Ever wondered what makes those everyday plastic gadgets tick?
Essential tools for injection mold making include CAD software for design, CNC machines for precision shaping, mold bases, inserts, ejector pins, cooling systems, and precise measuring instruments to ensure molds meet exact production specifications.
I remember my first time stepping into a mold factory, the hum of CNC machines filling the air. It was a lot like assembling a complex puzzle—every piece had to fit just right. Understanding the tools was one thing, but mastering them was where the magic happened. Let’s dive deeper into each tool and uncover some advanced techniques that can take your mold-making skills to the next level.
CAD software is used for design in mold making.True
CAD software assists in creating precise designs for molds.
CNC machines are not used in injection mold making.False
CNC machines are essential for shaping molds with precision.
- 1. How Does CAD Software Enhance Mold Design?
- 2. How Do CNC Machines Transform Mold Making?
- 3. Why Are Mold Bases and Inserts Crucial?
- 4. How Do Ejector Pins Affect Mold Functionality?
- 5. What Are the Best Cooling Systems for Molds?
- 6. How Can Measuring Instruments Improve Mold Accuracy?
- 7. Conclusion
How Does CAD Software Enhance Mold Design?
Imagine transforming complex designs with just a few clicks, bringing creative visions to life with precision and ease. That’s the magic of CAD software in mold design.
CAD software enhances mold design through precise 3D modeling, error reduction, support for complex geometries, real-time simulations, improved collaboration, and optimized manufacturability, ensuring cost-effective and high-quality results.
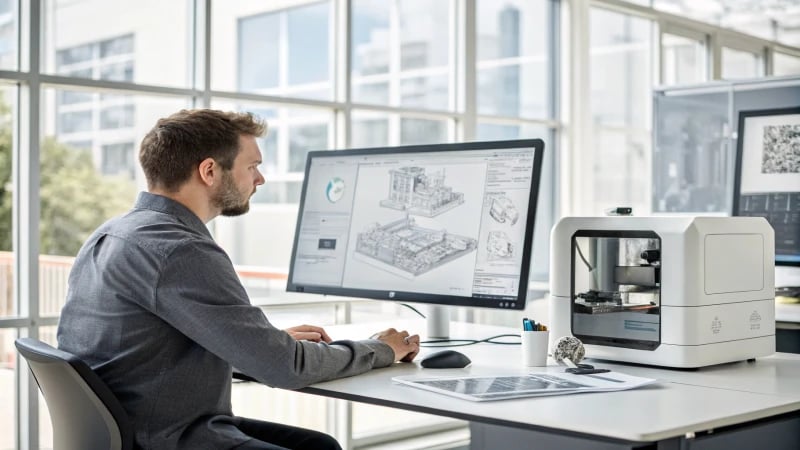
Streamlining the Design Process
As someone who’s spent countless nights perfecting designs for consumer electronics, I’ve come to appreciate how CAD software revolutionizes the process. It allows me to swiftly create and tweak intricate shapes with remarkable 3D modeling1 tools. This transformation is like going from drawing with crayons to painting with fine brushes.
Feature | Benefit |
---|---|
Parametric Design | Allows easy adjustments and iterations |
Library Components | Speeds up repetitive design tasks |
Enhancing Precision and Accuracy
Precision in mold design isn’t just a technical requirement—it’s an art form. I’ve learned that one tiny error can throw off an entire production run. Thankfully, CAD tools come to the rescue with precise measurements and tolerancing2 capabilities, allowing me to catch potential issues long before they become costly mistakes.
Facilitating Collaboration and Communication
Working in a team can sometimes feel like trying to sync up a dance routine over the phone. But with modern CAD solutions, sharing designs in real time has become a game-changer. It feels like having my team right beside me, improving communication and streamlining our workflow.
Improving communication3 between designers and engineers is crucial for aligning project goals efficiently.
Optimizing for Manufacturability
One of the most satisfying aspects of using CAD software is its ability to simulate the injection molding process. This foresight lets me anticipate manufacturing challenges, minimizing material waste and production costs4. It’s like having a crystal ball that helps me ensure that every design not only looks good but is ready for the production line.
By embracing these features, I’ve found that meeting both functional and aesthetic requirements becomes less of a juggling act and more of a graceful dance, making CAD software an indispensable partner in the mold design journey.
CAD software streamlines mold design processes.True
CAD tools allow quick creation and modification of designs, enhancing efficiency.
Modern CAD solutions hinder team collaboration.False
CAD tools support real-time sharing, improving collaboration and communication.
How Do CNC Machines Transform Mold Making?
Ever wondered how those intricate molds for your favorite gadgets come to life? Let me take you on a journey through the world of CNC machines and their pivotal role in mold making.
CNC machines revolutionize mold making by providing unmatched precision, efficiency, and the ability to create complex designs. They automate production, ensuring consistent quality and accuracy in molds.
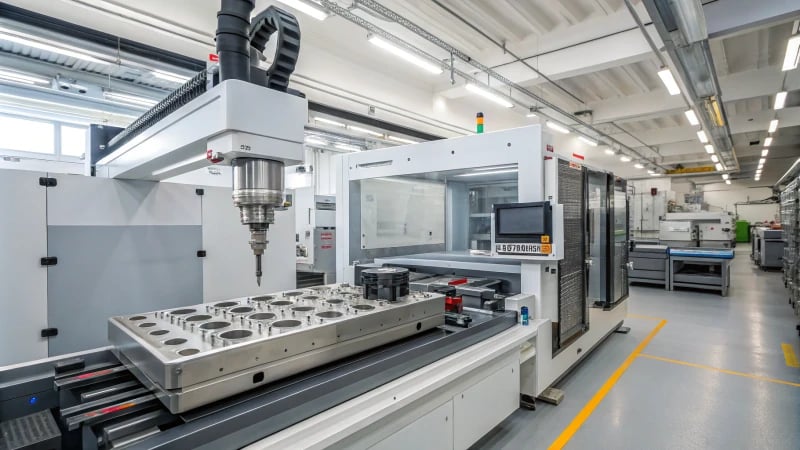
Precision and Accuracy
Imagine trying to carve a delicate sculpture by hand—every minute detail counts, and one slip could ruin the whole piece. This is where CNC machines, or Computer Numerical Control machines, come in. They excel at delivering the high precision and accuracy needed in mold making5. By using computer-aided designs (CAD) for programming, CNC machines ensure each mold meets exact specifications. I remember the first time I saw a CNC machine in action; it was like watching an artist at work, crafting with meticulous detail that seemed almost magical compared to the traditional manual methods.
Efficiency and Time Savings
The automation of CNC machines is a game-changer. Back when I started, the manual machining process was like watching paint dry—painfully slow. But CNC machines changed all that. They operate continuously, only pausing for maintenance or programming updates. This relentless efficiency leads to faster turnaround times and improved productivity. It’s like having a dedicated team working round the clock, but without the coffee breaks.
Feature | Manual Machining | CNC Machining |
---|---|---|
Precision | Moderate | High |
Speed | Slow | Fast |
Consistency | Varies | Consistent |
Complex Geometries and Designs
In my early days, tackling complex designs felt like solving a puzzle without all the pieces. CNC machines opened up a new world of possibilities, allowing us to create intricate designs that were once impossible or highly impractical with manual methods. This capability is especially valuable in industries requiring detailed molds, such as automotive or consumer electronics6. With CNC machines, it’s as if we’re equipped with a magic wand that brings our most imaginative designs to life.
Cost Implications
Yes, the initial investment in CNC machinery can be hefty, much like buying a new car. But just like a reliable vehicle, it pays off in the long run. Reduced material waste and lower labor costs lead to significant savings. Plus, minimizing errors means fewer defective products, which translates into more money saved.
Versatility and Flexibility
CNC machines are like the Swiss Army knives of manufacturing—they’re incredibly versatile. Whether it’s metals, plastics, or composite materials, these machines handle them all with ease. Their flexibility makes them an indispensable tool in modern manufacturing processes7, enabling us to switch between projects seamlessly without missing a beat.
CNC machines improve mold making precision.True
CNC machines use CAD for programming, ensuring molds meet exact specifications.
Manual machining is faster than CNC machining.False
CNC machines operate continuously, reducing production time compared to manual methods.
Why Are Mold Bases and Inserts Crucial?
Ever wondered what makes injection molding so precise and adaptable? It’s all about the mold bases and inserts!
Mold bases offer a sturdy foundation, while inserts provide customization, crucial for efficient production by reducing setup time and enhancing precision in plastic part manufacturing.
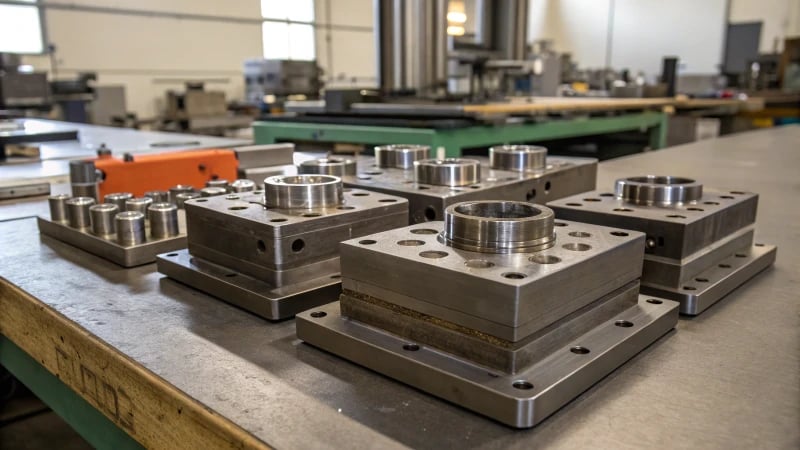
The Role of Mold Bases in Manufacturing
In the world of injection molding, mold bases are like the backbone of the operation. Picture them as the reliable foundation of your house—without them, everything else falls apart. When I first started designing molds, I quickly learned how crucial these bases are. They aren’t just slabs of steel or aluminum; they are the very structure that holds everything together, enduring the intense pressures and temperatures that come with molding.
Key Benefits of Mold Bases:
- Stability: Imagine building a house without a solid frame. Mold bases give you that robust framework, ensuring everything aligns perfectly and errors are minimized.
- Interchangeability: This was a game-changer for me. Switching inserts without changing the entire base saved us so much time and hassle.
- Cost Efficiency: Less downtime means more production, which is always a win in manufacturing.
Feature | Benefit |
---|---|
Durability | Long-lasting use |
Precision | Accurate part creation |
Flexibility | Quick adaptations |
How Inserts Enhance Flexibility and Customization
Think of inserts as the customizable features on your favorite gadget. They’re what make your designs come to life in exactly the way you envisioned. I remember one project where we needed to make last-minute changes to a design. Thanks to inserts, we managed it without any major overhaul—just a simple swap, and we were good to go.
Advantages of Using Inserts:
- Customization: You can easily tweak designs to create new product variations without starting from scratch.
- Reduced Lead Time: Faster setups mean quicker production cycles—something every designer loves.
- Material Efficiency: Using materials only where needed helps reduce waste and optimize costs.
Flexibility in design8 through inserts supports innovation by enabling designers like Jacky to experiment with new shapes and functions without major overhauls.
Balancing Precision and Efficiency
By combining sturdy mold bases with versatile inserts, we achieve both precision and efficiency. This balance is essential for producing high-quality products swiftly, especially in fast-paced markets like consumer electronics. With this setup, we’re always ready to adapt to new market trends or customer demands without skipping a beat.
Explore how mold technology is advancing by delving into modern manufacturing techniques9. These insights can help designers stay ahead in a rapidly evolving industry.
Mold bases are typically made of wood.False
Mold bases are usually made of steel or aluminum, not wood.
Inserts allow for reduced lead time in production.True
Inserts enable quicker setup and changeover, reducing production time.
How Do Ejector Pins Affect Mold Functionality?
I remember the first time I saw ejector pins in action during a factory tour—it was like watching a perfectly choreographed dance. These tiny components are truly unsung heroes in the molding process.
Ejector pins are crucial for safely releasing molded parts, enhancing mold functionality, and reducing defects by using appropriate materials and strategic placement.
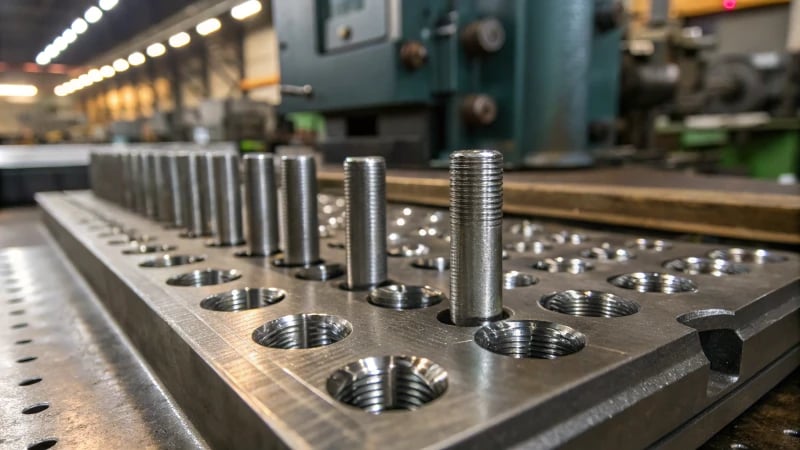
The Role of Ejector Pins in Molding
I’ll never forget the excitement of my first hands-on project involving ejector pins. At the time, I didn’t fully appreciate how these slender pieces of metal could make or break a production line. Their primary job is to gently nudge finished products out of molds. If they’re not up to the task, or if they’re positioned poorly, you could end up with defects like warping or cracks—or even find that the product doesn’t eject at all.
The effectiveness10 of ejector pins directly influences the overall quality of the molded parts and the efficiency of the production process.
Importance of Material and Design
Choosing the right material for ejector pins is like selecting the perfect pair of shoes for a long hike—you need durability and comfort. Hardened steel is often the go-to because it stands up to repeated use without wearing out quickly. But if you’re dealing with a more corrosive environment, stainless steel might be your best friend. And then there’s design to consider: should you go with tapered or straight pins? From my experience, tapered pins often work wonders for smoother releases.
Material | Benefits |
---|---|
Hardened Steel | High durability |
Stainless Steel | Corrosion resistance |
Aluminum Coating | Lightweight and precise |
Optimizing Ejector Pin Placement
Imagine trying to push a stubborn piece of toast out of a toaster with one finger—it’s not very effective, right? Ejector pin placement works on a similar principle. You want even force distribution to prevent any part distortion or surface defects. I’ve found that simulation software can be a lifesaver here, helping to pinpoint exactly where to place these pins for optimal results.
Proper placement11 is key to preventing part distortion or surface defects.
Troubleshooting Common Issues
Common hiccups with ejector pins include leaving marks on your finished product or failing to eject completely. It’s like trying to pull a sticky label off a new gadget—it’s frustrating when it doesn’t come off cleanly. To tackle these issues, adjusting the stroke length or realigning the pins can be crucial steps. Regular checks for wear and tear are also important; they ensure everything runs smoothly without unexpected snags.
Understanding these elements can transform how you approach mold design, making it easier to integrate ejector pins effectively and improve product quality. For more deep dives into injection molding best practices, check out injection molding best practices12.
Ejector pins can cause product warping if misplaced.True
Improper placement of ejector pins can lead to uneven force, causing warping.
Aluminum coating on ejector pins is the most durable option.False
Hardened steel is more durable than aluminum coating for ejector pins.
What Are the Best Cooling Systems for Molds?
Ever find yourself puzzled over which cooling system to choose for your molds? Let’s explore options that could transform your production process!
The best mold cooling systems vary by need, typically using water for rapid heat removal or oil for precise temperature control, especially in complex molds.
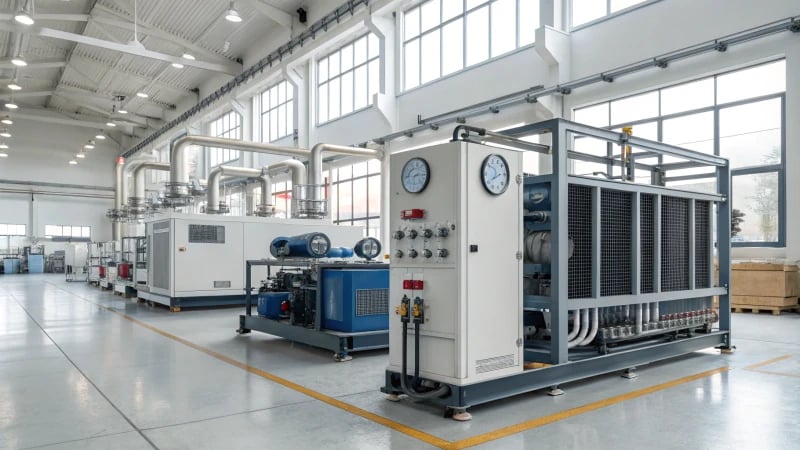
Understanding Different Cooling Systems
Navigating the maze of cooling systems can feel like a daunting task, especially when each choice affects your mold’s performance and the final product’s quality. Over the years, I’ve come to realize how pivotal these systems are—not just in theory but in practice. Once, I faced a massive delay in production because our cooling system couldn’t keep up. It was a learning moment that emphasized the importance of choosing the right system.
Water-Based Cooling Systems
Water-based cooling is like that reliable old friend who’s always there when you need them. It’s the go-to for many due to its sheer efficiency and cost-effectiveness. Water zooms through the mold channels, absorbing heat faster than I could down my morning coffee. But beware—it can be a bit corrosive if you’re not careful, much like how my bike rusted after that one rainy season.
Cooling System | Advantages | Disadvantages |
---|---|---|
Water | Efficient, Cost-effective | Corrosive potential |
Oil-Based Cooling Systems
Now, oil-based systems are a bit like the artist of the group—precise and consistent. They warm up slowly, which is perfect for molds with delicate details. I remember being amazed at how stable the temperature remained during a particularly tricky project. It’s like using a paintbrush instead of a roller; more effort and expense upfront, but worth it for the masterpiece.
| Oil | Precise, Stable | Higher cost |
Advanced Cooling Techniques
For those like me who enjoy pushing boundaries, advanced techniques such as conformal cooling13 are exciting to explore. Imagine 3D-printed channels shaped perfectly to your mold—it’s like having a custom-fit suit! While it’s a bigger investment initially, the payoff in cycle time reduction is significant.
Hybrid Cooling Systems
And then there are hybrid systems—mixing water and oil to get the best of both worlds. It’s like having a convertible car: flexible and adaptable to whatever comes your way. This approach allows me to switch gears easily between different projects without missing a beat.
Understanding these systems’ nuances is key to optimizing mold performance. It ensures that each product not only meets but exceeds quality standards. With new cooling technology14 advancements, staying informed can give you that competitive edge in our ever-evolving industry.
Water cooling is the most efficient method for molds.True
Water cooling quickly absorbs heat, making it efficient for rapid cooling.
Oil-based systems are cheaper than water-based systems.False
Oil systems are more expensive due to precise temperature control capabilities.
How Can Measuring Instruments Improve Mold Accuracy?
Ever wondered how the secret to flawless manufacturing lies in precision? Measuring instruments hold the key!
Measuring instruments boost mold accuracy by providing precise measurements, detecting deviations early, and ensuring production consistency, leading to reduced waste, enhanced quality, and cost savings.
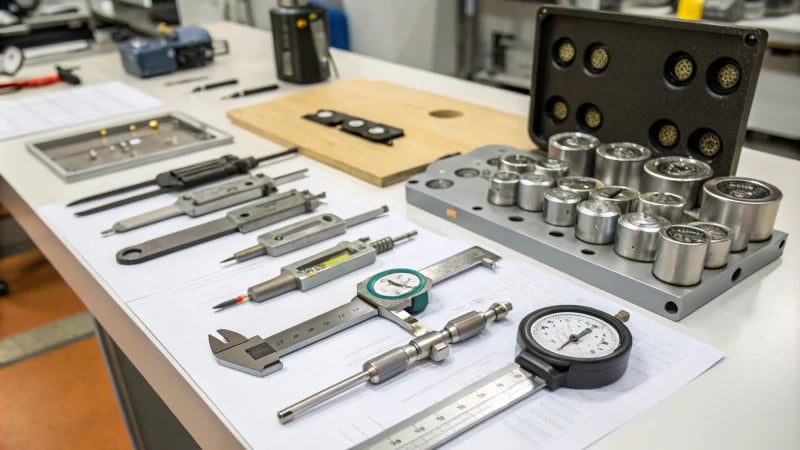
Importance of Measurement in Mold Accuracy
I’ve always been fascinated by the intricacies of mold design, especially when it comes to achieving that perfect fit. It’s not just about aesthetics; it’s about functionality and precision. That’s where measuring instruments come into play. Imagine having a tool like a coordinate measuring machine (CMM) at your disposal—it’s like having a superpower for ensuring every component aligns perfectly with the intended design specifications15. For someone like me, who’s been in the field for over a decade, these tools are indispensable.
Types of Measuring Instruments
-
Coordinate Measuring Machines (CMMs): These machines are like the maestros of precision. They use probes to measure the physical geometrical characteristics of an object with such accuracy that it feels like magic.
-
Laser Scanners: Picture this: a device that captures the entire 3D model of a mold. It’s like having a digital eye that spots even the slightest imperfection.
-
Calipers and Micrometers: They’re like the unsung heroes of measurement—small but mighty, ensuring every little detail fits just right.
Instrument | Accuracy Level | Best For |
---|---|---|
CMM | ±0.002 mm | Complex geometries |
Laser Scanner | ±0.01 mm | Surface detail |
Calipers | ±0.02 mm | Basic measurements |
Benefits of Using Measuring Instruments
These tools aren’t just about precision; they’re about peace of mind:
- Early Detection of Errors: Knowing that errors are detected early means fewer sleepless nights worrying about production delays16.
- Consistency Across Batches: Consistency across batches is another plus—no more surprises when quality checks are due.
- Cost Efficiency: Reducing errors translates directly into less waste and fewer rejections, which is music to any designer’s ears.
Real-world Application Examples
In my career, I’ve seen firsthand how precise molds can make or break a project:
- In the automotive industry, molds for safety components17 like airbags and brakes must be flawless because lives depend on them. Measuring tools ensure these molds meet rigorous safety standards, preventing costly recalls and fostering trust.
- The same goes for electronics manufacturing, where even the tiniest error can lead to faulty components. Advanced measuring techniques allow us to create reliable devices that consumers love and expect.
For someone in my shoes, understanding and utilizing these tools isn’t just beneficial; it’s essential for staying competitive in this ever-evolving industry.
CMMs measure mold geometries with ±0.002 mm accuracy.True
CMMs are designed for high precision, matching complex geometries.
Laser scanners have lower accuracy than calipers.False
Laser scanners are more accurate than calipers, capturing detailed 3D models.
Conclusion
Essential tools for injection mold making include CAD software, CNC machines, mold bases, inserts, ejector pins, cooling systems, and measuring instruments to ensure precision and efficiency in production.
-
Learn how 3D modeling in CAD software allows designers to visualize complex geometries, improving design accuracy and efficiency. ↩
-
Discover how CAD software improves precision through advanced tolerancing capabilities, reducing errors and ensuring high-quality molds. ↩
-
Explore how CAD tools facilitate better communication among design teams through real-time collaboration features. ↩
-
Find out how simulating the injection molding process with CAD software can lead to cost-effective design solutions. ↩
-
This link offers insights into how CNC technology enhances precision, crucial for achieving high-quality molds. ↩
-
Discover real-world applications of CNC machines in crafting molds for consumer electronics, a sector known for complex designs. ↩
-
Explore the diverse applications of CNC technology across various manufacturing sectors, highlighting its adaptability and efficiency. ↩
-
Discover how inserts allow for easy design modifications, enabling diverse product variants with minimal changes. ↩
-
Explore advancements in mold technology that enhance efficiency and innovation in manufacturing processes. ↩
-
This link offers deeper insight into how ejector pins influence the efficiency and quality of injection molding. ↩
-
Discover optimal strategies for ejector pin placement to enhance mold performance and reduce defects. ↩
-
Explore comprehensive guidelines on injection molding practices involving ejector pins for better results. ↩
-
Learn about the benefits of using 3D-printed channels for cooling molds, which can improve heat distribution and reduce cycle times. ↩
-
Discover the latest advancements in cooling technology that could enhance mold efficiency and product quality. ↩
-
Understanding design specifications helps in achieving precise measurements and maintaining quality standards in mold production. ↩
-
Exploring this link explains how early error detection prevents costly disruptions in manufacturing. ↩
-
Discover how precise molds ensure safety and reliability in automotive parts, crucial for consumer trust. ↩