Remember that feeling when a project just clicks, and everything falls into place effortlessly?
Effective mold design hinges on understanding material properties, optimizing cooling channels, and ensuring proper venting to enhance production efficiency and product quality, vital for large-scale manufacturing in industries such as consumer electronics.
While these initial tips offer a glimpse into effective mold design, there’s much more to explore. I remember the first time I nailed a complex mold design—it felt like solving a challenging puzzle. With each new project, diving deeper into advanced strategies and lesser-known insights can refine your approach and unlock even greater success in your designs. Let’s uncover those hidden gems together.
Understanding material properties is crucial for mold design.True
Material properties affect mold durability and product quality.
Proper venting is optional in effective mold design.False
Proper venting prevents defects by allowing air to escape.
- 1. How Do Material Properties Influence Mold Design?
- 2. How Do Cooling Channels Boost Mold Efficiency?
- 3. Why Is Proper Venting Crucial in Mold Design?
- 4. How does CAD software improve the precision of mold design?
- 5. What Are Common Mistakes in Mold Design and How to Avoid Them?
- 6. How Does Effective Mold Design Impact Production Costs?
- 7. Conclusion
How Do Material Properties Influence Mold Design?
Every mold tells a story, and it all starts with understanding the material it’s made from.
Material properties such as thermal conductivity, shrinkage, and viscosity are crucial in mold design, impacting cooling rates, precision, and surface finish, thereby enhancing production efficiency and product quality.
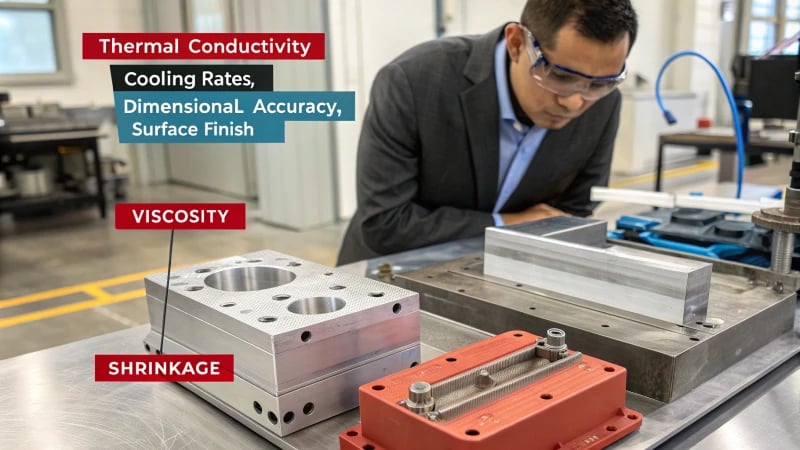
Key Material Properties in Mold Design
When I first dipped my toes into mold design, I was amazed at how much the material properties could dictate the entire process. Thermal Conductivity is one of those pivotal characteristics. I remember working on a project where we used high thermal conductivity materials to hasten production. It was a game-changer but also a challenge to control perfectly to avoid defects.
Shrinkage always keeps me on my toes. It’s fascinating yet tricky since every material behaves differently upon cooling. I once relied heavily on software tools1 to predict shrinkage accurately—saving me from a potential design disaster! Here’s a quick reference table I often use:
Material Type | Typical Shrinkage (%) |
---|---|
Polyethylene (PE) | 1.5 – 3.0 |
Polypropylene (PP) | 1.0 – 2.5 |
Acrylonitrile Butadiene Styrene (ABS) | 0.4 – 0.9 |
Then there’s Viscosity—the ease or resistance with which a material flows. I’ve learned that materials with higher viscosity might need higher injection pressures2 to fill complex molds, a lesson I discovered during a particularly intricate design.
Impact on Cooling Process
The cooling phase is crucial and can make or break the cycle time and part quality. I’ve often opted for materials like aluminum due to its excellent thermal conductivity; it’s enhanced cooling efficiency remarkably in many projects but isn’t always ideal for high-pressure scenarios.
Surface Finish Considerations
Material choice can significantly affect the surface finish of the molded part. In my experience, polymers with additives usually result in smoother finishes, which means less post-processing work—something I always appreciate. For instance, PC/ABS blends often deliver an aesthetic edge that meets client expectations.
Material Selection Strategies
Balancing cost, performance, and processing ease is like walking a tightrope. I perform thorough material compatibility3 analyses to ensure that my choices offer optimal performance while being cost-effective.
By grasping these properties deeply, I’ve been able to make informed decisions that boost mold performance and assure high-quality outcomes. It’s all about finding that sweet spot where art meets science.
High thermal conductivity reduces mold cooling time.True
Materials with high thermal conductivity dissipate heat quickly, shortening cooling time.
All polymers have the same shrinkage rate.False
Different polymers contract differently; shrinkage varies by material type.
How Do Cooling Channels Boost Mold Efficiency?
Ever wondered how a simple tweak in mold design could supercharge your production line?
Cooling channels optimize mold efficiency by maintaining consistent temperatures in injection molding, reducing cycle times, and improving product quality by minimizing defects.
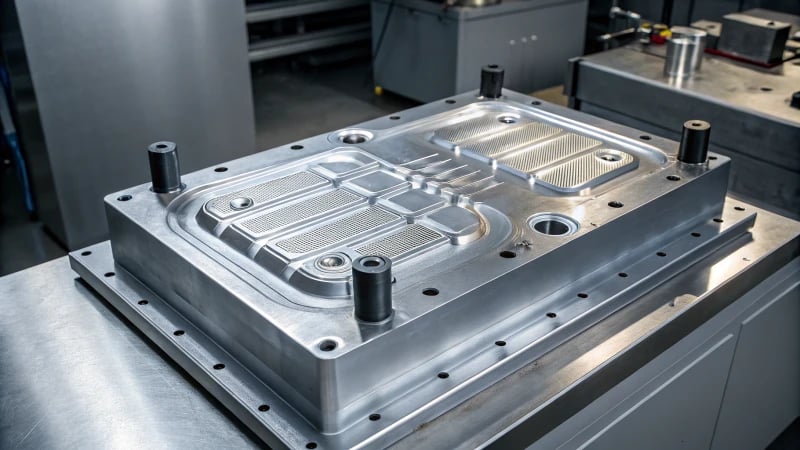
Understanding Cooling Channels
I remember the first time I dove into mold design, being fascinated by the intricate network of cooling channels. These aren’t just random pathways; they’re carefully crafted routes for coolant to flow, whisking away heat from the molded part. It’s like giving your mold an efficient air conditioning system! This ensures a consistent temperature4 throughout the process, which is crucial for maintaining the integrity of your design.
Impact on Cycle Time
In one of my early projects, I discovered how strategic cooling could shave precious minutes off cycle times. Imagine cutting down the production time, not just by seconds, but by minutes! Faster cooling translates to shorter cycles, which means you can push out more products without compromising on quality. When the mold cools evenly, it prevents issues like warping or other defects, guaranteeing high-quality outcomes every time.
Benefits | Description |
---|---|
Reduced Cycle Time | Shortens production cycles for higher throughput |
Improved Quality | Minimizes defects like warping or sink marks |
Enhancing Product Quality
It’s amazing how cooling channels directly impact the quality of the finished product. I once faced a challenge where inadequate cooling led to noticeable sink marks on our parts. After tweaking the channel design, we achieved uniformity, resulting in better product integrity5. It’s these moments of problem-solving that make me appreciate the art of mold design even more.
Design Considerations
Designing cooling channels is like solving a complex puzzle where every piece needs to fit perfectly. You need to consider factors like channel diameter, spacing, and coolant flow rate. I learned this the hard way during a particularly challenging project where balancing these elements was crucial for maintaining efficiency.
Factor | Importance |
---|---|
Diameter | Affects coolant flow and heat extraction |
Spacing | Ensures even cooling across the mold surface |
Coolant Flow Rate | Determines speed and efficiency of heat removal |
Mastering these aspects empowers designers like me to optimize mold performance effectively. For those wanting to dive deeper, exploring resources on mold design techniques6 is incredibly beneficial. This knowledge equips us to make informed decisions that enhance both our designs and production efficiency.
Cooling channels reduce mold cycle time.True
Efficient cooling channels allow faster cooling, shortening production cycles.
Channel diameter does not affect coolant flow.False
The diameter of cooling channels impacts the flow and heat extraction efficiency.
Why Is Proper Venting Crucial in Mold Design?
Ever wondered why some molds fail while others churn out perfect parts every time? It’s often down to one tiny detail: venting.
Proper venting in mold design ensures trapped gases escape during molding, preventing defects like burn marks, ensuring high-quality parts, and enhancing manufacturing efficiency.
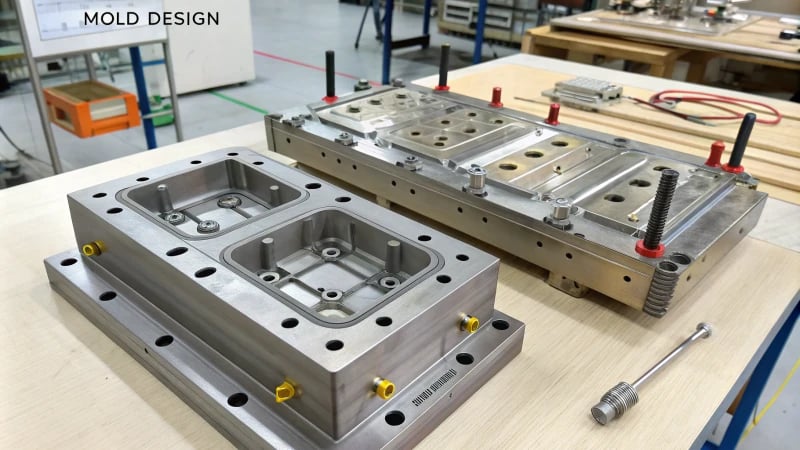
The Role of Venting in Mold Design
In the world of mold design, I’ve learned that it’s the little things that make a big difference. Proper venting is like letting your molds breathe, allowing trapped gases to escape during the plastic injection molding process7. Picture this: without it, air gets stuck inside, much like when you try to squeeze into jeans that are just a size too small. This can lead to defects.
Issue | Impact on Parts |
---|---|
Air Entrapment | Burn marks, voids |
Incomplete Fill | Weakened structural integrity |
These defects don’t just make parts look bad; they can turn what should be a sturdy piece into a fragile mess. That’s why every vent must be meticulously designed for smooth production.
Types of Venting Techniques
I’ve tried various venting techniques over the years, and understanding them can be as crucial as knowing your morning coffee order. Here are the basics:
- Venting Slots: These are like tiny escape routes for gases, perfect for thin-walled parts.
- Venting Pins: Strategically placed pins, a lifesaver for deep cavity molds.
- Venting Inserts: Customizable inserts, much like choosing toppings on a pizza, tailored to specific part requirements.
Choosing the right technique can feel like picking the right tool from a toolbox; it all depends on factors like part geometry and material properties.
Calculating Vent Depth and Width
One of the trickiest parts of mold design is getting the vent depth and width just right. I remember spending long nights tweaking these calculations because an incorrect size can lead to poor venting or unwanted flash. Here’s a quick guide:
- Vent Depth: Typically less than 0.1 mm for most plastics to avoid flash.
- Vent Width: While wider vents help gas escape, they must be balanced carefully to prevent flash.
Thankfully, tools like computer-aided design (CAD) software8 can simplify these calculations, ensuring both optimal performance and part quality.
Focusing on proper venting isn’t just about ticking boxes; it’s about ensuring high-quality products that meet client expectations and industry standards. If you’re eager to explore more, consider delving into advanced mold design techniques9 for innovative solutions that tackle challenging projects head-on.
Venting slots are used in thin-walled parts.True
Venting slots allow gases to escape easily, ideal for thin walls.
Vent depth should exceed 0.1 mm for most plastics.False
Vent depth should be less than 0.1 mm to prevent flash.
How does CAD software improve the precision of mold design?
When I first stumbled into the world of mold design, precision felt like a mythical creature, always just out of reach. But then came CAD software, and everything changed. How does it manage to turn chaos into order?
CAD software improves mold design precision through detailed visualization, simulation, and analysis, allowing early flaw detection, error reduction, and optimal mold performance in production.
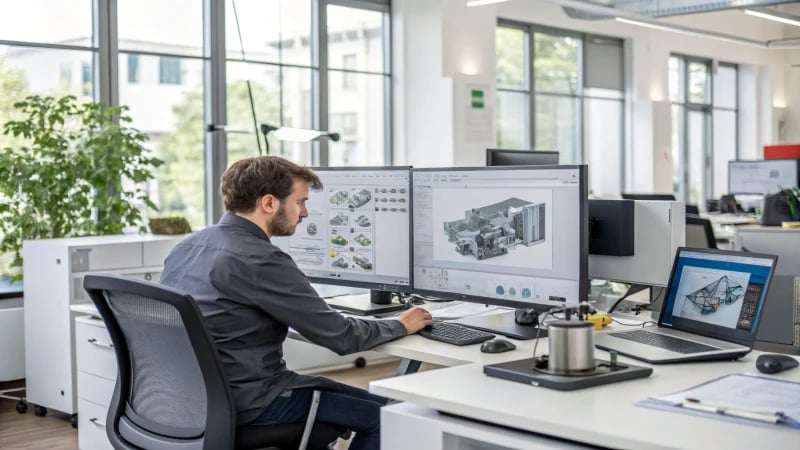
Advanced Visualization and Simulation
In my early days of mold design, I often found myself struggling to imagine how different components fit together. But with CAD software’s advanced visualization10 capabilities, it’s like having a magical window into the future. I can craft detailed 3D models and explore every nook and cranny, making precise tweaks that ensure my designs aren’t just functional but also visually stunning. Plus, the simulation tools are a game-changer. They let me run stress tests and thermal analyses—saving me from countless headaches down the line.
Feature | Benefit |
---|---|
3D Modeling | Allows comprehensive visualization of mold design |
Simulation Tools | Enables stress and thermal analysis to predict performance |
Integration with FEA Tools
I remember the first time I integrated Finite Element Analysis (FEA) into my CAD workflow—it was like unlocking a superpower. FEA helps me unravel complex phenomena like heat transfer and material deformation long before we hit the production floor. This means I can choose materials wisely and ensure structural integrity with confidence. The beauty of FEA in CAD is that it allows for endless experimentation—changing a design based on analysis results feels more like solving a puzzle than just work.
Utilizing FEA tools within a CAD environment also allows for iterative testing and optimization. Designers can modify designs based on analysis results, improving both the precision and functionality of the mold design process.
Collaboration and Efficiency
Working in a team, I’ve learned that communication is key—and CAD software nails it with cloud-based platforms for real-time updates. It keeps everyone on the same page, which is essential when you’re juggling multiple projects. Then there’s the automation feature—oh, how it frees up my time! Tasks like dimensioning and drafting used to eat up hours, but now, I can focus on refining designs to perfection.
Explore automation capabilities11 in CAD software to understand how they contribute to efficiency in mold design workflows.
Thanks to these features, CAD software isn’t just a tool; it’s like having a teammate who never misses a detail. From visualization to collaboration, it empowers me—and countless other designers—to achieve the precision we’ve always dreamed of.
CAD software allows for 3D mold visualization.True
CAD's 3D modeling capabilities enable detailed examination of mold designs.
FEA tools in CAD are used for stress testing only.False
FEA tools analyze heat transfer and material deformation, not just stress.
What Are Common Mistakes in Mold Design and How to Avoid Them?
Ever found yourself tangled up in a design problem that just wouldn’t go away?
Avoid common mold design mistakes like poor cooling systems, inadequate venting, and incorrect material selection by prioritizing meticulous testing, detailed calculations, and expert consultations.
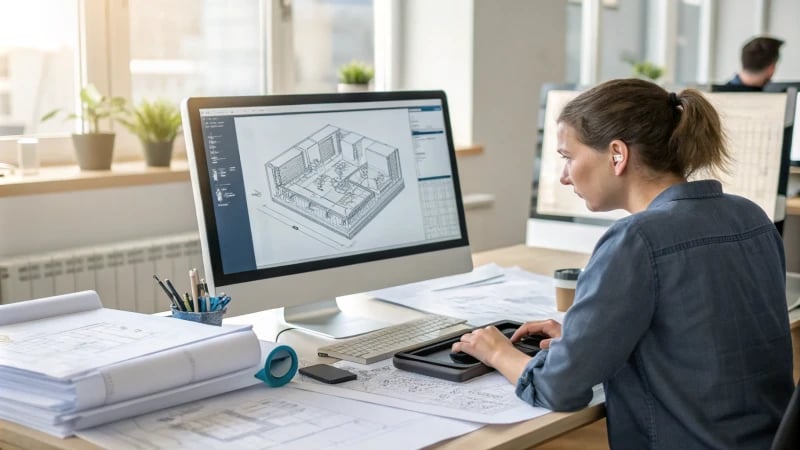
I remember my early days in mold design when a small oversight felt like it could derail everything. Back then, I learned the hard way how crucial it is to avoid certain pitfalls that can lead to costly mistakes.
Poor Cooling System Design
A few years ago, I discovered just how vital a well-designed cooling system is. Imagine spending hours perfecting a mold only for it to warp or shrink because the cooling wasn’t uniform. It was frustrating! Nowadays, I ensure even cooling by implementing efficient cooling channels12 and using advanced simulation tools.
Cooling Design Aspect | Importance |
---|---|
Uniformity | Prevents warping and shrinkage |
Efficiency | Reduces cycle time |
Simulation Tools | Enhances design accuracy |
Inadequate Venting
I once had a project where insufficient venting caused air traps that resulted in short shots. It’s a classic mistake. Now, I make sure to incorporate adequate vents tailored to the part’s geometry and material characteristics, preventing those pesky burn marks.
Incorrect Material Selection
Choosing the right material can make or break a mold. Early in my career, I picked a material that wore out rapidly under stress. Lesson learned! Now, consulting with material specialists13 ensures the material fits the specific application needs.
Lack of Collaboration with Engineers
Skipping collaboration with engineers is a trap I fell into before. Missing out on their insights can lead to major setbacks. These days, I prioritize regular meetings and feedback sessions with production engineers to catch potential issues early.
If you’re like me and eager to keep refining your craft, dive into resources like design checklists14 and case studies from the industry. They’ve been invaluable in my journey to optimizing designs.
Addressing these common mistakes requires a proactive approach and continuous learning—principles that have helped me significantly improve the quality and efficiency of my mold designs.
Uniform cooling prevents warpage in molded parts.True
Uniform cooling ensures even temperature distribution, reducing defects.
Incorrect material selection has no impact on mold longevity.False
Wrong materials can wear rapidly, leading to mold failure.
How Does Effective Mold Design Impact Production Costs?
Ever wondered how a tiny tweak in mold design could save you big bucks on production? Let me walk you through the magic behind it.
Effective mold design reduces production costs by minimizing material waste, shortening cycle times, and enhancing product quality, thereby maintaining competitiveness.
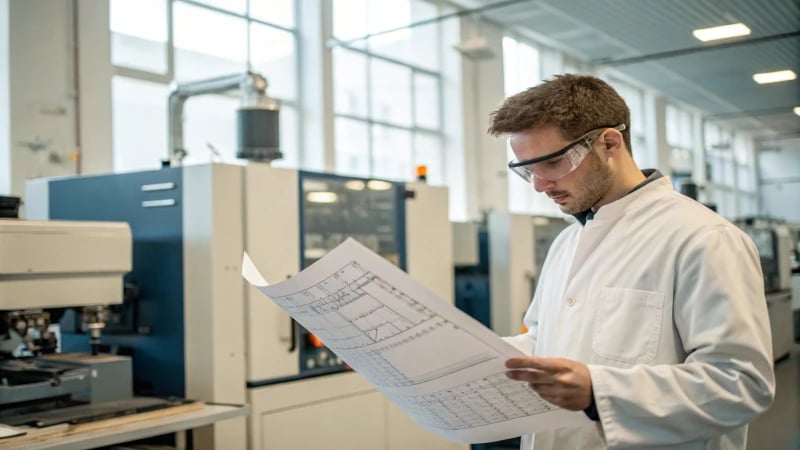
The Role of Material Efficiency
I remember a project where we were aiming to reduce costs without sacrificing quality. The key was tweaking the mold design to use just the right amount of material—no more, no less. By focusing on minimal wall thickness15, we managed to cut down on excess material. It was like finding that perfect balance in a recipe that makes everything taste just right.
Cycle Time Reduction
During another project, we revamped our approach to the mold’s heat transfer and ejection processes. The transformation was incredible—our production cycles became faster, almost like someone pressed the fast-forward button on a movie. Using features like conformal cooling channels16, we improved heat dissipation and watched as our output soared.
Design Feature | Impact on Production |
---|---|
Minimal wall thickness | Reduces material use |
Conformal cooling channels | Shortens cycle time |
Enhancing Product Quality
One of my favorite moments in design is seeing a product come out just right—consistent and flawless. It’s like that feeling you get when you finally nail a tough recipe. Effective mold designs ensure uniform flow and minimize defects, which means fewer parts get rejected. Techniques such as flow simulation analysis17 help predict issues before they become real problems.
Long-Term Financial Benefits
Investing in top-notch mold design is like buying quality tools—they pay off over time. With durable materials and precise engineering, our molds last longer, saving us from frequent maintenance headaches. I’ve learned to always consider the total cost of ownership18 because it’s a game changer for long-term success.
In summary, when I focus on effective mold design, I’m not just thinking about the immediate process improvements. It’s about setting up for substantial savings in the long run and keeping that competitive edge in the market.
Minimal wall thickness reduces production costs.True
Using minimal wall thickness strategies decreases material waste, cutting costs.
Conformal cooling channels increase cycle time.False
Conformal cooling channels enhance heat dissipation, reducing cycle time.
Conclusion
Effective mold design hinges on understanding material properties, optimizing cooling channels, and ensuring proper venting to enhance production efficiency and product quality in manufacturing processes.
-
Click to learn how advanced software tools can accurately predict material shrinkage, aiding in precise mold design. ↩
-
Explore how viscosity impacts mold filling and what strategies improve flow for complex geometries. ↩
-
Discover methods for assessing material compatibility to enhance performance and cost-effectiveness in mold design. ↩
-
Discover how cooling channels help maintain consistent temperatures during molding for optimal efficiency. ↩
-
Learn how proper cooling reduces defects like warping and improves overall product quality. ↩
-
Explore advanced techniques for designing effective cooling channels in molds. ↩
-
This link provides an overview of why venting is critical in plastic injection molding, emphasizing its role in preventing common defects. ↩
-
This resource offers detailed guidance on calculating optimal vent dimensions, crucial for avoiding flash and ensuring effective gas escape. ↩
-
Explore innovative mold design strategies that enhance venting efficiency, reducing defects and improving part quality. ↩
-
Discover how 3D visualization tools in CAD software enhance design precision by allowing detailed examination of mold structures. ↩
-
Learn about the automation features in CAD software that improve efficiency by handling repetitive tasks in mold design workflows. ↩
-
Efficient cooling channels are critical for reducing cycle times and preventing defects. This link provides techniques for designing effective cooling systems. ↩
-
Selecting the right material is crucial for durability and performance. This link offers guidance on choosing materials based on application needs. ↩
-
Checklists help ensure all design aspects are considered. This link provides a comprehensive list tailored for mold designers. ↩
-
Explore how minimal wall thickness can lead to significant material savings in mold design. ↩
-
Learn how conformal cooling channels can enhance heat dissipation and reduce cycle times. ↩
-
Discover how flow simulation analysis helps predict issues and improve product quality. ↩
-
Understand why considering the total cost of ownership is vital for long-term savings. ↩