Do you want to improve your plastic injection molding process? I have been in your position. Knowing the important factors truly changes everything.
The duration of plastic injection molding is influenced by the injection cycle, material characteristics, part size and shape, and mold design. Understanding these factors can enhance production efficiency and quality.
When I first entered the world of plastic injection molding, I felt overwhelmed by the details. But over time, I learned about several key factors. These factors probably influence the duration of the process a lot. The composition of the injection cycle and the intricacies of mold design both play a role. Each element contributes. The cycle consists of injection time, cooling time and ejection time. Getting these times right is very important. Efficiency and quality depend on it. I discovered that adjusting the parameters improved our production outcomes. The whole experience became much more rewarding.
Material characteristics affect injection molding duration.True
The type of material used in injection molding influences the cycle time due to varying properties like viscosity and cooling rates.
Part size has no impact on injection molding efficiency.False
Larger parts generally require longer cycle times, impacting overall efficiency in the injection molding process.
What Makes Up an Injection Molding Cycle?
Have you ever thought about what happens during an injection molding cycle? Understanding this process not only increases manufacturing efficiency but also improves product quality. Let’s explore this together!
An injection molding cycle consists of injection, holding, cooling, mold opening, and ejection stages, vital for enhancing production speed and ensuring high-quality parts.
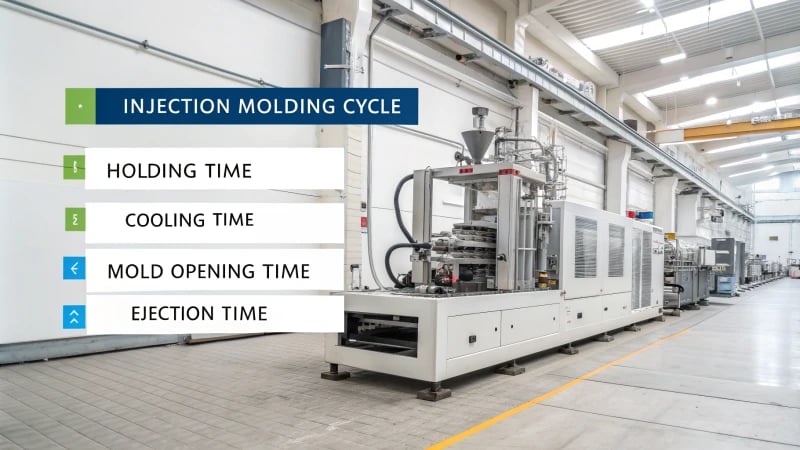
Understanding the Injection Molding Cycle
As a designer, I often admire how complex the injection molding cycle is. It feels like a well-organized dance. Each stage has a very important role in creating plastic parts with precision. The cycle includes five main stages: injection time, holding time, cooling time, mold opening time, and ejection time.
Stages of the Injection Molding Cycle
- Injection Time: This is where the process starts. Molten plastic enters the mold cavity, usually in just 0.5 to 1 second for smaller parts. Factors influencing this include:
- Fluidity of the plastic melt
- Injection pressure
- Injection speed
- Complexity of the mold cavity
Factor | Description |
---|---|
Fluidity | Determines how easily the plastic flows into the mold |
Injection Pressure | Higher pressure can increase flow rate but may affect part quality |
Injection Speed | Faster speeds reduce injection time but can lead to defects |
-
Holding Time: After the mold is filled, this phase begins. This stage is very important for keeping pressure while the plastic cools and shrinks. It usually lasts about 5-10 seconds, depending on:
- Characteristics of the plastic material
- Wall thickness of the part
-
Cooling Time: Cooling time is often the longest part of the cycle, allowing molded parts to cool and solidify in the mold. It can take 10-20 seconds for thin parts and over a minute for thicker ones. Factors affecting cooling time include:
- Thermal properties of the material
- Wall thickness and shape of the part
-
Mold Opening Time: After cooling, this step occurs quickly and takes about 1-3 seconds.
-
Ejection Time: Finally, ejection takes place when the molded part is removed from the mold cavity in about 1-2 seconds.
Influencing Factors on the Cycle Composition
- Plastic Material Characteristics: Different plastics behave differently under heat and pressure. For example, plastics with high thermal conductivity cool quickly while crystalline materials need longer times to ensure proper crystallization.
- Part Size and Shape: Bigger or thicker parts take longer to cool because they lose heat slowly; I often change my designs based on these factors when working on complex shapes.
- Process Parameters: The mix of injection speed, pressure, and holding time is important; balancing speed and quality is necessary for maintaining efficiency while meeting product standards.
- Mold Design: A good cooling system in mold design can really reduce cycle times; innovations like conformal cooling channels inspire me because they allow uniform cooling.
For those eager to learn more about optimizing these stages for better production, exploring injection molding process optimization1 is recommended.
Cooling time is the longest phase in the injection molding cycle.True
Cooling time varies significantly based on part thickness, making it the most extended phase in the injection molding process.
Mold opening time takes longer than ejection time in injection molding.False
Mold opening typically lasts 1-3 seconds, while ejection takes only 1-2 seconds, making ejection faster.
How Do Material Properties Affect Molding Duration?
Have you ever thought about how the materials we pick affect the molding process? The link between material characteristics and molding time probably really matters in our injection molding projects. Projects might change with this knowledge.
Material properties greatly impact molding duration, with thermal conductivity facilitating cooling and complex part design influencing injection speed and holding times needed for quality assurance.
Understanding Injection Molding Cycle Composition
In the workshop, I see the complex process of injection molding. Each cycle follows a timed order of events. Material properties influence everything. Here’s a quick look at the stages in an injection molding cycle:
-
Injection Time: This starts when the plastic melt enters the mold cavity. I worked with a very fluid plastic that injected in just 0.5 seconds! Fluidity, pressure and mold complexity affect this stage.
-
Holding Time: After filling, pressure holds to allow for shrinkage during cooling. This stage lasts from 5 to 10 seconds based on material and thickness. Longer holding ensures precision. Patience pays off here!
-
Cooling Time: Cooling takes the longest. Thermal properties matter the most here. Thin-walled parts cool in 10-20 seconds. Thicker parts need more than a minute. It feels like a very long time, but it helps me plan better.
-
Mold Opening and Ejection Time: These steps are quick, taking about 1-3 seconds to open and 1-2 seconds to eject. Success feels great when the part comes out easily!
Material Characteristics Impacting Molding Duration
Materials chosen impact cycle times a lot. Some materials cool faster due to high thermal conductivity – it’s a real game-changer!
Influence of Part Size and Shape
Size and shape are also important! Part dimensions and complexity affect cycles:
- Larger Parts: These cool slower because heat dissipates slowly. A large component took more time than I expected once.
- Complex Shapes: Intricate designs need adjustments in injection speed and holding time for good quality. This affects molding time, so don’t forget!
Role of Injection Molding Process Parameters
Process settings matter equally:
- Injection Speed and Pressure: Faster speeds reduce time but might hurt quality. The right balance is very important.
- Holding Pressure: Proper holding pressure ensures quality but increases cycle time too. Balancing them is a big challenge!
For more on optimizing these parameters, check out process optimization techniques.
Importance of Mold Design in Cooling Efficiency
Mold design is crucial too! A good cooling system can change everything:
- Cooling System Design: Holding Pressure:Fast cooling channels shorten cooling time. Conformal cooling designs improve uniformity and efficiency – it’s really amazing!
Optimized mold designs improve cycle times a lot.
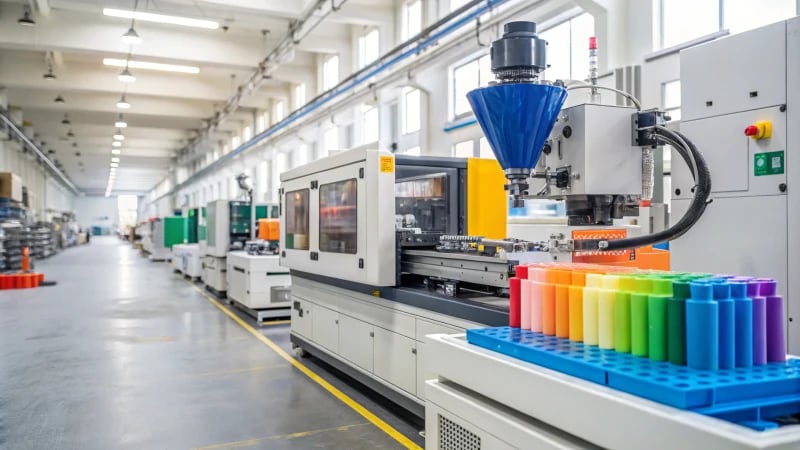
Understanding Product Design and Material Traits
I spent years working in product design and mold shaping. One thing I learned is that small details of material traits are very important. These details often hold the key to really improving our work steps. So, let’s explore this topic further together!
Importance of Material Traits in Product Design
The specific properties of materials used in product design can dramatically influence the overall quality and efficiency of the process. Here are some key factors:
Material Trait | Impact on Product Quality |
---|---|
Durability | Materials with higher durability ensure longer-lasting products. |
Flexibility | Flexible materials allow for more complex designs without breaking. |
Surface Finish | The surface finish affects both aesthetics and functionality of the product. |
For instance, selecting a material with optimal durability will not only enhance product lifespan but also improve user satisfaction.
Influence of Design Complexity and Size
The dimensions and complexity of the product being designed are critical considerations:
- Larger Products: These generally require more robust materials to maintain structural integrity.
- Complex Designs: Products with intricate designs may necessitate specialized materials to achieve desired performance characteristics.
Role of Design Parameters in Material Selection
Design parameters also play a pivotal role in determining material selection:
- Weight Considerations: Lighter materials can enhance usability but may compromise strength, necessitating a balance.
- Cost Efficiency: Selecting cost-effective materials ensures project viability while maintaining quality standards.
For a more detailed analysis of how these parameters affect product design, refer to material selection strategies2.
Importance of Testing Material Properties in Design Efficiency
Testing material properties is another critical aspect that influences design outcomes:
- Material Testing Methods: Efficient testing methods expedite selection processes and thus improve overall design duration. For example, rapid prototyping can provide immediate feedback on material performance.
Utilizing optimized testing protocols can lead to significant improvements in design efficiency. Learn more about advanced testing techniques
Higher thermal conductivity reduces cooling time in molding.True
Materials with high thermal conductivity cool faster, leading to shorter overall injection molding cycle times.
Complex part shapes always increase molding duration.False
Intricate designs may require longer injection and holding times, affecting the overall cycle duration positively or negatively based on adjustments made.
How Does Mold Design Influence Cycle Efficiency?
Have you ever thought about how mold design affects efficiency in injection molding? I have experienced this challenge while trying to understand production optimization. Let’s explore how mold design influences cycle efficiency!
Mold design plays a key role in improving cycle efficiency in injection molding. It does this by improving cooling systems, adjusting material characteristics and refining process settings. These elements cooperate to shorten cycle times. They also guarantee a top-quality outcome.
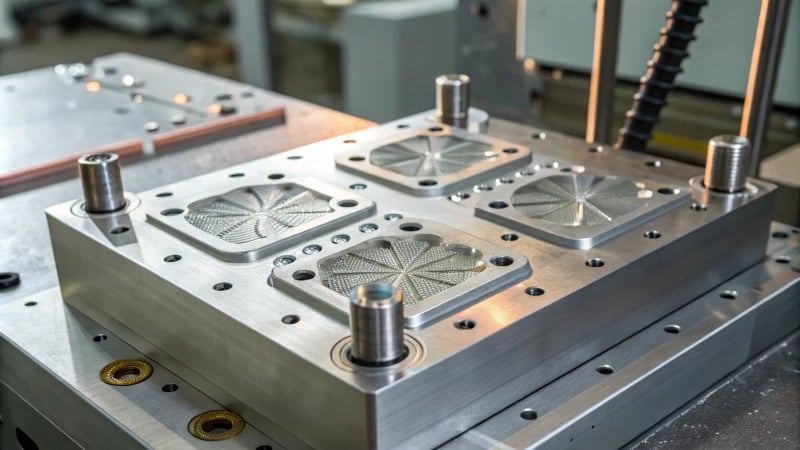
Understanding Injection Molding Cycle Steps
The injection molding cycle is like an orchestra, with each part working together for a perfect result. A full cycle includes several important steps:
-
Injection Time: Here, the process begins. Molten plastic enters the mold. When I first watched this, I was amazed. It was like a wave of molten gold filling a treasure chest! For small parts, this happens in just 0.5 to 1 second. Timing depends on plastic fluidity and mold complexity.
-
Holding Time: After filling, pressure remains for 5-10 seconds to avoid shrinkage. This is like holding onto special moments in life – just a bit longer to let things settle properly.
-
Cooling Time: This step takes the longest time. As a designer, I watch as parts cool. Thin walls cool in about 10-20 seconds, while thicker ones take over a minute. This stage tests patience, much like waiting for dough to rise!
-
Mold Opening & Ejection Time: These quick steps last 1-3 seconds for opening and 1-2 seconds for ejection. This is the cycle’s grand finale. Seeing the finished part emerge is really rewarding.
How Mold Design Improves Efficiency
Now, let’s look at how mold design impacts cycle efficiency:
- Cooling System Design: A good cooling system reduces cooling times and speeds up cycles. I’ve tried conformal cooling techniques. The results amazed me! It’s like finding the right puzzle piece that speeds up the process.
Cooling Method | Efficiency Impact |
---|---|
Conformal Cooling | High |
Standard Cooling | Moderate |
-
Material Characteristics: Plastic choices greatly affect cycle times. Materials with high thermal conductivity cool faster than crystalline ones. It’s amazing how a simple material choice affects efficiency.
-
Part Complexity: Complex shapes are tricky! I remember a project where intricate designs needed careful changes in injection speed and holding times to keep quality. Balancing these parameters is like walking a tightrope; success follows when done right.
Example: Think of a finely detailed part. Sometimes we hold it longer to keep its delicate shape.
Improving Injection Molding Parameters
Here are key parameters that improve cycle efficiency:
- Injection Speed: Faster speeds reduce injection times, but quality must stay high. It’s a balance needing skill and practice.
- Holding Pressure: Right pressure reduces defects but may increase cycle time. I often adjust settings until they work perfectly.
Conclusion on Mold Design and Cycle Efficiency
In short, good mold design improves injection molding cycle efficiency through better cooling, material selection and design details. This knowledge has improved my manufacturing practices and product quality. If you want to learn more about improving mold design, check out our detailed analysis on mold design optimization3. Together, we really achieve outstanding results!
Efficient cooling systems reduce injection molding cycle times.True
Cooling system design directly impacts cycle efficiency by minimizing cooling times, enhancing overall production speed and quality.
Complex part designs always increase injection molding cycle duration.False
While complex designs may require longer holding times, efficient mold design can mitigate delays, making this claim not universally true.
How Can I Optimize Process Parameters for Better Results?
Improving process settings feels like solving a complex puzzle in manufacturing. Trust my words. Adjusting these settings involves more than just numbers. It’s about creating something special. How do we achieve this?
To optimize process parameters, focus on understanding material properties and part design. Utilize Design of Experiments (DOE) and the Taguchi method for data-driven decisions, enhancing manufacturing efficiency and product quality.
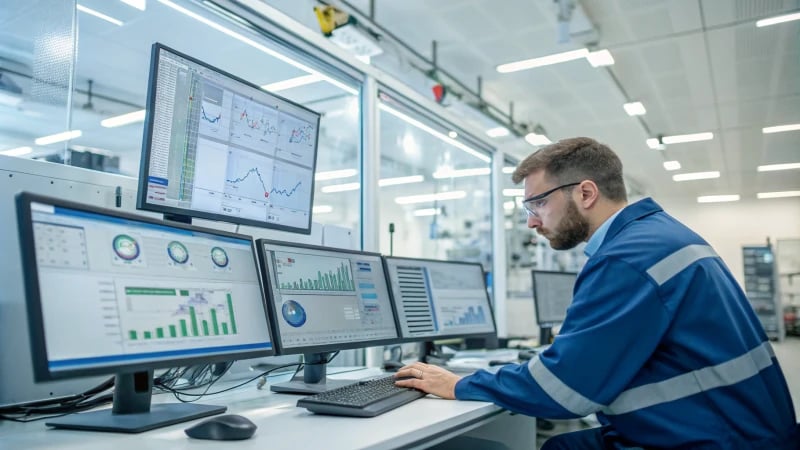
Understanding the Injection Molding Cycle
To optimize process parameters, it’s essential to grasp the composition of the injection molding cycle. This cycle encompasses several stages:
- Injection Time: Refers to how long it takes to inject the plastic melt into the mold cavity.
- Typical Duration: Usually within 0.5-1 second for small parts.
- Holding Time: The time pressure is maintained after filling the mold, generally between 5-10 seconds.
- Cooling Time: A significant duration where the plastic solidifies, varying greatly based on material properties.
- For thin-walled parts, this may be around 10-20 seconds, while larger parts might exceed 1 minute.
- Mold Opening and Ejection Time: These are relatively short, usually around 1-3 seconds each.
Optimizing each of these stages can lead to improved efficiency and product quality. For a more detailed breakdown of these phases, refer to this comprehensive guide4.
Influencing Factors on Optimization
Several influencing factors can dictate how effectively you can optimize your process parameters:
Factor | Description | Impact on Cycle Time |
---|---|---|
Plastic Material Characteristics | Different materials have distinct thermal and rheological properties. | High thermal conductivity reduces cooling time, while crystalline plastics require longer cooling. |
Part Size and Shape | Larger or complex parts need more careful parameter adjustments. | Increased size can significantly lengthen cooling time due to heat dissipation. |
Injection Molding Process Parameters | Parameters like injection speed and pressure impact cycle time and part quality. | Faster injection speeds can shorten times but may reduce quality if not managed well. |
Mold Design | An efficient mold design with optimized cooling channels can greatly improve cycle times. | Conformal cooling designs can accelerate cooling processes. |
By addressing these factors, you can achieve a better balance between efficiency and product integrity. For more insights into the influence of material properties on injection molding, check out this article5.
Methodologies for Optimization
To effectively optimize process parameters, employing methodologies like Design of Experiments (DOE) and the Taguchi method can yield substantial benefits:
- Design of Experiments (DOE): This statistical method allows you to systematically change multiple variables to identify their effect on outcomes. By conducting controlled experiments, you can find the optimal settings for injection speed, pressure, and cooling times.
- Taguchi Method: Focused on robust design, this approach aims to improve quality by minimizing variation through careful parameter selection. It helps in identifying which parameters are most significant to performance and consistency.
Using these methodologies provides actionable insights and leads to data-driven decisions that enhance overall efficiency. For more detailed methodologies related to manufacturing optimization, please visit this resource6.
Injection time typically lasts 0.5-1 second for small parts.True
This claim reflects the standard duration for injection time in the injection molding cycle, which is crucial for optimizing efficiency.
Using DOE can improve injection molding process efficiency.True
Design of Experiments (DOE) systematically tests variables, leading to optimized settings and improved manufacturing outcomes.
Conclusion
Key factors affecting plastic injection molding duration include cycle stages, material characteristics, part dimensions, process settings, and mold design. Mastering these can improve production efficiency.
-
Learn more about optimizing each stage of the injection molding process for better efficiency and quality. ↩
-
Discover how different material properties can optimize your molding processes and improve product quality. ↩
-
Explore advanced techniques in mold design that can improve cycle efficiency and reduce production time. ↩
-
Explore effective optimization techniques that can enhance your production processes for improved results. ↩
-
Learn about the methodologies that can help streamline your manufacturing processes. ↩
-
Discover the impact of different material characteristics on injection molding cycles. ↩