Deciding on the right size for an injection molding machine feels like piecing together a puzzle. For designers like me, Jacky, it’s all about balancing efficiency and quality.
The right size of an injection molding machine is determined by material type, shot size, and clamping force, which affect machine performance and product quality. Matching machine specifications to production needs is essential.
You know, when I first started working in mold design, understanding these factors felt daunting. But with experience, I realized it’s a bit like cooking a complex dish. Each ingredient—material type, shot size, clamping force—plays its part in creating something exceptional. Let’s break down how these components work together to shape your production outcomes.
Material type is often the first thing I consider. Different materials behave differently under pressure and heat. For example, when working with a sturdy polymer, I need a machine that can handle higher temperatures and pressures to ensure the material flows correctly into the mold. It’s like knowing the right temperature to bake a cake so it rises perfectly.
Then there’s shot size, which reminds me of portioning ingredients. Too little, and the product lacks definition; too much, and you’re wasting resources. It’s crucial to measure precisely so every piece of the puzzle fits together seamlessly.
Finally, clamping force is like the hand that holds everything in place during production. It needs to be just right—not too firm that it damages the mold, nor too weak that it lets material seep out.
Balancing these factors is an art I’ve honed over years of trial and error, just like finding that perfect recipe that works every time. Each project brings its unique challenges, but with careful consideration of these elements, I ensure that our designs meet both functional and aesthetic requirements while optimizing for large-scale production.
Clamping force is crucial for machine size selection.True
Clamping force ensures the mold stays closed during injection, affecting size.
Material type doesn't affect injection molding machine size.False
Different materials require different pressures and temperatures, impacting size.
How does material type affect machine size?
When I first delved into the world of manufacturing, I quickly realized how crucial material type is in determining machine size and efficiency.
Material type affects machine size by determining the required strength, durability, and processing capabilities. Machines are tailored to handle specific material properties, influencing their dimensions and design.
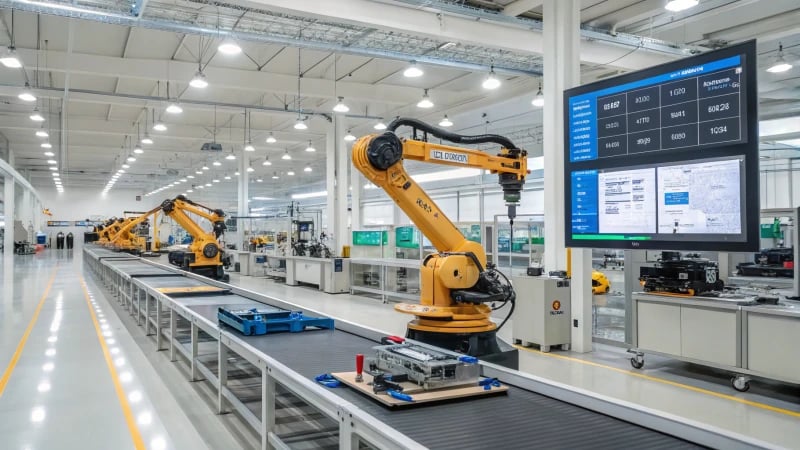
Material Properties and Machine Requirements
I remember back when I was trying to process a particularly tough metal for a project. The metal’s hardness meant I needed a machine with serious power and durability. It’s these unique material properties—like hardness, tensile strength, and elasticity—that guide what kind of machine is required.
For instance, machining metals1 often requires larger, more robust machines due to their hard nature. On the flip side, plastics demand machines with fine control for precision due to their more delicate nature. It’s fascinating how different materials set such distinct demands on machinery.
The Role of Machine Design
In my early days in the field, I learned quickly that a machine designed for wood is worlds apart from one meant for steel. Each machine must be crafted with the material’s thermal and physical attributes in mind, ensuring efficiency and preventing any mishaps.
Material | Typical Machine Features |
---|---|
Metals | High torque, coolant systems |
Plastics | Precision control, low heat generation |
Composites | Versatile tool paths, adaptive speed |
Impact on Production Efficiency
Choosing the right machine isn’t just about fitting the bill—it can make or break productivity. I’ll never forget a time when an oversized machine led to soaring energy costs on a project. An oversized machine can waste energy, while an undersized one might stall operations.
In industries like plastic molding2, getting the right machine size is pivotal for maintaining product quality. I’ve seen firsthand how undersized machines can falter with intricate molds, whereas larger machines could inflate costs unnecessarily.
Cost Implications of Machine Size
Machine size doesn’t just affect what you pay upfront; it also impacts ongoing expenses. Larger machines typically consume more power and require greater maintenance. Finding that balance—matching machine size with material needs—is key to keeping costs down.
I recall a project where using a CNC machine3 tailored to specific materials dramatically cut production costs by reducing tool wear and optimizing cycle times. It drove home just how essential it is to align machine capabilities with material requirements.
Metals require larger machines than plastics.True
Metals' hardness demands robust machines; plastics need precision.
All materials need the same machine features.False
Different materials require distinct machine features for efficiency.
Why Is Clamping Force Crucial in Machine Selection?
Imagine being in the middle of a high-stakes manufacturing project and realizing your parts aren’t as precise as they should be. That’s why clamping force is a game-changer!
Clamping force is vital in machine selection as it ensures part stability and accuracy, preventing defects such as warping or misalignment during manufacturing.
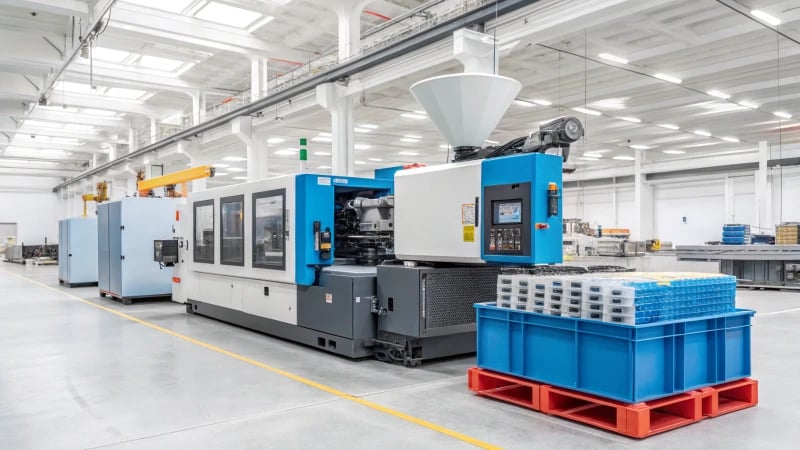
Understanding Clamping Force
When I first dove into the world of manufacturing, the concept of clamping force seemed straightforward, but the more I worked on projects, the more I realized its importance. Clamping force is the pressure applied to hold a workpiece securely during a manufacturing process. This force must be just right—enough to prevent any movement but not so much that it damages the workpiece or tooling.
Impact on Stability and Precision
I remember one particular project where I underestimated the clamping force needed for injection molding. The parts came out warped, and it was a costly mistake. In processes like these, inadequate clamping force can lead to defects in plastic components4, such as warping or incomplete filling. A stable clamping force keeps the mold closed, ensuring precision and alignment.
- Stability: Proper clamping force prevents part displacement, ensuring consistent production quality.
- Precision: High clamping force enhances tooling alignment, crucial for complex or tight-tolerance parts.
Calculating Clamping Force
Calculating the right clamping force is like solving a puzzle. It involves factors like part size, material type, and machine specifications. Typically, the clamping force required is calculated using various considerations:
Factor | Consideration |
---|---|
Part Geometry | Larger parts require more clamping force |
Material Type | Harder materials may need increased force |
Machine Specs | Machine’s max clamping capacity limits choice |
For a detailed approach, see clamping force calculations5.
Role in Machine Efficiency
I’ve learned that the right clamping force isn’t just about making good parts; it’s about maintaining your machinery too. It enhances machine longevity by reducing wear and tear on both tools and machines. Plus, it optimizes cycle times, which is key to improved operational efficiency.
By understanding these principles, professionals like Jacky can make informed decisions when selecting machinery, ensuring optimal production results without compromising on quality or efficiency. For more insights, explore our machine selection guide6.
Clamping force prevents part displacement.True
Proper clamping force ensures parts stay in place, maintaining quality.
Excessive clamping force improves tool longevity.False
Excessive force increases wear and tear, reducing tool life.
How Do Technical Specifications Influence Machine Sizing?
Imagine standing at the crossroads of innovation and practicality, where machine sizing can make or break your designs. It’s a journey I’ve taken countless times in my career.
Technical specifications guide machine sizing by defining dimensions, load capacity, and power needs, ensuring the machine is suitable for its purpose, optimizing performance, and maintaining cost-effectiveness.
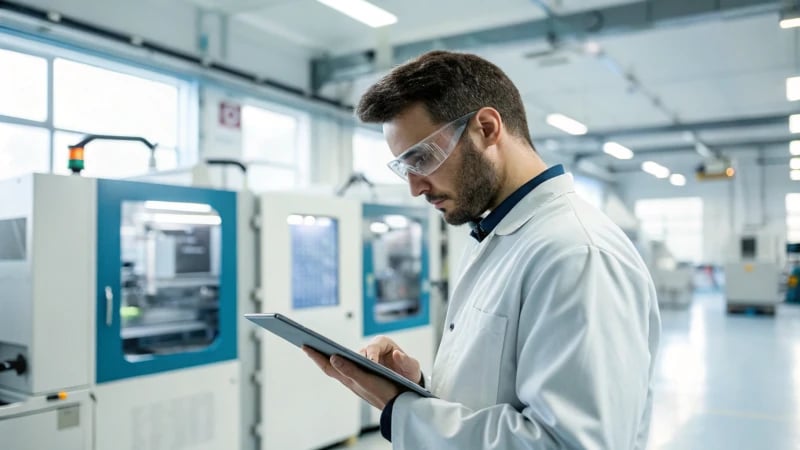
Understanding the Role of Technical Specifications
Navigating through the maze of technical specifications feels like flipping through the blueprint of a dream project. Each dimension, load capacity, and energy consumption detail is like a clue in a treasure map leading to the perfect machine. When I first started out, I remember poring over these specs late into the night, coffee in one hand, calipers in the other, trying to align my ideas with machine capabilities.
Key Specifications to Consider
-
Dimensions: I’ve learned that size can define not just space but also scope. I recall a project where we had to squeeze a behemoth of a machine into a tiny workspace—it was like trying to fit a grand piano into a shoebox.
-
Load Capacity: This is the backbone of efficiency. There was this time when an underestimation led to hilarious yet costly breakdowns—lesson learned!
-
Power Requirements: Matching these needs with facility capabilities is crucial. I’ve seen firsthand how mismatched power needs can trip an entire production line like a domino effect.
Specification | Importance |
---|---|
Dimensions | Fit within operational space constraints |
Load Capacity | Aligns with intended usage demands |
Power Needs | Matches facility power infrastructure |
Examples of Specification Influence
Once, while working on a plastic component design7, I encountered the pitfalls of inadequate load capacity. The machine struggled and so did our timelines—it was a costly oversight that taught me the value of getting the specs just right. On the flip side, using CAD tools has been a game-changer for visualizing and adjusting these specs—it’s like having a sneak peek into the future of your project. It helps dodge unnecessary expenses that come with oversized machines and has made my projects far more cost-effective8.
Exploring Multiple Perspectives
In the world of design, understanding technical specifications goes beyond just numbers and measurements; it’s about marrying creativity with reality. As a product designer, this focus allows me to craft components that not only meet client expectations but also resonate with operational demands. Engineers in my circle often emphasize power needs and load capacity—they’re the unsung heroes ensuring machines hum efficiently within safe parameters. Meanwhile, procurement teams juggle these specs to balance budgetary constraints while still hitting quality benchmarks.
For more insights, exploring resources that delve into how industry trends9 influence machine sizing criteria can broaden your understanding of manufacturing settings. These perspectives underscore how technical specifications are pivotal in sculpting machine sizing decisions, a key step in achieving desired operational results.
Dimensions affect machine installation space.True
Machine dimensions must fit within operational space constraints for proper installation.
Oversized machines always increase efficiency.False
Oversized machines can lead to unnecessary costs without providing added value or efficiency.
What Are the Consequences of Choosing the Wrong Machine Size?
Imagine setting off on a road trip with a car that’s too small for all your luggage. That’s what choosing the wrong machine size feels like in manufacturing.
Choosing the wrong machine size can increase costs, delay production, and reduce product quality. Selecting the right size is essential for efficiency and optimal performance in manufacturing.
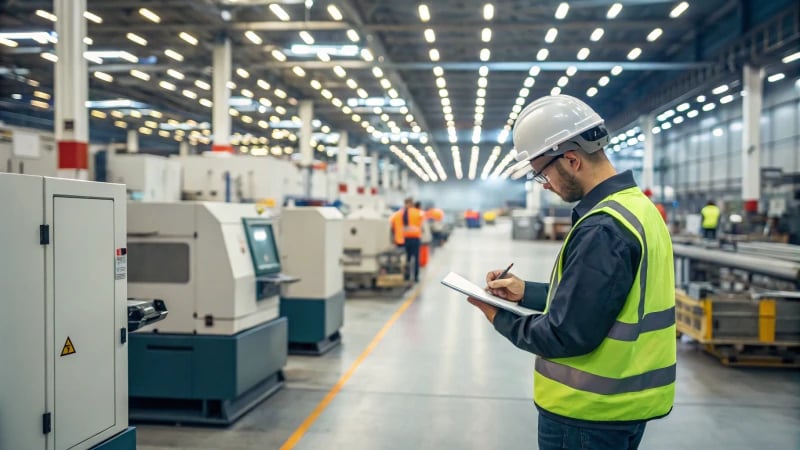
Financial Implications
Selecting an incorrect machine size can lead to significant financial setbacks. I remember a time when we decided to upgrade our machinery, thinking bigger would be better. It wasn’t long before we realized that the larger-than-necessary machines were guzzling energy like an old SUV. Our operational costs shot up, leaving us scrambling to adjust. On the flip side, I’ve also seen how smaller machines can drag down production, causing costly delays that no one wants to explain to the boss.
Scenario | Consequence |
---|---|
Machine too large | Increased energy and maintenance costs |
Machine too small | Production delays, missed deadlines |
Operational Efficiency
Operational bottlenecks often arise from using machines that are improperly sized for the task. I’ve learned that operational hiccups often start with the wrong machine size. There was this project where we used an oversized machine that couldn’t even operate at its best. It was like trying to swat a fly with a sledgehammer—totally overkill and inefficient. Conversely, using a machine that’s too small is like asking a bicycle to do the work of a truck; it just doesn’t cut it and can even lead to breakdowns.
- Reduced Throughput: A smaller machine can’t handle large volumes efficiently, leading to reduced throughput.
- Overload Risks: Overworking a small machine can lead to frequent breakdowns, disrupting the entire production schedule.
Quality Control Concerns
Quality is king in our line of work, and I’ve seen firsthand how the wrong machine size can jeopardize that. The quality of the final product can suffer if the wrong machine size is used. Picture using a tiny machine for a massive mold—uneven cooling and product warping become your new reality. It’s heartbreaking to see hard work not meet the mark because of equipment mismatches.
For instance, using a machine that’s too small for a large mold can cause uneven cooling and warping of the final product.
Strategic Decision-Making
Understanding these pitfalls makes strategic decision-making crucial. Whenever I’m planning for new equipment, I ask myself about production volume, product specs, and future scalability. It’s like playing chess—thinking several moves ahead to avoid checkmate.
Understanding the consequences of machine size misalignment helps in making informed strategic decisions10. When planning for new equipment purchases or upgrades, consider factors such as production volume, product specifications, and future scalability needs.
Considerations for Future Scalability
- Evaluate Production Needs: Align machine size with current and projected production needs.
- Flexibility: Opt for machines that offer flexibility in operation to adapt to varying production demands.
- Long-term Vision: Plan for scalability to accommodate future growth without frequent replacements.
Engaging in detailed analysis and consultation with equipment specialists has been my go-to strategy for choosing the right machine size. It’s saved me from plenty of headaches and kept projects on track.
Larger machines always improve production efficiency.False
Oversized machines may not operate at optimal capacity, wasting resources.
A small machine can lead to product defects.True
Small machines may struggle with precision, causing product inconsistencies.
Conclusion
Choosing the right size of an injection molding machine is crucial for efficiency, quality, and cost-effectiveness, influenced by material type, shot size, clamping force, and technical specifications.
-
This link explores how metals’ hardness influences the design and power requirements of machining equipment. ↩
-
This link provides insights into selecting machine sizes for effective plastic molding. ↩
-
This link offers information on how CNC machine sizes impact production costs. ↩
-
Explore common defects caused by insufficient clamping force to enhance understanding of its impact on product quality. ↩
-
Learn the method for calculating clamping force to ensure accurate and efficient molding processes. ↩
-
Gain comprehensive insights into selecting the right machinery for your specific manufacturing needs. ↩
-
Discusses how machine specs affect design processes, crucial for producing high-quality plastic components. ↩
-
Analyzes how proper sizing can reduce costs, benefiting budget-conscious manufacturing operations. ↩
-
Offers insights into current trends affecting machine size decisions, useful for staying competitive. ↩
-
Discover strategies for selecting the right machine size based on long-term business goals. ↩