Do flow marks on injection molded items frustrate you? Probably, they do. You’re definitely not the only one feeling this way!
Improved mold design cuts down on flow mark defects by changing runner systems, gate layouts and exhaust setups. These changes let plastic move more smoothly. This reduces turbulence and improves surface quality.
How do these small mold design changes improve your production line? In my years in the mold industry, I have witnessed how these adjustments greatly benefit production. Changing runner shapes like choosing circular designs for easy flow or trapezoidal for better processing can lower flow resistance a lot. Polishing these runners creates a smooth path for the plastic, preventing flow marks. Really smooth paths.
Gate design is also important. Picking the right gate type and size is like discovering a wonderful recipe – it just brings everything together perfectly. Pinpoint gates work for tiny, precise pieces, while fan gates suit larger surfaces. Correct gate location and size let the melt flow evenly, reducing flaws. Very important.
Exhaust design matters too. Correctly placed exhaust slots or breathable materials make a big impact. These parts let trapped gases escape, allowing the melt to flow like a calm river instead of a stormy sea, resulting in fewer flow marks.
These mold design tips help achieve both visual appeal and functional excellence. They change product results, bringing quality and satisfaction. Quality and satisfaction matter most.
Mold design optimization improves product surface finish.True
Optimized mold designs enhance melt flow, reducing surface defects.
Flow marks are caused by improper cooling of the mold.False
Flow marks result from uneven melt flow, not cooling issues.
How does runner system design reduce flow marks?
Some molded products appear perfect. Others do not look as good. The runner system design holds the secret!
Runner system design plays a vital role in reducing flow marks by adjusting runner shape, size, surface finish and gate design. The system allows smooth melt movement. Resistance decreases. Product quality improves.
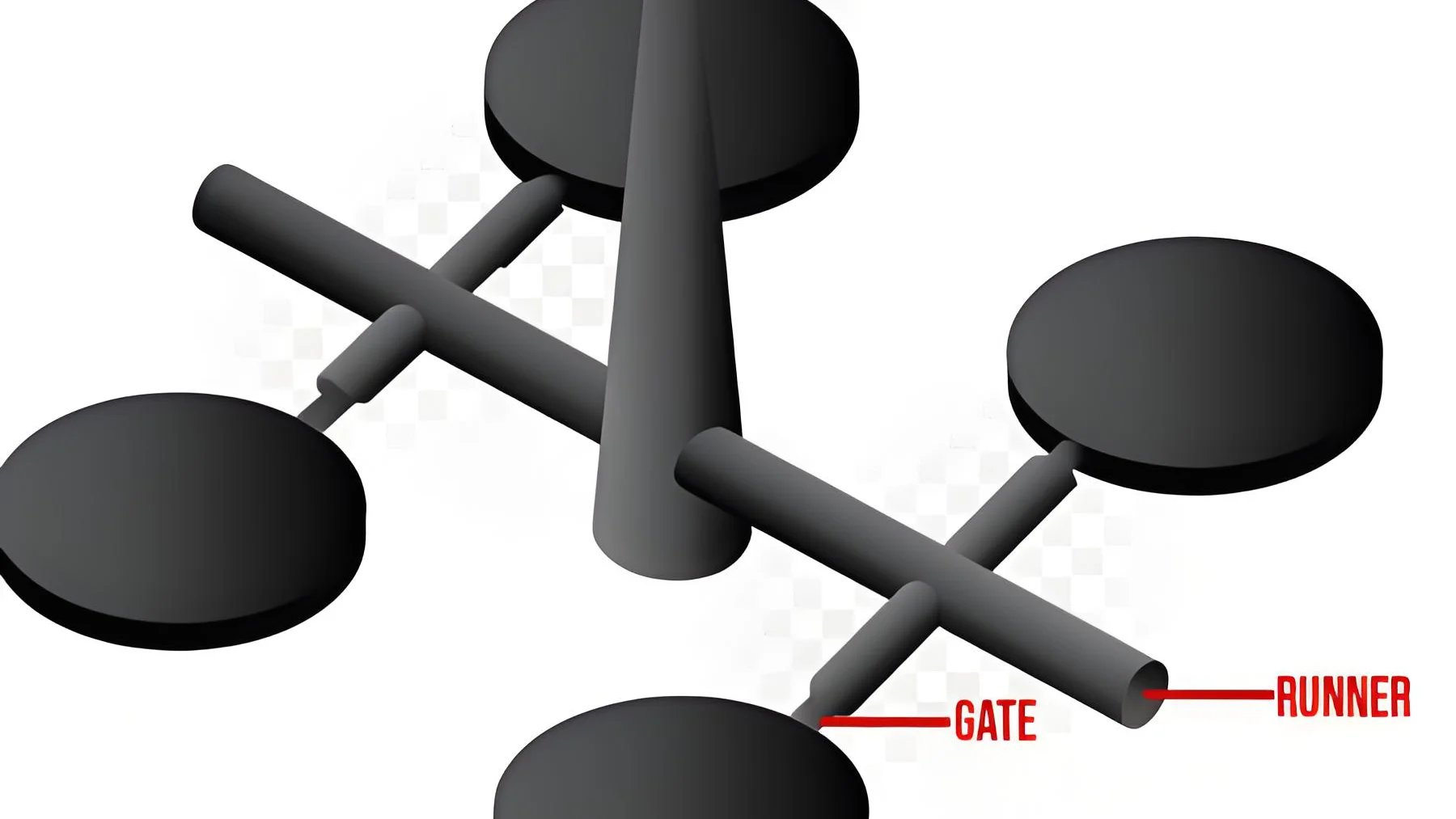
Importance of Runner Shape and Size
A well-designed runner system is essential for managing plastic melt flow. Circular runners are preferred for minimizing resistance, while trapezoidal runners offer easier processing.
Product Size | Main Runner Diameter | Branch Runner Diameter |
---|---|---|
Small | 3-5mm | 4-8mm |
Large | 6-10mm | 4-8mm |
Balancing product size with material flow is important for runner design. Dive into this detailed guide on runner design1 if interested.
Enhancing Runner Surface Finish
Improving surface finish reduces melt resistance, achieving a roughness of Ra0.4-0.8μm through precision machining. This technique prevents turbulence and subsequent flow marks.
Look at these precision machining techniques2 for more info.
Gate Design Optimization
Choosing the right gate type and size is crucial. A pin-point gate suits small products with high aesthetic needs, while fan gates are better for larger items.
Gate Type Examples:
- Pin-point Gate: Allows high-speed, even flow.
- Fan Gate: Great for wide injection range.
Gate placement affects melt spread and product look; it’s crucial. Learn about different gate types and placements3.
Exhaust Design Improvements
Finding out the power of exhaust slots was eye-opening. Slots at final filling points, like corners, ensure better flow and less marking. Using breathable materials4, such as breathable steel, helps gas escape in complex molds.
Focusing on these runner system designs has truly bettered the quality of molded items—fewer flow marks and smoother finishes every time.
Circular runners minimize resistance better than trapezoidal.True
Circular runners provide smoother flow paths, reducing melt resistance.
Pin-point gates are unsuitable for small products with aesthetic needs.False
Pin-point gates are ideal for small products requiring high aesthetic standards.
How Does Gate Design Influence Flow Mark Formation?
Do you ever think about how the delicate craft of gate design could really influence your injection molding projects? This aspect is very important – more important than you might believe.
Gate design affects flow mark creation by controlling how molten plastic goes into the mold. It changes the speed, path and spread. Choosing and adjusting the gate’s type, spot and size very carefully helps reduce flow marks. Quality of the final item improves greatly.
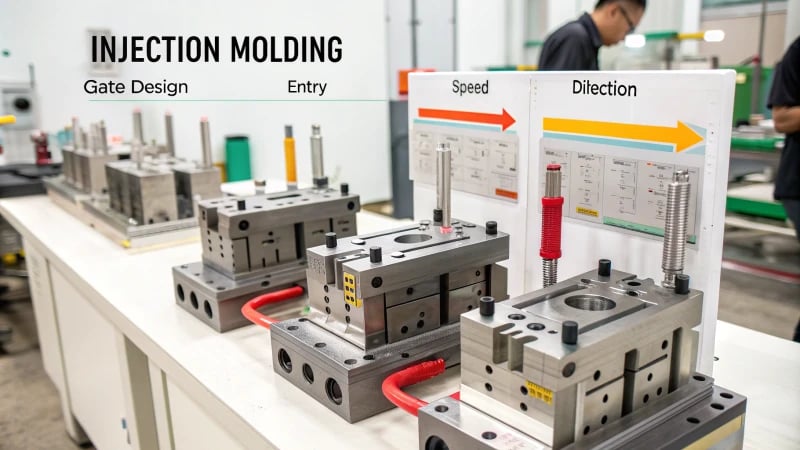
Gate Type and Flow Marks
In my journey as a product designer, I learned that picking the right gate type seems like choosing the right tool for a home project. When you choose correctly, everything fits together very well. Imagine creating parts where every detail counts. A pin-point gate helps here by letting the melt flow fast and evenly. It feels like the joy of cooking a good meal. For bigger surfaces, fan or side gates spread the melt like butter on toast, reducing any ugly buildup.
Gate Type | Suitable For | Key Benefits |
---|---|---|
Pin-point | Small parts with high finish | Fast, uniform filling |
Fan | Large flat surfaces | Even distribution |
Side | Various geometries | Versatile placement |
Location and Its Impact
In molding, location is all about planning, like setting up a perfect trip. Place gates on thicker walls to lower resistance. This way, the melt spreads smoothly through the mold, similar to choosing good stops on a journey for a smoother ride. In circular products, centering the gate covers everything equally, like starting in the middle of a city. For long shapes, place gates at smart points, like knowing when to rest on a long drive to keep things smooth.
Size Matters
The right gate size needs to fit perfectly, like choosing shoes that fit just right. A very small gate pushes the melt too quickly, similar to rushing tasks and missing details. A gate that is too big slows things down, affecting quality. Find the sweet spot where everything flows smoothly.
Beyond Gates: Runner and Exhaust System
Optimizing the runner system is like preparing an instrument before playing. A round runner reduces resistance like hitting a perfect note. Trapezoidal designs make processing easier. The surface finish of runners is also important – think of polishing an instrument for a smoother sound.
Additionally, effective venting strategies5 ensure trapped gases don’t lead to turbulence.
Feature | Importance |
---|---|
Runner Shape | Affects melt resistance |
Surface Finish | Stabilizes flow |
Venting | Prevents turbulence |
Complex molds need breathable materials like a room with fresh air. This helps things flow smoothly without hitches.
Integrating Design Elements
The blend of gate design and molding elements feels like leading an orchestra. Each part helps achieve harmony in manufacturing results. By focusing on how elements work together, I can create solutions that meet special product needs6. Each design I handle meets all the important points.
Pin-point gates reduce flow marks in small parts.True
Pin-point gates allow fast, uniform filling, reducing flow marks on small parts.
Larger gate sizes increase shear rates.False
Larger gate sizes lower shear rates, affecting fill quality and flow mark formation.
Why Is Exhaust Design Crucial in Mold Optimization?
I first explored mold design and discovered the crucial role of exhaust design.
Exhaust design plays a key role in mold optimization. It lets trapped air and gases exit, stopping defects such as flow marks. A smoother melt flow results. This process probably improves the look of the products. Structural strength gets better too.
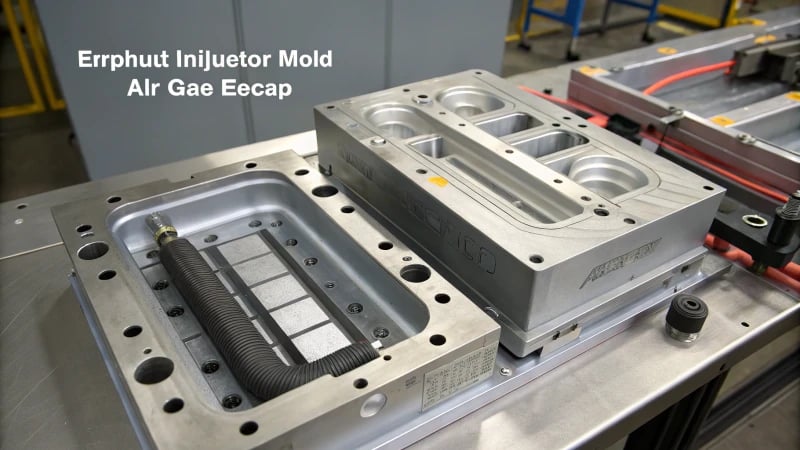
Understanding Exhaust Design in Molding
When I first explored mold design, the importance of exhaust design surprised me. I found out that allowing air and gases to escape during molding is not just a step – it’s crucial for good product quality. Without this, flaws like flow marks7 and burn marks could damage the product. Things like exhaust slots and materials that let air through are very important.
Exhaust Slot Configuration
I worked on a project where correct exhaust slot placement was essential. Precision mattered – locating the slots at the last stage of fill, like tricky corners or areas with different wall thickness. Dimensions were also very crucial.
Slot Feature | Dimension |
---|---|
Depth | 0.02-0.04mm |
Width | 3-5mm |
Correct slot design was essential to reduce trapped air and improve flow. This was crucial.
Using Breathable Materials
In some difficult molds, materials that breathe, like breathable steel, helped us a lot. These allowed gases to escape efficiently, especially in places where normal slots didn’t work well. This method improved the flow, making tough molds easier to handle.
Connection with Runner System
Joining exhaust design with the runner system was important too. A smooth runner surface reduced flow resistance, which helped the melt flow into the cavity well. A rough surface could create turbulence and trap air – something to avoid.
Importance of Gate Design
Where to place the gate also impacted exhaust effectiveness. Placing gates in thicker sections improved flow and reduced trapped air by balancing pressure throughout the cavity. It showed how connected all parts are.
Using good exhaust designs has often improved mold efficiency and product quality for me, especially in consumer electronics8. For someone skilled like Jacky, knowing these techniques is very important for successful projects.
Exhaust slots are placed at the last point of fill.True
Slots are located at corners or wall thickness transitions to minimize trapped air.
Breathable steel is used in all mold designs.False
Breathable steel is used in areas prone to air entrapment, not universally.
How do you implement breathable materials for better mold performance?
Have you ever thought your molds might not reach their full ability? New materials with breathability can give them another chance!
Using materials that let air pass in mold design involves placing steel inserts that allow air to escape. This helps air and gases leave the mold. It also helps the flow of the melted material. Using these materials really helps reduce problems like flow marks.
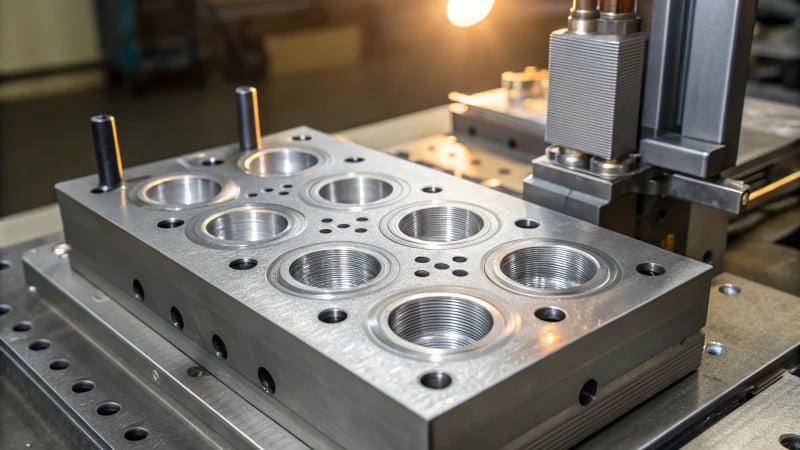
Understanding Breathable Materials
First time I heard about breathable materials, I thought of tiny lungs inside molds. They let gases out, stopping problems like air pockets and flow marks. They really change things where gas gets stuck.
Breathable materials, such as breathable steel9, are engineered to allow gases to escape from the mold cavity, preventing defects like air pockets and flow marks. They are used strategically in areas prone to gas entrapment.
Benefits of Breathable Materials
-
Gas Exhaust Control: Imagine a mold taking a big breath, letting out trapped air and gases. These materials help gases flow out, keeping the melt flow smooth.
-
Longer Mold Life: Less pressure and stress mean molds last longer. Your molds grow old gracefully!
Application in Mold Design
I worked on a mold with a complex shape. Air got trapped and it was frustrating. Adding breathable materials in problem areas really helped.
Product Type | Recommended Material Placement |
---|---|
Complex shapes | Internal structural areas |
Flat surfaces | Corners and edges |
Techniques for Best Results
-
Runner System
- Circular runners lower resistance for plastic melt flow. Truly effective approach!
- Smooth surfaces stop turbulent flow – precision in machining and polishing is critical.
-
Gate Design
- Pin-point gates suit products needing good looks. They work wonders!
- Gates in thicker wall sections help better diffusion.
-
Exhaust Slots
- Put slots where melt reaches last – this helps remove gas. Strategic placement is key.
- Balance slot dimensions for venting without hurting mold strength.
Practical Steps
- Choosing Materials: Think about the material characteristics10 that your mold needs.
- Design Integration: Work with skilled designers to add breathable materials into current designs.
- Testing and Adjustment: Test thoroughly to optimize insert placement and size. Adjust based on how they perform.
Breathable materials really improve product quality and reduce waste—a new path in mold design. Try them and watch your molds transform!
Breathable materials prevent mold defects like air pockets.True
Breathable materials allow gases to escape, preventing air pockets.
Flat surfaces benefit most from breathable material use.False
Complex shapes benefit more from breathable materials than flat surfaces.
Conclusion
Optimizing mold design through improved runner systems, gate types, and exhaust setups significantly reduces flow mark defects in injection molded products, enhancing both appearance and functionality.
-
This link provides an in-depth guide on runner system design principles, aiding designers in optimizing their processes. ↩
-
Discover advanced machining techniques that improve runner surface finish, crucial for reducing flow resistance. ↩
-
Understand various gate types and placements to enhance melt distribution and minimize flow marks. ↩
-
Learn how breathable materials improve gas discharge in molds, enhancing melt flow and reducing imperfections. ↩
-
Learn about effective venting strategies that prevent defects in molded products by allowing trapped gases to escape. ↩
-
Discover techniques to optimize product design, enhancing quality and reducing defects in manufacturing. ↩
-
Explore common defects like flow marks caused by inadequate exhaust design, aiding in prevention strategies. ↩
-
Learn how exhaust design impacts the molding of consumer electronics, crucial for designers like Jacky. ↩
-
Learn about breathable steel’s properties and its role in enhancing mold performance. ↩
-
Find criteria for selecting the right breathable materials for your specific needs. ↩