Think back to the first moment you tried to repair something, only to discover it was more difficult than you expected.
To enhance the toughness of high hardness die steel, apply processes like heat treatment, cryogenic treatment, and surface coating, along with alloying to improve durability and performance.
These methods build a very strong base. Exploring each process deeply often uncovers really clever tricks. Techniques work wonders and turn your die steel into something tough. Great performance comes from small changes like adding nickel or adjusting heat during treatment. This change seems like giving die steel its own coach to reach full power.
Adding 1% nickel improves die steel toughness.True
Nickel refines grains, enhancing the steel's toughness.
Forging ratio of 6 enhances die steel toughness.False
Optimal forging ratio is 3 to 5 for uniformity and toughness.
How Does Alloying Improve Die Steel Toughness?
Visualize tools that last longer and work better by simply changing their mix. That’s the wonder of alloying in die steel.
Alloying strengthens die steel toughness by adding nickel, molybdenum and vanadium. These elements make the grains smaller, which helps steel resist wear and tear. This approach increases the strength of the steel. It really works well with special alloying and heat treatment methods.
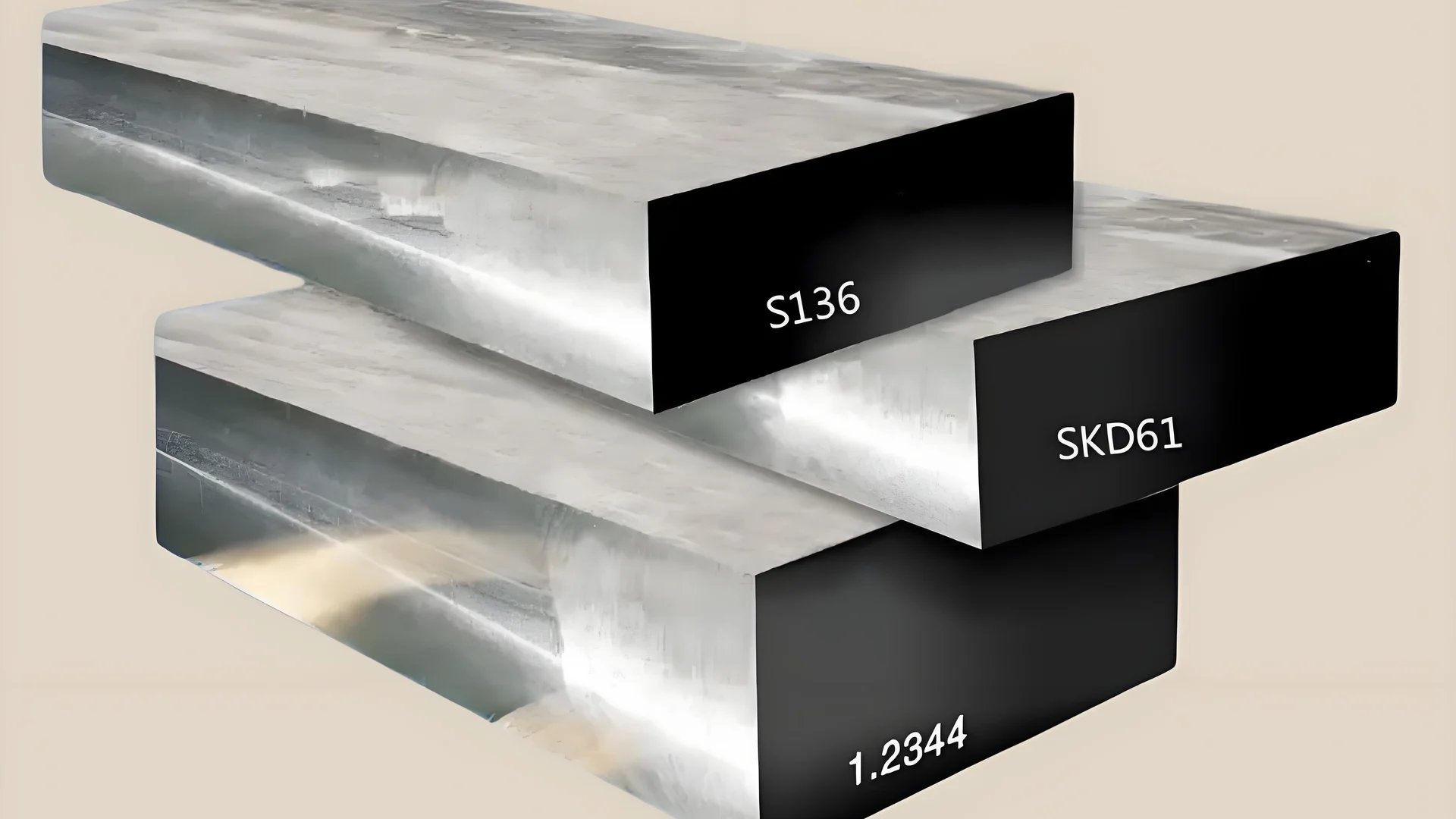
The Role of Alloying Elements in Increasing Toughness
Alloying die steel involves introducing various elements to refine its properties. For instance, nickel is added to enhance toughness and fatigue resistance. Adding 1% to 1.2% nickel to H13 steel can effectively refine grains, thus improving the toughness of the steel.
Molybdenum is known for improving strength and toughness while resisting tempering softening. This makes it an essential component in achieving a balanced toughness in die steel.
Vanadium works by forming stable carbides that prevent grain growth, with just 0.2% to 0.3% effectively improving the material’s toughness.
Microalloying Technology
Microalloying incorporates trace elements like niobium and titanium. These elements form fine carbides or nitrides within the steel, acting as crystal nuclei during solidification and hot working. This process significantly refines the grain size from tens of microns to several microns.
Element | Effect on Steel |
---|---|
Nickel | Increases toughness and fatigue resistance |
Molybdenum | Enhances strength and resists softening |
Vanadium | Forms carbides to prevent grain growth |
Optimization of Heat Treatment Processes
Heat treatment feels like a spa day for steel. Tempering treatment, for instance, involves multiple cycles (2-3 times) at specific temperatures (e.g., 550-600℃ for Cr12MoV steel) to transform residual austenite into martensite, enhancing toughness.
A revolutionary approach is deep cryogenic treatment with tempering. Imagine steel facing extreme cold at -120℃ before slowly warming. This shift improves grains, making steel tougher and more stable.
Improvement Through Hot Working Processes
The working method matters as much as what you add to the steel. The forging process enhances uniformity and the distribution of die steel’s streamline, significantly boosting toughness with a typical forging ratio between 3 and 5.
Through controlled temperature and multiple upsetting operations, the material’s structure becomes more uniform.
In the rolling process, controlling the rolling temperature (800-900℃) and using appropriate cooling methods like air or mist cooling can refine grains and improve overall performance.
Insights into Microalloying Technology
Further exploring microalloying with niobium and titanium reveals how these elements shrink grain size during solidification and hot work, improving grain size reduction1 during solidification and hot working.
These alloying elements combined with new techniques help create a steel that is very tough—perfect for difficult tasks in manufacturing and tool making.
Adding 1% nickel improves die steel toughness.True
Nickel refines grains, enhancing toughness in H13 steel.
Deep cryogenic treatment reduces steel brittleness.True
Cryogenic treatment transforms austenite to martensite, improving toughness.
How does heat treatment enhance steel properties?
Have you ever thought about how steel becomes something strong and dependable?
Heat treatment changes steel’s microstructure using methods like annealing, quenching and tempering. These methods increase steel’s strength, durability and resistance to wear. Construction, manufacturing and tool creation need such steel. Strong steel is very important. Special processes create this strength.
The Basics of Heat Treatment
Years in metalwork show me how heat treatment changes everything. Visualize starting with raw steel, then using heat and cold to shape it for engineering needs. The metal’s tiny structure changes to become better without altering its form. Techniques like annealing2, quenching3, and tempering4 are each special in their own way.
Alloying Treatment
On a project, adding nickel to steel changed everything. Think of it as giving steel hidden strength against wear and breakage. Bringing in elements like nickel (Ni), molybdenum (Mo), and vanadium (V) can greatly improve how steel performs. Nickel increases strength, molybdenum gives more power, and vanadium keeps the structure neat by stopping grain growth.
Element | Benefits |
---|---|
Nickel | Increases strength |
Molybdenum | Gives more power |
Vanadium | Prevents grain growth |
Small amounts of niobium (Nb) or titanium (Ti) also help refine grains, which really matter for strength and toughness.
Heat Treatment Process Optimization
Tempering Treatment: Often, several tempering rounds achieve ideal strength and flexibility. For example, Cr12MoV steel improves a lot when tempered at 550-600°C.
Deep Cryogenic Treatment: Think of cooling steel to temperatures as low as -196°C! This shifts remaining austenite to martensite, refining grains and increasing toughness.
Improvement of Hot Working Process
Forging Process: I hammered die steel until it was perfect. A proper forging ratio reduces large grains and enhances toughness.
Rolling Process: By managing rolling and cooling, a refined grain structure appears. It’s like urging steel to be its very best.
Uniting these heat treatment processes with smart alloying helps steel not just meet but go beyond expectations in various applications, like mold design or large-scale structures. Knowing these methods can really change steel’s role in complex engineering tasks.
Adding 1% nickel improves H13 steel toughness.True
Nickel refines grains and enhances toughness in H13 steel.
Deep cryogenic treatment occurs above 0℃.False
Cryogenic treatment is performed between -80℃ and -196℃.
How Can Cryogenic Treatment Enhance Die Steel Performance?
Freezing temperatures might truly harden steel. Cryogenic treatment perhaps holds the key to strengthening die steel.
Cryogenic treatment cools die steel to very low temperatures. This process improves toughness and stability. It changes retained austenite into martensite. It also refines the steel’s microstructure. This treatment offers better wear resistance and longer fatigue life.
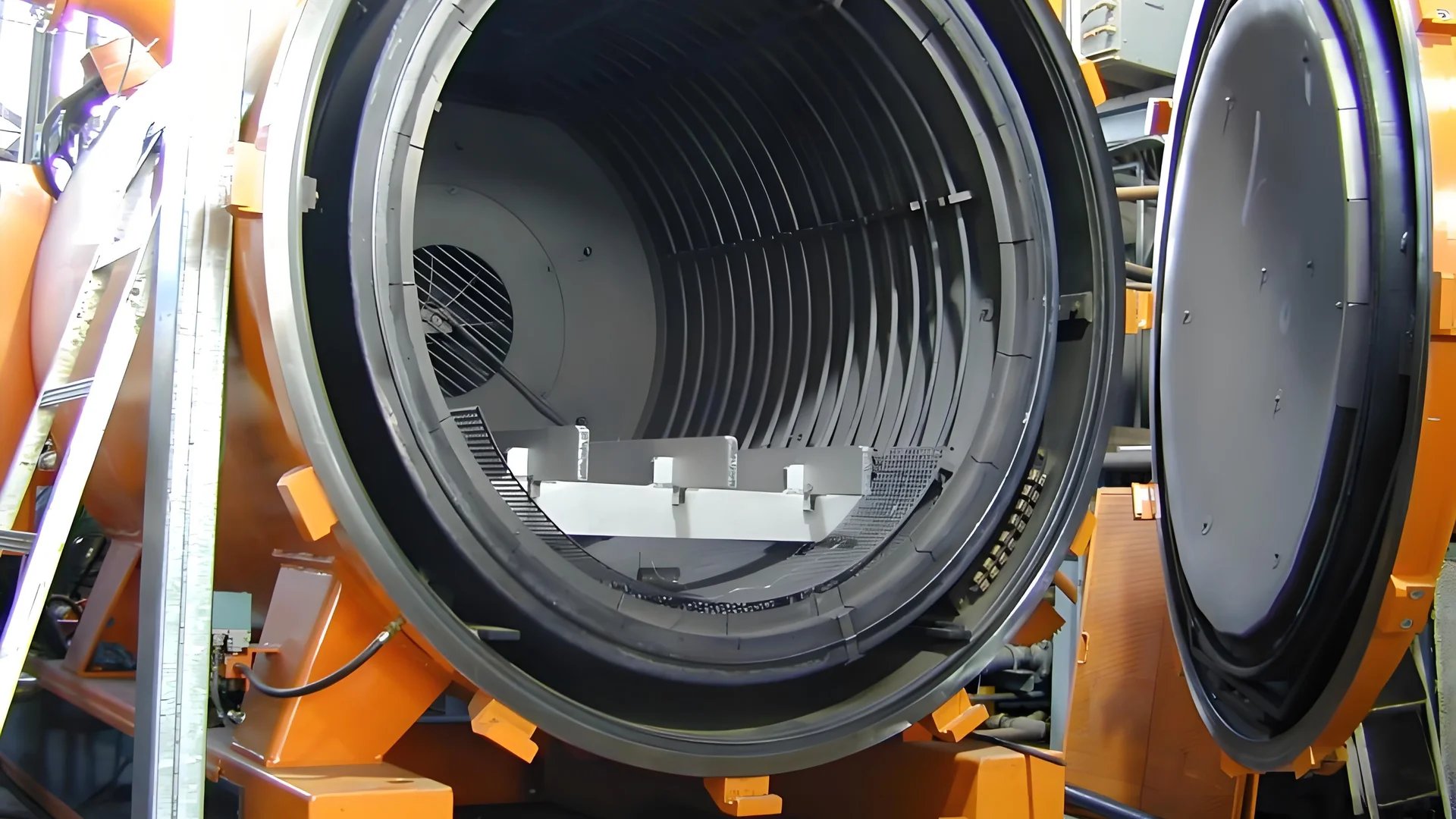
Understanding Cryogenic Treatment
I remember hearing about cryogenic treatment for the first time. My thoughts went straight to sci-fi films with freezing scenes. In reality, this process is not only about cold. It changes material structures in a nearly magical way. Cooling items to between -80°C and -196°C, then warming them, really increases die steel’s strength and balance. Steel enjoys a refreshing spa-like day!
Cryogenic treatment involves cooling materials to sub-zero temperatures, typically between -80°C and -196°C, to alter their microstructure. This treatment is followed by tempering, which enhances toughness and dimensional stability. The process converts retained austenite into martensite, refining grains and improving overall performance.
Benefits for Die Steel
Think of die steel as a reliable friend. Strength is very important for this friend. Cryogenic treatment increases hardness, wear resistance, and fatigue life. It turns your trustworthy buddy into a superhero, ready for tough tasks.
Die steel treated with cryogenics can achieve better hardness, wear resistance, and fatigue life. For example, cryogenic processing enhances the transformation of residual austenite into martensite, a harder phase, resulting in improved wear resistance.
Integration with Alloying Techniques
Blending cryogenic treatment with alloying techniques5 is like adding fire to a strong engine. Adding nickel or molybdenum really improves steel’s ability.
Integrating cryogenic treatment with alloying techniques such as adding nickel or molybdenum can further improve steel performance. Nickel adds toughness and fatigue resistance—it’s like giving steel a strong shield—while molybdenum increases strength and helps resist temper softening.
Cryogenic Treatment vs. Conventional Heat Treatment
Some things work better in harmony. Cryogenic treatment and regular heat treatments like tempering are such a pair.
Together they refine grains and increase toughness beyond what each does alone.
It’s a dream team in sports where every player gives something special,
boosting the group’s performance.
Treatment Type | Effect |
---|---|
Cryogenic Treatment | Refines grain structure and converts residual austenite to martensite |
Tempering | Reduces brittleness, improves toughness |
Practical Applications and Considerations
Experience shows cryogenic treatment lengthens tool life greatly in die-casting and stamping industries.
Like any investment,
it’s vital to check costs and processing times before starting.
Balance performance gains with practicality; find the sweet spot.
Practical applications of cryogenic treatment include improved tool life in die-casting and stamping industries.
However,
it is essential to consider factors such as cost implications and processing times when implementing this treatment in manufacturing.
Future Prospects and Research Directions
The future seems bright as research keeps improving cryogenic processing steps.Matching it with microalloying may reveal more ways to boost die steel.Exciting possibilities abound.Discovering new ways to improve this vital material is thrilling.Ongoing research aims to optimize cryogenic processing parameters
to maximize benefits.Studiess on combining cryogenics with microalloying could yield exciting developments,
offering new avenues for enhancing die steel performance.
Adding 1% nickel improves die steel toughness.True
Nickel refines grains and enhances steel's toughness and fatigue resistance.
Cryogenic treatment transforms austenite to martensite in die steel.True
Deep cryogenic treatment promotes this transformation, enhancing toughness and stability.
Why is optimizing hot working processes essential?
Think of the time you repaired something at home and it worked really well afterward. Optimizing hot working processes does the same for metals. This happens on a much larger scale.
Improving hot working processes is key for increasing metal strength. Controlling tiny structure changes during heating helps the metal last longer. Such control results in better performance. Metal parts really become more durable.
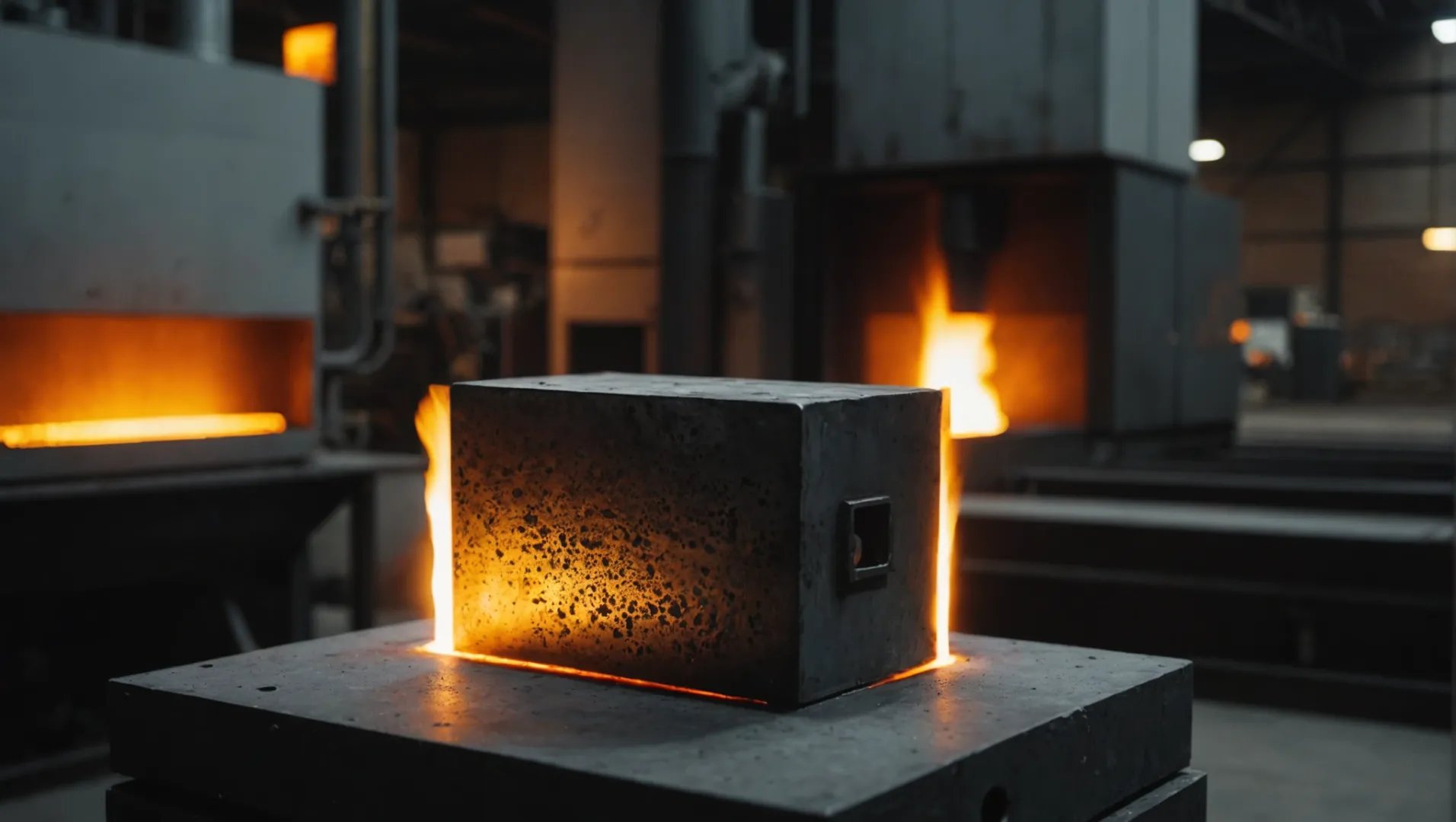
The Role of Alloying Treatment
Alloying is like adding secret ingredients to a favorite recipe – just a pinch here and a touch there to create something truly special. When I first learned about metallurgy, alloying captured my interest. Adding elements such as nickel (Ni), molybdenum (Mo), and vanadium (V) to steel dramatically increases toughness and resistance to fatigue. I vividly recall the first time I saw the effect of nickel in H13 steel. It was like a master chef at work; suddenly, the grains became refined and the steel was much tougher.
Alloy Element | Impact on Steel |
---|---|
Nickel (Ni) | Increases toughness |
Molybdenum (Mo) | Enhances strength |
Vanadium (V) | Prevents grain growth |
Microalloying takes us deeper into this process. Adding small amounts of elements like niobium (Nb) and titanium (Ti) refines grain size, significantly strengthening and toughening the steel.
Heat Treatment Process Optimization
Heat treatment is like a spa day for steel, allowing it to relax and reach its best form. I managed a project where tempering treatments made a huge difference. Increasing the number and duration of tempering sessions greatly improved steel toughness. Quenching followed by multiple tempering sessions reduced brittleness.
Deep cryogenic treatment is another technique. Imagine chilling the steel to very low temperatures, which turns residual austenite into martensite, refines grains, and improves dimensional stability. These treatments refine grains and optimize properties, helping steel6 perform well under stress.
Improvement of Hot Working Process
The forging process is truly an art. Proper temperature and pressure balance improves uniformity and die steel distribution. I witnessed this change myself – a forging ratio of 3 to 5 broke coarse grains.
Process | Key Factor |
---|---|
Forging | Ratio of 3-5 for uniformity |
Rolling | Controlled temperature |
Controlled rolling is also key. Keeping the final rolling temperature between 800-900°C along with suitable cooling dramatically improves performance. It’s like when everything falls into place – the overall result for the material7 is astonishing.
Nickel enhances die steel toughness by 1% addition.True
Adding 1% nickel to H13 steel improves toughness by refining grains.
Cryogenic treatment reduces steel brittleness effectively.True
Cryogenic treatment transforms austenite to martensite, improving toughness.
Conclusion
Enhancing the toughness of high hardness die steel involves alloying with nickel, molybdenum, and vanadium, optimizing heat treatments like tempering and cryogenic processes, and improving hot working techniques.
-
This link explores microalloying technology’s impact on steel properties, offering insights into how trace elements like niobium and titanium refine grain size. ↩
-
Learn how annealing alters metal properties to increase ductility and reduce hardness. ↩
-
Explore quenching’s role in rapidly cooling metal to enhance strength and hardness. ↩
-
Discover how tempering modifies quenched steel to improve toughness and reduce brittleness. ↩
-
Explore how integrating alloying techniques enhances die steel performance when combined with cryogenic treatment. ↩
-
Explore how deep cryogenic treatment enhances material properties by refining grains and improving toughness. ↩
-
Learn about controlled rolling techniques that optimize microstructures, enhancing overall material performance. ↩