Have you ever marveled at how everyday plastic items are created? The magic lies in a process called injection molding.
The four key elements of injection molding processing are plastic materials, injection molding machines, molds, and process parameters. Each plays a critical role in determining the quality and efficiency of the final product.
While this summary provides a snapshot of these crucial elements, let’s dive deeper into each one to unveil their intricate roles and how they work together to optimize the injection molding process.
Injection speed affects product quality in molding.True
Proper injection speed ensures complete filling and reduces defects.
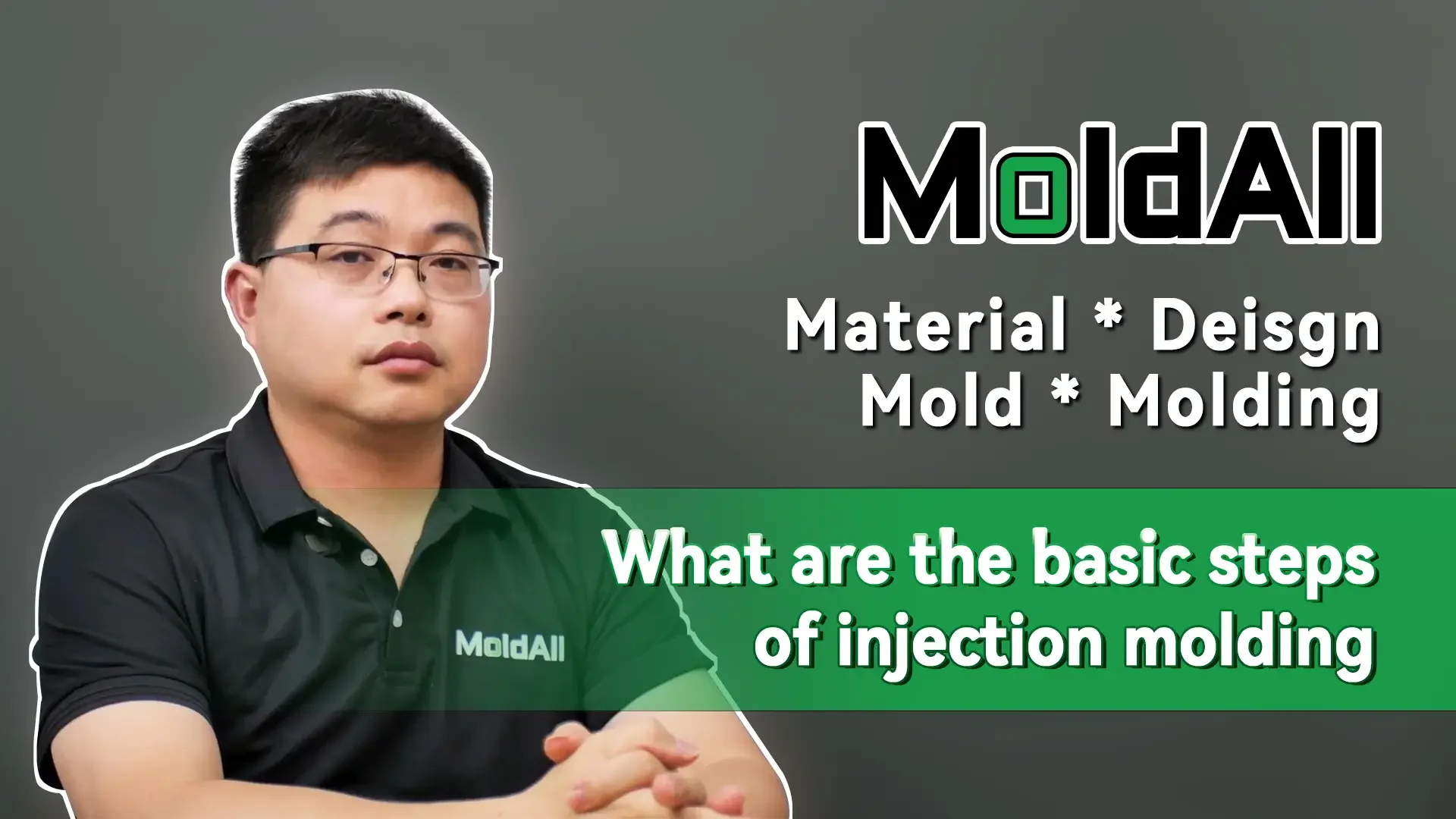
How Do Different Plastic Materials Affect Injection Molding?
Different plastic materials significantly influence the injection molding process, impacting the final product’s quality and performance.
Plastic materials impact injection molding through fluidity, shrinkage, heat resistance, and mechanical properties. These factors determine the ease of mold filling, dimensional accuracy, and product durability.
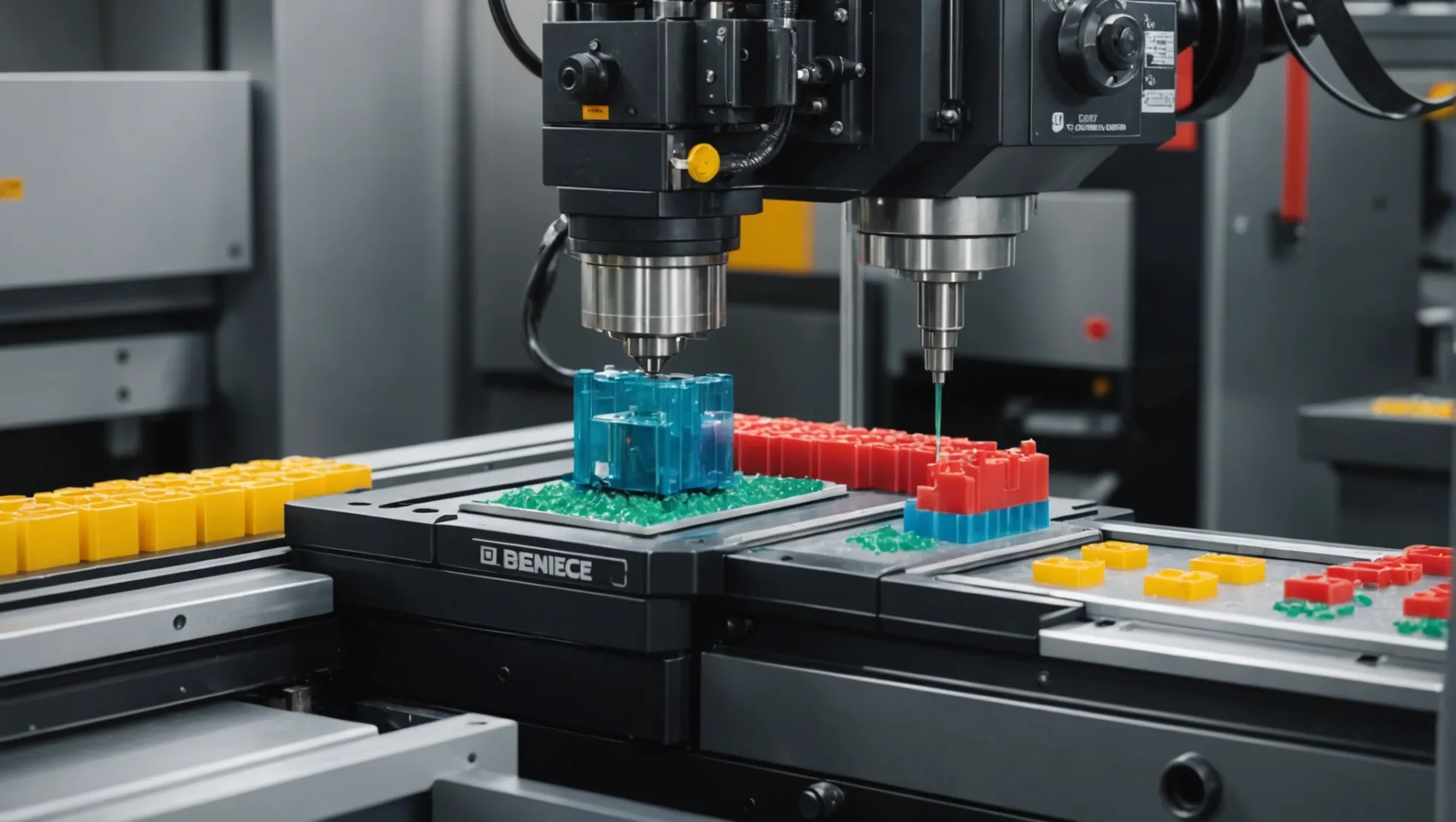
Fluidity and Its Impact on Mold Filling
The fluidity of a plastic material is crucial in determining how easily it can fill the mold cavity during injection molding. Materials with high fluidity can navigate complex mold geometries more efficiently, reducing the likelihood of incomplete fills. However, they often experience greater shrinkage upon cooling, which can affect the dimensional accuracy of the final product. Conversely, materials with low fluidity require higher injection pressures and temperatures to ensure complete cavity filling, potentially increasing production costs and energy consumption.
For example, polypropylene1 is known for its excellent fluidity, making it suitable for intricate designs but prone to significant shrinkage. On the other hand, polycarbonate2 typically exhibits lower fluidity, necessitating careful adjustment of injection parameters to avoid defects.
Shrinkage Rates: Planning for Precision
Shrinkage is a natural occurrence as plastics cool and solidify, with rates varying significantly among different materials. This aspect must be carefully considered when designing molds and setting process parameters. For instance, nylon3 has a relatively high shrinkage rate, requiring precise compensation in mold design to achieve desired dimensions. Failure to account for shrinkage can lead to products that don’t meet size specifications, resulting in costly redesigns and delays.
Heat Resistance: Choosing Materials for High-Temperature Applications
Products destined for high-temperature environments must be molded from materials with excellent heat resistance. Such materials can endure elevated processing and service temperatures without deforming or degrading. Acrylonitrile butadiene styrene (ABS)4, for instance, offers decent heat resistance but may not suffice for extreme conditions where polyetheretherketone (PEEK)5 would be more appropriate due to its superior thermal stability.
Mechanical Properties: Strength and Durability Considerations
The intended use of the product dictates the selection of plastic based on its mechanical properties like strength, hardness, and toughness. For applications requiring high impact resistance, such as automotive parts, impact-modified polycarbonate6 is a popular choice. In contrast, applications demanding rigidity might benefit from using polystyrene7, known for its excellent hardness and rigidity.
Understanding these characteristics helps manufacturers choose the right plastic material that aligns with their product’s performance requirements and manufacturing constraints.
Polypropylene has high fluidity in injection molding.True
Polypropylene's high fluidity allows it to fill complex molds easily.
Nylon exhibits low shrinkage rates in molding processes.False
Nylon actually has a relatively high shrinkage rate in molding.
What Role Does the Injection Molding Machine Play in Processing?
Injection molding machines are the powerhouse behind the production of countless plastic products, ensuring precision and efficiency.
Injection molding machines are essential in processing as they control injection pressure, speed, clamping force, and plasticizing ability. These elements ensure precise, efficient, and consistent production, influencing product quality and reducing defects.
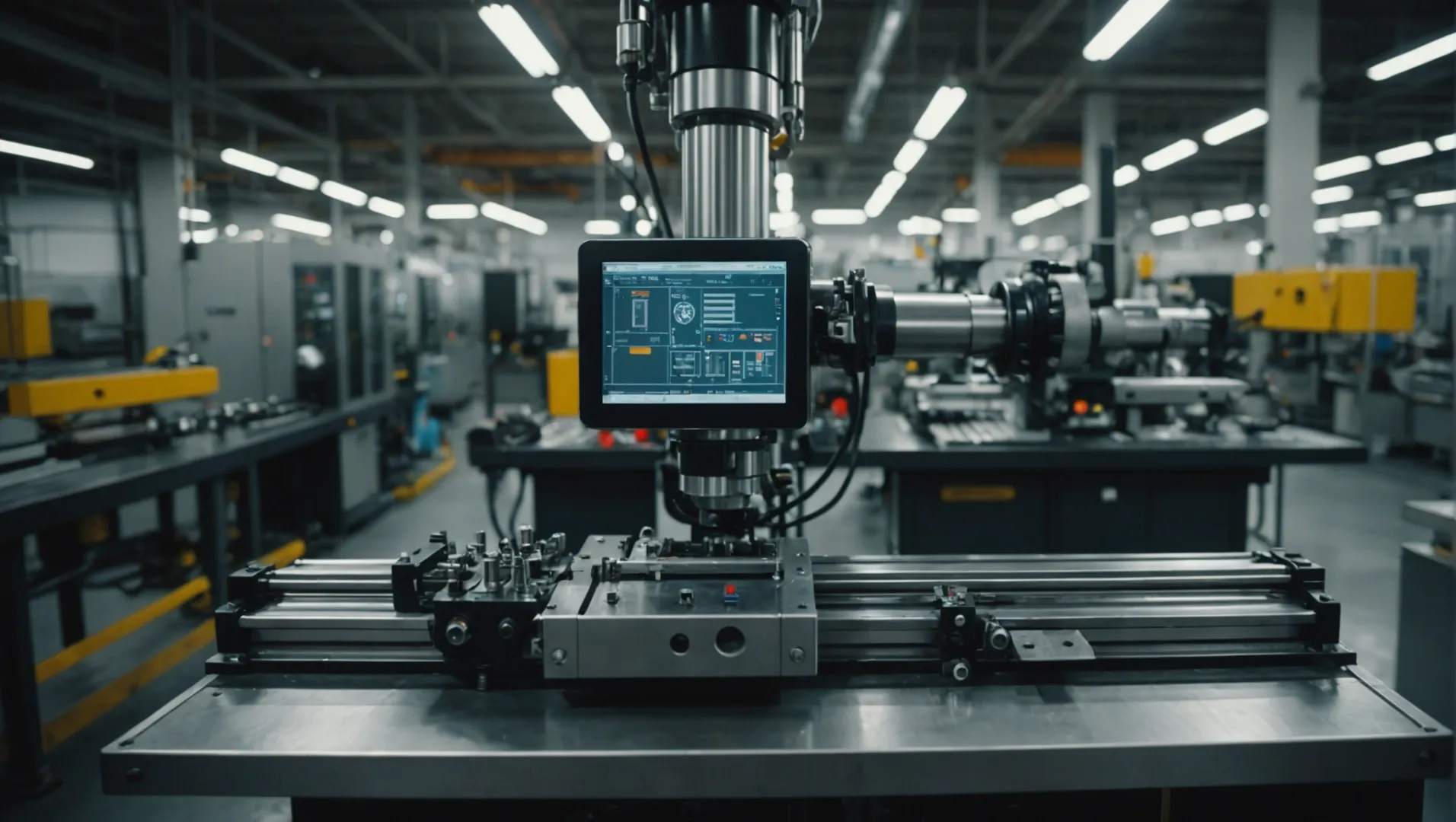
The Core Functions of Injection Molding Machines
Injection molding machines are integral to the manufacturing process due to their ability to mold complex shapes with precision. They operate by melting plastic granules and injecting them into molds under high pressure. This process is crucial in industries ranging from automotive to medical devices, where accuracy is non-negotiable.
Injection Pressure: Driving Force
One of the primary roles of an injection molding machine is to apply injection pressure. This pressure ensures that the molten plastic fills every crevice of the mold cavity, achieving the desired shape and detail. High injection pressure is particularly vital for products with intricate designs or thin walls, as it prevents incomplete filling and ensures structural integrity.
Injection pressure must be carefully calibrated to suit different materials and product specifications, striking a balance between sufficient filling and minimizing defects.
Injection Speed: Balancing Act
Injection speed is another critical parameter managed by the machine. It dictates how quickly the molten plastic is injected into the mold. A faster injection speed can enhance production rates but may lead to defects such as flow marks or bubbles if not properly controlled. Conversely, a slower speed might improve quality but reduce efficiency.
The key is to find an optimal speed that maintains product quality while maximizing throughput, a challenge that underscores the machine’s role in process optimization.
Clamping Force: Seal of Assurance
The clamping unit of an injection molding machine provides the necessary force to keep the mold closed during injection. This clamping force prevents the mold from opening under pressure, which would lead to defects like flash or incomplete products.
The required clamping force is determined by factors such as the projected area of the part and the injection pressure. Calculating this accurately is crucial for maintaining product consistency and minimizing material waste.
Plasticizing Ability: Ensuring Homogeneity
The plasticizing unit of the machine is responsible for melting and homogenizing the plastic material before injection. Effective plasticizing ensures that the material is uniformly melted, reducing the likelihood of defects such as sink marks or voids in the finished product.
A high-quality injection molding machine will have superior plasticizing capabilities, allowing for a wide range of materials and applications.
By managing these elements—pressure, speed, clamping, and plasticizing—the injection molding machine serves as the linchpin in producing high-quality molded parts consistently and efficiently. Understanding these roles can help manufacturers optimize their injection molding process8 for better performance and reduced costs.
Injection molding machines ensure product quality.True
They control pressure, speed, and clamping to reduce defects.
Injection speed has no impact on production rates.False
Faster speeds increase rates but can cause defects if uncontrolled.
Why Is Mold Design Critical in Injection Molding?
Mold design is the backbone of successful injection molding, impacting product quality and production efficiency. Discover its critical role here.
Mold design is crucial in injection molding because it determines the shape, precision, and quality of the final product. A well-designed mold ensures efficient production, minimizes defects, and influences the overall manufacturing cost.
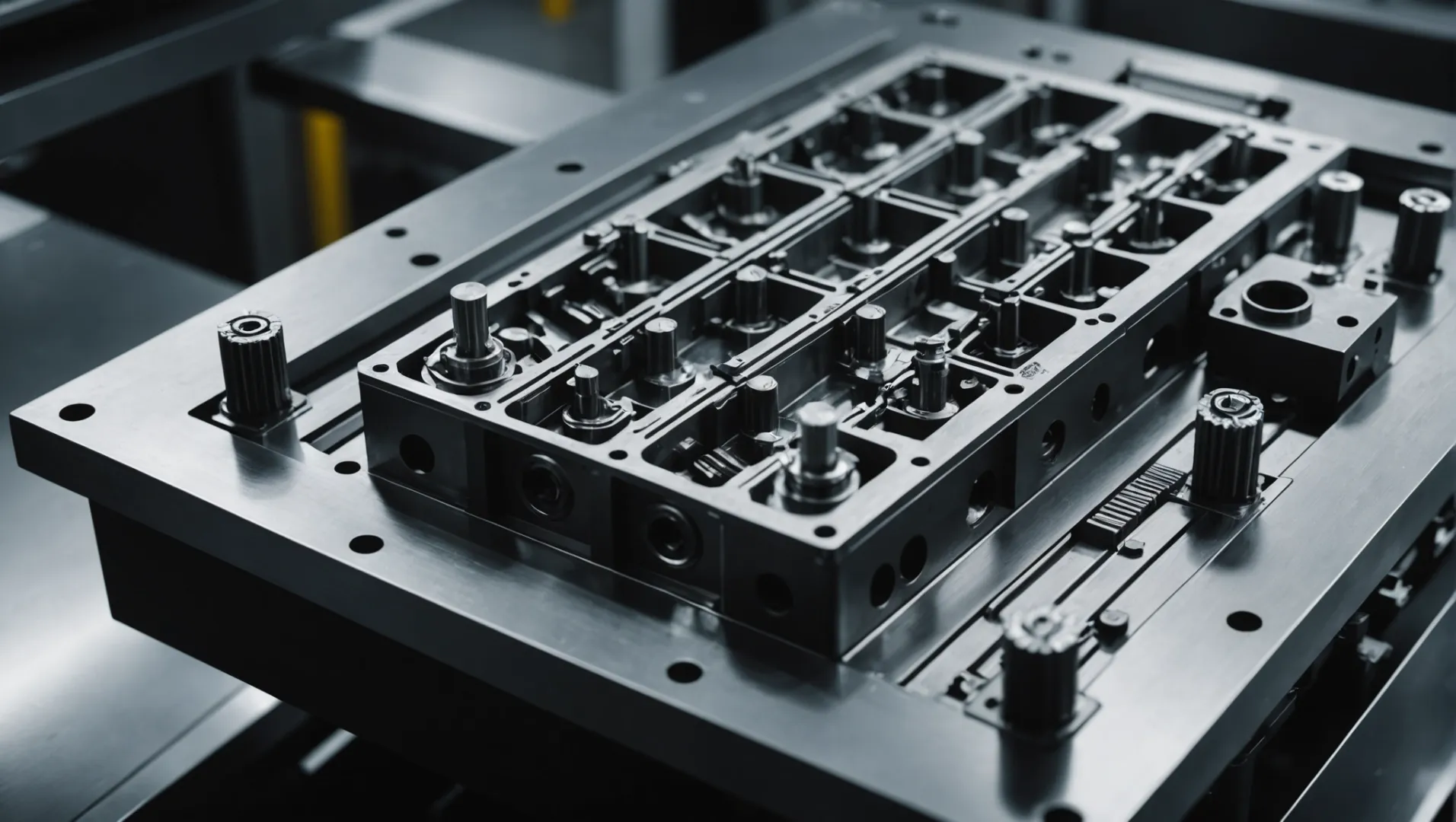
The Role of Mold Structure
The mold structure9 plays a vital role in ensuring that injection molded products meet their shape, size, and precision requirements. A complex mold structure might include side core pulling mechanisms to accommodate intricate designs without compromising product quality. For instance, molds with precise alignment features ensure minimal parting lines on the final product.
Material Selection for Molds
Choosing the right mold material10 is essential to cater to different production needs. Steel molds are preferred for high-strength and mass-production requirements due to their durability and wear resistance. Conversely, aluminum molds are lighter and more suited for short production runs or prototyping due to their quicker processing times.
Material Type | Advantages | Disadvantages |
---|---|---|
Steel | High strength, wear resistance | Longer production time, costlier |
Aluminum Alloy | Lightweight, short processing time | Less durable, suitable for small batches |
Importance of Cooling Systems
The cooling system within a mold can significantly affect the molding cycle and product quality. Efficient cooling designs help reduce cycle times by rapidly lowering the product’s temperature, thereby minimizing deformation and shrinkage. This aspect is particularly important when dealing with larger or more complex parts.
Exhaust Systems in Mold Design
A well-designed exhaust system is critical for removing air trapped within the mold cavity during the injection process. Without adequate venting, defects such as bubbles or burn marks may appear on the product surface. This aspect ensures a smooth ejection process and enhances the aesthetic and functional quality of the final product.
Interplay Between Mold Design and Other Elements
Mold design doesn’t function in isolation; it interacts with other elements like plastic materials and process parameters. For example, a material’s fluidity influences how the mold should be designed to ensure complete filling without excessive pressure. Likewise, mold cooling systems must align with material shrinkage rates to maintain dimensional accuracy.
Steel molds are best for short production runs.False
Steel molds are durable and suited for mass production, not short runs.
Efficient cooling reduces cycle time in injection molding.True
Cooling systems lower product temperature quickly, reducing cycle time.
How Do Process Parameters Influence Injection Molding Outcomes?
In injection molding, process parameters dictate the path from raw material to finished product. But how exactly do these variables shape the outcome?
Injection molding outcomes are significantly influenced by process parameters such as temperature, time, and pressure. These factors determine the melt flow, cooling rate, and overall product quality. Adjusting these parameters is crucial for achieving desired product specifications and minimizing defects.
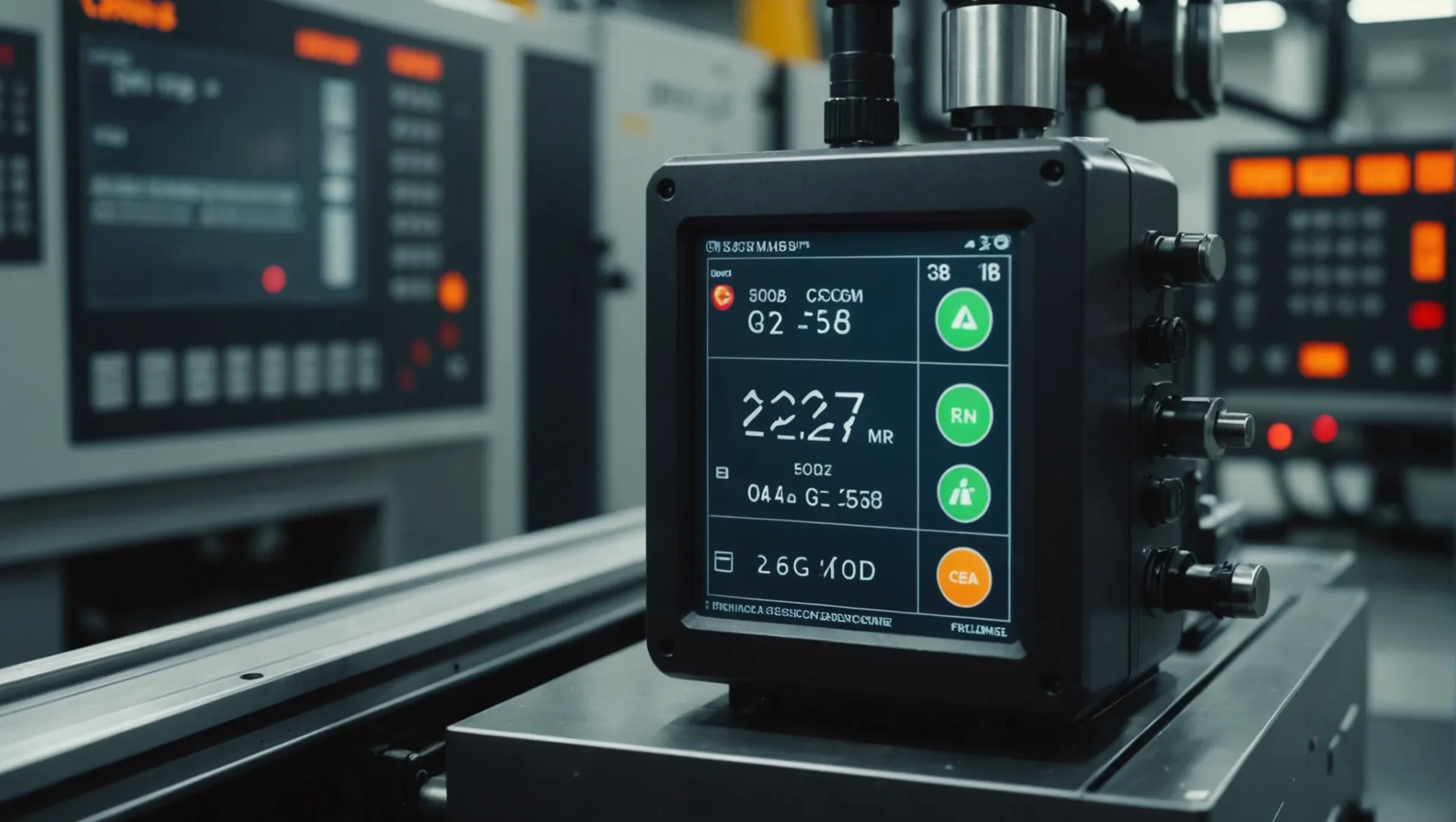
The Crucial Role of Temperature
Temperature management in injection molding is multi-faceted, involving the barrel, nozzle, and mold temperatures.
-
Barrel Temperature: This should be aligned with the plastic material’s melting point to ensure thorough melting without degradation. Deviations can lead to incomplete melting or thermal degradation, affecting product strength.
-
Nozzle Temperature: Typically slightly lower than the barrel to prevent drooling, nozzle temperature ensures a smooth transition of molten plastic into the mold.
-
Mold Temperature: This impacts surface finish and dimensional accuracy. For example, higher mold temperatures improve surface quality but may extend cycle times.
Time Management in Injection Molding
Time factors such as injection, holding, and cooling times are pivotal for optimal molding outcomes.
-
Injection Time: It must be optimized based on part size and complexity to ensure full cavity filling without defects like short shots.
-
Holding Time: During this phase, pressure is maintained to counteract shrinkage as the material cools. Incorrect holding time can lead to warping or sink marks.
-
Cooling Time: Adequate cooling is essential to ensure part stability and reduce cycle time. Too short a cooling time can result in incomplete solidification, while too long can affect throughput.
Pressure Parameters and Their Impact
Pressure in injection molding isn’t just about filling the mold; it’s crucial for shaping the final product.
-
Injection Pressure: Critical for ensuring that the mold cavity is filled completely, especially for intricate designs. Insufficient pressure can result in incomplete parts.
-
Holding Pressure: This compensates for material shrinkage during cooling. Adjustments to holding pressure can improve dimensional stability and reduce defects.
Interdependency of Parameters
These parameters do not operate in isolation. For instance, an increase in barrel temperature might necessitate adjustments in injection speed to maintain quality. Explore temperature and pressure dependencies11 for more insights.
Understanding and optimizing these interdependent parameters is crucial. This balance ensures high-quality products while maintaining efficiency and reducing waste in manufacturing processes.
Barrel temperature affects product strength.True
Proper barrel temperature ensures thorough melting, avoiding degradation.
Cooling time has no effect on product stability.False
Adequate cooling time is crucial for ensuring part stability.
Conclusion
Mastering these four elements is essential for achieving excellence in injection molding. Consider their interplay to enhance product quality and process efficiency.
-
Discover why polypropylene’s fluidity benefits complex designs.: Polypropylene is a thermoplastic with excellent moisture resistance, good fatigue strength, and a low coefficient of friction. ↩
-
Learn about polycarbonate’s low fluidity challenges.: Polycarbonate injection molding is a sophisticated process that presents unique challenges for manufacturers. With its outstanding strength, … ↩
-
Explore nylon’s high shrinkage impact on precision.: The shrinkage of molded plastic parts can be as much as 20% by volume when measured at the processing and ambient temperature. ↩
-
Uncover ABS’s limitations in high-temperature scenarios.: ABS is a widely used 3D printing filament with good impact resistance and flexural strength. It also exhibits moderate heat resistance, making … ↩
-
See why PEEK excels in extreme heat applications.: PEEK is a semi-crystalline polymer and exhibits much higher shrinkage compared to an amorphous thermoplastic. Moreover, cooling from a much higher processing … ↩
-
Understand its role in high-impact applications.: It translates to reasonable room temperature impact strength. It does not take into account any requirements for low-temperature (below 0 °C) impact strength. ↩
-
Learn about polystyrene’s rigidity advantages.: Solid or rigid form: this polystyrene type is transparent, rigid, brittle, and moderately strong in its unmodified state. Foam form: the most … ↩
-
Learn strategies to enhance molding efficiency and product quality.: Steps to INJECTION MOLDING Process Optimization · 1. Tool functionality examination · 2. Short shot testing · 3. Gate seal studies · 4. Sample parts evaluation/ … ↩
-
Understand how mold structure affects product quality and design precision.: The feeding system of an injection mold primarily transports the plastic melt from the nozzle of the injection molding machine to each cavity. ↩
-
Explore the pros and cons of different mold materials.: Plastic materials for injection molding range from commonly used polymers to specialty plastics and polymer blends. ↩
-
Discover how temperature and pressure settings influence product quality.: The color dispersion and melting of the material are optimized by back pressure. Doing so can cause strain on the plastic injection molding machine, reduce the … ↩