Did you ever work hard on a design, just to see it twist in unexpected ways?
Addressing warping problems in injection molded items requires uniform wall thickness. The design of ribs should be strategic. Simplified shapes help. Symmetrical layouts also play a role. These methods balance shrinking forces. A smooth cooling process reduces warping. Warping is minimized.
I remember my first struggle with shape problems – it was very annoying. Then I found that knowing design details was really important. Keeping wall thickness the same helps with cooling. Think of a smooth plastic gadget꞉ thicker sides than the bottom mean it cools unevenly and bends.
Carefully planning ribs really matters. Imagine a plastic bracket; ribs that are too thick or badly placed cause bending. Control size and position. Align with natural shrinkage direction to protect the product.
Simplicity helps a lot. Complex shapes may look nice but make cooling hard. Simple designs or using symmetry, like a balanced cross-section for a beam, keep shrinkage even. This lowers the risk of problems.
These tactics changed how I do injection molding. Now my designs stay strong. Following these ideas might be what you need for your next project.
Uniform wall thickness reduces warpage in molded parts.True
Uniform wall thickness helps balance shrinkage forces, reducing warpage.
Asymmetrical designs prevent warpage in injection molding.False
Symmetrical designs are recommended to reduce warpage risks.
How Does Wall Thickness Influence Warpage?
Some plastic parts remain flawless, while others twist out of shape. They sometimes warp so badly you can’t tell what they were supposed to be.
Wall thickness is important for cutting down warpage. It affects how evenly a plastic part cools. Thickness also influences stress distribution. Even wall thickness reduces shrinkage differences. Shrinkage differences cause warpage. Design needs smooth changes. Gradual transitions decrease stress points.
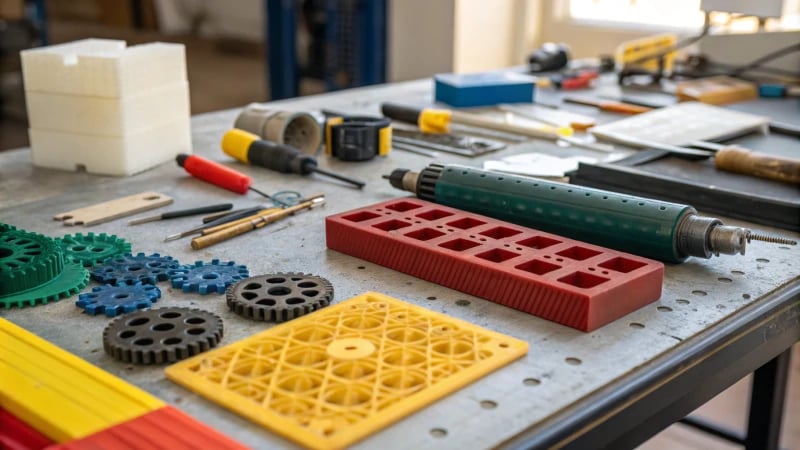
Importance of Uniform Wall Thickness
When I began learning about mold design, I felt confused. Small changes in a part’s wall thickness could ruin its strength. It was like folding paper as a child – doing it right created something beautiful, doing it wrong left a mess.
Maintaining a uniform wall thickness in injection-molded parts is crucial for reducing warpage. Uneven thicknesses cause differential cooling rates, leading to internal stresses and deformation. For instance, picture a rectangular plastic box1 that twists because its walls are not even. Perfect uniformity might not always happen, but smooth changes from thick to thin walls help avoid abrupt changes.
Design Optimization for Wall Thickness
Reducing warping involves careful thinking. In design, I focus on wall thickness transitions. If changes are needed, gradual shifts lower stress. It’s like slowly stepping into cold water instead of jumping.
To minimize warpage, designers should ensure that areas with necessary variations have gradual transitions. For example, if a wall transitions from thick to thin, the change should be gradual to reduce stress concentrations. Additionally, consider using a symmetrical design approach2 to balance the forces during cooling.
Ribs and Reinforcements
Placing ribs carefully increases strength without thick walls. It requires precision.
The strategic placement of ribs can enhance part strength without increasing wall thickness excessively. Ribs should be thinner than the main wall to prevent uneven shrinkage and should not exceed 0.6-0.8 times the primary wall thickness to avoid warping due to uneven shrinkage.
Wall Thickness | Rib Thickness | Warpage Potential |
---|---|---|
Uniform | 0.6x | Low |
Uneven | >0.8x | High |
Even spacing is necessary to avoid local shrinking issues; once, I worked on a plastic bracket product3 where uneven rib placement caused surprises.
Product Shape Considerations
Complex shapes affect plastic flow and cooling, risking warping.
Simplifying shapes or adjusting the mold design can help mitigate these effects by considering gate design and mold structure. Symmetrical designs balance shrinkage forces and greatly help reduce warping in complex parts.
Using these ideas in design and manufacturing has shown me that small changes can really improve quality and reliability—details matter a lot.
Uniform wall thickness reduces warpage in molded parts.True
Uniform thickness ensures even cooling, minimizing internal stresses.
Ribs should exceed 0.8 times wall thickness to prevent warping.False
Ribs exceeding 0.8 times the wall thickness increase warpage risk.
How does rib design impact warpage in injection molding?
I recall the first moment I understood how a small change in design could succeed or fail a project entirely.
Rib design affects bending in injection molding by controlling how much the material shrinks. Proper size, spread and direction of ribs distribute shrinkage forces evenly. This reduces bending. Rib thickness should stay between 0.6-0.8 times the wall thickness to really limit warpage. Very crucial to note.
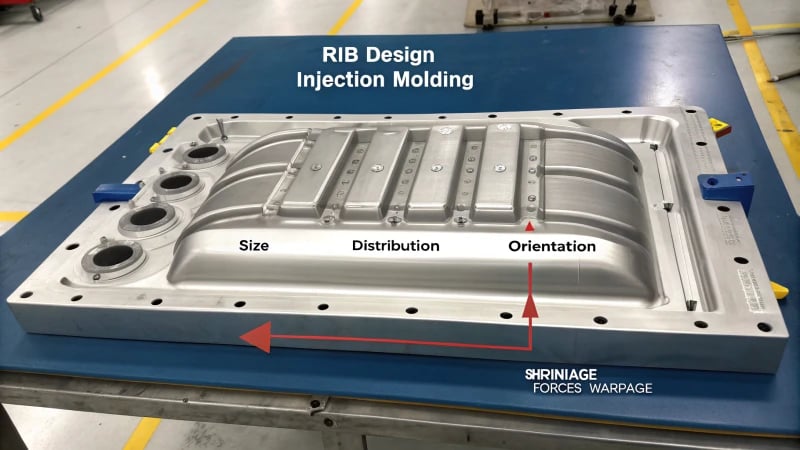
The Role of Rib Design in Injection Molding
I remember a project where rib design changed everything. Ribs in injection molding do more than strengthen parts. They act like hidden champions, keeping things strong without using too much material4. However, improper rib design can lead to warpage, a common defect where the part distorts after cooling.
Importance of Rib Thickness and Distribution
During a plastic bracket redesign, I learned the importance of rib thickness and spacing. Ribs should be 0.6-0.8 times the wall thickness. This concept was crucial for me as it helps prevent differential shrinkage, which causes warping.
Rib Thickness | Wall Thickness | Ratio |
---|---|---|
2mm | 2.5mm | 0.8 |
1.5mm | 2mm | 0.75 |
1.8mm | 3mm | 0.6 |
Thick ribs led to more shrinkage than nearby areas, creating distortion. Evenly spacing ribs is very important; too many in one spot results in uneven shrinkage—a problem I try to avoid by spreading them evenly.
Considering Shrinkage Direction
Understanding shrinkage direction is like reading a part’s cooling map. In round parts, radial ribs spread shrinkage forces equally across all directions, minimizing potential warpage by balancing forces that occur during cooling.
Simplification and Symmetrical Design Principles
I like keeping designs simple, especially with product shapes because complex shapes complicate flow and cooling during injection molding, making them prone to warping issues. A past project showed me the strength of symmetrical designs; they balance shrinkage well, cutting down warping risk.
For example, designing a plastic beam with a symmetrical cross-section kept its integrity during cooling by allowing even shrinkage forces.
Using these rib design ideas not only prevents defects but also enhances the overall efficiency of the manufacturing process5. By optimizing rib design, manufacturers can achieve high-quality parts with minimal defects, ensuring better product performance and longevity.
Rib thickness should be 0.6-0.8 times wall thickness.True
This ratio helps prevent differential shrinkage, reducing warpage.
Complex rib designs reduce warpage in injection molding.False
Complex designs complicate flow and cooling, increasing warpage risk.
Why is shape simplification important for minimizing warpage?
Picture an artist sculpting a masterpiece, yet the clay refuses to maintain its form. That’s the experience of warpage in injection molding. Simplifying the shape truly helps here.
Shape simplification plays a vital role in reducing warpage during injection molding. It helps achieve even cooling and shrinkage. The process lowers the complexity of flow paths. Stress points decrease significantly. Shrinkage forces achieve balance. More stable products emerge as a result.
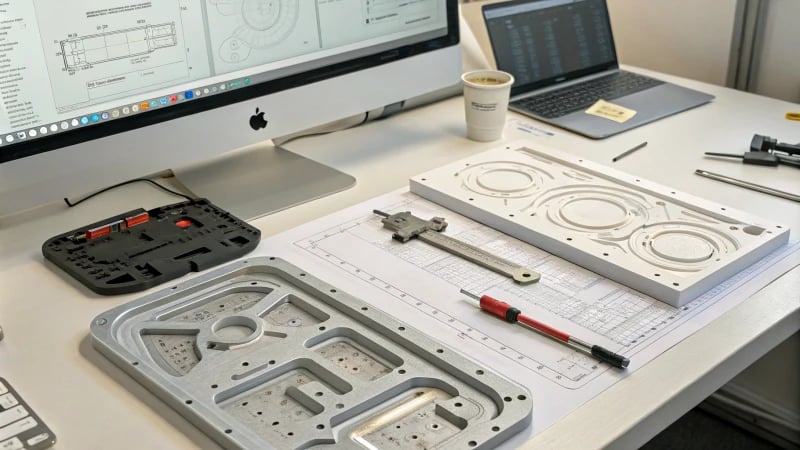
The Role of Shape Simplification in Warpage Prevention
I remember my first encounter with warpage issues. It felt like a nightmare trying to understand why my beautiful design ended up looking like wrinkled paper. That’s when I realized keeping things simple is crucial. In injection molding, complicated shapes often lead to uneven cooling and shrinkage6, which causes warping. Simplifying shapes really helps with consistent material flow and even cooling.
Maintaining Uniform Wall Thickness
One crucial lesson I learned was about wall thickness. Imagine you’re building a sandcastle and if a wall is thicker than the rest, it collapses unevenly. The same happens with designs. Keeping wall thickness uniform is essential to stop stress from concentrating in one area, which leads to warping7. When I design a simple rectangular box, I always keep the wall thickness the same on all sides. If thickness needs changing, I make sure it transitions smoothly to avoid sudden changes that cause warping.
Ribs and Their Strategic Placement
Ribs are tricky. They add strength without needing more thickness, but they must be designed wisely. Keeping ribs within 0.6-0.8 times the wall thickness helps them to be effective without causing problems. I once placed ribs radially on a round part; it balanced shrinkage well and reduced bending.
Factor | Recommendation | Example |
---|---|---|
Wall Thickness | Keep uniform | Rectangular box |
Ribs Size | 0.6-0.8 times wall thickness | Plastic bracket |
Rib Distribution | Uniformly placed | Circular parts |
Symmetrical Design Principles
Symmetry in design changed everything for me. It balances shrinkage forces and lowers the risk of warping. Think of a seesaw perfectly balanced in the middle; that’s the effect of symmetry. For example, designing a plastic beam with symmetrical cross-sections leads to even cooling, cutting down on distortion potential.
Avoiding Complex Geometries
Complex shapes are tempting – I’ve been there – but they mess up material flow and cooling processes. If avoiding them isn’t possible, adjust your gate and mold designs to handle these challenges and reduce their effects on cooling processes8.
Applying these principles has revolutionized my approach to design challenges, resulting in strong creations that survive manufacturing problems while keeping their integrity and purpose intact. Using these strategies effectively has truly increased product reliability and really boosted my confidence in creating high-quality work every time.
Uniform wall thickness prevents warpage.True
Consistent wall thickness ensures even cooling, reducing stress points.
Complex shapes promote consistent material flow.False
Complex shapes lead to uneven cooling and shrinkage, causing warpage.
How Does Symmetrical Design Contribute to Reduced Warpage?
Have you ever thought about stopping your creations from twisting and turning against your wishes?
Symmetrical design reduces bending by balancing shrinking forces throughout a product. Uniform wall thickness helps stability. Proper rib design supports strength. Simple shapes also contribute to strong and dependable manufacturing.
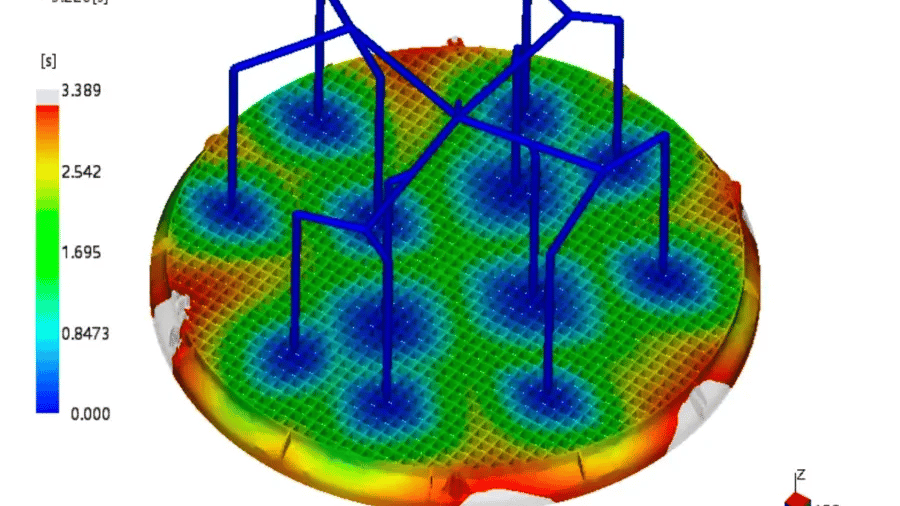
The Role of Symmetrical Design
There was a time when I worked hard on designing a complex part for a new gadget. I sat at my desk, surrounded by sketches and coffee mugs late into the night. Many designers, like me, notice that using symmetrical design in a product acts like a secret weapon. It fights against uneven cooling and shrinking problems. Symmetrical shapes help spread shrinkage forces equally, just like balancing weights can keep a see-saw steady.
In manufacturing, particularly in injection molding9, maintaining symmetry can mitigate the effects of uneven cooling and shrinkage. When a product is designed with symmetrical geometry, it ensures that shrinkage forces are distributed evenly.
Uniform Wall Thickness
A key lesson I learned early is the importance of uniform wall thickness. Think of cooking pasta. If one side is thicker, it won’t cook right. Likewise, in injection molding, uneven wall thickness leads to different cooling rates and causes warping. I strive for uniform wall dimensions in the product but introduce gradual changes if variations are necessary.
Design Element | Effect on Warpage |
---|---|
Uniform Wall | Reduces differential shrinkage |
Gradual Transitions | Minimizes stress concentrations |
Optimizing Ribs and Reinforcements
Ribs intrigue me. They are like quiet heroes of structure. Designing them the same on both sides and spreading them evenly stops the awful localized shrinking that causes warping. I usually keep rib thickness at 0.6-0.8 times the main wall thickness for a perfect blend.
Ribs are crucial for enhancing structural integrity without increasing wall thickness. However, their design must be symmetrical and evenly distributed to avoid localized shrinkage that could lead to warping.
Simplifying Product Geometry
I learned that complexity can be tricky. Complex shapes create problems with the flow and cooling of plastic melts. Now, I try to simplify shapes when I can; however, when complexity can’t be avoided, I tweak the design to reduce the effect on flow dynamics.
Optimized mold designs10 can also contribute to reducing warpage by ensuring even distribution of material during the injection process.
Balancing Shrinkage Forces
Symmetry influences more than just how things look. Take beams, for example: A symmetrical design can balance shrinkage forces during cooling and reduce warping.
Designers like me use CAD tools early to simulate these factors, saving many hours and headaches.
The principle of symmetry applies not only to external shapes but also to internal structures like ribs.
For instance, a symmetrical layout in a beam structure can balance out shrinkage forces on either side during cooling, thus minimizing warpage.
Designers who specialize in product design11 often leverage CAD tools to simulate and adjust these factors early in the design process.
This foresight helps achieve optimal outcomes in both aesthetics and functionality without compromising manufacturing efficiency.
Following these principles has allowed me to craft designs that meet high standards while improving manufacturing efficiency.
Symmetrical design reduces warpage in injection molding.True
Symmetrical design ensures even distribution of shrinkage forces.
Varying wall thickness helps prevent warpage.False
Varying wall thickness causes uneven cooling, leading to warpage.
Conclusion
Optimizing product design through uniform wall thickness, strategic rib placement, and simplified shapes effectively reduces warpage in injection molded parts, enhancing strength and manufacturing reliability.
-
This link explains how uneven wall thickness leads to cooling rate differences, causing warpage. ↩
-
Explore how symmetrical designs can balance shrinkage forces and minimize warping in molded parts. ↩
-
Learn about optimal rib design techniques to reduce warpage while maintaining part strength. ↩
-
Explore how effective material usage impacts rib design and part quality. ↩
-
Learn how rib design optimization can enhance manufacturing efficiency and reduce defects. ↩
-
Explore how uneven cooling leads to warpage in molded parts, essential for understanding design improvements. ↩
-
Learn why consistent wall thickness prevents warpage by ensuring even cooling. ↩
-
Discover how strategic gate design can mitigate complex shape impacts on cooling. ↩
-
Explore this link to understand the impact of design choices in injection molding on warpage issues. ↩
-
Learn about the role of optimized mold designs in minimizing warpage during manufacturing. ↩
-
Discover how CAD tools assist designers in optimizing product designs for better functionality and reduced warpage. ↩