel temperature should be set between 180 – 220°C. This range helps the material melt perfectly, reaching the right fluidity.
-
Mold Temperature: Now consider the mold temperature. It’s crucial for product quality. I once worked on a precision electronic part needing the mold temperature between 60 – 80°C. This range helps maintain fluidity during cooling. This focus on detail really mattered in the final product.
In addition to temperature, do not ignore material drying parameters. For absorbent materials like nylon (PA), drying at 80 – 90°C for 4 – 6 hours is essential. I learned this when skipping this step caused bubbles in my product. That was a lesson I will never forget!
Injection Parameter Adjustment
Once temperatures are correct, move to injection parameters. This step is critical and often makes me a bit nervous.
-
Injection Speed: Product wall thickness and complexity decide the speed. For thin-walled products, I start with speeds of 30 – 50 mm/s. I check surface quality on test molds. If I see issues like flow marks, I adjust the speed.
-
Injection Pressure: I set the initial pressure around 100 – 120 MPa for complex products. Fine-tuning based on fill results is crucial. If filling is insufficient, increase the pressure. Finding the sweet spot is important!
Optimization of Holding Pressure Parameters
Next is optimizing holding pressure and time. This step prevents shrink marks on thicker products.
- Holding Pressure: For wall thicknesses of 5 – 8mm, I set holding pressure around 60 – 80 MPa with holding times of 10 to 15 seconds. Watching test molds for shrink marks helps me refine these settings.
Wall Thickness (mm) | Holding Pressure (MPa) | Holding Time (seconds) |
---|---|---|
5 – 8 | 60 – 80 | 10 – 15 |
<3 | <30 | <10 |
Determination of Cooling Parameters
Cooling parameters are also critical. Cooling time directly affects product integrity.
- Cooling Time: Thicker products need longer cooling times. A product with a thickness of 10mm might need about 30 – 40 seconds to cool, while a thinner one (3mm) could cool in just about 10 -15 seconds. Checking temperature after demolding avoids deformation!
Repeated Validation and Fine-Tuning
Finally, engage in repeated validation and fine-tuning. This phase can feel dull, but it really brings results.
Conduct batch trials to assess overall product quality and production efficiency. If issues arise—like dimensional deviations or defects—I analyze potential causes and adjust parameters sequentially until stability in quality is achieved. It often takes several iterations to perfect settings due to interconnected nature of parameters involved.
- Begin with small adjustments based on observed defects and refine each parameter carefully; patience and persistence lead the way.
For more insights into injection molding processes, explore in-depth methodologies11 that may improve your production efficiency and product quality.
Barrel temperature affects the fluidity of plastic materials.True
Correct barrel temperature ensures optimal melting, impacting the fluidity of plastics during injection molding.
Cooling time is irrelevant for product integrity in injection molding.False
Cooling time is crucial; inadequate cooling can lead to product deformation and defects.
Conclusion
Learn effective strategies for optimizing injection molding parameters like temperature, pressure, speed, and cooling time to improve product quality and manufacturing efficiency.
-
Discover how temperature settings can optimize your injection molding process, enhancing product quality and efficiency. ↩
-
Discover how different materials affect parameter settings for improved manufacturing efficiency. ↩
-
Learn about optimizing parameters based on specific material characteristics to enhance product quality. ↩
-
Find insights on testing and validating parameter settings through material property analysis. ↩
-
Understand the role of cooling times influenced by material properties for better mold performance. ↩
-
Explore continuous validation techniques in manufacturing to maintain quality through material analysis. ↩
-
Clicking this link will provide you with detailed guidelines on injection speed optimization that can help improve your production quality. ↩
-
This link provides insights into techniques that can optimize your injection molding process, enhancing production efficiency and product quality. ↩
-
Learn about best practices for validating cooling times in your production runs, ensuring high-quality outputs. ↩
-
Explore effective techniques to maintain composure under pressure and improve performance in high-stress situations. ↩
-
Clicking this link will provide you with detailed methodologies that can help you optimize your injection molding processes efficiently. ↩