Selecting the correct gate type in injection molding resembles choosing the ideal tool for a home project. Each option comes with its unique features and advantages.
Point gates perform well in injection molding. They give a very good appearance and design that works with automation. However, they also present challenges. The mold requires complexity. Pressure losses are significant too.
Understanding point gates can truly transform your design work. I recall my own experience when selecting a gate type for a big project. The choice felt overwhelming, but learning the details of point gates was crucial. These gates really impact your projects. However, watch out for possible mistakes. Know these potential pitfalls.
Point gates enhance the appearance quality of molded parts.True
Point gates provide a smoother finish, improving the visual quality.
Point gates reduce the complexity of mold structures.False
Point gates increase mold complexity due to their intricate design.
How Do Point Gates Enhance Appearance Quality?
I remember the first time I saw a perfect plastic piece. The surface was so smooth and shiny. It probably looked like an expensive car’s finish. I began to ask myself꞉ what is the secret behind such amazing quality?
Point gates lift the look of surfaces. They do this by raising the speed and heat of the flow. Surfaces become shiny and clear with almost no visible gate marks. This design choice offers great flexibility. Designers place gates in smart spots. This not only gives plastic parts a nice appearance but also keeps them strong.
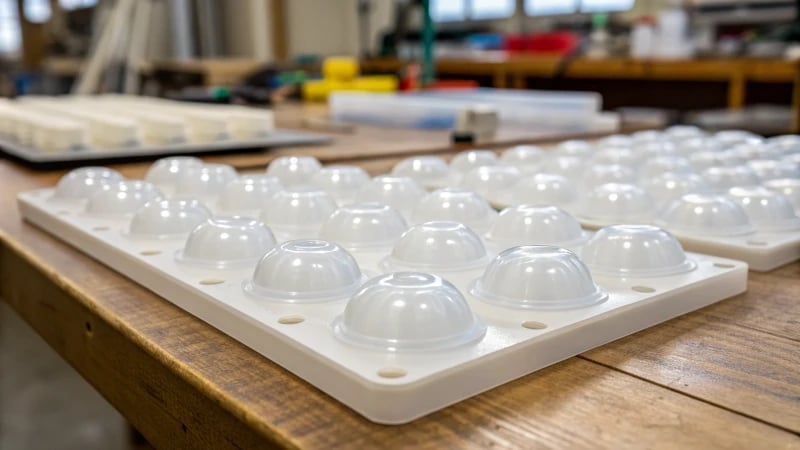
Advantages of Point Gates in Improving Looks
In my early days of designing products, it was hard to balance function and looks. Point gates changed everything for me. These small yet powerful parts, called fine water gates, have revolutionized how we get top-quality looks in molded products. When hot, liquid plastic moves through these gates, the fast flow and heat create a shiny finish. Really shiny.
Table: Key Advantages of Point Gates
Advantage | Description |
---|---|
Good appearance quality | High flow velocity increases temperature, resulting in a glossy surface. |
Flexible position selection | Allows strategic gate placement, meeting structural and design requirements. |
Easy automation | Facilitates automated production by automatic gate removal. |
One amazing quality is the almost hidden gate mark after trimming, keeping the product’s smooth appearance. This is very important for consumer electronics1 where first impressions matter a lot.
Flexible Placement for Better Design
I discovered that the flexibility of point gates changes the game. Designers position gates exactly where needed for both function and looks. They fit different shapes like barrels or boxes. This flexibility is key to creating designs that are beautiful and strong.
Moreover, removing gates automatically when the mold opens speeds up production. This saves time and reduces costs, meeting the fast pace of modern manufacturing.
Challenges and Things to Think About
Using point gates has some challenges. My team often deals with difficult mold structures that raise costs.
High flow rates can stress areas near the gate, which can crack brittle materials.
Table: Challenges Associated with Point Gates
Challenge | Description |
---|---|
Complex mold structure | Requires intricate mold designs, increasing manufacturing costs. |
Stress concentration | High flow rates cause molecular orientation, leading to potential cracking. |
Material selectivity | Not suitable for all plastics; high-viscosity materials may degrade or discolor. |
Selecting the right material is crucial to avoid issues like degradation or color changes that hurt the product’s look.
Despite these issues, point gates are still a top pick for better looks in injection molding but need careful balance with cost and material choices.
Learning their strengths and limits has allowed me to improve both how products look and work.
Point gates increase flow velocity for glossy finishes.True
Point gates enhance appearance by boosting flow velocity, raising temperature.
High flow rates from point gates can cause material cracks.True
Increased flow rates lead to stress concentration, risking cracks in brittle materials.
Why is position flexibility important in mold design?
Have you ever tried putting a square peg into a round hole? Designing a mold without flexible positions feels a bit like that.
Position flexibility in mold design offers the best gate placement. It cuts stress and lifts product quality. Designers can adjust to different structural needs easily. Also, they keep efficiency high and costs low.
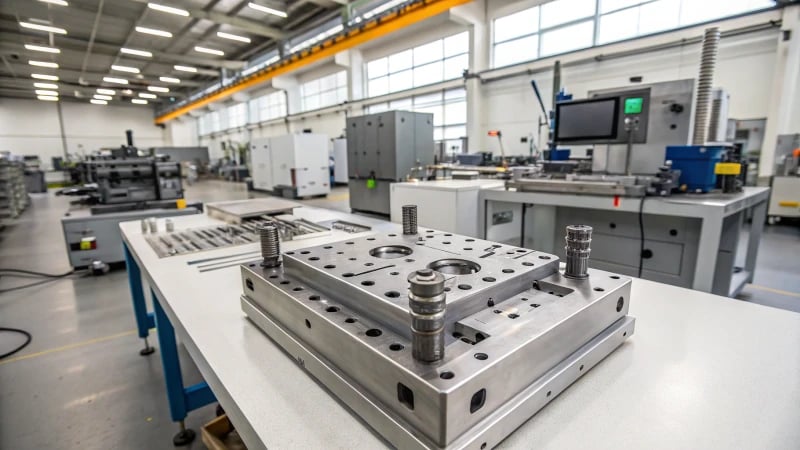
The Role of Gate Positioning
They say, "location, location, location"! Gate positioning in mold design is like that. I remember my first project and realized how much gate positioning affects quality and functionality. Flexibility in gate placement allowed me to set gates strategically, minimizing stress concentration2 and ensuring smooth and even material flow. The finish was very satisfying, like finishing a great book.
Advantages of Position Flexibility
- Design Adaptability: Fewer restrictions on gate placement felt freeing. It was like shifting from a fixed to a growth mindset. I met specific structural and aesthetic needs, even for tricky shapes like barrel-shaped3 or shell-shaped designs.
- Production Efficiency: Flexibility in positioning improved system operation. Gates were placed perfectly for easy removal after molding, reducing labor costs and speeding up the production cycle4.
Advantages | Details |
---|---|
Design Freedom | Allows diverse gate positions, adapting to various product structures and aesthetics. |
Automated Production | Simplifies automation with gates positioned for easy removal post-molding. |
Reduced Residual Stress | Optimal gate placement minimizes stress, improving dimensional accuracy and stability of products. |
Challenges and Considerations
It’s not all easy; flexibility in positioning brings challenges. Complex mold structures can raise design and manufacturing costs. More injection pressure might be needed, increasing energy use.
Overcoming Material Limitations
Materials have personalities—some react to temperature changes or high flow rates. Understanding materials’ properties is crucial to prevent degradation or discoloration.
Practical Application in Mold Design
Adding position flexibility is like learning a dance; it requires understanding both materials and design needs. Software tools helped me simulate different gate placements to find efficient configurations for my product designs5. CAD tools let me try various gate positions, focusing on less stress concentration and better material flow efficiency.
Mastering flexibility in mold design improves product quality and efficiency, leading to innovative and effective manufacturing solutions. With planning and simulation techniques such as those found in advanced software tools (simulation techniques6), the benefits outweigh the challenges.
Gate positioning affects mold quality.True
Strategic gate placement minimizes stress and ensures uniform material flow.
Position flexibility increases mold design costs.True
Complex structures for flexible positioning can raise design and manufacturing costs.
What Are the Challenges of Using Point Gates?
Understanding point gates in mold design resembles solving a tricky puzzle. Every part needs to fit just right to achieve success.
Point gates present several challenges. Mold structures become very complex. High injection pressure experiences loss. Stress concentrates in specific areas, leading to risks. Large parts do not suit point gates. Material compatibility is selective. Some materials might work; others probably will not.
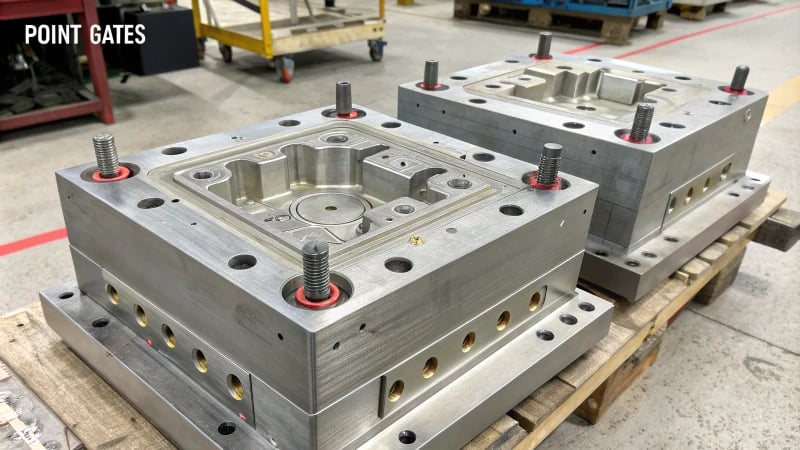
Complex Mold Structure
At first, a double-parting surface mold seemed daunting. It was like solving a tricky puzzle of design issues. With point gates, the problem grows, bringing high design expenses and maintenance troubles. Debugging turns into a long journey, slowing production.
Aspect | Challenge |
---|---|
Design | Increased cost due to complex mold |
Manufacturing | Maintenance complexity |
Debugging | Extended production cycles |
Large Injection Pressure Loss
Point gates bring challenges. The tiny gate size reduces injection pressure, causing the molding machine to work harder. Energy bills go up and equipment expenses increase in pursuit of good production.
This increases energy7 consumption and equipment costs, challenging efficient production.
Stress Concentration Risks
Handling stress concentrations causes worry. High flow rates at point gates change molecules in ways that may cause cracks, especially in brittle materials. Watching material properties8 is crucial to avoid these problems.
Unsuitability for Large Plastic Parts
Large parts do not mix well with single point gates. Warping becomes a common issue. Every project suffers when one point gate fails to cope with size, leading to a chaotic design.
Plastic Part | Challenge with Point Gates |
---|---|
Large Parts | Warping and deformation risks |
Multiple Gates Needed | Increased mold complexity |
Multiple gates become necessary but add complexity and cost.
Consider using multiple gate systems9 to balance pressure and fill cavities evenly.
Selective Material Compatibility
Picking the right material feels like choosing the perfect puzzle piece. Not all plastics survive the pressure or heat of point gates. Careful material selection prevents degrading or discoloring and keeps the final product in excellent condition.
It’s essential to select materials that maintain performance when processed through point gates10.
Point gates increase mold design costs.True
Point gates require double-parting surface molds, raising design costs.
Point gates suit all plastic materials.False
High-viscosity or heat-sensitive plastics may degrade with point gates.
When Should You Avoid Using Point Gates?
Understanding injection molding resembles putting together a puzzle with mismatched parts. Point gates sometimes give this feeling, particularly when the pressure mounts.
Point gates should be avoided for large plastic parts, high-viscosity materials or products needing minimal stress concentration. These situations may lead to increased mold complexity and costs, outweighing the benefits.
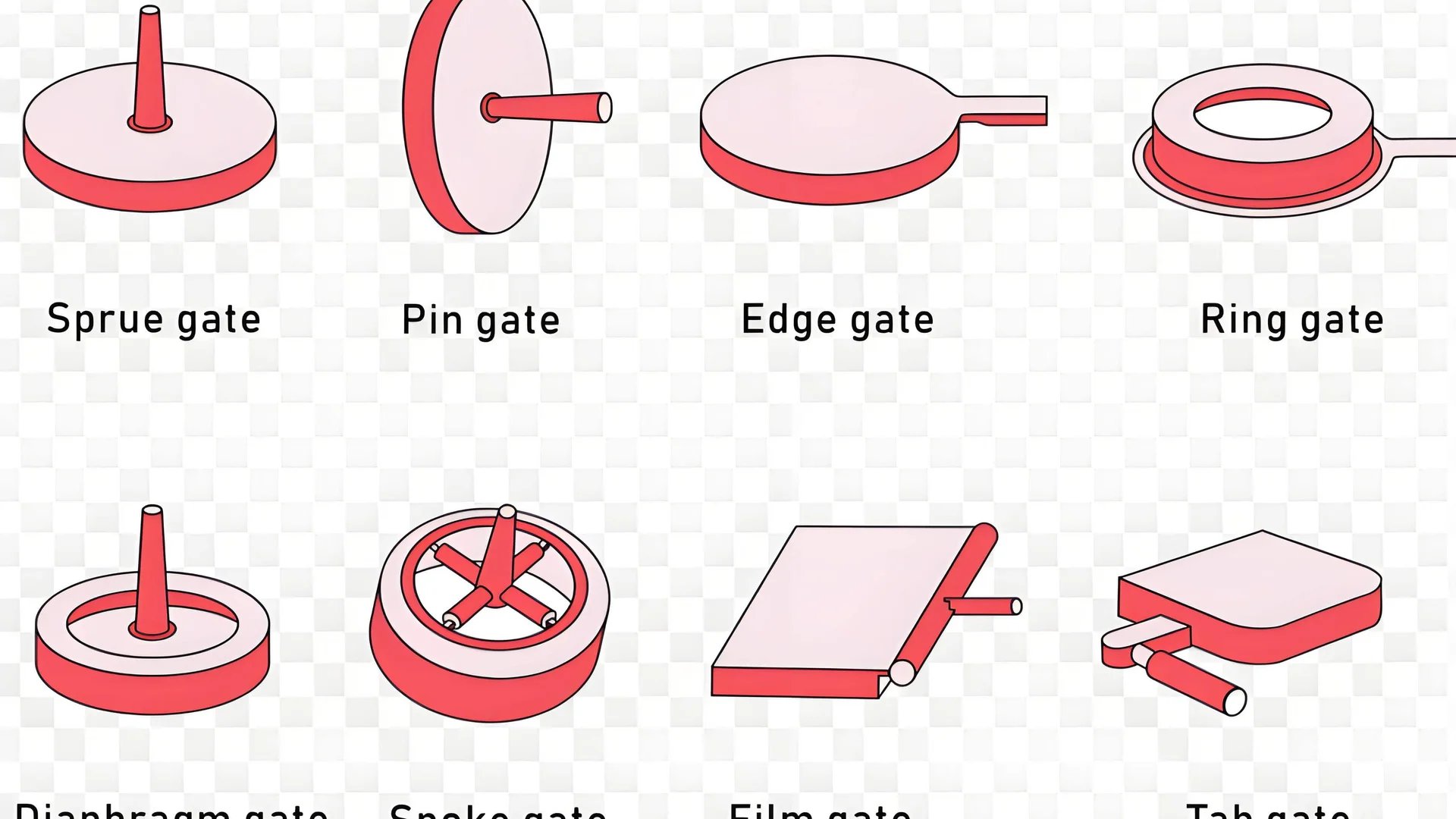
Challenges with Large Plastic Parts
I still remember my first encounter with point gates in injection molding. Excitement filled me at their possible use for both good looks and better work. But, problems hid beneath the surface, like in any good story.
Point gates work well for small items but not for big ones. I learned this the hard way when a project twisted and bent due to uneven melt distribution. Realizing multiple gates were needed was a big moment, but they made mold design harder.
Issue | Reason | Solution |
---|---|---|
Warping | Uneven melt distribution | Use multiple gates |
Increased costs | Complex mold design | Optimize gate placement |
Production delays | Debugging complexity | Simplify mold structure |
Material Limitations
Then came materials – thick or heat-sensitive plastics that seemed tricky. Imagine baking a cake with an oven that’s too hot. That’s what it’s like when these materials break down or change color at the gate. Looking at alternative gate types11 became necessary.
Stress Concentration Risks
At first, I admired point gates for reducing remaining stress. But high flow rates could twist molecules, creating local stress. Bad news for brittle plastics12 that crack at the gate—a lesson not to forget.
- Injection Pressure Loss: Smaller gate sizes increase flow resistance, causing serious injection pressure loss. This means needing a bigger machine, which isn’t cheap.
- Complex Mold Structure: Making molds with point gates often needs a double-parting surface. It complicates things, like more pieces in an already hard puzzle. This complexity could slow production and cause debugging problems.
- Material Selectivity: Not every material works with point gates. Thick plastics may resist flowing through, leading to defects or incomplete fills.
These challenges taught me that point gates are not always the right choice. It’s crucial to look at these factors carefully to meet quality without surprise costs or delays. Every project has its needs; always study your product design before picking point gates.
Point gates cause warping in large plastic parts.True
Uneven melt distribution from a single gate leads to warping.
High-viscosity plastics work well with point gates.False
High-viscosity plastics may not flow efficiently, causing defects.
Conclusion
Point gates enhance injection molding with excellent appearance and flexible positioning but pose challenges like complex mold structures, high pressure loss, and material selectivity.
-
Explore why aesthetics are crucial in consumer electronics design. ↩
-
Explore how strategic gate placement minimizes stress concentration, improving part quality. ↩
-
Discover how adaptable gate positions enhance mold designs for complex shapes. ↩
-
Understand how optimal gate placement boosts production speed and reduces costs. ↩
-
Learn about CAD tools that help find the best gate positions for mold designs. ↩
-
Gain insights into simulation methods that refine mold designs for better results. ↩
-
Learn about the relationship between injection pressure and energy usage. ↩
-
Understand how stress concentrations form and their impact on materials. ↩
-
Discover how multiple gates can enhance filling and reduce warping. ↩
-
Find out which materials perform well with point gate systems. ↩
-
Explore different gate types to find suitable alternatives that meet your material and design needs. ↩
-
Understand how stress concentration affects brittle plastics and strategies to minimize cracking. ↩