Have you ever questioned why a small detail such as the primary channel’s length in injection molding is so important?
The length of the main channel in injection molding directly affects the pressure needed during the process. Longer channels demand higher pressure to overcome thick resistance. This pressure is crucial. The mold fills properly with enough pressure. Both machine performance and product quality depend on this.
At the beginning of my work in injection molding, I did not realize how the main channel’s length could really affect everything. A project came along with a longer channel and my usual settings stopped working. The longer length needed higher pressure to push past more resistance. This experience showed me that even small changes can greatly impact production efficiency. Realizing these details helps mold designers like us choose wisely, which probably prevents expensive errors and really improves product quality.
Longer main channels increase injection pressure.True
Longer channels require more pressure to overcome viscous resistance.
Shorter channels reduce mold filling efficiency.False
Shorter channels generally improve efficiency by reducing resistance.
How Does Pressure Loss Affect Injection Molding?
I’m in the workshop, looking at an injection molding machine, thinking about how to let things flow smoother. Everything comes down to knowing pressure loss. Understanding pressure loss is key.
The pressure loss principle in injection molding focuses on the pressure drop that happens as flowing molten plastic moves through mold channels. This material encounters resistance because of its thickness and the length of the channels.
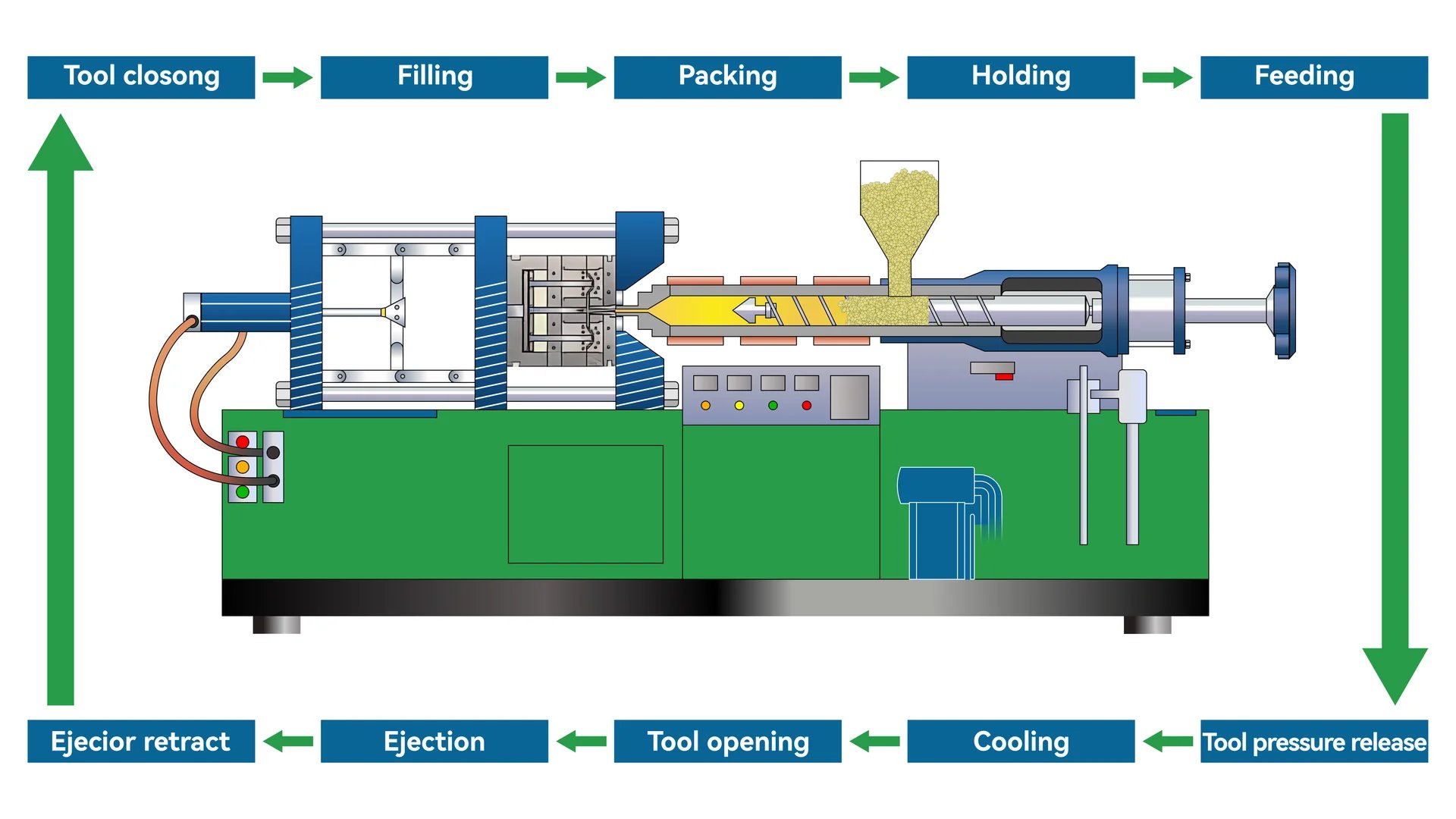
Understanding Pressure Loss in Injection Molding
When I began learning about injection molding, the term pressure loss1 seemed like just another technical word. But as I learned more, it became clear that it is crucial to the process. Picture the plastic melt as a stream pushing through the main channel of a mold. It fights viscous resistance, similar to running down a windy hall. Longer halls create more drag, just like our plastic stream.
Factor | Description |
---|---|
Channel Length | Longer channels increase friction, causing more pressure loss. |
Material Viscosity | Higher viscosity leads to increased resistance and pressure drop. |
Using Fluid Dynamics
For understanding this flow, I use models like the Newtonian fluid model2. For circular pipes, the Hagen-Poiseuille law guides me. It shows how pressure loss changes with pipe length. It’s similar to predicting how wind moves a kite depending on string length.
Effects on Injection Molding
Higher Injection Pressure Needed: I think about a project with thin-walled products. The channel was too lengthy, requiring more injection pressure to fill it correctly. It’s similar to inflating a balloon with a small hole – more force is needed!
Demand for Better Machine Performance: Sometimes, longer channels push our machines out of their comfort zone. Adjusting speed and pressure is like tuning a guitar – difficult but necessary for the right note.
Effects of Uneven Pressure
A difficult part is handling uneven pressure distribution. It’s like frosting a cake evenly – too much frosting on one side ruins the whole dessert! This may cause quality issues3 such as warping or size differences, which are bad for product consistency.
Practical Tips
Designing molds with shorter channels or changing material thickness helps a lot. Simulations are my key tool; they act like practice before the actual production run. This preparation helps save time and resources, keeping the process smooth.
By learning these ideas, I have made my injection molding processes easier, achieving precision and smoothness. Using these methods reduces waste and really increases overall production efficiency.
If you’re interested in fluid dynamics in injection molding, maybe look at this resource4.
Longer channels increase pressure loss in injection molding.True
Longer channels cause more friction, increasing pressure loss.
Higher viscosity decreases pressure loss in injection molding.False
Higher viscosity increases resistance, leading to more pressure loss.
How does main channel length influence injection pressure?
Have you ever thought about the impact of the main channel’s length in injection molding on your design? It could be the secret champion or the hidden troublemaker.
The main channel’s length in injection molding influences injection pressure. Long channels increase resistance. Viscous friction rises. More pressure fills the mold properly. High pressure is necessary.
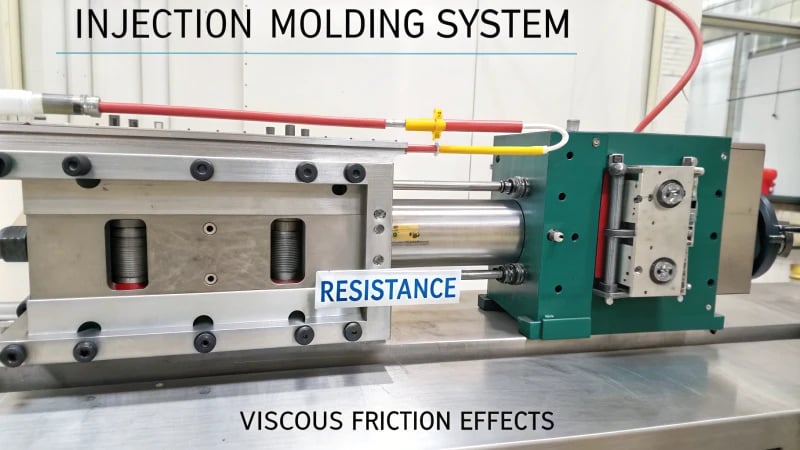
The Role of Pressure Loss Principle
In my early days designing molds, I first met the idea of pressure loss. It felt like discovering a hidden guide explaining why some designs failed. Think of the plastic molten material as a marathon runner. As it travels down the main path, every inch adds more resistance due to thick friction. It’s similar to the runner battling strong winds. Longer paths add more friction, causing notable pressure loss.
We often use the Hagen-Poiseuille law for round pipes or similar formulas for different shapes to predict this loss. These calculations remind me of planning a road trip; every mile brings more things to think about. Understanding this is vital for choosing main path sizes, making sure our designs succeed beyond just looking good on paper.
Impact on Injection Pressure Requirements
In one project with thin gadgets, I saw how a longer main path raised the pressure needs. The extra length called for more force to push plastic smoothly into every corner of the mold. It felt like inflating a huge balloon carefully – not easy but key for the perfect shape.
The main channel’s length directly affects the demand for injection pressure. As the length increases, so does the pressure required to ensure smooth mold filling, especially crucial when dealing with thin-walled plastic products where melt fluidity5 is paramount.
Implications for Injection Molding Machines
Once, we tested our machines with a very long path design. I clearly recall the tense moment while adjusting settings, hoping we wouldn’t need stronger machines. These tweaks, like speeding up and increasing force, felt like giving machines extra energy drinks. However, this came with risks of faster wear or lower product quality.
Parameter | Impact of Increased Channel Length |
---|---|
Injection Pressure | Higher demand to overcome increased resistance |
Machine Performance | Requires machines with greater pressure output |
Pressure Distribution | Leads to uneven distribution within the mold |
Longer main channels may exceed standard pressure capacities of molding machines, necessitating machines with higher ratings or specific adjustments in injection parameters.
Uneven Pressure Distribution Concerns
A long main path often causes uneven pressure, threatening product consistency. I remember facing warping problems from pressure differences along the path. It was like baking a cake in a bad oven: possible to get burnt edges and raw center.
An extended main channel also results in varied pressure distribution inside the mold. The differential between the melt’s front and rear ends grows, causing potential quality issues like warping or dimensional deviations that affect stability of the injection process6.
These stories taught me that every design choice, like path length, needs careful thought. Balancing these factors means our products not only hit quality targets but really outshine in performance and durability.
Longer channels increase injection pressure requirements.True
Longer channels cause higher friction, demanding more pressure for mold filling.
Shorter channels lead to uneven pressure distribution.False
Uneven pressure is more likely in longer channels due to increased resistance.
How does injection molding machine performance get impacted?
Curious about what happens inside an injection molding machine? The process resembles assembling a complex puzzle that probably results in flawless manufacturing.
Injection molding machines rely on factors such as pressure loss, injection pressure demand, machine capacity and pressure distribution. Mastering these factors increases molding efficiency. It really improves product quality.
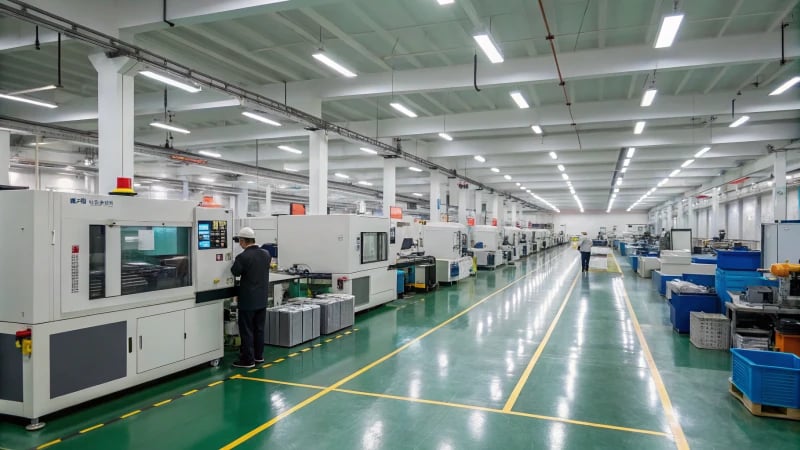
Pressure Loss Principle
Once, I stood by a huge machine, watching plastic melt flow like syrup on a spoon. I found the pressure loss principle fascinating. As plastic moves through the main channel, it meets thick resistance, much like when we walk through water. Longer journeys mean more pressure disappears, like plastic getting tired from a long walk! The Hagen-Poiseuille law7 helps predict this loss.
Factor | Impact on Pressure Loss |
---|---|
Length | Increases with longer channels |
Diameter | Decreases with larger diameters |
Viscosity | Higher viscosity leads to higher loss |
Specific Impact Analysis
Rising Injection Pressure Need
During a thin-walled plastic project, details were crucial. Longer main channels required higher injection pressure to fill the mold swiftly and evenly. It felt like running against the wind; without pressure, the product might not fill correctly. This could cause big issues.
Higher Requirements for Machine Capability
Long channels often push machines beyond normal limits. Selecting a machine with a higher pressure rating was challenging, much like picking the right car for a long trip. We adjusted injection speed and pressure, trying to balance quality with the potential wear on molds.
Adjustment | Potential Impact on Product |
---|---|
Increase Speed | May cause defects |
Increase Pressure | Risk of damaging molds |
Uneven Pressure Spread
The main channel’s length can disrupt pressure spread in the mold, like an uneven garden hose splashing water unpredictably. I’ve seen this cause warping or shape differences, creating products slightly off from their original design. These minor flaws can be really frustrating, especially when accuracy is very important.
- Warping: Distortion in shape due to uneven cooling.
- Dimensional deviation: Variations in size from intended dimensions.
Understanding these factors is truly like having a guide, leading to the best injection molding processes8 for high-quality production and effective machine use.
Longer channels increase pressure loss in molding machines.True
According to fluid mechanics, longer channels lead to higher pressure loss.
Higher viscosity decreases pressure loss in molding machines.False
Higher viscosity actually increases pressure loss, not decreases it.
How Can Designers Optimize Main Channel Length for Better Results?
Have you ever thought about how changing the main channel length might completely change your design results?
Designers improve main channel length by understanding how pressure loss works. Managing injection pressure properly is important. Uniform pressure distribution matters as well. These factors are vital for creating efficient molds. They help in producing high-quality results.
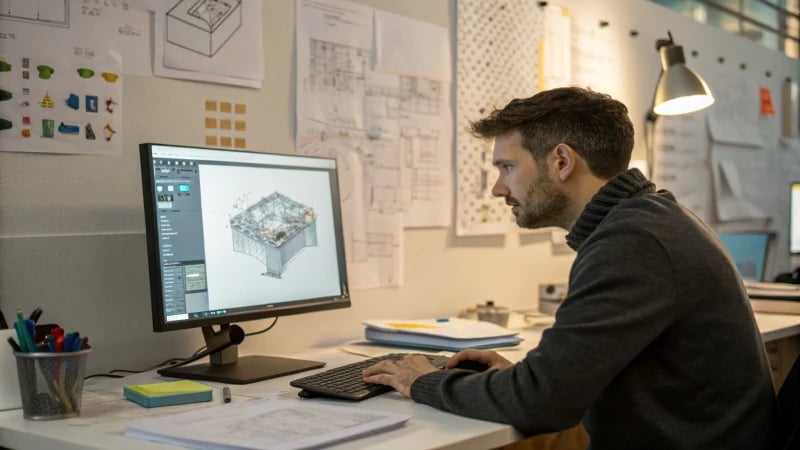
Understanding Pressure Loss Principles
When I first began in design, I did not realize how a small change like adjusting the main channel length could greatly affect the final product. Think about making a piece for a detailed mold. The length of that main channel is more than just a technical part; it changes everything. It’s similar to finding the right beat in a song – get it wrong and the whole thing feels off.
The length of a main channel directly affects pressure loss due to viscous resistance—it’s like pushing syrup through a straw. According to fluid mechanics9, this loss grows with the length of the channel, beautifully explained by the Hagen-Poiseuille law for circular pipes, and similar formulas apply to non-circular pipes. Picture it: each extra millimeter adds friction, taking energy from the flow.
Impact of Increased Injection Pressure Demand
Longer channels necessitate higher injection pressures to overcome resistance and fill molds efficiently. If you’ve worked on thin-walled products with high fluidity requirements, you’ll understand these demand precise pressure management to avoid problems like poor filling—it’s like squeezing toothpaste through an extra-long tube.
Parameter | Effect of Long Channel | Optimization Strategy |
---|---|---|
Pressure | Increased | Use machines with higher pressure ratings |
Flow | Potential blockages | Adjust injection speed |
Improving Injection Molding Machine Performance
I once had to decide between upgrading our machines or adjusting settings to handle a longer channel. Long channels may require machines exceeding normal pressure outputs. Designers must choose machines with higher ratings or adjust parameters like injection speed. However, these changes can impact product quality and mold longevity.
- Adjustment Effects:
Ensuring Even Pressure Distribution
Keeping pressure even across molds with long channels is very important. Uneven pressure might result in warping or shape issues—like baking an uneven cake because the heat wasn’t spread out properly. Uneven pressure across molds from long channels can lead to quality issues such as warping or dimensional deviations.
Key Considerations:
- Pressure differences increase with length, requiring careful monitoring.
- Effective design includes simulations to predict and mitigate uneven distributions using advanced CAD tools11 which aid designers in visualizing and optimizing these elements effectively.
Using these techniques has been critical in maintaining product stability12 and quality of our products. Every project should run as smoothly as possible—it’s not just about finishing the work; it’s about truly mastering the art of design.
Longer channels increase pressure loss.True
Longer channels lead to more viscous resistance, increasing pressure loss.
Higher injection speed reduces cycle time without any drawbacks.False
While it reduces cycle time, it may stress molds and affect quality.
Conclusion
The main channel length in injection molding significantly impacts injection pressure, affecting machine performance and product quality due to increased resistance and uneven pressure distribution.
-
Click to explore detailed explanations of pressure loss mechanisms in injection molding. ↩
-
Learn about how Newtonian fluid models apply to plastic melt flow in molds. ↩
-
Discover how uneven pressure affects product quality in injection molding. ↩
-
Gain insights into fluid dynamics models applicable to injection molding processes. ↩
-
Learn why melt fluidity is critical in thin-walled products, influencing design choices. ↩
-
Explore how uneven pressure impacts product quality and process stability. ↩
-
This link delves into fluid mechanics principles affecting pressure loss, essential for understanding injection molding. ↩
-
Discover strategies for optimizing the injection molding process for improved efficiency and product quality. ↩
-
Explore fluid mechanics to understand how it influences channel length optimization. ↩
-
Learn methods to avoid warping, a common issue with uneven pressure distribution. ↩
-
Discover top CAD tools that assist in mold design and optimization. ↩
-
Find strategies to enhance product stability despite pressure variations. ↩