Ever found yourself staring at a maze of molds, wondering where to begin? I’ve been there, and I know just how crucial mastering multi-cavity mold design is.
Key factors in designing multi-cavity molds include material selection, cavity balance, cooling system design, and efficient ejection methods, essential for high production efficiency and consistent quality.
I remember my first project, standing in front of that daunting array of molds, feeling overwhelmed yet eager to learn. While understanding the basics gave me confidence, delving deeper into each element revealed nuances I hadn’t considered. Let’s break down these factors together, and unlock the potential for improved efficiency and quality in mold design.
Material selection is not important in mold design.False
Material selection is crucial for ensuring durability and functionality.
Efficient ejection methods enhance production efficiency.True
Efficient ejection reduces cycle time, boosting overall production rates.
- 1. How does material selection impact mold design?
- 2. Why is Cavity Balance Important in Multi-Cavity Molds?
- 3. Why Is Cooling System Design Critical in Mold Efficiency?
- 4. How Can I Optimize Ejection Methods for High-Volume Production?
- 5. What Challenges Do Designers Face in Multi-Cavity Mold Design?
- 6. How Can Advanced CAD Tools Enhance Mold Design Precision?
- 7. Conclusion
How does material selection impact mold design?
Every mold designer knows the struggle of balancing material choices with design requirements. It’s not just about picking something that looks good—it’s about crafting a mold that stands the test of time and performs efficiently.
Material selection affects mold design by influencing durability, cost, and thermal efficiency, ensuring robust molds, cost-effective production, and high-quality products.
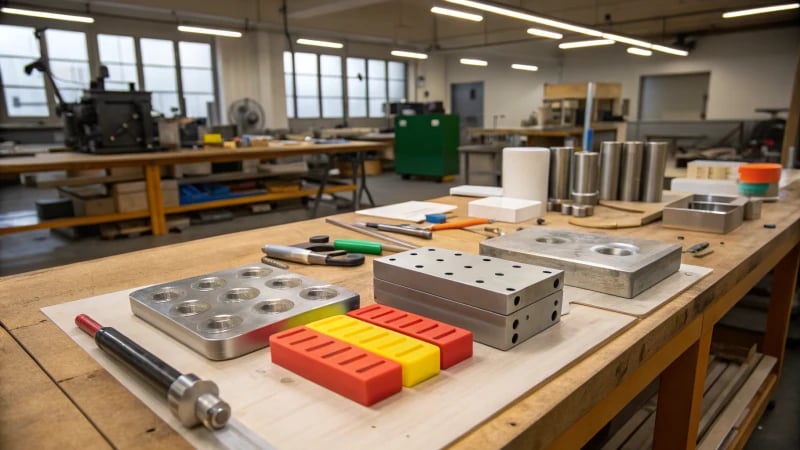
Durability and Longevity
Material selection can significantly impact the durability and longevity of a project. I remember the first time I had to choose between stainless steel and aluminum for a project. It was a bit like deciding whether to invest in a luxury car or go for something more economical but less durable. Stainless steel, with its resilience against wear and corrosion1, felt like the safe bet for long-term use. However, its high cost made me hesitate. Aluminum seemed tempting for quick prototypes where the budget was tight and longevity wasn’t crucial.
- Stainless Steel: A champion in corrosion resistance, perfect for projects where durability is non-negotiable.
- Aluminum: My go-to for experimental runs when we’re still feeling out the production process.
Cost-Effectiveness
Budget constraints are a constant companion in design work. I’ve learned that sometimes, it’s worth splurging on materials that promise longevity, especially when the end goal is mass production. But there are moments when going with a more affordable option like aluminum is the smart move, particularly for short-term projects.
Material | Cost | Durability |
---|---|---|
Stainless Steel | High | High |
Aluminum | Moderate | Low |
Thermal Conductivity
I recall a project where cooling time was eating into our production schedule. That’s when I discovered the magic of beryllium-copper. Its thermal conductivity was a game changer, slashing cycle times and boosting efficiency—a real lifesaver when deadlines loomed.
- Beryllium-Copper: An unsung hero in thermal management, turning our frantic timelines into manageable schedules.
Aesthetic and Functional Requirements
In my line of work with consumer electronics2, the aesthetic finish is just as crucial as functionality. I’ve had to balance materials that offer sleek finishes with those providing structural integrity. It’s like trying to find that perfect pair of shoes—stylish yet sturdy.
Real-World Applications
Thinking back to an automotive project, the stakes were high. We needed materials that could withstand both stress and temperature extremes. Choices here aren’t just about technical specs; they’re about peace of mind knowing the final product won’t fail under pressure.
Designers like me must navigate these factors, juggling material properties to ensure every design decision aligns with the ultimate vision for quality and performance. Understanding these nuances helps craft products that aren’t just built to last but also exceed expectations in every way.
Stainless steel is the most cost-effective mold material.False
Stainless steel is durable but not cost-effective due to high costs.
Beryllium-copper improves cooling efficiency in molds.True
Beryllium-copper's excellent thermal conductivity enhances cooling rates.
Why is Cavity Balance Important in Multi-Cavity Molds?
Ever wonder why some molded parts are just perfect while others are a nightmare? The secret often lies in cavity balance, especially when dealing with multi-cavity molds.
Cavity balance in multi-cavity molds ensures uniform filling, crucial for consistent quality and dimensions, reducing defects, shortening cycle times, and boosting production efficiency.
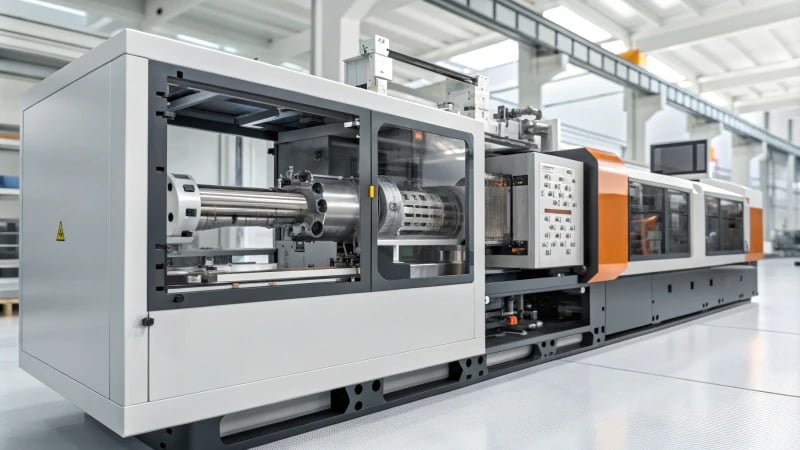
Understanding Cavity Balance
Cavity balance refers to the equal distribution of material flow within the mold during the injection process. In multi-cavity molds, achieving cavity balance3 is vital to ensure each cavity fills at the same rate. This uniformity prevents issues like warping or uneven cooling, which can compromise part quality.
Let me take you back to the first time I realized the power of cavity balance. I was still getting my feet wet in mold design when a senior colleague showed me the ropes. It was like watching a master chef balance the flavors of a complex dish.
Importance in Injection Molding
The role of cavity balance cannot be overstated in injection molding4. It directly influences the quality and consistency of the molded parts. When cavities are not balanced, some may fill faster than others, leading to variations in part dimensions and surface finish. These inconsistencies can result in increased scrap rates and compromised product performance.
I remember the first project where I really had to grapple with this concept. We had a batch of phone cases that kept turning out differently, even though they were supposed to be identical. It turned out the issue was with unbalanced cavities.
Benefits of Achieving Cavity Balance
- Improved Part Quality: Balanced cavities lead to uniform part dimensions, enhancing overall quality.
- Reduced Cycle Times: Proper cavity balance allows for simultaneous filling, reducing cycle times.
- Minimized Defects: With balanced filling, defects such as short shots or flash are minimized.
Benefits | Details |
---|---|
Consistency | Uniform part dimensions |
Efficiency | Reduced cycle times |
Quality | Minimized defects like warping and flash |
Techniques to Achieve Cavity Balance
I’ve found several techniques useful in achieving this elusive balance:
- Gate Design Optimization: By adjusting gate sizes or locations, you can control how material flows into each cavity.
- Flow Simulation Software: Utilizing flow simulation tools5 can help predict and adjust for flow imbalances before actual production.
- Runner System Adjustments: Modifying the runner system can aid in achieving even material distribution.
Challenges in Maintaining Cavity Balance
But let’s be real, keeping things balanced is easier said than done. Despite its importance, maintaining cavity balance can be challenging due to variations in material viscosity or changes in mold temperature that disrupt balance. It’s essential to continuously monitor these variables and adjust as needed for optimal performance.
Exploring these aspects from multiple perspectives helps mold designers6 optimize their processes for better outcomes.
Cavity balance reduces cycle times in injection molding.True
Balanced cavities fill simultaneously, shortening the overall cycle time.
Uneven cavity filling causes consistent part dimensions.False
Uneven filling leads to variations in part dimensions, not consistency.
Why Is Cooling System Design Critical in Mold Efficiency?
I remember my first days in mold design; I quickly learned how vital a cooling system was. It was like the heartbeat of the entire process, impacting everything from speed to quality. Let’s dive into why cooling systems are such a big deal.
Cooling system design is crucial for mold efficiency as it influences cycle times, product quality, and costs, reducing defects, improving energy efficiency, and increasing productivity.
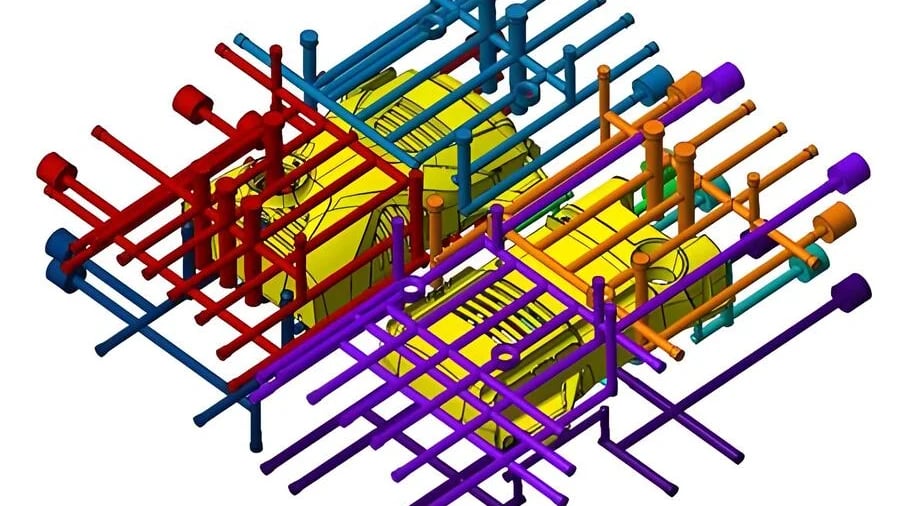
The Role of Cooling in Mold Efficiency
I can’t stress enough how essential an effective cooling system is in the injection molding7 process. It controls the cooling rate of the mold, which in turn affects cycle time and production efficiency. If cooling isn’t up to par, you might face issues like warping, sink marks, or parts that aren’t fully formed. It’s like baking a cake and realizing too late that you forgot to preheat the oven—frustrating and wasteful.
Key Considerations in Cooling Design
-
Uniform Cooling: From my experience, achieving uniform cooling across the mold is crucial. It ensures part integrity and avoids problems like differential shrinkage that can cause warping. I once had a project where uneven cooling nearly derailed us. It was a learning moment I won’t forget.
-
Material Compatibility: Different materials have their own thermal quirks. Understanding these helps in crafting a cooling system that maximizes heat transfer. It reminds me of pairing a fine wine with the right cheese—get it wrong, and the experience falls flat.
-
Flow Rate and Pressure: Meticulously calibrating the flow rate and pressure of your cooling medium is key for efficient heat removal.
Parameter | Impact on Efficiency |
---|---|
Flow Rate | Affects heat removal speed |
Pressure | Influences uniformity of cooling |
Thermal Conductivity | Determines cooling effectiveness |
Common Challenges and Solutions
-
Hot Spots: Sometimes, certain areas cool slower, leading to defects. I found that conformal cooling channels are fantastic for providing targeted cooling where it’s most needed, reducing these troublesome hot spots.
-
Cycle Time Reduction: By optimizing the cooling system design8, I’ve seen firsthand how manufacturers can slash cycle times, boosting production throughput significantly.
Advanced Cooling Techniques
Implementing advanced techniques like baffles or bubblers can greatly enhance heat removal in complex molds. And technologies like conformal cooling9 using 3D printing allow for customized cooling solutions that fit intricate geometries perfectly.
Understanding these elements of cooling design can lead to improved mold efficiency10, higher product quality, and reduced production costs. Trust me, once you master this aspect, you’ll wonder how you ever managed without it.
Uniform cooling prevents warping in molded parts.True
Uniform cooling ensures consistent shrinkage, preventing warping.
High flow rate decreases cooling effectiveness.False
A high flow rate enhances heat removal, improving cooling efficiency.
How Can I Optimize Ejection Methods for High-Volume Production?
Remember that time when a small tweak saved the day on the production floor? Optimizing ejection methods is like that—a simple shift leading to big wins in efficiency.
Optimize high-volume production ejection by selecting suitable systems, maintaining mold conditions, and utilizing advanced technologies. These steps improve efficiency, reduce cycle times, and enhance quality.
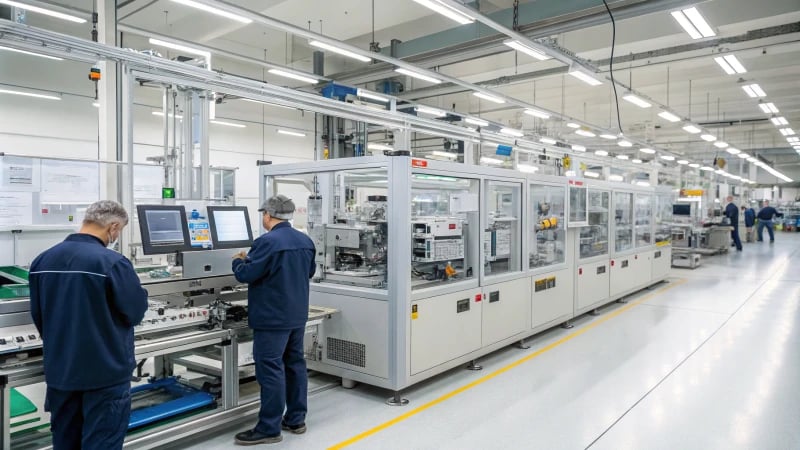
Selecting the Right Ejection System
Back when I first started working with high-volume production, selecting the right ejection system felt like navigating a maze. I quickly learned that you need to consider material type, part complexity, and production volume. Hydraulic ejectors became my go-to for intricate designs—they offer the precision needed. I once followed a comprehensive guide11 that really helped me evaluate different systems and pick the best fit for my projects.
Maintaining Optimal Mold Conditions
Let me tell you, mold maintenance is like taking care of a vintage car. You have to be diligent about regular inspections. I used to neglect this, thinking it was minor, until wear on the ejector pins led to a costly halt in production. Implementing a preventive maintenance schedule12 was a game-changer for extending mold life and boosting performance.
Leveraging Advanced Technologies
Advanced technologies are like the cherry on top of a well-oiled production process. Servo-driven ejectors, for instance, provide not just energy efficiency but also unparalleled control. Plus, integrating sensors13 for real-time monitoring has been invaluable for me in foreseeing and fixing ejection issues before they escalate.
Technology | Benefits |
---|---|
Servo-driven | Energy efficient and precise control |
Sensors | Real-time monitoring for proactive maintenance |
Customizing Ejector Designs
Customizing ejector designs can feel like tailoring a suit—everything needs to fit just right. I once worked on a project with complex molds, and using multi-pin systems was crucial for consistent part removal without delaying the cycle time. You might want to explore custom design techniques14 for improving efficiency in your own setups.
Analyzing Cycle Time Reduction
Reducing cycle time is often the unsung hero of production efficiency. I found that closely examining ejection speed and timing made all the difference. Using cycle time analysis tools15, I’ve been able to identify bottlenecks and streamline operations further—each second saved felt like a mini-victory.
Hydraulic ejectors offer precise control for intricate designs.True
Hydraulic ejectors provide precision, beneficial for complex parts.
Regular mold inspections are unnecessary for ejection efficiency.False
Regular inspections prevent wear, ensuring efficient ejection.
What Challenges Do Designers Face in Multi-Cavity Mold Design?
Ever tried tackling multi-cavity mold design? It’s like juggling—one wrong move and everything can fall apart. But mastering these challenges is what makes our designs shine.
Designers in multi-cavity mold design face challenges like balancing cavity pressure, ensuring part consistency, and managing thermal variations. These are addressed by optimizing runner systems and cooling channels.
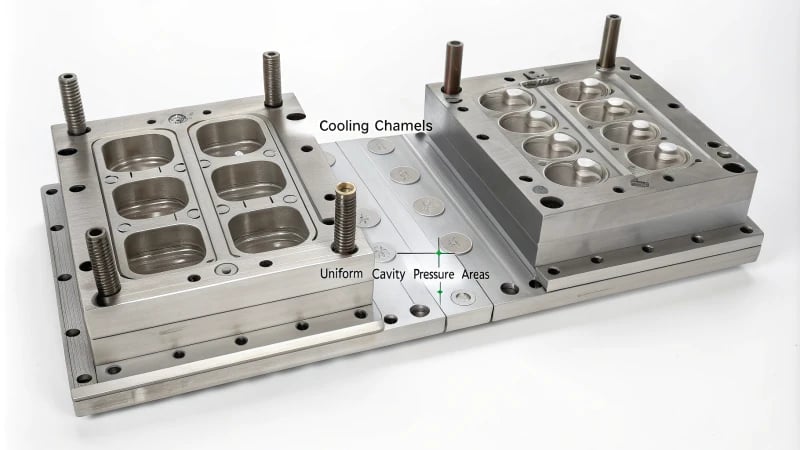
Understanding Uniform Cavity Pressure
I remember my first big project involving multi-cavity molds. It felt like walking a tightrope. Maintaining uniform cavity pressure was a constant battle. One day, I was staring at the screen, wondering why some parts were just slightly off. That’s when it hit me: the runner systems16 weren’t balanced. Each cavity was getting a different dose of pressure, leading to dimensional issues. The key was in optimizing the runner systems to distribute the melt evenly—something that often requires painstaking calculations and a bit of trial and error.
Ensuring Consistent Part Quality
Consistency across cavities isn’t just a buzzword; it’s a lifeline. I recall spending hours with CAD tools, trying to foresee any hiccups in part quality. One time, a slight variation in gate size threw everything off balance. The solution? Regular maintenance and precision machining became my new best friends. And let’s not forget those advanced CAD simulations17 that helped predict potential problems before they turned into costly setbacks.
Managing Thermal Variations
Thermal management can be like taming a wild horse. I once faced warping issues because the cooling rates weren’t consistent across all cavities. It taught me the value of designing effective cooling channels18. Software for thermal analysis became indispensable, helping me spot potential hotspots before they became problems.
Balancing Flow Rates
Flow rate balancing is akin to conducting an orchestra—everything has to be perfectly timed. I learned this the hard way when dealing with defects like short shots and flash. The gating system needed meticulous design so that each cavity filled simultaneously. Using mold flow analysis19 provided insights that were invaluable in adjusting flow rates to ensure uniform material distribution.
Challenge | Solution Strategy |
---|---|
Uniform Cavity Pressure | Optimize runner systems |
Consistent Part Quality | Precise machining and maintenance |
Thermal Variations | Effective cooling channels |
Flow Rate Balancing | Mold flow analysis |
These experiences taught me that while multi-cavity mold design can feel daunting, each challenge is an opportunity to refine our craft and produce impeccable results.
Uneven cavity pressure affects part dimensions.True
Variations in pressure can lead to inconsistent dimensions, impacting quality.
Thermal management is unnecessary in mold design.False
Effective thermal management prevents defects like warping and incomplete filling.
How Can Advanced CAD Tools Enhance Mold Design Precision?
Ever wonder how those sleek designs we rely on every day come to life? As a mold designer, I’ve found that precision is the secret sauce, and advanced CAD tools are my go-to for achieving it.
Advanced CAD tools improve mold design precision with accurate simulations, enable complex geometries, precise tolerances, real-time collaboration, and automated error detection, streamlining the design process overall.
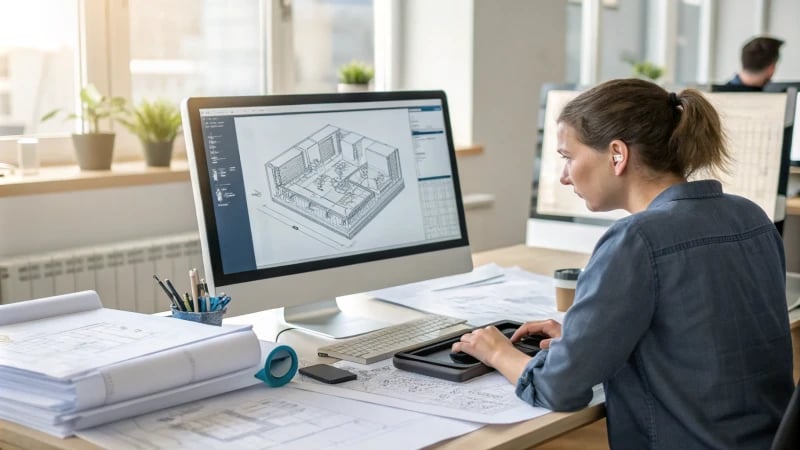
The Role of Simulation in Enhancing Precision
I remember the first time I watched a simulation of a mold design20. It was like peering into a crystal ball—predicting how materials would flow and where potential hiccups might arise. These simulations have saved me countless hours, allowing me to tweak and perfect designs before the first prototype is even molded. The beauty of these tools lies in their ability to uncover issues early on, saving on both time and material waste.
Simulation Benefits | Description |
---|---|
Early Error Detection | Identify design flaws before physical prototyping |
Cost Efficiency | Reduce costs associated with reworking and material waste |
Time Savings | Accelerate the design-to-production timeline |
Facilitating Complex Geometries
There was this one project I worked on that required some truly intricate internal structures. Using advanced CAD tools felt like having a magic wand. These tools allowed me to visualize designs in 3D, adjust them on the fly, and ensure that every little detail was just right. The algorithms handled complex geometries with ease, which meant I could focus on being creative without worrying about technical constraints.
- Visualize and adjust designs in 3D
- Implement precise measurements and dimensions
- Ensure consistency across all components
Real-Time Collaboration Features
Working across time zones and borders is part of the job now, and advanced CAD tools make it seamless. I can’t count the number of times real-time collaboration has saved the day. Imagine being able to share design updates21 instantly with colleagues across the globe and make tweaks together, right then and there. It reduces miscommunications and ensures we’re all on the same page.
Automated Error Detection and Corrections
Automated error detection feels like having an extra set of eyes checking over my shoulder. Advanced CAD systems spot potential issues that even seasoned designers like me might overlook. It’s like having a safety net that catches those small discrepancies before they snowball into major production problems.
By incorporating these capabilities into my workflow, I’ve seen firsthand how they lead to superior quality products and increased manufacturing efficiency. These tools have become indispensable in my quest for precision and excellence in mold design.
Advanced CAD tools can predict mold behavior under stress.True
CAD simulations test scenarios to foresee mold behavior, ensuring design precision.
Real-time collaboration in CAD tools reduces design precision.False
Collaboration minimizes miscommunications, enhancing precision by allowing instant updates.
Conclusion
Mastering multi-cavity mold design involves key factors like material selection, cavity balance, cooling systems, and ejection methods to enhance production efficiency and product quality.
-
Explores why stainless steel is preferred for its durability and resistance to wear and corrosion. ↩
-
Learn which materials ensure smooth surface finishes ideal for electronics. ↩
-
Discover the fundamentals of cavity balance and why it’s critical in ensuring consistent part quality. ↩
-
Learn about the significance of cavity balance in enhancing product consistency and reducing defects. ↩
-
Explore how flow simulation tools assist in predicting and correcting flow imbalances before production. ↩
-
Gain insights from seasoned designers on strategies to maintain cavity balance effectively. ↩
-
Explore the fundamental aspects of injection molding cooling systems and their impact on manufacturing processes. ↩
-
Learn about various strategies to optimize cooling systems for better efficiency in injection molding. ↩
-
Discover how conformal cooling enhances heat removal and reduces cycle time in complex molds. ↩
-
Understand the direct relationship between cooling design and mold efficiency improvements. ↩
-
Learn about various ejection systems, their benefits, and best uses. This knowledge helps you select the right system for your production needs. ↩
-
Understand how a preventive maintenance schedule can maintain optimal mold conditions, extending their lifespan and improving performance. ↩
-
Explore how sensors provide real-time monitoring, which aids in maintaining efficiency and preventing potential ejection issues. ↩
-
Find techniques for customizing ejector designs to enhance efficiency, ensuring better performance tailored to specific production needs. ↩
-
Gain insights into tools that help analyze cycle time reductions, identifying bottlenecks and opportunities to streamline operations. ↩
-
Discover strategies for optimizing runner systems, crucial for ensuring uniform melt distribution and preventing pressure drop issues in multi-cavity molds. ↩
-
Explore the advantages of using advanced CAD tools for simulating and predicting potential mold design issues before they occur. ↩
-
Learn how effective cooling channel design ensures uniform temperature distribution, crucial for managing thermal variations in molds. ↩
-
Understand the importance of mold flow analysis in predicting and adjusting flow rates for optimal material distribution. ↩
-
Explore how CAD simulations help in predicting mold design issues early, saving time and resources. ↩
-
Discover how real-time collaboration in CAD software enhances teamwork and design precision. ↩