Have you ever thought about how those complex plastic gadgets in your car get created? Multi-stage injection molding machines might be the solution.
Multi-stage injection molding machines are ideal for creating complex plastic products. These machines adjust speed and pressure at every step. Exact settings help achieve top quality results. They work well for items with different wall thicknesses and detailed inner designs. Specific material requirements are also handled with care.
When I first started learning about multi-stage injection molding, it was like discovering a new world full of possibilities. These machines can adapt to different industries’ needs. Picture creating a car interior part. The outside is thin and smooth, while the inside is strong and sturdy. Multi-stage injection treats each part just right. Gentle care goes to thin parts, while tough pressure shapes the thick ones.
I remember a project about making perfect plastic gears. The task was really difficult. However, with multi-stage injection, every groove got filled with precision, keeping the quality high. This technology suits both sleek phone cases and perfect cosmetic bottles. It delivers high accuracy and a perfect look. And let’s not forget tricky materials like PVC that are sensitive to heat. Multi-stage injection keeps them cool and strong. It’s like a tool that not only meets, but also anticipates, complex manufacturing needs.
Multi-stage injection molding is used in automotive parts production.True
Multi-stage machines handle complex designs and varied thicknesses, ideal for automotive.
Multi-stage injection molding cannot produce thin-walled containers.False
These machines excel in creating products with varied wall thicknesses, including thin walls.
- 1. How Do Multi-Stage Injection Molding Machines Handle Complex Geometries?
- 2. Why is Multi-Stage Injection Molding Essential for High-Precision Products?
- 3. How does multi-stage injection molding improve surface quality?
- 4. How Can Multi-Stage Injection Molding Machines Handle Different Materials Efficiently?
- 5. Conclusion
How Do Multi-Stage Injection Molding Machines Handle Complex Geometries?
Have you ever thought about how experts create detailed plastic pieces with exactness? Multi-stage injection molding machines use special methods to achieve this.
Multi-stage injection molding machines control complex shapes by adjusting speed and pressure carefully at each step. These machines fill with precision. No defects appear in both thin-walled and detailed parts.
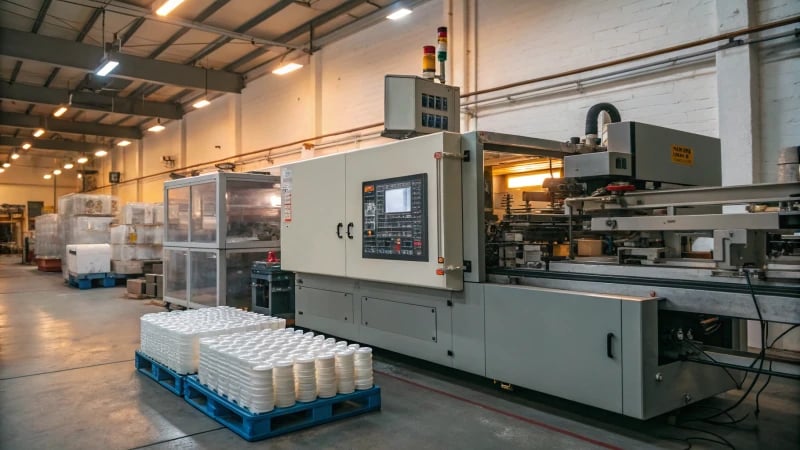
Balancing Thin and Thick Walls
Discovering multi-stage injection molding was like opening a new door to complex design. This method allows different wall thicknesses in one product. Very innovative. Visualize creating an automotive interior part with an outer layer just 2mm thin, while some areas need a strong 4mm thickness.
Wall Thickness | Injection Speed | Injection Pressure |
---|---|---|
Thin (<2mm) | 30 – 50 mm/s | Low |
Thick (>4mm) | 100 – 200 mm/s | High |
Begin gently with slower speeds (30 – 50mm/s) for thin sections to avoid problems. Then, increase speed (100 – 200mm/s) for thicker areas to get a complete fill and prevent short shots.
Controlling Internal Shapes
I once worked on a project with detailed plastic gears. High precision was essential but daunting. Multi-stage injection1 molding made it possible. Starting at a slow pace (30 – 40mm/s) let the material fill every gear groove smoothly without affecting their delicate structure. The machine adjusted over time to keep the product accurate, which really mattered for its function.
Achieving Exact Measurements
Precision is crucial, especially for electronic cases. Imagine molding phone cases where even a tiny mistake could be a big problem. Multi-stage injection acts precisely, adjusting speed and pressure to keep measurements exact so every piece fits perfectly.
- Example: In a phone case project, the accuracy was like art in engineering.
Guaranteeing Perfect Looks
Appearance matters a lot in cosmetic bottles. I once dealt with a line focused on perfect surfaces. Multi-stage injection’s beginning low-speed step avoided marks. Later steps released trapped gas, removing any silver streaks and giving a really flawless finish.
Handling Different Material Characteristics
Materials Sensitive to Heat
Working with PVC without damage was difficult until I used multi-stage injection. Starting at low speeds (20-40 mm/s), we controlled heat well, avoiding any material damage and keeping it intact.
Thick Materials
Polycarbonate lenses brought their own issues. These thick materials needed careful treatment.
Starting slowly (30-50 mm/s) and making changes as needed filled them without stress, keeping clarity intact.
Material Type | Initial Speed | Subsequent Adjustments |
---|---|---|
Heat-Sensitive (PVC) | 20-40 mm/s | Temperature control |
High-Viscosity (PC) | 30-50 mm/s | Stress management |
Exploring the capabilities of multi-stage2 injection molding offers the chance to create complex parts that reach top levels of quality and precision.
Thin walls require higher injection speed.False
Thin walls need lower speed (30-50 mm/s) to prevent defects.
Multi-stage injection reduces surface defects in cosmetic bottles.True
It prevents flow marks and allows gas release for a flawless finish.
Why is Multi-Stage Injection Molding Essential for High-Precision Products?
Precision molding goes beyond a simple method; it’s like an art that changes the way we craft detailed, top-notch products. Come with me as I explore the wonders of multi-stage injection molding and its significant effect on achieving outstanding manufacturing.
Multi-stage injection molding significantly improves the quality of high-precision products. It offers precise control over injection speed and pressure. This process increases accuracy in measurements. It also betters surface texture and strength. This is very important for complex and demanding uses.
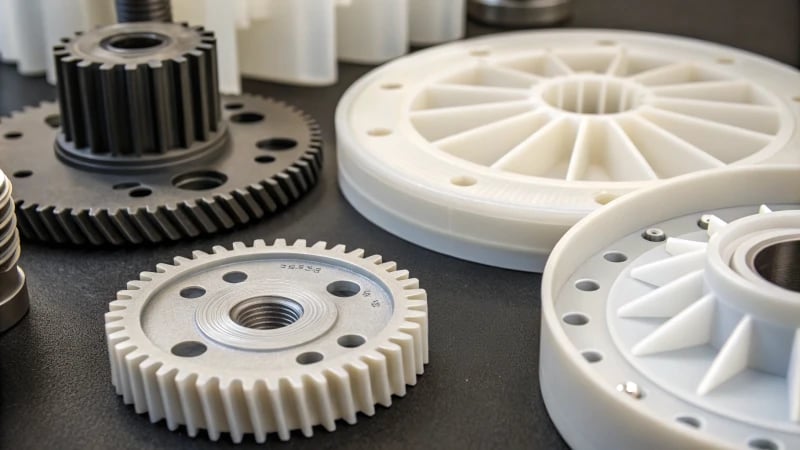
Precision and Dimensional Accuracy
Everything fits perfectly with multi-stage injection molding. Think about creating a smartphone case where every tiny bit matters. This method lets me control speed and pressure at each step. Accurate material fills up the mold smoothly. Precision is vital for electronic parts because even tiny mistakes can cause trouble. Precision3 is essential.
For example, in producing mobile phone shells, the process allows for millimeter-per-second level control, ensuring assembly meets stringent standards. The ability to finely tune parameters at each stage leads to exceptional precision.
Surface Quality Enhancement
Sometimes you see a product and think, "Wow, smooth!" Multi-stage injection molding helps achieve that. Imagine making clear cosmetic bottles. Slow injection at first helps prevent bad flow marks. Later, a slower pace removes gas bubbles, ensuring a perfect surface.
Consider the injection of transparent cosmetic bottles4. Multi-stage injection achieves flawless surfaces, enhancing the aesthetic appeal. This method is indispensable for products where appearance is paramount.
Complex Shapes and Internal Structures
Building a complicated plastic piece, like a gear, is tough. Multi-stage injection really helps here. Slow material filling allows the mold to handle complex shapes nicely. Increasing speed ensures thick areas fill without any problems.
This technique is vital for products combining thin and thick walls. Initial low speeds (30-50mm/s) suit thin parts, while increased speed (100-200mm/s) fills thicker sections without defects.
Handling Different Material Properties
Materials behave differently under stress. For example, with sensitive PVC, slow at first avoids overheating, much like slowly getting into a warm bath.
High-viscosity materials like polycarbonate need speed adjustments to fill perfectly without damage.
Understanding material needs is crucial; perfect timing is key.
Material Type | Initial Speed (mm/s) | Subsequent Adjustments |
---|---|---|
Heat-sensitive (PVC) | 20-40 | Adjust to fill within safe range |
High-viscosity (PC) | 30-50 | Adjust based on filling conditions |
The multi-stage approach is like talking with your materials – responding rightly so your creations not only meet but often surpass expectations.
Conversations with materials ensure product quality and functionality are consistently achieved.
Industry Use
In fields like automotive and electronics, where products have to be strong and precise,
multi-stage injection creates parts with different wall thicknesses easily.
Designing complex plastic pieces becomes easier with this technique,
enhancing efficiency and product quality significantly.
Multi-stage injection molding improves surface quality.True
It prevents flow marks and allows gas discharge, enhancing aesthetics.
High-viscosity materials require fast initial injection speeds.False
They need low initial speeds to ensure quality without internal stress.
How does multi-stage injection molding improve surface quality?
Have you ever been amazed at how stylish and perfect those luxury plastic products appear? Advanced techniques in multi-step injection molding create this appeal.
Multi-stage injection molding improves surface quality. It controls injection speed and pressure with great precision. This process reduces defects like flow marks and silver streaks. It fits complicated shapes and precise requirements. The appearance of the final product looks better.
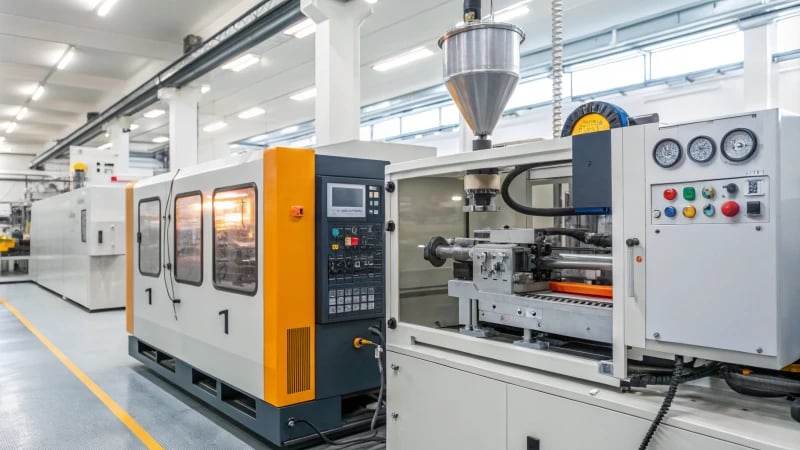
Understanding Multi-Stage Injection Molding
I remember seeing multi-stage injection molding for the first time. It was like music, each step timed perfectly to create something amazing. This method carefully changes speed and pressure during molding. This lets product designers5 control how materials flow and really improve how surfaces look, preventing common defects.
Application in Complex Shapes
Working on products with both thin and thick walls is a really interesting task. Automotive interiors are a good example; the outer part might be thin, while inside parts are thicker. By adjusting speed between 30 to 200 mm/s at different times, we fill every small corner perfectly, avoiding short shots that can be annoying.
Wall Thickness | Injection Speed (mm/s) | Pressure (kPa) |
---|---|---|
Thin (<2mm) | 30-50 | Moderate |
Thick (>4mm) | 100-200 | High |
Here’s a simple guide on how we tweak speed and pressure:
Precision in High-Demand Products
Precision is a must for things like electronic casings. The secret is controlling every tiny part of the injection process. We start slow to avoid breaking the cavity, then slowly increase speed to keep things accurate and well-made.
Enhancing Appearance Quality
How a product looks is very important, especially in cosmetic packaging. Multi-stage injection helps a lot here by starting with slow injection to stop ugly flow marks. Later steps push out any trapped gases smoothly.
Adapting to Material Properties
Each material needs different care. Over the years, this has become second nature to me. Some materials, like PVC, need a slow start to avoid breaking down. Others, like PC, need careful speed changes so we fill spaces without stress.
If curious about high-viscosity materials, there’s much to learn about high-viscosity material challenges6. Understanding these details of multi-stage injection molding helps designers improve product quality while handling complex shapes and materials efficiently.
By understanding the nuances of multi-stage injection molding, designers can enhance product quality significantly while addressing complex shape and material challenges. This flexible process optimizes both functional and aesthetic properties of plastic products efficiently.
Multi-stage injection reduces flow marks in molding.True
Controlled speed and pressure adjustments prevent surface defects like flow marks.
Thick walls require lower injection speeds in molding.False
Thick walls need higher speeds (100-200 mm/s) for complete filling.
How Can Multi-Stage Injection Molding Machines Handle Different Materials Efficiently?
Have you ever thought about how those smooth, intricate plastic items come to life so flawlessly? This text takes you on a journey through the world of multi-stage injection molding.
Multi-stage injection molding machines work well with different materials by carefully adjusting speed and pressure during the process. This flexibility leads to high-quality outcomes. Complex designs and varied material properties do not pose a challenge. The adaptability remains crucial.
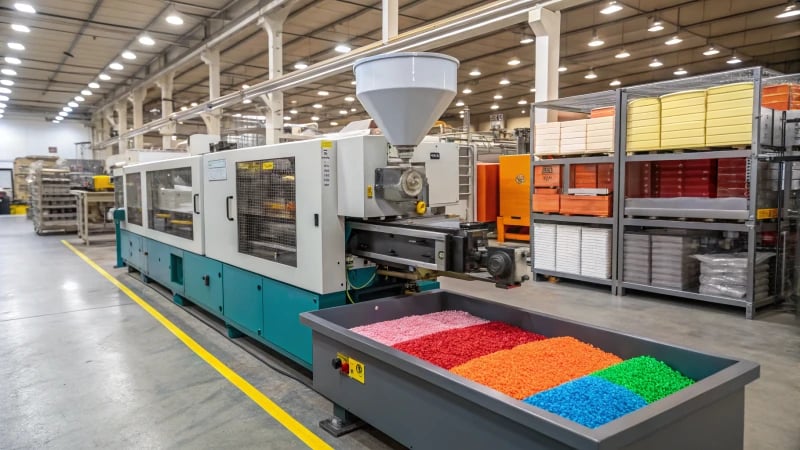
How Multi-Stage Injection Molding Changes Material Versatility
In my experience with mold design, multi-stage injection molding machines change everything. They work like a Swiss army knife, carefully fitting the needs of many different materials. By adjusting speed and pressure, these machines brilliantly handle both heat-sensitive and thick materials.
Injection Molding of Heat-Sensitive Materials
I recall my first time with polyvinyl chloride7 (PVC). This material feels like balancing on a tightrope, as it may break down easily if not handled right. Multi-stage machines begin gently with slow injection speeds to reduce heat, then slowly increase to fill the mold fully without overheating. They do this well.
Injection Molding of High-Viscosity Materials
Materials like polycarbonate (PC) demand a different skill. Multi-stage machines begin at a slow pace, then increase speed to lessen stress and keep high optical quality. This is especially important for making clear lenses.
Material Type | Initial Speed (mm/s) | Mid-stage Speed (mm/s) | Pressure Control |
---|---|---|---|
Heat-Sensitive | 20-40 | Adjustable | Prevent decomposition |
High-Viscosity | 30-50 | Incremental | Maintain optical quality |
Tackling Complex Product Designs
Imagine molding a product with both thin and thick sections – it feels like juggling fire! Multi-stage machines skillfully manage these complex designs. They start slowly for thin areas to stop any defects and go faster for thick parts to ensure a complete fill.
Products with gentle internal structures benefit too. The machine lets melted material flow gently into detailed areas first, then speeds up to keep the product’s strength.
Handling High-Precision Requirements
Making precise items like electronic casings requires absolute precision. Multi-stage injection molding becomes crucial here. The process starts with soft, slow filling to lower stress, then continues with precise control to reach exact standards. Precision matters very much.
Learn more about precision molding techniques8 to enhance product quality and consistency across production runs.
The flexibility of multi-stage injection molding machines is one-of-a-kind in this industry. They work quietly to guarantee our products hit top standards, no matter the complexity or sensitivity of the material. They’re the true heroes.
Multi-stage injection molding is ideal for heat-sensitive materials.True
It controls speed and pressure to prevent material decomposition.
High-viscosity materials are not suitable for multi-stage injection.False
These machines adjust parameters to handle high-viscosity materials efficiently.
Conclusion
Multi-stage injection molding machines enhance the production of complex plastic products by precisely controlling speed and pressure, ensuring high quality, dimensional accuracy, and superior surface finishes.
-
Explore how multi-stage injection improves the quality of intricate internal structures by precisely controlling the fill process. ↩
-
Discover detailed insights into multi-stage injection molding techniques that enhance production efficiency and product quality. ↩
-
Learn how precise control over injection parameters improves mold filling efficiency and product quality. ↩
-
Discover how controlled injection stages lead to flawless surfaces in cosmetic products. ↩
-
Explore how varying injection speeds during molding impacts surface defects, leading to improved finishes. ↩
-
Understand the complexities of molding high-viscosity materials to optimize product quality and reduce defects. ↩
-
Explore how multi-stage injection molding settings protect PVC from heat-induced decomposition. ↩
-
Discover advanced techniques in precision molding for ensuring high-quality electronic product casings. ↩