Have you ever felt your production line crawls like a snail?
Long cooling times in injection molds depend on product thickness and material type. Sticking to industry rules also matters. If cooling takes too long, it hurts our efficiency. It ties up our equipment. It might even ruin product quality. Product quality can really suffer.
Understanding these factors is just one part. To really reduce cooling times and achieve better manufacturing results, it’s very important to explore how each element interacts. I once saw our schedule slip because the cooling time increased without us noticing. That experience showed me the need to watch every detail closely. Let’s look into this more.
Cooling time for thin-walled parts exceeds 40 seconds.True
For thin-walled parts, cooling times over 30-40 seconds are excessive.
Extended cooling time increases equipment utilization rate.False
Long cooling times decrease equipment utilization by causing delays.
How Do Material Properties Influence Cooling Duration?
Do you know why some materials lose heat quickly? Their special qualities are the reason.
Material properties are important for cooling rates. Properties like thermal conductivity, specific heat and density are crucial. They affect how materials cool. Production processes such as injection molding depend on these properties. Materials solidify at different speeds. This influences both efficiency and quality.
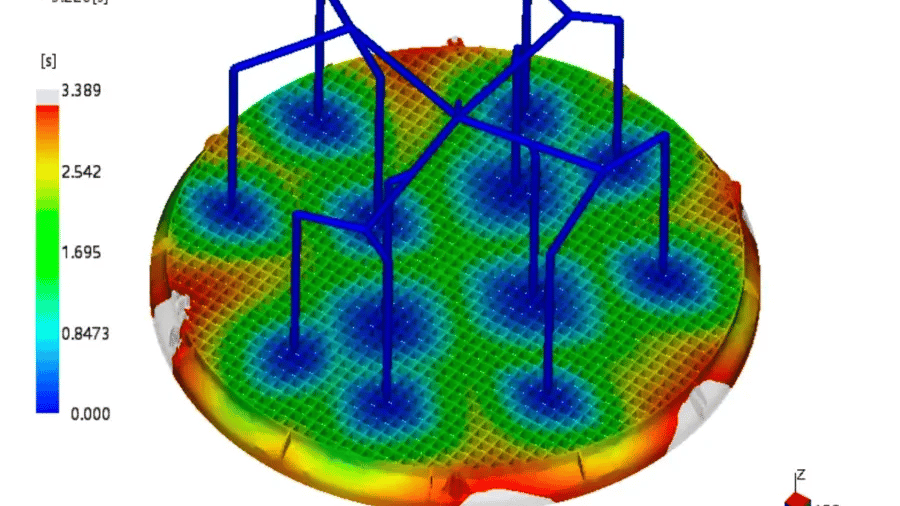
My Journey with Thermal Conductivity
I remember learning how much materials matter in cooling. This happened when I worked on some DIY projects in my garage. I had just finished a small metal sculpture. To my surprise, it cooled down very fast. That’s when I discovered thermal conductivity. Metals transfer heat quickly, so my sculpture was ready to touch soon after. But when I used plastic, I waited what seemed like an eternity. Plastics are slower at cooling because they have lower thermal conductivity.
Specific Heat Capacity: A Lesson in Patience
Another key moment was while baking cookies. The aluminum cookie sheet took ages to cool down. I found out this was due to its specific heat capacity, which is the energy needed to change its temperature. Materials like my cookie sheet store lots of heat and take a long time to release it. Patience is necessary here!
Density and Thermal Diffusivity in Everyday Life
Density taught me about cooling on a summer camping trip. We used ice packs to chill our cooler. The denser packs lasted longer without melting because density influences thermal diffusivity—a measure of how quickly heat travels compared to how much the material can store.
Impact on Industrial Standards
In industries, cooling and production times matter a lot, especially in injection molding4. Thin-walled parts should cool within 30-40 seconds; longer times cause production delays, similar to how my homemade ice cream faced issues without a good freezer.
Equipment Utilization: A Production Balancing Act
Think about your coffee machine taking forever—slow cooling makes equipment idle in factories too, lowering usage rates and hurting productivity. Running machines efficiently is really important in manufacturing.
Safeguarding Product Quality
I once tried making a clear soap bar at home that ended up with ugly streaks due to improper cooling times causing defects—similar issues occur with transparent plastics5. Correctly matching cooling with material properties avoids these issues as good quality depends on proper cooling.
Cooling time over 30 seconds is excessive for thin parts.True
For thin-walled injection molded parts, cooling over 30 seconds is excessive.
Excessive cooling time improves product dimensional accuracy.False
Excessive cooling time can cause dimensional inaccuracies, not improvements.
Why Should We Stick to Industry Standards for Cooling Times?
Cooling times play a major role. They are vital for smooth operation. They keep processes steady. High quality depends on these times. Cooling times are crucial for top-notch results. They really matter.
Following industry standards for cooling times is essential. It keeps products good and probably extends the life of machines. These rules stop problems like defects and downtime. Manufacturing stays smooth and durable with them.
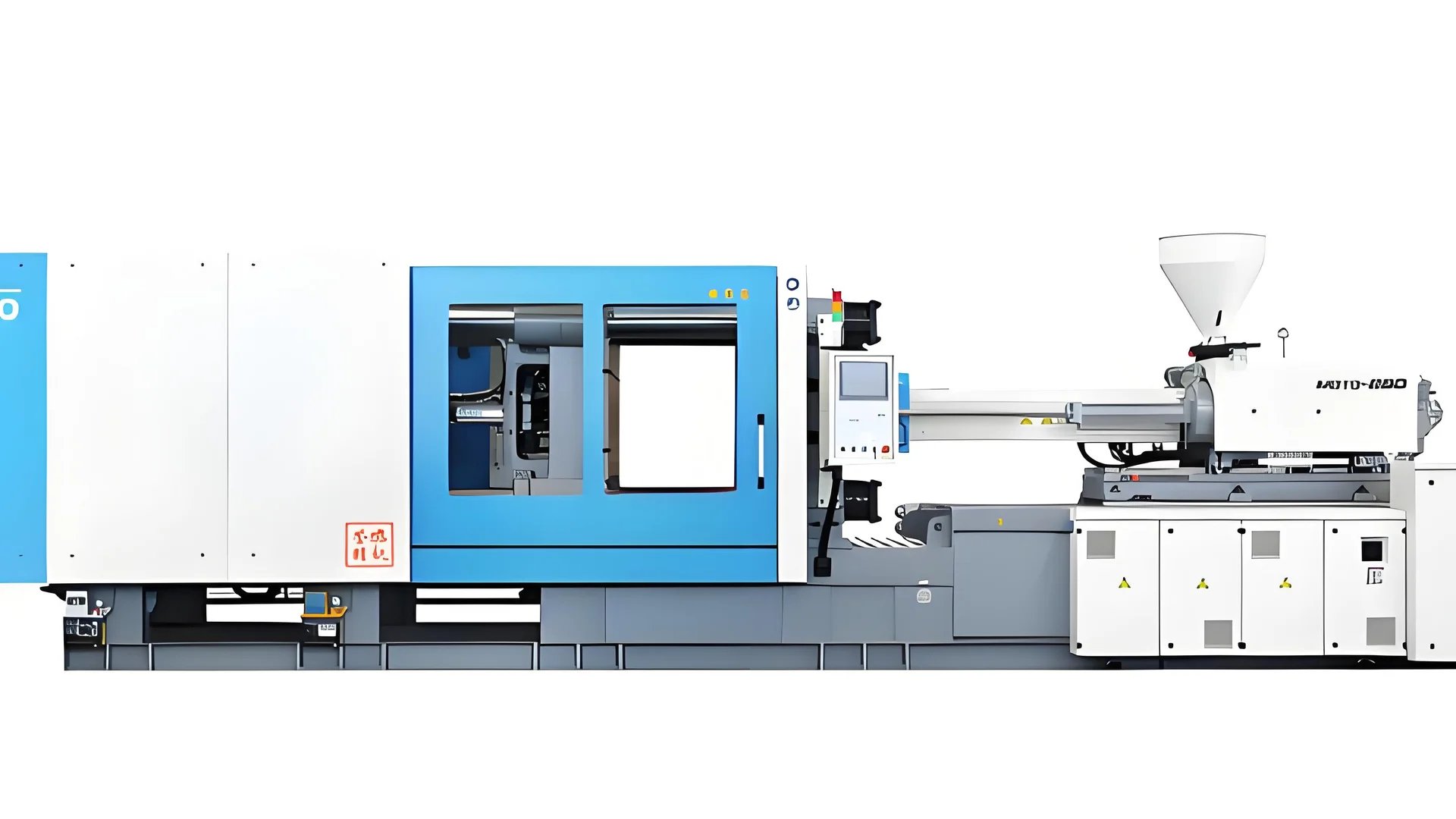
The Importance of Industry Standards in Cooling Times
Industry standards are more than just numbers; they help keep our work quality good. In the injection molding industry6, guidelines suggest that thin parts need 40 seconds, while thick parts require 120 seconds. These are not just numbers; they are lessons to keep our products great.
Specific product standards also play a significant role. For instance, I worked on electronic casings once, where cooling needed 20-30 seconds max to avoid any bad parts. Automotive interior parts follow similar norms based on size and thickness for the best results.
Effect on Production Efficiency
I have seen how a small change in cooling time changes everything. Imagine planning for 60 seconds but cooling takes 75 seconds—that’s a 25% drop in work speed! It’s not just about finishing on time; it’s about keeping things running smoothly.
Another crucial aspect is equipment utilization. Machines should not sit idle—idle machines are like parked cars that do nothing. Standard times keep the equipment busy at optimal use rates of 70-80%.
Protecting Product Quality and Mold Life
Long cooling times have caused problems in quality. I remember a project with size errors due to extra cooling, where tolerances were exceeded, affecting assembly performance. Looks matter too; appearance quality7 can deteriorate with visible defects like cold marks or warping due to improper cooling.
It’s also about molds—too much cooling damages molds, leading to cracks or rust appearing over time. Sticking to standards prevents these costly problems, extending mold life and reducing repairs.
In conclusion, industry standards are not just rules to follow—they help improve every part of production. From keeping quality to maintaining machines, industry standards8 really are crucial in manufacturing. Trust me, they are worth every second.
Cooling time over 40s for thin-walled parts is excessive.True
For thin-walled parts, cooling times exceeding 30-40 seconds are excessive.
Long cooling times never affect equipment utilization negatively.False
Excessive cooling reduces equipment utilization, dropping it below 70-80%.
How Can Excessive Cooling Time Impact Production Efficiency?
Have you ever thought about how a few extra seconds slow down your production line? Let’s explore why cooling times are more important than you might realize.
Too much cooling time in manufacturing, such as injection molding, reduces output efficiency. It stretches cycle times, wastes tools and threatens the quality of products. Adjusting cooling times to meet industry standards keeps productivity high. This is crucial for making sure that product quality stays excellent.
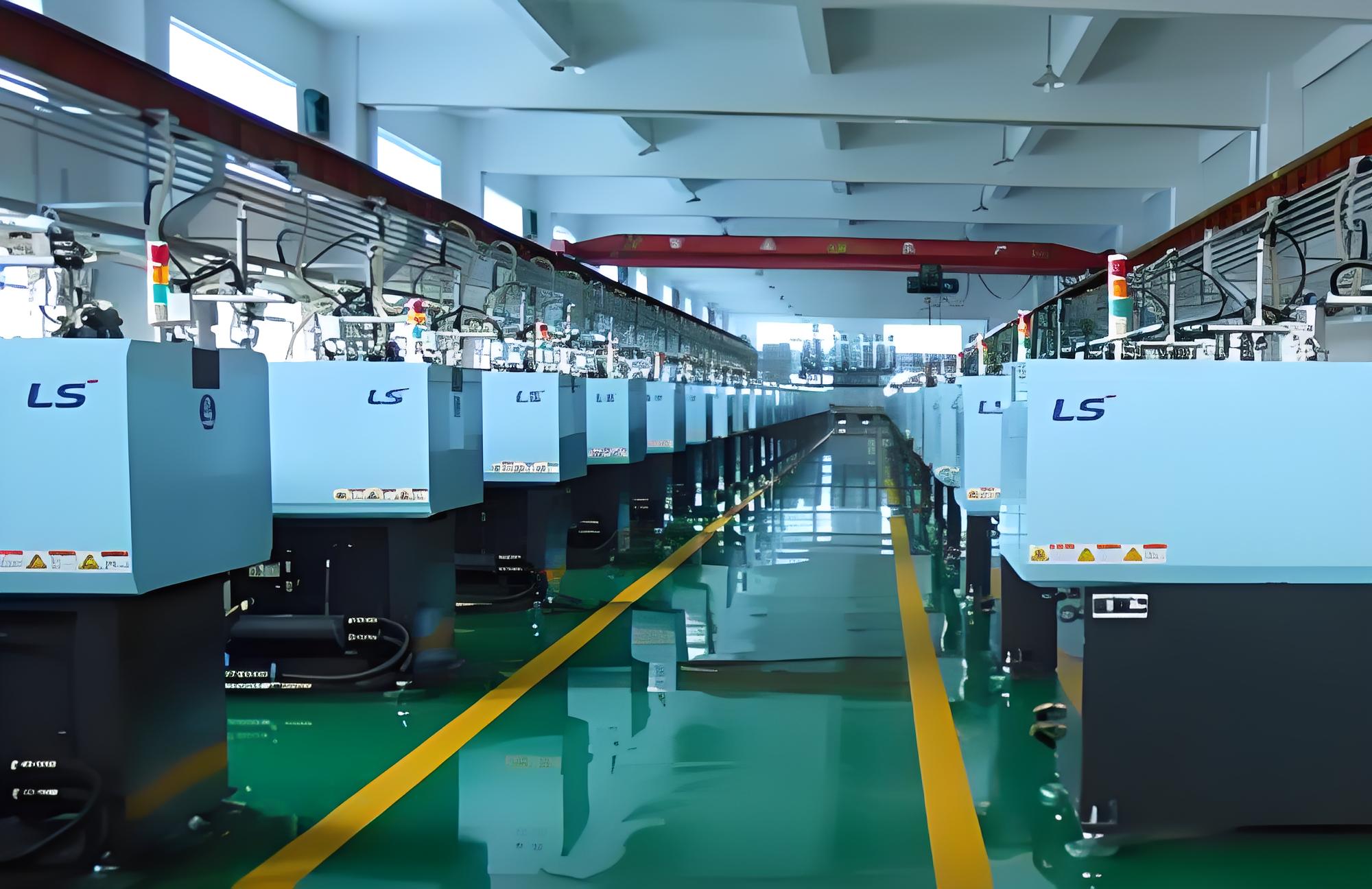
Understanding Cooling Time Standards
I remember my first visit to a busy factory floor. The machines created a rhythm like music. But if cooling takes too long, it feels like a sudden silence. Industries like injection molding need to follow cooling time rules. Thin parts cool in less than 30-40 seconds. Thick parts may cool in 100-120 seconds. Ignoring these times often requires changing the process.
Effects on Molding Cycle and Equipment Utilization
Long cooling shifts the whole production cycle. Picture being at a concert where the band pauses too long. The energy drops. Similarly, if cooling takes 45 instead of 30 seconds, a 60-second cycle might stretch to 75 seconds. Output might drop by over 20%, making it difficult to meet production schedules—like missing a beat in a song. Machines sit idle, waiting to cool parts, lowering equipment utilization rates below the ideal range of 70-80%. This is inefficient for overall production9 operations.
Impact on Product Quality
It’s frustrating to spend time on a project and then face issues. Too much cooling causes size mistakes; parts may not fit due to shrinking. Imagine designing with a tolerance of ±0.1mm and seeing ±0.2mm instead—it’s a problem! Transparent plastics can get unwanted marks if cooled too much, affecting aesthetics and functional integrity. Maintaining dimensional accuracy10 and visual quality is essential for consumer satisfaction and brand reputation.
Influence on Mold Life
Long cooling also harms molds over time—it’s like leaving a car engine on without moving; eventually, wear and tear show up. Cooling for too long leads to mold damage like thermal fatigue or corrosion, reducing their lifespan and increasing maintenance costs—affecting the mold’s durability11. Monitoring mold conditions and adjusting cooling times can mitigate these issues, prolonging mold life and maintaining consistent production levels.
Cooling time over 40 seconds is excessive for thin-walled parts.True
Thin-walled parts should cool in less than 40 seconds to avoid inefficiency.
Long cooling times improve injection mold equipment utilization.False
Excessive cooling times reduce equipment utilization, lowering productivity.
Conclusion
Excessive cooling times in injection molds, influenced by product thickness and material properties, significantly impact production efficiency, product quality, and mold life, necessitating adherence to industry standards.
-
Discover how cooling time affects overall production efficiency. ↩
-
Learn strategies to improve efficiency in cooling processes. ↩
-
Understand how cooling time influences dimensional accuracy. ↩
-
Explore how thermal conductivity impacts injection molding processes. ↩
-
Find methods to prevent cold marks in transparent plastic products. ↩
-
Gain insights into specific cooling time benchmarks in injection molding. ↩
-
Understand how improper cooling affects product aesthetics. ↩
-
Explore why standards are vital in optimizing manufacturing processes. ↩
-
Discover how prolonged cooling impacts machinery downtime and productivity. ↩
-
Learn techniques for ensuring precision in molded parts. ↩
-
Understand how cooling duration influences mold lifespan. ↩