Ever wonder how to perfect the cooling time in injection molding?
The right cooling time in injection molding depends on part thickness, material properties, and mold design, affecting cooling efficiency and product quality.
I remember my early days in the mold industry when I first realized how crucial cooling time was. It was a challenging project where we struggled with warped parts and costly delays. That’s when it hit me: every second counts. Understanding the role of part thickness was a game-changer. Thicker parts, like those I worked on for a consumer electronics line, always took longer to cool, often leading to bottlenecks in production if not properly managed.
Material properties were another eye-opener for me. The intricacies of different plastics meant that what worked for one type didn’t necessarily work for another. And let’s not forget mold design; it’s like the silent director behind the scenes, dictating how smoothly things run. Diving into these elements not only improved my projects but also brought efficiency to the whole process. In this blog, let’s explore these aspects further and uncover how they can enhance your molding journey.
Part thickness affects cooling time in injection molding.True
Thicker parts take longer to cool, affecting cycle times.
Material properties have no impact on cooling time.False
Different materials conduct heat differently, altering cooling rates.
How Does Part Thickness Affect Cooling Time?
Ever wondered why some parts take longer to cool in injection molding? It’s all about the thickness!
Thicker parts in injection molding require longer cooling times due to higher material volume retaining heat, impacting cycle times and product quality.
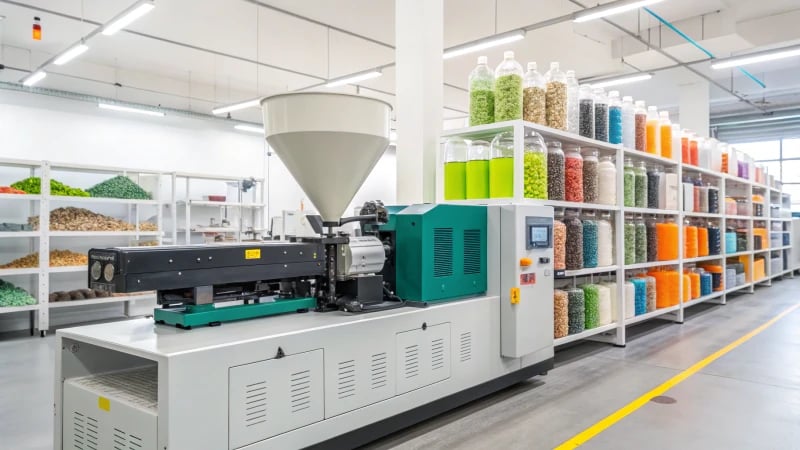
Understanding the Relationship Between Thickness and Cooling Time
Have you ever found yourself waiting impatiently for something to cool down? Like that piping hot cup of coffee you couldn’t resist but sip a little too soon? That’s precisely what happens in the world of injection molding when part thickness1 comes into play. The thicker the part, the longer it takes to cool off. It’s like trying to ice a cake with an extra layer; the more material there is, the more time it needs to settle into a solid state.
Heat Transfer Dynamics
I remember working on a project where we had to mold a particularly thick piece. It was a real puzzle because the heat just didn’t want to leave the party! The rate of heat transfer in these situations is slower, much like when you’re bundled up in layers during a Canadian winter—each layer adds resistance to the cold. Engineers often use software to simulate cooling rates2, tweaking designs to dodge those prolonged wait times.
Part Thickness | Cooling Time |
---|---|
Thin | Short |
Moderate | Moderate |
Thick | Long |
Influence on Product Quality
Longer cooling times can sometimes be a bit of a double-edged sword. I once faced an issue where a project component warped because it cooled unevenly. Just like leaving your snow boots too close to the heater overnight, it ended up looking pretty wonky by morning. By adjusting the mold design3, we managed to get everything back on track, ensuring even thick parts cooled evenly.
Material Considerations
And let’s not forget, not all materials are created equal. Some polymers can handle thickness with ease due to higher thermal conductivity, like finding that perfect blanket that’s warm but not stifling. So, when designing components, it’s essential to consider these material properties4 for optimal cooling rates.
Thicker parts always cool faster than thinner parts.False
Thicker parts have more heat to dissipate, slowing cooling time.
Material choice can affect cooling time in thick parts.True
Materials with higher thermal conductivity may reduce cooling time.
How Do Material Properties Influence Cooling Time?
You know, sometimes the smallest details can make the biggest difference. Especially when it comes to understanding how materials behave during cooling!
Material properties such as thermal conductivity, specific heat capacity, and viscosity significantly affect cooling time by determining heat transfer efficiency, influencing cooling efficiency and production quality in processes like injection molding.
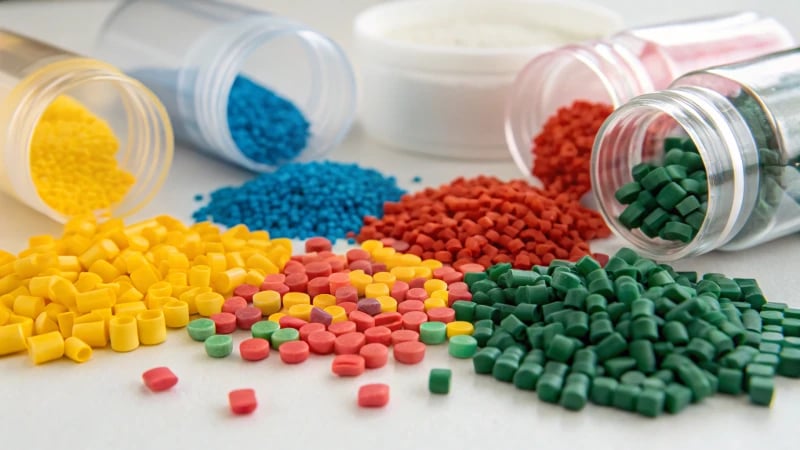
Thermal Conductivity and Its Impact
Let me take you back to a project I was working on last year. I had to design a cooling system for a client who was producing metal parts at a breakneck speed. The secret sauce? Understanding thermal conductivity. This property is all about how fast a material can conduct heat away. Think of metals like copper, which are like the Usain Bolt of heat transfer—speedy and efficient. With copper’s high thermal conductivity, heat was out the door in no time, drastically reducing cooling time.
Material | Thermal Conductivity (W/mK) |
---|---|
Copper | 401 |
Aluminum | 237 |
Polyethylene | 0.42 |
Here’s a quick comparison: copper’s thermal conductivity5 is much higher than most polymers, making it effective for applications requiring rapid cooling.
The Role of Specific Heat Capacity
Now, imagine you’re trying to cool down after a workout—some materials are like a cold glass of water, absorbing heat without much fuss. This is where specific heat capacity comes into play. It tells us how much heat a material can soak up before its temperature starts changing. Materials with lower specific heat capacities are quick to heat up and cool down, much like how fast I felt refreshed after that drink. This aspect is crucial when optimizing cooling times in injection molding.
Specific heat capacity influences cooling time optimization6, especially in processes like injection molding.
Viscosity’s Effect on Heat Transfer
Picture this: you’re stirring honey versus water. Honey’s resistance to flow is like high-viscosity materials in manufacturing—they make it tough for heat to distribute evenly. This means they need more time to achieve a uniform temperature. Once, I worked with a particularly tricky resin that had a high viscosity; it taught me the importance of factoring in viscosity for predicting how materials will cool during manufacturing.
Understanding viscosity helps in predicting cooling behaviors7 in various manufacturing scenarios.
Combining Material Properties for Optimal Cooling
Balancing these properties can feel like trying to bake the perfect cake—each ingredient must be measured just right to achieve the desired result. In my experience, creating composite materials that blend high thermal conductivity with moderate specific heat can be an ideal solution. It’s a careful dance of analyzing each property and seeing how they mesh together to deliver optimal cooling performance.
In conclusion, understanding these material properties is key to improving manufacturing efficiency and product quality. Designers like me can use this knowledge to tweak and perfect production processes, ensuring everything runs smoothly from start to finish.
Copper cools faster than polyethylene due to higher conductivity.True
Copper's thermal conductivity is 401 W/mK, much higher than polyethylene's 0.42.
Materials with high specific heat capacity cool down quickly.False
High specific heat capacity means materials absorb more heat, cooling slowly.
How Does Mold Design Affect Cooling Time?
Ever wondered how tweaking mold design can speed up cooling time?
Mold design significantly impacts cooling time by influencing material choice, geometry, and cooling channel layout, enabling shorter cycle times, increased efficiency, and improved product quality.
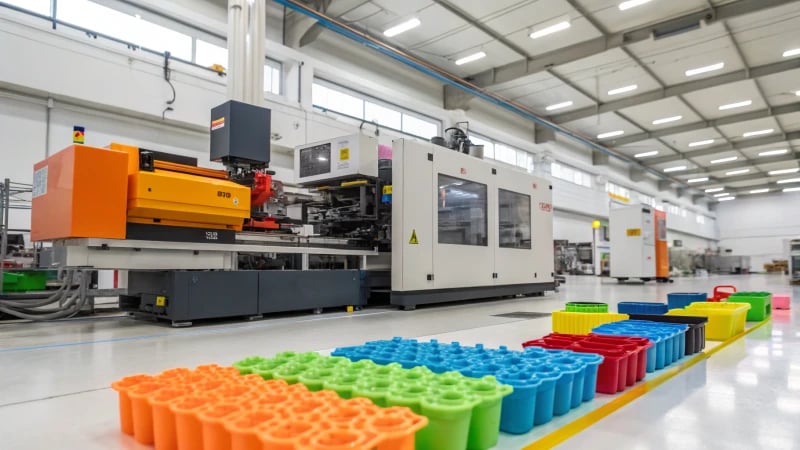
Material Selection’s Impact
When I first started tinkering with mold design, I quickly learned that the material we choose for the mold can make a world of difference. It’s all about thermal conductivity. Think about it—materials like beryllium copper can really amp up cooling efficiency. I remember comparing steel molds8 with aluminum ones; while steel is sturdy, aluminum cools so much faster. It felt like a lightbulb moment realizing how much the right material could speed things up.
Mold Geometry Considerations
Designing molds isn’t just about making something that looks cool; it’s about functionality too. Complex shapes can be tricky because they tend to create hot spots, slowing everything down. I once worked on a plastic bottle project where we rethought the whole design to maintain uniform wall thickness. Using CAD software to simulate the mold filling and cooling process was eye-opening—it helped us trim the cooling time by 20%!
Cooling Channel Design
I’ve seen firsthand how smart placement of cooling channels can revolutionize mold performance. Imagine channels that perfectly trace the part’s contour—they can seriously cut down on hot spots. Comparing straight-line channels with conformal cooling9 designs was like night and day; conformal cooling was a game-changer for us. Once, we switched to this method, and the cooling time plummeted.
Cooling Channel Type | Benefits |
---|---|
Straight-line | Simplicity, lower cost |
Conformal | Improved cooling efficiency |
Spiral | Uniform cooling for complex parts |
Analyzing Cooling Time Calculations
Using cooling time calculators10 has been another revelation in my design journey. These tools allow me to estimate cycle times by considering all the nuances of mold design—from thermal properties to part geometry. Simulating different scenarios with a cooling time calculator has helped me pinpoint the optimal designs, making my work not only more efficient but also more precise.
Understanding how each aspect of mold design influences cooling time is like piecing together a puzzle. By focusing on material choice, geometry, and cooling channels, I’ve been able to create more efficient and effective molds, ultimately leading to better products and happier clients.
Aluminum molds cool faster than steel molds.True
Aluminum has higher thermal conductivity than steel, dissipating heat quickly.
Symmetrical mold designs increase cooling time by 20%.False
Symmetrical designs reduce cooling time by 20%, not increase it.
How Do You Accurately Calculate Cooling Time?
When I first delved into the world of product design, calculating cooling time felt like solving a complex puzzle. It’s crucial, but are there formulas that really nail it?
Accurately calculating cooling time involves formulas considering material properties, geometry, and environmental conditions, crucial for optimizing production and ensuring high quality.
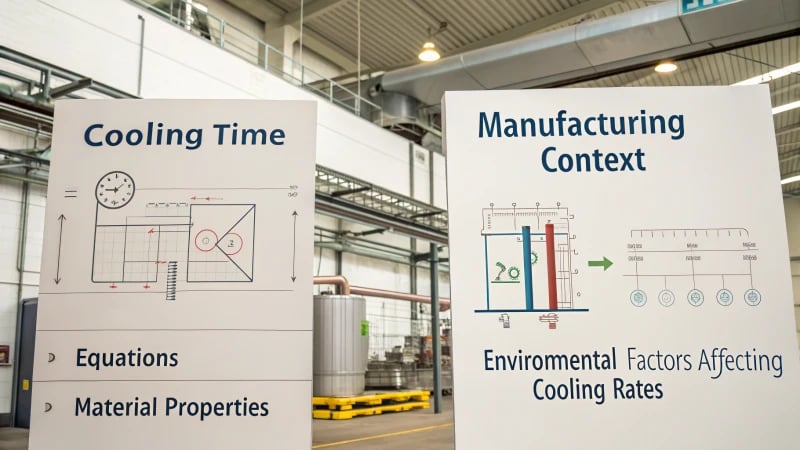
Understanding the Basics of Cooling Time Formulas
Back when I was just starting out in product design, I realized that cooling time wasn’t just about waiting for things to chill. It’s a dance of variables like material properties and geometry. For instance, the thermal conductivity11 and specific heat capacity of the materials I worked with played a significant role, much like a secret sauce in a recipe.
Key Factors Influencing Cooling Time
-
Material Properties
- Thermal Conductivity
- Specific Heat Capacity
-
Geometry of the Component
- Thickness
- Surface Area
-
Environmental Conditions
- Ambient Temperature
- Cooling Medium (air, water)
Back then, it was always a challenge to predict how different factors like thickness or surface area would affect the cooling process. But once you crack that code, it’s incredibly satisfying.
Common Formulas Used in Industry
Formula Name | Description |
---|---|
Newton’s Law of Cooling | Estimates cooling based on the temperature difference between object & env. |
Fourier’s Law | Relates heat conduction with temperature gradient and material properties. |
These formulas were like my trusty sidekicks, helping me create simulation models that could predict cooling times with surprising accuracy.
Simulation Tools and Software
Fast forward to today, and tools like Moldflow12 have become my go-to. They provide real-time insights by simulating thermal profiles during molding, which is like having a crystal ball for cooling predictions.
Practical Applications in Mold Design
By understanding these formulas and using simulation tools, I’ve learned to tweak designs for cooling channels effectively. It’s all about making production cycles more efficient without compromising quality. Over the years, I’ve dug into countless engineering textbooks13 and academic papers to get a better grasp of these concepts.
Leveraging these formulas and tools has been a game-changer, allowing me to ensure that every design not only meets aesthetic standards but also functional ones, making my work both rewarding and impactful.
Material properties affect cooling time calculations.True
Thermal conductivity and specific heat capacity are key factors.
Cooling time formulas ignore environmental conditions.False
Formulas consider ambient temperature and cooling mediums.
How Can I Optimize Cooling Times?
Ever found yourself staring at a production line, willing it to cool faster? I know I have. Let’s dive into some real-world strategies to make that happen.
Enhance thermal conductivity, adjust mold temperature, and design efficient cooling channels to optimize cooling times, improve heat transfer, reduce cycle times, and maintain product quality.
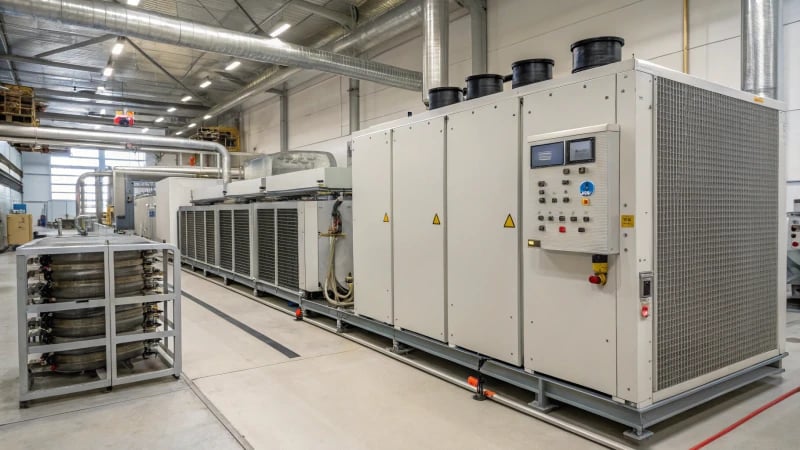
Enhancing Thermal Conductivity
Imagine standing by a machine, watching the seconds tick by as you wait for it to cool. I’ve been there. The secret sauce? Improving thermal conductivity. Think of it like wearing a sweater in winter; the better the fabric, the warmer you stay. Using highly conductive materials14 for molds, such as integrating copper inserts into aluminum molds, is like upgrading your sweater to a heated jacket—it makes a world of difference in reducing cycle times by enhancing heat transfer.
Adjusting Mold Temperature
Remember the time I forgot to adjust the oven temperature and ended up with a cake that was cooked on the outside but gooey inside? Keeping mold temperature optimal is similar—it’s all about consistency. By using temperature control units15, you can adjust mold temperatures precisely, ensuring products don’t warp, much like ensuring your cake rises evenly.
Efficient Cooling Channel Designs
It’s a bit like finding the perfect route on a GPS that avoids all the traffic. Designing efficient cooling channels ensures even heat distribution. Using conformal cooling techniques16 that mimic the geometry of your parts is like choosing the scenic route; it allows for uniform heat removal, and simulation software can guide you in mapping out these channels effectively.
Monitoring and Automation
Think of automated monitoring systems as having a smart assistant who never sleeps. They keep an eye on temperature fluctuations, adjusting parameters in real-time, which significantly reduces human error. Automated monitoring systems17 alert you to potential issues before they become a problem, like having an early warning system for your production line.
Utilizing Heat Exchangers
Have you ever repurposed leftovers into a delicious new meal? Employing heat exchangers is similar—they reclaim waste heat and put it back into your production process. This not only saves energy but also accelerates cooling. Exploring different types of heat exchangers18 can lead to considerable improvements, much like turning yesterday’s roast into today’s stew.
Practice | Benefit | Example |
---|---|---|
Thermal Conductivity | Faster Heat Dissipation | Copper Inserts |
Mold Temperature | Consistent Cooling | Temperature Control Units |
Cooling Channels | Even Heat Removal | Conformal Techniques |
Monitoring & Automation | Consistent Production | Automated Systems |
Heat Exchangers | Energy Efficiency | Waste Heat Reclaim |
Each of these strategies is like a puzzle piece in the grand design of optimizing cooling times. They’re not just technical tweaks; they’re part of crafting a seamless production process that keeps everything running smoothly and efficiently.
Copper inserts in molds improve heat transfer efficiency.True
Copper's high thermal conductivity enhances heat dissipation, reducing cycle times.
Automated monitoring systems increase human error in cooling processes.False
Automation reduces human error by adjusting parameters in real-time.
Conclusion
Cooling time in injection molding is influenced by part thickness, material properties, and mold design. Optimizing these factors enhances production efficiency and product quality.
-
Explore how varying part thickness impacts the cooling duration during injection molding, offering insights into production efficiency. ↩
-
Discover simulation tools that help predict and optimize cooling rates for different part thicknesses in injection molding. ↩
-
Learn about effective mold design strategies that promote uniform cooling and reduce defects in molded parts. ↩
-
Understand how different material properties can alter cooling times, aiding in better material selection for designs. ↩
-
Exploring copper’s high thermal conductivity helps understand its efficiency in rapid cooling applications, offering insights into material selection. ↩
-
Understanding specific heat capacity’s impact on cooling time aids in optimizing injection molding processes for faster production cycles. ↩
-
Exploring viscosity’s role in heat transfer provides insight into how materials cool, essential for efficient process design. ↩
-
Learn about the differences in thermal conductivity between steel and aluminum molds, and how it affects cooling times. ↩
-
Discover how conformal cooling channels can enhance efficiency by providing better heat removal compared to traditional methods. ↩
-
Find tools that help estimate cycle times based on mold design factors like thermal properties and part geometry. ↩
-
This link delves into how different material properties influence cooling times, offering valuable insights for design optimization. ↩
-
Explore how Moldflow software can optimize cooling time predictions, enhancing design accuracy and efficiency. ↩
-
Discover highly recommended textbooks that provide comprehensive knowledge on thermal dynamics, useful for understanding cooling time calculations. ↩
-
Explore materials that improve thermal conductivity, enhancing mold efficiency. ↩
-
Learn how temperature control units maintain optimal mold conditions. ↩
-
Discover how conformal cooling enhances heat removal in mold designs. ↩
-
Understand how automation improves consistency and reduces errors in cooling. ↩
-
Find out which heat exchangers can improve energy efficiency in production. ↩