Have you ever wondered how to ensure your molded parts are perfectly uniform? Let’s dive into the art and science of achieving wall thickness uniformity in injection molding!
Controlling wall thickness uniformity in injection molding involves optimizing mold design, adjusting process parameters, selecting appropriate materials, and maintaining equipment. Each step ensures consistent quality and prevents defects such as warping or inconsistent cooling.
By understanding the intricacies of these strategies, manufacturers can enhance their production processes, yielding high-quality parts with minimal defects. Dive deeper into the specifics of each method to elevate your injection molding techniques.
Mold design doesn't affect wall thickness uniformity.False
Mold design is crucial as it determines plastic flow, impacting uniformity.
What Role Does Mold Design Play in Wall Thickness Uniformity?
Mold design is fundamental to achieving uniform wall thickness in injection molding, impacting product quality and performance.
Mold design influences wall thickness uniformity by determining plastic flow, reducing stress concentration, and optimizing cavity and runner layouts. Proper gate placement and balanced runner systems ensure even distribution of material, minimizing defects.
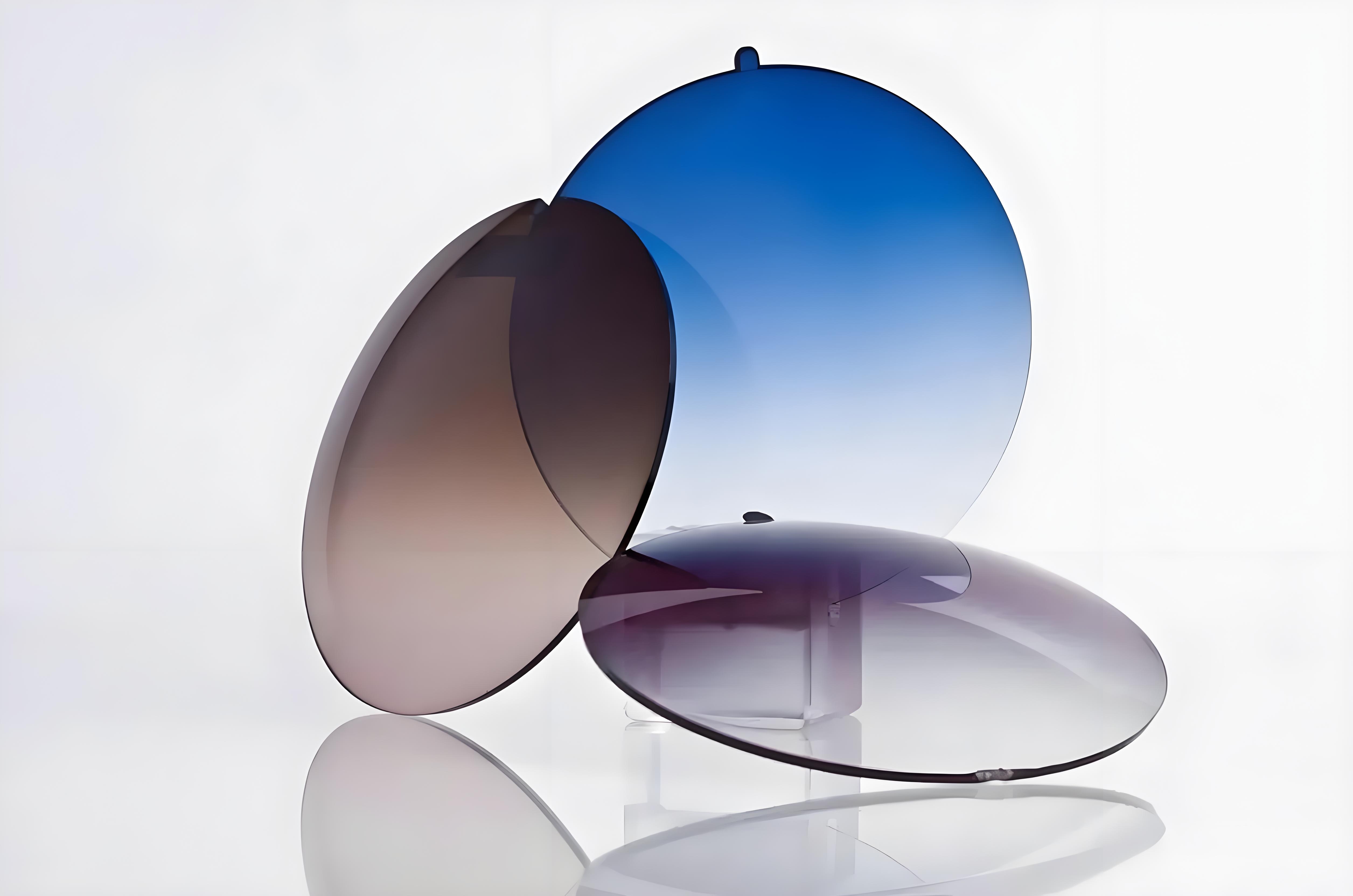
The Significance of Gate Placement
A crucial aspect of mold design1 is the strategic placement of gates. Gates should be positioned near thicker sections of the mold to facilitate a smooth flow of molten plastic into thinner areas. This approach reduces flow imbalance and ensures the entire cavity is filled uniformly. For example, in a part with varying thicknesses, placing the gate closer to thicker sections prevents overfilling in thinner regions.
Balanced Runner Systems
Another important factor is the design of the runner system. A balanced runner layout ensures that the filling time and pressure are consistent across the mold. By optimizing the shape and size of runners, manufacturers can reduce flow resistance, allowing for a more uniform distribution of plastic. An efficient runner system minimizes variations in wall thickness, preventing defects like warping or sink marks.
Aspect | Impact on Uniformity |
---|---|
Gate Placement | Ensures even filling by directing flow |
Runner System Design | Balances pressure and filling time |
Cavity Design Considerations
When designing the cavity, smooth transition curves should connect areas with different wall thicknesses to avoid stress concentrations. Sharp changes in thickness can lead to uneven cooling and subsequent warping. For complex shapes, splitting the cavity into simpler sections can improve control over wall thickness during molding.
Case Study: Implementing Optimized Mold Design
Consider a manufacturer producing automotive parts with varied wall thicknesses. By redesigning the mold with optimized gate placement and a balanced runner system, they achieved a reduction in defects by 25%, enhancing overall product quality. Such real-world examples illustrate the profound impact of mold design on wall thickness uniformity.
By focusing on these key elements within mold design, manufacturers can significantly enhance the consistency of wall thickness, leading to higher quality products.
Gate placement affects wall thickness uniformity.True
Strategic gate placement ensures even material flow, reducing defects.
Balanced runner systems cause wall thickness variations.False
Balanced runners minimize pressure variations, ensuring uniform thickness.
How Can Process Parameters Be Optimized for Consistent Wall Thickness?
Achieving consistent wall thickness in injection molding requires fine-tuning various process parameters. Discover how strategic adjustments can lead to superior product quality.
Optimizing process parameters for consistent wall thickness involves adjusting injection speed, pressure, and holding time. By tailoring these factors to the specific part design and material characteristics, manufacturers can ensure uniformity and reduce defects.
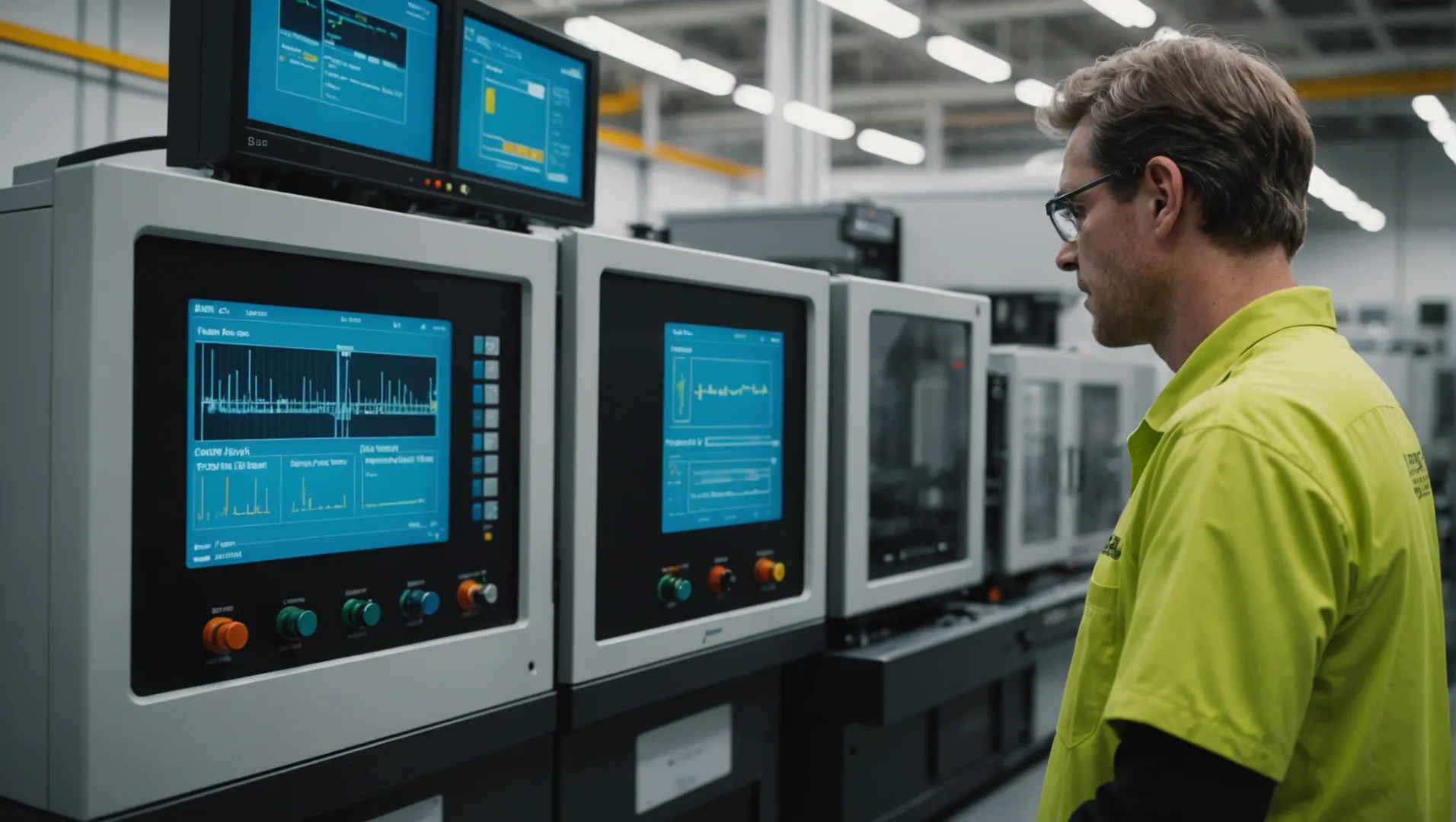
Injection Speed Adjustments
Injection speed is pivotal in controlling wall thickness. During the early filling stage, a higher speed ensures quick cavity fill. However, for areas with varying thickness, a multi-level injection speed control2 can be employed. This allows for faster filling of thicker sections and slower speeds for thinner parts, reducing overfilling risks.
Tailoring Injection Pressure
Excessive pressure may cause overfilling in thin areas while underfilling thicker ones. It’s crucial to set an appropriate injection pressure curve3 based on part shape and wall thickness distribution. Early stages can utilize higher pressures for smooth cavity entry, tapering off as filling progresses to mitigate excessive stress.
Holding Time and Pressure Management
In the holding phase, setting suitable holding time and pressure is vital for compensating material shrinkage and achieving uniform wall thickness. Longer holding times benefit thicker walls, while moderate pressure prevents internal stresses. These adjustments depend on the specific part geometry and material properties.
Parameter | Initial Setting | Adjustment Strategy |
---|---|---|
Injection Speed | High | Multi-level control |
Injection Pressure | High | Gradual reduction |
Holding Time | Short | Increase for thickness |
Holding Pressure | Low | Moderate balance |
By comprehensively understanding and adjusting these parameters, manufacturers can significantly enhance the consistency of wall thickness in their products, leading to higher quality outcomes.
Higher injection speed ensures quick cavity fill.True
Higher speeds fill cavities faster, reducing defects in thicker areas.
Low holding pressure increases internal stresses.False
Moderate holding pressure reduces internal stresses, not low pressure.
Why Is Material Selection Critical for Injection Molding?
Choosing the right material is a cornerstone of successful injection molding, influencing every aspect from performance to cost-efficiency. But why is this choice so pivotal?
Material selection is vital in injection molding as it affects flow properties, shrinkage, and ultimately, the uniformity of wall thickness. The right material ensures consistency, reduces defects, and matches the design specifications, enhancing overall product quality.

Understanding the Role of Material Properties
The properties of the chosen material significantly impact the flow behavior during injection molding. Materials with high fluidity can fill molds more easily, minimizing the risk of defects like voids or incomplete filling. Conversely, materials with poor fluidity may require adjustments in process parameters, such as increasing injection speed or pressure.
Additionally, the shrinkage rate of a material determines how much it will contract upon cooling. Selecting materials with uniform shrinkage characteristics helps maintain consistent dimensions and reduces the risk of warping.
Matching Material to Application Requirements
Not all materials are created equal. Some are designed to withstand high temperatures, while others may offer superior tensile strength or flexibility. It’s essential to choose a material that aligns with the specific application requirements of the final product. For instance, using thermoplastics4 like ABS for parts needing impact resistance can ensure longevity and performance under stress.
Modifying Materials for Enhanced Performance
In some cases, base materials are modified to improve their properties. Additives can enhance fluidity or reduce shrinkage, allowing for better control over wall thickness uniformity. For instance, adding plasticizers can make a material more pliable, while flow aids can facilitate smoother filling of complex mold geometries.
Addressing Moisture Content and Processing Conditions
Before injection molding, it is crucial to ensure that the selected material is properly dried. Moisture can negatively affect fluidity and cause defects in the finished product. Certain materials may also require preheating or the addition of antistatic agents to enhance processing performance. By understanding these requirements, manufacturers can avoid potential pitfalls that compromise product quality.
Considering Environmental and Economic Impacts
Finally, material selection should also consider environmental sustainability and cost-effectiveness. Biodegradable plastics are becoming increasingly popular as manufacturers strive to reduce their ecological footprint. Cost considerations, meanwhile, involve balancing material price with performance benefits to ensure profitability without sacrificing quality.
Material selection in injection molding is an intricate process that demands careful consideration of various factors. By choosing the appropriate material, manufacturers can optimize production efficiency and deliver products that meet both functional and aesthetic standards.
Material fluidity affects mold filling in injection molding.True
High fluidity materials fill molds easily, reducing defects.
All materials have the same shrinkage rate upon cooling.False
Materials vary in shrinkage rates, affecting dimension consistency.
How Does Equipment Maintenance Affect Wall Thickness Control?
Proper maintenance of injection molding equipment is vital for controlling wall thickness, ensuring uniformity, and reducing defects.
Equipment maintenance in injection molding impacts wall thickness control by ensuring machine accuracy and reliability. Regular servicing, monitoring, and upkeep of machinery components like the injection system and sensors help maintain consistent process parameters, leading to uniform wall thickness and high-quality products.
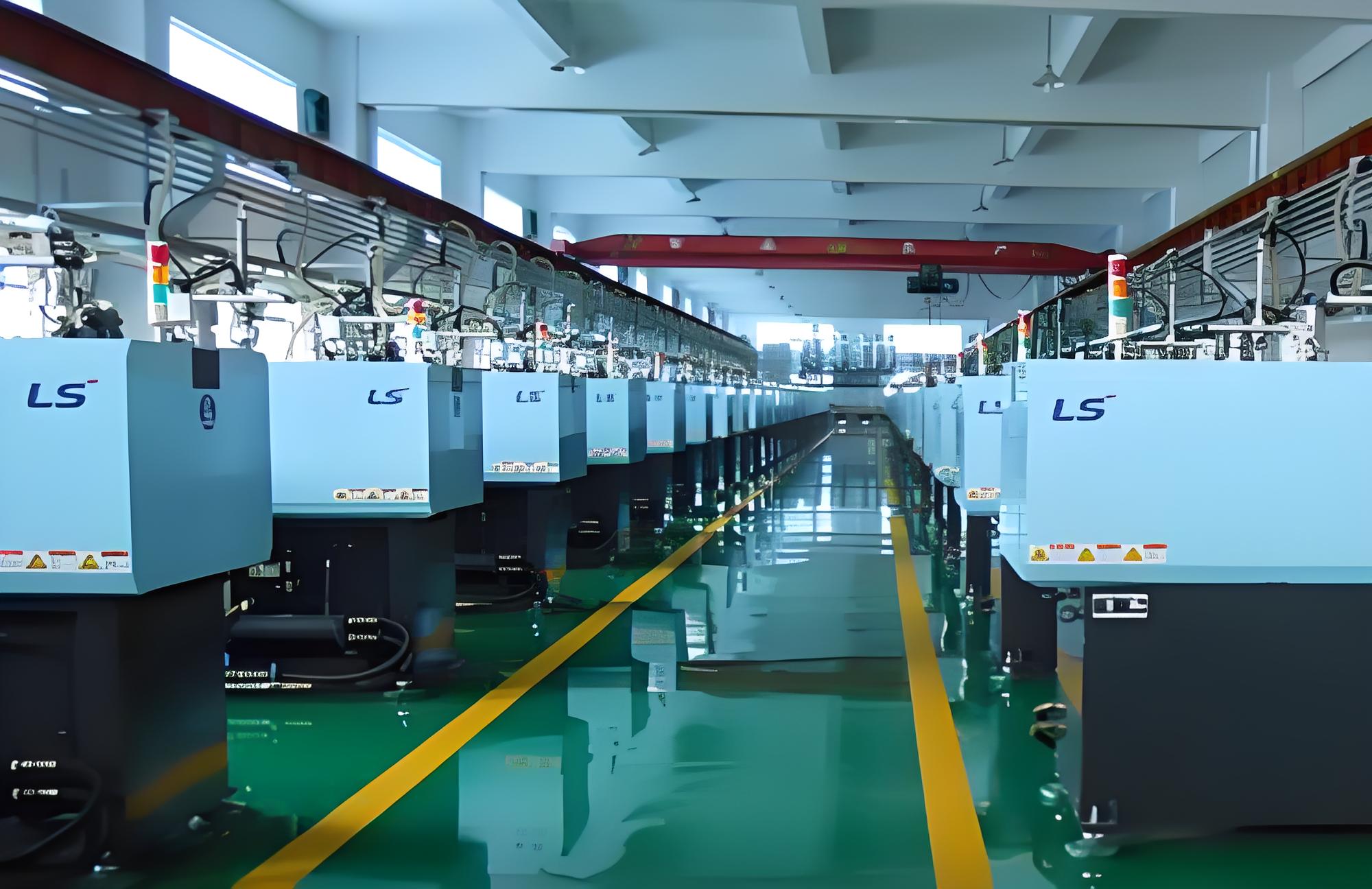
Importance of Regular Equipment Maintenance
Regular maintenance of injection molding machines is essential for maintaining their performance and accuracy. It involves routine inspections and servicing of the injection system, clamping system, and hydraulic system. This ensures these components operate efficiently, preventing deviations that could lead to uneven wall thickness.
A well-maintained machine reduces the risk of unexpected breakdowns, ensuring that production continues smoothly without interruptions that can affect wall thickness consistency. Regular cleaning prevents impurities from entering the plastic, which can compromise the molding quality.
Role of Process Monitoring Systems
Advanced process monitoring systems, such as pressure and temperature sensors, are critical in ensuring consistent wall thickness. These systems provide real-time data that allows for immediate adjustments to process parameters, helping to maintain uniformity.
By integrating advanced monitoring technologies5, manufacturers can fine-tune settings like injection speed and pressure to adapt to changes in material behavior or environmental conditions, thus enhancing wall thickness control.
Establishing a Quality Control System
Implementing a robust quality control system is crucial in detecting deviations in wall thickness early. Regular testing and analysis of injection molded parts can identify issues quickly, allowing for timely corrective actions.
A systematic approach to quality control involves setting benchmarks for acceptable variations in wall thickness and employing tools like statistical process control (SPC) to monitor these variations. This proactive strategy not only helps in maintaining uniformity but also improves overall product quality.
Importance of Training and Documentation
Ensuring that operators are well-trained in equipment maintenance protocols is essential for consistent wall thickness. Comprehensive training programs should cover routine maintenance tasks, troubleshooting techniques, and the use of monitoring systems.
Additionally, maintaining detailed documentation of maintenance activities can help identify patterns in machine performance and guide future maintenance efforts. This documentation serves as a valuable resource for understanding how specific maintenance practices impact wall thickness control.
By integrating training programs6 and detailed documentation into the maintenance strategy, manufacturers can ensure that equipment operates at optimal levels, consistently producing high-quality parts.
Regular maintenance ensures uniform wall thickness.True
Routine servicing prevents deviations in machine performance, maintaining consistency.
Advanced sensors have no impact on wall thickness control.False
Sensors provide real-time data for adjustments, ensuring uniformity.
Conclusion
Achieving uniform wall thickness in injection molding is a blend of art and science. By honing in on design, parameters, materials, and maintenance, you can dramatically enhance product quality.
-
Discover how gate placement affects material flow and wall uniformity.: In injection molding, each cavity in a mold must contain a small opening called a gate, which allows hot plastic to enter the cavity before passing through … ↩
-
Learn how multi-level speed control ensures even cavity filling.: Strength at the Seams: High-speed injection can enhance the strength of the weld lines, making them less noticeable. Prevention of Cooling Deformities: A swift … ↩
-
Discover how adjusting pressure curves impacts product quality.: Walls in any plastic-molded part should be no less than 40 to 60 percent that of adjacent walls, and all should fit within recommended thickness ranges for the … ↩
-
Explore thermoplastics’ diverse applications and their benefits in injection molding.: Thermoplastic molding is a manufacturing process that works to create fully functional parts by injecting plastic resin into a pre-made mold. ↩
-
Learn how cutting-edge sensors improve process consistency and product quality.: Kistler offers sensors to monitor cavity pressure and temperature in the injection molding process – the fundamental basis for efficient monitoring and control. ↩
-
Explore training programs that enhance operator skills in equipment upkeep.: This program details procedures for proper mold care before, during, and after a production run – stressing important safety considerations for mold handling. ↩