Navigating the complexities of injection molding costs can feel like wandering through a maze. But once you know the key factors, it becomes much clearer!
To accurately estimate injection molding costs, consider factors like material, design, processing, and testing expenses. Methods such as empirical calculation, material coefficient, and analogy offer frameworks to determine these costs effectively.
While this overview provides a snapshot of key cost factors, delving deeper into each component reveals hidden complexities and potential cost-saving opportunities. Let’s explore the detailed breakdowns and strategies that can make your cost estimations more precise and reliable.
Material choice affects injection molding costs.True
Different materials vary in cost and performance, impacting expenses.
What Factors Influence Material Costs in Injection Molding?
Material costs in injection molding are pivotal in determining overall production expenses and can vary widely based on multiple factors.
Material costs in injection molding are influenced by the type and quality of materials used, including mold core and frame materials, as well as standard parts like screws and springs. The selection impacts both the cost and performance of the mold.
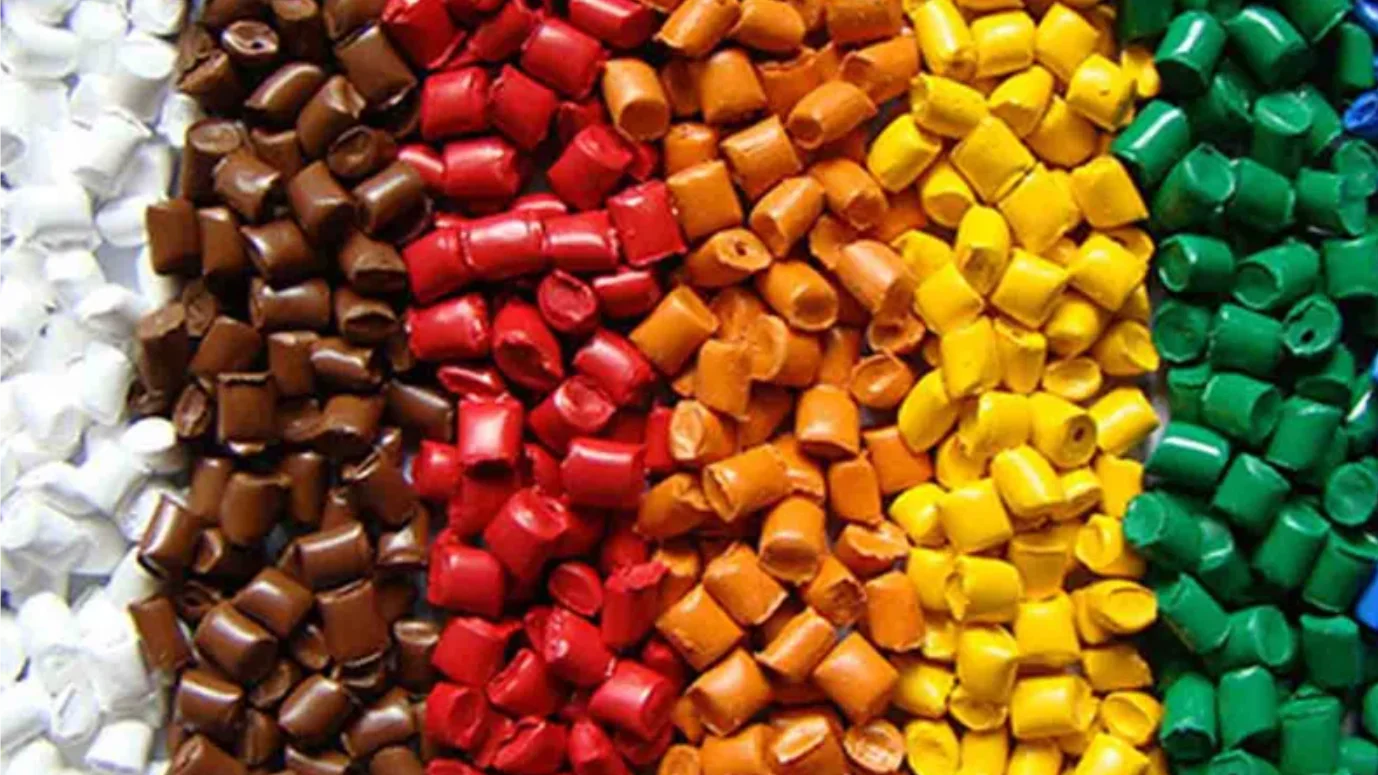
Understanding Material Types and Their Impact
One of the primary influencers of material costs in injection molding is the choice of materials for both the mold core1 and mold frame. Mold cores often use diverse types of steel, such as P20, 718, and H13, each varying significantly in price and properties. For example, P20 is a lower-cost option suitable for less complex molds, whereas H13 is more expensive but provides superior heat resistance.
The mold frame also plays a crucial role. Commonly made from cast iron or steel, the choice affects both cost and precision. Cast iron offers lower costs but compromises on strength and precision compared to steel.
Material | Cost Level | Key Properties |
---|---|---|
P20 Steel | Low | Simple structure, moderate durability |
718 Steel | Medium | Balanced durability and cost |
H13 Steel | High | Excellent heat and wear resistance |
The Role of Standard Parts
Standard parts such as screws, springs, guide posts, and bushings are essential for mold operation. The quality and precision2 of these parts not only affect the mold’s performance but also influence costs significantly. High-quality brands offer better durability but at a higher price point.
Design and Analysis Costs
Designing a mold involves extensive analysis to ensure it meets product specifications. This includes examining the product’s structural requirements, which can increase material costs if more expensive materials are needed to meet design complexities. Design analysis might involve sophisticated software for mold flow analysis3, which further adds to costs.
Processing Expenses
Machining processes like milling and EDM (Electrical Discharge Machining) can also impact material costs. Complex designs require more precise machining, leading to higher expenses. For instance, EDM is used for intricate parts, which not only requires special equipment but also involves slower processing speeds, thereby increasing costs.
Surface Treatment Costs
To enhance mold durability and performance, surface treatments such as nitriding or chrome plating are applied. Each treatment method varies in cost based on the required durability and resistance levels.
Understanding these factors helps manufacturers make informed decisions to optimize material selection for injection molding projects, balancing cost with performance needs.
P20 steel is costlier than H13 steel.False
P20 is a lower-cost option compared to the more expensive H13.
Cast iron mold frames are stronger than steel frames.False
Steel frames offer better strength and precision than cast iron.
How Does Design Complexity Affect Mold Pricing?
Design complexity significantly influences mold pricing, often impacting multiple cost factors including materials, labor, and time.
Design complexity affects mold pricing through increased costs in materials, precision machining, and extended design time. Complex designs demand more intricate mold structures and higher quality materials, thus raising overall expenses.
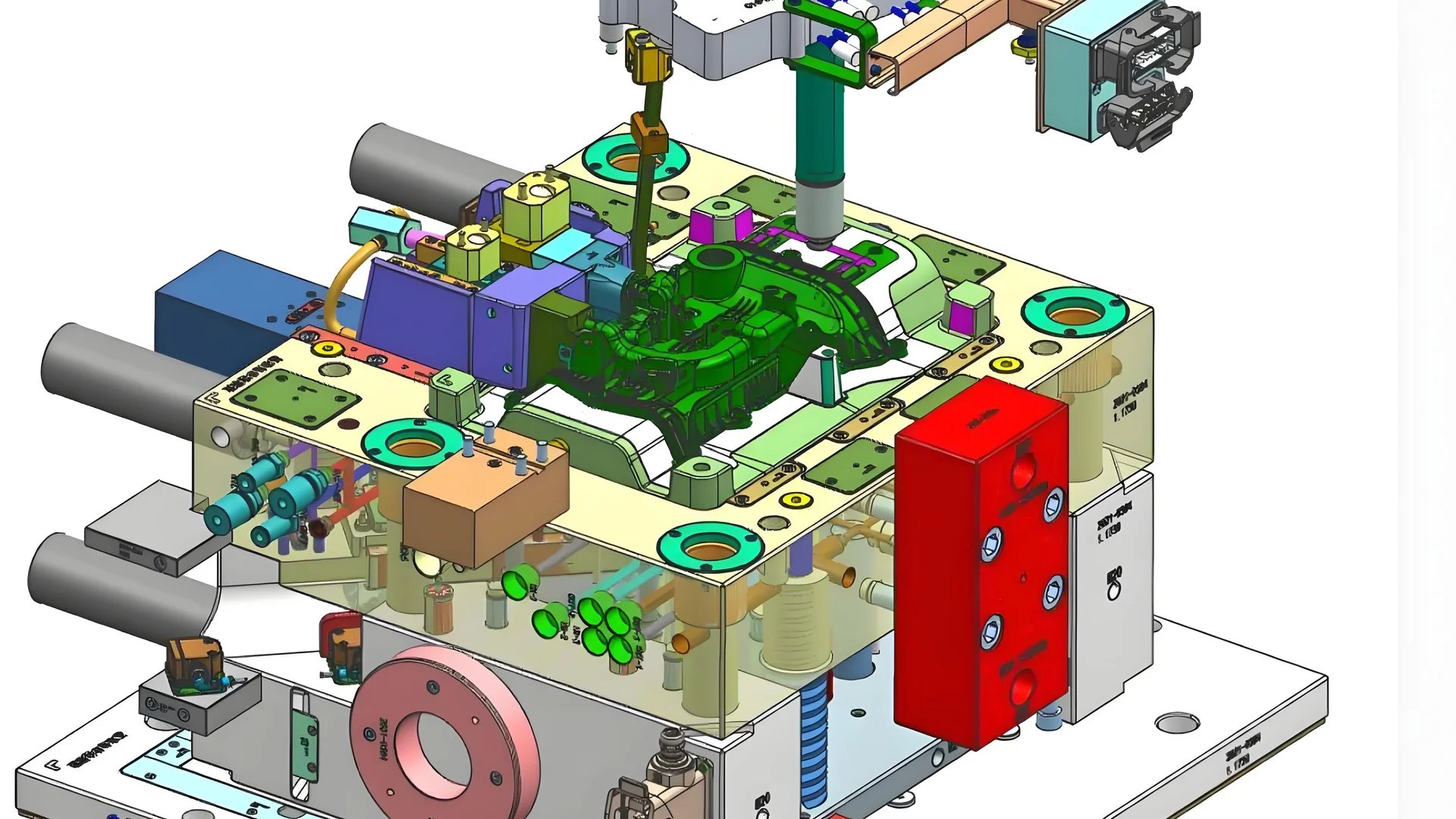
Material Selection and Costs
The complexity of a mold design directly impacts the choice of materials used. For instance, a mold requiring high precision and durability might use H13 steel due to its superior heat resistance and wear properties. However, this choice raises the material costs considerably compared to using less expensive alternatives like P20 steel. The selection of mold core materials4 is crucial as they need to withstand repeated cycles without degrading the quality of the final product.
Design Time and Expertise
Complex designs necessitate more time for product analysis and mold structure planning. Designers need to consider numerous variables such as cavity layout, cooling systems, and parting surface design, especially for products with unique features like multi-directional core extraction. This demands a designer with specialized expertise, which subsequently increases design costs. The process often involves iterative design verification and optimization using advanced software, further adding to the time and cost.
Processing Techniques
The intricacy of a mold’s design also dictates the processing techniques employed. Advanced machining processes like EDM (Electrical Discharge Machining) and wire EDM are often required for precision mold components. These methods are essential for achieving the required tolerances but are more costly compared to conventional machining techniques. For parts with complex geometries or fine features, wire EDM5 provides the necessary precision albeit at a higher cost.
Testing and Trial Costs
Complex designs may require extensive testing and adjustments during trial runs to ensure functionality and performance. This involves using specific plastic materials and professional operators for multiple iterations, increasing both material and labor costs. The more intricate the mold, the higher the likelihood of additional trial phases being necessary to perfect the design.
Overheads and Additional Factors
Beyond direct costs, overheads such as equipment depreciation, site rental, and management expenses also rise with increasing design complexity. Additionally, packaging and transportation might become more complicated and costly due to the specific handling needs of intricate molds.
The methods used for estimating costs6 should reflect these complexities by accounting for additional material and labor expenses associated with sophisticated mold designs.
Complex designs increase mold material costs.True
Complex designs require higher quality materials, raising costs.
Simple designs require advanced machining techniques.False
Advanced machining is needed for complex, not simple designs.
What Are the Key Processing Costs to Consider?
Processing costs in injection molding can significantly influence overall project expenses, making understanding them essential for cost-effective production.
Key processing costs in injection molding include machining, EDM, wire EDM, and surface treatment. These costs vary based on precision requirements, complexity, and equipment used.
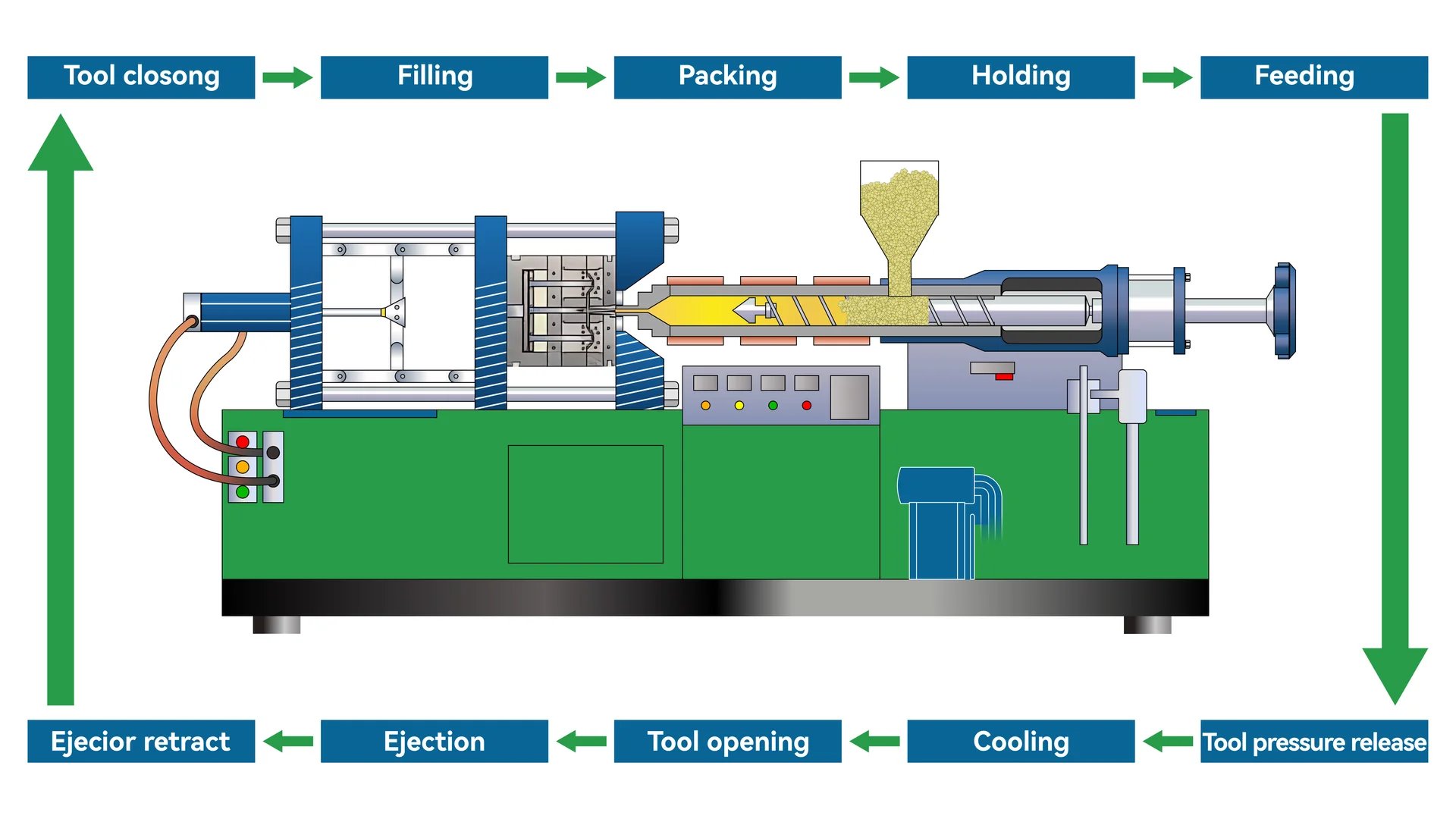
Machining Costs
Machining involves various processes such as milling, grinding, and drilling to achieve the desired dimensions and accuracy for mold components. These costs are determined by the complexity of the design and the precision required. For instance, using high-precision equipment for complex shapes will increase costs.
Process | Factors Affecting Cost | Example Scenario |
---|---|---|
Milling | Complexity and precision | High-precision equipment for complex parts |
Grinding | Material hardness and precision | Softer materials reduce costs |
Drilling | Number of holes and precision | Simple designs with fewer holes |
Electrical Discharge Machining (EDM)
EDM is crucial for creating intricate mold parts like cavities and cores. The cost is higher due to specialized equipment and slow processing speeds. This process is indispensable when high precision is required in challenging areas.
Wire EDM Costs
Wire EDM is utilized for crafting precise mold components, such as tiny holes and slots. The method is renowned for its high accuracy but comes with increased costs, especially for small, complex parts.
Surface Treatment Costs
Surface treatments like quenching, nitriding, and chrome plating enhance the durability and performance of molds. Costs vary widely based on the treatment type and specific requirements. For example, chrome plating may be more expensive but offers excellent wear resistance.
- Quenching: Offers basic hardening but at a lower cost.
- Nitriding: Provides surface hardness without distortion, moderately priced.
- Chrome Plating: Expensive but highly effective for wear resistance.
Understanding these processing costs helps in making informed decisions that balance quality and budget constraints in injection molding projects. Consider consulting with experts or using cost estimation models7 to achieve a comprehensive analysis of potential expenses.
EDM is cheaper than machining for complex parts.False
EDM is typically more expensive due to specialized equipment and slow speeds.
Chrome plating offers the best wear resistance for molds.True
Chrome plating is expensive but provides excellent wear resistance.
How Can Estimation Methods Optimize Your Budgeting?
Effective estimation methods can transform your budgeting process, ensuring resource efficiency and cost-effectiveness in your projects.
By applying estimation methods like empirical calculation, material coefficient, and analogy, businesses can optimize budgeting, predict expenses accurately, and identify potential savings in the injection molding process.
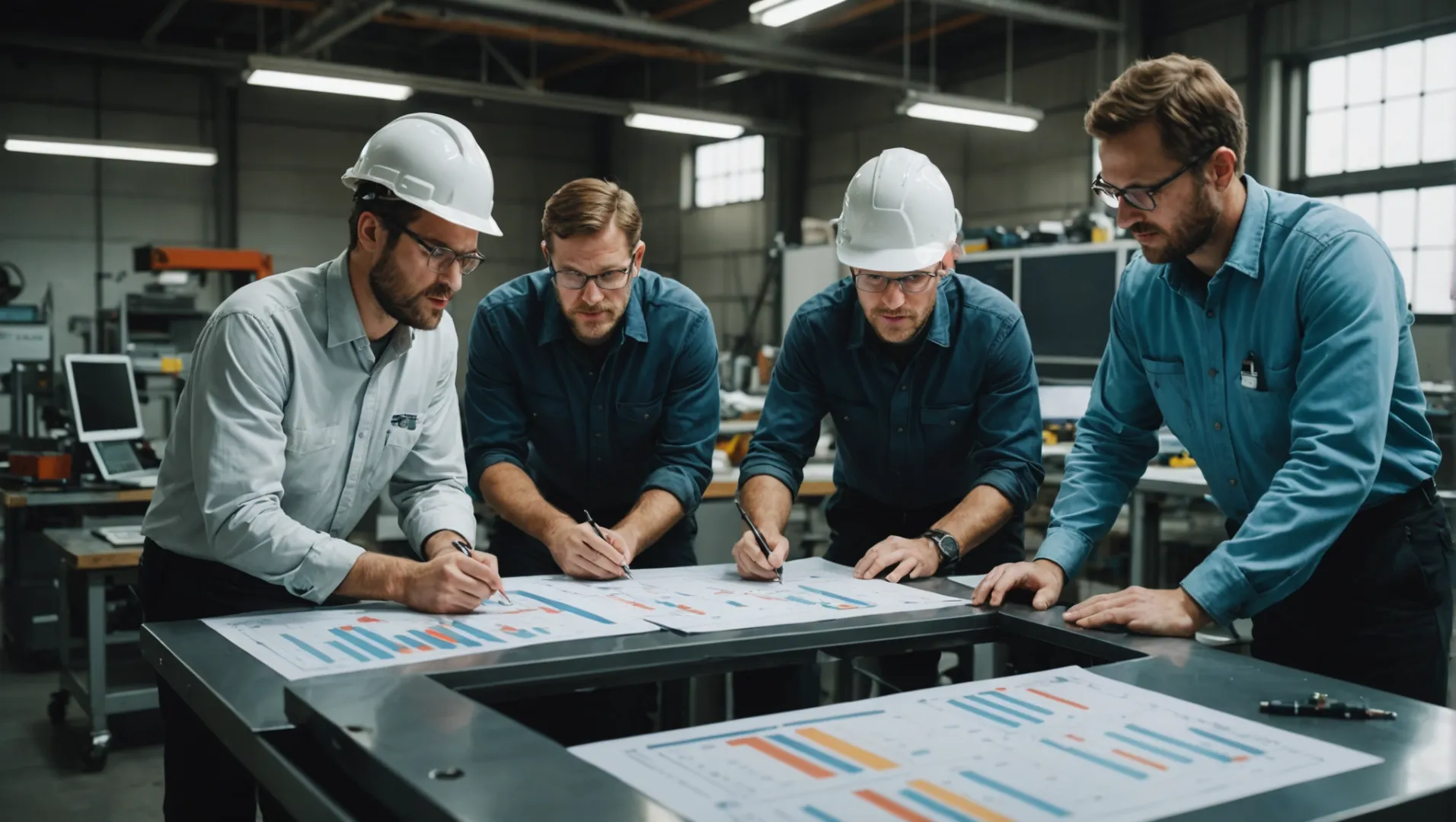
Understanding Estimation Methods
Estimation methods serve as vital tools for businesses looking to control costs and allocate resources effectively. In the context of injection molding, these methods help predict the total cost by breaking down expenses into manageable components.
-
Empirical Calculation Method
This method relies on historical data and industry standards to predict costs. Begin by calculating the total cost of materials, which includes mold core, frame, and standard parts. Design costs are typically estimated as a percentage of the total mold cost, often ranging between 10% and 15%.
Processing costs depend on the complexity of the mold. For example, core processing costs8 might be 1.5 to 3 times the material cost. Consider additional expenses such as testing, management fees, and transportation to reach a comprehensive estimate.
-
Material Coefficient Method
This approach involves calculating the material cost based on the mold’s size and multiplying it by a predetermined factor, typically between 3 and 6 for plastic injection molds. This method is particularly useful when rapid assessments are needed but should be adjusted based on market conditions and specific project requirements.
-
Analogy Method
Utilize this method by referencing similar projects. If a previous mold had comparable requirements, use its cost as a baseline. Adjust this figure to account for any unique features of the current project, like structural complexities or special materials required.
Benefits of Accurate Estimation
Accurate estimation methods provide several advantages:
- Predictive Accuracy: They reduce financial surprises by offering a clear picture of expected expenditures.
- Cost Optimization: Identifying potential areas for savings allows for more strategic allocation of resources.
- Enhanced Negotiation: A well-prepared budget fosters better discussions with suppliers and stakeholders.
By integrating these methods into your budgeting process, you enhance precision and control over your financial planning. For instance, leveraging historical data through the empirical calculation method can uncover areas where previous projects overspent or saved money, providing insights into future budgeting practices.
For further insights into maximizing cost efficiency in mold production, consider exploring similar methodologies9 that align with your specific industry needs.
Empirical method uses historical data for cost prediction.True
The empirical calculation method relies on historical data to estimate costs.
Material coefficient method is best for detailed cost analysis.False
The material coefficient method is used for rapid assessments, not detailed analysis.
Conclusion
Accurate cost estimation in injection molding is vital for budgeting and resource allocation. Understanding each cost component enhances project planning efficiency.
-
Explore different steel types to match cost with desired properties.: The most popular mold steel for plastic injection molding is P-20 Steel, which has strong wear resistance and is reasonably priced. ↩
-
Learn why precision impacts mold performance and cost.: The precision molds of molded products are an important condition to decide whether the products can reach the dimensional tolerance required … ↩
-
Discover how mold flow analysis reduces design errors.: Mold flow analysis (MFA) software simulates the flow of plastic, which allows you to elevate part and mold design to create products of impeccable quality. ↩
-
Discover how varying core materials impact durability and cost.: The core and cavity include the mold cavity and the mold core, which are tightly combined to form the overall shape and internal structure of the mold. ↩
-
Explore how wire EDM achieves high precision in complex molds.: Wire electrical discharge machining (wire EDM) is a process that works by continuously feeding a wire electrode under tension on a vertical axis … ↩
-
Learn effective strategies to estimate costs for intricate designs.: For molds with more complex geometries and primed for larger production runs of approximately 10,000+ units, the cost of mold can range from $5,000 to $100,000. ↩
-
Explore detailed methods to accurately estimate injection molding expenses.: The short answer: plastic injection molds cost anywhere between $100 for a 3D printed low-volume injection mold to $100,000+ for a complex multi-cavity … ↩
-
Discover how core processing impacts overall injection molding expenses.: The short answer: plastic injection molds cost anywhere between $100 for a 3D printed low-volume injection mold to $100,000+ for a complex multi-cavity … ↩
-
Learn innovative strategies to enhance cost efficiency in mold production.: Key strategies include optimizing part design for material and production efficiency, selecting cost-effective materials, ensuring efficient use of molds … ↩