In the world of injection molding, every detail counts. One detail that often gets overlooked is the mold release angle for lifter mechanisms—an aspect that can make or break production efficiency.
The mold release angle for an injection mold lifter mechanism depends on factors like material properties, lifter travel, and mold accuracy. For flexible materials, a 3° to 5° angle may suffice, whereas rigid materials might require 5° to 10° to avoid damage.
While this brief overview gives a foundational understanding, diving deeper into specifics like buckle shape and mold precision will enhance your design efficiency and longevity. Read on to explore these critical considerations in detail.
Flexible materials require smaller mold release angles.True
Flexible materials like TPE need 3°-5° angles due to high elasticity.
- 1. What Role Do Material Properties Play in Determining Release Angles?
- 2. How Does the Shape and Depth of Buckles Affect Release Angle Calculations?
- 3. Why Is Lifter Travel Critical to Designing Mold Release Angles?
- 4. How Do Mold Precision and Structure Impact the Release Angle Required?
- 5. Conclusion
What Role Do Material Properties Play in Determining Release Angles?
The properties of materials significantly influence the design of mold release angles, impacting efficiency and product integrity.
Material properties dictate release angles by determining the elasticity, rigidity, and deformation tolerance of the molded product. Flexible materials like thermoplastic elastomers require smaller angles, while rigid ones like polystyrene need larger angles to prevent damage.
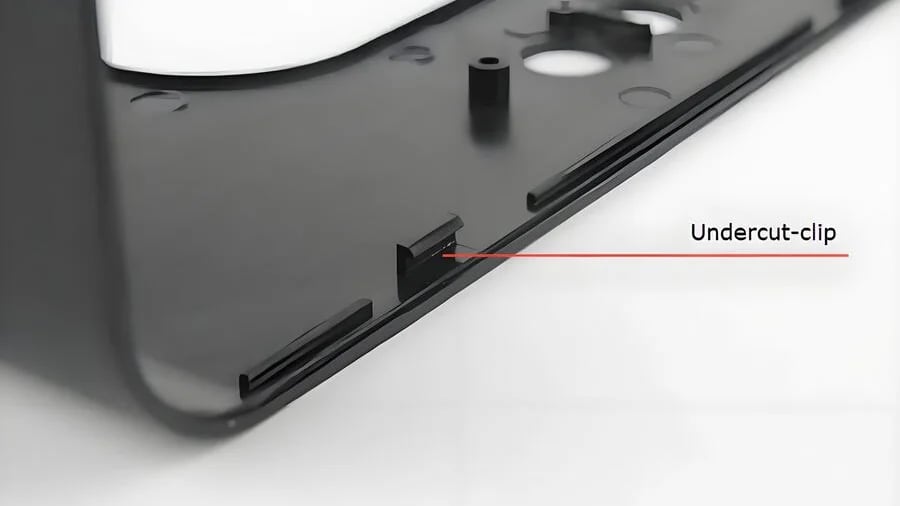
Understanding Material Properties
When designing an injection mold, choosing the right release angle is crucial for both functionality and longevity. Different materials exhibit unique characteristics that affect how they can be safely and efficiently demolded.
Elasticity vs. Rigidity
Consider the elasticity of thermoplastic elastomers1 (TPEs). Known for their high flexibility, TPEs can endure significant deformations without breaking. This means that a demolding angle of 3° to 5° is often sufficient. Conversely, materials like polystyrene2, known for their rigidity, require larger angles between 5° and 10° to reduce stress and prevent rupture during the release process.
Material Type | Typical Release Angle |
---|---|
Thermoplastic Elastomer (TPE) | 3° – 5° |
Polystyrene (PS) | 5° – 10° |
Impact of Material Deformation
The degree to which a material can deform under stress also influences the release angle. Materials with higher deformation tolerance allow for smaller angles because they can easily adapt to the lifter’s movement. In contrast, materials with low deformation tolerance require larger angles to avoid damage.
Case Studies: Practical Applications
In practice, these principles translate to various applications across industries. For example, in automotive manufacturing, where plastic parts3 need to withstand different environmental conditions, selecting the right material and corresponding release angle ensures durability and safety.
Example: Automotive Components
- Flexible Bumpers: Typically made from TPE due to its resilience, these components can be efficiently demolded with minimal angles.
- Dashboard Components: Often use rigid materials requiring careful consideration of larger angles to prevent cracking or splitting during demolding.
By considering these factors, manufacturers can optimize their processes, reducing waste and increasing efficiency in production. Understanding the material properties is not just about selecting an angle—it’s about ensuring the quality and performance of the final product.
TPEs require release angles of 3° to 5°.True
TPEs are flexible, allowing smaller angles for efficient demolding.
Polystyrene needs release angles larger than 10°.False
Polystyrene requires angles between 5° and 10° to prevent damage.
How Does the Shape and Depth of Buckles Affect Release Angle Calculations?
Buckle design is a pivotal factor in determining the release angle in injection molding, influencing efficiency and product integrity.
Buckle shape and depth significantly influence release angle calculations. Shallow, simple buckles allow for smaller angles (3°-5°), while deeper or complex designs require increased angles (7°-10°) to ensure smooth lifter release and prevent damage.
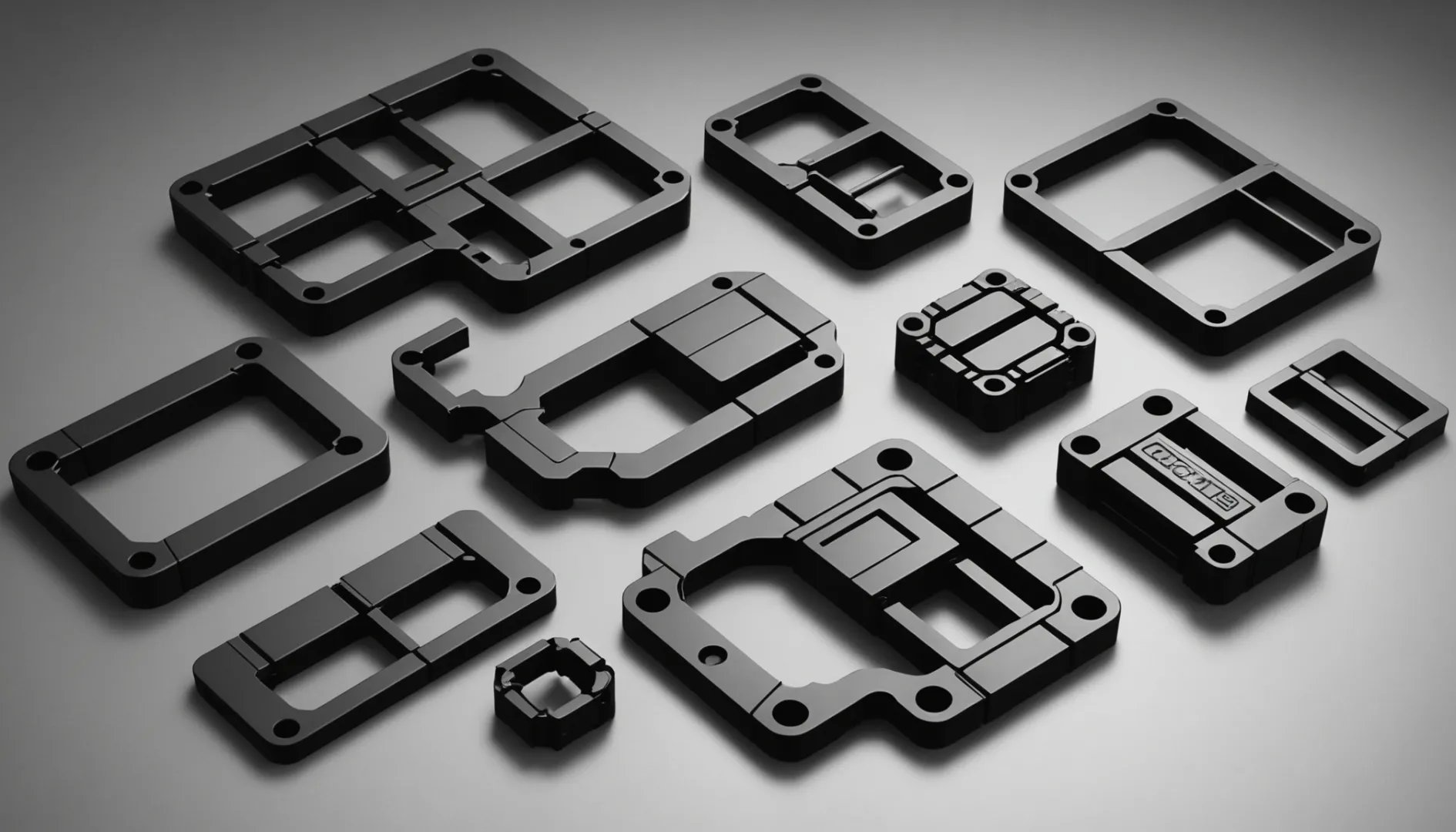
Understanding Buckle Dynamics
The intricacies of buckle design, including its shape and depth, play a significant role in the performance of injection molding processes. These factors directly impact the calculation of release angles, which are critical to ensuring that lifters can disengage from molded parts without causing damage.
Influence of Buckle Shape
Buckle shapes can range from simple geometries like circles and squares to more complex forms with curves and slopes. The complexity of a buckle shape often dictates the required release angle:
- Simple Shapes: For basic round or square buckles, a smaller release angle is usually sufficient. This is because there is less risk of interference during the lifter’s movement.
- Complex Shapes: Curved or irregularly shaped buckles necessitate larger release angles. The increased angle prevents the lifter from catching on the contour during extraction, thus avoiding potential damage.
For instance, while a round buckle might only need a release angle of 3°-5°, an intricate design could require 6°-10°.
The Impact of Buckle Depth
The depth of a buckle also greatly affects the necessary release angle. As the depth increases, so does the potential for resistance during the demolding process.
Buckle Depth | Recommended Release Angle |
---|---|
0.5 – 1mm | 3° – 5° |
2 – 3mm | 7° – 10° |
Shallow buckles allow for smoother lifter operation with lower angles, whereas deeper buckles require increased angles to facilitate effective release.
Case Study: Combining Shape and Depth
Consider a scenario where a mold features a deeply set, curved buckle. The depth alone might suggest an increased release angle, while the complex shape further supports this need. By increasing the angle to perhaps 8° or even 10°, one can mitigate risks associated with high resistance and potential part damage.
Real-World Application: Balancing Shape and Material Properties
While shape and depth are crucial, they must be considered alongside material properties. For example, thermoplastic elastomer (TPE) materials4 with their high elasticity might accommodate slightly smaller angles even with complex buckles, whereas polystyrene (PS)5 would require larger angles due to its rigidity.
Understanding these interactions is essential for optimizing injection mold designs, ensuring efficient production and quality results.
Simple buckles need a release angle of 7°-10°.False
Simple buckles require smaller angles, typically 3°-5°, not 7°-10°.
Deeper buckles increase necessary release angles.True
Increased depth requires larger angles to prevent demolding resistance.
Why Is Lifter Travel Critical to Designing Mold Release Angles?
Understanding the significance of lifter travel in determining mold release angles is pivotal for efficient and effective injection molding.
Lifter travel dictates the necessary mold release angle to minimize resistance and ensure smooth demolding. Shorter travel allows smaller angles (3°-6°), while longer travel requires larger angles (7°-10°) to counteract cumulative resistance.
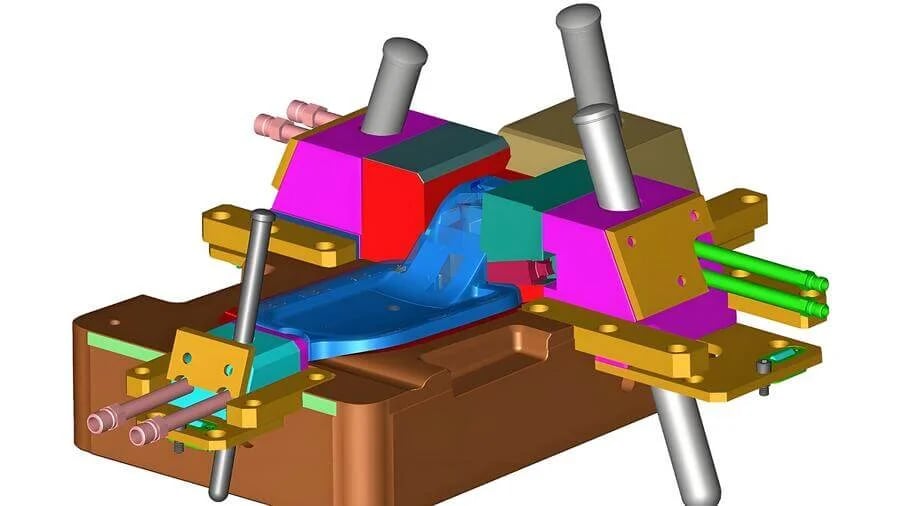
The Relationship Between Lifter Travel and Resistance
In the design of injection molds, the travel of the lifter is a fundamental aspect that influences the choice of release angle. The term "lifter travel" refers to the distance the lifter moves from its initial position until it is completely clear of the molded product. This movement is crucial because, as the lifter travels, it experiences resistance, which can increase with longer strokes.
When a lifter has a short travel distance, typically between 5 – 10mm, the release angle required can be relatively small, around 3° – 6°. This is because the shorter travel minimizes the resistance encountered by the lifter during demolding. However, if the lifter’s travel exceeds 15mm, a larger release angle, usually between 7° – 10°, becomes necessary. This adjustment compensates for the pronounced cumulative resistance that occurs over a longer stroke.
Examples and Practical Considerations
Consider a scenario where a lifter with a travel of 8mm is used in a mold for a product made from thermoplastic elastomer (TPE). Given TPE’s elasticity and the short lifter travel, a release angle of 4° could be sufficient. However, if the same mold uses polystyrene (PS), which is more rigid and has a longer lifter travel of 20mm, a larger angle of 9° might be required to prevent damage during release.
Lifter Travel | Recommended Release Angle for TPE | Recommended Release Angle for PS |
---|---|---|
5-10mm | 3°-5° | 5°-7° |
>15mm | 6°-8° | 7°-10° |
Effects on Mold Longevity and Efficiency
Appropriately adjusting the release angle based on lifter travel not only aids in seamless product release but also enhances mold longevity and operational efficiency. Using optimal release angles6 reduces wear on the mold components, minimizing maintenance needs and extending the mold’s service life. Additionally, ensuring smooth demolding decreases cycle times and improves production throughput.
Understanding these dynamics allows designers to tailor their mold designs more precisely to specific production requirements, enhancing both product quality and manufacturing efficiency.
Shorter lifter travel requires smaller release angles.True
Shorter travel minimizes resistance, allowing for smaller release angles.
Longer lifter travel reduces mold resistance.False
Longer travel increases resistance, necessitating larger release angles.
How Do Mold Precision and Structure Impact the Release Angle Required?
Precision in mold design significantly influences the release angle required for smooth demolding.
Mold precision affects the release angle; high precision allows for smaller angles, while lower precision necessitates larger angles to prevent interference.
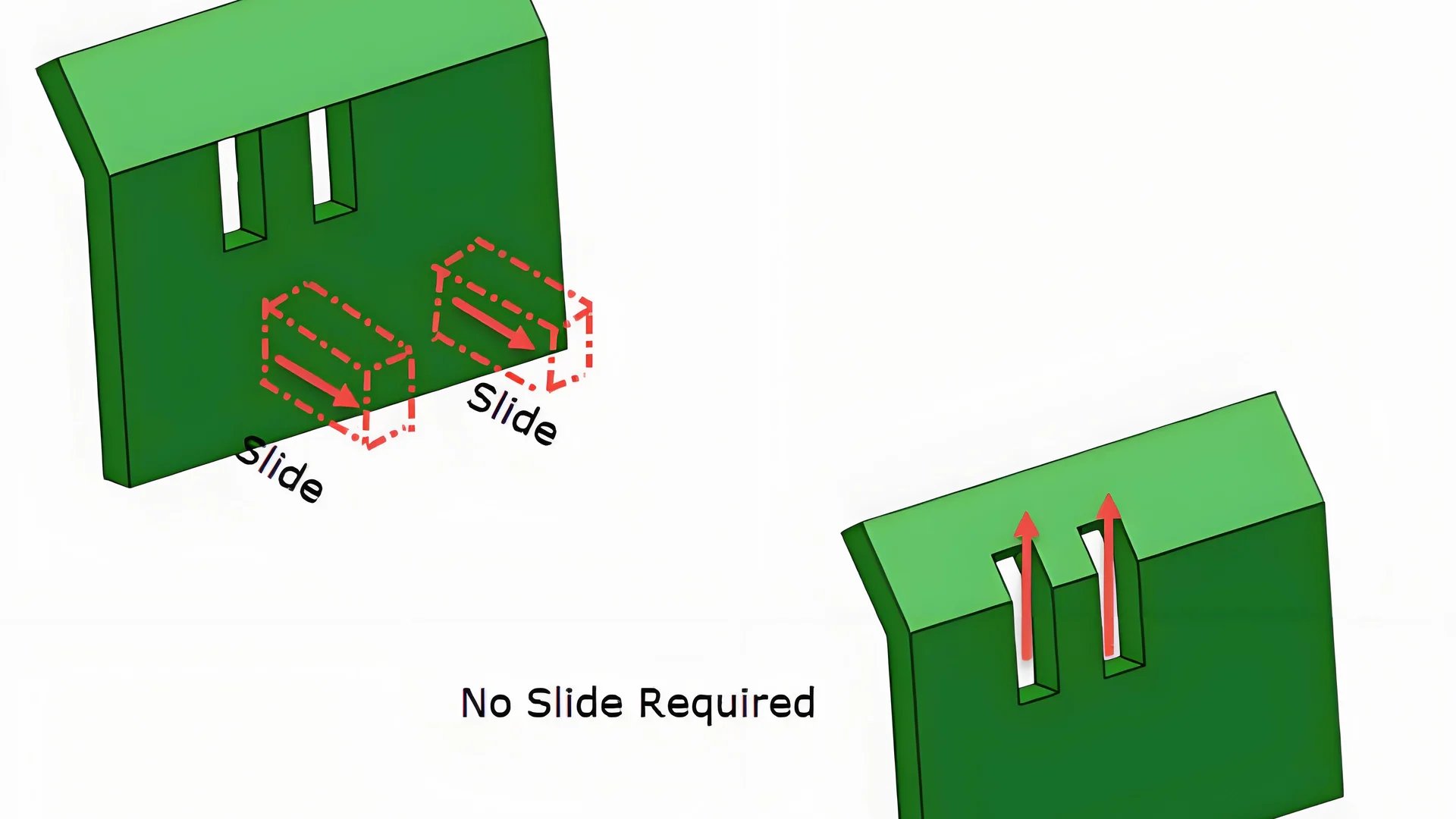
Precision in Mold Design
The precision of a mold plays a pivotal role in determining the required release angle for the lifter mechanism. In high-precision molds, the alignment and movement accuracy of the lifter are paramount. For instance, in precision injection molds with machining accuracy reaching ±0.01mm, the demolding angle can be as low as 4° – 6°, ensuring smooth and effective release. This is because precise molds allow for tighter control over tolerances, reducing the likelihood of interference during the lifter’s operation.
Conversely, when mold precision is low—say around ±0.05mm—there is an increased risk of misalignment and interference between the lifter and other mold components. In such cases, a larger release angle, typically between 6° – 10°, is necessary to compensate for these inaccuracies and to facilitate a smoother release process.
Influence of Mold Structure
The structure of the mold itself, including its overall design and complexity, also significantly influences the required release angle. A well-structured mold ensures that all parts function harmoniously, thereby minimizing friction and wear during lifter movement. For instance, molds with complex internal structures may require larger release angles to prevent the lifter from obstructing or damaging intricate features during ejection.
To illustrate this, consider molds that include multiple internal undercuts or intricate geometrical designs. Such designs may necessitate a meticulous approach to determining the optimal release angle, often requiring extensive simulations and tests7 to ensure that all components interact smoothly without causing damage.
Balancing Precision and Functionality
Achieving a balance between mold precision and functionality is crucial for efficient mold design. High-precision molds tend to be more expensive due to advanced machining requirements; however, they offer benefits such as reduced cycle times and lower maintenance costs over their lifespan. On the other hand, while less precise molds might be cheaper initially, they often require larger release angles and can result in increased wear on lifter mechanisms over time.
By carefully considering both the precision8 and structural aspects of a mold, designers can optimize the release angle for specific applications, enhancing both the performance and longevity of the injection molding process.
High-precision molds require smaller release angles.True
High precision allows tighter tolerance control, reducing interference.
Complex mold structures need smaller release angles.False
Complex structures often require larger angles to avoid obstructions.
Conclusion
By understanding the intricacies of mold release angles, you can optimize lifter designs for smoother operations and longer lifespan. Keep these factors in mind to enhance your injection molding processes effectively.
-
Learn how TPE’s flexibility affects mold release angles.: The ability to be stretched to moderate elongations. Upon the removal of stress, return to something close to its original shape. ↩
-
Understand why polystyrene needs larger release angles.: Polystyrene is a type of polymer that is transparent, rigid, brittle, and moderately strong in its unmodified state. It is a plastic made by … ↩
-
Discover why material choice is vital for car parts.: Because of its durability and chemical resistance, polypropylene is used in everything from bumpers to cable insulation to carpet fibers. ↩
-
Explore TPE’s unique elasticity that allows smaller release angles.: Explore different chemistries of thermoplastic elastomers (TPE materials) along with their uses, structure, types, properties and end-use applications. ↩
-
Learn why PS requires larger angles due to its brittle nature.: Polystyrene Properties and Mechanical Specifications · Ultimate tensile strength: 28 MPa · Elongation at break: 55% · Flexural modulus: 1930 MPa … ↩
-
Discover why choosing optimal release angles improves mold longevity and efficiency.: 1) A draft angle of 1½ to 2 degrees is required for most parts. This rule of thumb applies to parts with mold depths of up to 2 inches. At this size, draft as … ↩
-
Learn how simulations ensure optimal release angles in complex molds.: The vast majority of molds must work within a certain set of parameters that must be considered when running a proper simulation. In the case of … ↩
-
Discover why investing in high-precision molds can be cost-effective long-term.: Another advantage of high-precision plastic injection molding is that it can make components with a high level of detail and accuracy. These parts can be exact. ↩