Ever felt like you’re juggling two very demanding priorities at once?
Balance quality and cost in injection molding by selecting appropriate materials, optimizing mold designs, and adjusting process parameters to produce high-quality products affordably.
When I first stepped into the world of injection molding, it was like being at the crossroads of creativity and efficiency. The key to not only surviving but thriving here is understanding that every decision—from selecting raw materials to refining molds—is a chance to tip the scales in your favor. For instance, choosing the right engineering plastics can mean the difference between a part that stands the test of time and one that fails under stress. But it doesn’t stop at materials. Crafting a mold that ensures uniform cooling and perfect product dimensions is an art in itself, often requiring me to negotiate my way through design complexities. And then, there’s the thrill of optimizing processes—it’s a bit like tuning an instrument, where every tweak brings us closer to that perfect harmony of cost-efficiency and quality. This journey is about more than just manufacturing; it’s about creating value and achieving excellence in every product we bring to life.
Optimizing mold design reduces costs in injection molding.True
Efficient mold design minimizes material waste and improves production speed.
Higher quality always results in higher costs in injection molding.False
Strategic process optimization can enhance quality without increasing costs.
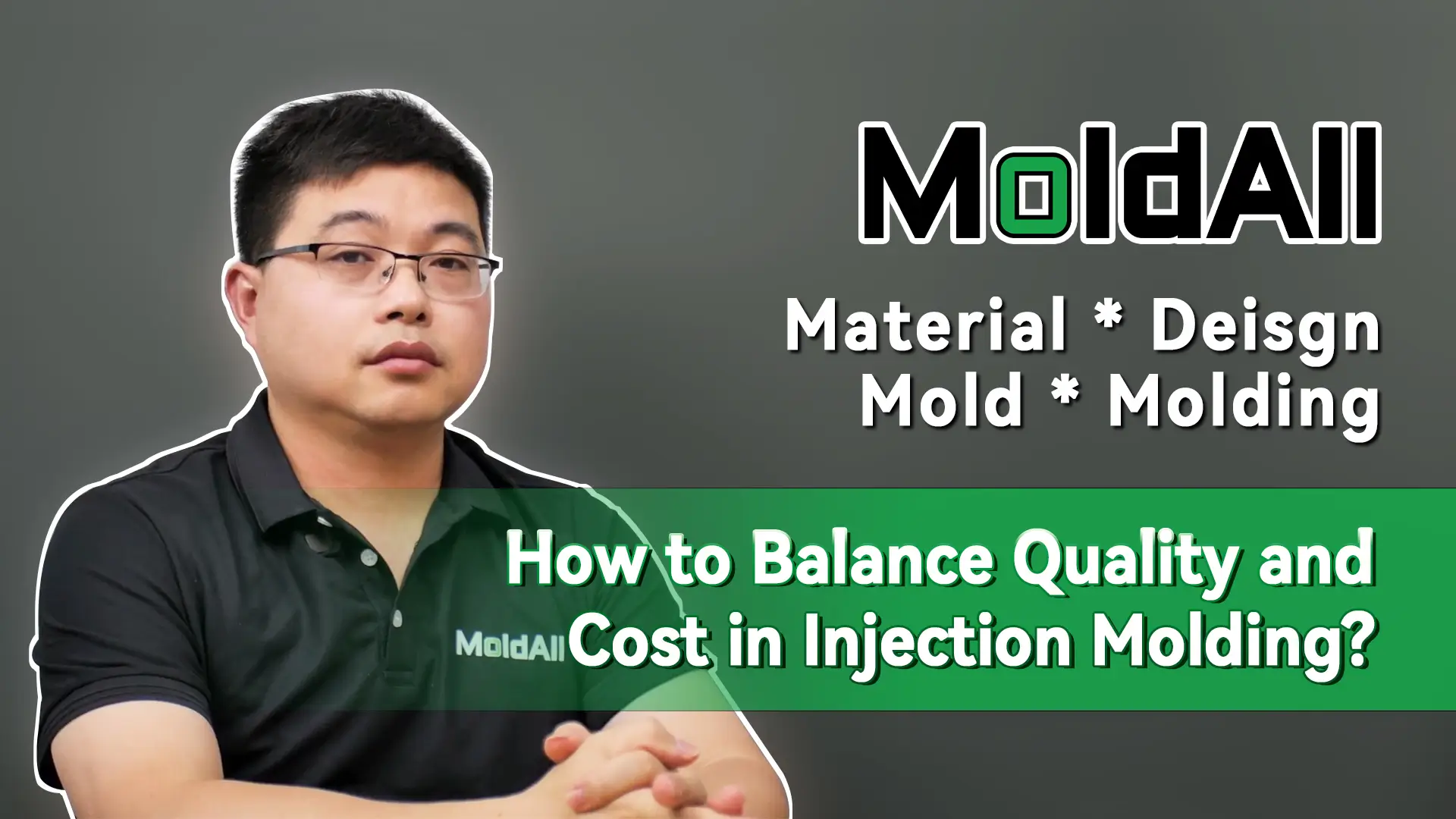
What Are the Key Factors in Raw Material Selection?
I remember the first time I realized how much choosing the right raw materials mattered. It felt like unlocking a secret to success that affected everything from product quality to sustainability.
Key factors in raw material selection include quality, cost, availability, and sustainability—essential for product performance, efficiency, and long-term success.
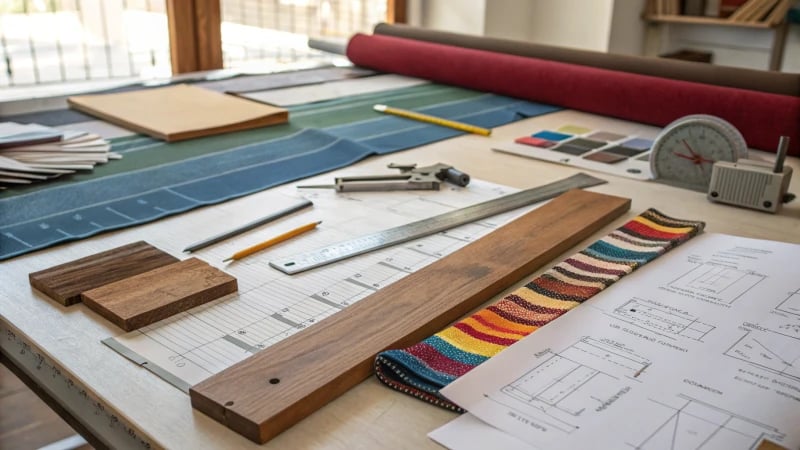
Quality Considerations
Back when I started working in product design, I learned quickly that quality was everything. Imagine trying to build a bridge using brittle wood when you have sturdy steel at your disposal. For me, selecting high-strength, high-toughness materials1 like polyamide or polycarbonate is like choosing the right foundation for a house. Ensuring strict control over physical properties like melt flow rate and chemical resistance has saved countless products from defects.
I once worked on an automotive project where we had to select materials that could withstand incredible stress and extend the service life of the parts. Impurities could have led to disasters, so we were meticulous about meeting stringent quality standards.
Cost Efficiency
Balancing quality and cost often feels like walking a tightrope. One memorable project involved replacing expensive engineering plastics with a blend of ABS and PS for a consumer electronics product. It had high aesthetic demands but didn’t require extreme mechanical properties. This decision was a game-changer in terms of cost.
I’ve found that negotiating with suppliers for better prices and volume discounts can be as rewarding as finding a great deal at my favorite store. Building strong supplier relationships has often led to more favorable terms and flexible delivery schedules.
Material | Application Example | Cost Strategy |
---|---|---|
ABS & PS | Consumer Electronics | Use blends for cost reduction |
PA & PC | Automotive Parts | Opt for long-term supplier contracts |
Environmental Impact
I’ve always been passionate about sustainability, which is why choosing eco-friendly materials is important to me. Using biodegradable plastics or recycled materials isn’t just a trend; it’s a responsibility. Evaluating the lifecycle impact—from production to disposal—ensures compliance with environmental regulations and meets consumer expectations for sustainable products.
Material Availability
Once, we faced a major delay due to a shortage of a key raw material, which taught me the importance of ensuring a steady supply. Diversifying supplier sources is like having backup plans for vacation; it mitigates risks of shortages or logistical disruptions.
Evaluating local versus international sourcing options based on availability, cost, and lead times has become second nature in optimizing supply chain efficiency.
The right balance of quality, cost, availability, and sustainability in raw material selection directly impacts product success and operational efficiency. Thoughtful consideration of these factors ensures optimized outcomes in manufacturing processes.
For more insights into improving your material selection strategy, consider exploring advanced material databases2. They offer detailed comparisons to guide your decision-making process.
High-toughness materials are ideal for mechanical stress.True
Materials like polyamide and polycarbonate withstand mechanical stress well.
Cost-effective materials always compromise on quality.False
Alternatives like ABS blends can maintain quality while reducing costs.
How does mold design impact cost and quality?
I’ve always been fascinated by the behind-the-scenes magic of manufacturing, especially how mold design can make or break the quality and cost of a product.
Mold design affects cost through material selection and production complexity, while it ensures quality via precise design and process management, leading to consistent and reliable products.
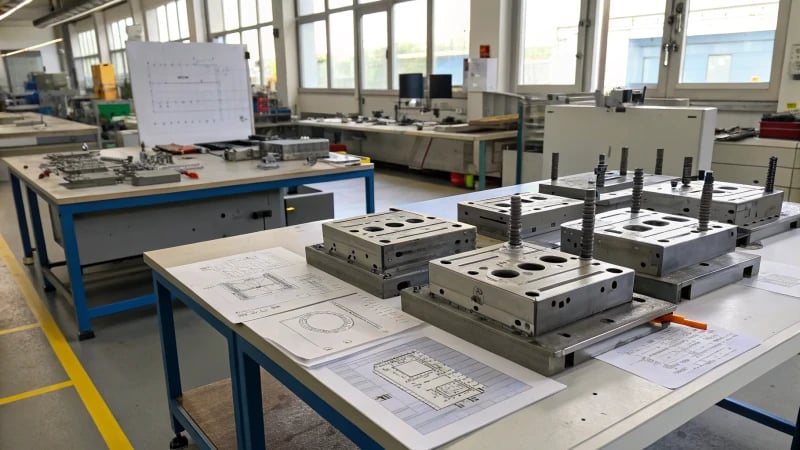
The Role of Raw Material Selection
I remember when I first had to choose materials for a project—it was like trying to pick the perfect ingredients for a recipe. The balance between cost and quality felt like a tightrope walk. Using high-strength engineering plastics like polyamide (PA) ensures durability but can strain the budget. On the other hand, blends like ABS offer a cost-effective alternative without sacrificing too much on quality, especially for less demanding applications.
Material | Quality | Cost |
---|---|---|
PA | High | High |
ABS | Moderate | Low |
Building relationships with suppliers is also crucial—I’ve found that negotiating terms not only reduces costs but also creates a more sustainable supply chain.
Precision in Mold Design
Precision in mold design is akin to crafting a masterpiece. It’s all about maintaining structural integrity and achieving perfect dimensional accuracy. Effective cooling systems are vital to prevent defects like shrink marks. Using high-quality mold steel like P20 and advanced techniques such as CNC machining not only prolongs the life of the mold but also ensures consistent product output.
Streamlining mold structures can significantly cut down manufacturing costs without compromising on quality. Simplifying designs by avoiding unnecessary complex features has saved me from many budget overruns.
Injection Molding Process Optimization
Optimizing the injection molding process can feel like fine-tuning an instrument—it requires careful adjustment of parameters like temperature, pressure, and speed. Real-time monitoring with advanced sensor technology ensures conditions are optimal, minimizing defects and maximizing yield.
Reducing scrap rates not only enhances quality but also slashes waste-related costs, promoting sustainable manufacturing practices3. By increasing efficiency through shorter cycle times, we can trim down energy and labor costs, impacting overall expense management while keeping quality standards high.
Using PA ensures high product durability.True
Polyamide (PA) is known for its high strength, ensuring durability.
Complex mold structures always reduce costs.False
Complex features increase initial investment in mold fabrication.
How Can Process Optimization Techniques Reduce Costs?
Ever wondered how to trim those pesky manufacturing costs without compromising on quality?
Optimize raw material selection, mold design, and injection molding to cut costs. Use cost-effective materials, boost efficiency, and uphold quality for substantial savings.
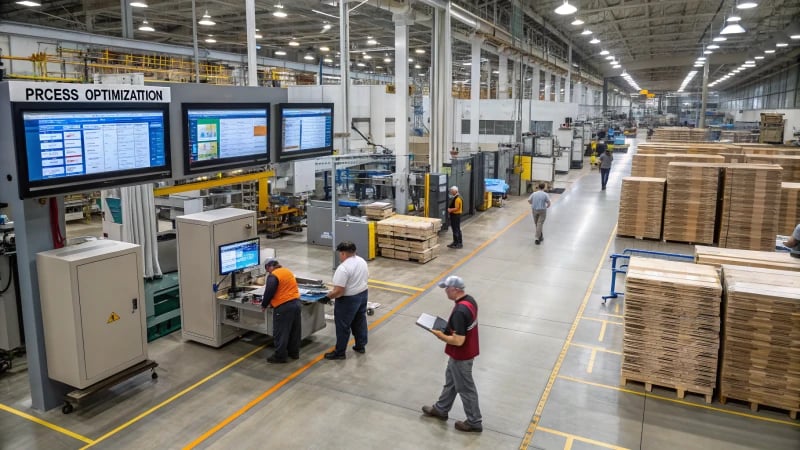
Raw Material Selection
Choosing the right raw materials4 isn’t just a technical decision—it’s like choosing the perfect ingredients for your favorite dish. Remember the time I picked up a cheaper chocolate brand for baking and ended up with a cake that was far less delightful? That’s why selecting materials like polyamide or polycarbonate ensures durability in high-stress applications, similar to choosing top-quality chocolate for that perfect cake. Negotiating long-term supplier relationships can feel like bargaining at a farmer’s market, where buying in bulk often means a better deal.
Material | Quality Benefits | Cost Strategy |
---|---|---|
PA, PC | High strength | Negotiate prices |
ABS | Visual appeal | Bulk discounts |
Mold Design and Manufacturing
Effective mold design is like crafting a custom-made suit; it must fit perfectly to prevent any embarrassing mishaps. Precision prevents issues like deformation and shrink marks—imagine wearing a suit with awkward wrinkles. Using high-quality steels and advanced manufacturing processes ensures that your mold, like your suit, lasts longer. Simplifying the design can be like finding a pair of universal cufflinks that work with any shirt, reducing costs while maintaining style.
- Quality: High-grade steel molds improve longevity.
- Cost: Simplified designs decrease production costs.
Injection Molding Process Optimization
Think of optimizing injection molding as fine-tuning your morning coffee routine. By adjusting the grind size and brewing time, you get the perfect cup every time. Similarly, fine-tuning parameters like temperature and pressure in molding can enhance product quality and efficiency. Just as monitoring your brew with a timer ensures consistency, real-time monitoring of molding processes reduces defects and boosts production rates.
- Quality Control: Use sensor technology5 for real-time monitoring.
- Efficiency: Adjust parameters to reduce scrap rates and cycle times.
By paying attention to these aspects, you maintain quality while slashing costs, much like preparing a gourmet meal on a budget. It’s all about dedication to detail and commitment to standards, ensuring we remain competitive in the market.
Choosing ABS over PA reduces material costs.True
ABS is generally less expensive than PA, making it a cost-effective choice.
High-grade steel molds increase production costs.False
While initially costly, high-grade steel molds save money by lasting longer.
How Can Advanced Monitoring Improve Product Quality?
Ever feel like product quality issues are haunting you? Advanced monitoring might just be the ghostbuster you need!
Advanced monitoring improves product quality by providing real-time insights for early defect detection, process optimization, consistency, waste reduction, and enhanced customer satisfaction.
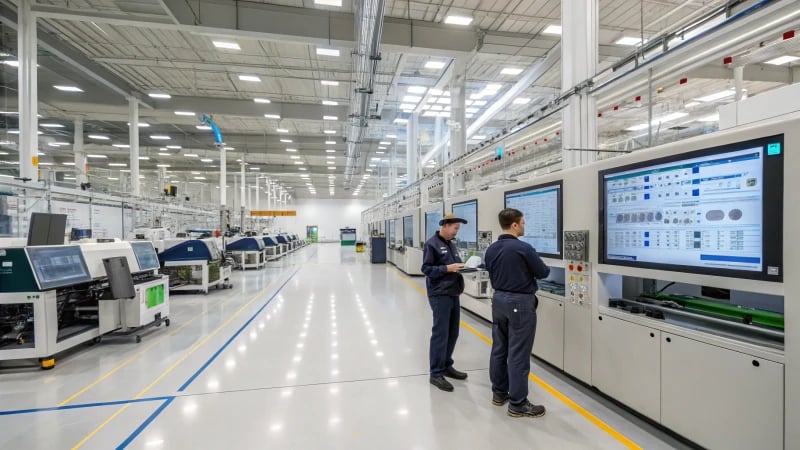
Real-Time Data Collection
I remember the first time I realized the power of real-time data. It was like having a backstage pass to my own production line, with sensors and IoT devices tracking every critical variable. Imagine the relief of knowing that any deviations from the norm, whether it be temperature or pressure, could be spotted and corrected immediately. This is especially crucial in processes like injection molding6, where maintaining the perfect melt flow can prevent costly defects such as warping or incomplete fills. It’s like having a guardian angel watching over each batch, ensuring consistency every time.
Predictive Maintenance
Then there’s predictive maintenance—think of it as a crystal ball for your equipment. By analyzing performance data, I could foresee potential failures and intervene before they spiraled into downtime disasters. For example, in mold design7, predicting wear and tear meant timely maintenance, extending the life of molds and safeguarding product quality. It felt like magic; problems were solved before they even existed.
Process Optimization
Advanced monitoring also opened the door to fine-tuning my processes in ways I hadn’t imagined. With detailed insights at my fingertips, adjusting parameters like injection speed and cooling time became second nature. This is particularly vital when juggling costs with quality—like evaluating ABS/PS blends to meet performance requirements8 without breaking the bank.
Aspect | Monitoring Focus | Example |
---|---|---|
Raw Material | Quality & Cost | ABS/PS blends |
Mold Design | Accuracy & Cost | P20 Steel usage |
Injection Process | Efficiency & Scrap Reduction | Parameter control |
With these tools, I’ve been able to refine my manufacturing processes to produce top-notch products while keeping efficiency high. It’s a win-win situation—enhanced product reliability leads to happier customers and a stronger brand reputation. And isn’t that what we all strive for?
Real-time monitoring reduces production defects.True
Real-time data helps identify deviations, allowing immediate corrective actions.
Predictive maintenance increases equipment downtime.False
Predictive maintenance minimizes downtime by preventing failures before they occur.
How Do Supplier Relationships Impact Cost Management?
Ever thought about how your morning coffee relies on a network of supplier relationships? It’s the same in business—those connections are key to cost management.
Strong supplier relationships enhance cost management by improving pricing, quality, and delivery timeliness, enabling strategic negotiations and collaborations that boost business value and efficiency.
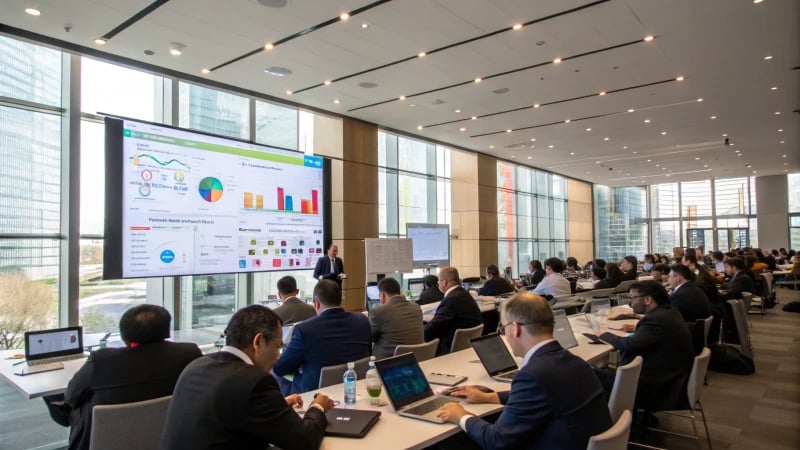
Understanding the Impact of Supplier Relationships
When I think about supplier relationships, I remember my first big project at MoldAll. I realized that these connections go beyond just transactions—they’re partnerships. Building long-term relationships9 with suppliers can open doors to cost advantages like negotiated discounts and flexible payment terms.
Raw Material Selection
Back then, I learned the hard way about the importance of selecting the right materials. Collaborating with suppliers on high-quality raw materials can prevent expensive defects. For example, in automotive parts, using polyamide (PA) or polycarbonate (PC) ensures durability.
- Quality Aspects: Working closely with suppliers helped me understand how critical it is to maintain quality standards. Checking properties like melt flow rate became second nature to avoid defects.
- Cost Aspects: Negotiating for cost-effective alternatives, like ABS/PS blends, can save costs without sacrificing quality. It was all about effective communication.
Material Type | Quality Focus | Cost Focus |
---|---|---|
PA/PC | High strength/toughness | Higher price |
ABS/PS Blend | Moderate strength | Lower price |
Mold Design and Manufacturing
I remember the first time I collaborated on mold design. It was clear how vital accurate designs are to reducing wastage and ensuring precision. Techniques like CNC machining became part of our quality arsenal.
- Quality Control: Getting supplier input on mold design helped ensure precision and reduce waste.
- Cost Efficiency: Simplifying mold structures with supplier insights cut manufacturing costs without losing functionality.
Injection Molding Process Optimization
Working with suppliers taught me that optimizing injection parameters is key for consistency. Advanced sensors became our eyes and ears on quality.
- Quality Assurance: Monitoring injection parameters with suppliers helps maintain consistency. It was a game-changer.
- Cost Reduction: Supplier insights helped us boost production efficiency by optimizing injection cycles, reducing energy and labor costs per unit.
The Strategic Value of Supplier Relationships
Effective supplier management isn’t just about haggling over prices. It’s about understanding their market conditions and integrating their expertise into your processes. Suppliers often have unique insights into market trends10, which can inform strategic decisions.
Through collaboration, we found that innovation in product development led to cost-effective solutions and better product offerings. Suppliers treated as partners rather than just vendors are more inclined to share valuable insights and resources.
Supplier relationship management (SRM) is an ongoing journey. Regular evaluations and feedback loops have helped us maintain mutually beneficial relationships, ensuring both parties work towards common goals. SRM tools11 have been invaluable in tracking interactions and optimizing outcomes.
Long-term supplier partnerships reduce overall costs.True
Partnerships lead to negotiated discounts and flexible terms.
Using ABS/PS blends increases production costs.False
ABS/PS blends are cost-effective, reducing production expenses.
Conclusion
Balancing quality and cost in injection molding involves strategic material selection, optimized mold design, and process efficiency to ensure high-quality products while managing expenses effectively.
-
Discover high-strength materials like polyamide that enhance durability in stress-prone applications. ↩
-
Explore comprehensive databases that provide detailed comparisons of materials for informed selection. ↩
-
Explore how optimizing injection molding processes contributes to sustainability by reducing waste and improving resource efficiency. ↩
-
Learn how selecting the right raw materials can enhance product quality while minimizing costs. ↩
-
Explore how sensors can enhance process monitoring and quality control in injection molding. ↩
-
Discover how real-time monitoring improves injection molding efficiency and reduces defects. ↩
-
Explore predictive maintenance strategies to enhance mold longevity and product quality. ↩
-
Understand how ABS/PS blends can meet performance requirements cost-effectively. ↩
-
Discover how building long-term partnerships with suppliers can lead to enhanced cost management and strategic advantages. ↩
-
Explore how suppliers can offer valuable insights into market trends that can inform strategic decisions. ↩
-
Learn about the top Supplier Relationship Management tools that help in optimizing costs and improving supplier interactions. ↩