Designing a mold runner system resembles cooking a perfect dish. Every little factor is important.
Designing a mold runner system requires attention to several factors. Material flow characteristics play a key role. The runner’s size and shape hold great importance. A balanced layout is necessary. Specific requirements for hot runner systems need careful consideration. These key elements lead to efficient production. Quality output is the result.
When I began creating mold runner systems, it felt like solving a tough puzzle. Every piece – such as material flow and runner arrangement – needed to fit perfectly. Smooth flow was essential. Dimensions were not the only focus; knowing how parts worked together was key. The right runner size was vital. This was especially true with materials having different flow behaviors. Small changes affected production efficiency and product quality a lot. Small changes! Now, we explore these details more to discover how they really change your design process.
Material flow characteristics impact runner design.True
Material flow affects efficiency and quality, crucial for runner design.
Runner size is irrelevant in mold design.False
Runner size is critical for balanced flow and efficient production.
- 1. How Do Material Flow Characteristics Influence Runner Design?
- 2. How Do You Choose the Right Runner Size and Shape?
- 3. How do I plan an effective runner layout?
- 4. What Special Considerations Are There for Hot Runner Systems?
- 5. Why Is Temperature Control Critical in Injection Molding?
- 6. Conclusion
How Do Material Flow Characteristics Influence Runner Design?
Have you ever thought about how the materials in injection molding change runner design? Let’s explore the interesting connection between how materials move and the shape of runners.
Material flow features decide the runner design. They decide channel size, shape and layout. Designers concentrate on optimizing flow. This reduces defects. Designers think about material compatibility. Flowability plays an important role too. Temperature effects are crucial for good molding results.
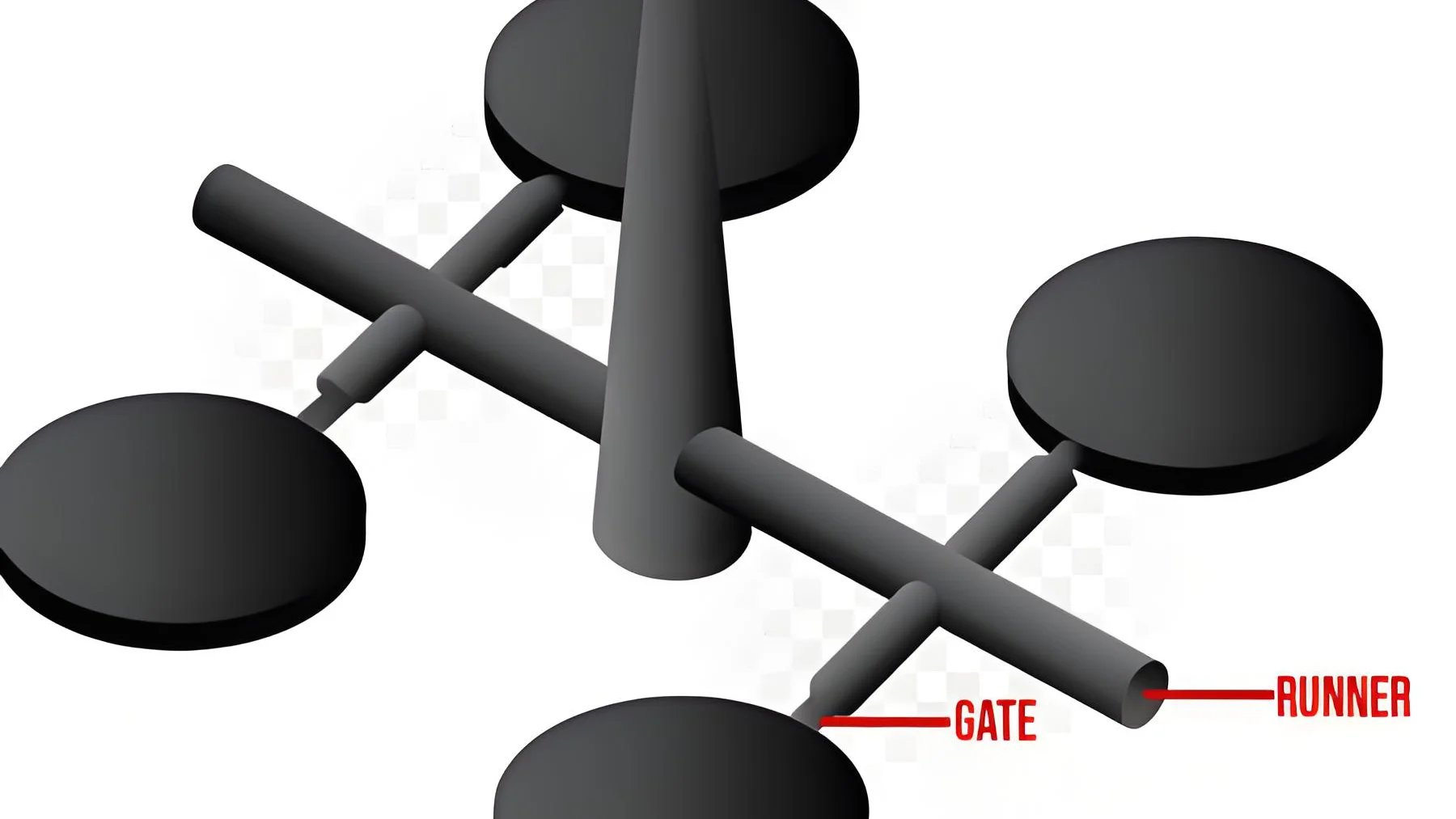
Flow Matching and Channel Size
To achieve optimal material flow, designers must align the flow channel size with the melt flow rate1 (MFR) of the molding material. I recall when I first needed to think about this; it felt like solving a secret puzzle. For instance, polystyrene (PS), known for high MFR, requires narrower channels. Conversely, working with glass fiber reinforced polyamide (PA), which has lower flowability, demands wider channels for smooth operation.
Example Table: Material vs. Channel Size
Material Type | Recommended Channel Width |
---|---|
High MFR (e.g., PS) | Narrow |
Low Flowability (e.g., PA) | Wide |
Temperature changes can disrupt processes, especially in hot runner systems. One time, when designing for thermoplastic elastomers (TPE), I understood that precise temperature control was key to maintaining ideal flow states.
Material Compatibility
Picking the right runner material feels like matching partners; everything should work well together without surprise reactions. Runner material must not react with molding materials chemically. For example, I learned this lesson when a project with polycarbonate nearly failed because it reacted badly with copper runners at high temperatures. Ever since, avoiding such combinations prolongs runner life and ensures consistent material performance2.
Runner Size and Shape Design
Choosing runner sizes includes more than just dimensions; it involves understanding how injection volume and nozzle size relate. The size of the runner should consider these factors. I often realized that a slightly larger main runner diameter than the nozzle helps improve connection and minimizes pressure loss. Adjusting branch runners based on cavity numbers and product sizes requires finesse.
Gate Size Examples
- Pin-point gate: Diameter between 0.5 – 1.5 mm.
- Fan-shaped gate: Thickness between 0.2 – 1 mm.
Choosing circular shapes when resistance should be low or rectangular when space is limited matters in handling flow resistance and complexity.
Runner Layout Planning
Always aim for a balanced runner design in multi-cavity molds to ensure simultaneous filling, saving time and stress. Asymmetric layouts might need adjustments or throttle valves to achieve equilibrium.
- Avoid dead corners: Use arc-shaped corners with a radius ≥ 1.5 times the runner diameter to prevent melt retention.
- Stagnant area checks: Ensure no parts cause long retention times to avoid degradation.
Special Considerations for Hot Runner Systems
Heating and Temperature Control
Keeping even heat in hot runners feels like a precise science task; even heat distribution is crucial in hot runners. Install heating elements like rods or coils around the plate evenly for equal distribution. For larger setups, use zone heating control3 with individual sensors for precision.
Sealing and Leakage Prevention
Preventing leaks is vital; high-quality seals like high-temperature resistant rubber or metal preserve both product quality and mold integrity. Regular checks and timely replacements are crucial tasks with major impact.
High MFR materials require narrow channels.True
High MFR materials like polystyrene need narrow channels for optimal flow.
Copper runners are suitable for polycarbonate molding.False
Polycarbonate reacts with copper at high temperatures, causing degradation.
How Do You Choose the Right Runner Size and Shape?
Have you ever thought about why picking the correct runner size and shape seems like putting together a puzzle?
When picking a runner size and shape, consider where it goes. Home decor needs the right mix of size and style. Factories benefit from smooth material flow and good temperature control for better production results.
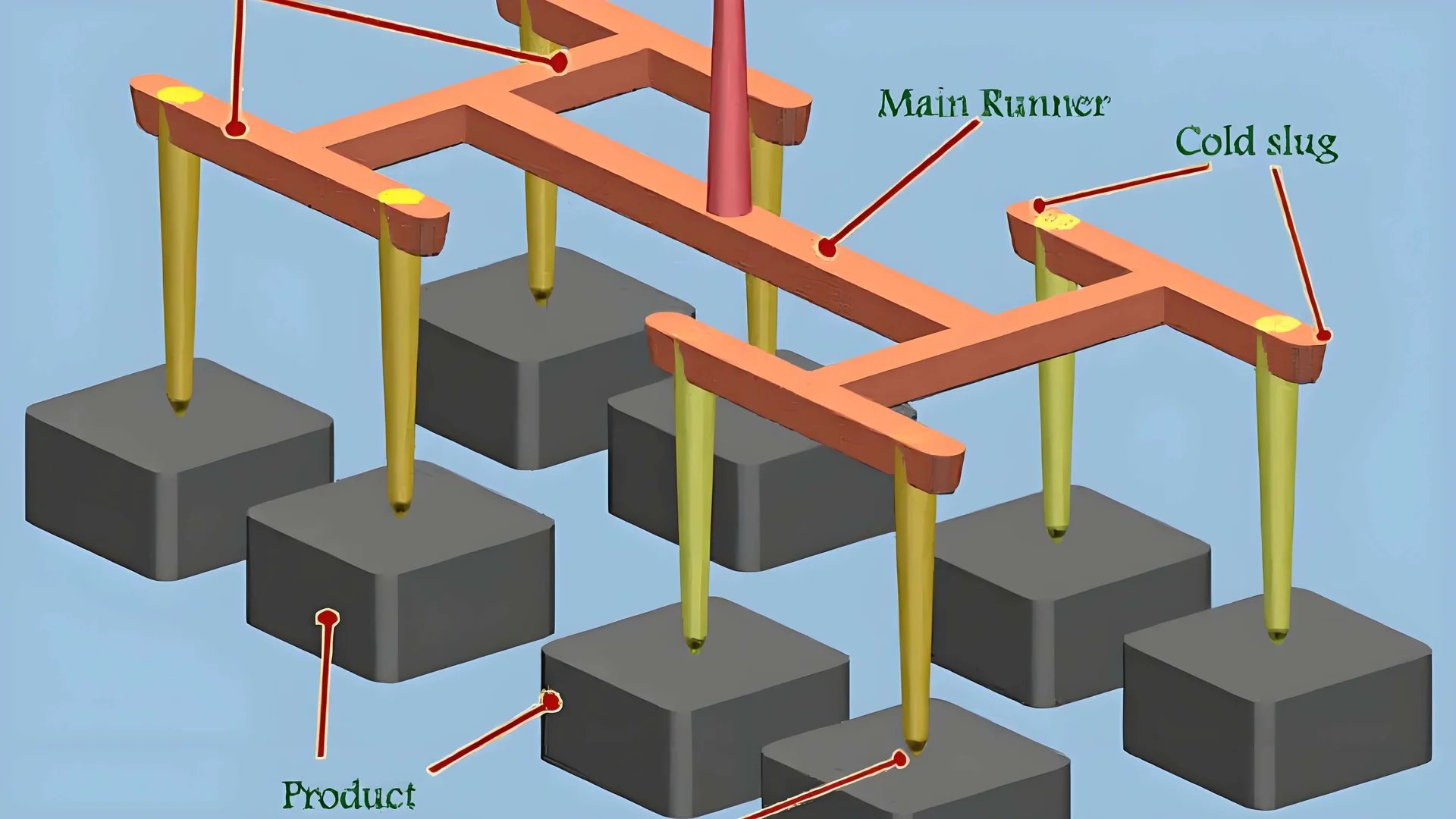
Understanding the Differences
Picking the right runner size and shape is always interesting to me. Choosing a hallway rug or designing a system in my workshop feels like each decision has its own rules. Getting it right is like solving a secret puzzle.
How Materials Move
In manufacturing, knowing how materials behave is important. Especially with materials like polystyrene or glass fiber reinforced polyamide. My first time with flow problems was tough. Understanding that the flow channel size must match the material’s melt flow rate was the key. It was hard to learn, but it showed me to respect how materials change with heat. This is especially true with tricky materials like thermoplastic elastomers.
Consider how temperature affects material flowability. In hot runner systems, precise temperature control4 is vital.
Concerns with Compatibility and Reactions
Learning about material compatibility taught me a lot. It’s not just avoiding bad reactions that ruin things; it’s also about keeping your runners lasting long. In one project, I saw polycarbonate react with copper. It showed me how small mistakes lead to big problems.
Ensuring that the flow channel does not chemically react with the molding material prevents degradation and prolongs channel life.
Designing Size and Shape
Main Runner Size
The main runner should be slightly larger than the machine’s nozzle by 0.5-1mm for a snug fit and less pressure loss. Keeping it short helps too, just like avoiding a too-long hallway rug you trip over.
Branch Runner Size
Size really depends on the work. Small, delicate pieces or materials that flow easily need smaller diameters; bigger products or thicker materials need larger diameters.
Gate Dimensions
Finding the right gate size is skillful work. You find the sweet spot based on your product’s wall thickness and material type.
Product Type | Recommended Gate Type | Diameter Range |
---|---|---|
Small Products | Pin-point | 0.5 – 1 mm |
Flat Products | Side | Depends on design |
Automated Molds | Latent | Variable |
Pin-point gates are great for detail, while fan-shaped gates have their own benefits.
Picking Shapes
I like circular runners because they have low resistance but are hard to form. Rectangular and trapezoidal shapes are simpler to create but have higher resistance challenges.
Planning the Layout and Avoiding Stagnation
Good runner layout means mold cavities fill evenly – like setting up dominos to all fall in sequence. Avoid dead corners by choosing arc-shaped turns over sharp angles; this reduces pressure loss.
Ensure no enlarged or reduced parts in the system to avoid degradation.
Hot Runner System Considerations
Temperature Control:
Zone heating in larger systems is crucial; it’s like making sure every room in a house is at the perfect temperature – not too hot, not too cold.
Arrange heating elements evenly around hot runner plates for uniform heat distribution.
In large systems, adopt zone heating control with independent sensors and controllers.
Preventing Leaks:
Good seals are essential; they are like silent protectors stopping leaks that might harm the product and equipment.
Utilize high-quality seals between system components to prevent melt leakage; regular checks and timely replacements ensure system integrity.
Discover more details5 about hot runner systems to stop leaks and keep manufacturing processes efficient. These steps help keep quality high and stop damage to molds or machines.
in my work, whether for decoration or industry, applying these principles helps me achieve design goals effectively every time.
Polystyrene requires narrow runner channels.True
Polystyrene's melt flow rate necessitates narrow channels for optimal flow.
Circular runners have higher flow resistance than rectangular ones.False
Circular runners offer low flow resistance, unlike rectangular shapes.
How do I plan an effective runner layout?
Have you ever thought about how a good runner layout shapes your molding process? Curious minds really ask this. Proper planning plays a vital role. Design affects success or failure.
Plan a good runner layout by thinking about how the material moves, the size and shape of the runners and keeping the layout balanced to avoid areas where nothing happens. These things are very important for getting the best injection molding results.
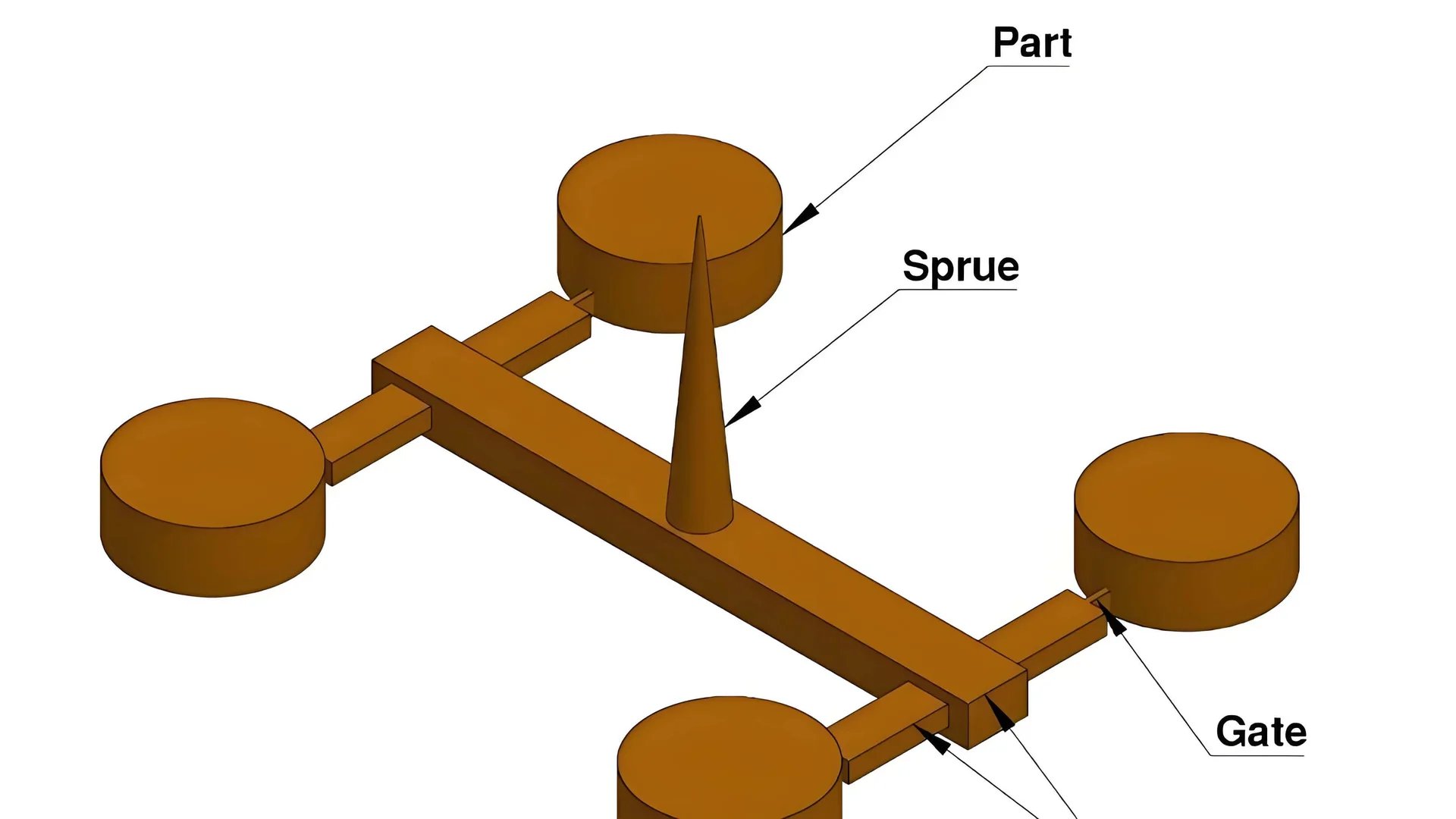
Material Flow Characteristics
Understanding the flow matching6 principles is essential. The flow channel size should align with the melt flow rate (MFR) of the molding material. For instance, materials with high MFR like polystyrene require narrower channels than materials like glass fiber reinforced polyamide, which need wider channels.
- Compatibility: Ensure the flow channel material is chemically inert with the molding material, avoiding reactions at high temperatures that could degrade materials.
I realized early on that matching the flow channel and the molding material is crucial. Using copper in runners with polycarbonate once led to unexpected reactions. I discovered this mistake during a project and it was a hard lesson.
Runner Size and Shape Design
Designing the runner size involves multiple considerations:
Component | Size Recommendations |
---|---|
Main Runner | Slightly larger than nozzle, 0.5-1mm |
Branch Runner | 3-6mm for small products, 8-12mm for larger |
Gate | Pin-point: 0.5-1.5mm, Fan-shaped: 0.2-1mm |
The shape of the runner is also critical:
- Circular runners offer low flow resistance but are complex to process.
- Rectangular and trapezoidal runners are easier to process but have higher resistance.
Finding the right runner size often feels like solving a puzzle. Here is a simple idea I stick to: choosing the shape is difficult too.
Balanced Layout Planning
For molds with multiple cavities, a balanced runner layout7 is vital. The runners from the main channel to each cavity should be uniform in length and shape to ensure simultaneous filling.
Balancing a layout feels like organizing a dinner; everything needs serving simultaneously and at the same temperature.
- Avoiding Dead Zones: Eliminate right-angle turns and narrow channels to prevent pressure loss and melt retention, which could degrade product quality.
I faced persistent quality issues once because of dead zones—tricky right-angle turns that trap melt and spoil product quality—that was an important lesson.
Special Points for Hot Runner Systems
The hot runner system requires meticulous planning:
- Heating Control: Employ zone heating control with independent sensors to maintain optimal temperatures throughout.
- Sealing: Use high-temperature resistant seals to prevent leaks, which can affect product quality and damage equipment.
Hot runner systems need accuracy. Independent sensors control heating zones to keep materials at ideal temperatures. A poor seal caused a leak once, ruining a whole batch; now I always use very heat-resistant seals.
These tips have significantly increased my efficiency and product quality in injection molding. Small changes in runner layout can greatly change production results—it’s really impressive.
Circular runners offer low flow resistance.True
Circular runners are designed to minimize the resistance encountered by the melt flow.
Right-angle turns in runners improve flow efficiency.False
Right-angle turns create dead zones, causing pressure loss and reducing flow efficiency.
What Special Considerations Are There for Hot Runner Systems?
Curious about how a hot runner system works in injection molding? Learn about the details that bring high efficiency and great product quality.
I focus on important parts when I design a hot runner system. Material flow matters. Runner size and shape are crucial. A balanced layout is also necessary. Precise temperature control is vital for top performance. Quality products probably result from all these factors.
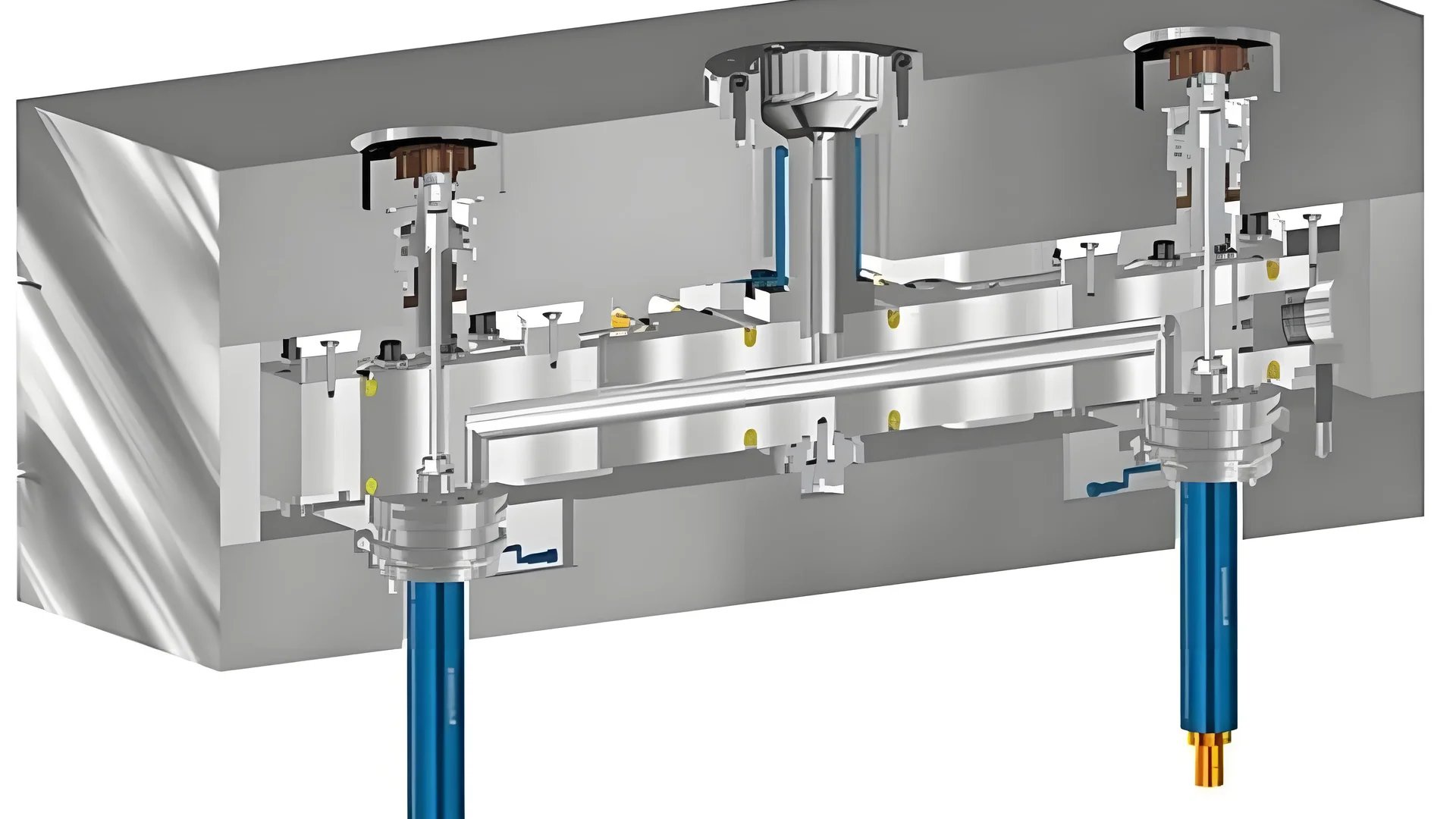
Material Flow Characteristics
I remember my first project with tricky material – glass fiber reinforced polyamide. It taught me an important lesson: materials behave differently. Flow channels must fit the melt flow rate (MFR). High MFR materials, like some polystyrenes, slide through smaller channels, whereas low flowability materials need more room. Each material needs its own space on the road.
Additionally, temperature matters a lot. Keeping thermoplastic elastomer at the right temperature means it flows nicely. Ensure material compatibility8 to avoid chemical reactions between the flow channel and molding materials.
Runner Size and Shape Design
Think of setting up a waterpark. Slides need the right size to keep everyone moving smoothly. In injection molding, runner size and shape are crucial:
Parameter | Consideration |
---|---|
Main Runner | Joins snugly with the machine nozzle, slightly bigger by 0.5-1mm for good connection. Shorter main runners mean less pressure loss. |
Branch Runner | Adjust diameter based on product size and material viscosity. |
Gate Size | Depends on wall thickness, material, and injection speed. |
Circular shapes are ideal but tricky to process; rectangular and trapezoidal shapes work better in tight spaces.
Runner Layout Planning
Balancing a runner layout is like planning a trip with friends: everyone needs an equal start to enjoy the ride. Equal runner lengths from the main channel fill cavities at the same time—it’s like sharing snacks equally on the journey.
Avoiding dead corners and stagnant spots is crucial—like ensuring no one gets stuck in traffic. Use arc-shaped corners with a radius 1.5 times the runner diameter to keep everything moving smoothly.
Heating and Temperature Control
Efficient hot runner heating is like baking cookies: even heat distribution is important:
- Well-placed heating elements around plates and nozzles ensure each part cooks evenly.
- Zone heating control provides accuracy with independent sensors for each zone.
- Insulation materials like ceramic fibers improve thermal efficiency without overheating mold parts.
Sealing and leakage prevention are vital—use high-quality seals between components to prevent melt leakage which can damage products and equipment. Regular seal checks are necessary, much like ensuring your oven keeps heat inside.
High MFR materials need wider hot runner channels.False
High MFR materials require narrower channels for optimal flow.
Balanced runner layout prevents melt retention.True
Equal runner lengths ensure even filling, avoiding retention.
Why Is Temperature Control Critical in Injection Molding?
Have you ever thought about why temperature is important in injection molding? It’s similar to baking a cake. Get the heat wrong and everything falls apart.
Temperature control in injection molding is important for keeping the material flow steady. It stops problems like warping. Proper temperature protects the mechanical properties of the final product. This process holds a key position in upholding quality and efficiency.
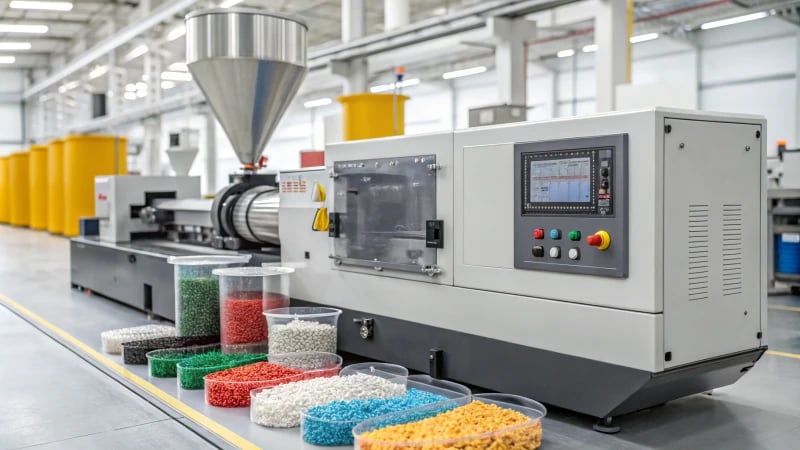
Material Flow Characteristics
My first project in injection molding felt like walking on a tightrope. Temperature played a crucial role. A small change could lead to success or failure. Imagine pushing honey through a straw. Too cold and nothing moves. Too hot and it spills everywhere.
In molding, different materials need special flow conditions. It’s like changing your coffee brew depending on the beans. For example, flow matching9 ensures that the channel size must fit the melt flow rate of the material. This prevents problems like incomplete filling or too much pressure.
Runner Size and Shape Design
Designing the runner system with temperature in mind resembles planning a road trip. You need to understand the land. Runner size should match the material’s thickness at different temperatures.
Material | Low Viscosity | High Viscosity |
---|---|---|
Polystyrene | 3-6 mm | 8-12 mm |
Glass Fiber Reinforced Polyamide | 6-10 mm | 10-15 mm |
Picture working with polystyrene or glass fiber-reinforced polyamide. Runner size changes based on whether you want a smooth ride or will risk some bumps.
Hot Runner Systems
Hot runner systems are like fine kitchens. Every detail needs precise control. Heating parts must spread heat evenly to keep uniform temperature across the system. In large systems, zone heating provides precise control of different sections, allowing for adjustments similar to cooking multiple dishes.
Temperature changes might affect material compatibility10. This could cause reactions that damage material quality or runner longevity. Regular checks for proper sealing and insulation stop leaks and uphold system strength.
Avoiding Defects
Good temperature management avoids defects like warping and sink marks. When I started, I learned that controlling the mold’s cooling speed ensures even solidification, reducing stress and bending in the end product—much like cooling a pie slowly to prevent cracks.
A well-balanced runner design stops local overheating and ensures even cavity filling, ensuring each slice of pie is perfectly baked.
Automation and Control Systems
Modern injection molding is a finely tuned craft with advanced systems automating temperature control. They monitor mold temperatures and adjust settings in real-time for optimal conditions, akin to using a smart thermostat at home.
Insulating materials, such as ceramic fibers11, cut heat loss and improve energy saving.
Knowing how temperature affects every part of injection molding helps designers like Jacky craft high-quality pieces effectively.
Temperature affects material flow in injection molding.True
Different materials require specific temperatures to ensure proper flow.
Hot runner systems do not require temperature control.False
Even heating is critical to maintain uniform temperature in hot runner systems.
Conclusion
Designing a mold runner system involves considering material flow characteristics, runner size and shape, balanced layouts, and temperature control for efficient production and high-quality output.
-
Understanding melt flow rate helps in selecting appropriate channel sizes for different materials. ↩
-
Material compatibility knowledge aids in choosing runner materials that won’t degrade or react chemically. ↩
-
Zone heating control ensures precise temperature regulation across large hot runner systems. ↩
-
Learn how precise temperature control can enhance efficiency and prevent issues in hot runner systems. ↩
-
Discover effective sealing techniques for hot runner systems to avoid leakage and maintain product quality. ↩
-
Discover how aligning flow channel size with material properties enhances injection molding efficiency. ↩
-
Learn how a balanced layout ensures even filling in multi-cavity molds, enhancing product consistency. ↩
-
This link provides strategies to prevent chemical reactions between different materials in hot runner systems. ↩
-
Learn about flow matching to enhance understanding of its role in improving efficiency and quality in injection molding. ↩
-
Discover how incompatible materials can affect mold integrity and product quality due to temperature-related reactions. ↩
-
Insulation materials are crucial for maintaining energy efficiency and preventing heat loss in injection molding systems. ↩