Have you ever wondered how the smallest details in molding could drastically affect a product’s quality?
Optimal gate location and size in injection molding are crucial for minimizing defects, ensuring effective filling, and influencing stress distribution and molecular orientation, directly affecting the product’s appearance, functionality, and strength.
When I first started learning about injection molding, I was very surprised by how much gate placement influenced the final product. It’s not just about putting a gate anywhere. Choosing the right spot is very important for both appearance and function. I discovered this the hard way while designing a transparent ornament. The gate sat right in the front, leaving an ugly mark that spoiled the clean look I really wanted.
Gate position also affects how stress spreads through the product. I recall a project where bad gate placement caused cracks. Stress concentrated in certain areas. These problems taught me that the right gate size and location are crucial. A gate that is too big or too small can cause flow marks or incomplete fills.
Understanding these small details changes how a product works and looks. This makes a big difference in a competitive market. So, whether you are designing a new gadget or trying to avoid annoying flow marks, remember that every choice matters in molding.
Gate size affects product strength in injection molding.True
Larger gates facilitate better flow, reducing stress concentration and enhancing strength.
Gate location does not impact product appearance.False
Incorrect gate placement can lead to visible defects such as flow lines.
How Do Gate Marks Affect Product Appearance?
Have you ever seen those annoying gate marks spoiling your product’s perfect finish? They really change transparency and gloss. Let’s explore how they do this and what steps we might take to fix it.
Gate marks are flaws from molding that harm a product’s look. They ruin transparency, gloss and smoothness. Right gate size and position are very important. This choice helps reduce these problems.
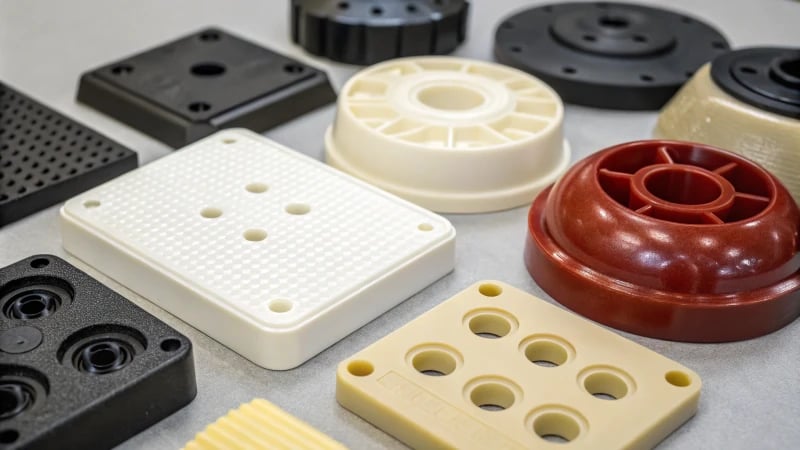
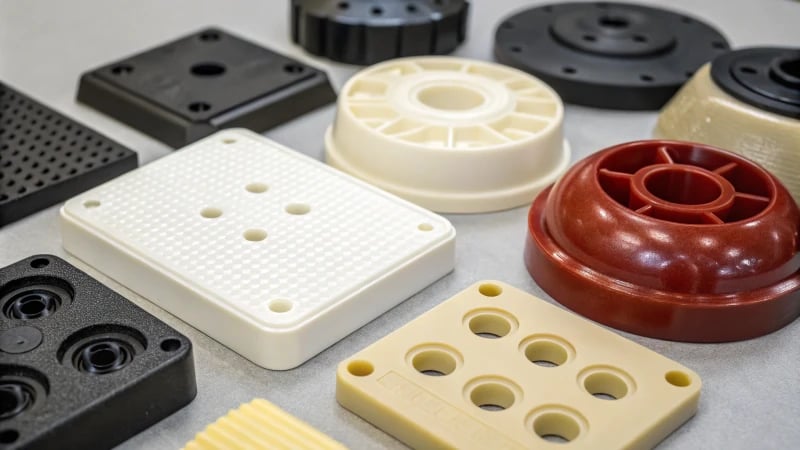
Appearance Performance
I remember noticing gate marks on a cherished project. It was a detailed clear ornament. A gate mark spoiled the transparency right in the center. This taught me how important gate placement1 is. When put in the wrong place, these marks can dull a product’s shine and gloss.
Gate Size | Effect on Appearance |
---|---|
Large | More prominent mark; affects gloss |
Small | Less noticeable; risk of insufficient filling |
Weld Marks and Flow Marks
I learned the hard way that the wrong gate spot leads to other issues. It causes weld marks too. Imagine designing with many holes and finding ugly weld marks where paths meet. Proper gate placement is crucial for a smooth finish.
- Flow Marks: Gate size is very important here. If too large, flow may slow down and cause stagnation. If too small, it might create erratic patterns.
Mechanical Properties Impact
Gate marks affect more than just looks. I noticed this when a product started cracking. Stress concentrated around the center was the reason. It highlighted how much gate location2 affects stress distribution and molecular orientation.
- Residual Stress: Different gate sizes can either reduce or increase stress problems, affecting product strength and stability.
- Molecular Orientation: In crystalline plastics, gate placement changes crystallinity, which impacts both density and hardness.
Molding Performance
Picking the right gate isn’t only about appearance; it’s about performance too. A badly placed gate leads to problems in filling thin sections, resulting in short shots. Correct positioning ensures even filling, which is crucial for maintaining structural strength.
Parameter | Impact |
---|---|
Gate Position | Affects fill in thin/complex areas |
Gate Size | Influences flow rate and melt flow |
I noticed large gates complicate demolding by increasing adhesion. Finding the balance between size and position is key as it optimizes aesthetics and functionality. Mastering this balance greatly improves product quality.
Explore more about molding performance3 to enhance your design strategies and production processes.
Large gates reduce gloss in molded products.True
Large gates leave prominent marks that diminish surface gloss.
Small gates cause more noticeable weld marks.False
Small gates are less likely to cause noticeable weld marks.
How Do Weld and Flow Marks Develop in Injection Molding?
At first, I saw weld and flow marks in injection molding. Solving this mysterious puzzle felt challenging. These marks probably affected the beauty of my creations. The function of my creations also suffered.
Weld marks happen when melted plastic fronts touch but do not fully combine. Flow marks appear because of uneven flow speeds. To lessen these flaws, one must change the gate position. Adjusting its size is also crucial.
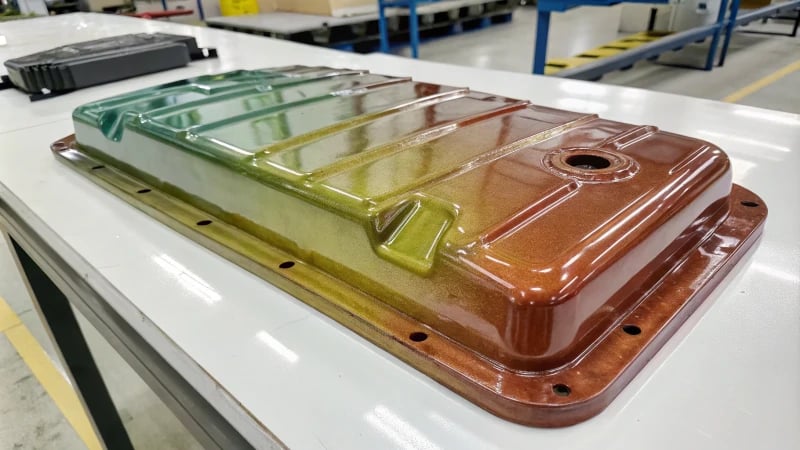
Understanding the Role of Gate Position
I remember the first time I learned how important gate position really is. I was working on a complicated design with many details, and troublesome weld marks were everywhere. I realized that bad gate placement caused these flow fronts to collide instead of merging smoothly. It’s like planning a trip without thinking about traffic – it just doesn’t work well.
In products with complex shapes or many ribs, placing a gate in the wrong spot can increase these weld marks. This affects both the appearance and the product’s performance.
Factors | Impact on Weld Marks |
---|---|
Gate Location | Poor positioning increases weld marks |
Gate Size | Smaller gates may fail to fill complex areas |
Gate Size and Flow Consistency
I discovered that gate size truly affects the flow consistency of molten plastic. Think about pouring syrup through a straw versus a wide jar – it’s the same idea here. A gate that’s too big might let the plastic move slowly, causing surface marks. Meanwhile, a tiny gate can create chaotic flow patterns, making the surface look like a toddler’s crayon drawing.
These problems impact not only looks but also strength. Uneven stress from poor gate design can weaken the product, like a mismatched puzzle piece disrupting the whole image.
Optimizing Gate Design for Better Molding Performance
I found that changing gate position and size could greatly improve results. Placing gates strategically for smooth flow paths and picking the right size prevents overflow. This approach improved both filling and removal stages.
- Position: Place gates where they support smooth flow paths, avoiding complex features.
- Size: Choose a size that balances sufficient flow without causing overflow or flash.
For example, placing gates near thin areas prevents short shots and guarantees full filling. It’s about finding the perfect spot where looks and function meet.
Learn more about gate design considerations4 to improve your molding process efficiency.
Improper gate position increases weld marks.True
Poorly positioned gates lead to flow separation and reconvergence, causing weld marks.
Large gate size always prevents flow marks.False
Large gates can cause slow melt flow, leading to stagnation and surface marks.
How Do Gate Parameters Affect Mechanical Properties?
Have you ever thought about how the smallest design choices actually change a product? Let’s explore gate parameters and their effect on mechanical properties.
Gate parameters, like position and size, are very important. They shape mechanical properties. These factors influence flow patterns, stress distribution and molecular orientation. Adjusting parameters changes strength, appearance and product performance. Improving a product this way is essential.
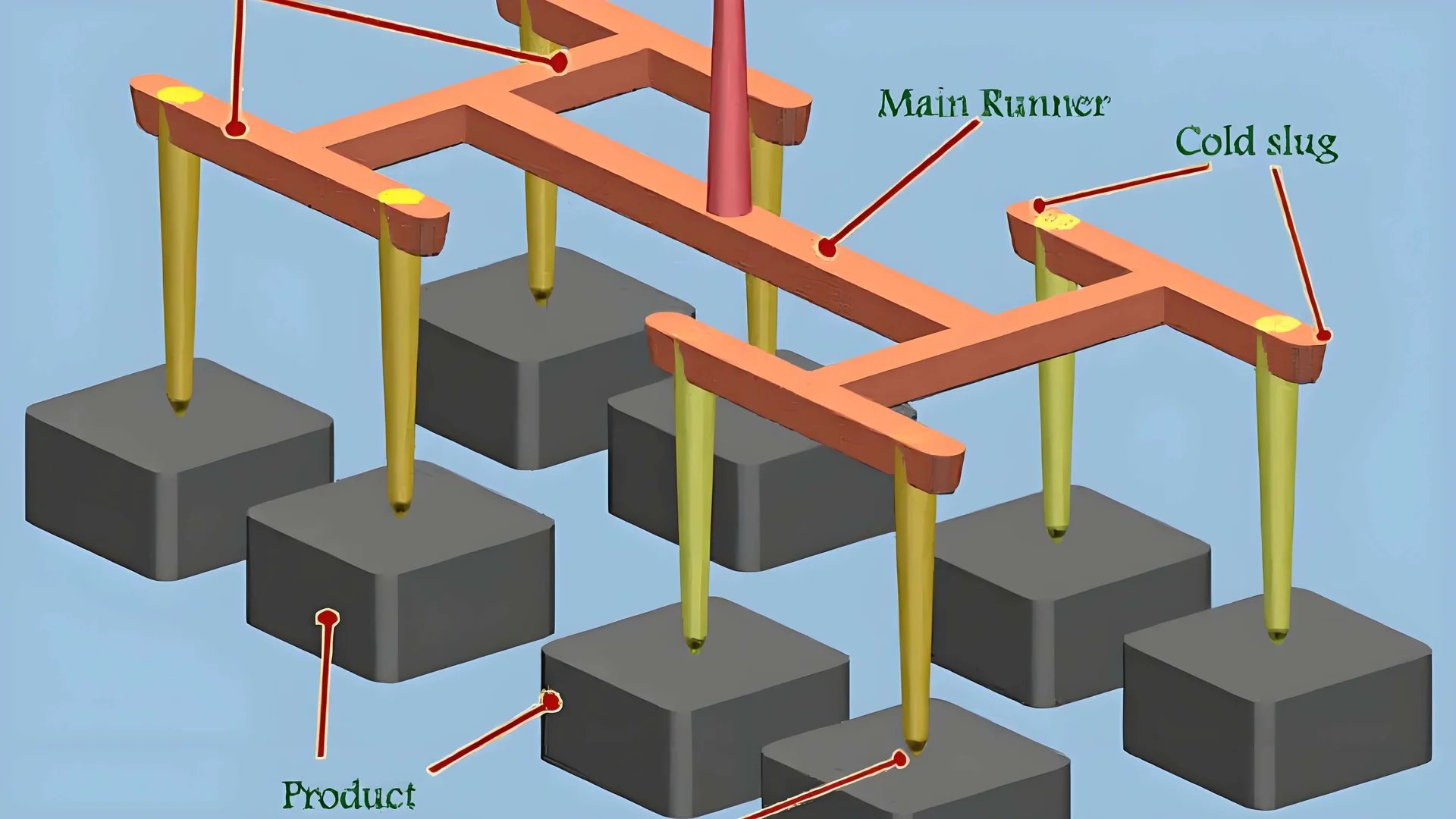
The Role of Gate Position
Gate position is crucial in determining the flow path5 of the melt within a cavity. It can influence both the appearance and mechanical properties of the final product. I remember my first experience with a poorly placed gate ruining a design. It was a transparent ornament project, and the gate mark ended up right in the middle, reducing transparency. When gates are placed at the edge, melt fills from edge to center, possibly generating residual stress concentrations that affect strength. Imagine squeezing toothpaste back into the tube; without even pressure, it becomes a messy ordeal.
Impact of Gate Size
Gate size plays a vital role in determining the melt flow rate and shear stress. Like in the Goldilocks story, it needs to be just right—neither too big nor too small. A larger gate allows slower melt entry, decreasing shear-induced stress but potentially causing uneven pressure distribution during holding. Conversely, smaller gates may lead to insufficient melt filling or high shear rates, both affecting mechanical integrity.
Gate Size | Effect on Mechanical Properties |
---|---|
Large | Lower shear stress, uneven pressure |
Small | High shear rate, potential filling issues |
I learned this when working on a sleek gadget case; we had to change the gate size a few times to get it just right.
Molecular Orientation & Crystallinity
The gate’s position and size affect molecular orientation6 and crystallinity in crystalline plastics. Proper placement can ensure unidirectional flow, leading to oriented molecules and directional strength variations. I recall a project with a long strip of plastic and a gate at one end; molecules aligned along the strip’s length increased tensile strength in that direction but weakened it perpendicularly. Imagine arranging planks on a wooden bridge—ideal for tension yet tricky for side forces.
Internal Residual Stress Distribution
Different gate positions cause varied pressure distributions during melt filling. This results in diverse residual stress patterns inside products. Gates on edges might focus stress at the center meeting point, potentially causing cracks under external forces. A careful analysis of pressure7 distribution is very necessary to mitigate these issues.
To sum up, understanding how gate details connect to mechanical properties is crucial for improving product design. Great design depends on these connections.
Gate position affects product's mechanical strength.True
Gate position influences melt flow path, impacting stress distribution.
Smaller gates decrease shear-induced stress in products.False
Smaller gates increase shear rates, raising shear-induced stress levels.
How Does Gate Design Affect Injection Molding Performance?
Did you ever think about how a small gate might decide the success or failure of your injection molding project?
Gate design shapes molding performance. It determines how molten plastic flows and influences cooling rates. Also, it affects pressure distribution. Good gate placement and size lead to better outcomes. Defects like weld lines and stress concentrations may reduce. High-quality final products often result.
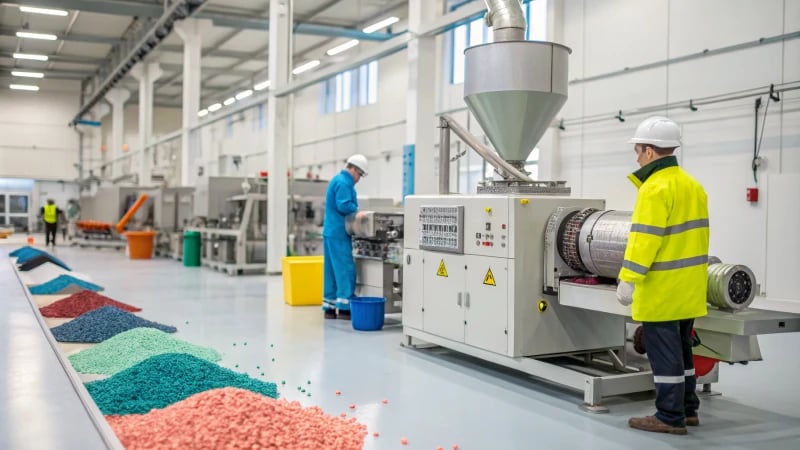
The Impact of Gate Positioning on Appearance Performance
Gate positioning is crucial for controlling the appearance8 of molded products. Poorly positioned gates can result in visible marks that degrade aesthetics, especially in transparent items. To minimize these, gates should avoid prominent areas.
-
Gate Marks: Once, a slightly bigger gate left a very noticeable mark during a client meeting. Larger gates spoil surface quality. Care is necessary.
-
Weld and Flow Marks: Wrong gate placement once caused complex flow paths on a product, creating visible weld marks. Now, I place gates to avoid complicated flows.
Mechanical Properties: Internal Residual Stress
I noticed how gate design affects mechanical properties through stress distribution. Different positions create varied pressure profiles, leading to stress concentrations that may cause cracks under load.
Factor | Effect on Mechanical Properties |
---|---|
Gate Position | Affects pressure and flow directions. |
Gate Size | Alters melt shear rates and stress. |
Changing the gate position really improved strength in one project.
Molding Performance: Ensuring Efficient Filling
The filling effect9 is influenced by gate design. Proper placement and size ensure smooth cavity filling, crucial for thin-walled parts.
-
Filling Challenges: Gates should be near complex structures to stop short shots, as I found out during a challenging project.
-
Demolding Issues: A tough demolding process taught me about gate size and position. Big gates increase sticking, making removal harder.
Molecular Orientation and Crystallinity
Crystalline plastics bring their own difficulties with gate design. I saw how molecular orientation affects tensile strength because of gate placement. Proper adjustments improve durability.
Understanding these aspects of gate design empowers engineers to enhance product durability and visual appeal. Curious minds interested in molecular orientation can explore molecular orientation techniques10 for deeper knowledge.
Gate size affects surface quality of molded products.True
Larger gates leave noticeable marks, impacting aesthetics.
Improper gate position reduces mechanical strength.True
Incorrect positioning causes stress concentrations, leading to cracks.
Conclusion
Gate location and size in injection molding significantly influence product appearance, mechanical properties, and performance, affecting defects like gate marks and stress distribution, crucial for high-quality outcomes.
-
Learn how gates function as entry points for molten material in molds, affecting product appearance. ↩
-
Understand the relationship between gate marks and product stress distribution and durability. ↩
-
Discover insights into optimizing gate design for improved filling and demolding processes. ↩
-
Gain insights into optimizing gate design for superior molding performance and reduced defects through this link. ↩
-
Explore how gate placement alters melt flow paths to improve product quality. ↩
-
Understand how strategic gate positioning affects molecular alignment and strength. ↩
-
Discover methods to analyze pressure distribution for reducing stress concentrations. ↩
-
Explore this link to see examples of how different gate positions can affect product aesthetics. ↩
-
Learn about the critical role of gate design in ensuring complete and uniform cavity filling. ↩
-
Discover techniques to manage molecular orientation for better mechanical properties in plastics. ↩