Injection molding is a craft that combines precision and creativity. It’s all about getting those tiny details just right.
Ensure injection mold accuracy through precise CAD modeling, strict tolerance management, advanced quality control, and regular maintenance and calibration of mold machinery.
Remember when you first learned to ride a bike? Wobbling at first, but with practice, each ride became smoother. Ensuring mold accuracy is a bit like that—it takes time and attention to detail. Diving deeper into strategies like precise CAD modeling and quality control can transform your approach, ensuring every product meets its mark. Let’s explore how these techniques can boost your injection molding processes, making them as smooth as a well-oiled machine.
CAD modeling is essential for mold accuracy.True
Precise CAD modeling ensures the design matches production needs.
Regular maintenance is unnecessary for mold accuracy.False
Maintenance prevents wear and tear, ensuring consistent mold precision.
What Are the Key Factors Affecting Mold Accuracy?
Have you ever wondered why some molds produce perfect products while others just miss the mark?
Key factors affecting mold accuracy include material properties, design intricacies, machining precision, and environmental conditions. Mastery of these elements ensures optimal mold performance and consistent, high-quality manufacturing.
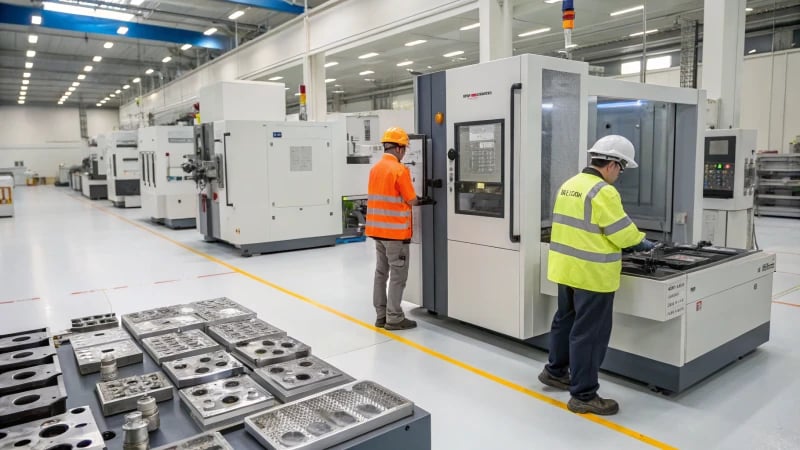
Material Properties
I remember the first time I chose a material for a mold without fully understanding its properties. It was a learning moment when I realized how much thermal expansion and wear resistance could affect dimensional stability1. Selecting a material with high thermal conductivity, for instance, can lead to more uniform temperatures, reducing warping and prolonging mold life.
Design Intricacies
The complexity of a mold design can sometimes feel like solving a puzzle. Early in my career, I learned the hard way that overlooking factors like wall thickness and draft angles can lead to serious issues like uneven cooling2. Since then, I’ve relied heavily on CAD software to simulate scenarios and catch potential design flaws before they become costly mistakes.
Machining Precision
Precision in machining is akin to art—it’s all about the details. Even with state-of-the-art CNC machines, I’ve found that the skill of the operator plays a pivotal role. Regular calibration and maintenance are non-negotiables in my book, ensuring that each product meets the exact specifications without any unpleasant surprises in final product dimensions3.
Environmental Conditions
I once worked on a project where temperature fluctuations wreaked havoc on our mold accuracy. The experience taught me the importance of controlling environmental conditions. By setting up sensors to monitor temperature and humidity, we managed to keep the molds from expanding or contracting unpredictably, safeguarding our product dimensions and maintaining consistent accuracy4.
Operational Parameters
Finding the right balance of injection speed, pressure, and temperature during molding can feel like a dance. It took several trials—and a lot of documentation—to perfect these settings for various materials and designs. Now, I see it as an opportunity to tweak and optimize processes continually.
Factor | Impact on Accuracy |
---|---|
Material Choice | Affects thermal expansion and dimensional stability |
Design Complexity | Influences cooling patterns and potential defects |
Machining Precision | Determines tolerance levels in mold creation |
Environmental Control | Prevents mold distortion due to temperature changes |
Operational Settings | Ensures appropriate pressure and speed during molding |
Every factor from material properties to operational settings plays a crucial role in determining mold accuracy. Embracing these challenges has not only improved my work but also deepened my appreciation for the intricate dance of mold-making.
Material choice affects mold's dimensional stability.True
Different materials expand differently with temperature changes, impacting stability.
Operator skill is irrelevant to machining precision.False
Operator skill ensures machines are used correctly, affecting precision.
How Does CAD Software Enhance Mold Precision?
Ever wondered how a simple idea becomes a precise, tangible mold? Let me take you on a journey where CAD software turns concepts into reality, with a touch of personal insight.
CAD software enhances mold precision through detailed design visualization, accurate process simulations, and precise dimensional control, reducing errors and improving production performance.
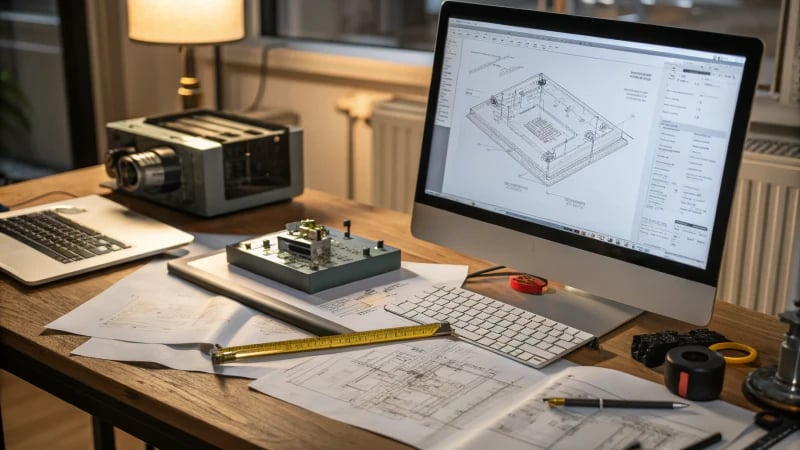
Visualization and Design Accuracy
When I first started using CAD software, it felt like opening a door to a new dimension of creativity. Imagine being able to see your mold design in 3D before it’s even made. I remember one project where this capability saved us from a costly mistake—visualizing the design helped us spot a potential flaw that we might have missed on paper. With CAD, I can adjust dimensions5 on the fly, ensuring that every line and curve is exactly as it should be.
Feature | Benefits |
---|---|
3D Modeling | Detailed visualization |
Parametric Design | Easy modifications |
Simulation Tools | Error detection |
Simulation of Molding Processes
One of the most fascinating things I’ve learned is simulating the entire molding process. Before CAD, predicting how materials would behave was like trying to guess the weather a month in advance. Now, with CAD software, I can simulate everything—from injection to cooling. It’s almost like conducting a virtual rehearsal. For instance, by tweaking variables such as temperature or pressure, I’ve been able to foresee and correct issues like warping or shrinkage6 before they become real problems.
Enhanced Dimensional Control
Precision is key in mold design, and CAD software puts that control at my fingertips. The ability to make precise measurements digitally means fewer headaches later. Early in my career, I recall manually measuring parts and hoping for the best—a nerve-wracking process! Now, with tools like tolerance analysis7, I can anticipate and address challenges long before they affect production.
Integration with CAM Systems
The seamless integration of CAD with CAM systems has been a game changer in my work. I love how it streamlines the transition from design to production. By translating digital designs directly into manufacturing instructions, I’ve seen projects move faster and with fewer errors. Automated CNC programming not only saves time but also ensures that each mold piece is crafted to perfection.
Real-World Examples
Let me share a scenario that still brings a smile to my face. We were designing a mold for a smartphone case and used CAD to simulate the injection process. By doing this, we identified potential air pockets early on and adjusted the gate locations accordingly. This proactive step not only saved us from unnecessary waste but also ensured the final product was flawless.
Scenario | Outcome |
---|---|
Air Pocket Issue | Adjusted gate location |
Warping Risk | Optimized cooling channels |
These experiences have shown me how indispensable CAD software is in achieving mold precision. It’s like having a trusted partner that helps me bring my ideas to life with unmatched accuracy.
CAD software allows for 3D mold visualization.True
CAD enables detailed 3D modeling, aiding in visualizing intricate mold designs.
CAD software cannot simulate molding processes.False
CAD can simulate molding processes to predict material behavior and optimize design.
How Do Tolerances Affect Injection Molding?
Have you ever wondered why some molded parts fit perfectly while others don’t? It all comes down to tolerances.
Tolerances in injection molding dictate acceptable dimensional variations, ensuring parts fit, function, and meet quality standards efficiently, balancing performance with production cost management.
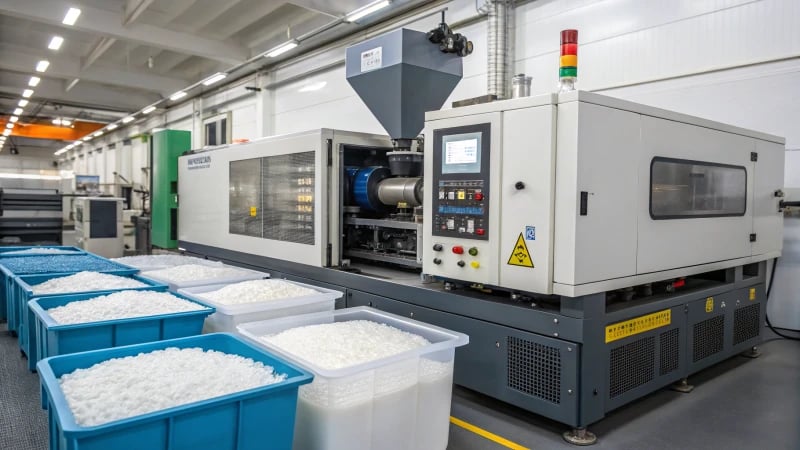
Importance of Tolerances in Part Design
When I first started working on injection molding8 projects, I was amazed at how something seemingly as simple as a few millimeters here or there could make or break a design. Tolerances are like the unsung heroes of injection molding. They set the boundaries for how much a part’s dimensions can vary from the original design without causing issues down the line. Imagine designing a part meant to fit into a smartphone casing—get those tolerances wrong, and you might end up with a device that doesn’t quite snap together as it should, resulting in increased waste or costly rework.
Tolerance Type | Typical Use Case | Example |
---|---|---|
Tight Tolerance | Critical components requiring precise fit | Gears in mechanical systems |
Loose Tolerance | Non-critical areas with less precision needed | Handles or cosmetic parts |
Impact on Manufacturing Processes
I remember one of my early projects where tight tolerances were crucial. The company I worked with wanted high precision for their new line of consumer gadgets. It taught me quickly that while tight tolerances can ensure perfect fits and finishes, they also mean more demanding manufacturing processes. You might need top-of-the-line machinery and longer production cycles, which can ramp up costs significantly.
On the flip side, I’ve seen scenarios where opting for looser tolerances allowed for quicker production but led to issues with the end product’s quality. Balancing these factors is a delicate art and science, something every designer like Jacky learns to master over time. By striking the right balance, we can reduce waste and enhance efficiency.
Standards and Guidelines
I’ve always found it reassuring to rely on established standards when setting tolerances. Standards like ISO 2768 or ANSI/ASME Y14.5 act as a safety net, providing detailed guidelines on permissible variations, which can really help streamline production and maintain consistency.
For example, ISO 2768 offers general tolerances for linear dimensions without needing individual specifications for each part. This kind of standardization can save so much time and hassle, ensuring that production lines run smoothly.
Standard | Description |
---|---|
ISO 2768 | General tolerances for linear dimensions and angles |
ANSI/ASME Y14.5 | Dimensioning and tolerancing standards |
Understanding these guidelines has empowered me to make more informed design choices, enhancing both performance and cost-effectiveness in projects. If you’re keen to dive deeper, exploring resources about standards in injection molding9 might just provide the insights you’re looking for.
Tight tolerances increase manufacturing costs.True
Tight tolerances require precise machinery and longer cycle times, raising costs.
Loose tolerances always improve product quality.False
Loose tolerances can speed production but may compromise product quality.
What are the most effective quality control measures?
Have you ever wondered what really keeps the wheels turning smoothly in manufacturing?
Effective quality control measures include Statistical Process Control (SPC), Six Sigma, and Total Quality Management (TQM) to identify defects, optimize processes, and maintain high product standards.
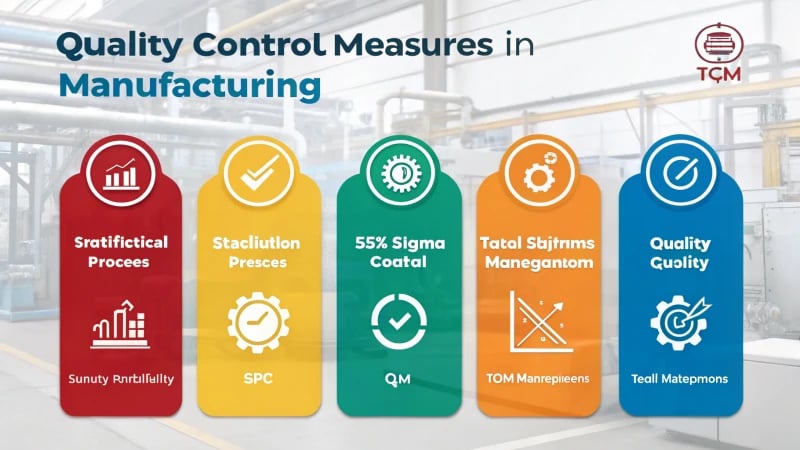
I remember the first time I walked into the production floor of our plant. The hum of the machines was almost musical, a symphony of precision and consistency. As someone who’s always been fascinated by how things work, I quickly learned that the magic behind this harmony is quality control.
Statistical Process Control (SPC)
When I first implemented Statistical Process Control, or SPC, it was like switching on a light in a dim room. Suddenly, I could see variations in the production process that I’d never noticed before. By using control charts, I could track these variations over time, allowing us to catch potential defects before they became costly issues.
Benefits of SPC | Description |
---|---|
Early Detection | Identifies issues before they become defects |
Process Improvement | Aids in refining production methods |
Data-Driven Decisions | Utilizes data for informed decision-making |
This approach didn’t just improve our product quality; it was a revelation in how we made decisions. Data wasn’t just numbers anymore; it was a roadmap.
Six Sigma
The Six Sigma journey was another eye-opener. With its disciplined approach, it felt like finally having a GPS for our processes. I recall the first project where we used DMAIC (Define, Measure, Analyze, Improve, Control). It was incredible to watch how defining the problem so clearly could transform our entire approach to manufacturing.
- Define: Identify the problem or improvement opportunity.
- Measure: Collect data relevant to the current process.
- Analyze: Determine root causes of defects.
- Improve: Implement solutions to address root causes.
- Control: Ensure that improvements are sustained over time.
Implementing Six Sigma can significantly enhance product quality10 and customer satisfaction by reducing defects to near zero.
Total Quality Management (TQM)
Total Quality Management was like discovering that the secret ingredient was all of us working together. TQM taught me that real success doesn’t just come from management directives but from every single team member feeling empowered and involved in quality initiatives.
- Customer Focus: Meeting and exceeding customer expectations.
- Total Employee Involvement: Engaging all employees in quality initiatives.
- Integrated System: Viewing an organization as a collection of interconnected processes.
- Process-Centric Approach: Understanding and improving key processes.
TQM encourages organizations11 to create a culture that fosters long-term success through customer satisfaction and employee involvement.
Incorporating these quality control measures has not only improved our manufacturing efficiency and product excellence but also created an environment where everyone is invested in producing the best possible results. Each method brings something unique to the table, contributing to a robust quality management system that keeps us ahead of the game.
SPC helps in early detection of defects.True
SPC identifies variations that could lead to defects, allowing early intervention.
Six Sigma does not use data-driven approaches.False
Six Sigma uses a disciplined, data-driven approach to reduce variability and defects.
How Can Regular Maintenance Improve Mold Reliability?
Ever felt like your molds have a mind of their own? Keeping them reliable is more than just luck—it’s about regular maintenance.
Regular maintenance improves mold reliability by reducing wear, identifying issues early, and maintaining performance, which decreases downtime, extends mold lifespan, and ensures consistent product quality.
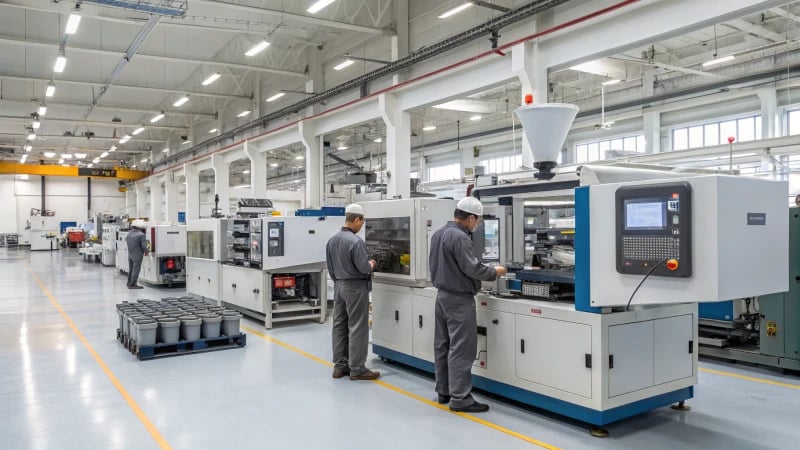
Preventing Wear and Tear
I remember my early days working on the production floor, watching molds churn out parts like magic. But, oh boy, the wear and tear they endured was something else. It’s like when you skip that oil change for your car—you’re asking for trouble. Regular inspection and cleaning12 of molds are essential. Just like noticing that little squeak in your car before it becomes a clank, catching scratches or corrosion early can save you heaps of stress later.
Maintenance Task | Frequency | Benefits |
---|---|---|
Cleaning | Weekly | Removes residue, reduces friction |
Lubrication | Monthly | Ensures smooth operation |
Component Inspection | Quarterly | Identifies wear and damage early |
Enhancing Consistency
The difference between a good day and a bad day at work often boils down to consistency. Remember that one time when everything just clicked? That’s what regular calibration checks13 can do for your molds. By ensuring they function within those tight tolerances, you reduce defects and hit those quality marks every time.
- Calibration: Aligns mold components to prevent misalignment.
- Temperature Control: Maintains consistent molding conditions.
Extending Mold Lifespan
It’s like nurturing a bonsai tree—patience and care pay off. A well-maintained mold is no different; it sticks around longer and saves you money on replacements. Following a mold part replacement14 schedule based on how often you use it and what the manufacturer suggests is a smart move.
Minimizing Downtime
Unexpected downtime? The bane of any manufacturing setup. I once faced an unexpected shutdown right before a major deadline—it was a nightmare. Implementing a preventive maintenance plan15 can keep molds production-ready and prevent those heart-stopping moments.
- Checklist:
- Check for leaks or cracks
- Verify proper lubrication
- Test mold alignment
Regular maintenance isn’t just about putting out fires as they spark; it’s about keeping the kitchen from catching fire in the first place. This approach not only prolongs the life of your molds but also boosts their reliability, making sure your manufacturing process runs smoother than a Sunday morning coffee routine. Keeping up with industry standards and guidelines ensures you’re always a step ahead in this game.
Regular cleaning reduces mold wear and tear.True
Cleaning removes residue and reduces friction, preventing wear.
Monthly lubrication is unnecessary for mold maintenance.False
Lubrication ensures smooth operation, preventing damage from friction.
Conclusion
Ensuring injection mold accuracy involves precise CAD modeling, strict tolerance management, regular maintenance, and advanced quality control techniques to optimize performance and product quality.
-
Discover how different materials impact the stability of molds under varying conditions. ↩
-
Explore the common reasons behind uneven cooling and how to address them. ↩
-
Learn about the importance of precision machining in achieving accurate molds. ↩
-
Find out how environmental factors influence the dimensional accuracy of molds. ↩
-
Learn how CAD software enhances design accuracy through precise modeling and error detection. ↩
-
Understand how CAD simulation helps predict and mitigate shrinkage in molds. ↩
-
Discover how tolerance analysis within CAD tools helps maintain dimensional accuracy. ↩
-
Learn about how tolerances are defined and their significance in maintaining part quality and functionality. ↩
-
Discover the key standards that dictate acceptable tolerance levels for various materials. ↩
-
Discover how Six Sigma methodologies contribute to improved product quality and reduced defects. ↩
-
Learn about how Total Quality Management fosters a culture of continuous improvement and customer satisfaction. ↩
-
Learn the benefits of regular inspection and cleaning for maintaining mold reliability and preventing damage. ↩
-
Discover how calibration checks maintain consistency and quality in mold performance. ↩
-
Find out about optimal schedules for replacing mold parts to extend their lifespan. ↩
-
Explore essential elements of an effective preventive maintenance plan to minimize downtime. ↩