Picture yourself deep in the process of crafting the ideal plastic piece where each tiny aspect holds significance.
In injection molding, the thickness and width of a film gate shape the flow of melted material. They affect how fast it travels and how long it takes to fill a mold. A gate of the right size improves molding quality. It should match the material’s qualities. This helps production move faster.
Thinking about my early mold design days, I recall a project where changing the film gate size felt like solving a tough puzzle. Watching tiny shifts in thickness or width lead to big changes in product quality was truly fascinating. For example, increasing the gate’s width, while keeping the thickness steady, allowed the melt to fill the cavity quicker, cutting down on possible flaws.
In another instance, I dealt with a material famous for bad flow. By adjusting the gate thickness, the melt flowed smoothly without cooling problems. This showed me that grasping and modifying these dimensions is key to design success. It goes beyond technical details. It’s about balance between design parts and how the material behaves.
Film gate width impacts melt flow rate in molding.True
The width of the film gate affects how quickly the melt flows.
Thicker film gates reduce filling time in injection molding.False
Thicker gates typically increase resistance, leading to longer filling times.
How Do Thickness and Width Affect Melt Flow Characteristics?
Curious about how the thickness and width of a mold affect material flow during production?
Thickness and width are essential for melt flow characteristics. These factors affect how efficiently molds fill and how good the final products look. Changing these sizes helps improve injection molding results. Improved product quality and appearance are achieved.
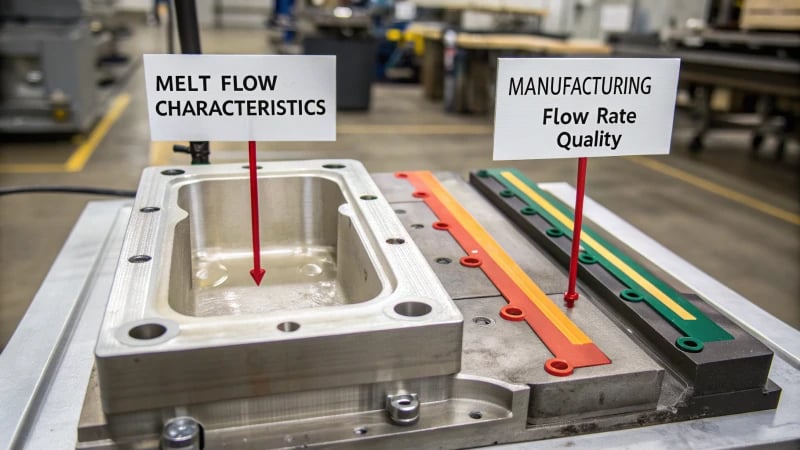
Synergistic Impact on Melt Flow
I spent many late nights working with molds in the workshop. The thickness and width of a film gate strongly affect melt flow. These dimensions determine the area where the melt moves, influencing the flow rate and speed. In one project, we increased the width of a film gate from 50mm to 100mm, keeping the thickness the same. The results were astonishing; the melt flow rate increased and filled the cavity faster than before. It really made a huge difference.
Parameter | Effect on Flow |
---|---|
Increase Width | Higher Flow Rate |
Maintain Thickness | Faster Cavity Filling |
Striking a balance is vital to avoid problems such as melt spraying or slow fill rates. This is really important.
Connected Impact on Molding Quality
It’s intriguing how the right mix of thickness and width brings uniform wall thickness and stable dimensions. Once, we worked on a rectangular part and adjusted these dimensions. The material spread evenly, reducing warping and improving quality. The change was remarkable.
Proper adjustment also minimizes gate and weld marks, enhancing appearance quality in plastic panel1 production. It feels magical when everything is perfect.
Interaction with Material Properties
Every material behaves differently, and knowing them is crucial. Polypropylene (PP) likes a thin gate thickness with a wide width due to its fluid nature. In contrast, glass fiber reinforced plastics call for thicker gates.
Material | Recommended Gate Dimensions |
---|---|
Polypropylene (PP) | Thin & Wide |
Glass Fiber Reinforced | Thick & Moderately Wide |
Materials like POM with high shrinkage require wider gates to balance volume loss as they cool. Understanding your material fully is important—a skill developed with curiosity and practice.
Explore these strategies to refine your injection molding processes2 and witness the changes yourself.
Increasing width increases melt flow rate.True
Wider gates allow more material to flow through, increasing the rate.
Thicker gates reduce cavity filling speed.False
Thicker gates actually facilitate faster cavity filling by allowing more flow.
How Do Gate Dimensions Influence Molding Quality?
Have you ever thought about how gate size plays a big role in whether a molding project succeeds or fails?
Gate sizes influence molding quality. They affect how the melt flows, the evenness of wall thickness and if the materials fit well together. Correct gate sizes allow smooth filling. Defects decrease. Product looks better.
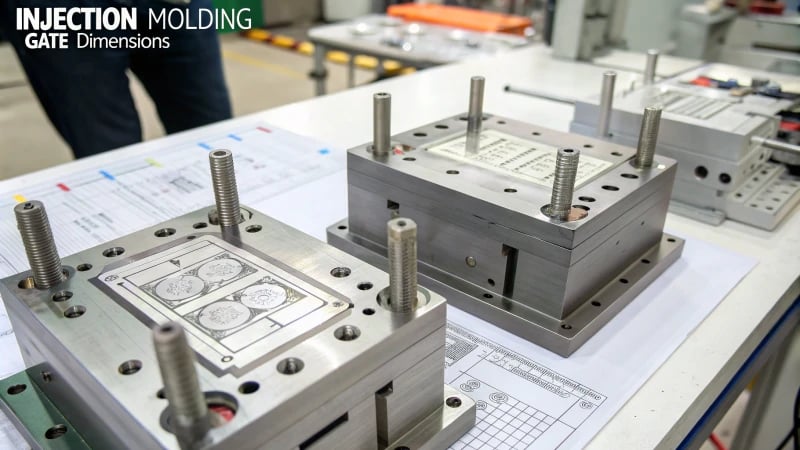
The Important Role of Gate Sizes
Gate sizes act like the magic ingredient in injection molding. I recall the first time I grasped their value – working on a project where small mistakes caused a whole batch of bad parts. That was a key learning experience. Gate thickness and width work together to determine the area where the melt flows. Think of trying to drink a thick milkshake through a thin straw versus a wide one – the flow changes a lot! A thicker gate keeps the flow steady, which is crucial for big parts. A wider gate lets cavities fill up faster, which is important when time is tight.
Thickness and Width
Balancing gate sizes is like finding rhythm in a song. If too wide or thick, you may get problems like melt spraying or incomplete fills – I’ve been there, sweating to figure out the problem. Finding that perfect spot is essential.
Gate Type | Effect on Flow |
---|---|
Thick | Slower, steady flow |
Wide | Faster cavity filling |
Linked Effects on Molding Quality
Gate sizes do more than affect melt flow characteristics3; they also help keep wall thickness even and dimensions stable. Getting this right is like threading a needle – it needs care. The right mix cuts down on warping and makes sure the final part looks and works well. I once had a project with very precise plastic parts. Getting the gate sizes right was challenging, but succeeding felt great.
Interaction with Material Characteristics
Different materials have unique needs – like how some people like tea while others like coffee. High fluidity materials require thinner gates for speed, while low fluidity ones need thicker gates to keep pressure.
Here’s a quick guide:
Material Type | Recommended Gate |
---|---|
High fluidity (e.g., PP) | Thinner, wider gate |
Low fluidity (e.g., GF) | Thicker gate for pressure stability |
Understanding these details helps improve molding processes and reach the best mix of quality and speed. This is something every designer probably wants. Every change and adjustment is a step closer to becoming skilled in molding.
Thicker gates ensure faster cavity filling.False
Thicker gates allow slower, steadier flow, not faster filling.
Wide gates help reduce weld lines in molding.True
Wide gates enable quicker filling, reducing weld line formation.
Why Is Material Compatibility Important in Gate Design?
Have you ever stood in front of a gate and wondered why it seems so strong and smooth? The secret lies in choosing the right materials that fit perfectly together.
Material compatibility in gate design is very important for strength against harsh weather and physical damage. This is very crucial. It guarantees smooth operation, safety and saves money in the long run.
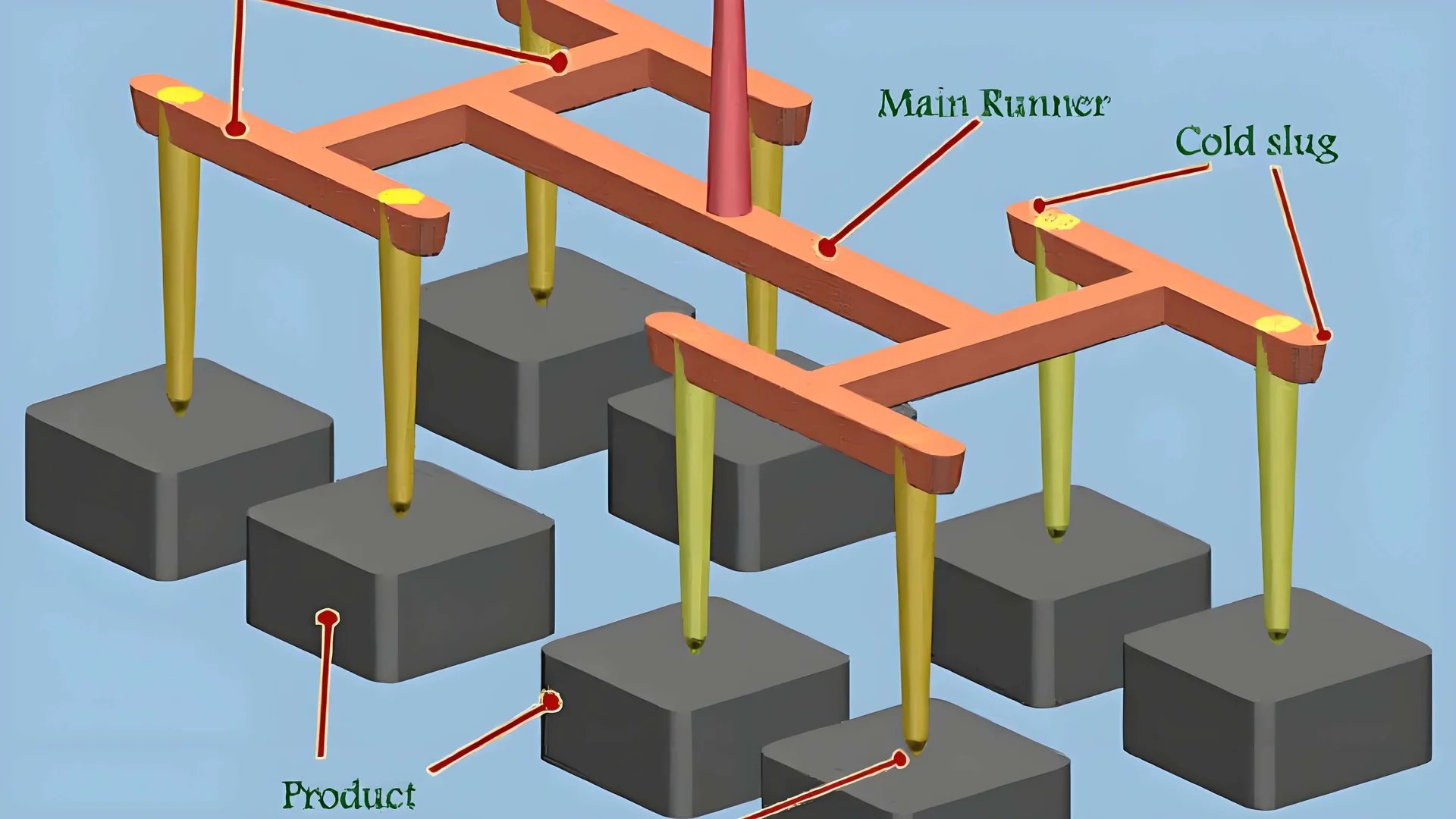
Stainless steel resists rust in humid environments.True
Stainless steel, especially with coatings, is corrosion-resistant.
Aluminum gates are ideal for high-impact areas.False
Aluminum is lightweight and may need reinforcement for high impact.
How Can You Optimize Film Gate Dimensions for Better Results?
Curious about how small changes in size can improve your plastic molding skills?
Optimizing film gate sizes involves adjusting width and thickness. This shapes how the melt flows. Balanced walls emerge. Adjustments uplift molding quality. They also refine how the end product looks. Defects decrease.
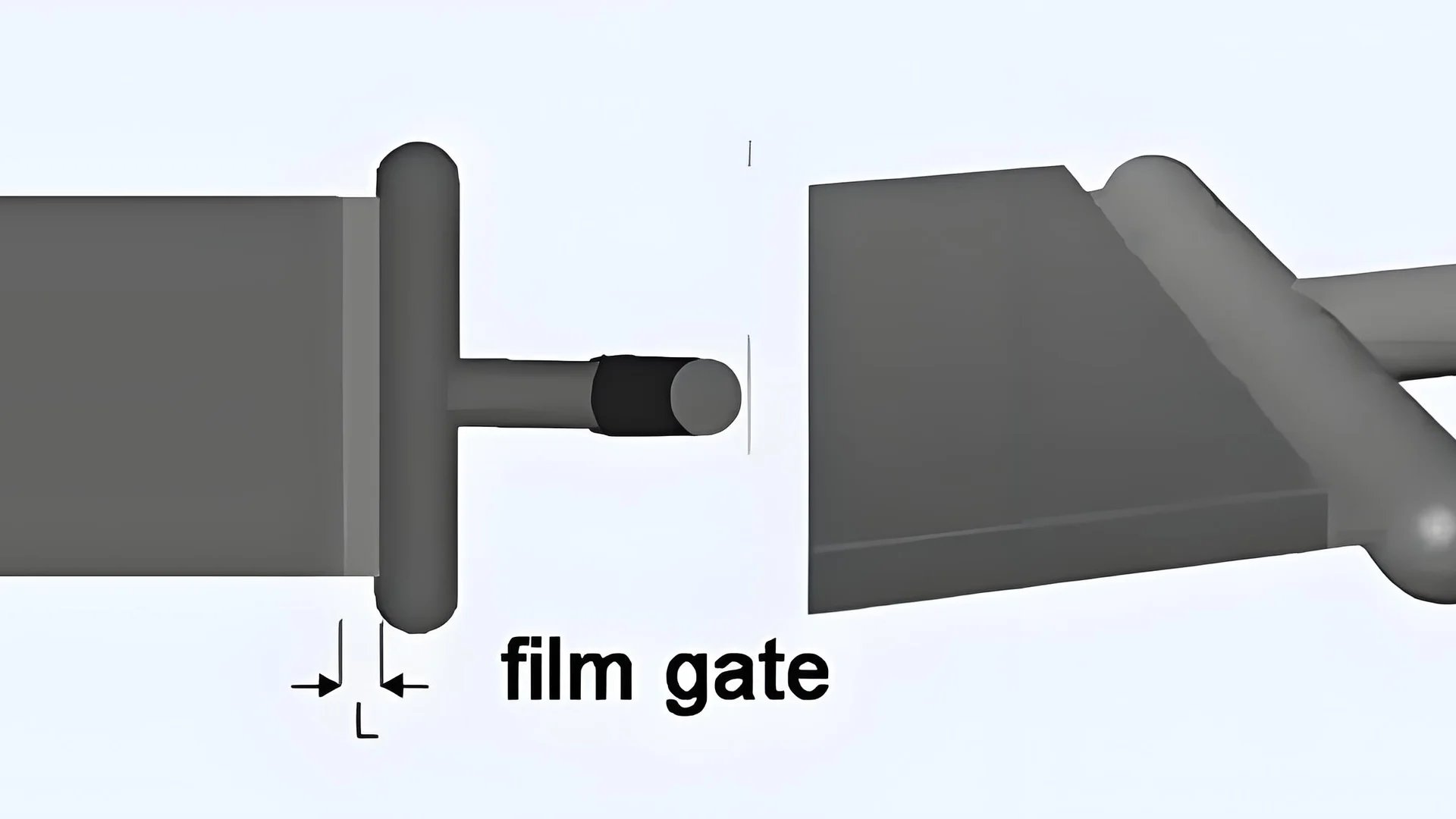
Grasping Melt Flow Basics
When I began learning about injection molding, I noticed how changing the size of the gate could alter the results. Picture this: widening the gate from 50mm to 100mm, while keeping the thickness at 1mm, really increased the melt flow rate. Cavities filled much faster. It felt like discovering a hidden trick in a video game.
Dimension | Width Increase | Flow Rate Impact |
---|---|---|
Scenario 1 | 50mm to 100mm | Increases |
Balance is crucial. Too much width and not enough thickness cause rapid flow. This may create defects like flow marks. If thickness increases but width decreases, flow slows, potentially underfilling thin parts.
Influencing Molding Outcomes
I recall adjusting gate size for a rectangular piece. Suddenly, melt spread evenly, reducing worries about warping. It was a true breakthrough!
Visual Finish Impact
Nothing beats seeing a smooth plastic part emerge. Proper gate size reduced marks. It was magical.
Interaction with Material Needs
I now see how different materials demand unique gate strategies. High-fluidity materials like polypropylene perform better with thin, wide gates. Thick gates suit low-fluidity materials, such as glass fiber-reinforced plastics.
Shrinkage matters too. When I worked with polyoxymethylene, tweaking gate size to combat shrinkage felt like puzzle-solving.
For further details on melt flow basics4 and material adjustments5, these resources really helped me. Blending hands-on practice with theory is key to mastering gate optimization.
Increasing gate width boosts melt flow rate.True
Wider gates increase the cross-sectional area, enhancing melt flow.
Narrow gates prevent weld marks in thin films.False
Narrow gates risk weld marks due to uneven melt distribution.
Conclusion
The thickness and width of a film gate in injection molding significantly influence melt flow, affecting filling speed, product quality, and material compatibility for optimal results.
-
Discover the impact of gate dimension adjustments on the appearance quality of plastic panels. ↩
-
Find strategies to enhance injection molding efficiency by understanding material properties and gate adjustments. ↩
-
This link provides insights into how gate dimensions influence the speed and consistency of melt flow, essential for optimizing part quality. ↩
-
Learn about how melt flow characteristics influence the injection molding process, focusing on optimizing film gate dimensions. ↩
-
Understand how different materials require specific film gate dimensions to improve molding outcomes. ↩