Choosing the right injection mold cooling system is crucial for delivering high-quality products efficiently.
To choose an effective injection mold cooling system, consider factors like the cooling medium (water, oil, or air), cooling pipe design, system controls, and the requirements of mold materials and products. These elements impact efficiency, quality, and cost.
But there’s so much more beneath the surface! Let’s delve deeper into each of these factors to unlock their secrets and empower your production process.
Water is the most cost-effective cooling medium for molds.True
Water has low cost and high heat dissipation, making it ideal for molds.
How Does Cooling Medium Selection Affect Mold Performance?
The choice of cooling medium in injection molding dramatically influences mold performance, product quality, and operational costs.
Selecting the right cooling medium—whether water, oil, or air—affects the heat dissipation efficiency, maintenance needs, and suitability for specific molding environments. Each medium offers unique advantages and challenges that impact mold performance and production efficiency.
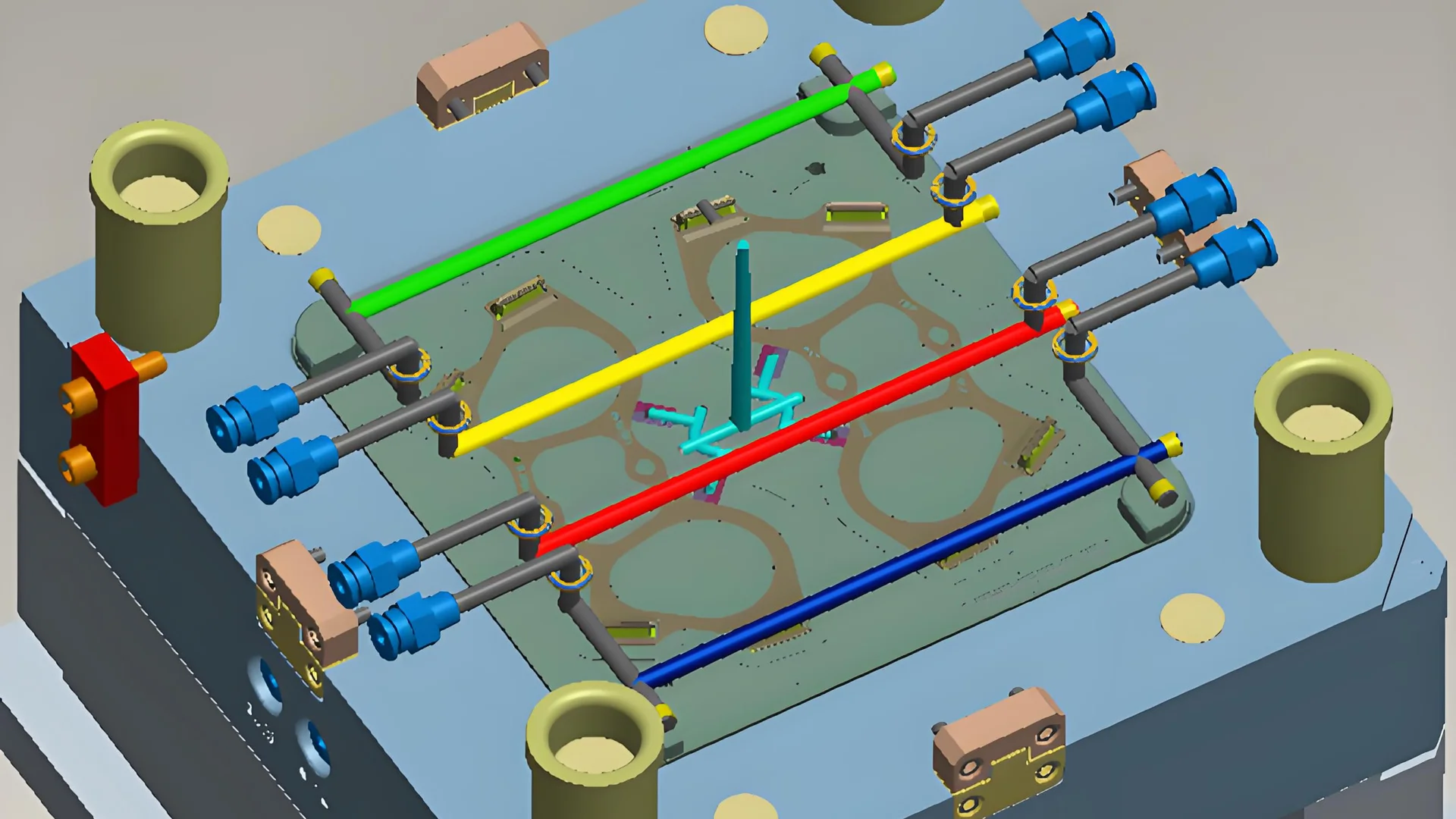
The Role of Water in Mold Cooling
Water is often the go-to cooling medium due to its exceptional heat dissipation capabilities and cost-effectiveness. Its large specific heat capacity allows it to absorb significant heat from the mold rapidly, effectively reducing mold temperature. However, water quality can affect performance; impurities may lead to scaling within the cooling channels, impacting efficiency. In colder climates, water might freeze, necessitating preventive measures.
Advantages | Disadvantages | Applications |
---|---|---|
Low cost | Potential for scale formation | Most injection molds with moderate cooling |
High heat dissipation | Risk of freezing in cold climates | |
Easily accessible |
Utilizing Oil for High-Temperature Molding
Oil is another viable cooling medium, particularly in scenarios requiring electrical insulation or operating at higher temperatures. Its high boiling point makes it suitable for molds that must withstand intense heat. Though more costly than water, oil provides a safer option in environments where electrical corrosion is a concern.
Despite its advantages, oil’s heat dissipation ability is slightly less effective than water’s, and it can be cumbersome to clean up spills or leaks. Thus, oil is best suited for high-temperature applications or those with strict insulation requirements.
Air as a Simple Cooling Solution
Air cooling offers simplicity, requiring no additional supply systems. It forms natural convection currents to carry away heat, making it suitable for smaller molds with low cooling demands. However, its limited heat dissipation capability restricts its use to auxiliary roles or simple, small injection molds.
Advantages | Disadvantages | Applications |
---|---|---|
No additional supply system | Poor heat dissipation | Simple small molds or auxiliary cooling |
Easy implementation | Limited to low-demand scenarios |
Considerations for Medium Selection
Choosing the right cooling medium involves understanding your specific molding requirements. Evaluating the thermal conductivity1 of your mold materials alongside product specifications can guide your decision. Also, consider the maintenance implications of each medium—such as cleaning needs for oil or water quality management—and their impact on long-term operational costs and mold longevity.
Understanding these nuances allows manufacturers to tailor their cooling systems effectively, enhancing both performance and efficiency.
Water is the most cost-effective cooling medium.True
Water is low-cost and offers high heat dissipation, making it economical.
Oil has better heat dissipation than water.False
Oil's heat dissipation is less effective than water's, despite its high boiling point.
What Role Does Cooling Pipe Design Play in Efficiency?
A well-designed cooling pipe system can significantly enhance injection molding efficiency and product quality.
Cooling pipe design is crucial for maintaining uniform mold temperatures, preventing defects, and optimizing the cooling process. Proper layout, diameter, spacing, and connection methods are vital considerations for achieving efficient heat dissipation.
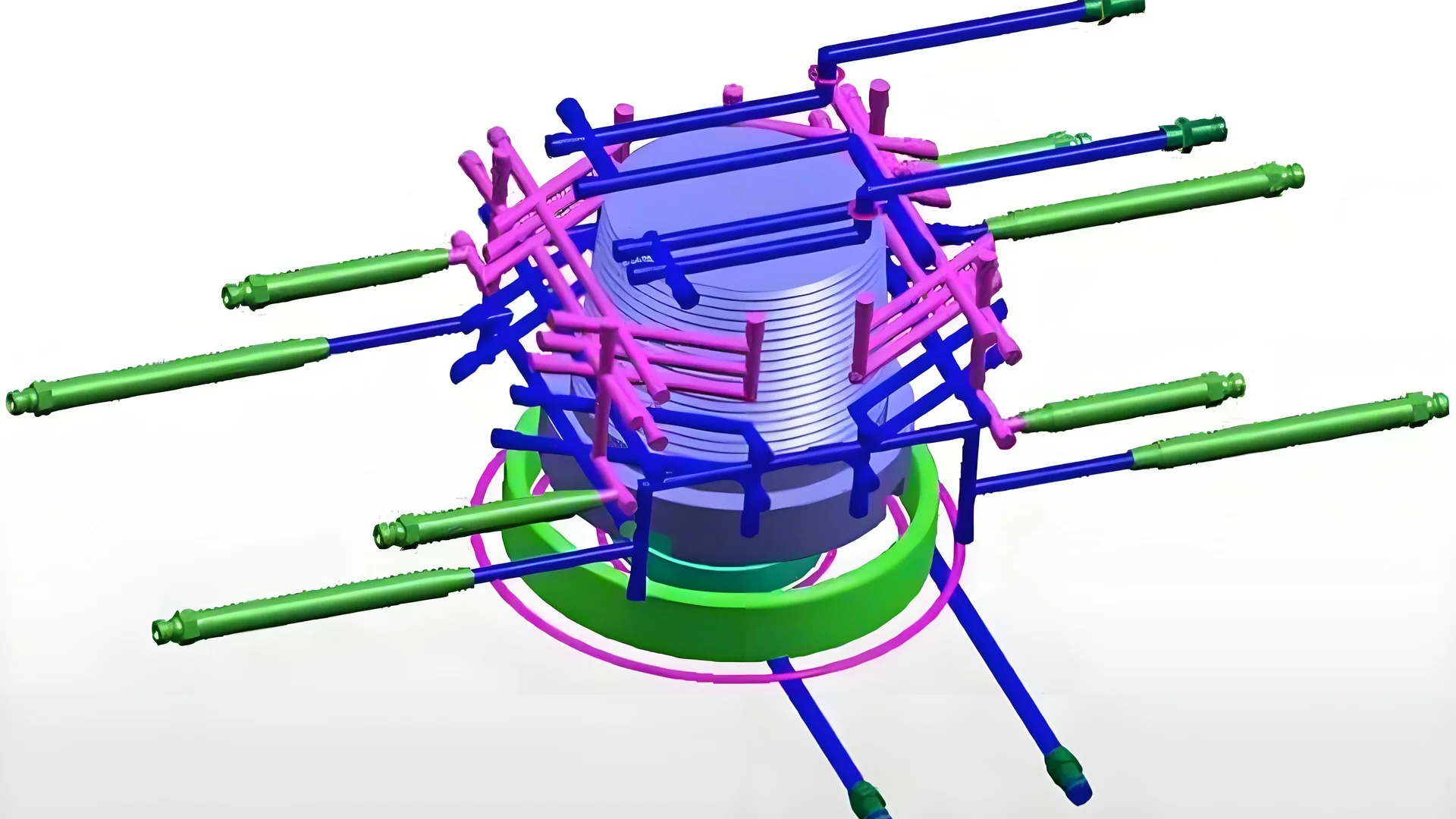
Pipeline Layout: Ensuring Even Cooling
The layout of cooling pipes within a mold is pivotal for uniform temperature distribution. For optimal results, pipes should be strategically distributed across essential areas like the cavity and core. This prevents localized overheating or overcooling, reducing defects such as warping or shrinkage. In cases where molds have intricate shapes, utilizing multi-layer or specially-shaped pipes can further enhance the cooling effect. Explore innovative pipeline layout strategies2 to tailor the cooling system to complex mold designs.
Pipeline Diameter and Spacing: Balancing Flow and Space
Choosing the correct diameter and spacing for cooling pipes is essential for balancing effective cooling with mold integrity. Larger diameters facilitate better flow rates, improving heat dissipation but at the cost of occupying more mold space. Conversely, smaller diameters can constrain flow but conserve space. Generally, a pipe spacing of 20mm to 50mm is recommended to ensure adequate cooling without compromising mold structure. Investigate optimal pipe configurations3 to match specific cooling needs and mold sizes.
Pipe Connection Methods: Ensuring Reliability and Maintenance Ease
Reliable connections are critical to preventing leaks that could lead to cooling failures or mold damage. Common methods include welding, threaded connections, and quick connectors, each suitable for different operational contexts. Quick connectors, for instance, are ideal for molds requiring frequent disassembly for maintenance. When selecting a connection method, consider the ease of maintenance4 alongside environmental factors and operational demands.
Temperature and Flow Control: Achieving Precision
Temperature control systems, equipped with sensors and PID controllers, enable precise regulation of mold temperatures by adjusting cooling medium flow rates. This precision helps avoid temperature extremes that could affect product quality. Additionally, controlling flow rates with flow meters and regulating valves ensures optimal cooling speeds tailored to specific injection processes. Explore advanced temperature control systems5 to enhance molding precision and efficiency.
Larger pipe diameters improve heat dissipation.True
Larger diameters allow better flow rates, enhancing heat dissipation.
Quick connectors are unsuitable for frequent disassembly.False
Quick connectors are ideal for molds needing frequent disassembly.
How Can Cooling System Controls Optimize Production?
Unlock the potential of your manufacturing line with optimized cooling system controls that boost efficiency and product quality.
Cooling system controls optimize production by maintaining precise temperature, flow, and cooling time, ensuring consistent product quality and efficient manufacturing.
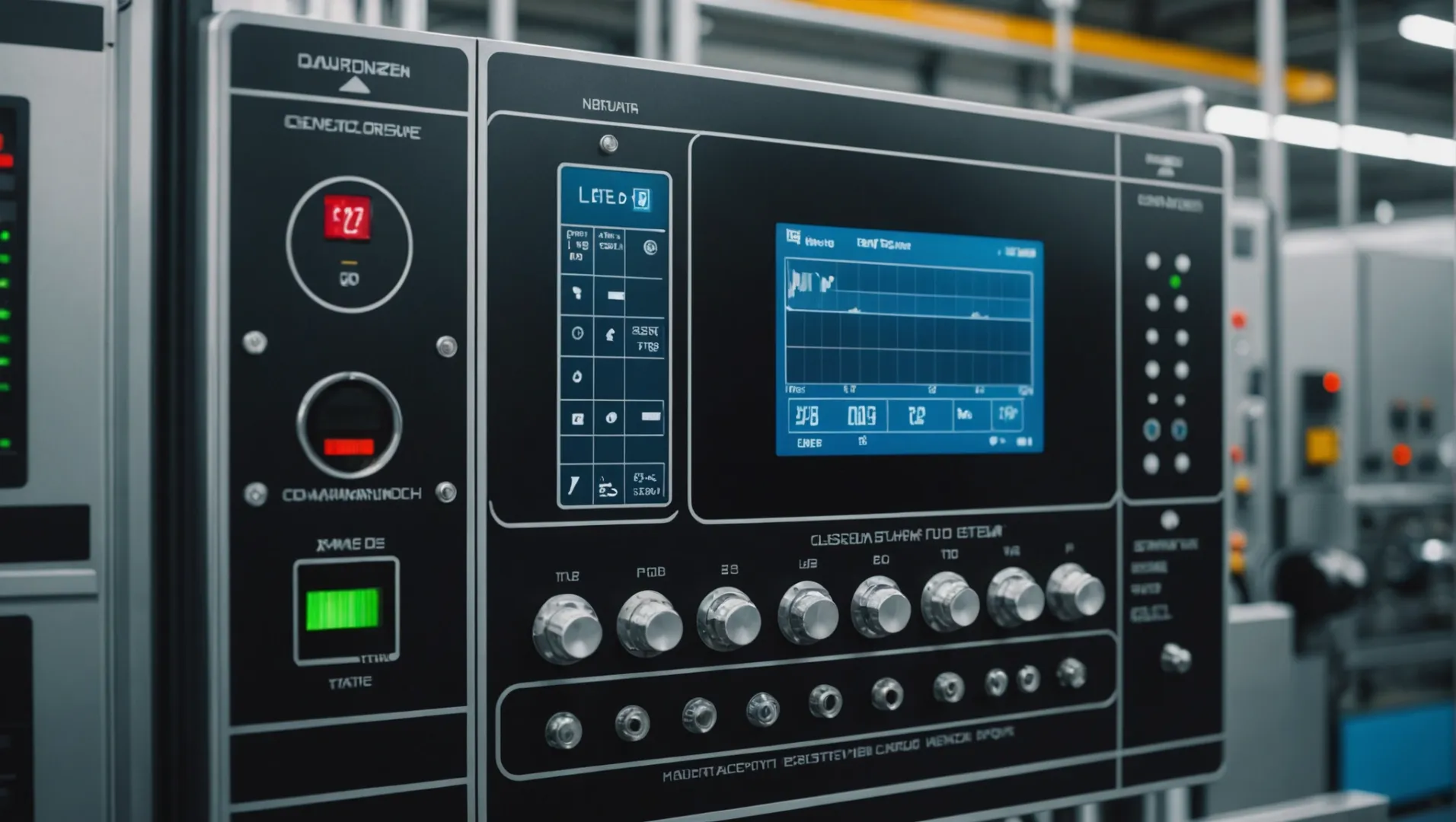
The Importance of Temperature Control
Temperature control is a critical aspect of any cooling system in manufacturing. By installing temperature sensors to monitor mold temperatures in real time, manufacturers can ensure that the temperature remains within a suitable range. This precise control helps prevent issues like overheating, which can lead to defects in the final product. Implementing automatic control equipment such as a PID controller allows for nuanced adjustments in temperature, which can be tailored to specific production needs6.
Flow Rate Adjustments
The flow rate of the cooling medium directly impacts the speed at which the mold cools. An optimal flow rate ensures that the mold temperature is maintained without compromising product quality. Equipment such as flow meters and regulating valves are essential for adjusting the flow rate as needed. This is particularly important when dealing with molds that have varying cooling requirements7 based on the complexity or size of the product being manufactured.
Cooling Time Management
Effective cooling time management is vital for optimizing production. If the cooling time is too short, it can lead to product deformation and dimensional instability. Conversely, excessively long cooling times reduce production efficiency. Determining the appropriate cooling time often involves experimentation and leveraging previous experiences. By carefully monitoring and adjusting the cooling duration during production, manufacturers can achieve a balance that enhances both quality and output.
Integration with Mold Materials and Product Specifications
The integration of cooling system controls with mold materials and product specifications is another key consideration. Different materials have unique thermal conductivity properties, influencing how they interact with cooling systems. For example, steel molds may require different cooling strategies compared to aluminum alloy molds. Similarly, products with thicker walls or intricate shapes may necessitate specialized cooling approaches to prevent defects such as shrinkage cavities.
In conclusion, by understanding and implementing advanced cooling system controls, manufacturers can significantly improve their production outcomes. These controls not only enhance product quality but also streamline operational efficiency, leading to reduced production costs and higher output quality. For more detailed insights into each aspect of cooling system controls, explore additional resources and expert opinions available online.
PID controllers adjust temperature in real-time.True
PID controllers use feedback to maintain precise temperature control.
Flow meters are unnecessary in cooling systems.False
Flow meters are crucial for monitoring and adjusting flow rates.
Why Are Mold Materials and Product Requirements Critical?
Understanding the significance of mold materials and product requirements is crucial for achieving high-quality injection molding results.
Mold materials and product requirements determine cooling efficiency and final product quality. The choice of mold material affects thermal conductivity, while product specifications influence cooling system design. Selecting appropriate materials and meeting product needs ensures superior mold performance and end-product excellence.
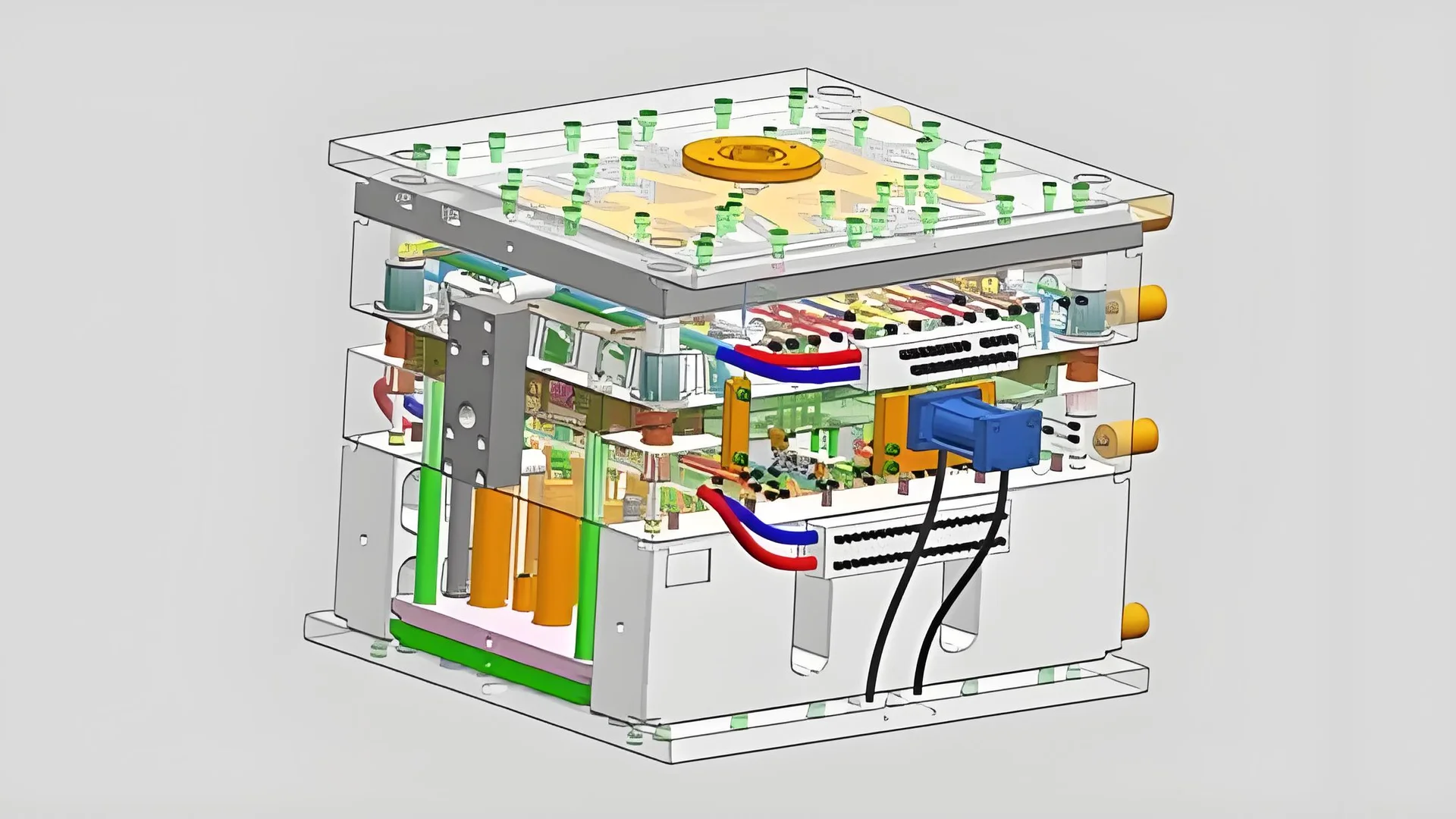
The Importance of Mold Materials in Cooling Systems
The choice of mold material directly impacts the thermal conductivity and, consequently, the cooling efficiency of an injection mold. For instance, steel molds are known for their excellent thermal conductivity, which facilitates rapid heat dissipation, reducing cycle times and enhancing productivity. In contrast, aluminum alloy molds, while lighter and easier to machine, have relatively lower thermal conductivity, which may require additional cooling considerations.
Specialty materials like hot work die steel might need unique cooling methods8 such as spray cooling to manage temperature effectively. This highlights the importance of aligning the mold material with the cooling system design to maintain optimal temperature control and prevent defects.
Product Requirements: Shaping the Cooling Strategy
Product specifications, including shape, size, and wall thickness, significantly influence the design of the cooling system. For products with thicker walls, enhanced cooling is necessary to avoid issues like shrinkage cavities. In such scenarios, strategically placed cooling channels can ensure even temperature distribution across the mold surface.
Furthermore, products requiring high surface quality demand meticulous cooling system design to prevent uneven cooling, which can lead to surface defects or warping. By considering these requirements, manufacturers can design a cooling system that not only meets but exceeds production expectations.
Balancing Mold Material and Product Needs
To achieve an ideal injection molding process, it’s essential to strike a balance between mold material properties and product demands. Evaluating factors such as thermal expansion coefficients and surface finish compatibility can guide the selection of both mold materials and product designs.
For example, if a product requires a specific surface finish, choosing a mold material that complements this requirement will be crucial. Similarly, understanding the thermal properties of mold materials can help in deciding whether additional cooling techniques9 are needed to meet stringent product specifications.
This comprehensive approach ensures that both mold material characteristics and product needs are integrated into the design process, leading to superior injection molding outcomes.
Steel molds have higher thermal conductivity than aluminum.True
Steel's thermal properties facilitate rapid heat dissipation, unlike aluminum.
Thicker products require less cooling to avoid shrinkage cavities.False
Thicker walls need more cooling to prevent shrinkage and defects.
Conclusion
By carefully considering these factors, you can enhance injection molding efficiency and product quality while reducing costs. Reflect on your specific needs to make the best choice.
-
Learn how mold material affects cooling medium selection.: For several decades now, the thermal conductivity of conventional tool steels used for plastic injection molding has been limited to 12-20 Btu/( … ↩
-
Discover tailored pipeline layouts for complex mold designs.: Keep the cooling system a proper distance from the parting line and the molded part. Make sure the cooling line diameter is large enough to … ↩
-
Learn about pipe configurations that enhance cooling efficiency.: When you take the part out of the mold, it needs to be cooled below the heat distortion temperature. This stops the part from relaxing and … ↩
-
Understand maintenance-friendly connection methods.: Three types of maintenance are performed on piping systems: routine periodic inspections, physical changes or expansions to a piping system, and unscheduled … ↩
-
Find systems that enhance molding precision and efficiency.: Integrating heating and cooling into the mold helps improve injection-molding control and flexibility. ↩
-
Explore how PID controllers ensure precise temperature regulation in cooling systems.: The purpose of a PID controller is to force feedback to match a setpoint, such as a thermostat, that forces the heating and cooling unit to turn on or off based … ↩
-
Learn about ideal flow rates to maintain effective mold cooling.: An important “rule of thumb” is that the capacity of a chiller is reduced by 2% per ËšF below 50ËšF. So, if the temperature is reduced by 5ËšF to 45ËšF, the … ↩
-
Explore innovative techniques for managing temperature in specialized molds.: The first part involves optimization of water flow rate and spray impingement height based on maximum surface cooling rate and heat flux value. The highest … ↩
-
Discover cutting-edge solutions to optimize your injection molding process.: For example, building several smaller cooling channels into the mold rather than one large one will provide more consistent results. ↩