Selecting between extrusion and injection molding in manufacturing can seem confusing. I have experienced this dilemma. This decision truly impacts product design and efficiency.
For mass production, extrusion offers cost efficiency and material use, while injection molding excels in creating precise complex shapes, ideal for both large and small batches.
Let’s explore the core of these processes. I remember struggling with a project decision. Should I choose extrusion for efficiency or injection molding for precision? Extrusion excels in mass production. It offers high efficiency and low mold costs. This method suits simpler shapes like pipes. When designs become complex, injection molding becomes superior. It allows for intricate designs with great accuracy. Both methods have advantages. Understanding these details can really influence your production approach.
Extrusion is more efficient for small batch production.True
Extrusion typically provides higher efficiency and lower costs for producing small batches compared to injection molding.
Injection molding is ideal for complex shapes.True
Injection molding excels at creating intricate designs with high precision, making it suitable for complex shapes.
- 1. What Are the Key Advantages of Extrusion Molding for Mass Production?
- 2. How Can Injection Molding Transform Product Flexibility in Small Batches?
- 3. What Factors Should Influence Your Choice Between These Two Molding Processes?
- 4. What Manufacturing Processes Do Different Industries Prefer?
- 5. Conclusion
What Are the Key Advantages of Extrusion Molding for Mass Production?
Have you ever thought about how companies produce many products quickly? Let’s look at how extrusion molding helps big factories produce items. It’s not just possible but really efficient.
Extrusion molding is really special in mass production. It has high efficiency and low mold costs. Material use is excellent. This process creates simple shapes without stopping. It minimizes waste and costs. Many manufacturers find it an ideal choice.
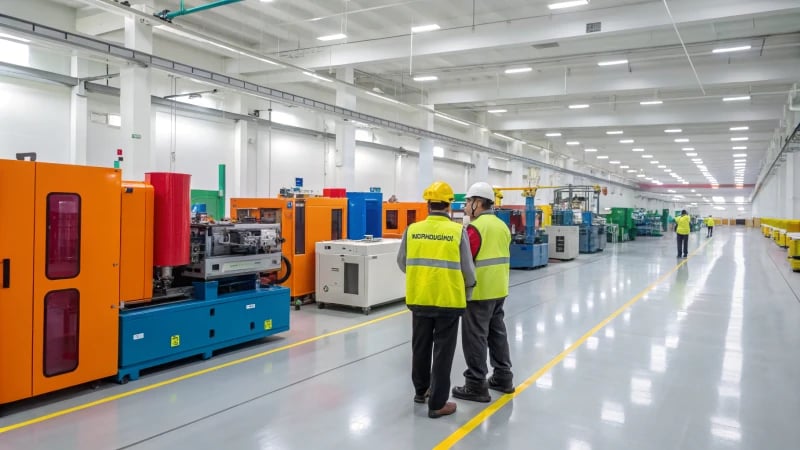
High Production Efficiency
Extrusion molding brings amazing benefits to mass production. I have learned to value this method over the years in the industry. It’s not only about manufacturing; it significantly improves efficiency, saves money and uses materials wisely. I have seen how it can dramatically change operations.
Extrusion molding is renowned for its high production efficiency. As a continuous production process, once the machinery is set up and operational, it can produce items without interruption. For example, in the creation of plastic pipes, the extruder maintains a steady output over prolonged periods. This efficiency is crucial for manufacturers aiming to meet high demand while keeping costs low.
To illustrate, consider a scenario where an extruder produces 100 meters of pipe per hour. This means that with optimal conditions, a factory could churn out thousands of meters in a single shift, significantly boosting productivity. More on production efficiency1.
Cost-Effective Mold Production
Another benefit is the low mold cost in extrusion molding. Compared to injection molding, especially for simple shapes like pipes, the design process for extrusion molds is less complex and faster. This simplicity leads to lower costs. This is crucial in large production where every penny matters.
Feature | Extrusion Molding | Injection Molding |
---|---|---|
Mold Complexity | Low | High |
Production Cycle Time | Short | Longer |
Cost per Mold | Lower | Higher |
In my project analysis, as production increases, the cost per unit drops a lot, which excites manufacturers. To explore more about mold production2.
High Material Utilization
A significant advantage of extrusion molding is its high material utilization. The process generates minimal waste compared to other manufacturing methods. Aside from some material loss during startup and shutdown phases, the continuous nature of extrusion means that materials are efficiently transformed into finished products.
Reducing waste saves on raw material costs. It also promotes sustainable practices, which is important today. This eco-friendly aspect can really improve a company’s reputation. Discover more on material utilization.
Comparison with Injection Molding
Though I love extrusion molding, it’s important to note its limits compared to injection molding. For complex designs needing high precision – like electronic parts – injection molding is better. It creates complex shapes with tight tolerances that extrusion cannot achieve.
However, for products suitable for extrusion, its benefits often outweigh those of injection molding due to lower costs and higher efficiency.
Criteria | Extrusion Molding | Injection Molding |
---|---|---|
Ideal Product Types | Simple shapes | Complex shapes |
Speed | Fast continuous | Slower due to cycle time |
Setup Costs | Low | High |
Here’s another helpful comparison: Explore more about molding techniques3.
Conclusion of Advantages
In summary, extrusion molding’s benefits – high production efficiency, affordable mold production and little material waste – make it a great choice for mass production. Whether it fits depends on your product’s specific needs and designs. It’s about finding where efficiency meets design!
Extrusion molding is more efficient than injection molding.True
Extrusion molding allows for continuous production, significantly increasing efficiency compared to the batch process of injection molding.
Extrusion molds are cheaper to produce than injection molds.True
The design and manufacturing of extrusion molds are simpler, leading to lower costs compared to the complex molds used in injection molding.
How Can Injection Molding Transform Product Flexibility in Small Batches?
Do you ever think about how factories keep up with fast-changing customer needs? Injection molding is very important. It helps products adapt, especially in small batch production. Let’s explore how this process functions and why it is significant.
Injection molding allows for product flexibility in small batches. It enables very quick mold changes. This process achieves high precision in complex shapes. Manufacturers efficiently meet different production needs. Costs do not become excessive.
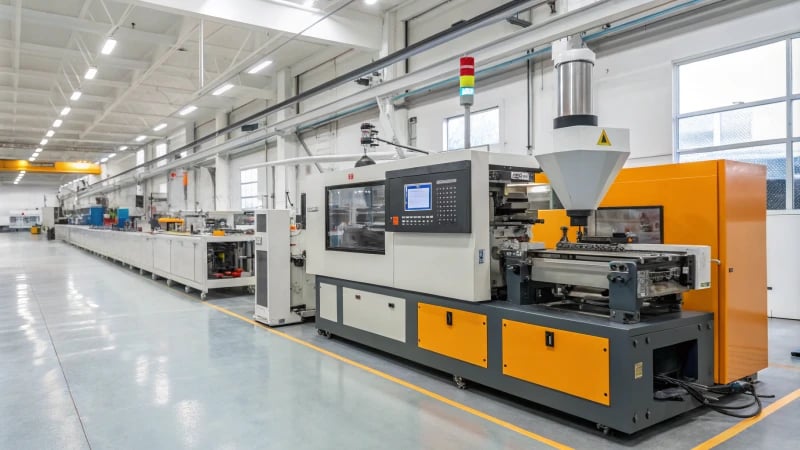
Understanding Injection Molding’s Role in Flexibility
Injection molding serves as more than just a manufacturing method; it’s a revolution, especially for making small batches of different products. I recall my first experience with this process – it felt like magic. A raw plastic pellet turned into a perfectly shaped part in just minutes. This quick adaptation is very important for industries where plans might change suddenly.
Traditional methods seemed very hard with long setup times. Injection molding, however, allows fast transitions from one product to another with little downtime. It’s crucial in today’s fast-paced market, where consumer tastes can change rapidly.
Quick Changeovers and Diverse Shapes
Changing molds is one of the most exciting aspects of injection molding. It’s almost like having many outfit choices! When a manufacturer wants to launch a new product, they simply replace the existing mold with a new design. This capability lets them quickly react to market demands and allows for a variety of shapes and sizes.
For example, a company I collaborated with specialized in custom plastic parts. With injection molding, they swiftly moved from producing smartphone cases to car components. It’s really remarkable how quickly they could adapt, especially in industries like consumer electronics that focus on innovation.
Cost Considerations for Small Batches
Now let’s discuss money. Creating injection molds requires an upfront investment, but, in my experience, the long-term advantages often outweigh these initial costs. Producing high-quality, precise components in small batches justifies that early expense.
Cost Factor | Injection Molding | Other Methods |
---|---|---|
Initial Mold Cost | High | Low |
Production Speed | Fast | Variable |
Flexibility in Design | High | Low |
Waste Material | Minimal | High |
Manufacturers manage mold costs through careful planning and design, keeping prices competitive even with low volumes. Companies like Jacky’s succeed on this model, focusing on high-end customized products.
Quality Control and Automation
Injection molding in small batch production offers significant automation advantages. My first glance at automated equipment monitoring real-time production was enlightening. It greatly reduces defect rates, guaranteeing that the output is consistent and dependable.
Automation allows skilled workers to focus on more complex tasks rather than routine ones. It’s like having several tireless helpers working beside you! Integrated technologies monitor every step, making quality control smooth and ensuring consistency across various batches.
Conclusion: The Future of Flexible Manufacturing
Looking forward, injection molding’s role in increasing product flexibility is very likely to grow. As technology and materials advance, manufacturers using this method will stay flexible – ready to address changing market trends and consumer needs efficiently.
As markets develop, our strategies for small batch production will also change, with injection molding at the forefront. If you are interested in maximizing production efficiency with this approach, I strongly recommend exploring this detailed guide4. It’s really worth your time!
Injection molding allows rapid changes in product design.True
This claim is true; injection molding's quick mold change capability enables manufacturers to adapt designs swiftly, meeting changing market demands effectively.
Injection molds are always cost-effective for small batches.False
This claim is false; while injection molds can be expensive initially, their long-term benefits may justify costs depending on production needs.
What Factors Should Influence Your Choice Between These Two Molding Processes?
Choosing between extrusion and injection molding feels very overwhelming. I have experienced this before. Weighing the pros and cons was challenging. The decision comes down to a few important factors. These factors really affect your production efficiency and the quality of your product.
When choosing between extrusion molding and injection molding, consider production volume, product complexity and costs. Each method offers unique benefits for specific manufacturing needs.
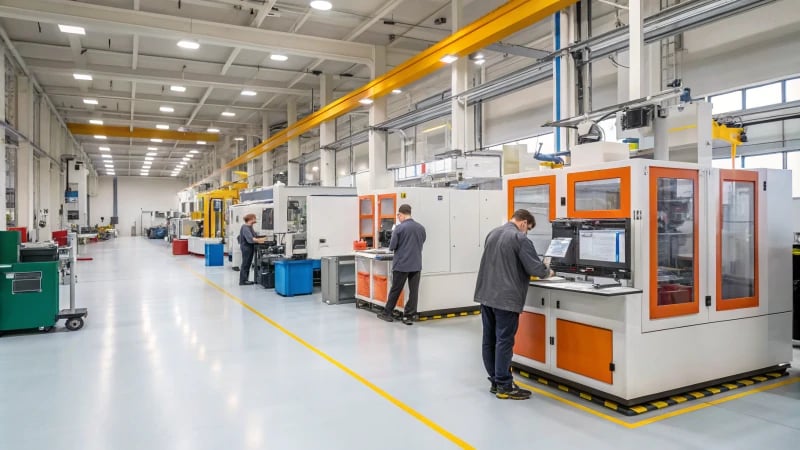
When considering the choice between extrusion molding and injection molding, several factors come into play that can significantly influence your decision. These factors include production volume, product complexity, and cost efficiency among others.
Production Volume
One of the primary considerations is whether you’re looking at mass production or small batch production.
Mass Production:
-
Extrusion Molding:
- High Production Efficiency: This method is a continuous production process that allows for sustained output once operational. For example, in producing plastic pipes, an extruder can run for extended periods, yielding high output rates.
- Relatively Low Mold Cost: For simpler product shapes, such as profiles, the mold design and manufacturing cycle is short, reducing costs significantly per unit produced.
- High Material Utilization: Waste is minimized in the extrusion process, with most material being used effectively during production.
-
Injection Molding:
- Complex and Diverse Shapes: This method excels when producing intricate designs requiring high precision, like electronic housings.
- High Degree of Automation: Automated systems can enhance efficiency and reduce defect rates through real-time monitoring.
Small Batch Production
For smaller runs, different dynamics come into play:
-
Extrusion Molding:
- Simple Equipment Debugging: The equipment setup for extrusion is straightforward, facilitating quicker changeovers between different products. This is particularly advantageous for producing various shapes without extensive downtime.
- Mold Cost Advantage: In small batches, the lower cost of extrusion molds becomes more pronounced, as the mold costs do not heavily impact overall expenses.
-
Injection Molding:
- Flexibility in Product Shapes: Injection molding allows for quick adjustments to mold designs, making it suitable for high-end customized products despite its higher initial mold costs.
Cost Implications
Understanding the cost structures associated with each method is crucial. Below is a simplified comparison:
Factor | Extrusion Molding | Injection Molding |
---|---|---|
Initial Mold Cost | Lower | Higher |
Production Speed | Continuous and high | Batch-based |
Waste Material | Minimal | Varies |
Flexibility in Design | Limited | High |
Automation Capability | Moderate | High |
Conclusion on Technical Aspects
Assessing technical capabilities such as material compatibility and specific production requirements can also guide your choice. For example, if your project requires rapid prototyping or frequent design changes, injection molding may be more suitable despite its higher costs. On the other hand, extrusion could be better for consistent high-volume production with less complexity in design.
In summary, evaluating these factors will empower you to make a more informed choice tailored to your specific production needs. Factors like automation capabilities, product shape complexity, and cost efficiency play vital roles in determining the best molding process for your projects. To dive deeper into specific molding techniques or machinery, consider exploring advanced molding techniques5 or cost-saving production strategies6.
Extrusion molding is ideal for high production volumes.True
Extrusion molding offers continuous production efficiency, making it suitable for mass production scenarios where high output is required.
Injection molding has lower initial mold costs than extrusion molding.False
Injection molding typically requires higher initial mold investment compared to extrusion, which has lower mold costs for simpler shapes.
What Manufacturing Processes Do Different Industries Prefer?
Have you thought about how some industries decide on their manufacturing methods? This world mixes efficiency with creativity. I am thrilled to tell you more about it. Let us explore together how various fields opt for extrusion or injection molding!
Various industries choose either extrusion or injection molding depending on their specific production needs. Efficiency, complexity and cost often influence their decisions. Extrusion benefits mass production due to its speed and cost efficiency. It operates very fast. High-precision sectors tend to select injection molding. This method forms complex shapes with accuracy. It really shapes with precision.
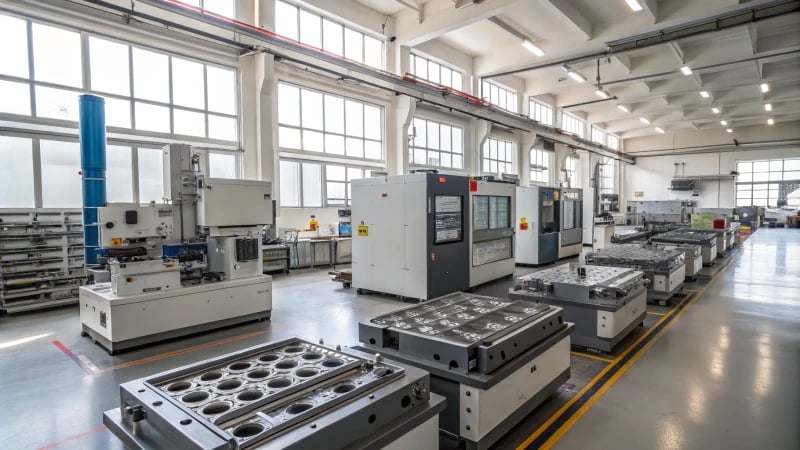
Mass Production vs. Small Batch Production
Understanding industry preferences for how things are made affects production plans a lot. In my journey in product design, I noticed that choosing between extrusion molding and injection molding involves more than just efficiency. It is about meeting special needs that might really help or harm a business.
In the manufacturing landscape, specific industries often favor either extrusion molding or injection molding based on their production needs.
For mass production, extrusion molding shines due to its high production efficiency. This continuous process allows for the quick and steady production of items like plastic pipes, where the extruder can operate for long durations. Moreover, industries that require simple shapes benefit from relatively low mold costs, making extrusion economically viable. The high material utilization also helps industries save on costs by minimizing waste during production. You can learn more about how these efficiencies impact production costs through detailed resources like production efficiencies7.
Extrusion is simple, especially for creating basic shapes. Producing a large amount of pipe fittings showed that relatively low mold costs allowed better budget use. There was also joy in seeing minimal material waste during extrusion; saving material helps in reducing overall costs.
On the flip side, when the need arises for products with complex shapes and high precision, such as automotive or electronics components, injection molding becomes favorable. Its capacity for diverse shapes and structures is bolstered by high degrees of automation, enhancing efficiency and maintaining quality control. Industries that prioritize precision often lean towards injection molding due to its sophisticated process controls.
Industry Preferences Based on Production Type
Industry | Preferred Process | Reason for Preference |
---|---|---|
Construction | Extrusion Molding | Simple shapes (e.g., pipes) and high volume outputs. |
Automotive | Injection Molding | Complex parts requiring high precision. |
Electronics | Injection Molding | Diverse product shapes and strict quality standards. |
Consumer Goods | Either | Depending on design complexity and production volume. |
The different preferences show the special needs of various industries. In small batch production, extrusion molding stays popular due to its simple equipment setup. When switching between different plastic profile shapes, the process adapts quickly without emptying the budget.
If flexibility in design and swift production are necessary, injection molding is very helpful. Although the mold costs more, for products needing frequent updates, like high-end customized items, it proves worth the investment despite initial costs.
Explore more about small batch efficiencies8.
Conclusion Avoidance Strategy
Understanding different industries’ manufacturing choices is important and involves careful thought. Factors like market demand, cost limits and technology changes influence how businesses decide on their production methods. In my experience, being aware of these factors is vital for successful product design and development.
Extrusion molding is preferred for mass production in construction.True
Construction industries favor extrusion molding due to its efficiency and suitability for producing simple shapes like pipes at high volumes.
Injection molding is ideal for automotive components due to precision.True
The automotive industry prefers injection molding for its ability to create complex parts with high precision and quality control requirements.
Conclusion
Explore the key differences between extrusion and injection molding, focusing on their efficiency, costs, and ideal applications for mass production or small batch needs.
-
Learn about the top benefits of extrusion molding and how it compares to other methods to improve your production processes. ↩
-
Find out how extrusion molding can enhance your manufacturing efficiency and reduce costs in your production line. ↩
-
Explore the differences between extrusion and injection molding to make informed decisions for your product designs. ↩
-
Explore this link to discover how injection molding can optimize your production processes and enhance flexibility in manufacturing. ↩
-
Discover in-depth analysis and comparisons between molding processes to help you decide effectively. ↩
-
Learn about cost-effective strategies to optimize your molding choices and improve profitability. ↩
-
Discover how different industries utilize manufacturing processes to enhance efficiency and meet product demands. ↩
-
Learn more about the advantages of each process in small batch production scenarios. ↩