Ever felt frustrated by fusion marks on injection molded products? Trust me, I have faced that too. Hard work often feels ruined by defects. Really disheartening.
To prevent fusion marks on injection molded products, optimize mold design, adjust molding settings, select suitable materials, and position gates correctly. Identifying the optimal injection speed and using fluid materials also enhance product quality.
My journey in injection molding has shown me that understanding mold design is key to handling fusion marks. Process adjustments and material choices are also vital. These elements matter in reaching that perfect finish. Each part is very important. It helps achieve great results.
Exploring these details is really essential. Sharing insights will probably improve your production quality.
Fusion marks can be completely eliminated in injection molding.False
While techniques can reduce fusion marks, complete elimination is often unrealistic due to various factors in the molding process.
Material selection plays a key role in preventing fusion marks.True
Choosing the right materials is crucial as it influences the flow and cooling rates, thus affecting fusion mark formation.
How Can Mold Design Help Prevent Fusion Marks?
Have you ever thought about how the tiny details of mold design affect product quality? Let’s explore the interesting world of injection molding. Unveil the secrets to stopping those annoying fusion marks.
Mold design helps prevent fusion marks by selecting optimal gate positions, adjusting runner systems, using suitable materials, and fine-tuning process parameters, which enhances the flow and melting of molten plastic.
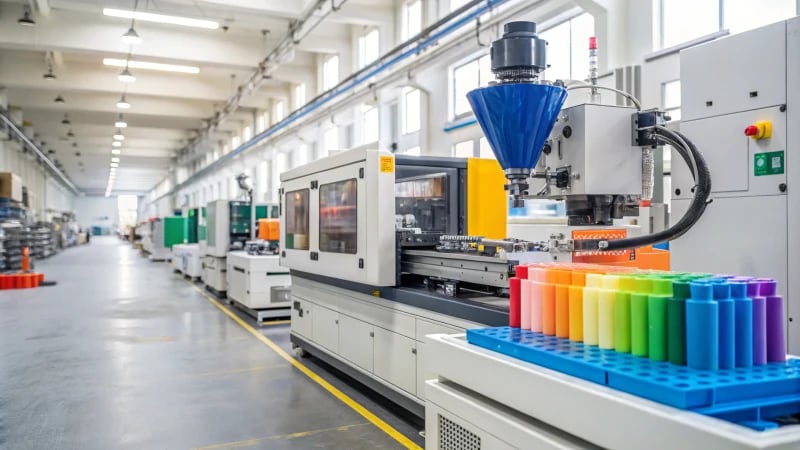
The Importance of Mold Design in Injection Molding
Mold design is crucial in the injection molding process, especially when it comes to minimizing defects like fusion marks. Fusion marks occur when two streams of molten plastic meet but fail to blend properly, leading to visible lines or imperfections on the product surface.
Optimizing Gate Position and Number
One of the first considerations in mold design is the gate position. A well-placed gate helps improve the flow path of the plastic melt, significantly reducing weld marks. For instance, employing a multi-point gate design can be beneficial for complex shapes with multiple thin-walled areas.
Imagine a plastic shell product designed with three gates located strategically at different positions; this setup allows the melt to fill the cavity simultaneously from various directions, thereby minimizing the possibility of weld marks.
Gate Type | Description | Benefits |
---|---|---|
Side Gates | Positioned on the side of the mold, allowing for a more direct flow. | Good for simple shapes. |
Pin-point Gates | Introduces melt in a jet-like shape, enhancing dispersion. | Reduces weld marks effectively. |
Latent Gates | Hidden gates that open during injection, improving aesthetics and functionality. | Reduces visible gating marks. |
Improving the Runner System
The runner system also plays a significant role in preventing fusion marks. A balanced runner system ensures an even flow of the plastic melt, while factors such as size and surface roughness can influence flow dynamics. For instance, using circular runners reduces flow resistance, allowing for smoother melt flow into the cavity.
Furthermore, incorporating diverters or buffers within the runner can help distribute the melt evenly across different branch runners, stabilizing the flow and minimizing turbulence upon entry into the cavity. This step is crucial as turbulence can lead to incomplete melting and increased fusion mark probability.
Adjusting Injection Molding Process Parameters
In addition to mold design, adjusting process parameters is essential in preventing fusion marks. Key adjustments include:
- Injection Speed: Increasing injection speed can enhance melt fluidity, promoting better fusion when streams converge. However, caution is necessary to avoid excessive speeds that may cause ejection problems.
- Injection Pressure: Sufficient pressure ensures complete filling of every cavity corner while preventing issues like flash. Finding an optimal range is vital to maintaining quality.
- Holding Parameters: Extending holding time and increasing pressure during cooling helps ensure that thicker wall areas receive adequate melt replenishment, further reducing weld marks.
Selecting Materials for Optimal Flow
Material selection is another critical factor. Choosing plastics with good fluidity can significantly reduce weld marks. For example:
- High melt flow rate materials like PP (polypropylene) allow for better blending in cavities.
- Adding lubricants can also enhance material fluidity, making it easier for melts to fuse correctly.
Ensuring materials are properly dried before use is equally important. For hygroscopic materials like Nylon (PA), a stringent drying protocol (80-90°C for 4-6 hours) is necessary to prevent defects that could contribute to weld marks.
By focusing on these aspects of mold design and injection molding parameters, manufacturers can significantly improve product quality and reduce defects like fusion marks.
Optimizing gate position minimizes fusion marks in molding.True
Strategically placing gates improves melt flow, reducing the chances of fusion marks appearing on molded products.
Material fluidity has no impact on fusion mark prevention.False
Choosing materials with high fluidity is essential as they blend better, significantly reducing the occurrence of fusion marks.
How Can I Optimize the Injection Molding Process Parameters?
Do you want to improve your injection molding skills? Start a journey with me to find out how to adjust your process for better efficiency and high-quality products. Let’s explore the details of mold design, setting changes and picking the right materials together!
Optimize injection molding by adjusting mold design, gate position, runner systems, injection speed, pressure, and mold temperature. Use materials with good fluidity to enhance product quality and reduce defects like weld marks.
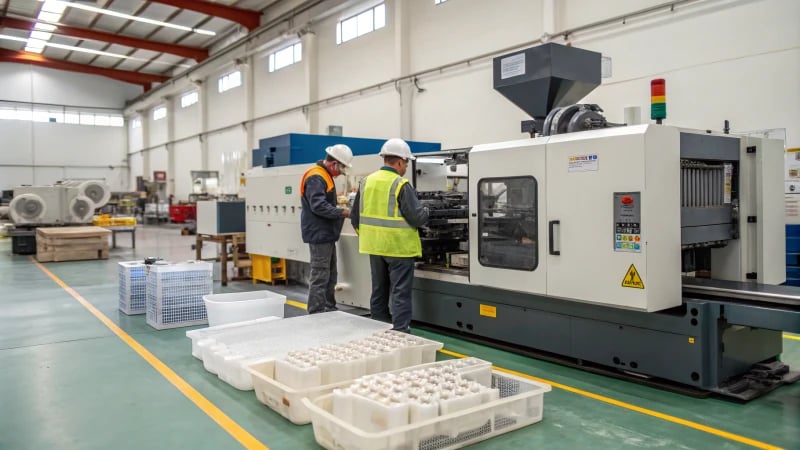
Understanding Mold Design
Optimizing the injection molding process begins with effective mold design. Key elements include:
- Gate Position and Number: The placement of gates impacts the flow of plastic melt. For complex shapes, consider a multi-point gate design to improve melt filling.
For instance, in a plastic shell, using three gates can help distribute the melt evenly, minimizing weld marks.
- Runner System: A balanced runner system ensures even flow. A circular runner is often preferred due to lower flow resistance. Polishing the runner surface reduces friction, allowing smoother melt flow.
Adjusting Injection Molding Parameters
Next, focus on adjusting injection molding process parameters. Consider these adjustments:
- Injection Speed and Pressure: Increasing injection speed maintains higher melt temperatures, which enhances fusion and reduces weld marks. However, excessive speed may lead to defects like ejection.
Parameter | Effect on Process |
---|---|
Increased Injection Speed | Higher melt fluidity |
Optimal Injection Pressure | Full cavity filling |
- Holding Parameters: Extending holding time and increasing pressure aids in better melt merging during cooling. For uneven wall thickness products, adjust holding times accordingly.
Material Selection and Processing
Choosing the right materials significantly influences outcomes. Key considerations include:
-
Fluidity of Materials: Select materials with high melt flow rates to enhance cavity fill and reduce weld marks. For example, PP (polypropylene) with a high MFR can improve performance.
-
Material Drying: Ensure materials are adequately dried to prevent defects during injection. For moisture-sensitive materials like nylon (PA), drying at 80-90℃ for 4-6 hours is essential to avoid quality issues.
Control of Mold Temperature
Finally, control the mold temperature effectively.
- Maintaining an appropriate mold temperature enhances melt fluidity and reduces the chance of solidification that can lead to weld marks. For high-viscosity materials like PC (polycarbonate), a higher mold temperature facilitates better blending of the melt.
In conclusion, optimizing injection molding involves a multifaceted approach focusing on mold design, process parameters, material selection, and temperature control. By examining each aspect thoroughly, manufacturers can enhance product quality and efficiency.
Multi-point gate designs improve melt filling in injection molding.True
Using multiple gates in mold design enhances the distribution of plastic melt, minimizing weld marks and ensuring better filling of complex shapes.
Higher mold temperatures reduce weld marks in injection molded products.True
Maintaining appropriate mold temperatures increases melt fluidity, reducing solidification risks that can lead to defects like weld marks during the injection process.
What Materials Should You Choose to Minimize Fusion Marks?
Material choice in laser cutting or engraving is crucial. Different materials affect the final product significantly. I discovered this in many projects. Each taught me about selecting the right material. This decision really influences the outcome. Let’s explore this together!
To minimize fusion marks in laser machining, choose materials with high fluidity, thoroughly dry them, and use additives to enhance flow properties for cleaner finishes and improved overall quality.
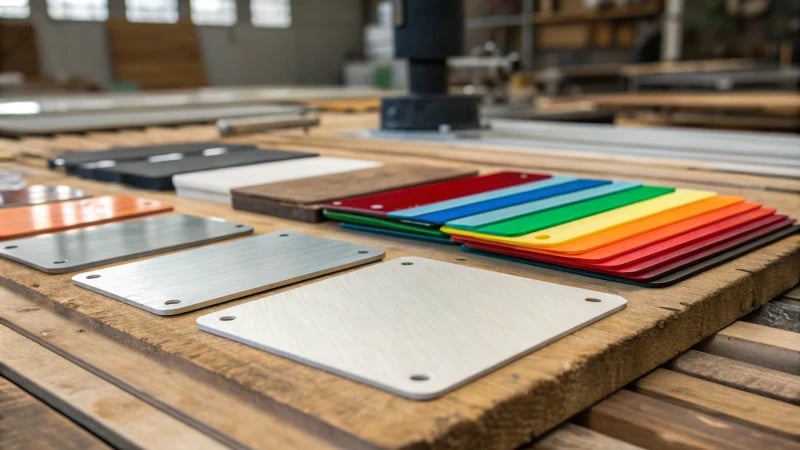
Understanding Fusion Marks
Fusion marks are tiny imperfections from laser cutting or engraving. They often arise from the interaction between a material’s properties and laser settings. Selecting the right materials is my secret technique to minimize these marks, leading to a cleaner finish.
Material Properties Impacting Fusion Marks
- Fluidity of Materials
Materials with good fluidity create a smoother melt during processing.
Here’s a table showcasing some common materials and their flow characteristics:
Material | Melt Flow Rate (MFR) | Comments |
---|---|---|
Polypropylene (PP) | High | Excellent for intricate designs |
Polycarbonate (PC) | Moderate | Good impact resistance |
Nylon (PA) | Low | Requires thorough drying |
For example, I once used high fluidity grade PP for a detailed project, which greatly reduced weld marks due to its superior flow properties.
-
Moisture Content
Moisture can really ruin materials like Nylon, leading to unwanted bubbles and imperfections.
Ensure thorough drying before use:- Drying temperature: 80-90°C
- Duration: 4-6 hours
This step is essential for preserving material integrity and reducing fusion marks.
-
Additives Improving Fluidity
I sometimes test with lubricants or additives that improve flow.
These can be very effective, especially for complex designs or when using materials that are hard to handle.
Selecting the Right Material for Your Project
When selecting materials, consider important factors:
- Application requirements: If appearance matters, I choose materials with high MFR.
- Environmental factors: Temperature and humidity affect performance; I always take them into account.
For more information on material selection, see this resource on material properties1.
Conclusion on Material Selection
Finally, I have learned that choosing the right materials and understanding them reduces fusion marks. Optimizing choices based on fluidity, moisture content, and additives is key to achieving better results in laser cutting and engraving.
High fluidity materials reduce fusion marks in laser cutting.True
Materials like polypropylene with high fluidity allow for better melt fusion, minimizing imperfections during laser processing.
Moisture in nylon increases the risk of fusion marks.True
Excess moisture in nylon can lead to bubbles and imperfections, worsening fusion marks during laser cutting or engraving.
What Are Common Causes of Fusion Marks in Injection Molding?
Have you ever seen those annoying fusion marks on your injection-molded products? I have too. Understanding why they happen really helps us improve. Let’s explore the main reasons for these defects!
Fusion marks in injection molding are commonly caused by poor mold design, inappropriate process settings, or unsuitable material choices, with key factors including gate positioning, injection speed, and material moisture. Understanding these factors enhances product quality.
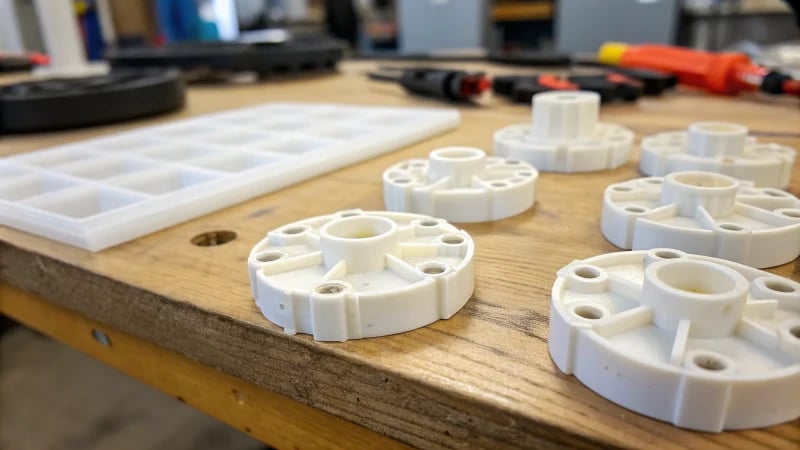
Mold Design
Mold design is a crucial factor in preventing fusion marks during injection molding. Optimizing the gate position and number can significantly influence the flow path of the plastic melt, minimizing weld marks.
For instance, employing a multi-point gate design in complex products can ensure a more uniform filling of the mold cavity. In a plastic shell product, setting three gates at different locations allows the melt to converge from various directions, effectively reducing the likelihood of weld marks.
Moreover, the type of gate plays a pivotal role. Pin-point gates, for example, enable the melt to enter the cavity in a jet-like fashion, promoting better dispersion and fusion of the melt, crucial for products with high aesthetic demands. My team really liked the quality improvement after that change.
Injection Molding Process Parameter Adjustment
Adjusting process parameters such as injection speed and pressure is vital in minimizing fusion marks. Increasing injection speed enhances the melt’s temperature and fluidity within the cavity, which aids in its convergence and fusion. However, caution must be taken not to set speeds too high to avoid quality issues like ejection—a lesson I learned well.
An example of this adjustment can be seen when injecting ribbed plastic products; increasing speed in the confluence area allows for quicker merging of melts. Additionally, optimizing holding parameters by extending holding time and increasing holding pressure can significantly reduce weld marks by ensuring better melting during cooling.
Material Selection and Processing
Choosing the right materials is essential to prevent fusion marks. Selecting plastics with high melt flow rates (MFR), such as high-fluidity grade polypropylene (PP), enhances the fluidity and blend of the melt within the cavity, thus reducing weld marks.
Furthermore, ensuring that materials are properly dried before injection molding is critical. Moisture in materials can lead to defects during processing and adversely affect melt fusion; making it crucial for moisture-sensitive materials like nylon (PA) to undergo thorough drying processes.
Factor | Description | Example |
---|---|---|
Mold Design | Optimize gate positions and types to enhance flow paths | Multi-point gates on complex shapes |
Injection Parameters | Adjust speed and pressure for optimal melt flow | Increased speed for rib confluence |
Material Selection | Use materials with good fluidity and ensure proper drying | High MFR PP; drying nylon at 80-90°C |
Each of these aspects plays a significant role in minimizing fusion marks in injection molded products, contributing to overall quality and appearance.
Optimizing gate design reduces fusion marks in molds.True
Proper gate positioning and design enhance melt flow, minimizing weld marks during injection molding.
High moisture content in materials causes fusion marks.True
Excess moisture can lead to defects in the melt, affecting fusion and resulting in visible marks on the product.
Conclusion
Learn how to minimize fusion marks in injection molded products through optimized mold design, precise process parameters, and careful material selection.
-
Discover detailed guidance on choosing materials to minimize fusion marks for your projects. ↩