Do you feel confused about the differences between extrusion and injection molding? Many others feel the same way! Let’s explore this interesting topic together.
Extrusion uses a continuous material feed with a rotating screw, while injection molding involves intermittent bursts of high-pressure material injection, leading to differences in process continuity.
In my journey through manufacturing, I recall the first time I encountered these two processes. It felt like meeting two unique people in a busy place – each having distinct strengths and quirks. To understand their differences, I will explain how they feed materials. Extrusion acts as a dependable friend, continuously supplying material through a rotating screw. Imagine a giant screw propeller pushing plastic forward to create things like pipes. Injection molding, in contrast, behaves like a quick thinker. It injects molten plastic into molds under high pressure, producing complex shapes like toys fast. Each method has its own rhythm and style. Knowing when to use each method is important for successful production.
Extrusion uses a continuous feed method for materials.True
In extrusion, materials are fed continuously through a rotating screw, ensuring a steady flow during the process.
Injection molding relies on a continuous material feeding process.False
Injection molding uses an intermittent feeding method, injecting molten plastic at high pressure rather than continuously feeding it.
How Does Continuous Feeding in Extrusion Impact Production Efficiency?
Do you often think about how nonstop feeding in extrusion improves production efficiency? This technique truly impacts material usage and the final product’s quality. Let’s explore it together!
Constant feeding in extrusion increases production efficiency. It keeps material flowing steadily. Downtime really decreases. Product quality remains consistent. Continuous feeding is especially effective compared to methods like injection molding. Injection molding interrupts the process.
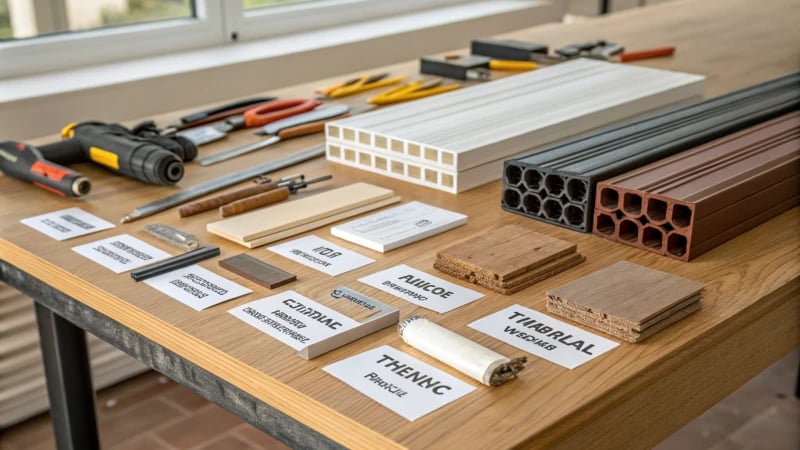
Understanding Continuous Feeding in Extrusion Molding
When I explored extrusion molding, one thing became very clear: continuous feeding is key to high production efficiency. Imagine it as a river. Raw materials flow steadily into the extruder’s barrel, powered by a screw, much like a giant propeller. This steady flow is crucial for creating consistent products. Products like plastic pipes1 need uniform shapes along their length.
Advantages of Continuous Feeding
-
Reduced Downtime:
Continuous feeding keeps the production line running smoothly without unnecessary stops. I remember when we switched to continuous feeding at work. The difference was really noticeable! We reached higher output rates because the production never had to pause.Benefit Description Higher Output Rates Continuous flow maximizes production time. Lower Operational Costs Fewer stops lead to reduced labor costs. -
Material Efficiency:
Continuous feeding greatly affects material use. With consistent input, we reduce waste significantly. In industries like food processing2, where sustainability is very important, this method shines. It allows manufacturers to better control and optimize resources.
Comparing Feeding Methods: Continuous vs. Intermittent
When I compare continuous feeding in extrusion to the intermittent approach in injection molding, it feels like contrasting a marathon runner with a sprinter:
Feature | Continuous Feeding (Extrusion) | Intermittent Feeding (Injection Molding) |
---|---|---|
Delivery Method | Constant flow into the mold | Periodic injection into the mold |
Production Rate | Steady and high | Variable, dependent on cycle time |
Control Over Quality | Stable due to consistent feed rate | Varies with each injection cycle |
Operational Stability and Quality Control
From my experience, how materials enter the system affects the product’s quality. By keeping a stable screw speed during extrusion, we achieved uniform pressure and flow. This made sure dimensions were accurate. For instance, producing profiles3 needed consistent wall thickness for both function and looks.
Conclusion on Efficiency Gains
Looking back at our journey with continuous feeding, it has truly been a game changer for our production efficiency. It’s not only about producing more products; it’s about getting operational stability and high quality that meets industry standards. Understanding these benefits has allowed us to optimize our processes effectively so we stay competitive in a fast-moving market.
Continuous feeding reduces downtime in extrusion processes.True
By minimizing interruptions, continuous feeding leads to higher output rates and efficiency during production.
Intermittent feeding is more efficient than continuous feeding.False
Continuous feeding provides steady flow and higher production rates compared to the variable nature of intermittent methods.
What Are the Advantages of Intermittent Injection Molding?
Have you ever asked why some products easily mix tough shapes with strength? That is the magic of intermittent injection molding! This process brings many benefits. It really changes manufacturing.
Intermittent injection molding is popular for its design flexibility. It saves costs through reduced material waste. It consistently produces quality products. It provides excellent control over processing settings. It is especially great for complex designs. It is very suitable for smaller production runs. This makes it a smart choice in modern manufacturing.
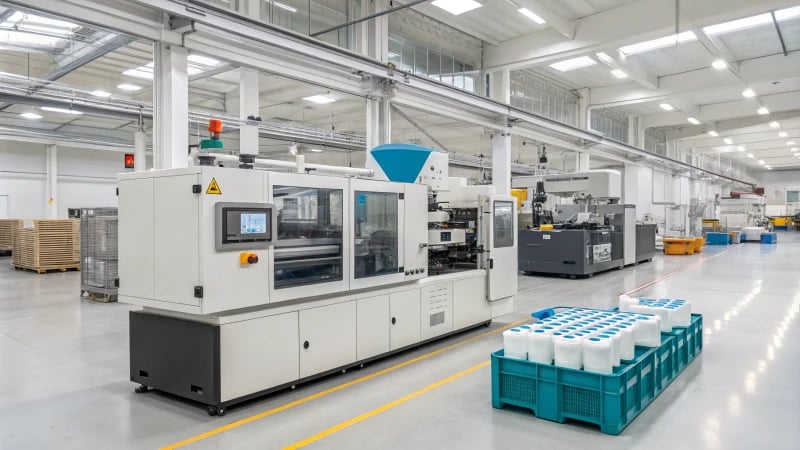
The Benefits of Intermittent Injection Molding
Intermittent injection molding offers significant advantages, particularly in terms of design flexibility and efficiency. This method allows for precise control over the amount of molten plastic injected into the mold, making it easier to produce intricate designs that might be challenging with other methods. For instance, products like customized plastic shells4 or toys5 can be manufactured efficiently due to the adjustable injection volume.
Moreover, this technique is particularly beneficial for small to medium production runs, enabling designers to quickly iterate on designs without the need for extensive retooling. This adaptability can lead to faster time-to-market for new products, as designs can be modified and tested rapidly.
Cost-Effectiveness in Production
While the initial setup costs for intermittent injection molding might be higher, its overall cost-effectiveness becomes apparent when considering its efficiency in material usage. Unlike extrusion, which continuously feeds material, injection molding uses only what is necessary per cycle, reducing waste.
Cost Factor | Intermittent Injection Molding | Extrusion Molding |
---|---|---|
Setup Costs | Higher initial costs | Lower initial costs |
Material Waste | Less waste due to precise use | More waste in continuous flow |
Production Volume | Ideal for low to medium volumes | Ideal for high volumes |
Time to Market | Faster with fewer iterations | Slower due to continuous process |
By optimizing the material feed and reducing waste, manufacturers can achieve significant savings in the long run. This makes intermittent injection molding a compelling choice for companies looking to balance quality and cost in their production processes.
Improved Product Quality and Consistency
One of the notable advantages of intermittent injection molding is its ability to produce high-quality products consistently. The controlled injection process ensures that molten plastic fills every cavity of the mold completely, minimizing defects such as short shots or inconsistent wall thickness.
This consistency is vital for products that must meet stringent quality standards, especially in industries like consumer electronics where performance and aesthetic appeal are critical. The ability to maintain uniformity in production results in higher customer satisfaction and reduced returns due to defects.
Greater Control Over Processing Parameters
Intermittent injection molding provides greater control over processing parameters compared to other methods. Each injection cycle allows for fine-tuning of factors such as temperature, pressure, and injection speed. This adaptability is crucial when working with different materials or during variations in production needs.
For example, adjusting the injection speed can significantly impact the final product’s surface finish and mechanical properties. Manufacturers can experiment with various settings to achieve optimal results, allowing for innovations in product design and functionality. The flexibility in parameter adjustments means that changes can be implemented swiftly without major disruptions to the production line.
Conclusion
While this section refrains from drawing conclusions, it’s important to recognize that intermittent injection molding offers numerous advantages, making it a valuable option for manufacturers aiming for efficiency, quality, and innovation. By understanding these benefits, designers and engineers can make informed decisions on the most suitable manufacturing processes for their projects.
Intermittent injection molding allows for complex design flexibility.True
This method enables precise control over molten plastic, facilitating intricate designs that are hard to achieve with other techniques.
Intermittent injection molding reduces material waste compared to extrusion.True
By using only the necessary material per cycle, this technique minimizes waste, making it more cost-effective in the long run.
When Should You Choose Extrusion Over Injection Molding?
Understanding manufacturing might feel like walking through a maze. I recall my first days in product design. I faced a tough decision. Should I choose extrusion or injection molding? Choosing the right method seemed really confusing.
Decide between extrusion and injection molding by thinking about how complex the product is, how much you need to produce, the material features and the costs. Use extrusion for simple shapes and large quantities. Choose injection molding for detailed designs and smaller amounts.
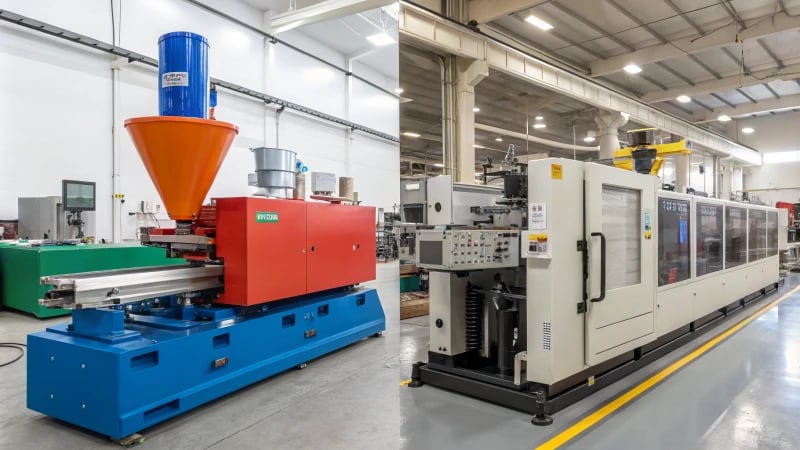
Understanding Method Selection in Different Scenarios
Choosing between different manufacturing methods, such as extrusion and injection molding, largely depends on the specific requirements of your product design. Here are key factors to consider:
-
Product Shape and Complexity
If your product has a constant cross-sectional shape, like plastic pipes or profiles, the extrusion molding method is ideal due to its continuous flow characteristics. This method ensures that long products are produced efficiently and consistently. For example, in the production of plastic pipes6, the material is pushed through a mold die, allowing for a stable output.In contrast, if you need to create complex shapes, such as intricate toy designs or electronic casings, injection molding is more appropriate. This method allows for high precision and the ability to fill complex cavities under pressure, ensuring that every detail of the design is captured effectively.
-
Production Volume
Consider your production needs:Method Ideal for Production Volume Extrusion Molding High volume continuous Injection Molding Lower to medium volume Extrusion molding is best when producing large quantities of uniform products over time. However, if your project requires smaller runs with a focus on quality and detail, injection molding becomes the preferred choice.
-
Material Properties
The type of plastic or material being used can also influence the decision. Some materials are better suited for extrusion due to their flow characteristics at elevated temperatures. For instance, thermoplastics used in extrusion can be continuously fed into molds without compromising their integrity.On the other hand, injection molding is more flexible with various materials, including thermosetting plastics that require higher pressures to form. Understanding the material behavior in both methods can aid in making a more informed choice.
-
Cost Considerations
When comparing costs, extrusion typically has lower initial tooling costs if you are focusing on high-volume production with relatively simple designs. However, injection molding may involve higher upfront costs due to complex molds but can provide cost savings in mass production of detailed components.
Practical Examples to Illustrate Method Choice
-
Scenario for Extrusion:
A manufacturer wants to create a series of standard plastic pipes for plumbing systems. Given the consistency required and high demand, extrusion is the most logical choice. Learn more about extrusion molding techniques7. -
Scenario for Injection:
A designer is tasked with creating a limited edition toy with intricate features and multiple colors. Injection molding’s precision and ability to handle diverse materials make it suitable for this project. Explore injection molding applications8.
By carefully evaluating these aspects—product shape, volume, material properties, and costs—you can make a more informed decision on which manufacturing method aligns best with your project goals.
Extrusion is ideal for complex product shapes.False
Extrusion is best for products with constant cross-sectional shapes, not complex designs. Injection molding is preferred for intricate shapes.
Injection molding suits lower production volumes better than extrusion.True
Injection molding is more efficient for lower to medium production volumes, while extrusion excels in high-volume continuous production.
How Do Material Properties Affect the Choice Between Extrusion and Injection Molding?
I first entered the world of manufacturing and learned something important. Material properties very much influence the decision between extrusion and injection molding. These characteristics probably make a big difference in our industry.
Material properties greatly affect the choice between extrusion and injection molding. They determine how to feed materials, the pressure needed and how efficiently production runs. Understanding these factors is key. It’s really important to optimize manufacturing processes for different materials.
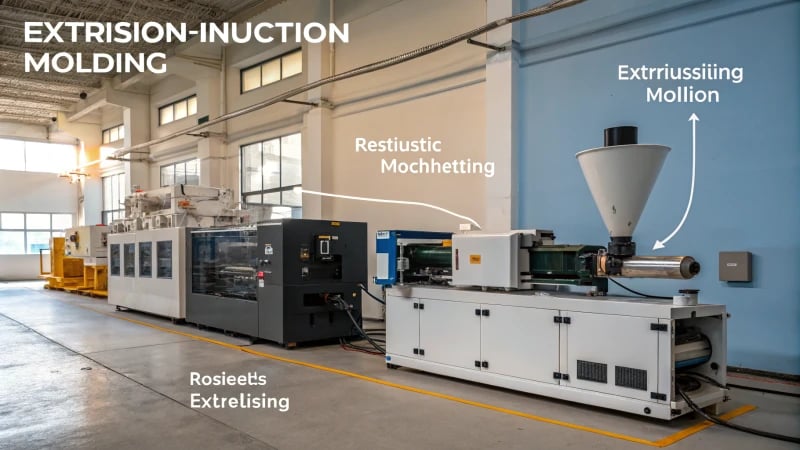
Understanding Material Feeding Methods
Understanding the small details of material properties has become a very important part of my journey. It amazes me how a simple trait decides the best way to create a product. Let’s explore this together.
The choice between extrusion and injection molding significantly depends on the properties of the materials being used. Each process has a distinct method for feeding materials into the mold, which can impact the final product’s quality and performance.
In extrusion molding, materials go into a rotating screw without stopping. Imagine a big screw pushing the material forward. I once visited a factory making plastic pipes. Watching the plastic particles being continuously pushed through the die was fascinating! This method is perfect for making long, continuous shapes. Think of pipes or profiles used in building.
On the other hand, injection molding operates on an intermittent basis. First, plastic granules go into a hopper where they melt before being injected into a closed mold at high pressure. I worked on a toy design where details were essential. This method helped achieve those complex features easily. It’s like creating a detailed sculpture quickly and efficiently!
Key Differences in Material Handling
Feature | Extrusion Molding | Injection Molding |
---|---|---|
Feeding Method | Continuous | Intermittent |
Pressure Characteristics | Stable pressure throughout | High pressure during injection |
Product Shape | Long and uniform shapes | Complex shapes with varied dimensions |
Cycle Time | Continuous production | Defined cycles for each injection |
Impact of Material Properties
I found out that the physical traits of materials decide which process suits them best. Materials requiring stable high-temperature delivery work well in extrusion. The continuous flow allows better temperature control and uniform heating. I’ve seen materials that deform easily maintain quality due to extrusion.
Conversely, materials needing specific characteristics during rapid cooling fit well in injection molding. The fast nature of this process is crucial for filling molds quickly, helping preserve delicate details in the final product. Watching a perfectly detailed casing come to life is really satisfying!
Cost Implications and Efficiency
Cost is another thing I’ve considered in my career. Generally, extrusion is more cost-effective for large-scale production of simple shapes because it runs continuously. In one project, we needed thousands of identical parts – extrusion was the clear choice! However, for smaller batches of complex items needing precision, injection molding proved more efficient despite higher initial costs.
By analyzing these factors—material properties, production methods, and cost implications—I’ve made smart decisions that optimize functionality and manufacturability for specific applications. Exploring the differences between molding techniques9 could be interesting if you’re curious! Understanding these details has been a rewarding journey!
Extrusion molding is ideal for producing long, uniform shapes.True
Extrusion molding continuously feeds material, making it suitable for items like pipes that require consistent cross-sections.
Injection molding is more cost-effective for large-scale production.False
While extrusion is generally cheaper for large runs, injection molding excels in precision for smaller, complex items despite higher costs.
Conclusion
Learn about the differences in material feeding methods between extrusion and injection molding, focusing on efficiency, production rates, and suitability for different product designs.
-
Explore this link to discover expert insights on optimizing extrusion processes through continuous feeding, enhancing your operational efficiency. ↩
-
This resource provides detailed information on how different feeding methods affect production rates and quality in extrusion. ↩
-
Learn more about operational strategies that leverage continuous feeding to boost manufacturing efficiency. ↩
-
Explore how intermittent injection molding can optimize your production process and enhance product quality. ↩
-
Learn about cost savings and efficiency improvements offered by intermittent injection molding techniques. ↩
-
Discover detailed insights on when to use extrusion vs injection molding based on specific scenarios. ↩
-
Learn about various applications and benefits of injection molding for complex designs. ↩
-
Find out how to evaluate production volume requirements for different manufacturing methods. ↩
-
Learn more about the differences between extrusion and injection molding processes and their applications in manufacturing. This link provides useful comparisons. ↩