All Posts
blog & article
read our latest newsletter
Whether you’re curious about material selection, product design, mold design, mold making and injection molding, feel free to ask us anything. Our team is ready to provide the guidance and insights you need.
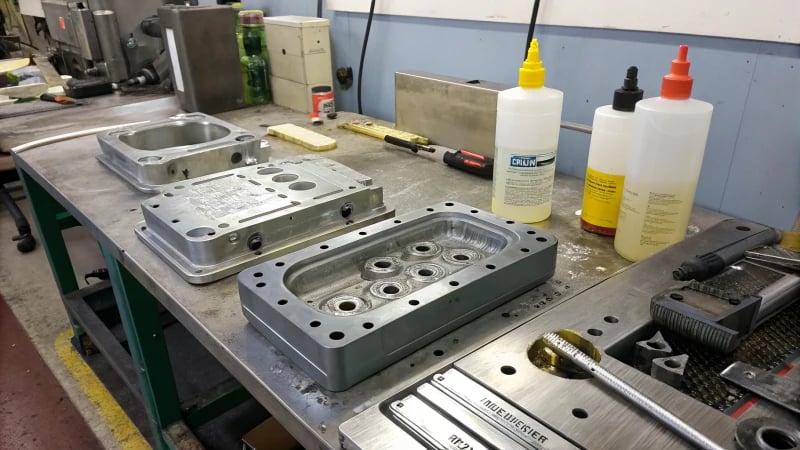
What Are the Steps to Successfully Plate Injection Molded Parts?
Plating injection molded parts involves several critical steps to ensure a successful outcome. Start with thorough cleaning using solvents like ethanol to remove contaminants. Next, enhance surface roughness through mechanical or chemical methods for better adhesion. Sensitization and activation treatments ...
Quality Inspection
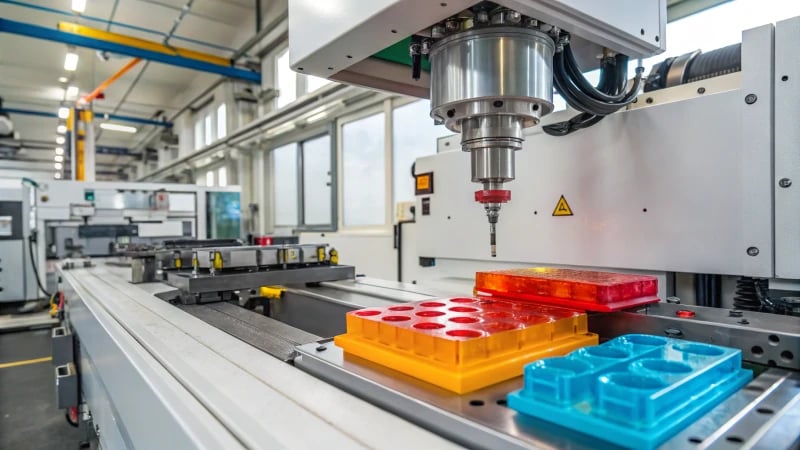
How Can You Balance Quality and Cost in Injection Molding?
This article explores how to balance quality and cost in injection molding by focusing on raw material selection, mold design, and process optimization. It emphasizes the importance of choosing high-strength materials like polyamide for durability while also considering cost-effective alternatives ...
OPTIMIZATION
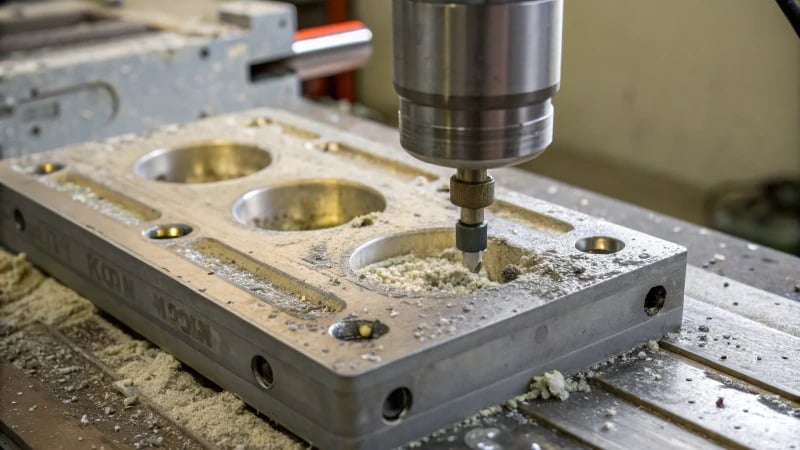
How Can You Identify Signs of Wear and Tear in Injection Molds?
This article discusses how to identify signs of wear and tear in injection molds that can affect product quality. Key indicators include dimensional deviations, surface quality deterioration, and increased filling pressure. Recognizing these early signs can prevent costly repairs and ...
Quality Inspection

What Are the Best Strategies to Reduce Costs in Injection Molding?
Reducing costs in injection molding requires a strategic approach that includes optimizing mold design by selecting the right number of cavities and simplifying structures. Choosing cost-effective materials like general-purpose plastics over engineering ones can significantly lower expenses while maintaining product ...
OPTIMIZATION
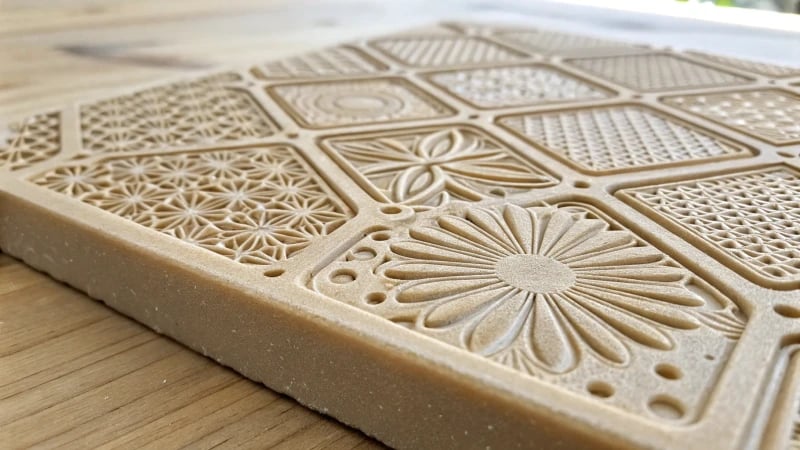
How Can You Texture Injection Molded Surfaces Effectively?
This article delves into the various techniques for effectively texturing injection molded surfaces. Methods such as chemical etching, laser texturing, electrospark machining (EDM), and physical vapor deposition (PVD) are explored in detail. Each technique offers unique benefits tailored to different ...
MANUFACTURING

What Are the Mechanics Behind a Three-Plate Mold?
Three-plate molds are essential tools in plastic manufacturing, consisting of a fixed plate, an intermediate runner plate, and a moving plate. This design allows for improved efficiency and quality control by enabling flexible sprue systems and precise melt flow paths. ...
MANUFACTURING
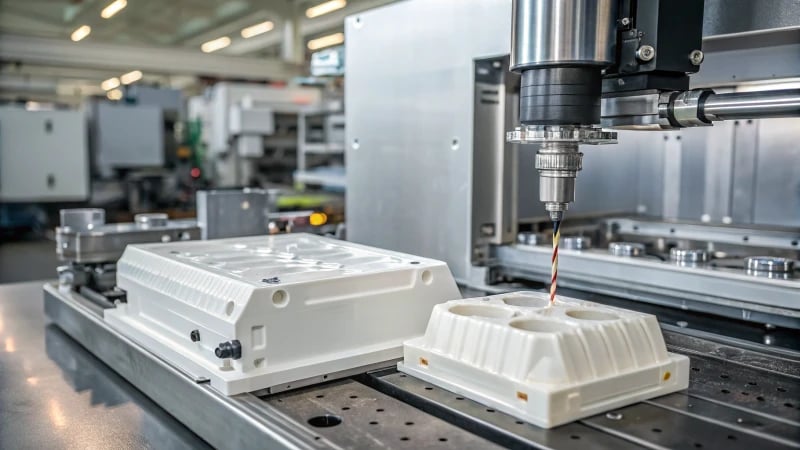
How Can You Effectively Prevent Knit Lines in Injection Molding?
Knit lines can compromise the appearance and durability of injection-molded products. To effectively prevent them, focus on optimizing mold design through strategic gate placement, runner system improvements, and exhaust setup. Adjusting process parameters such as temperature, speed, and pressure is ...
OPTIMIZATION

What Are Effective Solutions for Fixing Short Shots in Injection Molding?
Short shots in injection molding can disrupt production and lead to defective parts. This article provides practical solutions to tackle this issue by focusing on key factors such as melt flow rate (MFR), temperature sensitivity of materials, gate design, runner ...
OPTIMIZATION
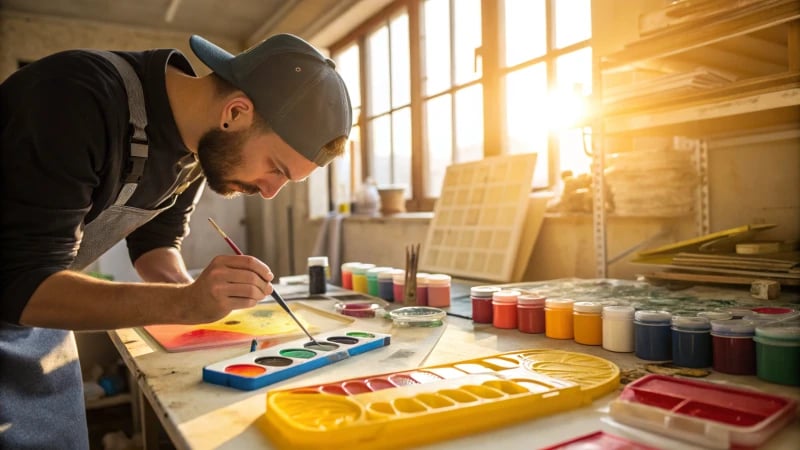
What Are the Best Techniques for Painting Injection Molded Products?
This guide explores the best techniques for painting injection molded products. It emphasizes the importance of meticulous surface preparation, selecting compatible paints based on material properties, and applying them using appropriate methods like spraying or brushing. The article also discusses ...
OPTIMIZATION
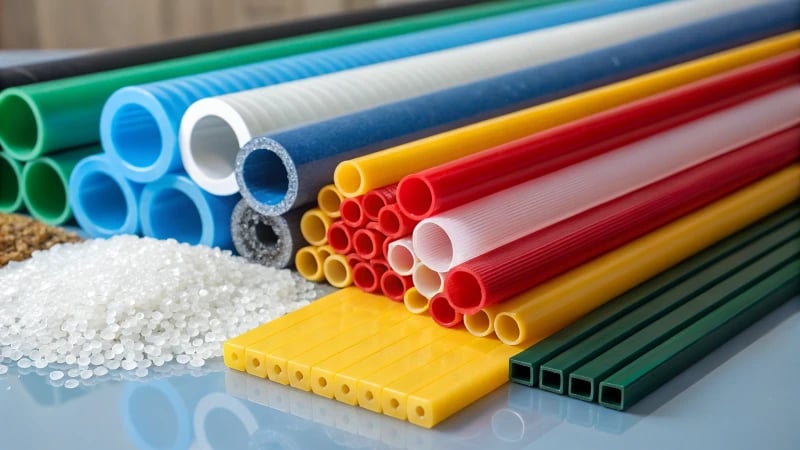
What Are Engineering Plastics and How Are They Used in Injection Molding?
Engineering plastics have transformed manufacturing by providing high-performance materials that excel in injection molding. These plastics offer exceptional mechanical strength, thermal stability, and chemical resistance, making them ideal for creating intricate and reliable parts. Commonly used types include polyamide (nylon) ...
Materials Recommendations
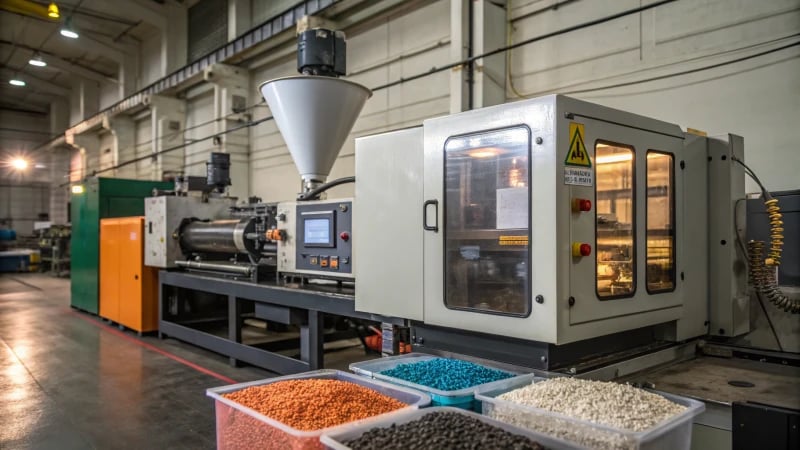
Is Bakelite Suitable for Injection Molding?
Bakelite can be effectively used in injection molding, but it presents unique challenges due to its thermosetting properties. This article explores the essential requirements for successful Bakelite molding, including precise temperature control during both the injection and curing phases. Adequate ...
MANUFACTURING
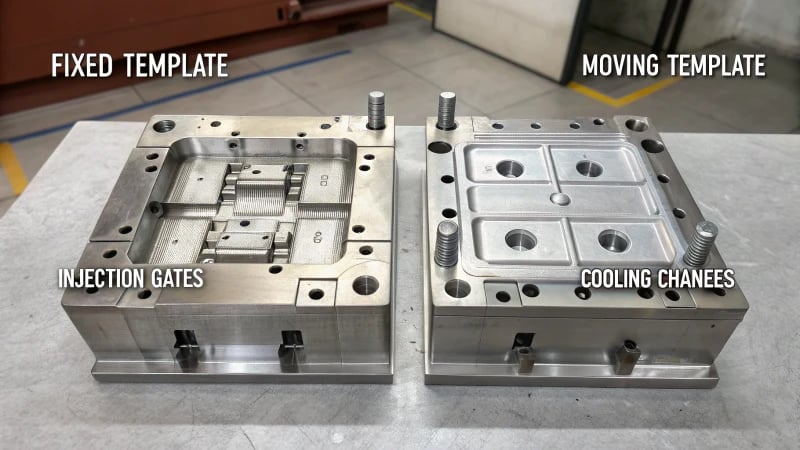
How Does a Two-Plate Mold Function in Injection Molding?
Two-plate molds are essential in injection molding, featuring a moving and fixed template that forms the cavity for molten plastic. Their straightforward design allows for efficient production of various plastic components, including consumer electronics cases, toys, and containers. While they ...
MANUFACTURING
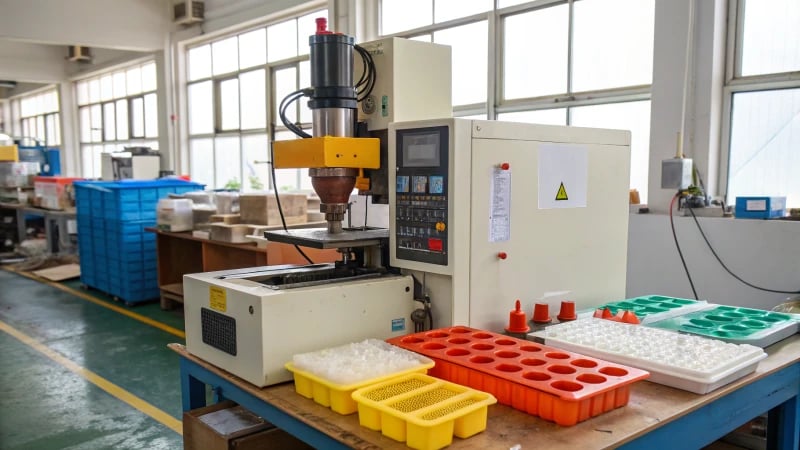
How Does Desktop Injection Molding Work?
Desktop injection molding is a compact and efficient process that allows users to create small plastic parts directly from their workbench. These machines are designed for low clamping forces, making them suitable for prototyping, educational purposes, and hobbyist applications. The ...
Uncategorized
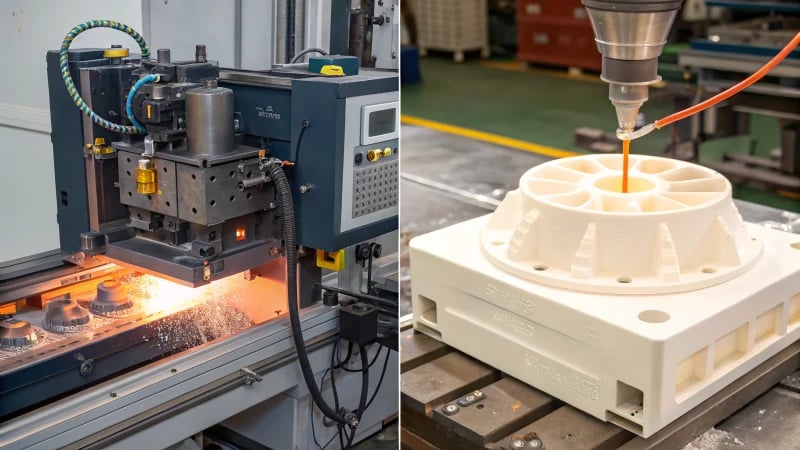
Injection Molding vs. Rotational Molding: What’s the Difference?
This article explores the differences between injection molding and rotational molding, two key manufacturing processes for plastic parts. Injection molding is best suited for high-volume production of intricate designs, utilizing molten plastic injected into precise molds under high pressure. In ...
MANUFACTURING
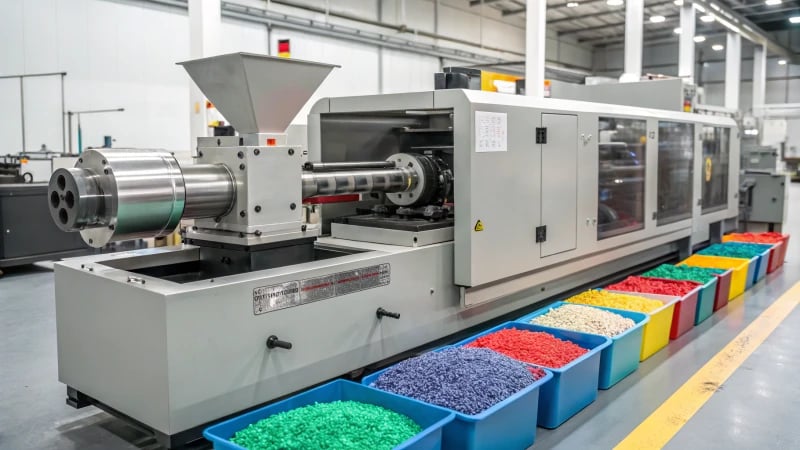
How Does Bakelite Injection Molding Differ from Other Plastic Injection Molding?
This article explores the distinct characteristics of Bakelite injection molding compared to other plastic processes. Key differences include a 1:1 screw compression ratio for Bakelite versus 1:3-1:4.5 for thermoplastics, and the fusing process of Bakelite at higher temperatures (150-180°C) compared ...
MANUFACTURING
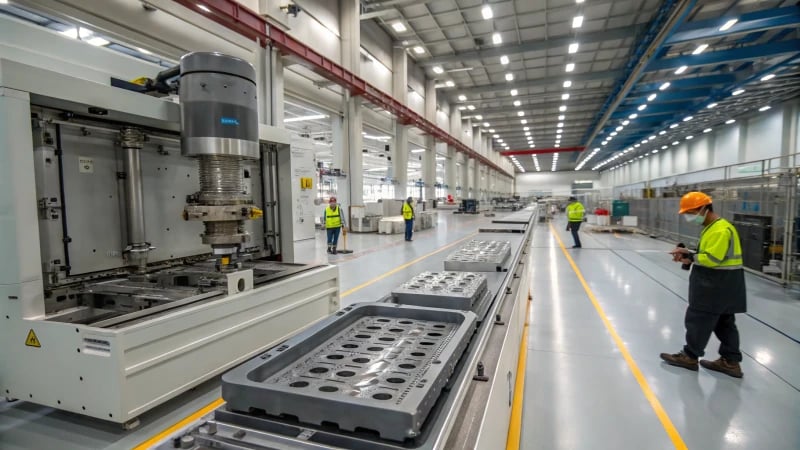
How Efficiently Can an Injection Molding Machine Operate with 6 Cavity Molds?
This article explores the efficient operation of injection molding machines using 6-cavity molds. Key factors include adequate clamping force to prevent defects like flash, sufficient injection capacity to fill all cavities uniformly, proper mold mounting for compatibility with machine specifications, ...
MANUFACTURING
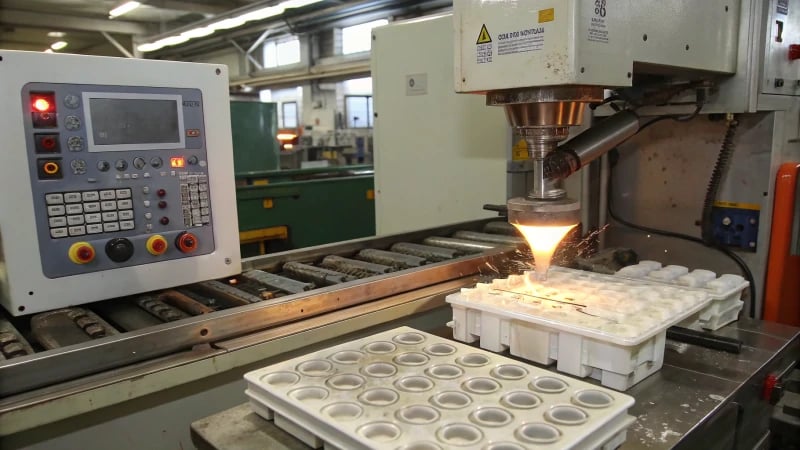
How Does an Injection Molding Machine Create Button Molds?
This article explores how injection molding machines produce button molds. It details the importance of mold design, including cavity shape and ejection systems, as well as material selection like ABS and polypropylene. The injection molding process involves melting plastic pellets, ...
MANUFACTURING
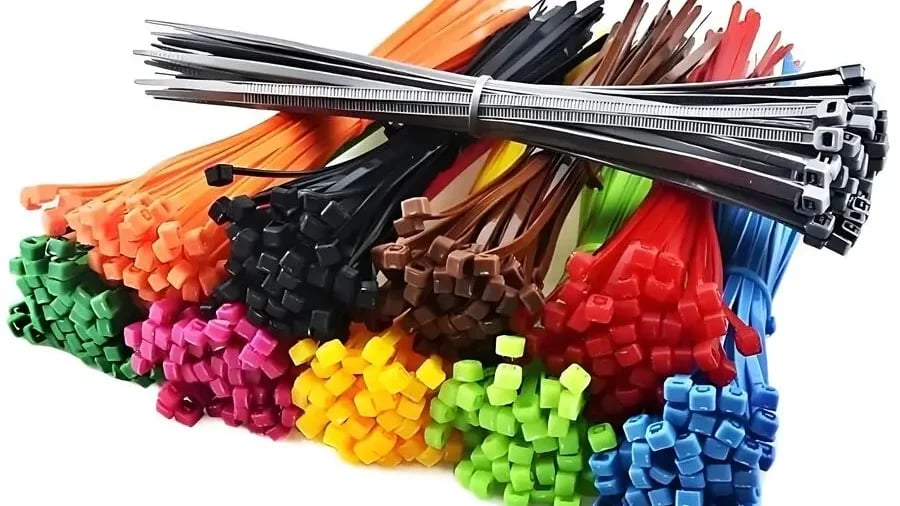
How Does an Injection Molding Machine Produce a Nylon Cable Tie?
This article explores how injection molding machines create nylon cable ties. It details the importance of mold design, material selection (Nylon 6/6), and the injection molding process. Each step is crucial for producing durable and flexible cable ties that meet ...
MANUFACTURING

How Can Injection Molding Machines Be Used to Manufacture Phone Cases?
Discover how injection molding machines manufacture phone cases by heating plastic pellets, injecting them into molds, and maintaining strict quality control. This process involves precise mold design, material selection like TPU or PC, and rigorous inspections to ensure each case ...
MANUFACTURING
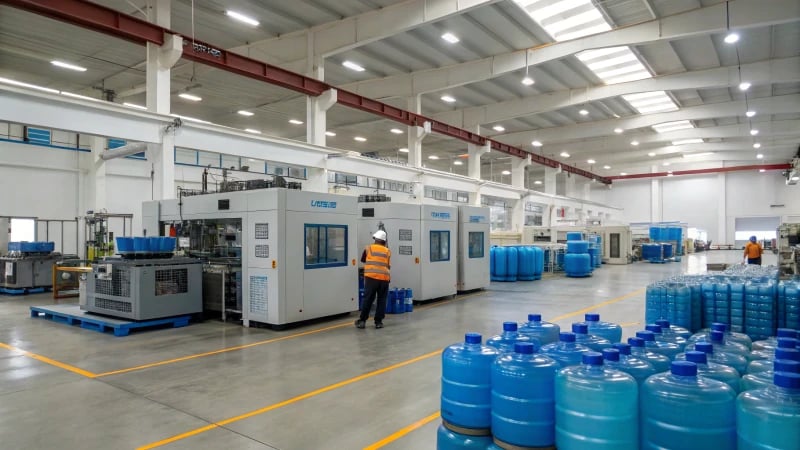
How Do Injection Molding Machines Produce Water Tanks?
This article explores how injection molding machines produce water tanks, detailing the intricate processes involved from mold design to material selection. It highlights the importance of choosing suitable thermoplastics like HDPE and PP for their durability and chemical resistance. The ...
MANUFACTURING
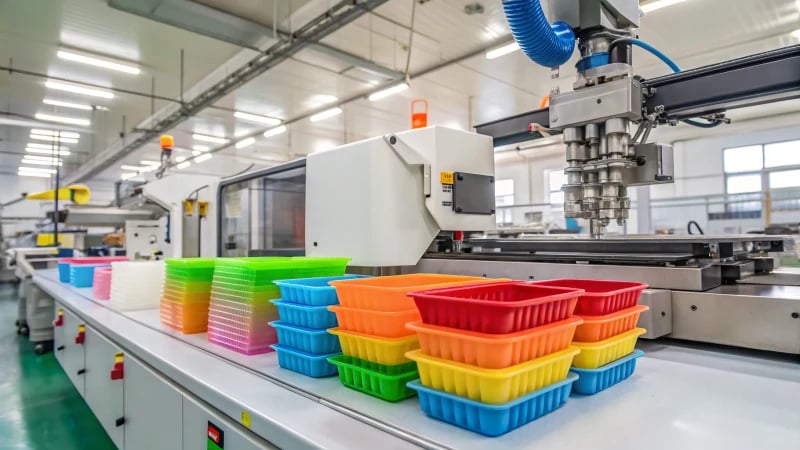
How Can Injection Molding Revolutionize the Production of Food Containers?
Injection molding is transforming the production of food containers by enhancing efficiency and sustainability. This process utilizes food-grade plastics like polypropylene and high-density polyethylene to create durable, safe containers that comply with FDA regulations. Key considerations include selecting appropriate materials, ...
MANUFACTURING
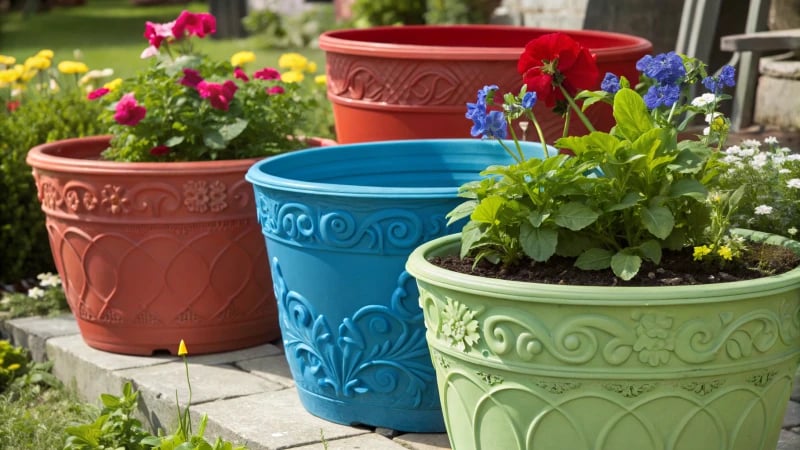
How Can Injection Molding Machines Be Used to Manufacture Flower Pots?
This article explores how injection molding machines are utilized to manufacture flower pots. It details the process of designing custom molds, selecting appropriate materials like polypropylene and HDPE, and the efficient injection-molding method that produces consistent, high-quality pots. The advantages ...
MANUFACTURING
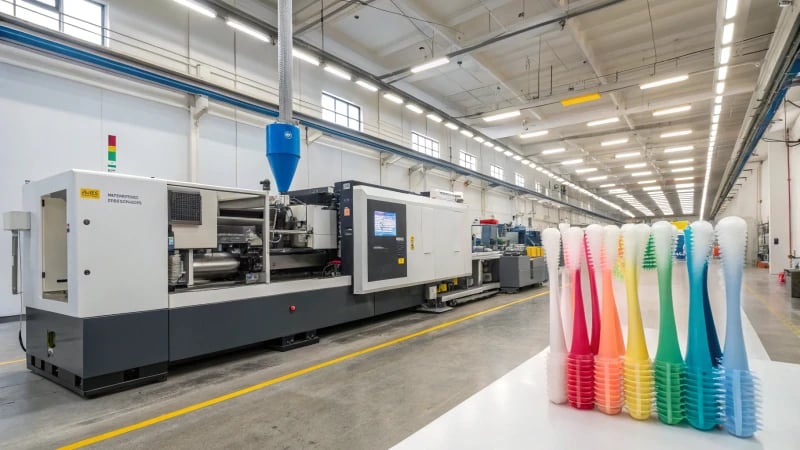
How Are Toothbrushes Made Using Injection Molding Machines?
This article explores the fascinating process of toothbrush manufacturing through injection molding. It details how complex molds are designed to create ergonomic handles and heads, the selection of thermoplastic materials like polypropylene for durability and flexibility, and the precise injection ...
MANUFACTURING
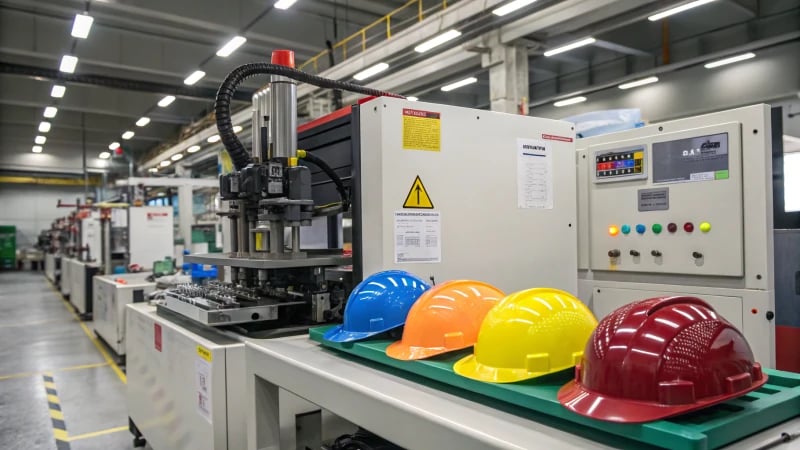
How Can an Injection Molding Machine Be Used to Make Helmets?
This article explores how injection molding machines are used to manufacture helmets. It covers material selection, including polycarbonate and ABS for their impact resistance and cost-effectiveness. The importance of mold design is highlighted, detailing how molds must conform to the ...
MANUFACTURING
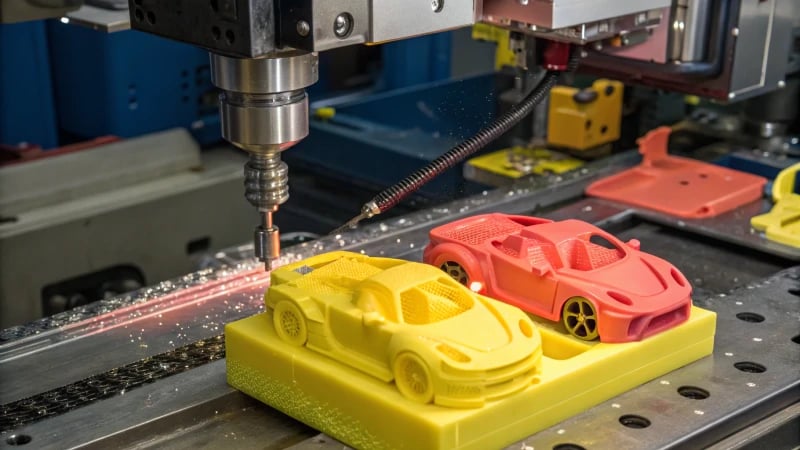
How Can an Injection Molding Machine Create a Toy Car?
This article explores how injection molding machines manufacture toy cars. It details the critical steps involved: designing molds for car bodies, wheels, and axles; selecting appropriate plastics like ABS and PMMA; executing the injection molding process by melting pellets and ...
MANUFACTURING
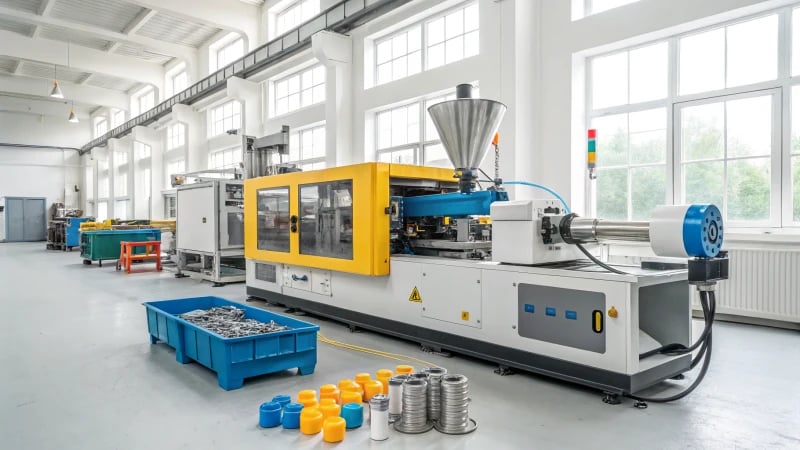
Can Injection Molding Machines Produce Both PPR and PVC Fittings?
This article explores how injection molding machines can produce both PPR (polypropylene random copolymer) and PVC (polyvinyl chloride) fittings. It highlights the advantages of using injection molding for each material, detailing the unique process requirements for optimal production. For PPR, ...
MANUFACTURING
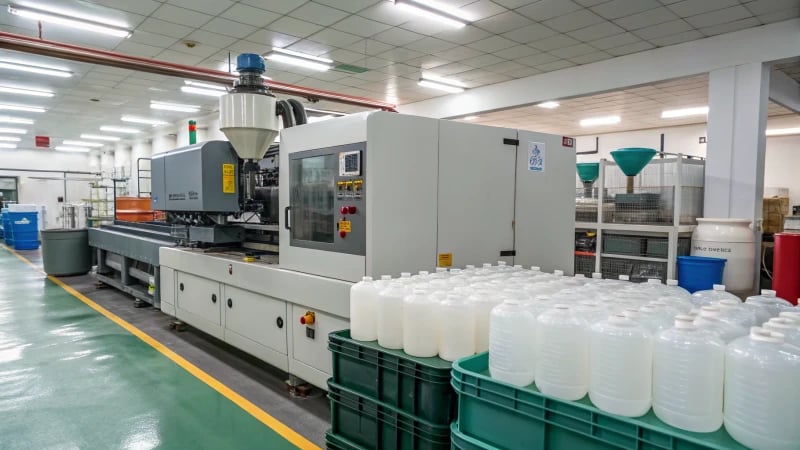
Die Casting vs. Injection Moulding: What Are the Key Differences?
This article explores the key differences between die casting and injection moulding, two essential manufacturing processes. Die casting primarily uses non-ferrous metals like aluminum and zinc, requiring high temperatures and pressures to create strong, precise components. In contrast, injection moulding ...
MANUFACTURING
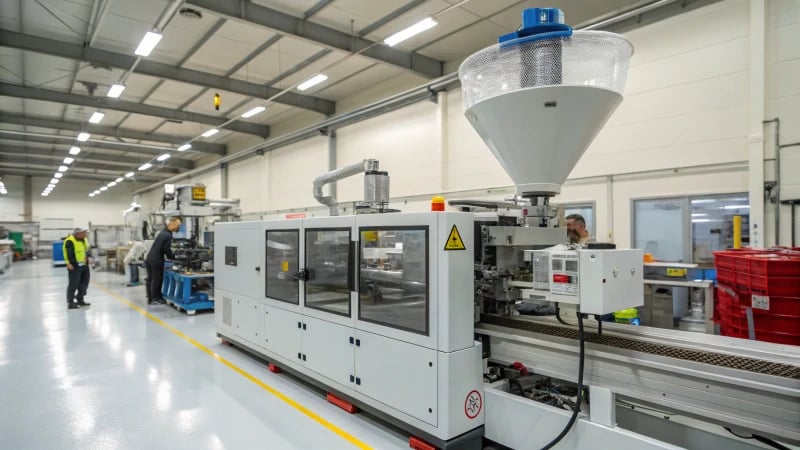
How Efficiently Can an Injection Molding Machine Produce PVC Fittings?
This article explores how injection molding machines produce PVC fittings with efficiency. It highlights the importance of material compatibility, custom mold design, and process control in achieving high-quality outputs. Additionally, it addresses challenges such as heat stability and the need ...
MANUFACTURING
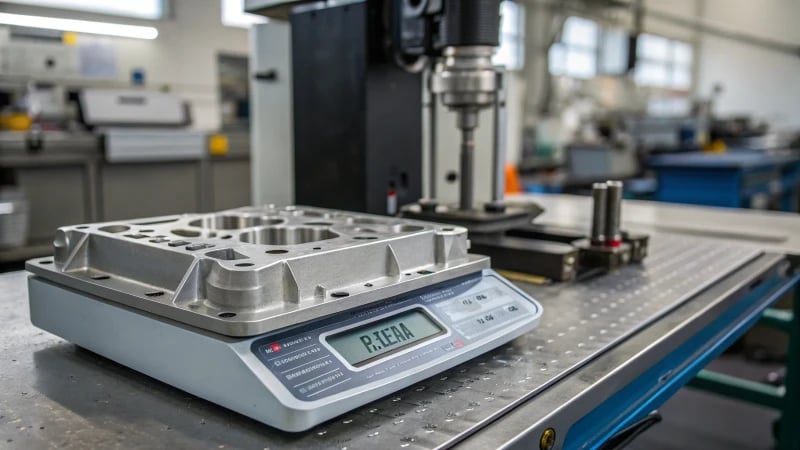
What Are the Most Effective Ways to Reduce Part Weight in Injection Molding?
Reducing part weight in injection molding is crucial for enhancing efficiency and sustainability. Key strategies include optimizing design through wall thickness reduction, incorporating hollow structures, and refining rib designs. Material selection plays a vital role; using lightweight polymers like polyethylene ...
DEVELOPMENT
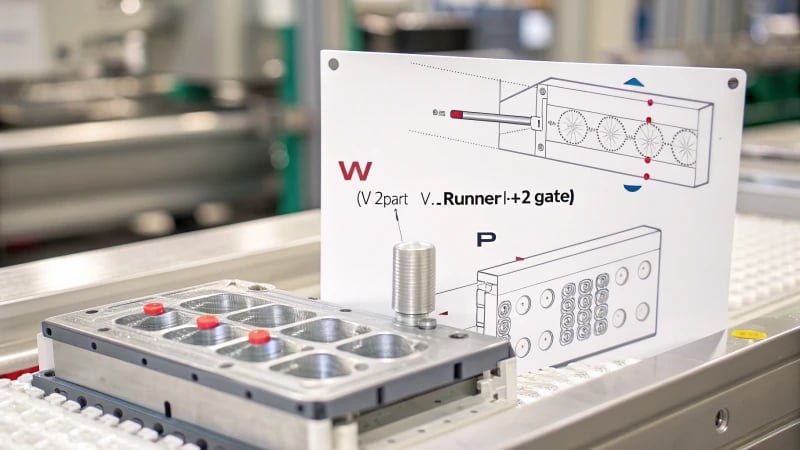
What Are the Steps to Calculate Shot Weight in Injection Molding?
Calculating shot weight in injection molding is essential for optimizing material use and product quality. This guide outlines the steps to determine shot weight using theoretical methods—calculating part volume with geometric formulas—and practical approaches like machine metering systems or weighing ...
MANUFACTURING