Imagine if you could elevate your mold making process with technology that makes every step smoother and more efficient.
3D printing revolutionizes mold making by reducing costs, enhancing efficiency, and providing design flexibility, enabling faster, more precise mold creation, improving product quality, and accelerating time to market.
I remember the first time I saw a 3D printer in action—it was like witnessing the future unfold right in front of me. The precision, the speed, and the sheer creativity it allowed were nothing short of mind-blowing. For someone like me, who’s been knee-deep in the mold industry for years, the potential benefits were immediately clear. But what about those hidden perks and strategies that can take this technology to the next level? Let’s explore how 3D printing can truly transform our processes, sharing stories from real-world applications that are setting the bar in our industry.
3D printing reduces mold making costs by 50%.False
While 3D printing reduces costs, the exact percentage varies widely.
Complex molds are created faster with 3D printing.True
3D printing allows for quicker prototyping and production of intricate designs.
- 1. How Does 3D Printing Revolutionize Mold Making?
- 2. How Can 3D Printing Help Save Costs in Mold Production?
- 3. Can 3D Printing Improve Design Flexibility for Complex Molds?
- 4. How Does 3D Printing Revolutionize Mold Making Efficiency?
- 5. How Are Industries Adapting to 3D Printed Molds?
- 6. What Challenges Should You Consider When Implementing 3D Printing in Mold Making?
- 7. Conclusion
How Does 3D Printing Revolutionize Mold Making?
I remember the first time I saw a 3D printer in action—it was like witnessing magic! The way it transformed a digital design into a tangible object was mesmerizing, especially in the world of mold making.
3D printing revolutionizes mold making by offering design flexibility, cost efficiency, and rapid production, enabling intricate designs and quick iterations for a more efficient and innovative manufacturing process.
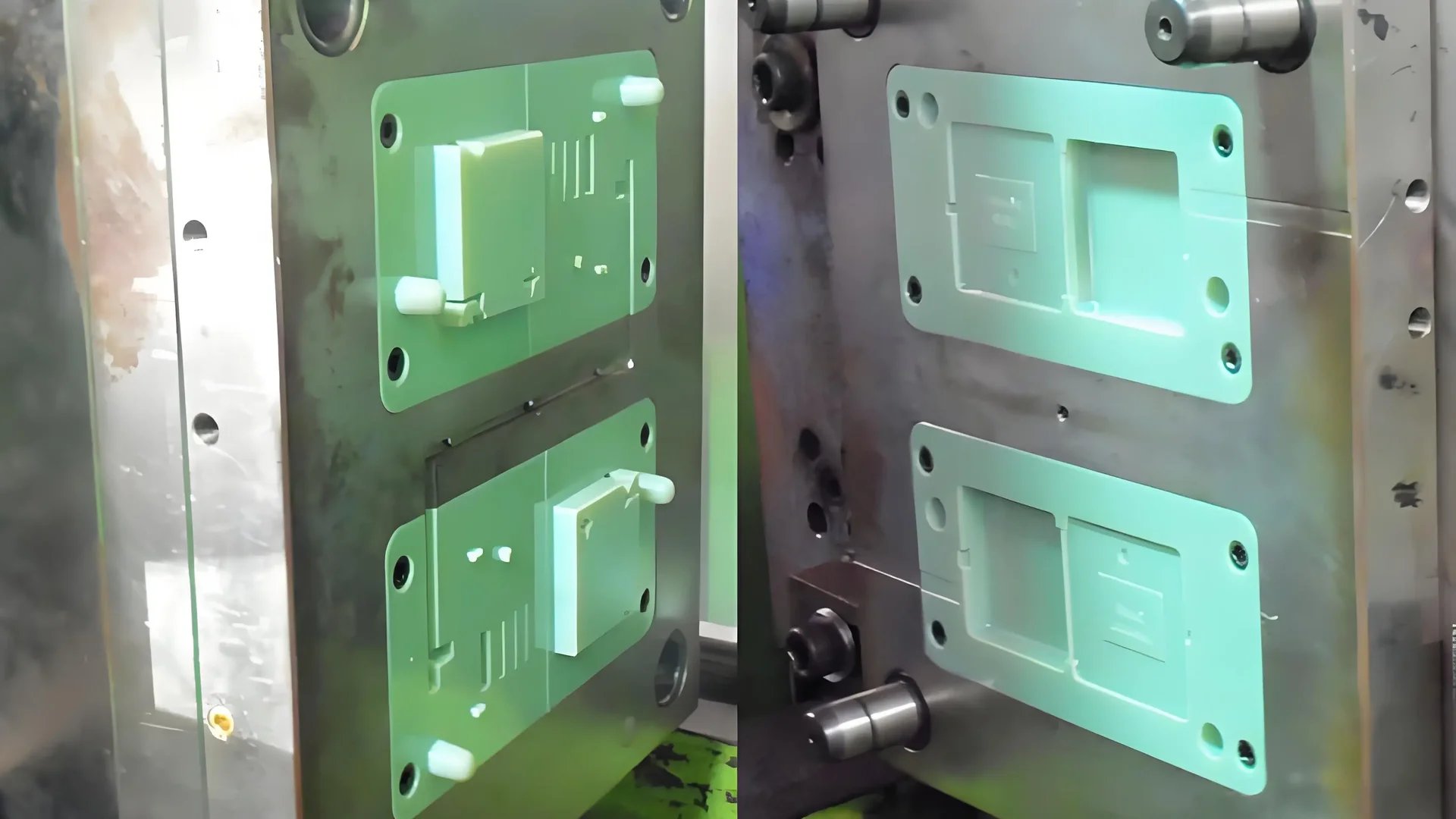
Enhanced Design Flexibility
I can still recall the challenges I faced with traditional mold making—the constraints on design were often frustrating. With 3D printing, however, those limitations seem to melt away. Suddenly, I could explore complex geometries and innovative structures without worrying about skyrocketing costs or time-consuming processes. This technology allows me to be more daring and creative in my designs. For instance, I once had an idea for an intricate pattern that seemed impossible with conventional methods. But with 3D printing, I could bring that vision to life effortlessly.
Cost Efficiency
When I started incorporating 3D printing into my work, one of the biggest revelations was how much more cost-effective it was. The traditional methods often left me staring at piles of wasted materials, not to mention the manual labor involved. Now, with 3D printing, I use only the material that’s necessary. It’s like a breath of fresh air for my budget! Plus, the reduction in manual work means I can focus my energy on refining designs and pushing creative boundaries.
Traditional Molds | 3D Printed Molds |
---|---|
High material waste | Minimal waste |
Labor-intensive | Automated processes |
Speed of Production
The speed of production is another game-changer I’ve experienced firsthand. In the past, waiting weeks—or even months—for prototypes was just part of the job. But now, with 3D printing1, I can have a prototype ready within days. This rapid turnaround has allowed me to iterate more frequently and fine-tune my designs in real-time. It’s like having a secret weapon that keeps me ahead of the competition.
Ability to Customize and Innovate
Customization has always been a crucial aspect of what I do. With 3D printing2, tailoring designs to specific customer needs or adapting to market trends becomes so much easier. I can experiment with new materials and techniques without having to start from scratch each time. It’s incredibly empowering and has opened up a whole new world of possibilities for innovation.
Exploring these benefits further has truly transformed my approach to mold making, enabling me to stay competitive and embrace new challenges head-on. For more insights on design flexibility3 and other advantages, there are plenty of resources available online.
3D printing in mold making reduces material waste.True
3D printing uses only necessary materials, minimizing wastage.
Traditional molds allow for more intricate designs than 3D printing.False
3D printing offers greater design flexibility for complex geometries.
How Can 3D Printing Help Save Costs in Mold Production?
Picture yourself slashing mold production expenses by a whopping 70%. With 3D printing, this isn’t just a dream—it’s a reality!
3D printing reduces mold production costs through eliminating traditional tooling, minimizing material waste, and accelerating prototyping, thereby streamlining operations and cutting labor and material expenses.
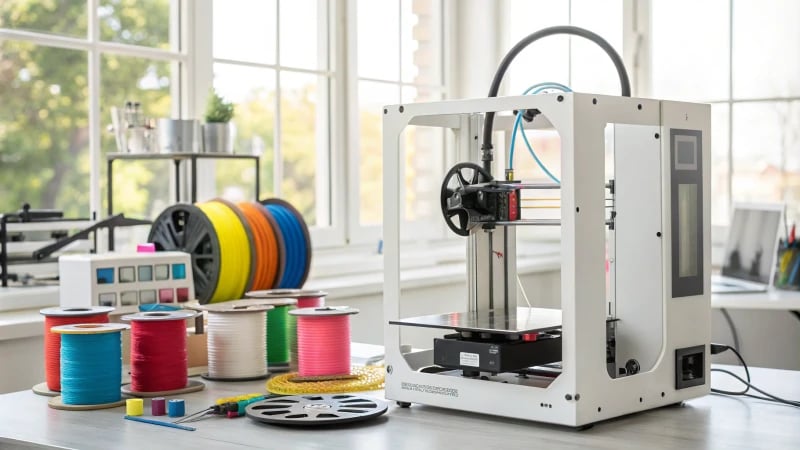
Cost Savings through Reduced Tooling
I remember when I first got into mold design, waiting weeks for custom tooling to be made. It was not only costly but painfully slow. Now, thanks to 3D printing4, I can skip those long wait times. We produce molds directly without the need for expensive and specialized tooling. It’s like fast-forwarding the process and saving a hefty chunk of change in the process!
Material Efficiency
In the early days of my career, I cringed at the amount of material wasted using traditional methods—watching heaps of it turn into scrap. But with 3D printing, it’s like having a craftsperson who uses just the right amount of clay to sculpt a masterpiece. The additive process builds molds layer by layer, significantly reducing waste.
Method | Waste Produced |
---|---|
Traditional | High |
3D Printing | Low |
Rapid Prototyping
Rapid prototyping with 3D printing is like having a magic wand. I can test and tweak designs in real-time, refining them until they’re just right. This agility not only saves time but trims down costs in product development cycles5. It’s like being able to press ‘undo’ on design mistakes without losing precious time or money.
Simplifying Complex Designs
I’ve always loved pushing the boundaries of design complexity. 3D printing lets me do just that—creating intricate geometries that would be impossible with conventional methods. This means fewer components and assemblies, which ultimately means lower production costs. Plus, it’s satisfying to know I can innovate without the looming shadow of budget constraints.
Labor Reduction
Back when I started, I spent countless hours on repetitive tasks that drained creativity. But now, with 3D printing, the streamlined workflow means less reliance on skilled labor for mundane jobs. This gives me more time to focus on what I love most: innovating and creating.
Flexibility in Production
The flexibility 3D printing offers is like having a tailor on standby to make alterations without charging an arm and a leg. Changing designs doesn’t come with the usual hefty costs of retooling. This adaptability supports customization6 and keeps us nimble in responding to market demands without the financial headache.
By embracing these elements, I’ve found that manufacturers like myself can truly leverage 3D printing to drive cost efficiency in mold production.
3D printing eliminates the need for traditional tooling.True
3D printing creates molds directly, bypassing traditional tooling costs.
3D printing increases material waste in mold production.False
3D printing is additive, using only necessary material, reducing waste.
Can 3D Printing Improve Design Flexibility for Complex Molds?
Ever wondered how 3D printing could revolutionize mold design, especially when dealing with those pesky complex shapes?
3D printing enhances design flexibility for complex molds through intricate details, faster production, and rapid prototyping, liberating designers from traditional constraints and promoting unprecedented innovation.
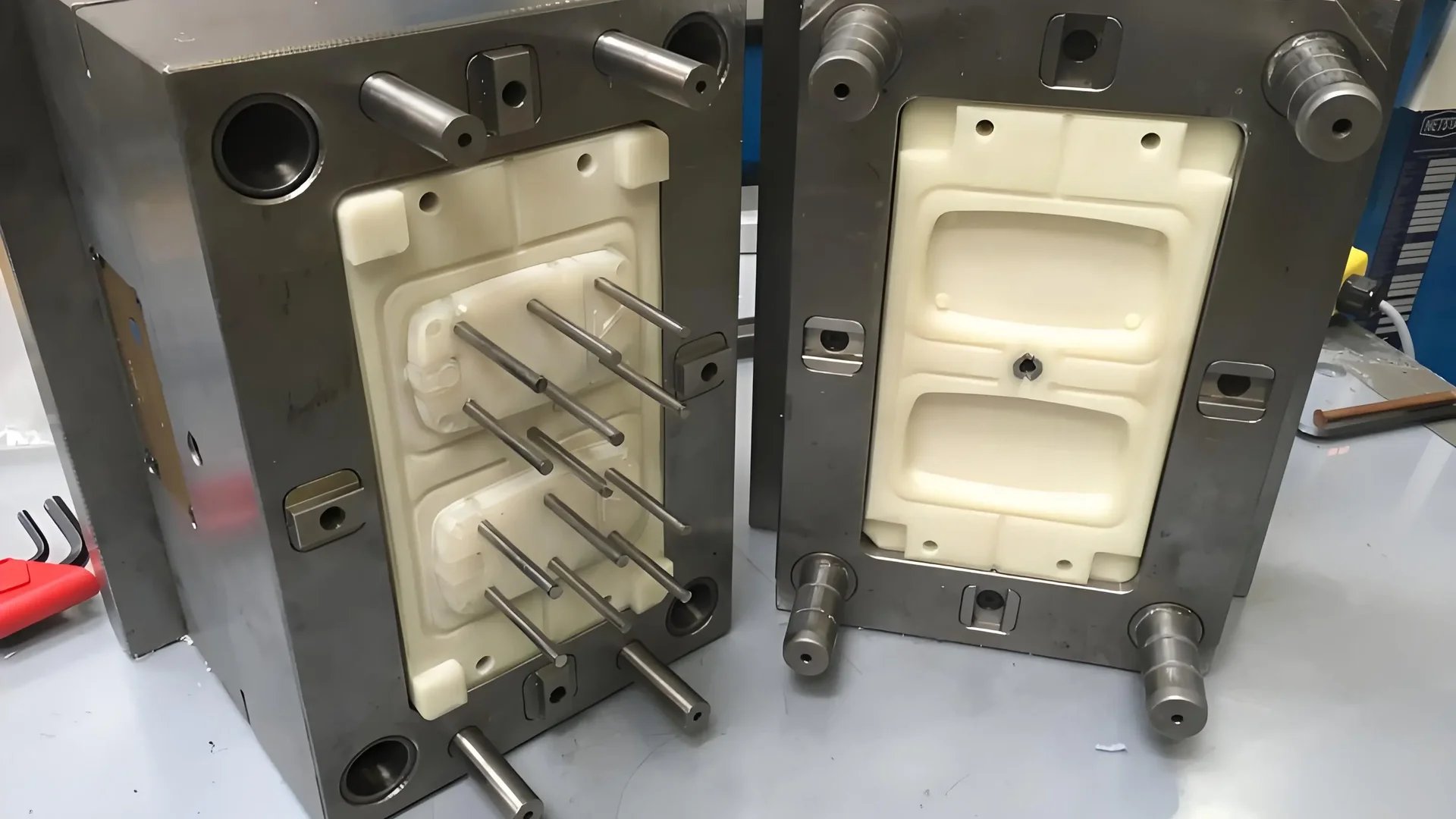
Embracing Intricate Geometries with 3D Printing
I remember my early days in mold design when achieving complex geometries felt like an impossible task. I often found myself wrestling with traditional machining limits, where the intricate details I dreamt of were just out of reach. But with 3D printing technology7, a whole new world opened up. By constructing layer upon layer of material, I could finally realize those complex structures that were once too costly or even impossible to produce.
Think about those fascinating lattice structures or the organic shapes that require precision engineering. With 3D printing, not only can I design these molds with less material waste, but I can also enhance both cost and performance. This newfound flexibility has allowed me to push the boundaries of innovative product designs, ensuring they meet every specific functional requirement.
Accelerating the Prototyping Phase
Prototyping used to be such a drawn-out process. But the advent of 3D printing changed everything. Now, I can rapidly produce multiple iterations of a design within days instead of weeks, testing and refining each version without breaking the bank. This capability has transformed how I approach exploratory designs, as I can afford to take risks without the fear of costly mistakes.
For instance, just last month, I was working on a new mold design that required several tweaks. Thanks to 3D printing, I was able to create and test several prototypes swiftly. This rapid prototyping has not only sped up our time-to-market but also improved the quality of the final product by allowing us to iron out any design flaws early in the process.
Comparing Traditional and 3D Printing Methods
Aspect | Traditional Mold-Making | 3D Printing |
---|---|---|
Material Constraints | High | Low |
Lead Time | Weeks | Days |
Cost Efficiency | Varies | Often Higher Savings |
Design Complexity | Limited | High Flexibility |
The table above really encapsulates what I’ve experienced firsthand: 3D printing outshines traditional methods in lead time and design complexity. The freedom it provides is truly game-changing.
Challenges and Considerations
Of course, as with any innovation, there are challenges. For instance, I’ve had to navigate issues like material strength and surface finish quality. Scaling up for mass production still presents hurdles that require careful consideration. In some cases, sticking to traditional methods makes sense because of existing infrastructure or familiarity.
Exploring successful case studies involving 3D printed molds8 has been instrumental in overcoming these challenges. As materials technology continues to advance, I’m excited about the expanding potential and reliability of 3D printed molds in industrial applications. This journey into the future of mold-making is as thrilling as it is promising.
3D printing reduces mold production lead time to days.True
3D printing's rapid prototyping capabilities significantly cut down lead times.
Traditional mold-making allows for more intricate designs than 3D printing.False
3D printing offers high design flexibility, surpassing traditional methods' limitations.
How Does 3D Printing Revolutionize Mold Making Efficiency?
Imagine the thrill of transforming an idea into a tangible product in record time. That’s exactly what integrating 3D printing into mold making offers.
3D printing revolutionizes mold making by reducing lead times, minimizing waste, and enabling rapid prototyping, thus enhancing efficiency, flexibility, and cost-effectiveness in production and design.
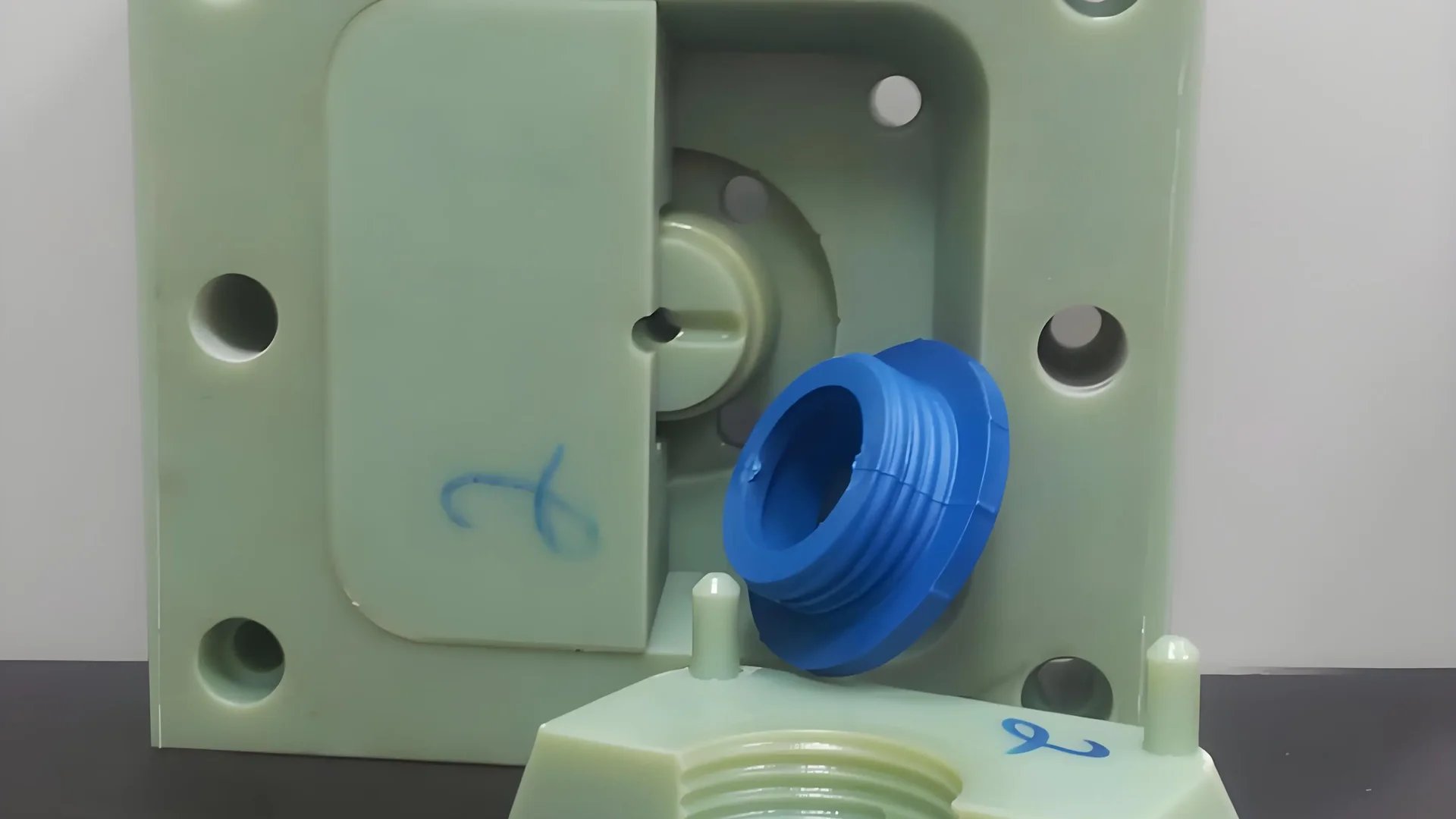
The Power of Rapid Prototyping
You know that feeling when you’re racing against the clock to finalize a design, only to be stymied by the slow pace of traditional prototyping? I’ve been there more times than I can count. Enter 3D printing9, a game-changer in mold making. It lets designers like us test out multiple iterations of a mold in the blink of an eye, which means less time waiting and more time creating. I remember the first time we shaved weeks off our timeline—it felt like a miracle.
Material Efficiency and Waste Reduction
Let’s be real: nobody likes waste. When I first started in mold design, I was appalled at how much material ended up in the trash. Then I discovered the beauty of 3D printing technology10, which uses only what’s necessary. This isn’t just eco-friendly; it also saves money—something my boss loves to hear.
Traditional Method | 3D Printing |
---|---|
High material waste | Minimal waste |
Long lead times | Short lead times |
The precision offered by 3D printing ensures that molds are created with exact specifications, minimizing the need for post-processing adjustments.
Enhanced Design Flexibility
The freedom 3D printing gives us is like nothing I’ve ever experienced. Imagine crafting complex geometries that were once impossible. It’s like being an artist with a whole new palette of colors. We can now explore intricate designs, like lattice structures, that reduce weight without sacrificing strength.
By embracing these new possibilities, companies can stay ahead of market trends and cater to increasingly demanding consumer expectations.
Case Studies: Real-World Applications
I’ve seen firsthand how industries are thriving by embracing 3D printing in mold making. Take the automotive sector, for instance—they’re producing custom, lightweight components faster and cheaper. A case study11 I came across recently reported a 30% decrease in production costs for an automotive giant after adopting 3D printed molds.
Embracing 3D printing isn’t just about keeping up with trends; it’s about leading them. It’s about innovation, efficiency, and setting a new standard for what’s possible in manufacturing.
3D printing reduces mold prototyping time to hours.True
3D printing allows rapid prototyping, cutting time from weeks to hours.
Traditional mold making produces less material waste than 3D printing.False
Traditional methods have high waste, while 3D printing minimizes it.
How Are Industries Adapting to 3D Printed Molds?
Ever wondered how 3D printed molds are shaking up industries like automotive and healthcare?
Industries are adopting 3D printed molds to enhance production efficiency, reduce costs, and increase design flexibility, benefiting sectors such as automotive, aerospace, and healthcare through rapid prototyping and accelerated product development.
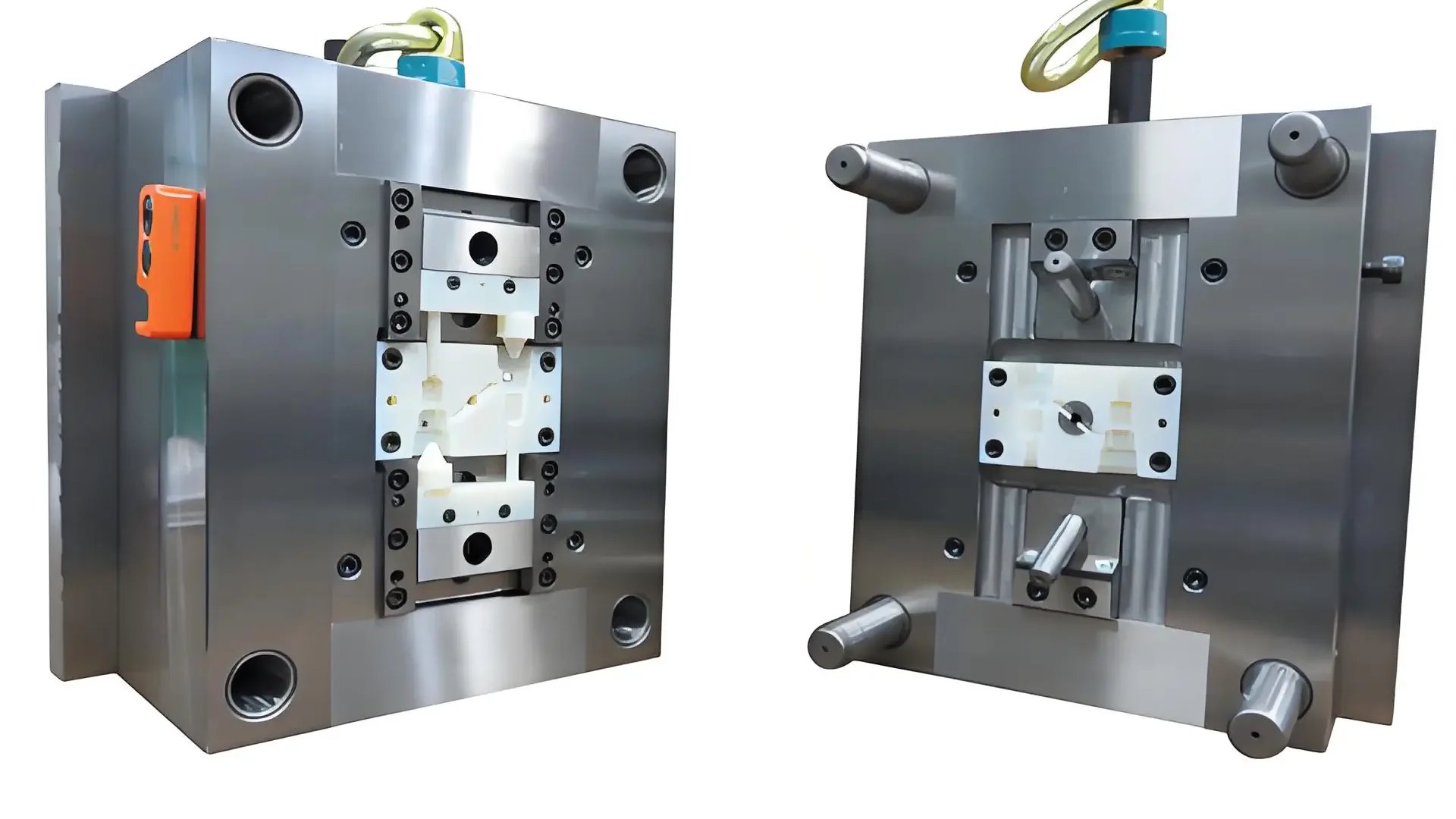
Embracing Flexibility and Customization
When I first stumbled upon 3D printed molds, it felt like discovering a magic wand for design flexibility. Imagine being able to tweak a mold design on a whim without the usual headache of retooling12. This is exactly what 3D printed molds offer—an opportunity to innovate without restraint.
Automotive Industry
In my early days working with automotive designs, the idea of creating intricate mold geometries seemed like a far-off dream. But now, thanks to 3D printing, companies can bring these complex designs to life without breaking the bank. It’s like giving designers the freedom to paint with a full palette of possibilities.
Benefits | Traditional Molds | 3D Printed Molds |
---|---|---|
Cost | High | Lower |
Design Flexibility | Limited | High |
Prototyping Speed | Slow | Fast |
Aerospace Advancements
Aerospace is another realm where 3D printed molds are making waves. Picture this: manufacturers are now able to churn out intricate aircraft parts13 in record time, which used to be a painstakingly slow process. It’s like turning an old bicycle into a sleek, high-speed motorcycle overnight.
Cost Efficiency and Environmental Impact
There’s something deeply satisfying about knowing you’re not just cutting costs but also doing your bit for the planet. By using 3D printed molds, industries can significantly reduce material waste. This means less inventory and a smaller carbon footprint through on-demand production14. It’s a win-win situation—both for the bottom line and for Mother Earth.
Healthcare Innovations
I remember chatting with a colleague in healthcare design who was amazed by how quickly they could produce custom molds for medical devices with 3D printing. It’s revolutionary because it means patient care is not only faster but also more personalized. Each mold can be tailored to fit individual needs, improving outcomes dramatically.
By exploring these examples15, it’s clear how adaptable 3D printed molds are, revolutionizing sectors by solving specific industry challenges.
3D printed molds reduce production costs in aerospace.True
They minimize material waste and enable faster production of parts.
Traditional molds offer more design flexibility than 3D printed molds.False
3D printed molds provide higher design flexibility due to easy modifications.
What Challenges Should You Consider When Implementing 3D Printing in Mold Making?
3D printing in mold making is like stepping into the future of manufacturing, but it’s not without its hurdles. Let me walk you through what I learned when I tried to bring this tech into my own design process.
When implementing 3D printing in mold making, consider material limitations, surface finish quality, cost factors, and integration with existing processes to enhance efficiency and production outcomes.
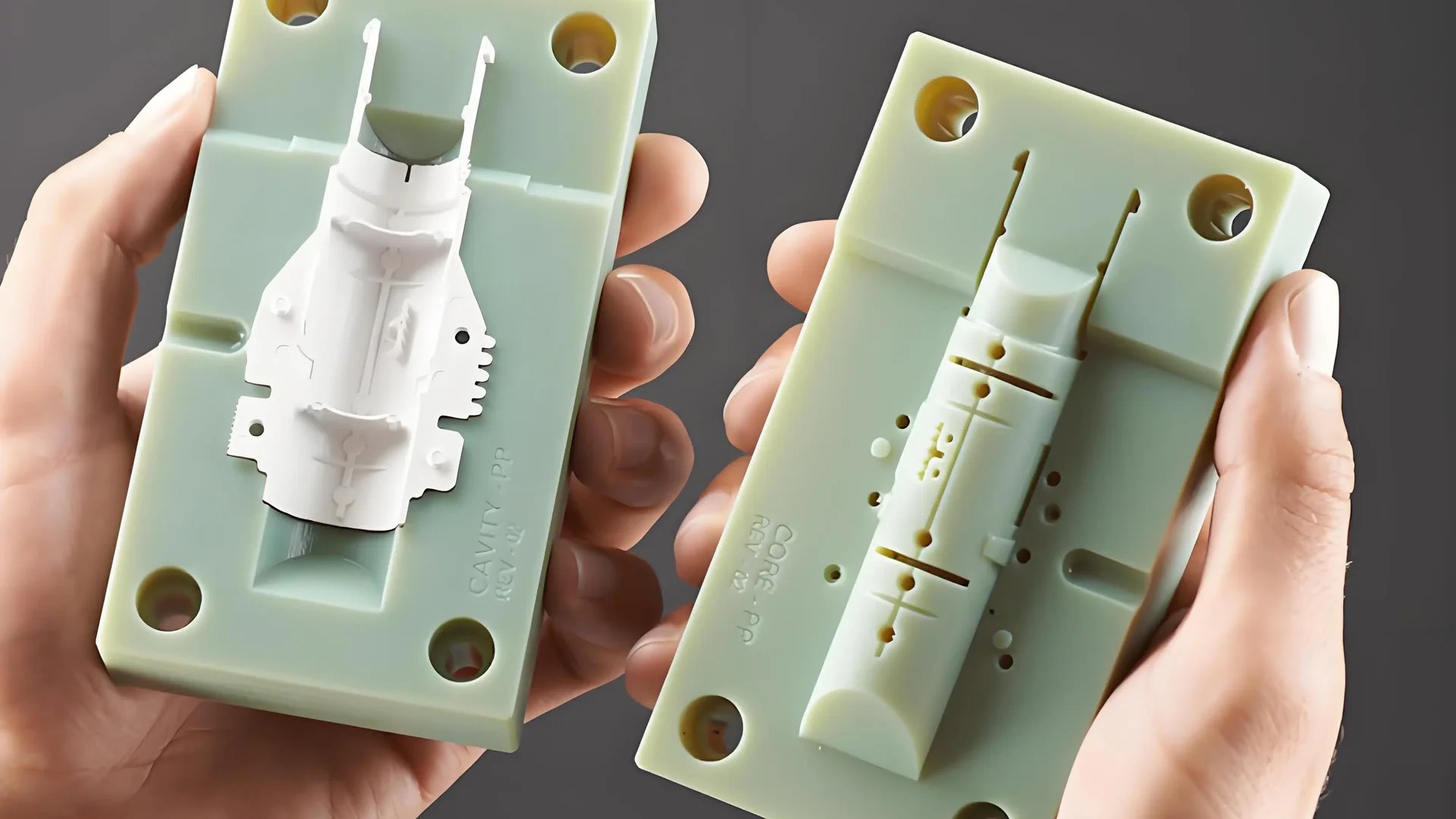
Material Limitations
When I first considered using 3D printing for mold making, I was excited by the possibilities. However, I quickly ran into the issue of material limitations16. Traditional molds use robust metals like steel, which can handle the wear and tear of production. But many 3D printers primarily work with polymers. This made me question whether the materials available could really meet the durability and heat resistance needed for my projects. It was a bit like trying to build a house out of straw when you’re used to bricks.
Surface Finish Quality
Achieving the perfect surface finish quality was another hurdle. I remember the first time I held a 3D-printed mold in my hands; it felt more like a prototype than a finished product due to the visible layer lines and surface roughness. I had to dive into researching different finishing techniques17 to figure out how to get that smooth finish essential for my products’ functionality and appearance. Each technique added time and cost, which were crucial factors in deciding whether this was the right direction for me.
Cost Considerations
The cost was another significant consideration. While the promise of reduced material waste was tempting, the initial investment in high-quality 3D printers seemed daunting. I had to perform a cost-benefit analysis18 to see if the long-term savings from less waste and quicker production could really offset those hefty upfront expenses.
Factor | Traditional Mold Making | 3D Printing |
---|---|---|
Initial Investment | Low | High |
Material Waste | High | Low |
Surface Finish | Smooth | May require polishing |
Integration with Existing Processes
Integrating 3D printing into my existing mold-making processes was like learning a new language. It required a thorough evaluation of how this new technology could fit within my current workflows and figuring out how to train my team to use it effectively. The learning curve felt steep and slightly intimidating, affecting productivity in those early days. But seeing examples from successful companies19 provided me with a blueprint for planning and mitigating potential disruptions.
By addressing these challenges head-on, I’ve been able to prepare more effectively for implementing 3D printing technology in my mold-making endeavors, ensuring a smoother transition and optimized outcomes.
3D-printed molds are more durable than traditional steel molds.False
3D-printed molds often use polymers, which are less durable than steel.
Initial investment in 3D printing is higher than traditional methods.True
High-quality 3D printers require substantial upfront investment compared to traditional methods.
Conclusion
3D printing revolutionizes mold making by enhancing design flexibility, reducing costs, and speeding up production. It allows for rapid prototyping and minimizes material waste, driving innovation in manufacturing.
-
Learn about how rapid prototyping with 3D printing speeds up production timelines significantly. ↩
-
Learn about how rapid prototyping with 3D printing speeds up production timelines significantly. ↩
-
Uncover how customization capabilities in 3D printing encourage innovation and adaptation to market changes. ↩
-
Explore how eliminating traditional tooling needs can lead to substantial cost savings in mold production. ↩
-
Learn about the advantages of rapid prototyping for faster product development cycles. ↩
-
Discover how 3D printing supports customization and adaptation in manufacturing. ↩
-
Explore how 3D printing handles complex geometries better than traditional methods. ↩
-
Gain insights from real-world applications of 3D printed molds in various industries. ↩
-
Explore how rapid prototyping through 3D printing can transform mold making processes with speed and efficiency. ↩
-
Understand how additive manufacturing reduces waste and improves cost-efficiency in mold making. ↩
-
Learn from real-world examples how companies benefit from integrating 3D printing into their mold making processes. ↩
-
Discover how easy it is to modify designs with 3D printed molds, saving time and costs in retooling processes. ↩
-
Learn about the rapid production of complex aircraft components through 3D printed molds in aerospace. ↩
-
Explore how on-demand production with 3D printing reduces inventory costs and environmental impact. ↩
-
Gain insights into how different sectors are utilizing 3D printed molds to solve industry-specific challenges. ↩
-
Explore the various materials available for 3D printing molds and understand their properties. ↩
-
Learn about techniques to enhance the surface quality of 3D-printed molds. ↩
-
Understand the financial implications and potential savings when using 3D printing. ↩
-
Discover how companies have successfully adopted 3D printing into their processes. ↩