For designers like Mike in the plastic manufacturing industry, choosing the right molding process is crucial.
Insert molding embeds a preformed part within molded material, while overmolding applies additional layers to an existing part for enhanced functionality or aestheticas.
While both insert molding and overmolding offer unique advantages, understanding their distinct processes and applications can significantly impact product design and manufacturing efficiency. Letโs delve deeper into each method to uncover their potential benefits and decide which is more suitable for your next project.
Insert molding embeds parts before adding material.True
Insert molding integrates a preformed part within the mold before additional material is added.
Overmolding cannot improve product aesthetics.False
Overmolding enhances aesthetics by layering material over an existing part.
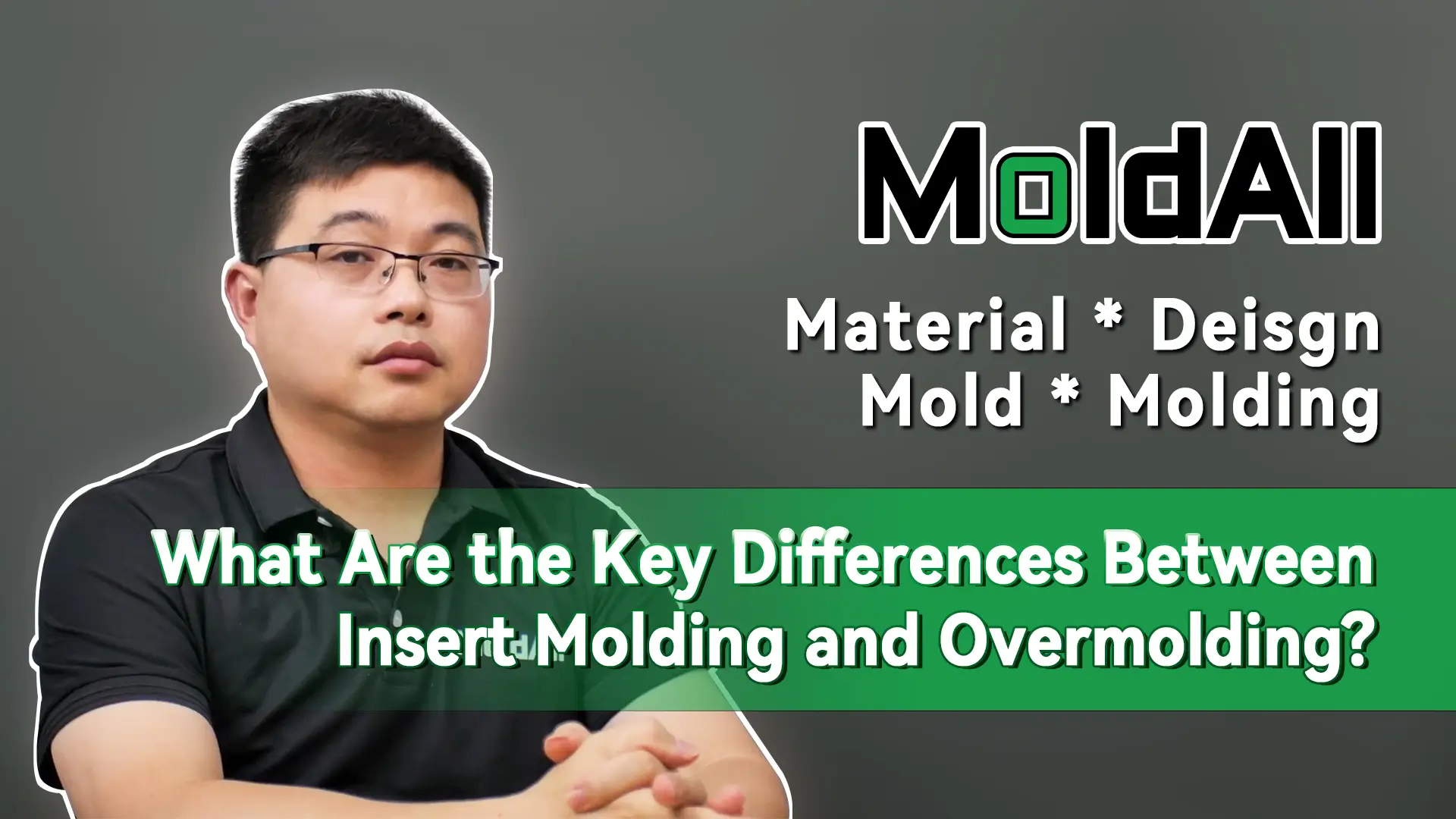
- 1. How Does Insert Molding Work and What Are Its Advantages?
- 2. What Is Overmolding and When Should It Be Used?
- 3. What Are the Common Applications of Insert Molding and Overmolding?
- 4. How Do You Decide Between Insert Molding and Overmolding for Your Project?
- 5. What Are the Cost Implications of Using Insert Molding vs. Overmolding?
- 6. Conclusion
How Does Insert Molding Work and What Are Its Advantages?
Insert molding is a powerful manufacturing process combining metal or other components within molded plastic, enhancing product functionality and reducing assembly time. Understanding its intricacies can optimize design and production.
Insert molding involves embedding materials like metal into plastic during molding, enhancing strength, reducing assembly time, and boosting functionality over traditional methods.
The Insert Molding Process
Insert molding involves placing a pre-formed component, typically made of metal, into the mold cavity before the injection of plastic. The plastic then surrounds the insert, embedding it securely within the final product. This process allows for the integration of multiple materials, improving both functionality and durability.
Step-by-Step Breakdown
- Design Phase: Engineers design both the mold and insert1 to ensure a seamless fit.
- Insert Placement: The insert is accurately positioned within the mold cavity.
- Injection: Molten plastic is injected into the mold, encapsulating the insert.
- Cooling: The mold cools, solidifying the plastic around the insert.
- Ejection: The finished part is ejected, revealing a robust composite component.
Advantages of Insert Molding
Insert molding offers several benefits over traditional assembly methods:
Advantage | Description |
---|---|
Cost Efficiency | Reduces labor costs by eliminating secondary assembly operations. |
Enhanced Strength | Provides additional structural integrity by bonding materials together during molding. |
Design Flexibility | Enables complex designs that incorporate multiple materials or features in a single step. |
Compact Design | Allows for smaller product footprints by integrating components directly into the mold. |
Applications Across Industries
This method is particularly advantageous in industries requiring precise and durable components:
- Consumer Electronics: Inserts are often used in products needing electrical contacts or threaded inserts.
- Automotive: Components like gears and bushings benefit from the added strength of insert molding.
- Medical Devices: Ensures the integrity and safety of devices by securely embedding necessary components.
Considerations for Designers
For designers like Mike, understanding these benefits can help optimize product designs for both performance and manufacturability. Collaborating closely with mold designers during the early stages of product development can lead to more effective use of insert molding techniques. Itโs crucial to consider material compatibility2 to avoid issues like thermal expansion or chemical interactions between the insert and plastic.
The importance of choosing the right insert material cannot be overstated; factors such as durability, conductivity, and weight will influence the final productโs performance. Exploring these options with a focus on specific application needs ensures that insert molding delivers its full potential.
Insert molding reduces assembly time significantly.True
Insert molding eliminates the need for secondary assembly operations, saving time.
Insert molding is only used in the automotive industry.False
Insert molding is used in various industries, including electronics and medical devices.
What Is Overmolding and When Should It Be Used?
Curious about overmolding? This versatile manufacturing process can revolutionize product design by combining multiple materials. Dive in to explore how it enhances functionality and aesthetics.
Overmolding involves molding one material over another for enhanced grip, aesthetics, or functionality. Itโs ideal for use in electronics, tools, and automotive industries.
Understanding the Basics of Overmolding
Overmolding involves injecting a secondary material over a substrate, which could be metal or plastic. This technique allows designers to create complex, multi-material products without the need for additional assembly. One classic example is creating a toothbrush with a soft grip handle.
Benefits of Overmolding
- Enhanced Grip: Soft materials like thermoplastic elastomers (TPE) can be overmolded onto hard plastic to improve grip.
- Aesthetic Appeal: Multiple colors or textures can be achieved, enhancing the visual appeal3 of a product.
- Added Functionality: Overmolding can provide electrical insulation or waterproofing.
Applications of Overmolding
Industry | Common Use Case |
---|---|
Electronics | Soft-touch buttons |
Automotive | Seals and gaskets |
Consumer Goods | Ergonomic handles on tools |
Each application leverages overmoldingโs ability to combine materials seamlessly, offering both functional and aesthetic improvements.
Design Considerations for Overmolding
- Material Compatibility: Choose materials that bond well together to avoid delamination.
- Mold Design: Accurate CAD models4 are essential for precise mold creation.
- Cost Implications: While overmolding can add costs, it reduces the need for post-processing or additional assembly steps.
Understanding material compatibility5 and selecting the right design approach can lead to successful overmolded products, offering significant value in diverse applications.
Overmolding is used to create toothbrush grips.True
Toothbrushes often use overmolding for soft grip handles.
Overmolding cannot provide waterproofing.False
Overmolding can add waterproofing by using appropriate materials.
What Are the Common Applications of Insert Molding and Overmolding?
Insert molding and overmolding revolutionize how components are manufactured, seamlessly integrating multiple materials for enhanced functionality and aesthetics. But what makes these processes so widely utilized across various industries?
Insert molding and overmolding enhance product durability and aesthetics by integrating metals or adding layers in plastics, commonly used in electronics and medical devices.
Electronics: Crafting Precision and Functionality
In the electronics industry, both insert molding and overmolding are pivotal. Insert molding is used to securely encase delicate circuits within durable plastic housings6, ensuring longevity and protection from external factors. This process is ideal for crafting connectors that require a combination of metal and plastic components.
Overmolding, on the other hand, allows manufacturers to create user-friendly grips on devices like remote controls or game controllers by layering softer materials over hard plastics. This not only enhances comfort but also provides an aesthetically pleasing finish that is crucial in consumer electronics.
Medical Devices: Ensuring Safety and Efficiency
In the medical field, insert molding is often used to embed needles or other metal components within plastic, creating safe, single-use devices like syringes. The technique ensures that these components remain sterile and secure within their plastic casings7.
Overmolding is equally significant here, offering ergonomic designs for medical tools that require precision handling. By using softer, non-slip materials as outer layers, these tools ensure a better grip for healthcare professionals, enhancing both safety and efficiency.
Automotive Industry: Merging Strength and Flexibility
Automotive applications benefit greatly from these techniques. Insert molding creates robust dashboard components8 by incorporating metal inserts for added strength where needed.
Meanwhile, overmolding is used to improve the tactile feel and aesthetics of interior elements such as steering wheels and gear knobs. By applying softer materials over rigid structures, manufacturers can offer enhanced comfort and luxury appeal to consumers.
Application Area | Insert Molding | Overmolding |
---|---|---|
Electronics | Circuit Encapsulation, Connectors | Device Grips |
Medical Devices | Syringe Production, Secure Components | Ergonomic Tool Design |
Automotive | Dashboard Strengthening | Steering Wheel Comfort |
Consumer Goods: Enhancing Everyday Products
Beyond industrial uses, these techniques also revolutionize consumer goods. Insert molding helps in crafting durable kitchen tools by combining metals with plastics, while overmolding provides grip-enhanced handles on utensils, making them user-friendly.
The diversity of applications showcases the versatility of both processes in producing high-quality, durable products across industries. Discover more9 about how these processes innovate product design today.
Insert molding is used for creating ergonomic grips.False
Insert molding is primarily for embedding components; overmolding creates ergonomic grips.
Overmolding enhances the aesthetics of steering wheels.True
Overmolding adds softer materials to improve feel and appearance of steering wheels.
How Do You Decide Between Insert Molding and Overmolding for Your Project?
Choosing between insert molding and overmolding can be pivotal for your projectโs success. Each technique offers distinct advantages, affecting cost, production speed, and product functionality. Understanding these differences is crucial for optimizing your manufacturing process.
Choose between insert molding and overmolding by evaluating material compatibility, design complexity, production volume, and desired functionality, as both offer unique benefits tailored to specific project needs.
Understanding Insert Molding and Overmolding
Insert Molding involves encapsulating a pre-placed insert (often metal) within molten plastic. This method is ideal when you need added strength and conductivity in the final product. On the other hand, Overmolding adds layers of materials over a base part, offering enhanced ergonomics and aesthetics.
Aspect | Insert Molding | Overmolding |
---|---|---|
Key Benefit | Combines materials for strength and durability | Offers versatility in design and touch-feel |
Ideal For | Electrical parts needing conductive properties | Handheld devices requiring a soft grip |
Key Considerations for Your Decision
-
Material Compatibility: Evaluate whether the materials you are using can successfully bond in either method. Some materials10 are better suited for insert molding due to their heat-resistant properties.
-
Design Complexity: Insert molding often requires simpler designs since the inserts must fit precisely within the mold. Overmolding allows for more complex designs since it can be layered over existing structures.
-
Production Volume: If you expect high-volume production, consider the speed and cost-efficiency of each method. Insert molding may have higher initial costs but can be more cost-effective in the long run for mass production.
-
Desired Functionality: Consider the end-use of your product. For example, if tactile feel or color variation is important, overmolding11 offers greater flexibility in these areas.
Practical Examples
- Consumer Electronics: Insert molding is often used in electronic connectors to integrate metal components for improved conductivity.
- Automotive Parts: Overmolding might be chosen for dashboard components to provide a softer finish.
By analyzing these factors, youโll be better equipped to choose the technique that aligns with your project requirements12. Each methodโs unique benefits can enhance different aspects of your product, from strength to user interaction.
Insert molding is ideal for complex designs.False
Insert molding suits simpler designs due to precise insert placement.
Overmolding enhances tactile feel of products.True
Overmolding adds layers that improve ergonomics and touch-feel.
What Are the Cost Implications of Using Insert Molding vs. Overmolding?
Choosing between insert molding and overmolding can significantly impact manufacturing costs. Understanding these implications helps designers optimize budgets and timelines while meeting production goals efficiently.
Insert molding generally has lower tooling costs but may need more labor. Overmolding incurs higher initial mold costs but offers reduced assembly time and enhanced product durability.
Understanding Insert Molding Costs
Insert molding involves placing a pre-made component, such as a metal or plastic piece, into a mold before injecting plastic around it. This method often results in lower tooling costs. However, there might be increased labor expenses for manually placing13 the inserts, especially in low-volume productions.
Key Cost Factors:
- Tooling: Generally cheaper due to simpler mold designs.
- Labor: Potentially higher as manual insertion is required.
- Material: Costs depend on the insert material used.
Cost Element | Insert Molding |
---|---|
Tooling | Lower |
Labor | Higher |
Material | Variable |
Analyzing Overmolding Expenses
Overmolding involves creating a single part using multiple materials. The initial tooling costs are typically higher due to the need for more complex mold designs that can accommodate multiple material layers. However, this method can streamline production by eliminating14 post-production assembly, potentially saving on labor costs.
Key Cost Factors:
- Tooling: Higher due to complexity.
- Labor: Lower as it reduces assembly time.
- Material: Requires careful selection to ensure compatibility.
Cost Element | Overmolding |
---|---|
Tooling | Higher |
Labor | Lower |
Material | Compatibility |
Factors Influencing Choice
-
Production Volume: For high volumes, the initial investment in overmolding may be justified by long-term savings in assembly and labor.
-
Product Design Complexity: Insert molding might be more cost-effective for simpler designs or when using high-value inserts that are difficult to bond reliably.
In conclusion, understanding these aspects can help you make a more informed decision between these two methods, optimizing both cost and efficiency in your projects. Consider reading more about the tooling and labor implications15 for deeper insights into cost management strategies in molding processes.
Insert molding has lower tooling costs than overmolding.True
Insert molding typically requires simpler mold designs, reducing tooling costs.
Overmolding increases labor costs due to complex assembly.False
Overmolding reduces labor costs by eliminating post-production assembly steps.
Conclusion
Insert molding embeds pre-formed parts within plastic, enhancing strength and reducing assembly time, while overmolding layers materials for improved aesthetics and functionality. Both processes serve diverse industrial applications.
-
Explore different strategies for designing molds that accommodate inserts, improving accuracy and efficiency.ย โฉ
-
Learn about material compatibility to ensure successful bonding and avoid issues like thermal expansion.ย โฉ
-
Learn how overmolding enhances product design through aesthetic improvements, offering insights into color and texture applications.ย โฉ
-
Discover why precise CAD models are critical in designing molds for overmolding, ensuring high-quality production results.ย โฉ
-
Explore key factors in material compatibility for successful overmolding, preventing issues like delamination.ย โฉ
-
Learn how insert molding protects sensitive electronics, ensuring durability and performance.ย โฉ
-
Explore how insert molding is crucial for producing safe and sterile medical instruments.ย โฉ
-
Understand the role of insert molding in enhancing automotive component durability.ย โฉ
-
Discover the versatility of overmolding in enhancing everyday consumer goods.ย โฉ
-
Learn about materials that excel in insert molding, ensuring strong bonds and durability.ย โฉ
-
Discover why overmolding can enhance product functionality through improved design and aesthetics.ย โฉ
-
Understand how different molding methods meet varied project needs and specifications.ย โฉ
-
Explore how manual insertion impacts labor costs in insert molding.ย โฉ
-
Learn how overmolding can streamline production by reducing assembly time.ย โฉ
-
Gain insights into managing tooling and labor costs effectively in molding processes.ย โฉ