Curious about the different shapes that extruded products take? Let’s explore this fascinating world together.
Extrusion is a plastic processing technique. It produces continuous shapes with unchanging cross-sectional forms. You probably encounter pipes, rods and unique profiles designed for various purposes. Designers and engineers must understand these shapes. This knowledge helps in creating both functional and attractive products.
As a designer, I often feel fascinated by the versatility of extrusion. This process produces continuous profiles with consistent cross-sectional shapes. These shapes include everything from sturdy pipes to intricate special profiles. I remember the first time I saw a beautifully designed frame profile for a plastic door. It was truly a game changer in both looks and functionality. Each shape, whether a simple rod or a complex decoration, holds a unique purpose. These shapes meet the specific needs of various applications.
Extrusion creates products with constant cross-sectional shapes.True
Extrusion technology consistently produces items like pipes and rods with uniform cross-sections, essential for various engineering applications.
Extruded products can only be cylindrical in shape.False
Extrusion allows for a variety of shapes, not limited to cylinders, including specialized profiles for diverse uses.
What Are the Benefits of Using Extruded Shapes in Manufacturing?
Do you ever think about how extruded shapes change your manufacturing work? Extruded shapes offer many benefits. They probably provide the solution you need.
Extruded shapes in manufacturing present numerous advantages. They are very cost-effective. This approach allows for flexible designs. These shapes often demonstrate superior performance. Manufacturers often use this method for products like pipes. Custom profiles for different uses are also created this way.
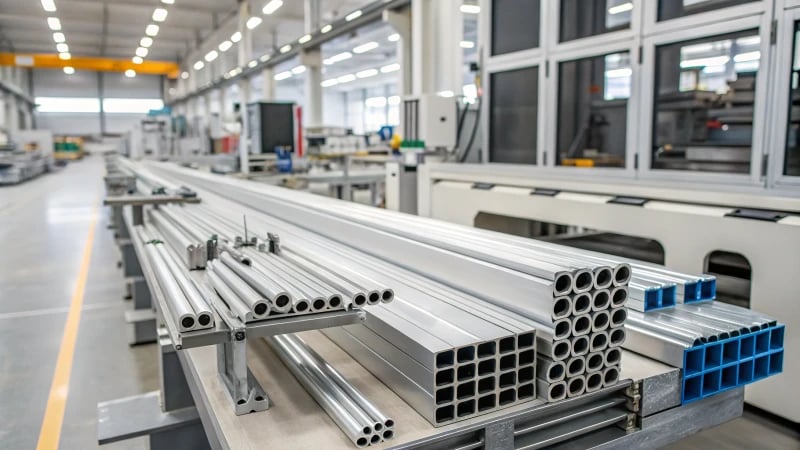
Understanding Extrusion in Manufacturing
When I first learned about extrusion during my manufacturing experiences, I was very impressed by its efficiency and wide use. It felt like discovering a new level in a video game. Everything suddenly became clear! Extrusion is an amazing method for shaping plastic. It creates products with continuous shapes and even designs. This process simplifies production and opens many design possibilities.
Diverse Product Range
Extrusion plays an important role in many industries. It helps people like me create different shapes needed for specific purposes. Costs remain reasonable and performance stays high. Extrusion is like having a magic tool to bring your design ideas to life.
I love the many different shapes extrusions offer. These shapes serve different industrial needs. Here’s a glimpse of some typical extruded forms I often use:
Product Type | Description | Applications |
---|---|---|
Pipe | Used for water and gas supply, available in different wall thicknesses and diameters. | Plumbing, drainage, construction. |
Rod | Regular geometric shapes, useful as blanks for machining or supporting structures. | Manufacturing, construction. |
Special Profiles | Complex shapes designed for specific applications, like decorative frames or architectural elements. | Interior design, construction. |
Cost-Effectiveness of Extrusion
One great advantage of using extruded shapes is their cost-effectiveness. At first, large-scale production and its potential to reduce unit costs amazed me. Materials like aluminum, both light and strong, offer excellent performance without high costs. Many cost-saving strategies exist in choosing extrusion instead of traditional machining methods. It’s empowering to pass these savings to my customers.
Manufacturers can explore cost-saving measures1 when choosing extrusion over traditional machining methods.
Design Flexibility
Extrusion allows great freedom in design. Creating detailed profiles to meet functional needs has changed my projects a lot. Once, I had to create a custom design for an interior project. It was exciting to produce something special! This flexibility improves function and greatly enhances the look of the final products.
Want to learn more about design innovations in extrusion2? Dive in! It’s really worth it.
Performance Characteristics
Extruded shapes perform very well; they usually have high strength compared to their weight and last long, which suits them for many uses such as car parts and building supports. Adjusting material properties in extrusions lets me meet specific needs effectively.
Interested in material performance in manufacturing3? There’s so much to explore!
Conclusion
In summary, using extruded shapes in manufacturing offers many benefits ranging from diverse products and cost efficiency to design freedom and strong performance traits. I have seen this transformation personally; for modern manufacturing needs, extrusion is a strong option. Consider exploring its potential for your projects—you might find the ideal solution you have been looking for!
Extruded shapes are cost-effective for large-scale production.True
The extrusion process reduces the cost per unit significantly, making it economical for manufacturers producing large quantities of products.
Extrusion limits design flexibility in manufacturing.False
Contrary to this claim, extrusion actually offers significant design flexibility, allowing for intricate and custom profiles tailored to specific applications.
How Does the Extrusion Process Influence Product Quality?
Have you ever thought about how the extrusion process molds the quality of plastic products we use every day? This process is fascinating. It plays a very important role in the finished products.
The extrusion process strongly affects product quality. Material selection, screw speed, temperature control, moisture content and cooling rate play important roles. Knowing these factors really helps in improving plastic manufacturing. This understanding also leads to high-quality results.
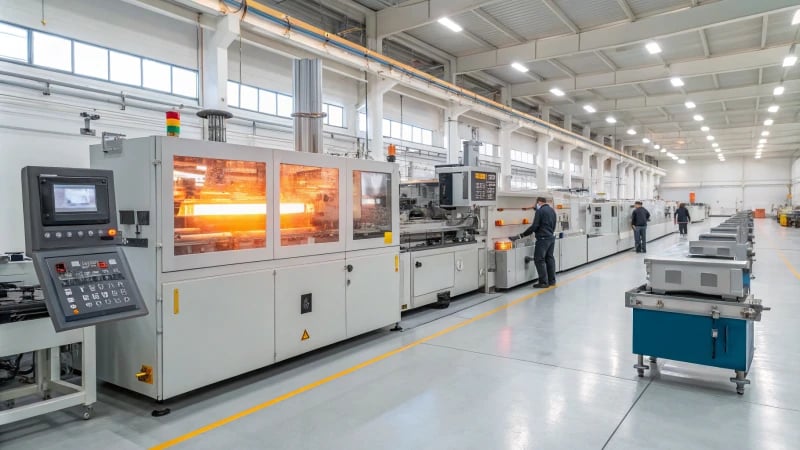
The extrusion process is a crucial technology in plastics manufacturing, impacting the quality of the final products significantly. Various factors, such as the material used, processing parameters, and design specifications, contribute to the end result.
Key Factors Influencing Product Quality
-
Material Selection
- The right polymers are critical. A thermoplastic choice once made my project easier and improved results. Material affects product properties; do not underestimate it.
- Learn more about material choices4 that can impact extrusion outcomes.
-
Screw Speed and Design
- Screw speed impacts shear rates and viscosity. Fast screws improve mixing but can create bubbles; monitoring is important.
- Consider looking into screw design influences5 on product quality.
-
Temperature Control
- Temperature management is delicate. Low temperatures cause incomplete melting while high temperatures degrade material; I learned this the hard way.
- Explore how temperature affects material behavior6 during extrusion.
Types of Extruded Products
The extrusion process is versatile, producing various shapes tailored to specific applications:
Type | Description | Example Applications |
---|---|---|
Pipe | Typically circular cross-sections; used in plumbing and drainage systems. | Water supply and gas pipes |
Rod | Can be circular or square; often used as blanks for machining or structural components. | Plastic rods for manufacturing |
Special Profiles | Complex shapes designed for specific functions, such as frames for doors and windows. | Architectural decorations |
-
Moisture Content
-
Cooling Rate
- Cooling rate impacts crystallinity and strength; it is crucial for accuracy. Controlled cooling transformed a project I worked on.
- Investigate the effects of cooling methods on product characteristics8.
-
Quality Control Measures
- Quality control is vital in extrusion; careful inspections have saved us from major issues with visual checks and dimensions being really important.
By understanding these factors, designers and engineers can optimize the extrusion process to enhance product quality effectively. Each aspect interplays uniquely, making it essential for professionals like Jacky to consider all parameters during the design and production phases.
Material selection is crucial in the extrusion process.True
The type of polymer significantly affects the properties of extruded products, impacting overall quality and performance.
Higher screw speeds always improve product quality.False
While higher screw speeds enhance mixing, they can also introduce defects like bubbles, affecting quality negatively.
What Materials Are Commonly Used in Extrusion?
Extrusion serves as a crucial method in manufacturing. It turns many materials into continuous shapes. What materials probably create this transformation? Let’s explore the intriguing world of extrusion!
Extrusion often uses thermoplastics such as PVC, polyethylene, polypropylene and polystyrene. It also employs metals like aluminum, copper and brass. Each material has unique properties. These properties suit them for specific uses. Different applications need different materials.
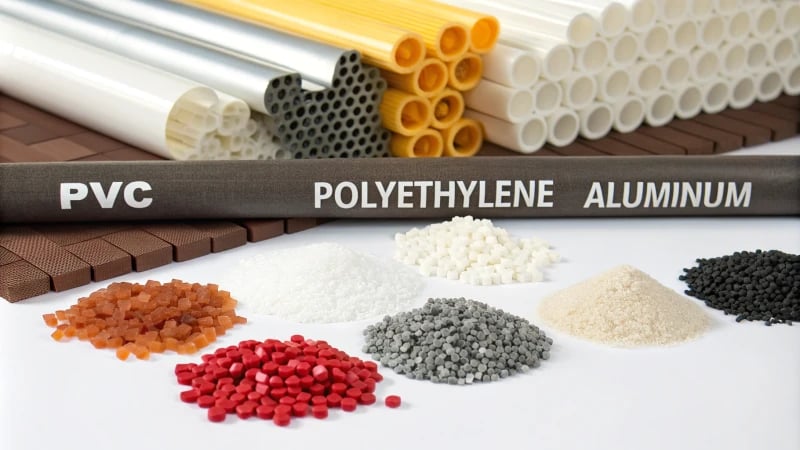
Common Thermoplastics in Extrusion
Extrusion transforms many materials into useful forms. This method mostly uses thermoplastics, which are preferred for their flexibility and easy processing. Some of the most common thermoplastics include:
Material | Characteristics | Applications |
---|---|---|
PVC | Durable, resistant to environmental factors | Pipes, fittings, and profiles |
Polyethylene | Excellent impact resistance, lightweight | Packaging films, bottles, and containers |
Polypropylene | Good chemical resistance and fatigue strength | Automotive parts, containers, and textiles |
Polystyrene | Rigid, easy to mold, good clarity | Consumer products, packaging, and toys |
My first project involved designing a PVC pipe. Its robustness was astonishing. It suits applications like plumbing and construction.
Metals Used in Extrusion
Thermoplastics often take center stage in extrusion. However, metals play an important role too. Commonly used metals include:
Material | Characteristics | Applications |
---|---|---|
Aluminum | Lightweight, corrosion-resistant | Structural components, frames |
Copper | Excellent conductivity and malleability | Electrical applications, plumbing |
Brass | Good strength and corrosion resistance | Plumbing fittings, decorative items |
The variety of metals used surprised me. The first time I saw aluminum extruded into window frames amazed me. Lightweight yet strong, it suits applications needing both strength and lightness.
Special Applications in Extrusion
Extrusion technology creates unique profiles for specialized uses. For example:
- Special profiles for architectural elements can have intricate designs that enhance beauty while also being structural. I have seen stunning door frames with complex shapes that looked amazing and served their purpose well.
- Rod and pipe extrusion creates consistent shapes for specific uses. I once worked on plastic rods used as structural supports. The precision of extrusion impressed me. Explore rod applications9.
Conclusion
Material choice in extrusion greatly affects product performance and application. A durable PVC pipe or an elegant aluminum frame needs careful material selection. Right material choice can impact both functionality and appearance. This balance is very important in effective design and manufacturing.
PVC is commonly used in extrusion for pipes and fittings.True
PVC's durability and environmental resistance make it ideal for pipe applications in extrusion processes.
Aluminum is the only metal used in extrusion processes.False
While aluminum is popular, other metals like copper and brass are also commonly extruded for various applications.
What Applications Benefit from Specific Extruded Profiles?
Have you ever thought about how those complex plastic shapes we see daily are created? Let’s explore the interesting world of extruded profiles. These shapes influence many industries!
Extruded profiles are very important for many uses. They include pipes for moving fluids and rods for machining. They also include special shapes for architectural designs. Each profile is crafted uniquely. Each has a specific purpose to fulfill industry needs. They improve how things work. These profiles also really add to how things look.
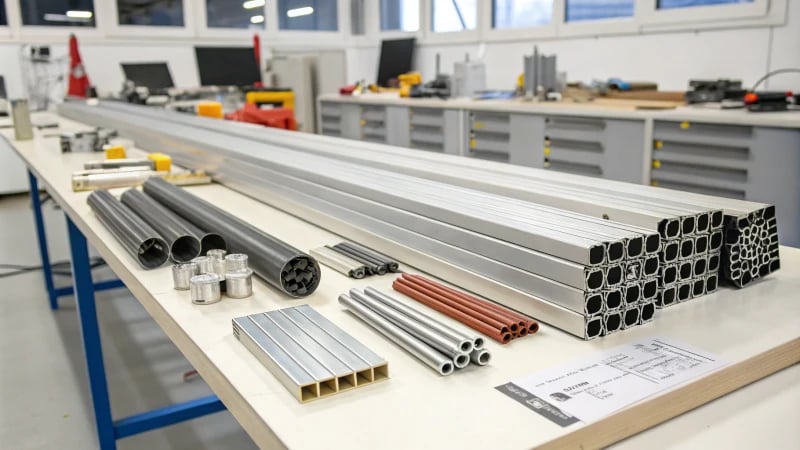
Understanding Extruded Profiles in Different Applications
Extrusion felt like finding a hidden treasure in manufacturing. Shaping materials into continuous profiles with a constant cross-section is amazing! This process changes how we create components for specific uses. It touches my passion for design and innovation deeply.
1. Pipes: Versatile Solutions for Fluid Transport
Let’s explore pipes, a common extrusion application. I recall my first plumbing project where I picked materials. The variety of extruded pipes surprised me! Water supply pipes bring drinking water to homes. Drainage pipes remove waste. Gas pipes carry natural gas safely. Their versatility is impressive.
Pipe Type | Common Use | Features |
---|---|---|
Water Supply | Drinking water distribution | Circular cross-section, various thickness |
Drainage | Wastewater removal | Durable and resistant to corrosion |
Gas | Transport of natural gas | High pressure tolerance |
Selecting the right pipe seems overwhelming. Strict regulations exist. I once had to balance safety and efficiency in another project. Every detail was crucial! Curious about pipe applications? Discover more here10.
2. Rods: Essential Components for Various Industries
Extruded rods interest me too. I initially viewed them as basic materials. Soon, I saw their importance in different industries. Extruded rods form Machining Blanks for designing. They have circular or square shapes and different lengths. Such versatility!
Rod Shape | Application | Benefits |
---|---|---|
Circular | Machining | Easy to cut to length |
Square | Support structures | Stable and versatile |
Customization feels like a dream. I love creating unique solutions. Interested in rod applications? Visit this link11.
3. Special Profiles: Tailored Solutions for Specific Needs
Special profiles are thrilling! Complex shapes fit certain applications. I recall working on Window and Door Frames with intricate designs. They looked beautiful and worked better with features like card slots and sealing grooves.
Profile Type | Application | Design Features |
---|---|---|
Window/Door Frames | Structural integrity and insulation | Polygonal cross-section |
Architectural Decorations | Aesthetic enhancement | Complex patterns with protrusions |
Special profiles reflect creativity and precision. They are not just shapes but key elements in constructing buildings! They surely bring structures to life. Learn more about these profiles here12.
Extruded pipes are used for transporting natural gas safely.True
This claim is true as extruded pipes are specifically designed to handle high pressure and ensure safe transport of natural gas.
Special profiles are not used in construction applications.False
This claim is false since special profiles, like window frames, are essential for structural integrity and insulation in construction.
Conclusion
Extrusion is a versatile plastic processing technique that creates continuous shapes such as pipes, rods, and special profiles for various applications while offering cost efficiency and design flexibility.
-
Clicking this link will provide you with detailed insights into cost-saving measures associated with extrusion that can benefit your manufacturing processes. ↩
-
Explore this link to learn about the latest design innovations in extrusion that can enhance your product’s functionality and aesthetics. ↩
-
This link offers comprehensive information on material performance characteristics crucial for making informed manufacturing decisions. ↩
-
Explore detailed insights on how extrusion parameters affect product quality for enhanced manufacturing processes. ↩
-
Gain a deeper understanding of screw speed impacts on product consistency and quality in extrusion processes. ↩
-
Discover best practices in controlling temperature during extrusion to improve product outcomes. ↩
-
Learn effective strategies for managing moisture in materials before extrusion to prevent defects. ↩
-
Understand how cooling rates impact the physical properties of extruded materials for better design choices. ↩
-
Learn about the various metals suitable for extrusion to diversify your manufacturing options. ↩
-
Exploring this query will provide you insights into the diverse applications of extruded profiles across various industries. ↩
-
Understanding the uses of specific extruded profiles can significantly benefit product designers and engineers in their projects. ↩
-
This search will help uncover innovative solutions involving extruded profiles tailored to meet unique design challenges. ↩