Have you ever wondered how the flow of plastic affects the products we see every day?
Understanding how plastic fluidity influences injection molding is crucial for optimizing manufacturing outcomes.
While grasping the basics is important, diving into the nuances of controlling plastic fluidity can elevate your manufacturing skills to new heights. Let’s explore some expert insights and practical strategies together.
Plastic fluidity affects mold filling performance.True
High fluidity ensures complete mold filling, reducing defects and improving product quality.
What Role Does Plastic Fluidity Play in Mold Filling Performance?
Plastic fluidity is a pivotal factor in injection molding, impacting the efficiency and quality of mold filling.
Plastic fluidity determines how well materials flow into mold cavities, impacting product completeness and quality. High fluidity ensures thorough filling, reducing defects like short shots and uneven surfaces, especially in intricate molds. Conversely, low fluidity can result in incomplete fills, compromising product integrity.

Understanding Plastic Fluidity
Plastic fluidity refers to the ease with which plastic melts flow into the intricate cavities of a mold during the injection molding process. This characteristic is crucial in determining the quality and efficiency of the final product.
Impact on Filling Performance
-
Complete Filling: High fluidity allows plastics to navigate complex mold geometries, ensuring that even the most intricate corners are filled. This reduces defects such as short shots, where the material fails to fill the entire mold, leaving gaps or incomplete sections.
-
Uniform Distribution: Good fluidity contributes to an even distribution of material throughout the mold. This uniformity is essential for maintaining consistent product density and reducing internal stresses that can lead to defects like warping or cracking during usage.
Practical Examples
Consider a scenario where you’re producing a thin-walled container. A plastic with superior fluidity will fill thin sections more reliably, creating a sturdy and visually appealing product. In contrast, using a plastic with poor fluidity might result in uneven wall thicknesses and potential weak spots.
The Interplay Between Fluidity and Mold Design
The design of the mold itself can amplify or mitigate issues related to plastic fluidity. For instance, increasing the size of the gate—the entry point of the plastic into the mold—can enhance fluidity, allowing for better flow into tight spaces.
Table: Impact of Mold Design on Fluidity
Mold Feature | Effect on Fluidity |
---|---|
Gate Size | Larger gates improve flow |
Runner Design | Optimized runners reduce flow resistance |
Surface Roughness | Smoother surfaces enhance flow |
Understanding these dynamics is vital for manufacturers aiming to improve product quality and production efficiency. Adjustments in mold design can compensate for limitations in material fluidity, enabling better control over the injection molding process.
By mastering these elements of plastic fluidity1, manufacturers can significantly boost their production outcomes, ensuring products that meet high standards of quality and performance.
High fluidity reduces mold filling defects.True
High fluidity ensures complete filling, minimizing defects like short shots.
Larger gates decrease plastic fluidity.False
Larger gates actually improve flow, enhancing fluidity in molds.
How Can Material Selection Influence Plastic Fluidity?
Choosing the right material is key to managing plastic fluidity in injection molding processes.
Material selection directly impacts the fluidity of plastics by affecting their molecular structure and composition. The choice of polymers, additives, and fillers can enhance or hinder flow properties, making it critical to select materials that align with specific molding requirements and product characteristics.

Understanding Polymer Basics
At the heart of plastic fluidity is the polymer itself. Different polymers possess unique molecular weights and structures, which significantly affect their flow properties. For instance, low molecular weight polymers typically exhibit better fluidity due to their simpler chain structures. Conversely, high molecular weight polymers may offer enhanced strength but can struggle with fluidity challenges.
Role of Additives and Fillers
Additives play a pivotal role in modifying the fluidity of plastics. Plasticizers, for instance, are added to polymers to increase flexibility and fluidity by reducing intermolecular forces. Common additives2 like lubricants and flow promoters also aid in achieving desired flow characteristics by reducing viscosity and improving lubrication between polymer chains.
Fillers such as glass fibers or mineral additives can either improve or impede fluidity depending on their concentration and distribution within the polymer matrix. While they can enhance mechanical properties, excessive fillers may lead to increased viscosity, thus challenging fluidity.
Tailoring Materials for Complex Designs
Selecting materials with optimal fluidity becomes crucial when dealing with intricate mold designs. For thin-walled components or products with detailed features, materials that offer superior fluid flow are essential to avoid defects such as short shots or incomplete fillings.
Materials like ABS (Acrylonitrile Butadiene Styrene) are often favored for their balanced properties of toughness and fluidity, making them suitable for complex shapes. Meanwhile, material selection tools3 can assist manufacturers in choosing polymers that best meet the demands of specific applications.
Importance of Material Testing
Testing different materials under simulated production conditions can provide insights into their fluidity performance. Techniques such as rheology testing help in understanding how different compositions behave under stress, guiding manufacturers to make informed material selections.
Conclusion
Material selection is a strategic decision that shapes the efficiency and quality of injection molding processes. By understanding the relationship between material composition and fluidity, manufacturers can tailor their choices to enhance production outcomes.
Low molecular weight polymers have better fluidity.True
Simpler chain structures in low molecular weight polymers enhance fluidity.
Excessive fillers always improve plastic fluidity.False
Excessive fillers increase viscosity, often reducing fluidity.
What Injection Molding Parameters Affect Fluidity Control?
Discover how adjusting injection molding parameters can optimize plastic fluidity for superior production outcomes.
Injection molding parameters such as temperature, pressure, and speed significantly influence plastic fluidity. Optimal control of these parameters enhances product quality by ensuring uniform density and reducing internal stress. Balancing these factors also boosts production efficiency by minimizing cycle times and energy consumption.
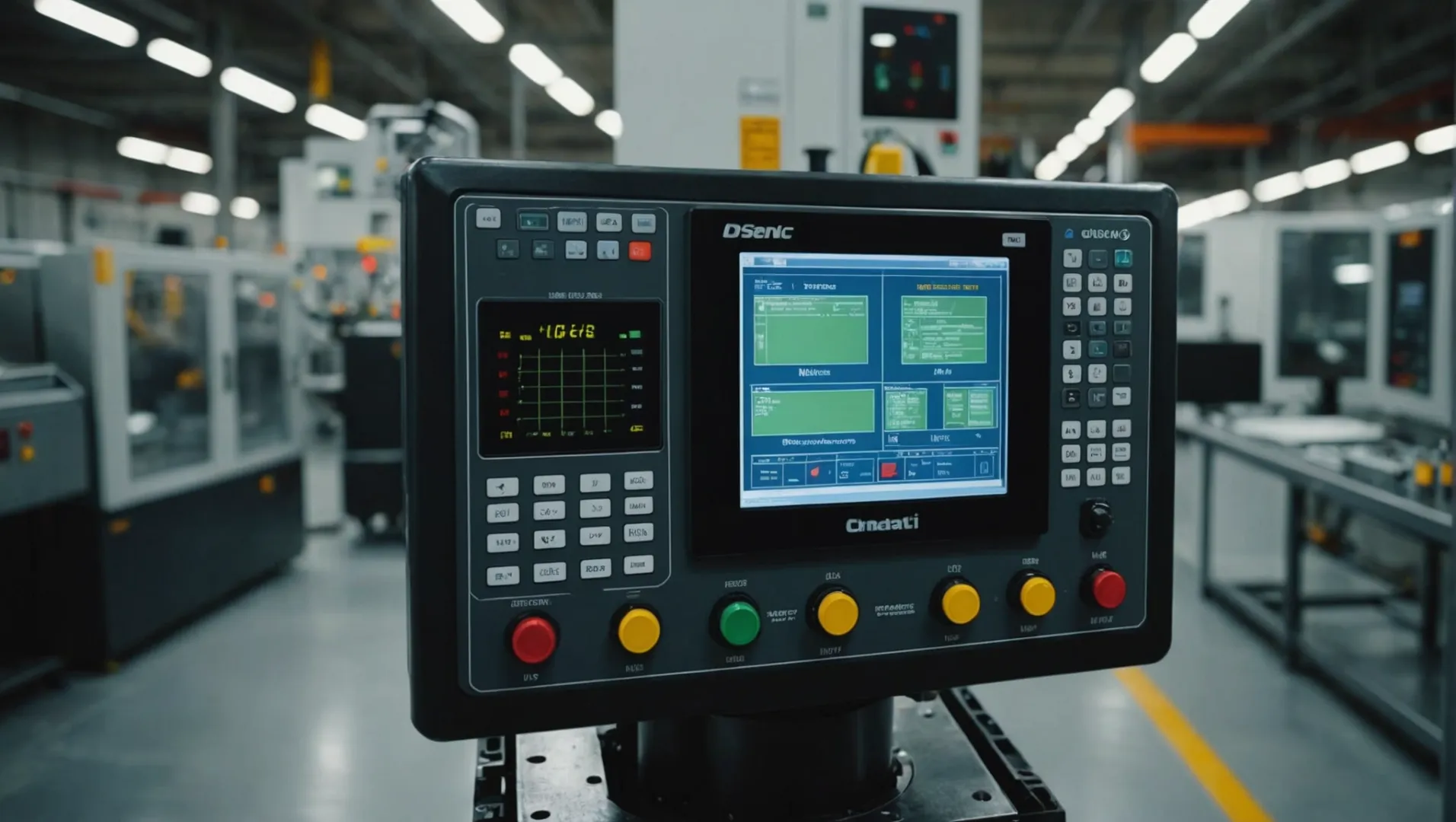
Temperature Adjustments and Their Impact
Increasing the injection molding temperature can reduce the viscosity of the plastic, enhancing its fluidity4. However, care must be taken not to exceed the material’s thermal limits, as excessive heat can lead to decomposition or other defects. Identifying the ideal temperature range involves considering both the material properties and the product requirements.
Pressure Dynamics in Fluidity Control
Applying higher injection pressure can improve fluidity by forcing the plastic into intricate mold sections. Yet, excessive pressure may introduce issues such as flash or increase internal stresses, potentially leading to product deformations. Finding the balance involves understanding the mold’s structural characteristics and the desired product specifications.
The Role of Injection Speed
Adjusting the injection speed is another crucial parameter for managing fluidity. A faster speed can assist in achieving better flow characteristics, especially in complex molds. However, too rapid an injection may result in defects like jetting. Calibration should align with both the product’s requirements5 and the plastic’s inherent flow properties.
Parameter Optimization Through Experimentation
A table illustrating the effects of varying each parameter could look like this:
Parameter | Effect on Fluidity | Potential Risks |
---|---|---|
Temperature | Reduces viscosity | Decomposition |
Pressure | Enhances mold filling | Flash, stress increase |
Injection Speed | Improves flow characteristics | Jetting |
Experimentation with these variables allows manufacturers to tailor their processes, ensuring optimal fluidity control for different plastics and mold designs.
In conclusion, mastering these parameters requires a nuanced approach that balances material properties with process conditions to achieve high-quality results.
Higher temperature reduces plastic viscosity in molding.True
Increasing temperature lowers viscosity, enhancing fluidity.
Excessive injection speed eliminates all mold defects.False
Too rapid injection can cause defects like jetting.
How Does Mold Design Impact the Fluidity of Plastics?
A well-thought-out mold design can significantly influence plastic fluidity, affecting the final product’s quality and production efficiency.
Mold design affects plastic fluidity by optimizing gate size, runner design, and surface roughness. These elements ensure plastics fill molds smoothly, enhancing product quality and production efficiency. Effective designs accommodate plastics with varying fluidity levels, improving manufacturing outcomes.
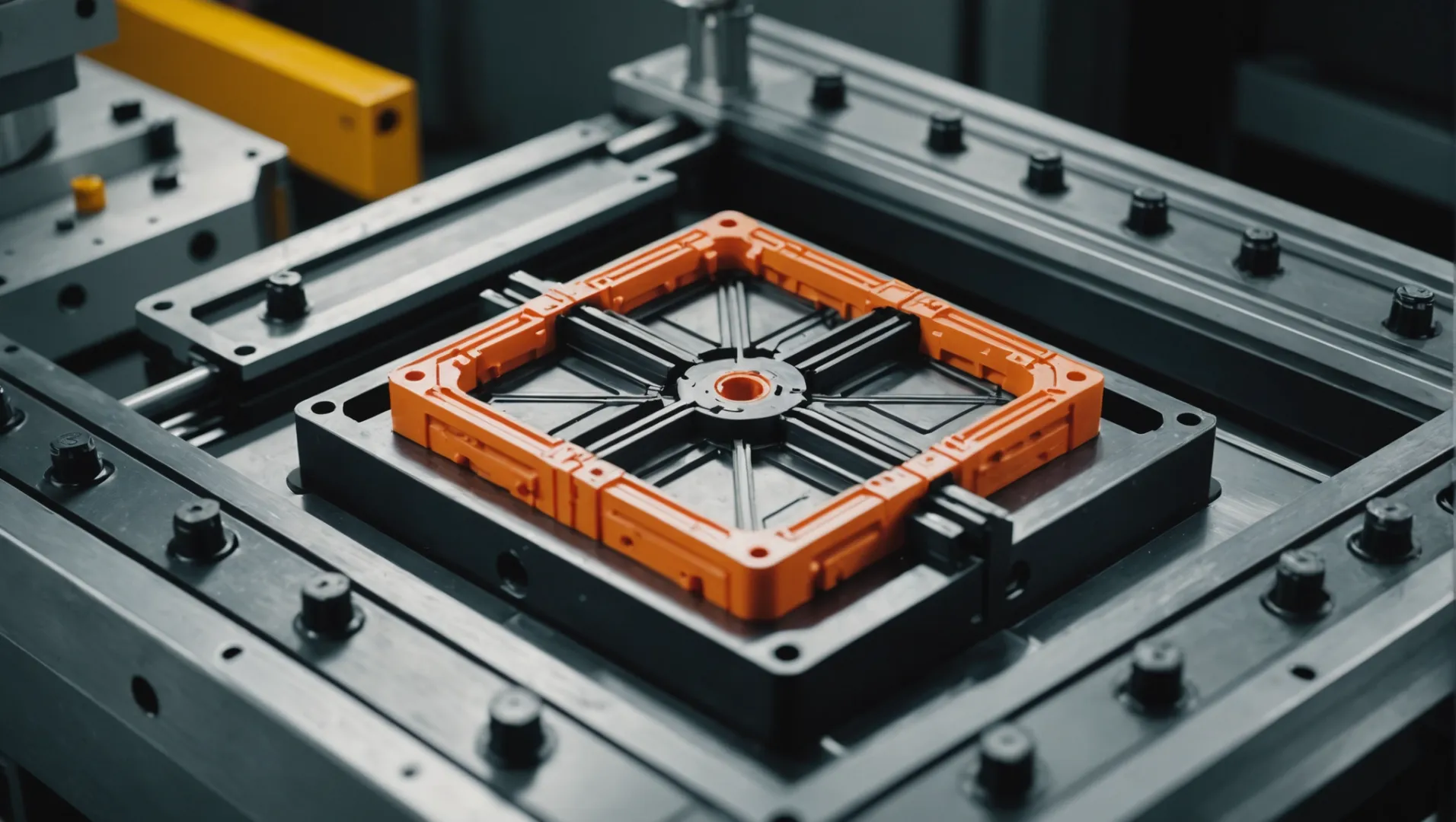
Optimizing Gate Size
The gate is the entry point where molten plastic enters the mold cavity. Properly sizing the gate is crucial for controlling plastic fluidity. An appropriately sized gate allows the plastic to flow at an optimal rate, reducing resistance and preventing defects like short shots or incomplete fillings. Large gates can enhance fluidity but may lead to excessive flashing, whereas small gates might impede flow.
Enhancing Runner Design
Runners are channels that guide molten plastic from the gate to various parts of the mold. A well-designed runner system balances flow and pressure, ensuring even distribution of material. By strategically placing runners and adjusting their dimensions, manufacturers can maintain consistent fluidity across complex molds. This approach is particularly beneficial when dealing with plastics of poor fluidity, as it ensures all sections are adequately filled.
Reducing Surface Roughness
Surface roughness within a mold can impede plastic flow by increasing friction and causing turbulence. By polishing mold surfaces and employing coatings that reduce friction, manufacturers can enhance fluidity. Smooth surfaces allow plastics to glide more easily, decreasing the likelihood of defects such as flow marks or ripples.
Incorporating Advanced Mold Features
For plastics with inherently low fluidity, integrating advanced mold features like multiple gates or hot runner systems can be advantageous. Multiple gates provide alternative entry points, ensuring that all areas of the mold are filled efficiently. Meanwhile, hot runner systems keep the plastic in a molten state, facilitating continuous flow and reducing cycle times.
Feature | Impact on Fluidity |
---|---|
Gate Size | Controls flow rate and pressure |
Runner Design | Ensures even distribution |
Surface Roughness | Reduces friction |
Advanced Mold Features | Enhances flow for low-fluidity plastics |
While these strategies offer significant benefits, it’s essential to tailor each element to the specific characteristics of the plastic being used. Explore more about gate size optimization6 to learn how it impacts fluidity and product quality.
Large gates always improve plastic fluidity.False
Large gates can enhance fluidity but may cause excessive flashing.
Surface roughness affects plastic flow in molds.True
Rough surfaces increase friction, hindering smooth plastic flow.
Conclusion
Mastering plastic fluidity can dramatically improve product quality and production efficiency. Take action today to enhance your injection molding processes.
-
Learn how optimizing fluidity enhances product quality and efficiency.: The most important factors are the viscosity and melt temperature of the plastic resin. The lower the viscosity of the plastic, the better its fluidity. The … ↩
-
Discover how additives modify plastic fluidity for better injection molding.: Plastics are not solely comprised of polymers, they also contain additives that enhance plastic functions by modulating their physical and chemical properties. ↩
-
Explore tools that aid in choosing suitable materials for complex designs.: Learn how to select the right material for your injection molding design with this technical overview of thermoplastic resins. ↩
-
Learn about temperature’s role in adjusting plastic viscosity effectively.: Temperature plays an essential role in injection molding, as it affects the viscosity of the molten material and the cooling time. ↩
-
Understand how speed adjustments enhance flow in intricate mold designs.: Increasing injection speed shortens the injection time, resulting in the production of high-quality products at significantly lower mold … ↩
-
Discover the impact of gate size on fluidity and product integrity.: This video explores the basics of sizing gates for your injection molded parts, to reduce shear stress and optimize part dimensions. ↩