Injection molding is more than just a manufacturing process; it’s an art form that can make or break a product.
To combat stress concentration in injection molding, select tough materials, optimize mold designs by avoiding sharp corners, adjust process parameters like temperature and pressure, and employ post-processing techniques like annealing.
But there’s so much more to explore. Let’s dig deeper into each of these strategies and discover practical tips and industry insights that can elevate your injection molding process.
Annealing reduces stress in injection molded parts.True
Annealing involves heating and slow cooling, relieving internal stresses.
How Does Material Selection Influence Stress Concentration?
Material selection plays a critical role in minimizing stress concentration during injection molding by influencing how stress is absorbed and distributed.
Material selection impacts stress concentration by choosing plastics with high toughness and adding modifiers to enhance material resilience, thereby reducing stress-induced defects.
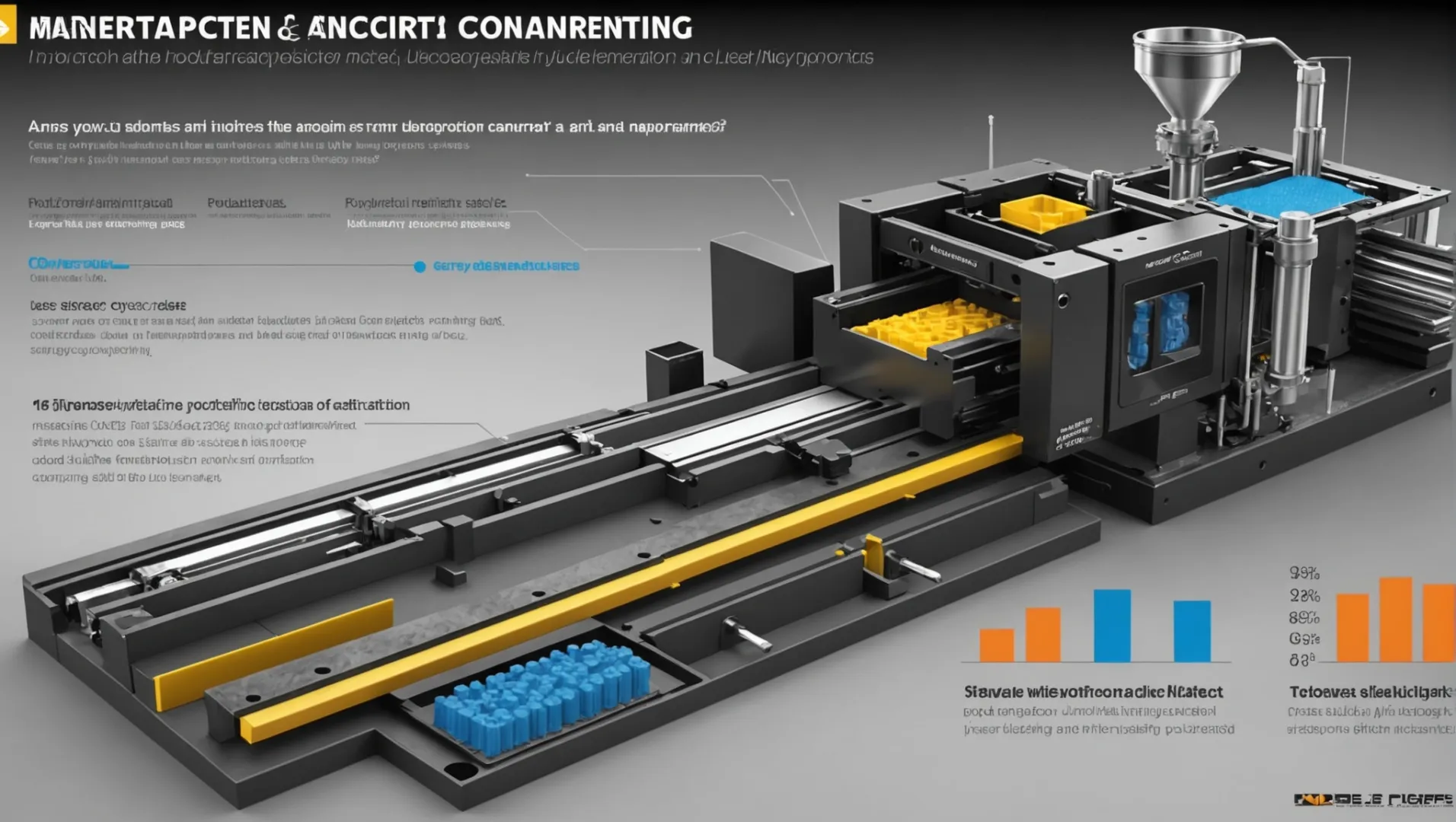
The Role of Toughness and Modulus
Selecting the appropriate plastic material is essential in managing stress concentration during injection molding. Materials with higher toughness and lower modulus are preferred because they can absorb and distribute stress more effectively. For example, engineering plastics like polycarbonate (PC) and polyamide (PA) are excellent choices due to their inherent strength and flexibility. These materials can withstand external forces without forming stress concentration points that may lead to defects such as cracking or deformation.
Enhancing Material Properties with Modifiers
Another strategy involves adding specific modifiers to the plastic composition. Modifiers such as toughening agents or impact agents improve the toughness and impact resistance of the material. By incorporating additives like ethylene propylene rubber into polypropylene (PP), manufacturers can significantly enhance its resilience. This approach reduces the likelihood of stress concentration, thereby improving the overall quality and durability of the molded products.
A Comparison of Material Properties
Material | Toughness | Modulus | Typical Application |
---|---|---|---|
Polycarbonate | High | Low | Automotive components |
Polyamide | Medium | Medium | Electrical enclosures |
Polypropylene | Low | High | Consumer goods |
This table highlights how different materials compare in terms of toughness and modulus, helping in selecting the right material for specific applications.
Practical Considerations in Material Selection
While choosing materials, one must consider factors such as cost, availability, and compatibility with existing manufacturing processes. For instance, while PC and PA offer superior toughness, their cost might be prohibitive for some applications. Therefore, balancing material properties with practical considerations is crucial in optimizing injection molding outcomes.
Understanding these aspects of material selection1 allows manufacturers to make informed decisions that minimize stress concentration and enhance product performance.
Polycarbonate has high toughness and low modulus.True
Polycarbonate is known for its high toughness, allowing it to absorb stress.
Polypropylene is used for automotive components.False
Polycarbonate, not polypropylene, is typically used in automotive components.
What Mold Design Techniques Help Minimize Stress?
Mold design plays a pivotal role in minimizing stress concentration during the injection molding process, enhancing product quality and durability.
Key mold design techniques to minimize stress include strategic gate placement, rounded corner transitions, and balanced cooling systems to ensure even stress distribution across the molded part.
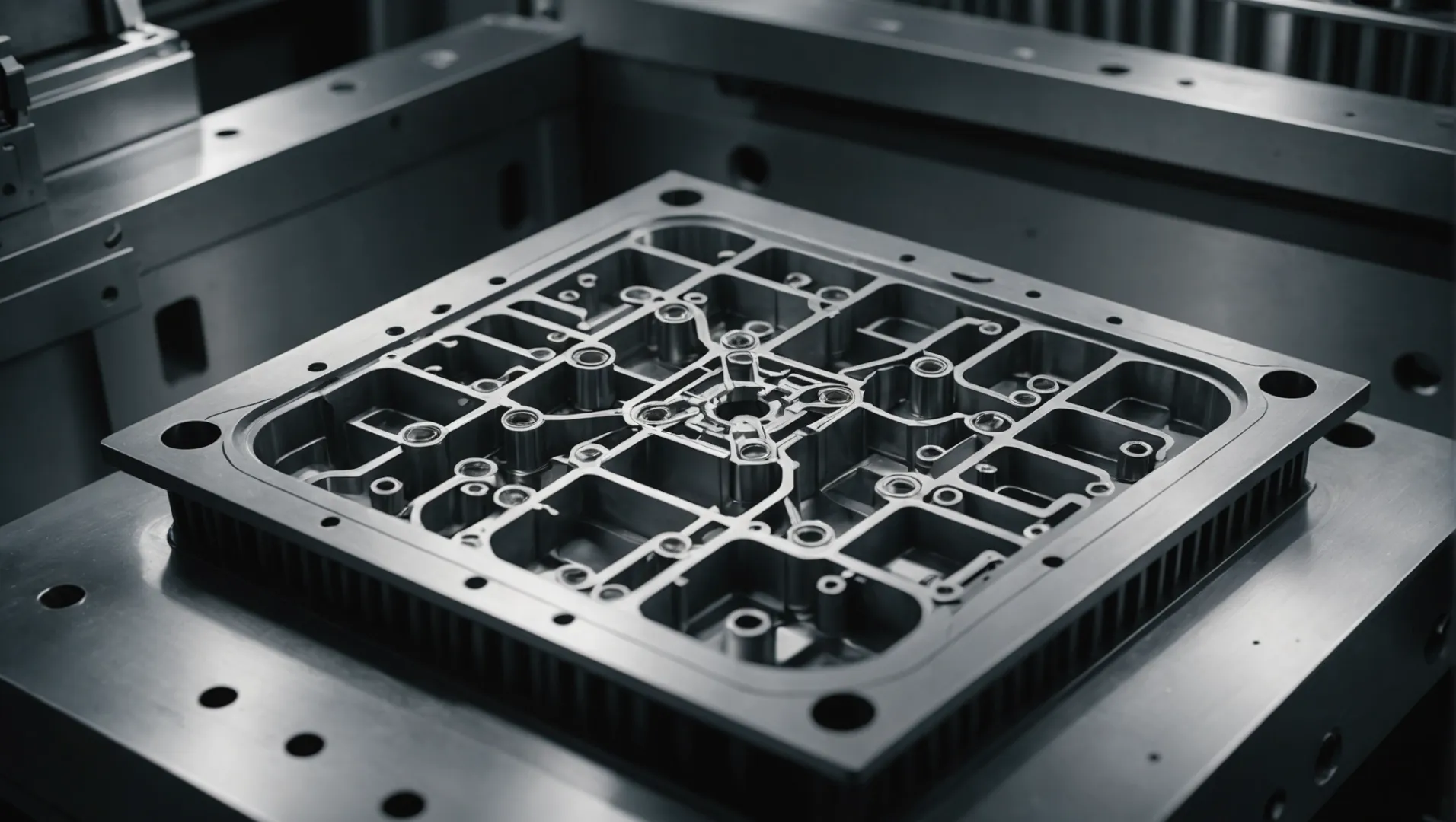
Gate Design: Strategic Placement for Stress Reduction
The gate’s location, shape, and size significantly impact stress distribution during molding. Avoid placing gates near weak or stress-prone areas. Instead, consider designs like multi-point or latent gates to promote uniform melt flow and reduce stress concentration.
- Multi-point Gates: Ensure balanced flow across complex parts.
- Latent Gates: Allow for hidden entry points, minimizing visible stress marks.
Mold Structure Optimization: Avoid Sharp Corners
To reduce stress, incorporate rounded corners and smooth transitions in the mold design. Sharp corners often become focal points for stress, leading to cracks or deformities.
- Use of Rounded Transitions: A larger fillet radius can dramatically lower stress.
- Smooth Curved Surfaces: Enhance the durability of parts by promoting even stress distribution.
Feature | Effect on Stress | Example Use Case |
---|---|---|
Sharp Corners | Increase Stress | Edges of Cubes |
Rounded Corners | Decrease Stress | Bottles |
Cooling System Design: Ensure Uniform Cooling
A well-designed cooling system is crucial in minimizing internal stress. Uneven cooling leads to temperature variations that can induce stress.
- Balanced Cooling Channels: Prevent local overheating or overcooling.
- Consistent Cooling Rates: Ensure uniform temperature drop across the mold.
Proper mold design extends beyond basic functionality, requiring an understanding of material behavior and processing conditions. By exploring advanced mold design techniques2, manufacturers can optimize their processes and produce superior products.
Rounded corners reduce stress concentration in mold designs.True
Rounded corners distribute stress evenly, preventing focal points.
Sharp corners in molds decrease stress on the product.False
Sharp corners increase stress, leading to potential cracks or deformities.
Which Process Parameters Are Key to Controlling Stress?
In injection molding, controlling stress is crucial to prevent defects and ensure product quality. Key process parameters play a significant role in managing stress levels during production.
Key process parameters for controlling stress in injection molding include adjusting injection temperature, pressure, speed, and cooling time to minimize stress concentration and ensure product integrity.
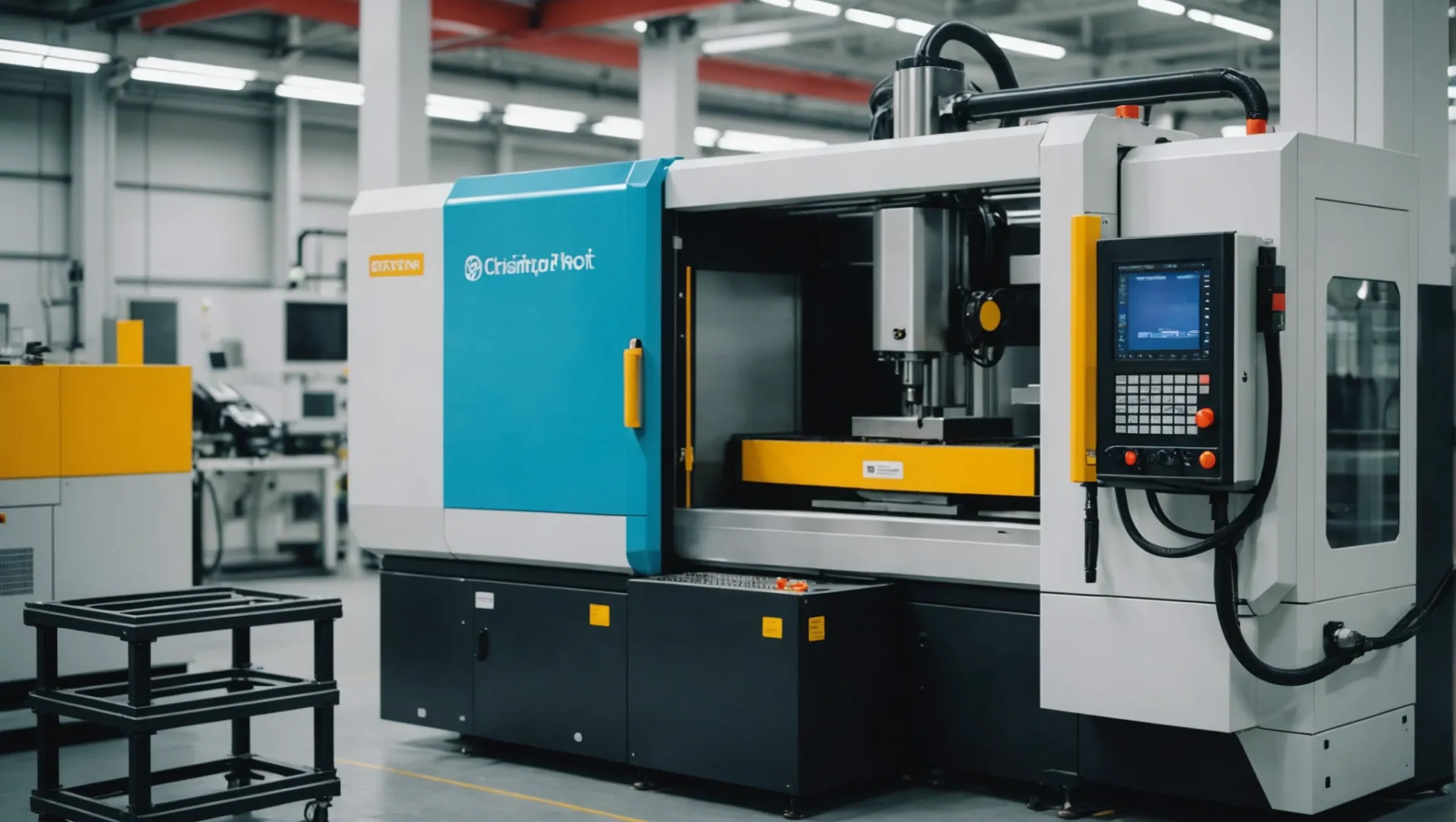
Adjusting Injection Temperature
Controlling the injection temperature is vital to reduce stress concentration during the injection molding process3. By increasing the temperature, the viscosity of the plastic melt decreases, allowing it to flow more smoothly into the mold. This reduced viscosity helps distribute the material evenly, minimizing stress. However, it’s essential to find a balance, as excessively high temperatures might lead to material degradation.
Example:
For polycarbonate (PC), a common material in injection molding, maintaining an injection temperature between 270°C to 310°C can optimize flow while preventing degradation.
Adjusting Injection Pressure and Speed
Lowering the injection pressure and speed can help reduce shear stress within the mold. Shear stress often leads to uneven material distribution and stress concentrations, which can cause defects such as cracking or warping.
Parameter | Low Setting | High Setting |
---|---|---|
Injection Pressure | Reduces shear stress | May cause voids |
Injection Speed | Better material flow | Risk of defects |
Note: While reducing these parameters can alleviate stress, they should be adjusted carefully to avoid issues like incomplete filling or shrinkage.
Extending Holding and Cooling Time
Extending both holding and cooling times can significantly impact stress levels in molded parts. Holding time ensures that the material is compacted well within the mold, reducing internal voids and potential stress points.
- Holding Time: A longer duration allows for better packing of materials, which minimizes internal stresses.
- Cooling Time: Slow cooling helps in uniform temperature distribution throughout the product, reducing thermal stress.
For instance, increasing cooling time by 10-20% can lead to more stable dimensions and decreased residual stresses, enhancing product durability.
Importance of a Balanced Approach
It’s crucial to approach process parameter adjustments with a balanced mindset. Overemphasizing one parameter might lead to detrimental effects on another aspect of the molding process. Therefore, regular monitoring and adjustments4 are essential to achieve the best results.
By carefully calibrating these process parameters, manufacturers can effectively control stress within molded products, ensuring higher quality and performance in their production lines.
Higher injection temperature reduces stress in molding.True
Increasing temperature decreases viscosity, allowing smoother flow and less stress.
Reducing cooling time lowers stress in molded parts.False
Longer cooling times help reduce thermal stress by ensuring uniform temperature distribution.
Why Is Post-Processing Essential for Reducing Stress?
In the realm of injection molding, post-processing stands as a vital step to mitigate stress concentration, ensuring product integrity and durability.
Post-processing techniques like annealing and humidity adjustment are essential in reducing stress by alleviating internal tensions in molded products. These methods fine-tune the final properties of the product, enhancing its dimensional accuracy and mechanical strength.
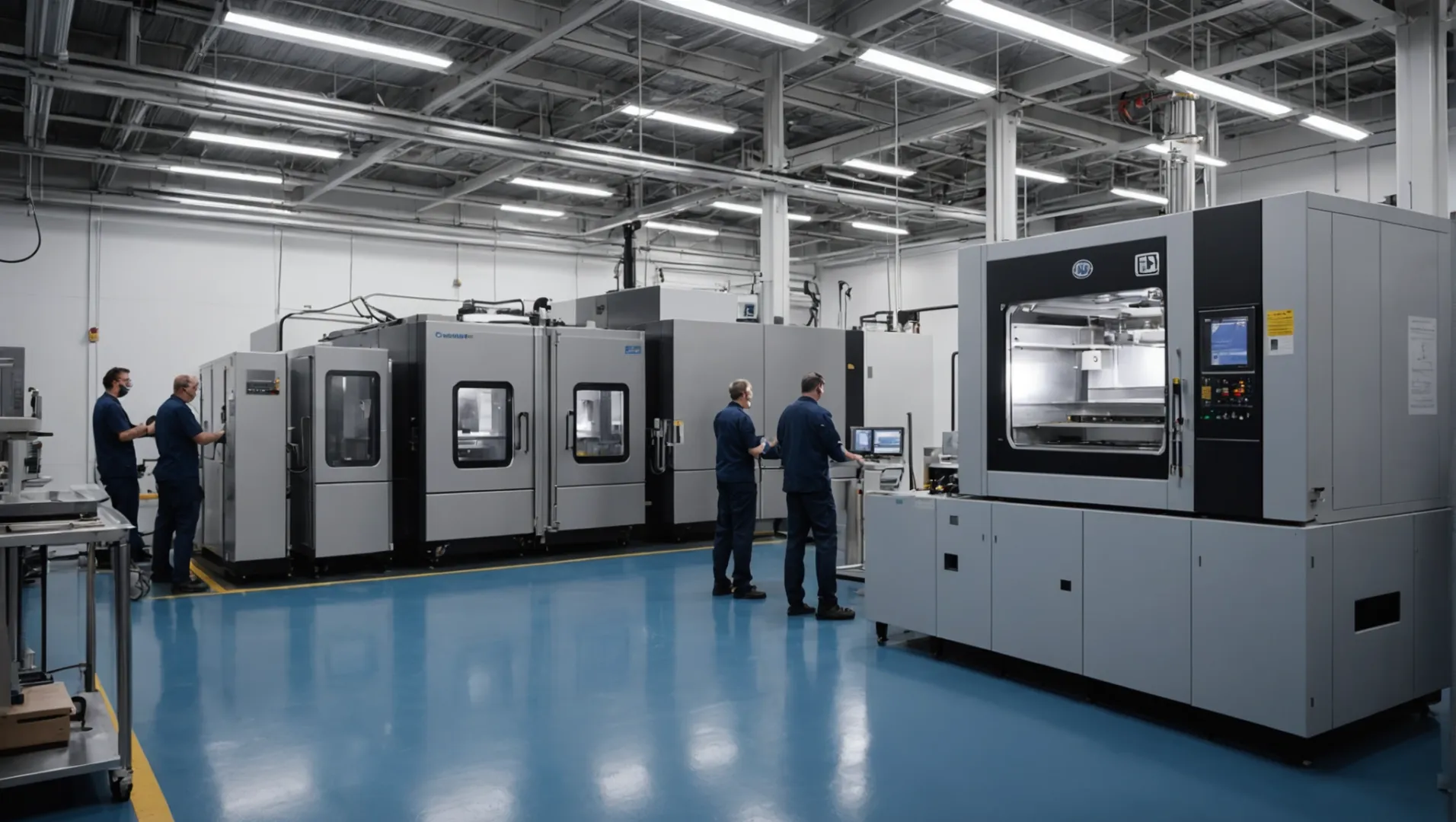
Understanding Post-Processing
Post-processing in injection molding involves additional treatments applied to molded parts to enhance their properties and performance. These treatments aim to address residual stresses that might have developed during the molding process. Stress can result from various factors like uneven cooling, rapid temperature changes, or material properties. By implementing effective post-processing, manufacturers can significantly reduce these stresses and improve product quality.
Annealing: A Core Technique
Annealing is a heat treatment process where the product is heated to a specific temperature and then allowed to cool slowly. This technique is crucial for products requiring high dimensional accuracy and mechanical strength. The annealing process helps in:
- Eliminating Residual Stresses: Heating allows molecules within the plastic to relax and rearrange, reducing internal stress.
- Improving Mechanical Properties: Proper annealing enhances toughness and flexibility.
For instance, a polycarbonate (PC) component might be annealed at a temperature tailored to its specific formulation, ensuring optimal performance. Learn more about annealing processes5.
Humidity Adjustment for Hygroscopic Materials
Certain plastics, like nylon, are hygroscopic, meaning they absorb moisture from the environment. This characteristic can influence stress levels within the material. Humidity adjustment involves controlling the environmental moisture level to:
- Balance Internal Moisture: Ensuring an optimal moisture content reduces stress-induced warping or deformation.
- Enhance Dimensional Stability: Proper humidity levels prevent fluctuations in size or shape due to moisture gain or loss.
By placing nylon components in a controlled humidity environment post-molding, manufacturers can achieve stable dimensions and reduced internal stress. Explore more on humidity control in manufacturing6.
The Role of Post-Processing in Modern Manufacturing
The significance of post-processing in reducing stress cannot be overstated. By fine-tuning conditions such as temperature and humidity, manufacturers can ensure that molded parts meet stringent quality standards while extending their lifespan. The strategic application of these techniques not only minimizes defects but also boosts customer satisfaction by delivering reliable products.
Post-processing is not merely a final touch; it is an integral component of the injection molding process that safeguards against potential stress-related failures. By understanding and implementing these techniques, industries can achieve superior product performance and efficiency.
Annealing reduces internal stress in molded products.True
Annealing relaxes molecules, reducing internal stress and enhancing strength.
Humidity adjustment is unnecessary for hygroscopic materials.False
Controlling humidity balances moisture, preventing stress-induced warping.
Conclusion
By addressing stress concentration through careful material selection, thoughtful mold design, precise process control, and effective post-processing, you can significantly enhance the quality and reliability of your molded products.
-
Explore various materials’ impact on stress concentration in injection molding.: As the temperatures increase or as the desired lifetime of the product increases, the allowable stress level at which the material can be used decreases … ↩
-
Discover innovative strategies for optimizing mold designs to enhance product quality.: Here are design, molding, and fixturing considerations to help you handle this unavoidable issue. ↩
-
Explore specific temperature ranges to optimize polycarbonate molding.: When we visited the molder to work on improving the part appearance, we found the mold temperature set at 75 F (24 C). When asked how I wanted … ↩
-
Learn techniques for effective monitoring and adjustment of parameters.: 1. Temperature Control: · 2. Injection Speed: · 3. Cooling Time: · 4. Plastic Material Selection: · 5. Screw Speed and Back Pressure: · 6. Injection … ↩
-
Discover detailed steps and benefits of annealing in plastic manufacturing.: Well it’s simply a process that involves heating a specific type of plastic below its glass transition temperature in order to ease all the internal pressures … ↩
-
Learn how controlling humidity impacts nylon’s dimensional stability.: The industry needs to catch up with this realization. It can be shown through these types of studies that for an unfilled nylon a moisture … ↩