Do you ever gaze at a plastic gadget and wonder about its origin? Explore the captivating realm of injection mold design!
The main rules for creating a good injection mold are functionality, cost, ease of use and strength. These rules help the mold fit product needs. They keep costs low and make production simple. They also ensure durability.
I recall visiting the factory and looking at a mold, puzzled by its complex design. I realized the importance of understanding these principles. Each principle helps turn an idea from paper into something real. In this journey, I will share stories and insights that have taught me lessons. I hope these stories connect with your experiences. They might help you improve your skills in mold design.
Mold strength is crucial for high-pressure injection molds.True
High-pressure injection molds require sufficient strength to prevent deformation.
Complex mold structures reduce manufacturing costs.False
Simpler mold structures are preferred to reduce costs and processing time.
How Does Functionality Influence Mold Design?
Let’s go on a journey into the interesting world of mold design and see how important functionality is. Mold design plays a big role in the quality of final products. This is true for both simple cups and complex gadgets.
Functionality in mold design revolves around meeting the product’s needs. The mold helps in easy demolding and wisely uses materials. Designers should really focus on product shape. Material flow also matters. Ejection methods are important for performance and reliability.
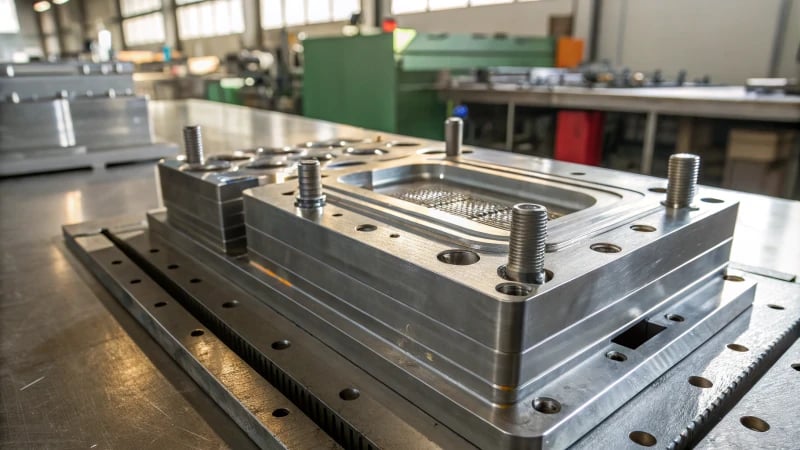
Functionality Guidelines in Mold Creation
I remember the first time I watched a complex mold coming together. I felt fascinated by how every detail needed to be exact to replicate a product’s shape1, size, and details perfectly. It’s like putting together a puzzle where every curve and edge counts. Think about molding a small, thin-walled part—every piece of plastic needs to flow correctly, or you’ll face irritating defects like short shots.
A well-designed pouring system is crucial. Imagine it as setting tracks for a train; if they’re wrong, the journey stops. For plastics that don’t flow easily, adjusting the gate’s size or shape might be necessary—like going from a single lane to a fan-shaped road for smoother passage.
Demolding is next. I once compared it to getting a cupcake out of a pan without breaking it. The ejector system needs designing so it pushes the product gently without causing damage. Special tools, like tilt ejectors, are necessary for complex shapes such as those with reinforcement bars.
Cost Considerations
Money factors are key in mold design, though often overlooked. Choosing correct materials can be like choosing the right ingredients for cooking—it impacts everything from price to lifespan. For low-batch production, cheaper steel might work, but high-precision molds call for quality steel.
I discovered early that simplifying a mold’s structure saves both money and time. It’s like streamlining a morning routine—cut what isn’t needed and more gets done quicker and cheaper. Using standard parts is like having Lego pieces that fit anywhere; they ease maintenance.
Processability and Dependability
Planning for processability is like organizing a kitchen: everything should be handy and simple to use. Avoiding steep cavity walls and tight corners simplifies machining and prevents problems.
Dependability is necessary because molds handle huge pressures; they need strength akin to a top athlete2. Main parts need careful calculations to cope with these forces. Moving parts like sliders should move easily, avoiding wear like a smooth machine.
Summary Table
Principle | Key Focus |
---|---|
Functionality | Accurate shape replication |
Economy | Material selection and cost |
Processability | Ease of manufacturing |
Reliability | Structural integrity and longevity |
Thinking about my mold design journey, I see it’s like crafting a work of art—balancing function, cost, ease, and dependability isn’t only important; it’s creative. Every project presents new challenges and learning opportunities, driving me to invent and improve my methods.
Mold materials should always be high-quality steel.False
High-quality steel is used for precision molds; lower-cost steel suits less demanding applications.
Ejector systems must prevent product damage during demolding.True
Effective ejector systems ensure smooth demolding, preventing product damage.
What Are the Economic Considerations in Mold Material Selection?
Curious about how the right mold material might impact your production process?
Choosing the right mold material depends on how long the mold will last, how much it needs to produce and how accurate it needs to be. Manufacturers probably opt for cheaper materials where high quality is not crucial. For important parts, they pick top-grade materials. This method helps find a balance between price, strength and usefulness. Very important.
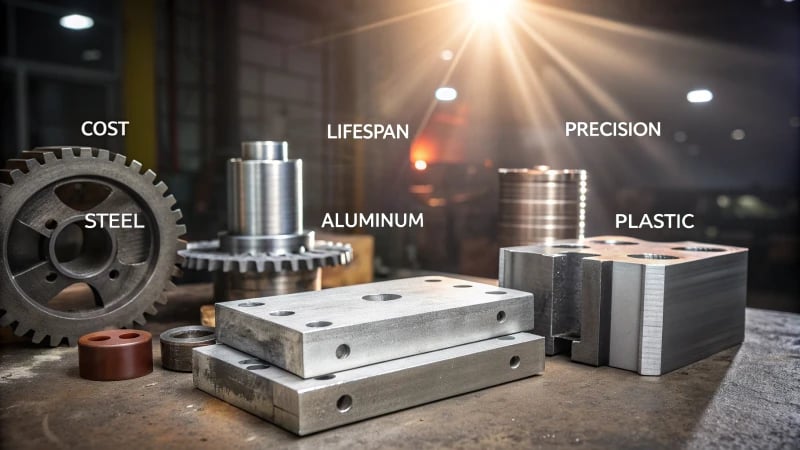
Assessing Mold Lifespan and Production Volume
I recall one of my early projects where I discovered that not all mold materials are the same. We needed to produce a large number of items, and I chose a cheaper material to save money. Bad choice. The molds wore out quicker than expected, causing expensive delays and extra work. From that experience, I learned an important lesson: high-quality steel is important for high-volume production because it lasts longer. For smaller batches, choosing less expensive materials is fine if it doesn’t lower the quality.
When selecting mold materials, evaluating the expected lifespan and production volume is critical. High-volume production molds should use high-quality steel to withstand repeated use. Conversely, small batch productions3 may benefit from using less expensive materials without sacrificing quality.
Balancing Material Cost with Precision Requirements
Precision is crucial in mold design. I’ve seen how even small mistakes can cause products to be rejected. In a project with intricate consumer electronics, we used high-quality materials for vital components like the die kernel to guarantee precision and strength. For less important parts, standard steel kept expenses under control. This plan helped us maintain necessary quality without spending too much on less important areas.
The choice of mold material significantly influences the precision of the final product. High-precision molds demand high-quality materials to ensure stability and durability. It’s wise to use cost-effective materials in non-critical areas while reserving premium options for essential components like the die kernel.
Component | Suggested Material | Reason |
---|---|---|
Die Kernel | High-quality steel | Critical for product shaping |
Die Embryo | Standard steel | Non-essential, reduces overall cost |
Simplifying Mold Structure to Reduce Costs
Simplicity is not just about looks; it’s also about saving money. By simplifying mold designs, such as using simple manifold shapes in the pouring system, I reduced extra parts and steps, cutting down material waste and costs. This plan is practical—simple molds meet production needs without being too complicated.
Optimizing mold structure can lead to significant cost savings. Simplifying designs helps in minimizing unnecessary parts and processing steps. For instance, adopting4 straightforward manifold shapes in the pouring system can reduce both material waste and processing expenses.
Utilizing Standard Parts for Cost Efficiency
A mentor once taught me the value of standard parts in mold creation. Using these parts in designs lowers manufacturing and maintenance costs and speeds up production—perfect for companies like mine that produce large quantities. Standard parts are interchangeable; they are ideal for making designs efficient and cost-effective.
Incorporating standard parts into the mold design promotes interchangeability, thus reducing manufacturing and maintenance costs. This approach also shortens the production cycle, making it more efficient for companies focusing on high-volume outputs.
Considering Processability for Economic Gains
Designing with processability in mind has saved me many problems. Avoiding overly complicated shapes that hamper machining reduces costs and improves manufacturability. By aligning design with CNC or EDM processes, manufacturing workflows are smoother—this approach saves both time and improves the overall quality of products.
Molds should be designed with ease of processing in mind. Avoiding complex shapes that complicate machining not only reduces costs but also enhances manufacturability by aligning design with machining processes5 like CNC or EDM ensures smoother manufacturing and assembly workflows.
Reflecting on these experiences has shown that smart choices in mold material selection are not just about reducing costs—it’s about balancing quality, function, and efficiency to support lasting manufacturing practices.
Mold design must ensure reliable demolding.True
Reliable demolding is crucial to prevent damage during ejection.
High-quality steel is unnecessary for all molds.False
High-quality steel is essential for high-precision, high-volume molds.
Why is processability crucial in mold manufacturing?
Recall that moment when a small change saved you many hours? In mold manufacturing, processability plays this crucial role. It affects everything, from expenses to quality.
Processability in mold manufacturing is crucial because it dictates how easily a mold is created, assembled and refined. This process directly affects production efficiency. It impacts how cost-effective the operations are. The quality of the final products is also influenced.
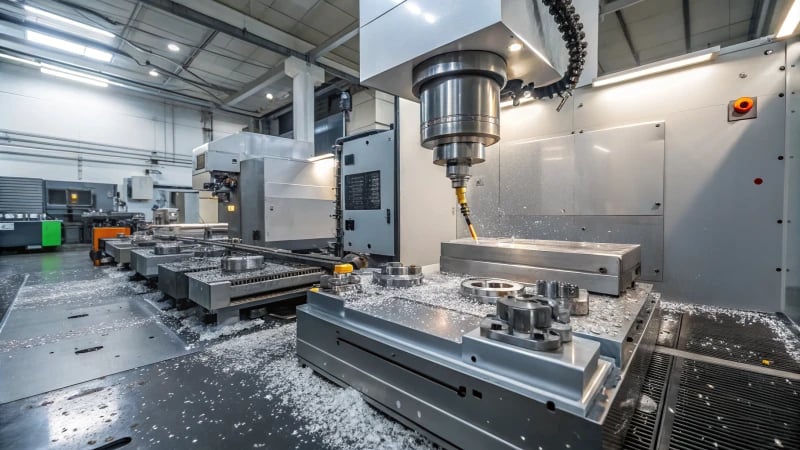
Understanding Processability
I recall the first time I understood how important processability was. It felt like a bright idea clicked in my mind. Imagine dealing with a mold that just doesn’t work, then realizing a small change in design could have avoided days of trouble. Processability keeps molds not only easy to create but also simple to adjust. Avoid steep cavity walls. This straightforward design choice cuts down on machining hassles, making manufacturing much easier. Very easy, indeed.
Processability refers to how easily a mold can be manufactured, assembled, and adjusted. The easier it is to process a mold, the more efficient the entire production process becomes. For instance, avoiding overly steep cavity walls can reduce machining challenges, enhancing the ease of manufacture6.
Influence on Cost
Think of a time when a tight budget pushed you to get creative with materials. Maybe you chose standard parts instead of custom ones. In mold-making, the materials and design decisions are key for keeping costs down. They really matter.
The choice of materials and design significantly impacts costs. Using standard parts and optimizing the mold structure can reduce manufacturing expenses7. For example:
Design Choice | Cost Impact |
---|---|
Standard Parts | Lower costs |
Complex Designs | Higher costs |
Improving Product Quality
Few things compare to seeing a product turn out perfectly after adjusting every tiny detail. Good processability helps molds consistently meet product specifications.
Effective processability ensures that molds meet product specifications reliably. For instance, reasonable gate sizing in the pouring system can prevent defects like short shots, ensuring uniformity in the final product quality assurance8.
Helping Assembly and Debugging
Once, I spent hours trying to fix a complicated assembly and wished for simpler designs.
Planning for easy assembly and debugging at the design stage can change this experience.
Features like adjustable gate sizes make trial molding adjustments smoother, improving performance.
Design considerations that prioritize easy assembly and debugging contribute to improved processability.
Features like adjustable gate sizes aid in fine-tuning during trial molding,
enhancing the mold’s performance optimization9.
Longevity and Reliability
Spending time processing a mold well pays off with longevity and dependability.
I remember a project where choosing the right material and treatments like nitriding increased
the mold’s lifespan a lot.
These choices help molds resist wear over time and support effective durability.
A well-processed mold is not just cost-effective but also durable.
Material selection and treatment processes such as nitriding can extend mold life,
supporting its ability to withstand wear over time durability strategies10.
Mold design must ensure reliable demolding function.True
Reliable demolding prevents product damage during ejection from molds.
Complex mold structures reduce manufacturing costs.False
Simple mold structures are cost-effective, reducing material and labor costs.
How Do Reliability Principles Impact Mold Longevity?
Have you ever thought about how reliable molds might last longer and save a lot of money over time?
Reliability principles act as hidden heroes for mold life. They focus on strong design, long-lasting materials and exact engineering. These principles really let molds last much longer. They reduce maintenance expenses. Product quality stays very high.
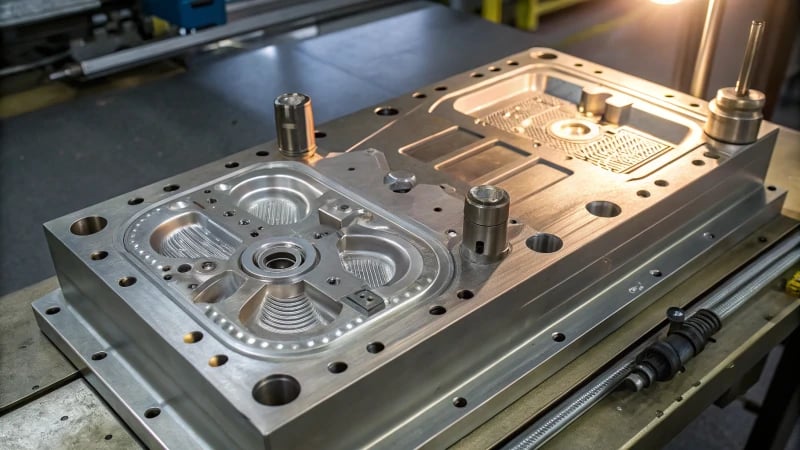
The Role of Mold Strength and Stiffness
I remember the first time I saw a mold buckle under high pressure. Mold strength really matters. Molds must have enough stiffness to handle injection pressures11 without bending. Especially for large or high-pressure molds, checking strength in important parts like the mold frame is crucial. They need to stay strong over time.
Importance of Material Selection
Choosing suitable materials is like selecting the best players for a team – it’s vital for good results. I’ve seen how making a mold surface harder reduces wear, especially under stress. This is essential for molds that experience a lot of force regularly.
Material | Benefits | Use Case |
---|---|---|
High-quality steel | Enhances durability | High-precision molds |
Nitrided steel | Increases surface hardness | Wear-resistant applications |
Designing for Reduced Wear and Tear
Think of designing a mold for less wear like planning a smooth trip – avoiding bumps. In an ejector system, moving parts smoothly means less damage. Proper oiling and space in moving parts like sliders prevent future issues.
Stability of Movable Parts
Smooth motion in molds with sideways core movements is crucial. Good design of guiding tools stops jamming and heavy wear. Regular maintenance checks prolong life.
Consideration of Environmental Factors
Environmental factors like corrosion affect mold life. Special coatings or materials help fight off damage from environmental conditions12. Planning for these challenges from the beginning prevents early failures and extends life.
Following these principles doesn’t just extend mold life – it also keeps quality consistent and lowers costs in production. These steps are vital for designers who focus on mold life and performance in tough settings. It also supports sustainability by increasing efficiency and cutting waste through long use.
Mold strength ensures long-term use without deformation.True
Strength and stiffness calculations prevent mold damage over time.
Using expensive materials always improves mold performance.False
Expensive materials are not always necessary; choose based on needs.
What are common challenges in injection mold design?
Understanding injection mold design is like piecing together a tricky puzzle. I truly know the feeling. I dealt with many choices and challenges to produce effective, error-free products.
In designing injection molds, designers often face common challenges. They need to control material flow well. Accurate mold alignment is really important. Choosing suitable materials requires careful thought. Balancing how a mold works, what it costs and how easy it is to make matters a lot. It is crucial to avoid problems and waste.
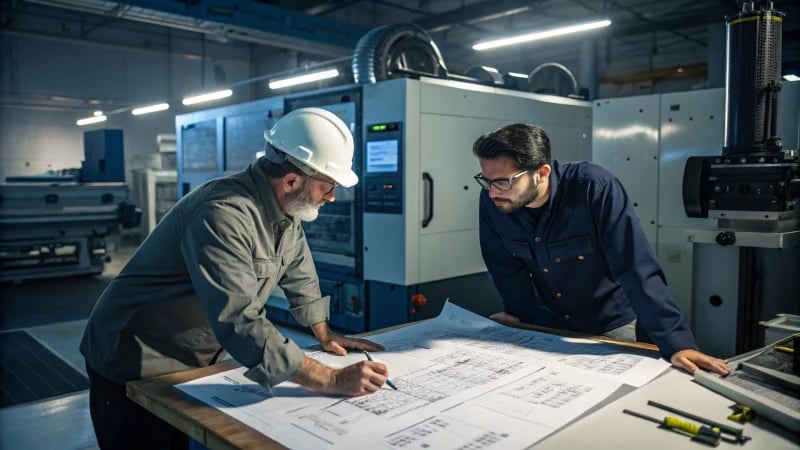
Material Flow Management
Think about pouring pancake batter too fast. It spills everywhere. Managing how molten plastic fills a mold feels similar. Bad material flow13 leads to short shots or shrink marks. It’s like lumpy pancakes that didn’t cook right. Thick plastics need the gate size or shape adjusted.
Issue | Solution |
---|---|
Short shots | Increase gate size or adjust gate location |
Shrink marks | Optimize cooling channels for uniform cooling |
Precision in Mold Alignment
Picture hanging a frame without using a level. Nearly impossible to get it right. Mold alignment needs the same precision. Misalignment can ruin your product and might even damage it during ejection. Correct alignment is very important and relies on well-designed ejector systems14.
Material Selection
Choosing the right materials is important, much like picking the best tool for a job. Decisions depend on the mold’s service life, production volume, and precision.
Consideration | Material Choice |
---|---|
High precision needed | High-quality steel |
Small batch production | Economical steel alternatives |
High-quality steel is good for large runs, while cheaper options work for smaller batches.
Complexity in Mold Structure
Solving a Rubik’s Cube reminds me of mold designs; they really can increase costs and time. Streamlining is important.
Using standard parts helps interchangeability15, reducing costs and making maintenance easy.
Balancing Functionality and Cost
Spending too much on a gadget with features you never use? Mold design can feel like that. Balancing complex designs with budget limits prevents wasting money.
Simplifying structures helps, as does using standard parts.
Processability Challenges
Forcing puzzle pieces together just causes frustration. Creating easy-to-manufacture mold parts prevents issues.
Avoid designs with steep cavity walls or tiny inner radii, which requires understanding CNC and EDM processes for smooth manufacturing.
Facing these challenges takes careful planning; good design principles matter. Reliable and easy-to-process molds are best, blending art and science to create something amazing.
Mold design should ensure reliable demolding function.True
Reliable demolding is crucial to prevent product damage during ejection.
Using high-cost materials always improves mold quality.False
High-cost materials aren't always necessary; use them based on mold requirements.
Conclusion
This article outlines essential principles for effective injection mold design, focusing on functionality, cost efficiency, processability, and reliability to enhance product quality and manufacturing efficiency.
-
Understand how accurate replication of product shapes influences functionality and quality. ↩
-
Learn how choosing the right materials impacts mold durability and cost-effectiveness. ↩
-
Explore how different materials impact costs in small batch productions, optimizing performance without overspending. ↩
-
Learn techniques to streamline mold designs, reducing unnecessary complexities and lowering production costs. ↩
-
Discover how CNC and EDM processes influence mold design, improving manufacturability and cost-effectiveness. ↩
-
Discover techniques to enhance mold processability, which leads to easier manufacturing and better quality products. ↩
-
Learn about strategies to minimize costs by optimizing mold designs and using standard parts. ↩
-
Explore methods to ensure high-quality outputs in injection molding by addressing common defects. ↩
-
Find out how to optimize mold performance through careful assembly and debugging practices. ↩
-
Uncover techniques for extending the lifespan of molds through material selection and treatments. ↩
-
Learn how mold strength calculations prevent deformation under pressure, ensuring longevity. ↩
-
Explore how different environmental factors can impact the durability and effectiveness of molds. ↩
-
Explore techniques to enhance material flow, minimizing defects like short shots or shrink marks. ↩
-
Learn about designing ejector systems that prevent product damage during demolding. ↩
-
Understand how standard parts can reduce costs and simplify maintenance in mold designs. ↩