Have you ever marveled at the gleaming finish on a plastic product and wondered how to achieve that shine yourself?
Achieve a high-gloss finish in injection molding by selecting high-gloss materials, optimizing mold design, ensuring a polished mold surface, and controlling molding temperature and pressure.
When I first started in the molding industry, I was fascinated by the intricate dance of science and art that goes into creating that perfect glossy finish. Every step, from selecting high-gloss materials like ABS to meticulously polishing the mold, felt like solving a complex puzzle. It’s all about precision and care—like when I added gloss-enhancing additives for the first time and saw the difference it made. Each tweak in temperature or pressure felt like a small victory. As I deepened my understanding, these details became more than technical steps—they were the keys to transforming ordinary plastic into something extraordinary.
Using gloss-enhancing additives boosts finish quality.True
Additives improve surface smoothness and reflectivity, enhancing gloss.
Polished mold surfaces are unnecessary for high-gloss finishes.False
A polished mold ensures a smoother product surface, crucial for gloss.

What Materials Are Best for High-Gloss Injection Molding?
Ever wondered how some products manage to shine so effortlessly? Let me take you on a journey through the world of high-gloss injection molding, where materials and techniques play a starring role.
For high-gloss injection molding, use polystyrene (PS) or acrylonitrile-butadiene-styrene (ABS) for their natural gloss, enhanced by additives. Consider mold design and injection process for optimal shine.
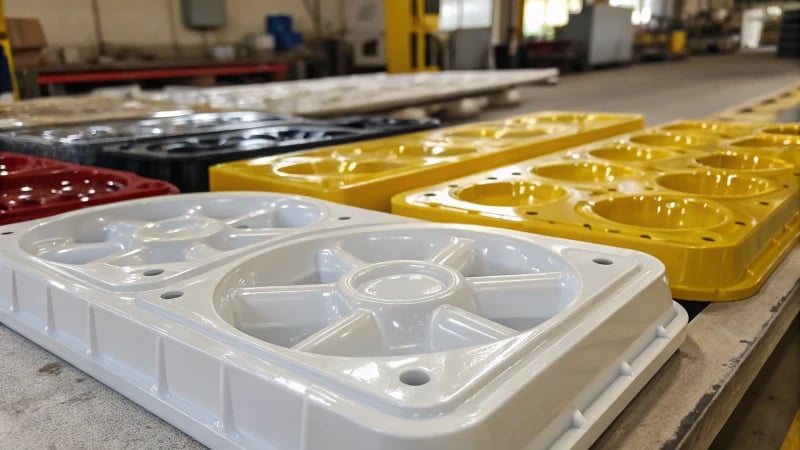
Material Selection for High Gloss
In my journey as a mold designer, I’ve often been amazed at how the right material choice can transform an ordinary product into something truly eye-catching. Material selection is key when aiming for a high-gloss finish. Polystyrene (PS) and acrylonitrile-butadiene-styrene (ABS) are my personal favorites because they naturally boast a glossy surface. These materials work wonders for high-end electronics or toys where aesthetics truly matter.
Material | Gloss Level | Common Applications |
---|---|---|
PS | High | Toys, containers |
ABS | High | Electronics, auto parts |
I’ve found that adding gloss-enhancing additives like brighteners can work magic on the surface finish, but balance is crucial. Add too much, and you risk compromising the mechanical properties of your material.
Mold Design Considerations
When I think back to the countless hours spent perfecting mold designs, I realize just how important the mold design is in achieving that sought-after glossiness. The quality of the mold’s surface is non-negotiable; achieving low surface roughness through precision machining and polishing is essential.
Utilizing special techniques such as chemical mechanical polishing or electrospark mirror machining can give you that mirror-like finish on the mold surface. This ensures that the plastic melt mirrors this smoothness perfectly, resulting in a high-gloss product.
Injection Molding Process Optimization
In my experience, tweaking the injection molding process can make all the difference. Controlling the temperature is crucial—higher temperatures can reduce melt viscosity, which helps fill the mold more completely and smoothly.
Managing pressure and speed during injection is also vital to avoid defects like flash or turbulence that can ruin your glossy surface. Implementing proper cooling strategies1 ensures uniform cooling and prevents surface defects.
By focusing on these elements—material choice, mold design, and processing techniques—you’ll be well on your way to achieving that high-gloss finish in your injection molded products. For those keen on pushing boundaries, explore advanced techniques2 to further refine your strategies and reach the pinnacle of manufacturing excellence.
Understanding these factors not only enhances product aesthetics but also boosts overall performance and quality across various applications3. Keep pushing for innovative solutions to stay ahead in this ever-evolving manufacturing landscape.
ABS is suitable for high-gloss electronic casings.True
ABS naturally has a glossy surface, ideal for electronics.
Polystyrene is unsuitable for high-gloss finishes.False
Polystyrene has a naturally high gloss, ideal for such finishes.
How does mold design influence gloss levels?
I’ve always been fascinated by how the tiniest details in mold design can dramatically affect the glossiness of plastic components. It’s like a magic trick hidden in plain sight, ready to transform everyday objects into sleek, glossy wonders.
Mold design affects gloss levels through surface quality, venting, and gate design. A smooth surface, efficient venting, and precise gate placement enhance the glossiness of injection molded parts.
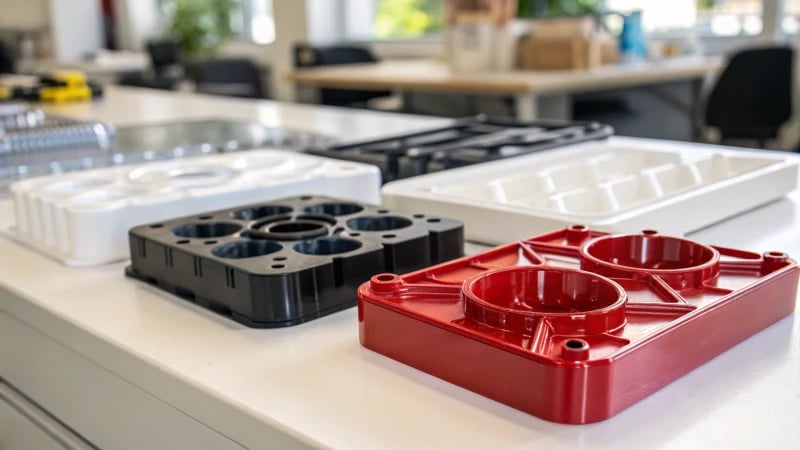
The Role of Mold Surface Quality
In my experience, the mold’s surface quality is like the canvas for a painter. It determines how the final piece will shine and captivate. Achieving that perfect high-gloss surface involves maintaining low surface roughness, typically between Ra0.2 – Ra0.4μm. I’ve spent countless hours refining this through precision machining and polishing techniques such as chemical mechanical polishing4. These meticulous processes ensure the plastic melt mirrors the mold’s smoothness, creating a stunning glossy finish.
Process | Description |
---|---|
Precision Machining | Achieves low roughness levels for smoother surfaces. |
Chemical Mechanical Polishing | Utilized for mirror-finishing to boost gloss levels. |
Optimizing Gate Design
Gate design is where the art of molding truly comes to life. I’ve found that choosing the right gate design is crucial for achieving consistent gloss across a product’s surface. For high-gloss parts, pin-point or latent gates are my go-to choices. They help reduce turbulence and weld marks during melt flow, promoting a uniform high-gloss finish. Placing the gate at a discreet location ensures that variations in surface gloss due to uneven melt flow are minimized.
Importance of Venting Design
The secret to that flawless finish often lies in proper venting. Good venting design ensures that air trapped within the mold cavity is expelled efficiently, allowing the melt to fill the cavity perfectly and achieve that coveted high-gloss finish. I’ve learned to pay attention to venting grooves, typically 0.02-0.05mm deep, along with using venting materials like breathable steel at parting surfaces. Proper venting prevents defects like air entrapment5, which can dull the final product’s shine.
Material Selection and Additives
Over the years, I’ve realized that choosing the right materials can make or break the gloss levels we aim for. High-gloss plastic materials like ABS are a fantastic choice if you’re looking to enhance gloss naturally. Adding gloss additives, such as brighteners, can also improve melt fluidity, resulting in smoother surfaces.
Material | Typical Use | Gloss Enhancement Strategy |
---|---|---|
ABS | Electronic housings, toys | Selection of high-gloss variants |
PC | Optical applications | Addition of brighteners for improved surface quality |
But it’s always a balancing act; too many additives might compromise the material’s mechanical properties.
In essence, getting that perfect glossy finish is a delicate dance of considering mold design elements like material selection, mold surface treatment, gate positioning, and venting strategies. Each step must be executed with precision to enhance the aesthetic appeal of plastic components without compromising their functionality or production efficiency.
High-gloss surfaces require Ra0.2 - Ra0.4μm roughness.True
Achieving high-gloss surfaces involves maintaining low surface roughness, between Ra0.2 - Ra0.4μm, through precision machining and polishing.
Venting grooves should be deeper than 0.05mm for best results.False
Venting grooves are typically 0.02-0.05mm deep to ensure air is expelled effectively, preventing defects.
Why Are Additives Crucial for Achieving High Gloss?
Ever wondered what makes that glossy finish so eye-catching?
Additives are vital for high gloss, enhancing surface smoothness, fluidity, and filling imperfections, creating a mirror-like finish essential for aesthetic and functional purposes.
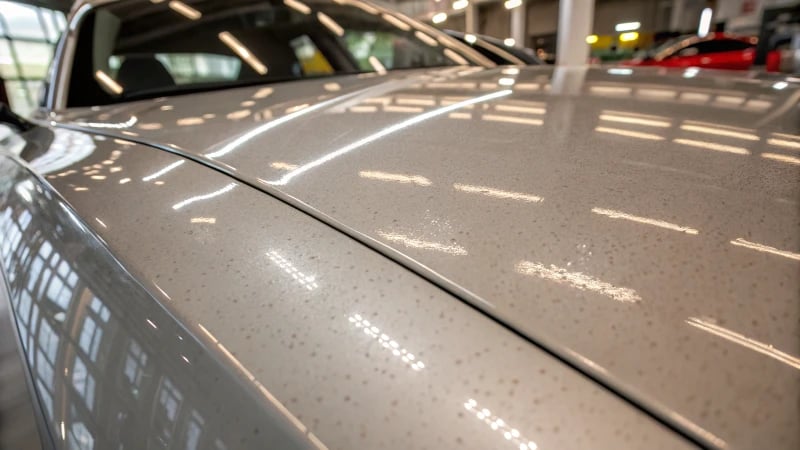
The Role of Additives in High-Gloss Finishes
So, I’ve spent countless hours trying to figure out why some of my projects just didn’t have that perfect, reflective shine I was aiming for. Turns out, the secret sauce is additives. These little wonders improve the fluidity of the plastic melt6, allowing it to fill molds more evenly and create a flawlessly smooth surface.
Material Selection and Additives
In my line of work, choosing the right material can make or break a project. I’ve seen this firsthand with materials like polystyrene (PS) and acrylonitrile-butadiene-styrene (ABS). Their natural glossiness is a dream to work with, especially when paired with the right gloss additives7 like brighteners. These materials have helped me achieve some pretty stunning finishes.
Material | Inherent Gloss | Suitable Additives |
---|---|---|
PS | High | Brighteners |
ABS | Very High | Brighteners |
Mold Design Considerations
I can’t stress enough how mold quality affects the final product’s gloss. My team and I once spent weeks perfecting the surface of a mold to reduce its roughness. We aimed for Ra0.2 – Ra0.4μm, and the results were spectacular. Additives further enhanced the finish by filling in microscopic imperfections.
Injection Molding Process
Temperature control8 during injection molding is another area I’ve had to refine over time. Playing around with temperatures (keeping them within 180℃ – 200℃) can significantly improve fluidity and gloss, although it’s a delicate balance to avoid any degradation.
Parameter | Recommended Range | Impact on Gloss |
---|---|---|
Temperature | 180℃ – 200℃ | Improved fluidity and gloss |
Pressure | Moderate | Enhanced surface finish |
Achieving Consistent Gloss
Consistency is key, right? Balancing additives, precision mold design, and controlled processes has been a game changer for me. Effective venting designs9 are crucial in ensuring that air doesn’t create imperfections in the finish.
Ultimately, additives not only fill tiny surface defects but also enhance colors, making them pop in a way that truly elevates the product’s aesthetic appeal.
Additives improve plastic melt fluidity for high gloss.True
Additives enhance fluidity, allowing even mold filling and smooth surfaces.
High temperatures increase viscosity in injection molding.False
High temperatures reduce viscosity, improving mold conformity and gloss.
How does temperature affect gloss in injection molding?
Ever wondered how the glossiness of your injection molded products is achieved? Let me take you through the fascinating role temperature plays in this process.
Temperature in injection molding influences plastic flow and viscosity, affecting surface gloss. Precise temperature control ensures a smoother, shinier finish.
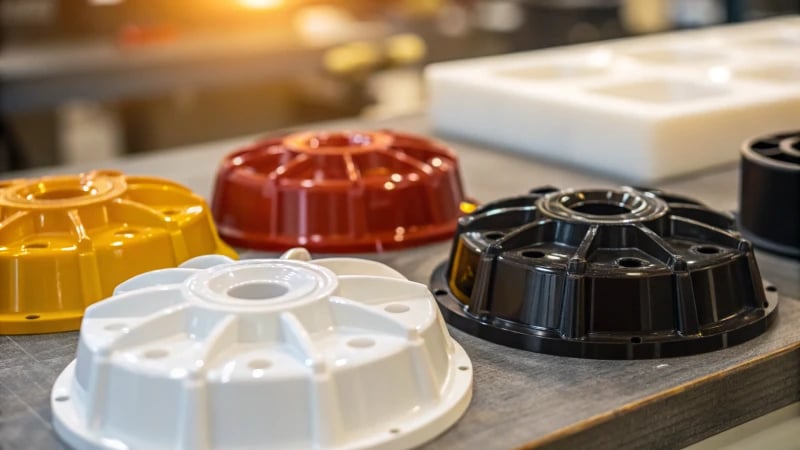
Temperature’s Impact on Material Viscosity
I still remember my first encounter with the magic of temperature control10 in injection molding. It was like discovering the secret ingredient in a family recipe. Higher temperatures can significantly reduce the viscosity of the plastic melt, allowing it to fill the mold cavity with ease, much like how a hot knife glides through butter. This results in that beautifully smooth surface we all aim for. However, crank it up too much, and it’s like leaving cookies in the oven for too long—degradation happens, especially with materials like polypropylene.
Temperature Range | Impact on Material |
---|---|
180℃ – 200℃ | Improved flow and gloss |
>220℃ | Risk of degradation |
Surface Gloss and Cooling Rate
Managing the cooling rate was a game-changer for me. Think of it as making sure every part of your cake cools evenly to avoid those unsightly cracks on top. A steady cooling rate ensures a uniform gloss across the product surface. If it’s inconsistent, you end up with defects like warping or dullness, not unlike a cake that sinks in the middle. By tweaking the cooling system layout11, achieving that perfect finish becomes a reality.
Balancing Injection Pressure and Speed
Temperature doesn’t work alone; it partners with pressure and speed. Picture driving a car—too slow, and you might not get there on time; too fast, and you could crash. Similarly, with injection molding, lower pressures can lead to inadequate cavity fill, while excessive speeds create turbulence. Both hurt gloss. That’s why I find it crucial to maintain optimal pressure and speed settings12 for a glossy, flawless surface.
Material Selection and Additives
Selecting the right materials is like choosing the finest ingredients for your signature dish. Opt for high-gloss materials such as ABS, and don’t shy away from using additives like brighteners to enhance gloss further. Just like adding a dash of vanilla can elevate your dessert, these additives improve melt flow but remember moderation is key to prevent compromising material properties.
Mold Design Considerations
The mold is where the magic happens—it’s like the canvas for your masterpiece. A high-quality mold surface directly impacts the product’s final appearance. Techniques like mirror finishing13 can make all the difference by replicating the mold’s smoothness onto your product.
In essence, understanding and controlling temperature within the injection molding process is akin to mastering an art form essential for achieving desired gloss levels in finished parts. It’s not just about aesthetics; it’s about ensuring functional performance and meeting those high standards we set for ourselves.
Higher temperatures improve plastic flow in molding.True
Higher temperatures reduce viscosity, improving flow and surface gloss.
Excessive cooling rates enhance surface gloss.False
Inconsistent cooling can lead to defects like warping, reducing gloss.
How Can You Prevent Defects That Affect Gloss Finish?
Ever struggled with achieving that perfect, shiny gloss finish? Trust me, it’s more than just an aesthetic choice—it’s a meticulous art.
To prevent gloss finish defects, use high-gloss materials, precision molds, and refine injection molding techniques. Ensure smooth mold surfaces and optimize process parameters for enhanced shine and quality in your products.
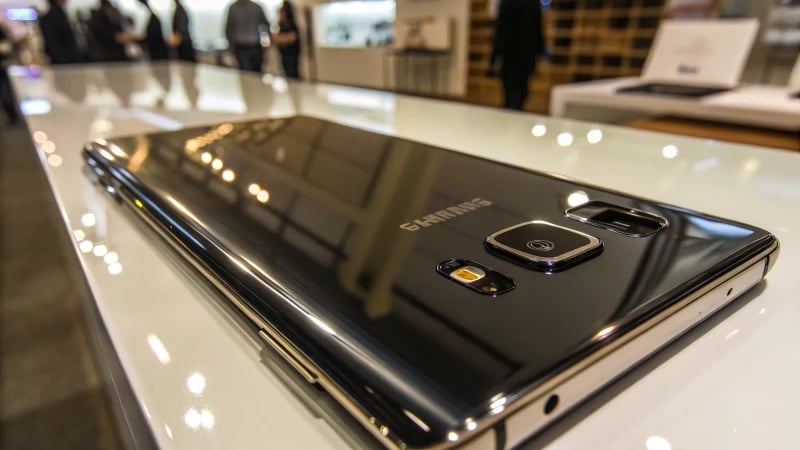
I’ve always been fascinated by the art of creating that flawless, mirror-like gloss on products. It all starts with picking the right materials. Imagine you’re picking out the perfect fabric for a custom suit—every detail matters. I usually go for high-gloss plastics like ABS or polystyrene because they naturally possess that sought-after shine. And just like adding a pinch of salt to a dish can enhance its flavors, introducing gloss additives14 can make the surface even smoother and shinier.
Material Selection Matters
When I first started in product design, I learned that the foundation of a great gloss finish begins with material selection. Choosing high-gloss plastic raw materials such as polystyrene or ABS can make a significant difference. These materials have an inherent sheen that’s perfect for products where appearance is key.
Additives for Enhanced Gloss
Think of gloss additives as the secret sauce in your recipe for success. By incorporating them, you can boost the surface quality of plastics like polycarbonate. But just like seasoning, too much can ruin the dish—so balance is key.
Mold Design Techniques
Designing a precision mold is akin to setting the stage for a blockbuster movie; everything needs to be perfect. I make sure the mold’s surface is polished to a near-mirror finish using methods like chemical mechanical polishing or electrospark mirror machining.
Aspect | Details |
---|---|
Surface Quality | Low roughness (Ra0.2 – 0.4μm) |
Gate Design | Pin-point or latent gates |
Venting Design | Effective exhaust measures |
Injection Molding Process Optimization
The magic really happens during the injection molding process. It’s like baking a cake—you need to get the temperature and pressure just right to ensure the perfect rise and texture. I carefully manage the injection temperature15 to achieve optimal melt flow, avoiding degradation that could ruin the finish.
Pressure Holding and Cooling
Controlling pressure holding time is crucial to avoid those pesky shrinkage marks. It reminds me of letting a cake cool down properly before slicing into it—patience is key for a perfect result. Plus, an optimized cooling system ensures that each part of the product cools evenly, preventing surface distortions and maintaining that gorgeous gloss.
High-gloss plastics like ABS prevent defects.True
ABS inherently possesses a high gloss level, reducing defect risks.
Uneven cooling causes shrinkage marks.True
Consistent cooling prevents shrinkage marks, ensuring a smooth finish.
Conclusion
Achieving a high-gloss finish in injection molding requires careful material selection, precise mold design, and optimized processing techniques to enhance aesthetics and product quality.
-
Learn effective cooling techniques to ensure uniform cooling, crucial for avoiding surface defects and enhancing gloss. ↩
-
Discover cutting-edge methods to further refine your injection molding process and achieve superior gloss finishes. ↩
-
Explore various industries where high-gloss finishes are essential, helping you understand broader applications and opportunities. ↩
-
Discover detailed methodologies to achieve mirror-finished mold surfaces for enhanced gloss levels. ↩
-
Learn how air entrapment impacts the quality and gloss of injection molded parts. ↩
-
Explores how brighteners improve plastic flow, ensuring even mold filling for smoother surfaces. ↩
-
Offers insight into selecting the right additives for achieving high gloss in ABS materials. ↩
-
Provides guidelines on temperature settings to optimize gloss during injection molding. ↩
-
Discusses venting strategies that prevent air entrapment and enhance surface finish. ↩
-
Learn how temperature adjustments can optimize material flow and improve product gloss. ↩
-
Discover methods to ensure consistent cooling and enhance surface finish. ↩
-
Find out how these parameters interact with temperature for better gloss. ↩
-
Explore how advanced mold polishing enhances product gloss. ↩
-
Discover how gloss additives can enhance the visual appeal of plastic products. ↩
-
Learn how temperature adjustments can improve the fluidity and appearance of your molded parts. ↩