Have you ever marveled at the crystal-clear clarity of a lens or a perfectly molded plastic casing? Achieving that level of transparency in injection molded parts is not just a science—it’s an art!
To achieve higher transparency in injection molded parts, select materials with high optical clarity like PMMA or PC, optimize molding parameters, control mold temperature, ensure sound mold design, apply post-processing techniques, and consider using appropriate additives.
While these initial strategies lay a strong foundation, each factor plays a unique role in determining the final product’s clarity. Let’s dive deeper into these aspects and uncover valuable insights essential for your projects.
PMMA is the best material for transparent injection molding.True
PMMA offers excellent optical clarity and high light transmittance, ideal for transparency.
What Are the Best Materials for Transparent Injection Molding?
Choosing the right material is crucial for achieving transparency in injection molded products. Certain materials offer superior optical clarity and durability, making them ideal for transparent applications.
The best materials for transparent injection molding include PMMA, PC, and PS, each offering unique properties that enhance optical clarity and performance in molded parts.

Polymethyl Methacrylate (PMMA)
PMMA is widely recognized for its excellent optical clarity and high light transmittance, often compared to glass. This makes it an optimal choice for applications like lenses and display panels. Its ease of processing and lower density compared to glass further enhance its appeal in transparent injection molding.
However, PMMA is brittle and may scratch easily, which might limit its use in environments requiring high impact resistance. Nevertheless, its affordability and clarity make it a popular choice.
Polycarbonate (PC)
Polycarbonate is another top choice due to its outstanding impact resistance and transparency. It is used in various applications where durability is crucial, such as eyewear lenses and safety shields.
PC offers better thermal resistance than PMMA, allowing for more robust applications. It is also less prone to scratching and offers good UV resistance, making it suitable for outdoor applications. However, it can be more expensive and requires careful handling during processing to prevent defects.
Polystyrene (PS)
While not as clear as PMMA or PC, PS offers good clarity at a lower cost, making it suitable for disposable applications such as food packaging or laboratory equipment. It is easy to process and has a high degree of versatility.
However, PS is not as strong or impact-resistant as PC, which limits its use in more demanding applications. Nonetheless, its cost-effectiveness and ease of processing make it a viable option for certain projects.
Material | Optical Clarity | Impact Resistance | Cost | Applications |
---|---|---|---|---|
PMMA | High | Low | Affordable | Lenses, display panels |
PC | High | High | Higher | Eyewear lenses, safety shields |
PS | Moderate | Low | Low | Food packaging, lab equipment |
Each of these materials offers distinct advantages that can be leveraged based on the specific requirements of your transparent molding project. For instance, if your primary need is impact resistance with transparency, polycarbonate applications1 might be your best choice. On the other hand, for projects prioritizing cost-efficiency without extreme strength requirements, polystyrene uses2 could be more appropriate. Understanding these properties allows you to select the material that best meets the balance of transparency, durability, and cost for your application.
PMMA is more impact-resistant than PC.False
PMMA is less impact-resistant than PC, which is known for its durability.
PS is the most cost-effective for transparent applications.True
PS offers good clarity at a lower cost, making it highly cost-effective.
How Do Injection Molding Parameters Affect Transparency?
Injection molding parameters are pivotal in defining the clarity and transparency of molded parts, influencing their suitability for high-clarity applications.
Optimizing injection molding parameters such as temperature, pressure, and speed is crucial for enhancing the transparency of molded parts. These adjustments help to reduce defects like bubbles and improve material flow.
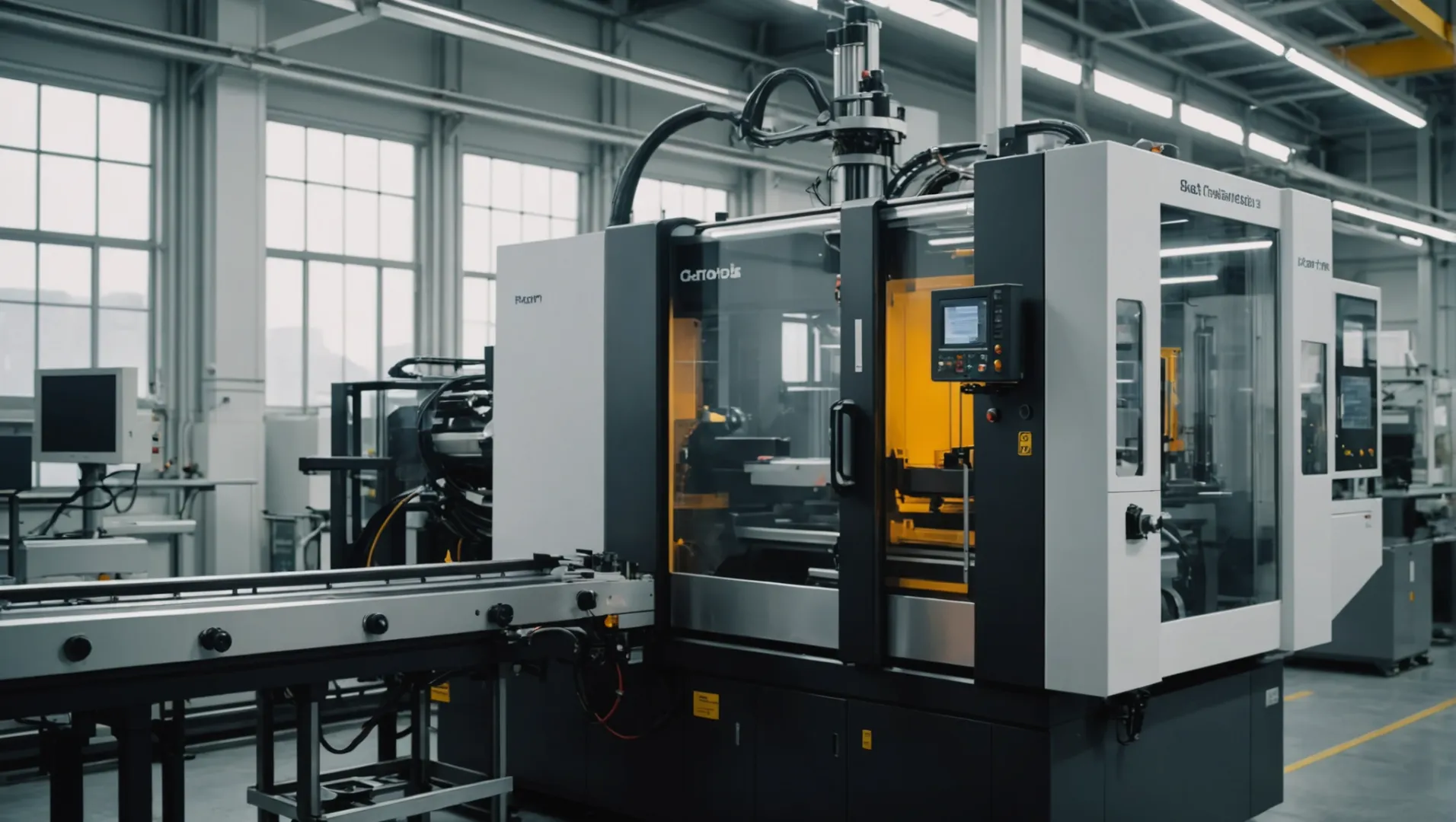
Understanding the Role of Injection Temperature
The injection temperature3 is a critical parameter affecting the transparency of molded parts. Higher temperatures increase the plastic’s fluidity, allowing it to flow more uniformly into the mold. This helps in minimizing the formation of bubbles and other defects that can cloud the material. However, excessively high temperatures can degrade the material, leading to discoloration or brittleness.
The Impact of Injection Pressure
Properly calibrated injection pressure ensures that the material fills the mold cavities completely and uniformly. High pressure enhances the material’s ability to penetrate complex mold geometries, reducing voids that compromise transparency. Nonetheless, extreme pressure can lead to flash or even damage the mold itself. It’s essential to strike a balance for optimal transparency.
Injection Speed Considerations
The speed at which material is injected into the mold also influences transparency. A slower injection speed may lead to premature cooling, causing incomplete fills and resulting in visible defects. Conversely, a too-fast injection can trap air within the mold, forming bubbles that obstruct clarity. Thus, moderating injection speed is essential for optimal results.
Optimizing Mold Temperature
Mold temperature has a direct effect on the cooling rate of the injected plastic. By increasing the mold temperature slightly, the material can remain molten longer, allowing it to fill even the most intricate parts of the mold without trapping air or creating surface defects.
Parameter | Effect on Transparency |
---|---|
Injection Temperature | Enhances flow; reduces bubbles; risk of degradation if too high |
Injection Pressure | Ensures full cavity fill; risk of flash if excessive |
Injection Speed | Balances fill time and defect prevention |
Mold Temperature | Controls cooling rate; prevents premature solidification |
By optimizing these parameters, manufacturers can significantly enhance the transparency of injection molded parts, making them suitable for demanding optical applications.
High injection temperature improves material flow.True
Higher temperatures increase fluidity, enhancing uniform mold filling.
Excessive injection pressure prevents flash formation.False
Too much pressure can cause flash, damaging the mold.
Why Is Mold Temperature Control Important for Transparency?
In the world of injection molding, achieving high transparency is vital, especially in applications demanding optical clarity.
Controlling mold temperature is crucial for transparency as it allows plastic to flow and fill molds smoothly, reducing defects and enhancing clarity.
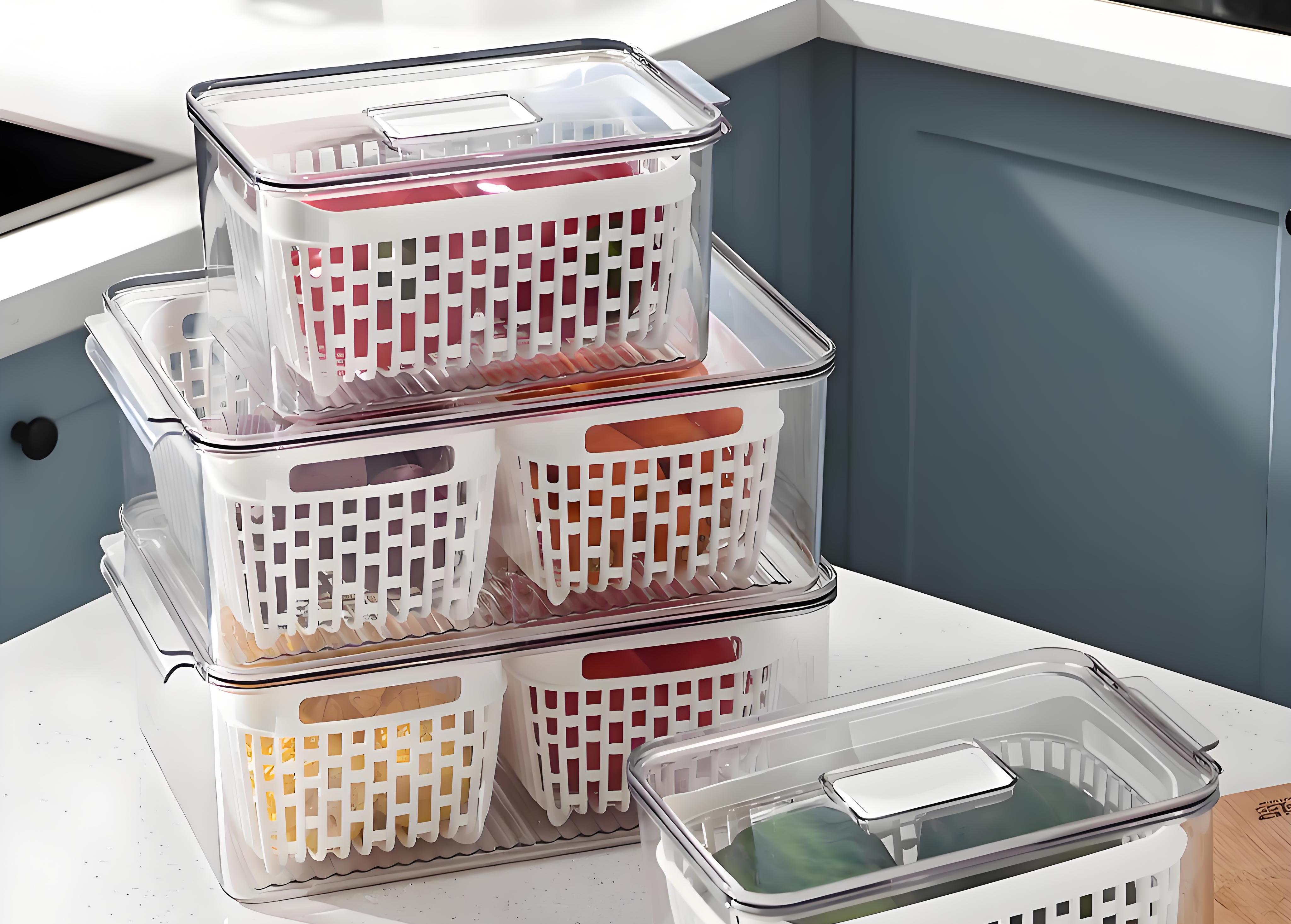
The Role of Mold Temperature in Injection Molding
Mold temperature significantly impacts the quality and transparency of injection molded parts. When molds are maintained at optimal temperatures, the plastic can flow more evenly, leading to a smoother surface finish and fewer internal defects. This process is essential for producing clear components like lenses or transparent casings.
Effects of Mold Temperature on Material Flow
A well-regulated mold temperature enhances the fluidity of materials such as polymethyl methacrylate (PMMA) and polycarbonate (PC), which are known for their high optical clarity. Higher mold temperatures slow down the cooling rate, allowing the plastic to maintain its molten state longer. This results in better filling of intricate mold geometries, reducing the likelihood of defects like weld lines and air bubbles, which can cloud transparency.
Mold Temperature | Effect on Transparency |
---|---|
Low | Increased defects, poor flow |
Optimal | Smooth flow, fewer defects |
High | Risk of degradation |
Balancing Temperature with Material Properties
While controlling mold temperature is vital, it must be carefully balanced with the properties of the material being used. For instance, excessively high temperatures can lead to thermal degradation of the polymer, causing yellowing or reduced mechanical properties. Therefore, understanding the thermal limits of your chosen material is crucial.
Practical Implementation Strategies
- Monitor and Adjust: Employ advanced monitoring systems to ensure consistent mold temperature throughout the molding cycle.
- Use of Thermal Insulators: Incorporating thermal insulators can help maintain stable temperatures and prevent heat loss.
- Integrating Cooling Channels: Properly designed cooling channels within the mold can aid in uniform temperature distribution.
By focusing on these strategies, manufacturers can significantly enhance the transparency of their injection molded products, ensuring superior quality and performance in applications where clarity is non-negotiable.
To explore more about achieving higher transparency in injection molded parts4, consider delving into advanced material science techniques and processing innovations.
Optimal mold temperature reduces transparency defects.True
Maintaining optimal mold temperature ensures smooth plastic flow, reducing defects.
High mold temperatures enhance material degradation risk.True
Excessively high temperatures can degrade polymers, affecting clarity and properties.
Can Additives Improve the Clarity of Molded Parts?
Exploring how additives can enhance the transparency of molded parts is crucial for achieving optimal clarity in manufacturing processes.
Additives like nucleating agents, plasticizers, and lubricants can significantly enhance the clarity of molded parts by improving the material’s crystallization and flow properties.
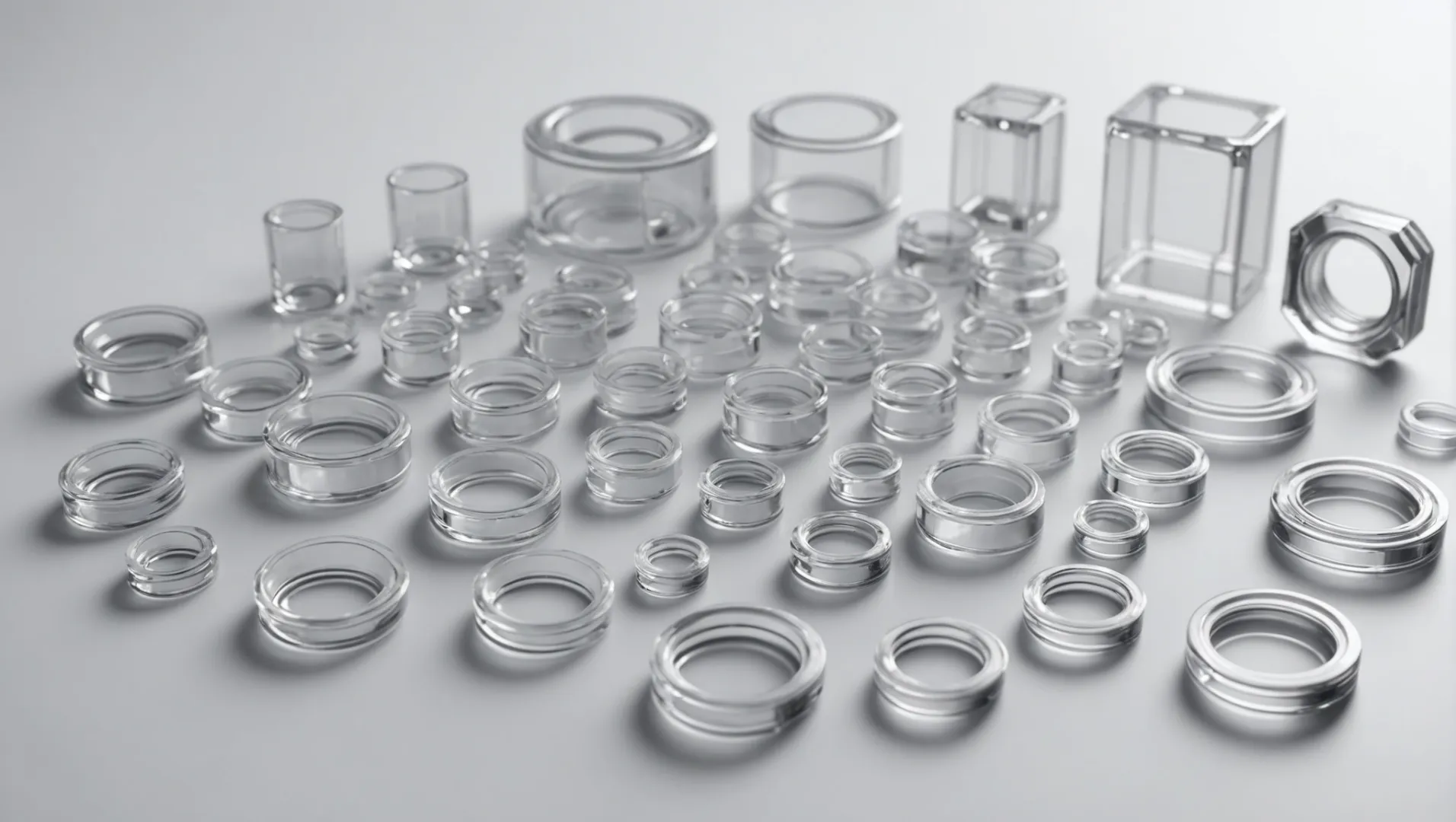
The Role of Nucleating Agents
Nucleating agents are essential additives that can promote crystallization5 within plastic materials. By enhancing the crystallization process, nucleating agents help in reducing spherulite size, resulting in clearer and more transparent molded parts. This improvement is particularly evident in materials like polypropylene, where transparency is not naturally high.
Benefits of Plasticizers
Plasticizers increase the flexibility and flow of plastic materials, which can significantly reduce the occurrence of defects during the molding process. This improved flow helps in achieving a smoother finish, thereby enhancing transparency. For instance, in PVC applications, plasticizers are often used to achieve a balance between flexibility and clarity.
The Impact of Lubricants
Lubricants help in reducing friction during the molding process. By lowering the resistance to flow, lubricants facilitate the even filling of molds, which is critical in achieving uniform clarity throughout the part. This results in fewer imperfections and bubbles, common challenges that reduce transparency.
Considerations and Cautions
While additives offer numerous benefits in improving clarity, it’s important to carefully consider the type and amount used. Excessive use of additives can lead to adverse effects such as reduced mechanical strength or unwanted discoloration. A thorough understanding of how each additive interacts with specific plastic materials is vital. Additionally, testing different combinations in a controlled environment can help determine the optimal mix for your specific needs.
For those interested in further exploring this topic, reviewing case studies where additives successfully enhanced product transparency can provide valuable insights into best practices and innovative solutions.
Nucleating agents reduce spherulite size in plastics.True
Nucleating agents promote crystallization, reducing spherulite size and enhancing clarity.
Excessive additives always improve molded part clarity.False
Too many additives can reduce mechanical strength or cause discoloration.
Conclusion
By applying these advanced techniques and considerations, I can enhance transparency and improve product quality. Reflecting on these strategies will help me optimize my processes for superior results.
-
Discover where polycarbonate’s transparency and durability are best utilized.: Polycarbonates and their blends are used in appliances, such as refrigerators, air conditioners, coffee machines, food mixers, washing machines, hair dryers … ↩
-
Learn about polystyrene’s cost-effective applications with good transparency.: Polystyrene is used across all industries, from toys and parts of consumer goods to insulation and packaging materials. It is also the … ↩
-
Discover how adjusting temperature improves flow and reduces defects.: Injection temperature. Injection temperature is appropriate for higher injection humidity on the premise that the plastic resin does not … ↩
-
Explore comprehensive methods for enhancing transparency in molded parts.: Check out the website for many great design tips that will help you with transparent injection molding or clear plastic injection molding. ↩
-
Understand how nucleating agents improve plastic clarity through crystallization.: The maximum possible crystallinity was between 53.9% and 60.0% for all the nucleated and plasticized PLA compounds. In every case, this crystallinity was higher … ↩