I first explored injection molding and found wonder in adjusting small aspects like injection speed. Achieving excellent product quality depends on these adjustments. Small changes hold great importance.
To improve impact strength in injection molding, I adjust the injection speed. I consider material properties, mold structure and specific product needs. Crystalline plastics need moderate speed for good crystallization. Non-crystalline plastics need careful speed control. This reduces internal stress. Gate design changes and runner systems also affect speed adjustments.
These first changes are important for improving strength. Understanding material behavior and mold design is key. Join me as I share more tips for different materials and products. This helps your molding work fit the goal every time.
Moderate speed aids crystallization in crystalline plastics.True
Crystalline plastics benefit from moderate speeds to allow proper crystallization.
Non-crystalline plastics require high injection speeds.False
Non-crystalline plastics need controlled speeds to minimize internal stress.
How Do Material Properties Affect Injection Speed?
Do you ever think about how materials’ characteristics influence injection speed in molding? This knowledge changes everything for quality and efficiency.
Material traits like thickness, crystal structure and heat flow greatly affect injection speed. Changing speed based on these traits helps achieve top molding quality. This adjustment stops problems like surfaces not filled all the way and stress lines.
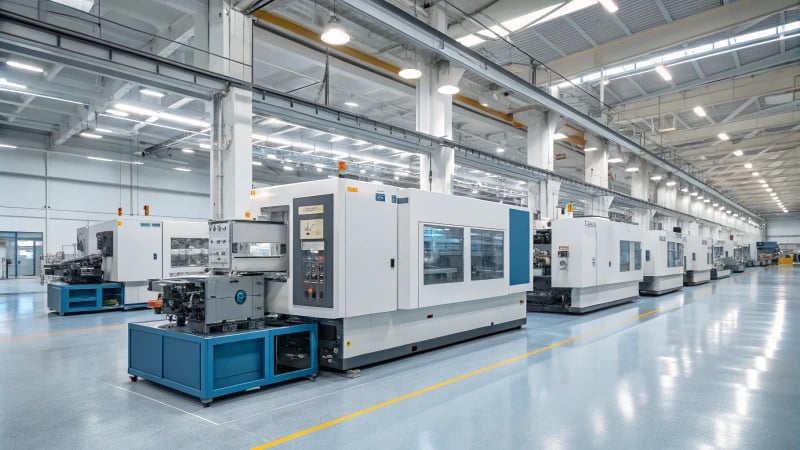
Understanding Material Viscosity
Viscosity plays a key role in molding. Think about pouring honey versus water – honey’s thickness needs a slow pour. In the same way, thick materials such as PVC1 need slow injection speeds to fill spaces correctly. It’s like dancing and finding the right pace. Rush and you stumble.
Crystalline vs. Non-crystalline Plastics
Crystalline Plastics: Look at polypropylene. It works well at speeds of 100-150 mm/s. Hitting this speed lets crystallization happen perfectly. Speeding up too much is like rushing a cake from the oven; it doesn’t set properly.
Non-crystalline Plastics: These, like polycarbonate, need a softer touch. Medium speeds of 50-100 mm/s suit them, reducing internal stress.
Thermal Conductivity and Injection Speed
Thermal conductivity also holds importance. Materials losing heat quickly can manage higher speeds. It’s like cooling off after exercise – some people do it easily!
Influence of Mold Structure
The mold’s shape matters too. Big gates welcome fast speeds, much like open doors at a party. Small gates call for a careful pace to avoid problems.
Balancing Product Requirements
Aesthetic products require moderate speed to dodge surface flaws. I’ve noticed that even tiny surface changes can be eye-openers in achieving the right mix of beauty and strength.
Understanding these factors goes beyond technical accuracy; it’s about creating something lovely and strong. Knowing materials as well as friends helps predict reactions and adjust for lasting products.
Injection Speed Table for Common Materials
Material | Recommended Speed (mm/s) |
---|---|
Polypropylene | 100-150 |
Polycarbonate | 50-100 |
High-density PE | 80-120 |
Polyoxymethylene | 60-110 |
High-viscosity materials require slower injection speeds.True
High viscosity increases resistance to flow, necessitating slower speeds.
Non-crystalline plastics require faster injection speeds than crystalline.False
Non-crystalline plastics benefit from moderate speeds for uniform filling.
How Does Mold Structure Influence Injection Speed Adjustments?
Did you ever stop to think about how a mold’s complex design controls the speed of material injection? It’s not only a technical detail. This is the key to creating an ideal product.
The mold’s structure is very important. Gate design and runner system strongly influence the injection speed. They form flow dynamics and heat transfer, which are very important for product quality. Product quality very much depends on these factors.
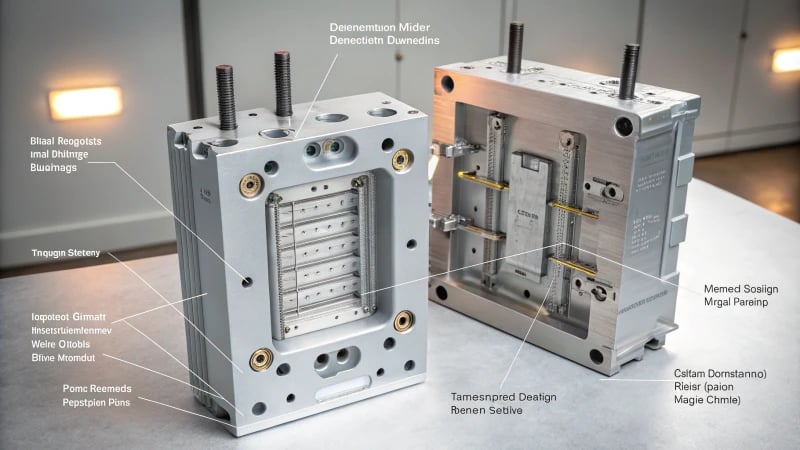
Understanding Mold Structure
When I started exploring molds, I didn’t know how much their structure affects everything – from injection speed to product quality. It’s like baking a cake; if the oven heat isn’t correct, your cake could be undercooked or burned.
Gate Design and Its Impact
The gate acts like a front door to your mold’s home. A larger gate, much like a wide entrance, allows quicker injection speeds, around 120-200 mm/s. I once worked with a big side gate for large plastic containers, where speed was crucial to avoid problems like melt spray. Smaller gates, like pinpoint ones, feel like narrow doorways where you must slow down (30-80 mm/s) to prevent issues.
Gate Type | Injection Speed (mm/s) |
---|---|
Large | 120-200 |
Small | 30-80 |
Explore more on gate design2.
Runner System Considerations
Runner systems resemble different highways. A hot runner system is like driving fast on a smooth freeway at 100 to 300 mm/s with little resistance. A cold runner system, with its bends, requires slower speeds (40-120 mm/s) to prevent losing control or overheating. Switching from a hot to cold system once taught me to adjust speeds carefully.
Learn more about runner systems3.
Material Properties and Injection Speed
The material type adds another layer to this complex puzzle. Crystalline plastics like polypropylene need controlled speeds (100-150 mm/s) for proper crystallization. I remember trying PP and seeing how the correct speed affected strength and finish. Non-crystalline plastics such as polycarbonate need moderate speeds (50-100 mm/s) to avoid internal stress.
Discover more about material properties4.
Product Requirements Influence
Each product presents its own demands. For high-quality appearance products, finding the right speed (50-150 mm/s) is crucial to keep the surface smooth. On thick-walled items, I had to adjust speeds (80-180 mm/s) to fill them correctly without stressing the material.
Understand more about product requirements5.
Large gates allow faster injection speeds.True
Large gates support speeds between 120-200 mm/s, enabling fast injection.
Cold runner systems handle higher injection speeds.False
Cold runner systems need slower speeds (40-120 mm/s) due to friction.
Why is Injection Speed Crucial for High-Quality Product Surfaces?
Picture achieving a flawless finish on a product’s surface. Everything depends on the gentle balance of injection speed.
Injection speed matters a lot in molding. It changes how plastics crystallize and lowers internal stress. The speed also affects how the surface of the product looks. Correct adjustment creates defect-free finishes. Very high quality.
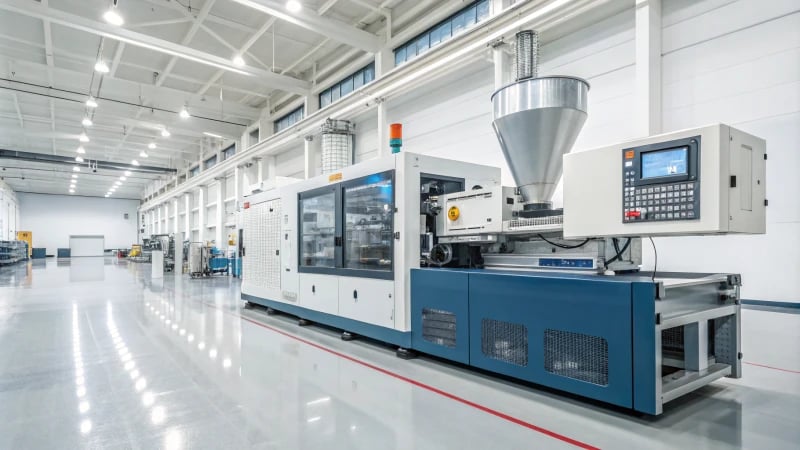
Understanding Material Properties
Injection speed must be adapted based on the material’s nature. For instance, crystalline plastics like polypropylene (PP) require a controlled speed to ensure optimal crystallization. Typically, PP‘s injection speed should be between 100-150 mm/s. This range allows adequate crystallization, which enhances the impact strength6.
In contrast, non-crystalline plastics such as polycarbonate (PC) need a different approach. Here, the aim is smooth cavity filling and minimal internal stress. PC should generally be injected at speeds between 50-100 mm/s. This helps avoid stress concentration and pores, maintaining impact strength.
Mold Structure Considerations
The mold’s structure plays a significant role in determining suitable injection speeds.
- Gate Design: Large gates can handle faster speeds (120-200 mm/s). However, pinpoint gates need slower speeds (30-80 mm/s) to avoid spraying and structural disorders.
- Runner System: In hot runner systems with large diameters and smooth surfaces, higher speeds (100-300 mm/s) are manageable due to reduced flow resistance. Cold runner systems require lower speeds (40-120 mm/s) to minimize pressure loss.
Product Requirements and Adjustments
The injection speed should also reflect the product’s intended use and appearance requirements:
Product Type | Recommended Speed (mm/s) |
---|---|
High appearance quality | 50-150 |
Large or thick-walled | 80-180 |
For products demanding superior surface quality, such as automotive parts, moderate speeds ensure a smooth finish without flow marks or silver streaks.
For large or thick-walled items, speeds must prevent insufficient filling while avoiding excessive internal stress. Using non-destructive testing7, designers can adjust speeds to achieve dense internal structures free from pores.
Understanding these dynamics helps designers optimize injection speeds for high-quality surfaces in consumer electronics, ensuring both aesthetic appeal and structural integrity. By considering material properties8, mold design, and product requirements, manufacturing outcomes can be enhanced effectively.
Crystalline plastics need injection speed of 100-150 mm/s.True
This speed range ensures optimal crystallization for impact strength.
Non-crystalline plastics should be injected at 120-180 mm/s.False
PC requires 50-100 mm/s to avoid stress and maintain quality.
What Special Considerations are Needed for Large or Thick-Walled Products?
Ever tried shaping a large plastic piece and found it didn’t fully meet your hopes?
When creating big or thick products, designers adjust material properties, mold shape and how fast injection happens. This action is important for both strength and beauty. This approach reduces stress inside the product. Quality improves greatly.
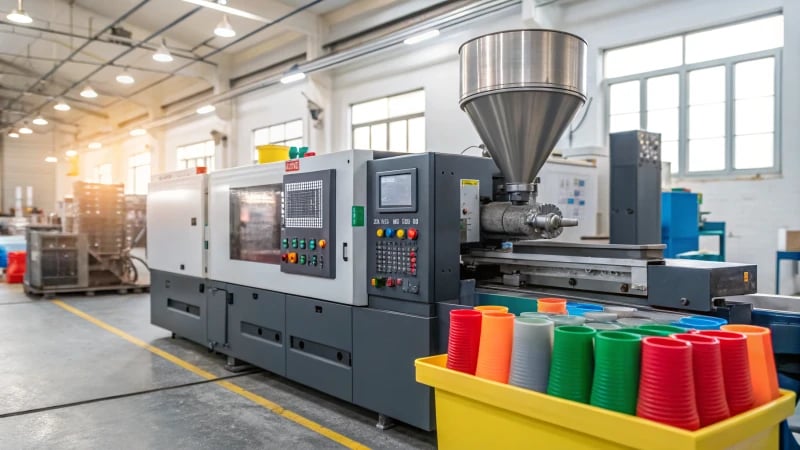
Material Properties and Injection Speed
I recall my early days in the industry facing crystalline plastics, such as polypropylene (PP). Adjusting the injection speed was challenging. PP needs a speed of 100-150 mm/s to build a strong crystalline structure. Going too fast disrupts crystallization. My first batch turned weak and uneven. But with practice, my molds became perfect!
Non-crystalline plastics, like polycarbonate (PC), demand patience and accuracy. These need a steady flow at 50-100 mm/s to fill molds without stress. My initial try was a mistake, but it taught me valuable lessons in molding’s art. Patience and precision really matter.
Plastic Type | Ideal Injection Speed | Potential Issues |
---|---|---|
Crystalline (PP) | 100-150 mm/s | Disrupted crystallization9 |
Non-crystalline (PC) | 50-100 mm/s | Increased internal stress |
Mold Structure Adjustments
Mold design is crucial. Large gates allow faster speed, 120-200 mm/s, for quick and smooth filling. Once, I forgot to adjust for a tiny gate. The result was a fragile product. This experience showed me the need to slow down to 30-80 mm/s for smaller gates.
Hot runner systems allow speeds of 100-300 mm/s because of lower resistance. Switching to a cold runner system surprised me with pressure losses10. My approach had to change.
Product-Specific Requirements
Thick-walled products need the right speed to avoid problems. Speeds of 80-180 mm/s achieve the best outcome. A client once disliked porous trash bin walls. Careful speed changes and testing solved it.
High-quality finishes, like in car interiors, need moderate speeds for smoothness. I spent many hours examining products under different lights for perfect results. Flawless finishing was really my goal.
These details strengthen large or thick-walled products, meeting functional and aesthetic standards. Thoughtful design helps expert designers like Jacky11 find the right balance.
Crystalline plastics need injection speeds over 200 mm/s.False
Speeds over 200 mm/s disrupt crystallization in crystalline plastics.
Hot runner systems allow speeds up to 300 mm/s.True
Hot runner systems reduce flow resistance, permitting higher speeds.
Conclusion
Adjusting injection speed in molding enhances impact strength by considering material properties, mold design, and product requirements, ensuring optimal crystallization and reduced internal stress for quality outcomes.
-
Learn how varying viscosity levels impact the flow and filling of materials during injection molding processes. ↩
-
Learn how different gate designs influence optimal injection speeds and product quality. ↩
-
Understand the differences between hot and cold runner systems and their impact on injection speed. ↩
-
Discover why material characteristics are crucial for setting the right injection speed. ↩
-
Explore how specific product needs dictate the best injection speed choices. ↩
-
Explore how controlled injection speeds influence polypropylene’s crystallization and impact strength. ↩
-
Learn about techniques to assess internal structures without damaging products. ↩
-
Discover how different material properties dictate the necessary injection speed for quality surfaces. ↩
-
Gain deeper insights into how crystallization affects material properties during injection molding. ↩
-
Understand how pressure losses in runner systems impact injection molding efficiency. ↩
-
Explore comprehensive guidelines on designing thick-walled products using injection molding techniques. ↩