When I began working with plastic molding, I soon noticed something important. This craft needs more than just technical skills. Understanding small details really matters in raising product quality. Here are some of the best practices I picked up during my journey.
For the best results in plastic molding, focus on perfecting mold design. Improve cooling systems for better efficiency. Regular mold maintenance is vital. Select ideal gate locations for smooth material flow. Arrange cooling channels carefully. Really stick to a maintenance schedule for molds.
Throughout my journey in plastic molding, I learned to appreciate the detailed process of design, cooling and maintenance. Each stage has valuable lessons. Mold design, manufacturing and usage each teach something important. I remember facing uneven wall thickness in my first project. This issue was very frustrating. Then, I learned how important gate design is. Now, I prioritize optimizing that part. Finding the right spot for the gate really changes everything.
Optimizing mold design improves product quality in plastic molding.True
A well-designed mold can enhance the precision and efficiency of the plastic molding process, leading to higher-quality products.
Proper maintenance of molds is unnecessary for effective molding.False
Regular maintenance is crucial for ensuring molds function correctly and produce consistent results in plastic manufacturing.
What Should You Consider When Designing a Mold?
The world of mold design offers an exciting journey for a designer. Understanding important factors really lifts your skills. The quality of the plastic parts you produce can improve dramatically. Let’s discover this realm together!
When designing a mold, look at where to put the gate for the best flow. Plan the cooling system layout to be even everywhere. Design the exhaust so it avoids defects. Pay attention to accuracy during manufacturing. Think about improving the surface quality. Regular maintenance is important for long-lasting molds. Maintenance keeps the molds working well and produces quality items.
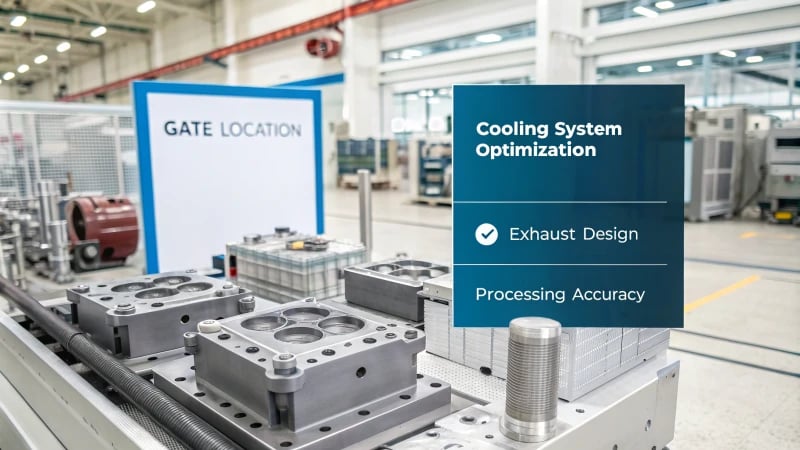
Understanding the Mold Design Stage
The mold design stage is crucial as it sets the foundation for successful plastic part production. Key considerations include:
-
Gate Design Skills: The gate location must be strategically selected, ideally at the thicker wall, to ensure smooth plastic flow and minimize defects. For example, when designing a plastic shell with uneven thickness, positioning the gate at the center of the thickest area can enhance filling efficiency.
-
Cooling System Optimization: Uniform cooling channel layout is essential. For uniform wall thickness, channels can be straight or spiral. However, for varying thicknesses, channels should be closer to thicker areas to prevent warping. For instance, denser cooling channels should be placed near thick-walled reinforcing ribs in parts.
Detailed Gate Design Considerations
The selection of gate types should align with product requirements:
Gate Type | Application | Benefits |
---|---|---|
Latent Gate | Products requiring high aesthetic quality | Leaves minimal gate marks after demolding |
Pinpoint Gate | Thin-walled, high-precision products | Controls flow speed and direction effectively |
For instance, using a pinpoint gate for mobile phone shells ensures both appearance and dimensional accuracy are met.
Importance of Cooling System Design
In the cooling system design, the choice of medium is significant:
- Water: Common due to cost-effectiveness and efficiency.
- Oil: Considered for applications needing rapid cooling or precision.
Example: When injecting optical lenses, controlling the cooling medium’s flow rate and temperature is critical to reducing internal stress.
Exhaust Design for Quality Assurance
Proper exhaust design prevents defects like bubbles and burns:
- Venting grooves should be adequately sized (0.02-0.05mm depth, 3-5mm width).
- Special materials like breathable steel can be used in deep-cavity applications to improve exhaust efficiency.
Key Considerations in Mold Manufacturing Stage
During manufacturing, maintaining processing accuracy is vital. Here’s a look at key dimensions and tolerances:
Dimension | Tolerance Range | Importance |
---|---|---|
Cavity Size | ±0.01mm | Affects overall product fit and function |
Gate and Runner Size | ±0.01mm | Ensures proper material flow and filling |
Using high-precision equipment (CNC machining, EDM) guarantees these tolerances are met.
Enhancing Surface Quality for Optimal Performance
Surface quality impacts both aesthetics and function:
- Polishing and nitriding improve mold surface characteristics, enhancing durability and demolding performance.
- For high-finish requirements, such as in automotive parts, surface roughness may need to achieve Ra0.01-0.05μm.
Mold Use and Maintenance Considerations
Mold trials are critical for quality control before mass production. Important aspects include:
- Adjustments Based on Trial Results: Observing defects like flash or bubbles allows for adjustments in pressure or gate size.
- Parameter Recording: Keeping track of temperatures and pressures during trials aids future production accuracy.
Regular Maintenance Practices for Longevity
To extend the life of molds, consider these maintenance practices:
- Regular Cleaning: Prevent accumulation of residue using specialized cleaning agents.
- Lubrication of Moving Parts: Ensuring smooth operation can be done every 1,000 to 5,000 products produced.
By focusing on these key considerations, designers like Jacky can enhance product quality and production efficiency effectively. To learn more about best practices in mold design, check out our detailed articles on mold design techniques1 and cooling optimization strategies2.
Gate location affects plastic flow efficiency in mold design.True
Strategically placing the gate at thicker areas enhances filling efficiency and minimizes defects during production.
Regular cleaning of molds is unnecessary for production quality.False
Regular cleaning prevents residue buildup, which can negatively impact the quality and longevity of molds in production.
How Does Cooling System Optimization Affect Product Quality?
Have you ever thought about how a cooling system affects a product’s quality? This idea may seem surprising. But really, better cooling methods greatly impact manufacturing. These improvements can really boost product performance. They also reduce faults.
Improving cooling systems directly affects how good a product is. It achieves this by spreading temperature evenly. It also shortens the cycle time during manufacturing. Better cooling really minimizes defects in products. It helps products hold their shape better. Structural integrity improves a lot.
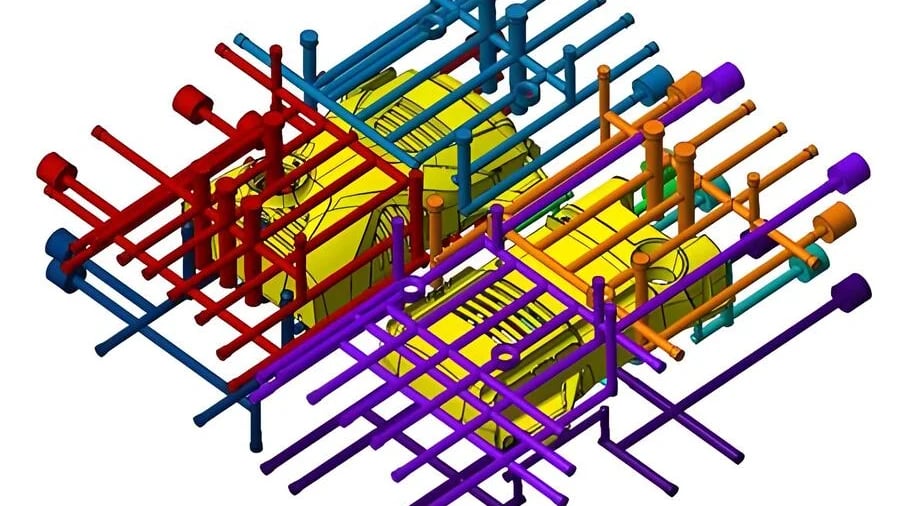
Understanding Cooling System Optimization
Cooling system improvement is key to producing better products during manufacturing. It provides even temperature distribution, which helps reduce cycle times and avoid defects. In my experience, focusing on these aspects showed a big change in our products.
For example, mold design is crucial. Cooling channel arrangements are vital. A good cooling system can stop warping and size errors. This is important for complex shapes, where uneven cooling causes defects. I remember working on a detailed mold and realizing that the design of the cooling channels was crucial – our product was perfect!
The Role of Mold Design
Good cooling begins at the mold design phase. Gate design is very important. Gate positions should be at thicker wall sections for smoother plastic flow. I learned how this simple change could prevent defects from excessive flow resistance.
Example:
- For plastic shell products, placing the gate at the thick wall center ensures good flow.
- Larger molds, like pallet molds, often need multiple gates for even filling.
Gate Selection and Its Impact on Quality
Choosing the right gate type is really important:
Gate Type | Use Case | Benefits |
---|---|---|
Latent Gate | Products with high appearance quality requirements | Minimal gate marks post-demolding |
Pinpoint Gate | Thin-walled, high-precision products | Precise control of flow speed and direction |
For example, when designing mobile phone shells, pinpoint gates kept both shape accuracy and look appealing. Details like this attract customers.
Importance of Cooling Medium
Choosing a cooling medium also matters a lot. Water is common because it’s cheap and cools well. Yet sometimes, oil is better for faster cooling or higher precision.
Example:
- For precise optical lenses, managing cooling water’s flow and temperature can greatly minimize internal stresses, improving quality.
Exhaust Design’s Influence on Product Quality
Exhaust design is very important too! Poor mold exhaust can cause bubbles or burning. Good venting grooves help avoid these issues. Deep-cavity molds benefit from breathable steel cores to enhance exhaust efficiency, ensuring products come out right.
Overall Impact on Production Efficiency
Using a strong cooling system plan not only improves product quality but also improves production efficiency. It reduces cycle times. When I applied these methods, I saw everything run better. It was rewarding to consistently produce high-quality products.
If interested in learning more about cooling systems, check out this interesting article3. It provides deeper insights into cooling system improvements and their benefits in industrial settings.
Cooling system optimization reduces manufacturing defects.True
Optimized cooling systems ensure uniform temperature, minimizing defects and enhancing product quality during manufacturing processes like injection molding.
Gate design impacts the flow of plastic during molding.True
The placement of gates in mold design significantly influences plastic flow, affecting product quality and dimensional accuracy in injection molding.
How Can I Maintain Molds for Long-Term Performance?
Mold maintenance is very important for every manufacturer. Years in the industry taught me valuable lessons. I discovered that careful upkeep really changes results. Let’s look at some main ways I found to improve mold life and efficiency.
Successful mold care includes routine cleaning to stop buildup. Regular inspections check for possible issues. Lubrication keeps moving parts smooth. Cooling systems need adjusting for product quality and long life. These practices help manufacturers avoid expensive repairs. They also improve efficiency in production over time.
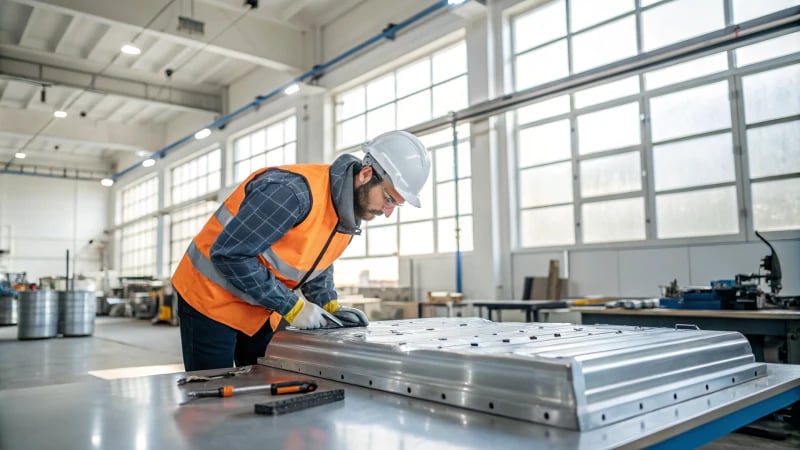
Understanding Mold Maintenance Practices
Maintaining molds is crucial to ensuring their long-term performance, especially in manufacturing contexts where precision and reliability are paramount. Proper maintenance not only prolongs the lifespan of molds but also enhances production quality.
-
Routine Cleaning
To keep molds working well for a long time, I have found a few basic steps that really help. Routine cleaning is important. Regular inspections are necessary. Lubricate moving parts often. Optimize cooling systems to stop defects. High production quality is important. Let me share some insights from my own journey in this field.Regular cleaning prevents plastic residue and dirt accumulation, which can lead to defects in the molded products. Using specialized cleaning agents helps maintain mold integrity.
For optimal results, consider the following cleaning techniques:
Cleaning Method | Description | Frequency |
---|---|---|
Soft Brushes | Gently remove debris without damaging surfaces | After every production run |
Compressed Air | Blow out dust and loose particles | Weekly |
Chemical Cleaners | Use specialized agents for stubborn residues | Monthly |
- Inspection and Lubrication
Routine inspections help identify potential issues before they escalate. Key areas to inspect include:- Cooling Channels: Ensure they are clear of blockages to maintain consistent cooling rates.
- Moving Parts: Lubricate sliders and ejectors regularly to prevent wear and tear.
Cooling System Optimization
The cooling system plays a significant role in the performance of molds. Proper design and maintenance of cooling channels can greatly impact the efficiency of the molding process.
- Design Considerations: Ensure cooling channels are uniformly distributed based on product wall thickness.
- Medium Selection: Water is typically used, but for specialized applications, other cooling mediums may be beneficial.
Trial and Adjustment Practices
Before putting molds into production, thorough trial runs are essential. During these trials, it’s vital to monitor for defects and adjust parameters as needed:
- Common Issues: Look for signs of material shortages or flash.
- Adjustment Strategies: Increase injection pressure or modify gate sizes based on trial observations. This iterative process ensures molds are fine-tuned for optimal performance.
- Documentation of Trials
Record all parameters during trials, such as temperature, pressure, and material flow rates. This documentation is invaluable for future troubleshooting and maintenance strategies.
Preventive Maintenance Schedule
Implementing a preventive maintenance schedule can significantly enhance mold longevity. Here’s a suggested maintenance timeline:
Maintenance Task | Frequency | Purpose |
---|---|---|
Mold Cleaning | After each production | Prevent residue buildup |
Lubrication of Moving Parts | Every 1,000 – 5,000 products | Ensure smooth operation and reduce wear |
Cooling Channel Check | Monthly | Identify blockages or leaks |
Comprehensive Inspection | Quarterly | Assess overall mold condition |
Conclusion
By applying these comprehensive maintenance practices, manufacturers can significantly enhance the longevity and performance of their molds, ensuring quality production and reducing costs associated with repairs or replacements. To learn more about optimizing your mold maintenance, check out these techniques4.
Routine cleaning prevents mold defects in production.True
Regular cleaning of molds eliminates residue and dirt, ensuring high-quality molded products and preventing defects during manufacturing processes.
Lubrication is unnecessary for mold maintenance.False
Lubricating moving parts is essential to prevent wear and tear, ensuring smooth operation and extending the lifespan of molds in production.
What Common Challenges Do Designers Face with Plastic Molds?
As a designer, I often face many challenges when working with plastic molds. This is especially true in the complex field of injection molding. Let’s explore some of these obstacles together.
**Designers often deal with problems related to plastic molds. Issues may arise from mold design, like gate placement or from cooling systems, exhaust design problems, processing accuracy, material selection, mold trials and ongoing upkeep. Grasping these challenges is very important for creating top-notch products and smooth production processes.
- Challenges in Mold Design
When designing molds, everything starts at the mold design stage, where mistakes are very easy to happen. One critical part is gate design. On a project, I placed a gate incorrectly, causing major flow issues. Ideal gate placement is at thicker wall sections to allow smoother plastic melt flow. For a plastic shell with uneven wall thickness, putting the gate in the thick area really helped. This small change made a big difference.
Larger or complex shapes probably need multiple gates for uniform filling. In one project, I designed a mold for a big plastic pallet. Using several edge gates worked wonders and led to an even fill. What a relief that was!
The gate type also counts. A latent gate reduces visible marks on high-quality items, while a pinpoint gate lets me control flow direction for thin-walled objects like phone cases.
- Cooling System Optimization
Next is cooling system optimization. This part probably feels like a juggling act. Proper layout of cooling channels is essential; they must be evenly spread based on product shape and wall thickness. My first mold warped because of badly-placed cooling channels. This mistake taught me a lot.
Choosing a cooling medium is another vital factor. I typically use water for its efficiency and low cost. For projects needing quicker cooling, oil has been useful. Changing flow rates and temperatures really refined my cooling strategies.
- Exhaust Design Issues
Poor exhaust design can cause problems like bubbles or burning in products. I once treated venting grooves as an afterthought. It ended badly! Proper venting grooves on the mold parting surface are crucial, especially for deep cavities. Generally, I choose grooves between 0.02-0.05mm in depth and 3-5mm in width. Using breathable materials for deep cavities improves exhaust efficiency significantly. It really makes a difference.
- Challenges During Mold Manufacturing
After finalizing designs, the real challenge is during manufacturing. Precision here is vital. I maintain tight control over processing accuracy, especially for key aspects like cavity size and gate details. For molds in high-precision electronics, tolerances must be within ±0.01mm. Absolutely no room for error!
Surface quality is very important too. Techniques like polishing and nitriding vastly improve mold surface conditions and extend their life.
- Material Selection and Heat Treatment
Choosing the right material for mold construction is quite daunting. For high-wear plastics, I use high-hardness steel like H13 after precise heat treatment. This choice ensures optimal performance.
- Mold Trial and Adjustment Challenges
I always do thorough mold trials before mass production to catch defects early. These may include lack of material or bubbles. Trial results guide adjustments, varying from increasing injection pressure to changing gate sizes.
- Regular Mold Maintenance
Regular upkeep is crucial for molds’ best performance. It includes cleaning to prevent residue buildup and lubricating moving parts occasionally – every 1,000 to 5,000 units produced. Keeping cooling channels clear hugely contributes to mold longevity.
For detailed insights on these challenges, explore our mold design strategies. Knowing these common issues has really helped me improve product quality and production processes in my work.**

1. Challenges in the Mold Design Stage
Designing a mold is a complex task that involves several crucial decisions that can greatly affect the product outcome. One common challenge is gate design. Selecting the appropriate gate location is vital. For instance, the gate should ideally be placed at the thicker wall to facilitate smoother flow of the plastic melt. This helps prevent defects caused by excessive flow resistance. When designing a plastic shell with uneven wall thickness, positioning the gate in the center of the thick wall area can lead to better results.
Moreover, for large or complex shapes, multiple gates may be necessary to ensure uniform filling. For example, using multiple edge gates for a large plastic pallet allows for quick and even filling of the cavity. Additionally, the choice of gate type must align with product requirements. A latent gate minimizes visible marks on high-quality appearances, while a pinpoint gate controls flow direction effectively for thin-walled products like mobile phone shells.
2. Cooling System Optimization
Another significant challenge lies in optimizing the cooling system. Proper layout of cooling channels is essential; they should be uniformly distributed based on product shape and wall thickness. For items with varying thickness, cooling channels must be strategically placed near thicker sections to prevent warping.
Product Type | Recommended Cooling Channel Layout |
---|---|
Uniform Wall Thickness | Straight or Spiral Channels |
Uneven Wall Thickness | Denser Channels near Thick Walls |
The choice of cooling medium also impacts efficiency. While water is commonly used due to its cost-effectiveness, alternatives like oil may be employed for faster cooling needs. Adjusting flow rates and temperatures can further refine cooling effectiveness.
3. Addressing Exhaust Design Issues
Inadequate exhaust design can lead to defects such as bubbles or burning in products. Implementing venting grooves at the mold parting surface and ensuring they are appropriately sized is critical. For deep-cavity products, using breathable materials can enhance exhaust efficiency. The recommended dimensions for venting grooves typically range from 0.02-0.05mm in depth and 3-5mm in width.
4. Challenges During Mold Manufacturing
Once the design is finalized, precision during manufacturing becomes paramount. Maintaining strict control over processing accuracy is crucial, especially for key dimensions like cavity size and gate specifications. For example, molds used for high-precision electronics often require tolerances within ±0.01mm, necessitating high-precision equipment like CNC machining centers.
The surface quality of molds also plays a critical role in product performance. Techniques such as polishing and nitriding can improve mold surface conditions and longevity.
5. Material Selection and Heat Treatment
Selecting the right material for mold construction can pose challenges as well. Molds intended for high-wear plastics must utilize materials that can withstand significant stress and wear, such as high-hardness steel like H13, which requires specific heat treatment processes to achieve optimal performance.
6. Mold Trial and Adjustment Challenges
Before mass production, conducting thorough mold trials is essential to identify defects such as lack of material or bubbles. Adjustments based on trial observations can include increasing injection pressure or adjusting gate sizes.
7. Regular Mold Maintenance
Finally, regular maintenance is crucial for ensuring optimal performance of molds. This includes cleaning to prevent residue buildup and lubricating moving parts periodically, such as every 1,000 to 5,000 units produced. Ensuring that cooling channels remain clear and operational also contributes significantly to mold longevity.
For more insights on overcoming these challenges, check out our detailed resources on mold design strategies5. Understanding these common issues can help designers like Jacky enhance product quality and streamline production processes.
Gate design impacts the quality of molded plastic products.True
Proper gate placement is crucial for ensuring smooth plastic flow and preventing defects in the final product.
Regular mold maintenance is unnecessary for optimal performance.False
Routine maintenance, including cleaning and lubrication, is essential to ensure molds operate effectively and last longer.
Conclusion
Discover best practices for optimizing plastic mold design, cooling systems, and maintenance to improve product quality and manufacturing efficiency.
-
This link provides expert insights into advanced mold design techniques that can enhance your production process. ↩
-
Explore effective strategies for optimizing cooling systems in mold design to improve product quality. ↩
-
Discover detailed strategies for optimizing your cooling systems and enhancing product quality in manufacturing processes. ↩
-
Explore advanced mold maintenance techniques that can save costs and enhance production efficiency. ↩
-
Explore this link for expert insights on overcoming challenges in plastic mold design and manufacturing to improve your projects. ↩