Food packaging is more than just a wrapper—it’s a guardian of our health.
Safety standards in food packaging injection molded products involve strict regulations on raw materials like polystyrene, polypropylene, and polyethylene. These materials must meet hygiene and safety requirements to prevent harmful substance migration into food. Technical challenges include ensuring material stability and precision in injection molding processes.
While these standards provide a foundation for safety, the technical challenges present significant hurdles that demand innovative solutions. Let’s dive deeper into how these factors influence food safety.
Polystyrene resins must comply with GB9692 standards.True
GB9692 ensures polystyrene's safety in food packaging by preventing harmful substance migration.
How Do Raw Material Standards Affect Food Safety?
Understanding raw material standards is crucial for ensuring the safety of food packaging, impacting consumer health and regulatory compliance.
Raw material standards for food packaging play a pivotal role in food safety by ensuring materials like resins meet specific hygiene and safety regulations. These standards prevent harmful substances from migrating into food, safeguarding consumer health and maintaining product quality.
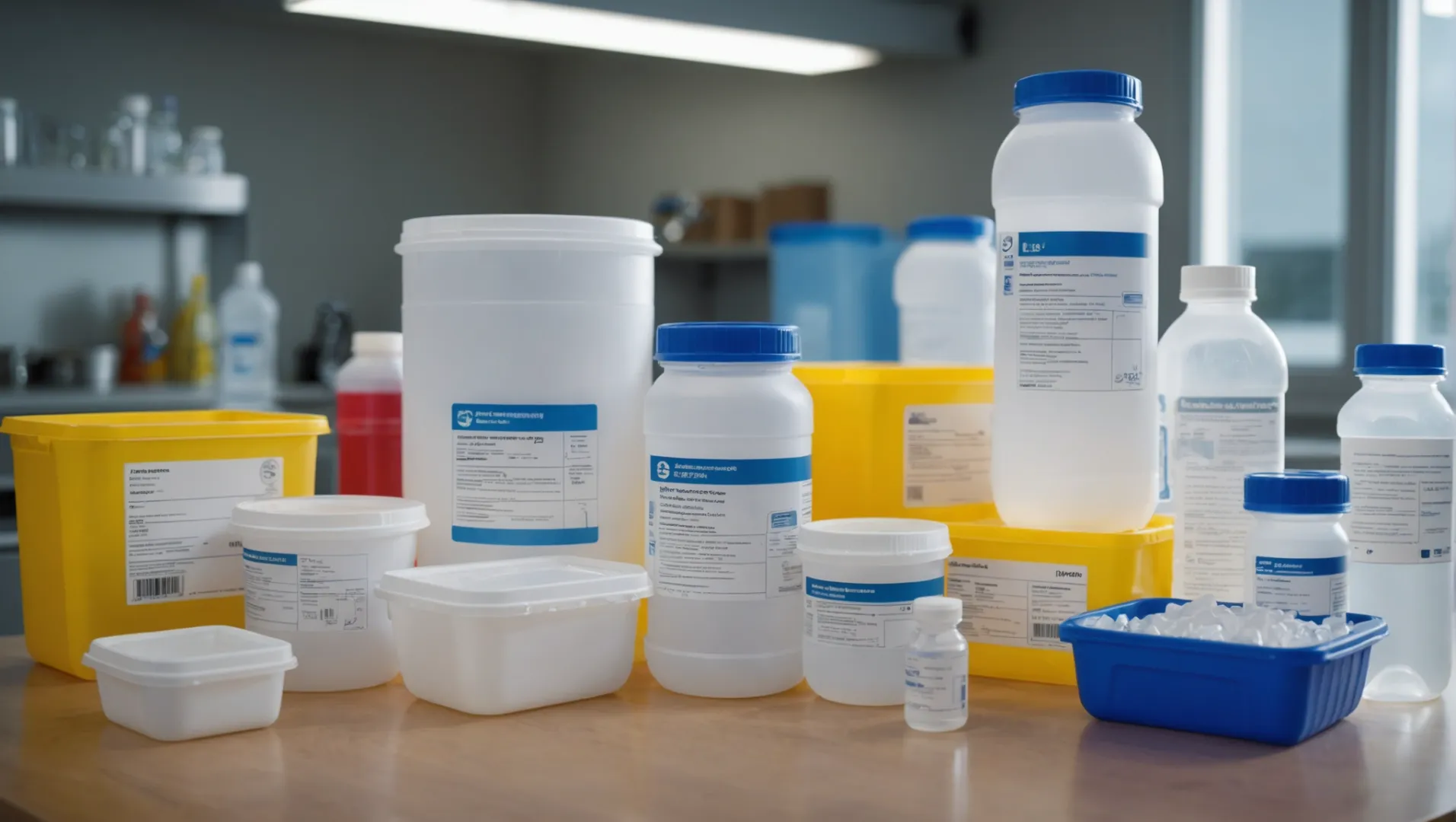
Importance of Raw Material Standards
Raw material standards are fundamental to the safety and quality of food packaging products. They set the criteria for material selection, ensuring that only materials that meet strict safety and hygiene regulations are used. This is crucial because the materials used can directly impact the safety of the food they contain.
Resin Materials:
-
Polystyrene Resins: These resins must comply with GB9692 standards, focusing on preventing the migration of harmful substances. By meeting these standards, polystyrene resins are deemed safe for use in food packaging, mitigating risks of chemical leaching into food items.
-
Polypropylene Resins: Governed by GB9693, these resins offer excellent heat resistance and chemical stability. The standard ensures that any potential contaminants in the raw material are controlled, maintaining the integrity of the food packaging.
-
Polyethylene Terephthalate (PET) Resins: With standards outlined in GB13114, PET is commonly used for beverage bottles. Compliance ensures that additives do not compromise food safety by migrating into consumable goods.
-
Polyethylene Resins: These must adhere to GB9691, commonly used in products like plastic wraps and bags. Ensuring raw material quality is critical to prevent any adverse health effects due to material degradation or contamination.
Standards for Additives and Printing Inks
Another critical aspect is the regulation of additives and inks used in food packaging. Additives must be non-toxic and approved for use in contact with food to avoid any health hazards. Similarly, printing inks must comply with GB9685 to ensure they do not leach harmful chemicals into food products.
Addressing Technical Challenges
Ensuring food safety through raw material standards also involves overcoming significant technical challenges:
-
Material Stability: Different foods require different packaging properties, which means selecting materials that remain stable under various conditions such as temperature fluctuations and exposure to acidic or oily foods. This stability prevents unwanted reactions that could compromise food safety.
-
Purity and Environmental Considerations: High purity levels are mandatory to prevent contamination. With increasing emphasis on sustainability, manufacturers are exploring environmentally friendly materials. However, these alternatives need thorough testing to ensure they match the safety standards of traditional materials.
Quality Assurance in Production
The implementation of stringent quality control measures throughout the production process is essential. Regular inspections and testing of raw materials ensure compliance with safety standards and help maintain consistent product quality.
In summary, adhering to raw material standards is not just about regulatory compliance; it plays a crucial role in maintaining food safety and consumer trust. By selecting appropriate materials and ensuring their purity and stability, manufacturers can effectively prevent contamination risks and uphold high safety standards in food packaging. For more on this topic, explore resin material standards in food packaging1.
Polystyrene resins must comply with GB9692 standards.True
GB9692 ensures polystyrene resins prevent harmful migration into food.
Polypropylene resins have no specific safety standards.False
Polypropylene resins are governed by GB9693 for safety compliance.
What Role Does Sanitary Control Play in Injection Molding?
Sanitary control is crucial in injection molding to ensure the safety and quality of food packaging products.
In injection molding, sanitary control ensures that the production environment, raw materials, and processes are free from contaminants. This is vital for preventing harmful substance migration into food packaging and maintaining product integrity.
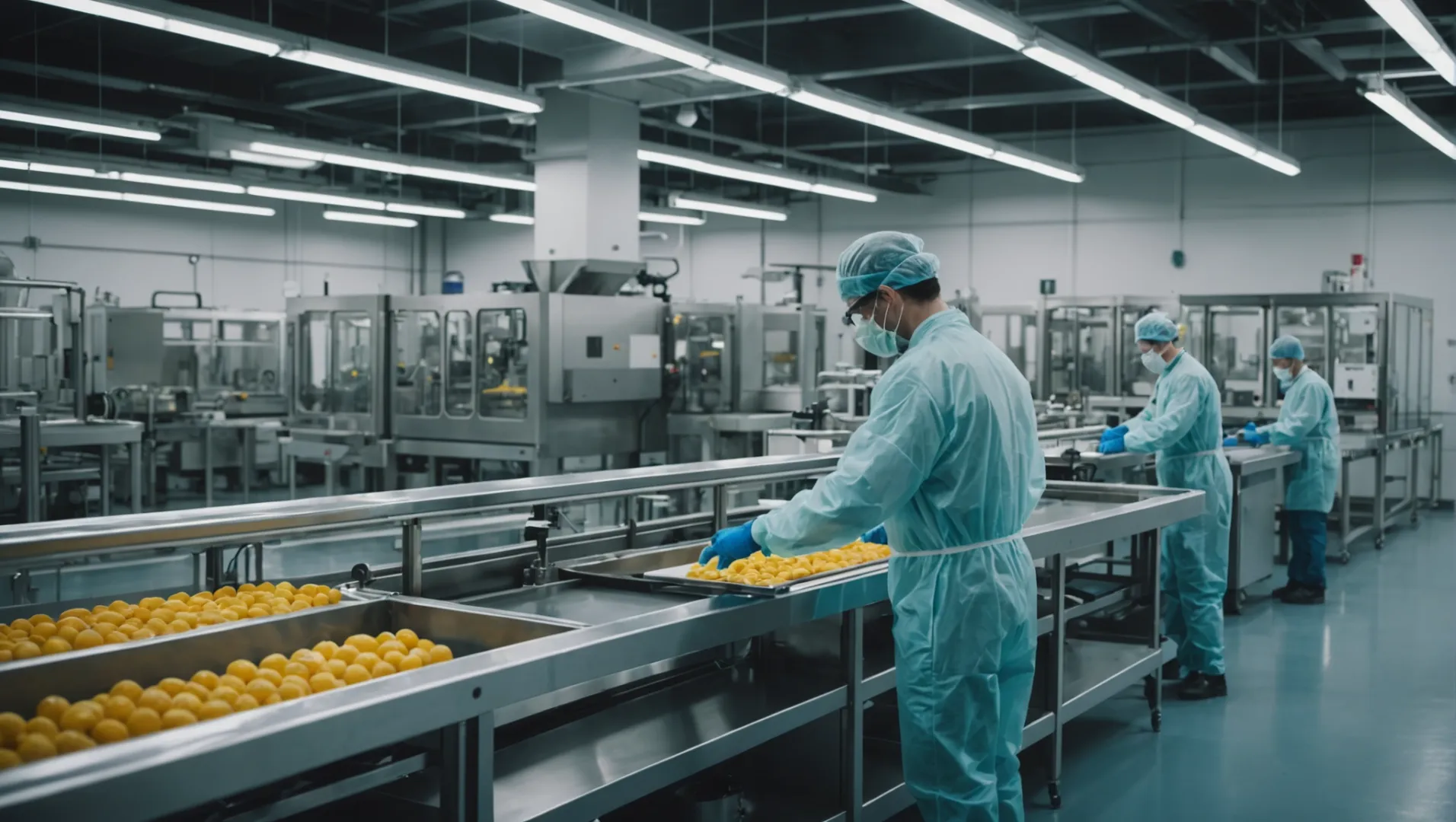
Importance of Sanitary Control in Injection Molding
Sanitary control plays a pivotal role in the injection molding process, particularly when the end products are intended for food packaging. The production environment needs to be meticulously maintained to prevent any form of contamination.
Ensuring a Clean Production Environment
A clean production environment is essential in food packaging2 to prevent contaminants from entering the molding process. The workshop must be kept free from dust, bacteria, and other pollutants through rigorous cleaning and disinfection measures. Regular checks and maintenance of equipment further ensure a contaminant-free environment.
Key Aspect | Sanitary Control Measures |
---|---|
Production Area | Frequent cleaning and sterilization; proper ventilation |
Equipment | Regular maintenance and cleaning |
Personnel | Use of protective clothing like masks and gloves |
Impact on Raw Materials
The selection and handling of raw materials are crucial for maintaining product safety. Strict hygiene protocols must be followed to prevent microbial contamination during storage and processing. For instance, polyethylene resins used must comply with specific safety standards to ensure no harmful chemicals are present.
Sanitary Control in the Production Process
The production process itself must adhere to sanitary standards to ensure the safety of the final product. Employees involved in the manufacturing process are required to follow hygienic operating procedures, wearing appropriate protective gear to prevent contamination.
Quality Assurance through Sanitary Practices
Quality control systems are established to monitor and evaluate each stage of production, ensuring compliance with sanitary standards. From raw material inspection to finished product testing, each step is designed to catch potential contaminants early on.
Implementing a robust sanitary control system not only ensures compliance with regulatory standards but also enhances consumer trust by guaranteeing the safety of food-contact products. By addressing these aspects, manufacturers can effectively mitigate risks associated with contamination in injection molding processes.
Sanitary control prevents contamination in injection molding.True
Sanitary control measures ensure that the production environment is contaminant-free.
Sanitary control has no impact on raw materials in molding.False
Strict hygiene protocols are crucial to prevent contamination of raw materials.
How Can Production Processes Impact Product Safety?
Understanding the intricacies of production processes is crucial for ensuring the safety of food packaging products.
Production processes impact product safety by enforcing stringent hygiene standards, precise equipment maintenance, and robust quality control measures. Ensuring a clean environment and proper staff training reduces contamination risks, while regular equipment checks and controlled operations enhance product integrity.
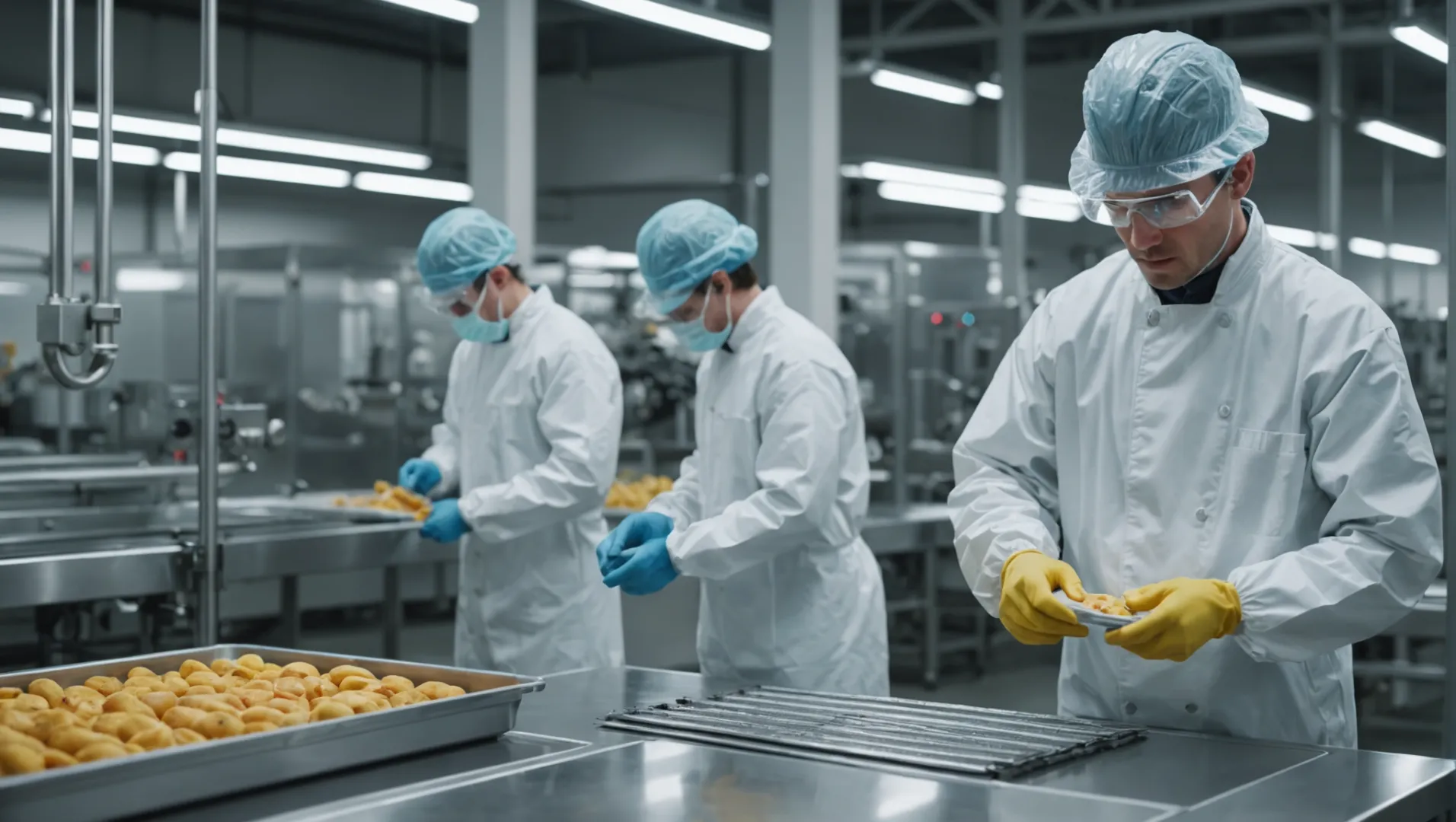
Ensuring a Hygienic Production Environment
A clean and well-maintained production environment is the cornerstone of product safety. Hygiene in the production area prevents contaminants like dust and bacteria from compromising product quality. Facilities should maintain strict cleanliness standards, incorporating ventilation and regular disinfection protocols to safeguard against pollutants. Staff should adhere to hygienic practices, including wearing appropriate protective clothing.
Read more about hygienic production environments3
Equipment Maintenance and Operation
The role of equipment4 in maintaining product safety cannot be overstated. Regular maintenance ensures that injection molding machines operate efficiently, reducing the risk of defects that could lead to product failures. Precision control over heating, cooling, and injection parameters is vital for producing high-quality items. This precision helps avoid issues like warping or material inconsistencies that can affect food safety.
Implementing Rigorous Quality Control
A robust quality control system is essential for identifying and mitigating potential safety issues. It involves comprehensive testing at various production stages, from raw materials to finished products. Online inspection technologies can offer real-time monitoring, ensuring prompt detection of deviations from safety standards.
Quality Control Aspect | Purpose |
---|---|
Raw Material Inspection | Ensures purity and compliance with safety standards |
Semi-finished Product Testing | Checks for defects during production to prevent waste |
Final Product Inspection | Verifies product meets all safety criteria |
Explore advanced quality control systems5
Addressing Microbiological Concerns
Injection molding processes must also account for microbiological safety. For products in direct contact with food, it is critical to ensure the absence of harmful microorganisms. Implementing stringent microbiological tests helps prevent contamination and protect consumer health.
Learn about microbiological safety in food packaging6
Regular equipment checks reduce contamination risks.True
Regular maintenance prevents defects and contamination, ensuring product safety.
Hygiene standards are optional in production processes.False
Strict hygiene is essential to prevent contaminants and ensure product safety.
What Innovative Technologies Are Addressing Current Challenges?
Exploring cutting-edge technologies offers solutions to the pressing challenges in food packaging injection molding.
Innovative technologies like AI-driven quality control, biodegradable materials, and advanced mold design are addressing challenges in food packaging injection molding. These advancements improve efficiency, safety, and environmental sustainability while meeting industry demands.
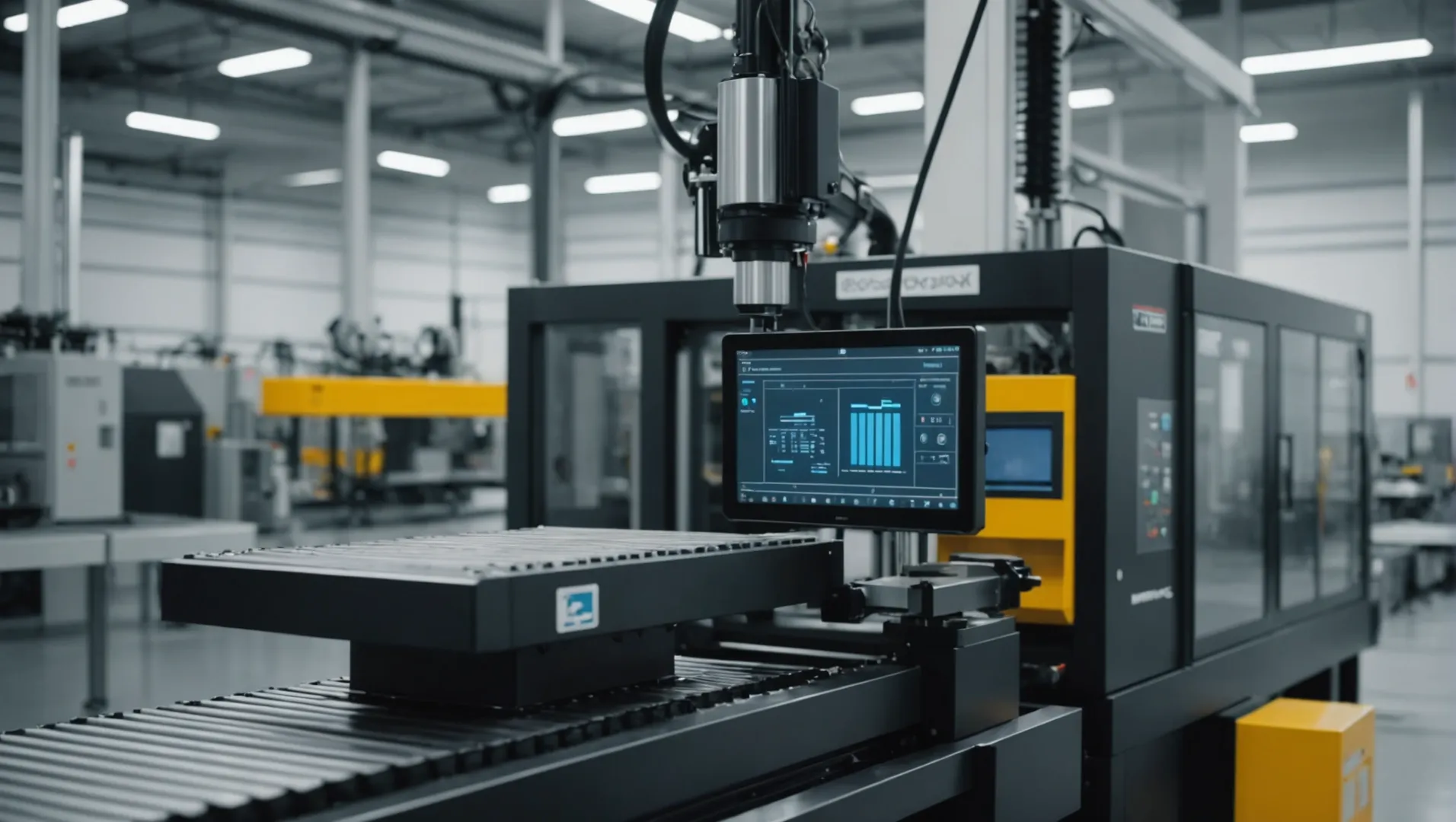
AI-Driven Quality Control
Artificial intelligence (AI) is transforming quality control in the food packaging7 industry by enhancing precision and reducing errors. AI systems utilize machine learning algorithms to analyze real-time data from sensors during the injection molding process. This technology allows for immediate identification of defects, such as warping or material shortages, thus improving production efficiency and product reliability.
Moreover, AI can predict potential failures by recognizing patterns that human operators might miss, thus facilitating preemptive maintenance and reducing downtime. Implementing AI-driven quality control not only assures compliance with stringent safety standards but also optimizes the overall manufacturing workflow.
Biodegradable Materials in Injection Molding
As environmental concerns grow, the shift towards biodegradable materials in food packaging has become imperative. Innovations in bioplastics8 have led to the development of materials like polylactic acid (PLA) and polyhydroxyalkanoates (PHA), which decompose naturally without leaving toxic residues.
Integrating these materials into injection molding processes presents a dual challenge: maintaining the functional integrity of the packaging while ensuring its environmental compatibility. Research is ongoing to enhance the mechanical properties of bioplastics, making them viable alternatives to traditional petroleum-based plastics.
Advanced Mold Design Technologies
The design and fabrication of molds are pivotal in overcoming technical challenges in injection molding. Innovations in 3D printing9 allow for rapid prototyping and testing of mold designs, significantly shortening the development cycle.
Additionally, computer-aided design (CAD) software enables precise mold engineering, facilitating better sealing, cooling, and demolding characteristics. These advancements reduce production errors and improve the consistency of the final products, addressing issues such as uneven wall thickness or color discrepancies.
By leveraging these innovative technologies, manufacturers can address current challenges effectively, ensuring high-quality food packaging that meets safety standards and aligns with sustainability goals.
AI improves quality control in food packaging.True
AI enhances precision and reduces errors in quality control.
Biodegradable materials are not used in injection molding.False
Biodegradable materials like PLA are used in injection molding.
Conclusion
Understanding safety standards and technical challenges is essential for ensuring consumer safety. Stay informed about evolving regulations to enhance product quality.
-
Discover comprehensive guidelines on resin safety for informed material choices.: Recycled food-contact plastics must meet the same compositional and specification requirements that apply to the virgin plastics. ↩
-
Explore how sanitary control ensures contaminant-free food packaging production.: Choose the right packaging for your product ingredients · Incorporate extra safety to ensure consumer confidence · Add proper safety labels to … ↩
-
Discover best practices for maintaining a hygienic production space.: Among other things to prevent cross contamination and to meet quality and HACCP requirements and standards such as BRC, IFS and FSSC 22000. But … ↩
-
Understand why regular maintenance is crucial for equipment efficiency.: Preventative equipment maintenance is key to extending equipment life and ultimately saving you time and money. ↩
-
Learn how advanced systems enhance product quality and safety.: Quality control is a process that uses best practices, strict adherence to standards, and specifications to deliver products without defects. ↩
-
Explore techniques to ensure microbiological safety in packaging.: Correct food packaging and processing to suit product formulation are essential to control microbes which could spoil food or cause consumer … ↩
-
Explore how AI enhances precision in quality control processes.: AI offers a faster, more accurate, and reliable way to inspect food products, ultimately leading to improved safety and compliance across the industry. ↩
-
Discover the benefits and challenges of using bioplastics.: Types of Biodegradable Plastic Resin · 1. Thermoplastic Starch-Based Plastics (TPS) · 2. Polyhydroxyalkanoates (PHA) · 3. Polylactic Acid (PLA). ↩
-
Learn about 3D printing’s role in innovative mold design.: Learn how to create 3D printed injection molds for low-volume, in-house injection molding to produce small, functional parts in production plastics. ↩