Have you ever struggled with annoying gate marks in injection molding? Many people face this problem. These small flaws impact the appearance of your products. Do not worry. I have some tips to help you handle them skillfully.
Grind gate marks manually or with machines. Use chemical methods. Better hot runner technology really helps. Change mold design. These ways probably reduce visible marks. This really improves how injection-molded products look.
Remember when I first tackled gate marks? I felt overwhelmed. Each method I tried taught me something new. Manual grinding, for example, feels satisfying. Sanding marks away on small plastic toys is rewarding. It takes time, but watching imperfections fade is satisfying.
Mechanical grinding offers precision and consistency. This method suits mass-produced items well. With the right tools, surfaces become smooth effortlessly. Chemical treatment is fascinating too. Experimenting with solvent wiping feels like magic. Marks disappear, but careful handling of solvents is essential.
Hot runner technology changed everything for me. Adjusting needle valve systems made high-end electronics flawless. Mold design optimization also stands out. Planning where to hide gates or adjusting angles is crucial. Thoughtful design makes a difference.
Each method has its own challenges and rewards. Overcoming these makes dealing with gate marks satisfying. These techniques truly transform ordinary products into exceptional ones.
Manual grinding is the most effective method for gate marks.False
While effective, manual grinding isn't always the best due to labor intensity.
Hot runner technology can reduce visible gate marks.True
Hot runner systems minimize material flow inconsistencies, reducing marks.
- 1. What are the Basics of Manual and Mechanical Grinding?
- 2. How Can Chemical Treatments Enhance Surface Quality?
- 3. How does hot runner technology help reduce gate marks?
- 4. How Can Mold Design Optimization Improve Product Aesthetics?
- 5. What Strategies Can Ensure Successful Project Outcomes Through Gate Reviews?
- 6. Conclusion
What are the Basics of Manual and Mechanical Grinding?
Ever looked at a bumpy surface and wished it felt soft like a baby’s cheek? Let’s explore the world of grinding. Both hand tools and machines offer something special.
Manual grinding uses tools like sandpaper. Start with rough grains and finish with smooth ones. It needs skill for small jobs. Mechanical grinding relies on machines. These machines offer efficiency and steadiness, good for making many items quickly.
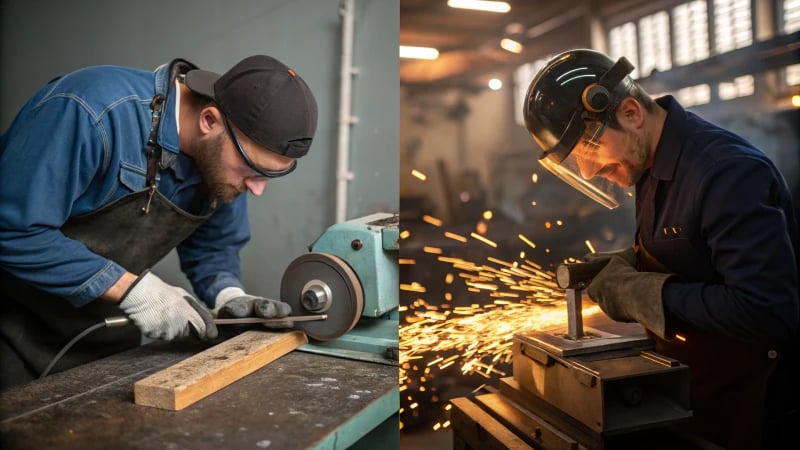
Understanding Manual Grinding
Manual grinding involves using hand tools like sandpaper or files to achieve desired surface finishes. Typically, this method starts with coarse grit sandpaper, such as 100-150 mesh, and gradually moves to finer grits like 400-600 mesh. This approach is often used in small-scale operations where high precision isn’t critical. For example, small plastic toys can be smoothed out manually to remove gate marks. However, it requires skilled workers as the final quality heavily depends on the operator’s expertise.
Manual Grinding | Characteristics |
---|---|
Tools Used | Sandpaper, Files |
Efficiency | Lower |
Skill Required | High |
Example | Small plastic toys |
Exploring Mechanical Grinding
Mechanical grinding leverages machines like grinders and polishers to perform tasks efficiently. These machines ensure consistency across batches, which is crucial in mass production settings. For instance, in the production of plastic shell products, machines equipped with automatic feeding devices can control grinding depth and speed precisely. Utilizing different particle sizes of abrasives can further enhance the surface finish quality.
Mechanical methods often involve advanced equipment1 which can be programmed for specific tasks, ensuring accuracy and uniformity.
Mechanical Grinding | Characteristics |
---|---|
Equipment Used | Grinders, Polishers |
Efficiency | Higher |
Consistency | High |
Example | Plastic shell products |
Safety Considerations and Applications
When engaging in either manual or mechanical grinding, safety is paramount. Protective gear such as gloves and goggles should always be used to prevent injuries. Additionally, understanding the specific applications of each grinding method can significantly improve the outcome. For example, while manual grinding suits smaller projects requiring a personal touch, mechanical grinding is best for large-scale production where uniformity is key.
The choice between manual and mechanical grinding ultimately depends on the project’s size, precision requirements, and resource availability. In scenarios where mass production2 is a priority, mechanical methods offer unmatched advantages in terms of speed and consistency.
Manual grinding requires high skill levels.True
Manual grinding depends on operator expertise for quality results.
Mechanical grinding is less efficient than manual.False
Mechanical grinding is more efficient, suitable for mass production.
How Can Chemical Treatments Enhance Surface Quality?
Ever thought about achieving flawless surfaces on your gadgets? That’s the wonder of chemical treatments!
Chemical treatments improve surface quality by melting materials, leading to smoother finishes. Solvent wiping and chemical polishing help remove gate marks, blending them perfectly with nearby surfaces. This process really enhances both appearance and function.
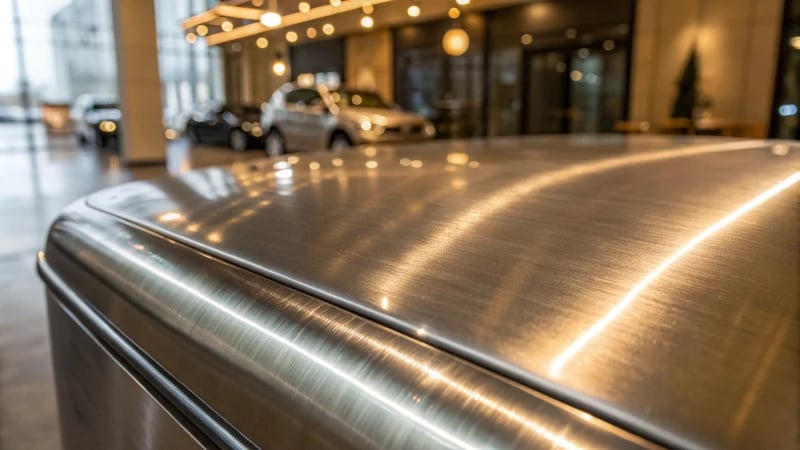
Solvent Wiping
Solvent wiping focuses on selecting the right organic solvent to fix imperfections. For instance, ABS plastic surfaces can be smoothed using acetone solution3. I gently wiped the gate marks with a cotton ball dipped in acetone, feeling like an artist smoothing a canvas. Yet, I had to avoid damaging other parts and being aware of environmental impact is crucial!
Plastic Type | Solvent | Application |
---|---|---|
ABS | Acetone | Gentle wiping on gate marks |
Chemical Polishing
Chemical polishing was another interesting technique I tried. It uses corrosive agents to make gate marks blend in perfectly with the surroundings. This involves a solution with polishing agents4 under controlled conditions, such as temperature and time, to prevent excessive corrosion. Adjusting things like temperature and time is critical to avoid too much corrosion.
- Chemical Agents: Corrosives and polishing fluids
- Temperature & Time: Important for preventing too much erosion
Efficiency and Application
I noticed chemical treatments help a lot in mass production where uniformity matters. In high-end electronics, these processes cut down many post-production steps by delivering nearly flawless finishes consistently.
Grinding Versus Chemical Treatment
Comparing grinding with chemical treatment was eye-opening. Manual and mechanical grinding improves surfaces but doesn’t match the precision of chemical methods. Integrating both methods can optimize surface quality.
- Manual Grinding: Uses sandpaper from coarse to fine
- Mechanical Grinding: Uses machines for uniform treatment
By combining these techniques, manufacturers meet both beauty and durability needs, making products strong and attractive in many industries. Trying different solvents and polishing agents opened more doors for better surface quality. Exploring solvent options5 can help find the right choice for specific materials and outcomes.
Solvent wiping only works on ABS plastic surfaces.False
Solvent wiping can be applied to various plastics, not just ABS.
Chemical polishing requires controlled temperature and time.True
Proper parameter control prevents excessive corrosion during polishing.
How does hot runner technology help reduce gate marks?
Curious about how we get those smooth and perfect surfaces on plastic items? Hot runner technology works like magic to lessen gate marks.
Hot runner technology is very important in injection molding. This system helps reduce gate marks by keeping the temperature and pressure steady. Needle valve systems and specially designed gates give smoother surfaces. These features decrease the need for extra work after molding.
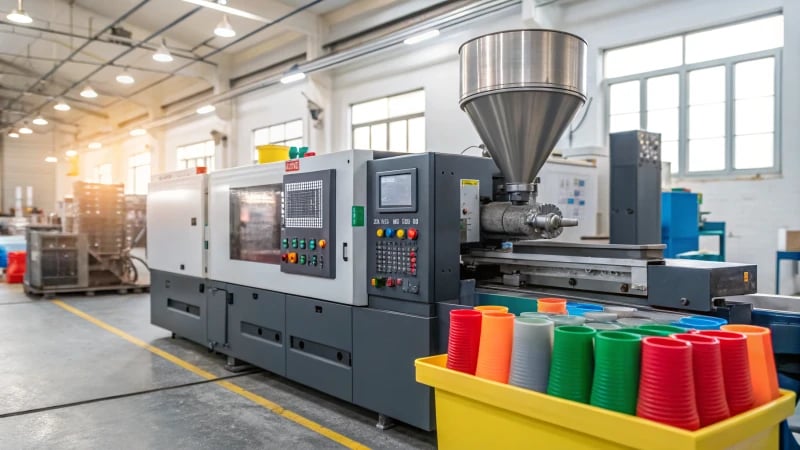
Understanding Hot Runner Technology
When I first saw hot runner technology, its complexity and efficiency impressed me. Hot runners keep the plastic liquid until it forms the shape, unlike cold runners that leave extra material you need to trim away. Picture baking a cake where the batter is smooth and nothing sticks to the bowl. That’s the kind of precision here.
The Mechanism Behind Reducing Gate Marks
In the beginning of my work with injection molds, I realized controlling temperature is crucial. Hot runners offer perfect control to keep the plastic flowing smoothly and reduce gate marks. It’s like pouring chocolate into a mold; if it’s too cool, it doesn’t fill evenly. Implementing needle valve systems6 provides additional control, making gate marks nearly invisible.
Types of Hot Runner Improvements
- Needle Valve Hot Runner Point Gate: Remember when I saw this system? It felt like magic watching it shape the gate so precisely. This system creates a sleek look found in expensive gadgets.
- Hot Gate Optimization Design: Tools like computer simulations are like being a plastic wizard, adjusting temperature and flow to perfect designs and hide marks.
Practical Benefits for Manufacturers
Using these technologies changed everything for us. Really changed everything.
Benefits | Description |
---|---|
Enhanced Aesthetics | Smoother product surfaces with reduced gate marks |
Efficiency | Reduced need for manual grinding7 and post-processing |
Cost Reduction | Less material waste due to efficient flow and reduced trimming |
Considerations and Challenges
Of course, challenges exist. Careful planning of mold design is vital for success with hot runners. It’s like planning a road trip; you need to know the stops for a smooth journey. Adjusting gate positions and angles is crucial in reducing gate mark visibility.
Let’s also think about chemical treatments8 I’ve tried, like solvent wiping or chemical polishing. These improve product looks with little manual work.
Future of Hot Runner Technology
After watching technology grow over the years, I feel excited about future hot runner advances. Faster cycles and better material use sound very promising. The future looks bright for making even smoother and more attractive products.
Hot runners eliminate gate marks completely.False
Hot runners minimize but do not completely eliminate gate marks.
Needle valves help control plastic flow in hot runners.True
Needle valves regulate flow, reducing gate marks in hot runner systems.
How Can Mold Design Optimization Improve Product Aesthetics?
Do you ever think about why certain products appear much nicer than others?
Mold design optimization improves how products look by positioning gates carefully. Hot runner technology helps in this process. Surface treatments are also applied. These steps reduce visible flaws on molded parts. They really make components look better. The final appearance matches what consumers want.
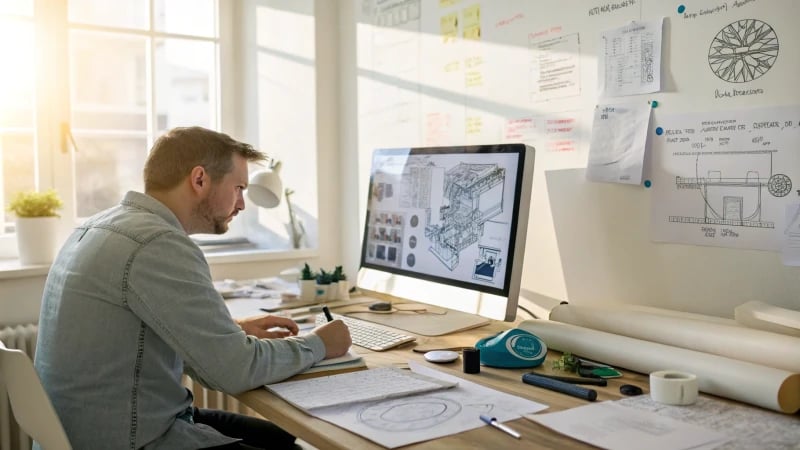
Strategic Gate Positioning
Imagine this: designing a fancy new device and wanting to hide any plastic entry marks. By placing gates9 in less noticeable spots, like the inside or edges, designers can minimize the impact of gate marks. I once worked on a design where smart gate placement led to a perfect flow of material. The result was a smooth surface without any visible marks. Very smooth.
Hot Runner Technology Improvements
Learning about advanced hot runners felt like discovering a new trick in a game. Utilizing advanced hot runner systems, like needle valve point gates, effectively reduces gate marks greatly, sometimes even removing them. It’s like gaining the ability to control gate size and shape. Using simulation software10, I adjusted the setup even more. The surface stayed clean and flawless.
Technology | Benefits |
---|---|
Needle Valve Hot Runner | Minimizes gate marks |
Simulation Software | Optimizes gate design |
Seeing these changes succeed on high-quality electronic shells is very exciting. Attention to detail is key.
Surface Treatment Methods
Surface treatments give products a fresh look, almost like a relaxing day at a spa. Machines grind for accuracy and evenness, while hands polish for finer touches. I watched an expert carefully improve a small toy, turning it into something special. Chemical ways, like solvent wiping and chemical polishing, can fix small flaws but require careful consideration of material safety and environment.
Considerations such as material compatibility and environmental impact are crucial when selecting a chemical treatment11.
Expanding Gate Distribution
For big or intricate designs, adding more gates works wonders. It’s like dividing tasks among a group, reducing strain on each entry point. Less pressure leaves fewer marks. We tried this on big plastic sheets and it worked great.
In large component manufacturing12, spreading gates all over the surface improved the overall finish.
Using these methods together optimizes mold design way beyond average expectations. The blend of creativity and technical skill is both demanding and fulfilling. It’s really fascinating.
Strategic gate positioning reduces visible defects.True
Correctly positioned gates minimize visible marks, enhancing aesthetics.
Needle valve hot runners increase gate marks.False
Needle valve systems reduce gate marks, improving product appearance.
What Strategies Can Ensure Successful Project Outcomes Through Gate Reviews?
Have you ever felt that your project was going in the wrong direction? Gate reviews could be your hidden tool.
Successful project results through gate reviews depend on clear standards, active involvement of stakeholders, careful data examination and flexible decision-making. Structured processes help the team. Communication plays a key role. Projects match their goals perfectly.
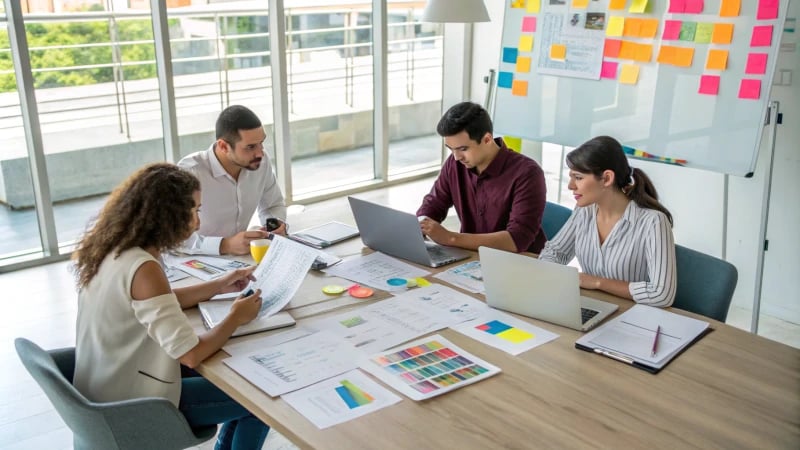
Understanding Gate Reviews in Project Management
Picture steering a ship through unknown seas. Project management feels like this. Gate reviews serve as my checkpoints, guiding me through the mist. They really matter for checking progress and confirming we’re following the right path to reach our important goals.
Key Strategies for Successful Gate Reviews
Clear Goals and Objectives
I learned that clarity means everything. Setting specific objectives and targets13 for each gate feels like drawing a map. This map guides everyone and shows progress.
Stakeholder Involvement
Involving everyone is like inviting different views to the table. Stakeholders notice risks and chances we might miss. Their insights shape our journey.
Detailed Data Review
Data acts as our compass. By studying metrics and indicators, I notice trends and adjust plans before drifting too far. It’s like changing direction based on weather reports.
Metric | Description |
---|---|
Trends | Observing patterns in data to guide decisions |
Adjustments | Modifying plans based on new insights |
Indicators | Key performance measures to track progress |
Adaptable Decision-Making
A structured plan keeps us steady, but sometimes winds change suddenly. Adaptability allows quick adjustments to keep the project focused on main goals.
Building Structured Processes
Creating a standardized framework is like building a strong base for the ship. It defines roles, duties, and timelines but stays flexible for various projects.
This involves setting up a standardized framework14 that outlines roles, responsibilities, and timelines adaptable to different project types.
Good Communication Practices
Regular updates and feedback are like the continuous sound of a ship’s radio. They keep everyone informed about changes and progress, ensuring we’re all heading in the same direction.
Establishing regular updates ensures all stakeholders are informed about project developments and any changes in direction.
Using these strategies, gate reviews become valuable for managing complex projects successfully. They help meet goals while facing challenges. It’s about understanding these details to lead projects toward success.
Gate reviews are only for financial assessment.False
Gate reviews assess multiple aspects, including progress, risks, and alignment.
Stakeholder engagement enhances gate review decisions.True
Involving stakeholders provides diverse insights, improving decision quality.
Conclusion
This article provides effective strategies for handling gate marks in injection molding, including grinding techniques, chemical treatments, hot runner technology, and mold design optimization to enhance product appearance.
-
Discover how modern grinding machines improve efficiency and precision in manufacturing processes. ↩
-
Learn why mechanical grinding is preferred for large-scale operations requiring uniform results. ↩
-
Discover why acetone is an effective solvent for smoothing ABS plastic surfaces. ↩
-
Learn about different agents used in chemical polishing and how they enhance surface quality. ↩
-
Explore various solvents suitable for treating different types of plastics effectively. ↩
-
Discover how needle valve systems enhance precision in injection molding, minimizing gate marks. ↩
-
Compare manual grinding techniques with hot runner benefits to understand efficiency improvements. ↩
-
Learn about chemical treatments that complement hot runner technology in reducing gate marks. ↩
-
Explore how strategic gate placement minimizes visible imperfections, improving product aesthetics. ↩
-
Discover top simulation tools that help in designing efficient hot runner systems to reduce defects. ↩
-
Learn how chemical treatments enhance surface quality by removing imperfections. ↩
-
Understand methods to minimize gate marks when manufacturing large components. ↩
-
Understanding clear criteria ensures that all team members align with project objectives, making reviews more productive. ↩
-
A standardized framework aids in streamlining processes, ensuring consistency across various projects. ↩