Are you ready to unlock the full potential of polypropylene in your injection molding projects? Let’s dive into some transformative strategies together!
Enhancing the strength of polypropylene in injection molding involves selecting high-crystallinity materials, using reinforcing fillers like glass or carbon fiber, optimizing the molding process, and applying post-processing techniques such as annealing.
While these initial steps lay a solid foundation for stronger polypropylene components, diving deeper into each strategy reveals nuanced approaches that can yield even greater improvements. Let’s explore these aspects in detail to ensure your production meets the highest strength standards.
Glass fiber enhances polypropylene's tensile strength.True
Glass fiber interlocks with the polymer matrix, distributing forces evenly.
What Role Do Reinforcing Fillers Play in Polypropylene Strength?
Reinforcing fillers are crucial in enhancing polypropylene’s strength, making it a versatile choice in injection molding.
Reinforcing fillers, like glass and carbon fibers, significantly boost polypropylene’s strength by improving its mechanical properties, allowing for more durable and robust applications.
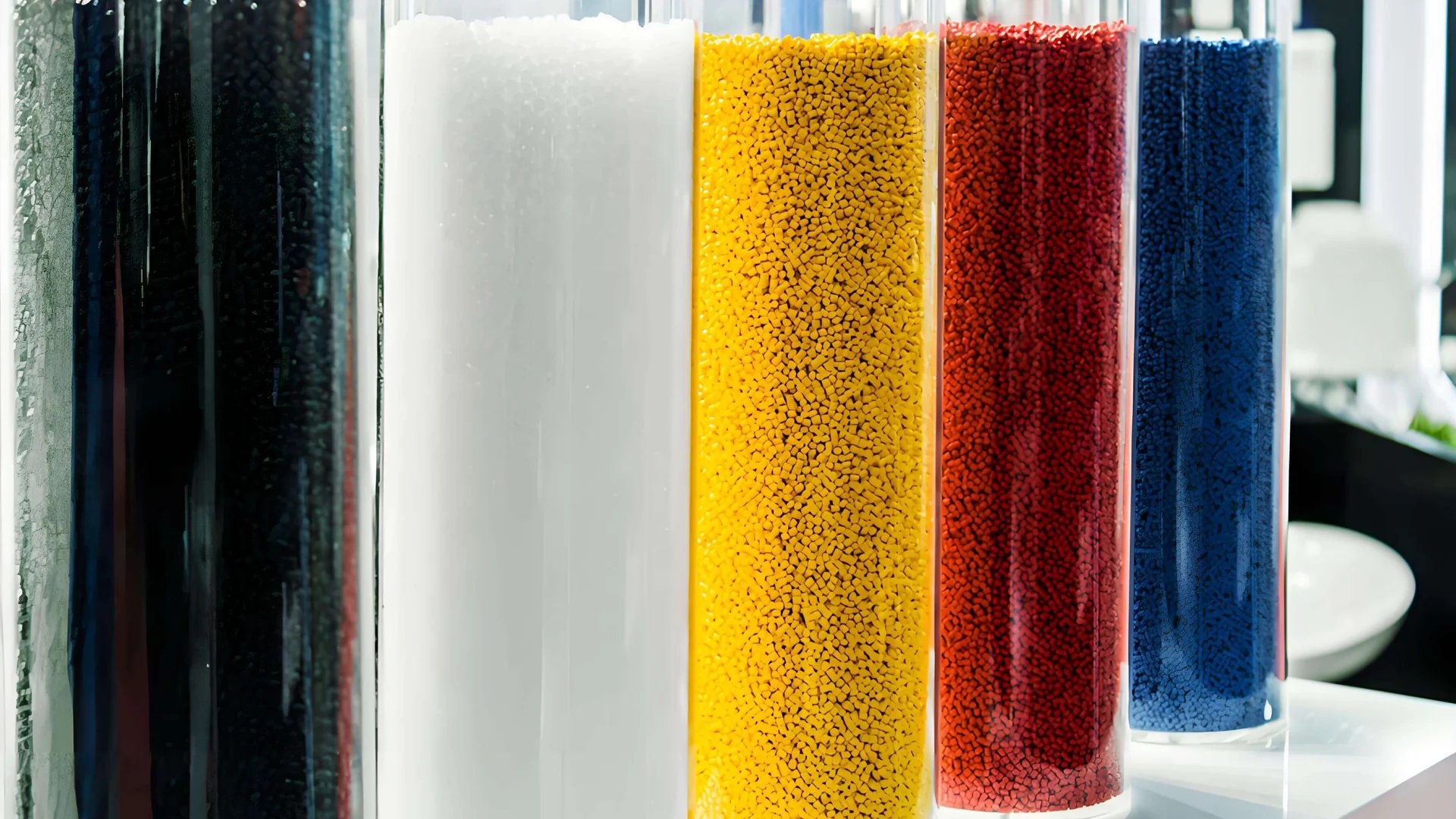
Types of Reinforcing Fillers
When it comes to reinforcing fillers, the two most effective types for polypropylene are glass fiber and carbon fiber.
Glass Fiber
Glass fiber is a widely-used filler due to its ability to substantially increase polypropylene’s tensile strength. It does so by interlocking with the polymer matrix, which distributes applied forces more evenly across the material. Typically, the glass fiber content in polypropylene can range from 10% to 40%, depending on the desired strength. A higher percentage can lead to improved strength but may complicate the processing.
Carbon Fiber
Although more costly than glass fiber, carbon fiber offers exceptional strength and stiffness. It’s often used in applications where weight is a critical factor and strength cannot be compromised. The addition of even a small amount of carbon fiber can dramatically enhance polypropylene’s mechanical properties.
Effects on Mechanical Properties
Adding reinforcing fillers directly impacts several mechanical properties of polypropylene:
- Tensile Strength: Both glass and carbon fibers improve tensile strength by providing additional support to the polymer structure.
- Impact Resistance: While enhancing rigidity, these fillers also help maintain or even improve the impact resistance of polypropylene.
- Dimensional Stability: Reinforced polypropylene exhibits less shrinkage and warping during the cooling phase, resulting in more dimensionally stable parts.
Considerations for Use
When incorporating reinforcing fillers, it’s essential to consider:
- Processing Conditions: Adjustments in processing conditions, such as temperature and pressure, may be necessary to accommodate the altered flow characteristics of filled polypropylene.
- Cost-Benefit Analysis: While fillers like carbon fiber offer superior reinforcement, they come at a higher cost. Evaluating the specific requirements of your application can help determine the most cost-effective solution.
- Environmental Impact: Some fillers may affect the recyclability of polypropylene. Therefore, considering sustainable options is vital for eco-friendly production practices.
In summary, reinforcing fillers play a pivotal role in enhancing polypropylene’s strength and usability in various applications. By carefully selecting and managing these fillers, manufacturers can significantly improve product performance and meet specific application requirements.
Glass fiber can increase polypropylene's tensile strength by 40%.True
Glass fiber content in polypropylene ranges from 10% to 40%, enhancing strength.
Carbon fiber is cheaper than glass fiber for reinforcing polypropylene.False
Carbon fiber is more costly than glass fiber but offers superior strength.
How Can Injection Molding Process Optimization Improve Polypropylene?
Injection molding process optimization is crucial for enhancing the strength of polypropylene components. Discover the key techniques involved.
Optimizing the injection molding process improves polypropylene’s strength by adjusting temperature, pressure, holding time, and mold design.
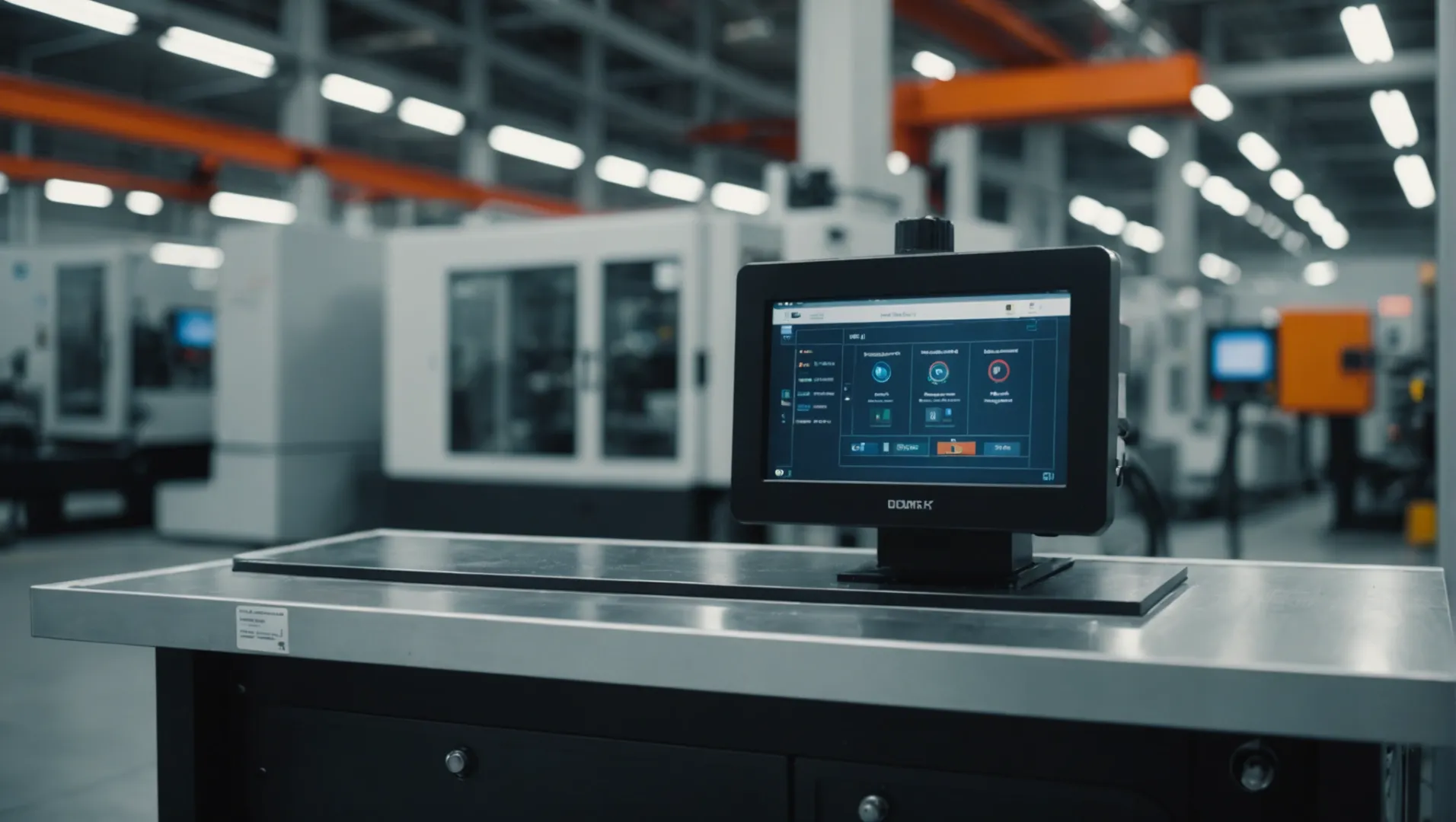
Increasing Injection Molding Temperature
Raising the injection molding temperature can significantly enhance the molecular alignment in polypropylene, leading to stronger components. It’s essential to keep the temperature within a specific range—typically between 200℃ and 250℃—to avoid degradation while ensuring optimal flow. Gradual temperature adjustments can help find the perfect balance, offering a marked improvement in strength.
Boosting Injection Pressure
Higher injection pressure ensures that polypropylene fills the mold tightly, reducing internal voids and defects. However, balancing this with mold longevity is key, as excessive pressure could lead to increased wear. The recommended range is 50MPa to 150MPa. Monitoring mold conditions closely during adjustments can prevent unnecessary damage, ensuring both product quality and equipment safety.
Adjusting Holding Time and Pressure
Extending the holding time and adjusting holding pressure allows polypropylene to cool and solidify thoroughly, minimizing shrinkage and warping. Typically, holding time ranges from 5s to 30s, while pressure should be 50% to 80% of the initial injection pressure. Considerations like product size, shape, and wall thickness are critical in determining the right parameters to reduce internal stress without compromising part integrity.
Mold Design Optimization
Innovative mold design can substantially improve polypropylene’s strength. Strategic gate placement and size ensure uniform filling, reducing stress and defects. Enhancing the cooling system promotes rapid and even crystallization, boosting strength. A uniform mold temperature prevents localized overheating or cooling, providing consistent quality across all parts. Understanding these mold design principles1 is crucial for optimizing the injection molding process.
Increasing temperature enhances polypropylene strength.True
Raising temperature improves molecular alignment, boosting strength.
Holding time should always be less than 5 seconds.False
Holding time ranges from 5s to 30s for optimal cooling and solidification.
What Are Effective Post-Processing Methods for Polypropylene?
To ensure robust polypropylene parts, mastering effective post-processing techniques is essential.
Effective post-processing methods for polypropylene include annealing to relieve stress and improve crystallinity, as well as surface treatments like spraying and electroplating to enhance durability and appearance.
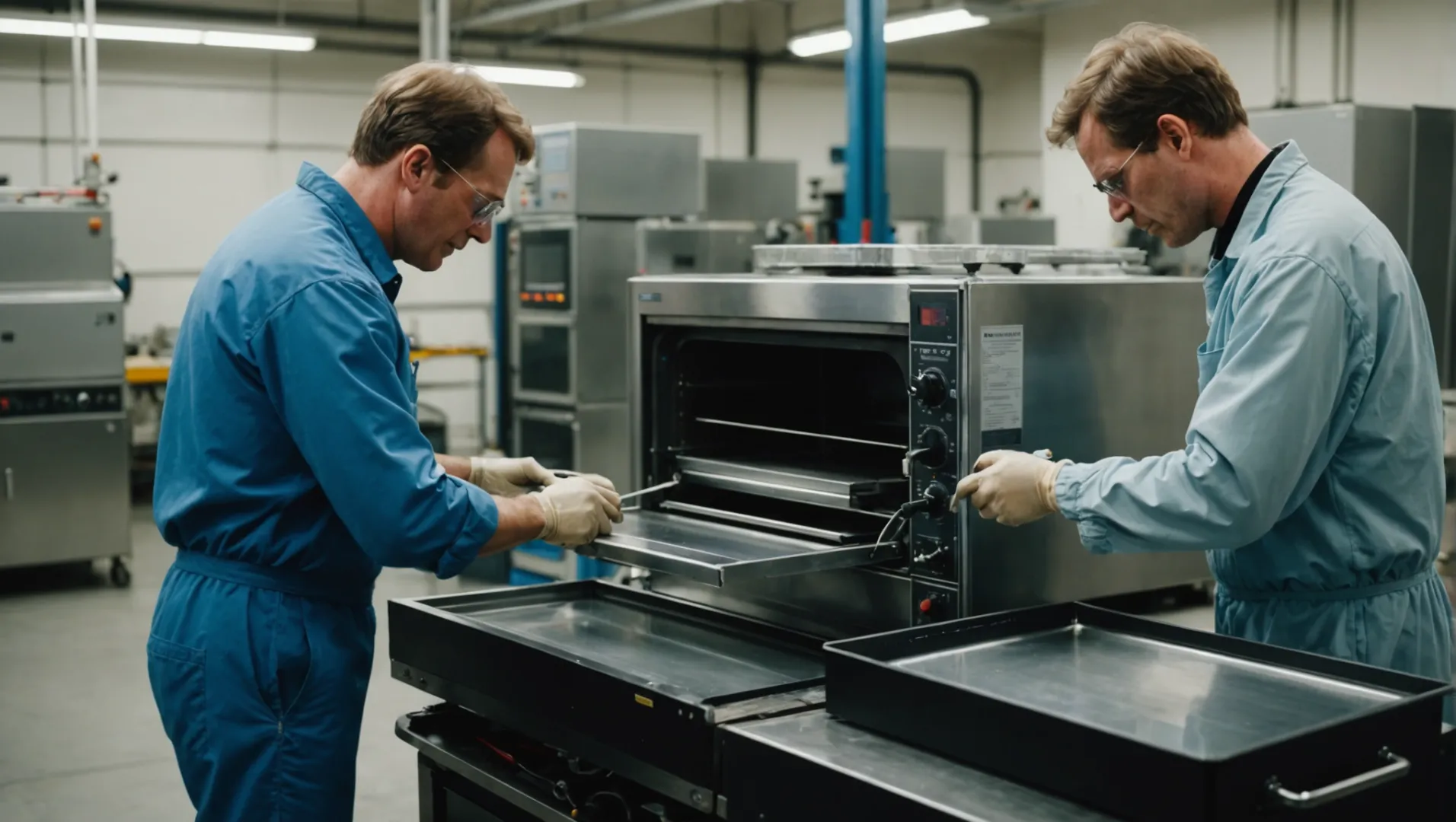
Annealing Treatment: Enhancing Strength and Stability
Annealing is a heat treatment process that can significantly improve the properties of polypropylene. By heating the material below its glass transition temperature, internal stresses are relieved, leading to improved crystallinity. This process can enhance the overall strength and stability of the molded parts.
Typically, the annealing temperature is set just below the glass transition temperature of polypropylene, and the duration may vary depending on the part’s size and thickness, ranging from several hours to tens of hours. It’s crucial to control both the temperature and time to prevent degradation of performance due to over-annealing.
Surface Treatment Techniques
Surface treatments can not only enhance the mechanical properties of polypropylene but also improve its aesthetic qualities. Options like spraying and electroplating can increase surface hardness and wear resistance, thereby indirectly boosting the part’s overall strength. Furthermore, these treatments add value by enhancing the visual appeal of the finished product.
When selecting a surface treatment method, it’s essential to balance product usage requirements with cost considerations. Each method offers different benefits:
Method | Benefits |
---|---|
Spraying | Increases surface hardness, enhances aesthetics |
Electroplating | Provides wear resistance, improves electrical conductivity |
Combining Techniques for Optimal Results
By integrating annealing with suitable surface treatments, manufacturers can achieve a dual benefit of improved internal properties and enhanced external durability. For example, combining annealing with electroplating can yield polypropylene parts that are both structurally robust and wear-resistant.
Understanding these post-processing techniques2 is vital for manufacturers aiming to produce high-strength polypropylene components efficiently. Tailoring these methods to specific applications ensures that each part not only meets but exceeds industry standards.
Annealing improves polypropylene crystallinity.True
Annealing relieves internal stresses, enhancing crystallinity.
Electroplating reduces polypropylene's wear resistance.False
Electroplating increases wear resistance by hardening the surface.
How Does Mold Design Influence the Strength of Injection Molded Parts?
Mold design plays a crucial role in determining the strength and quality of injection molded parts. But how exactly does it influence these characteristics?
Mold design influences the strength of injection molded parts by ensuring proper material flow, reducing stress concentrations, and enhancing cooling efficiency. Optimal gate placement, cooling systems, and part geometry are key elements that impact the mechanical properties and durability of the final product.
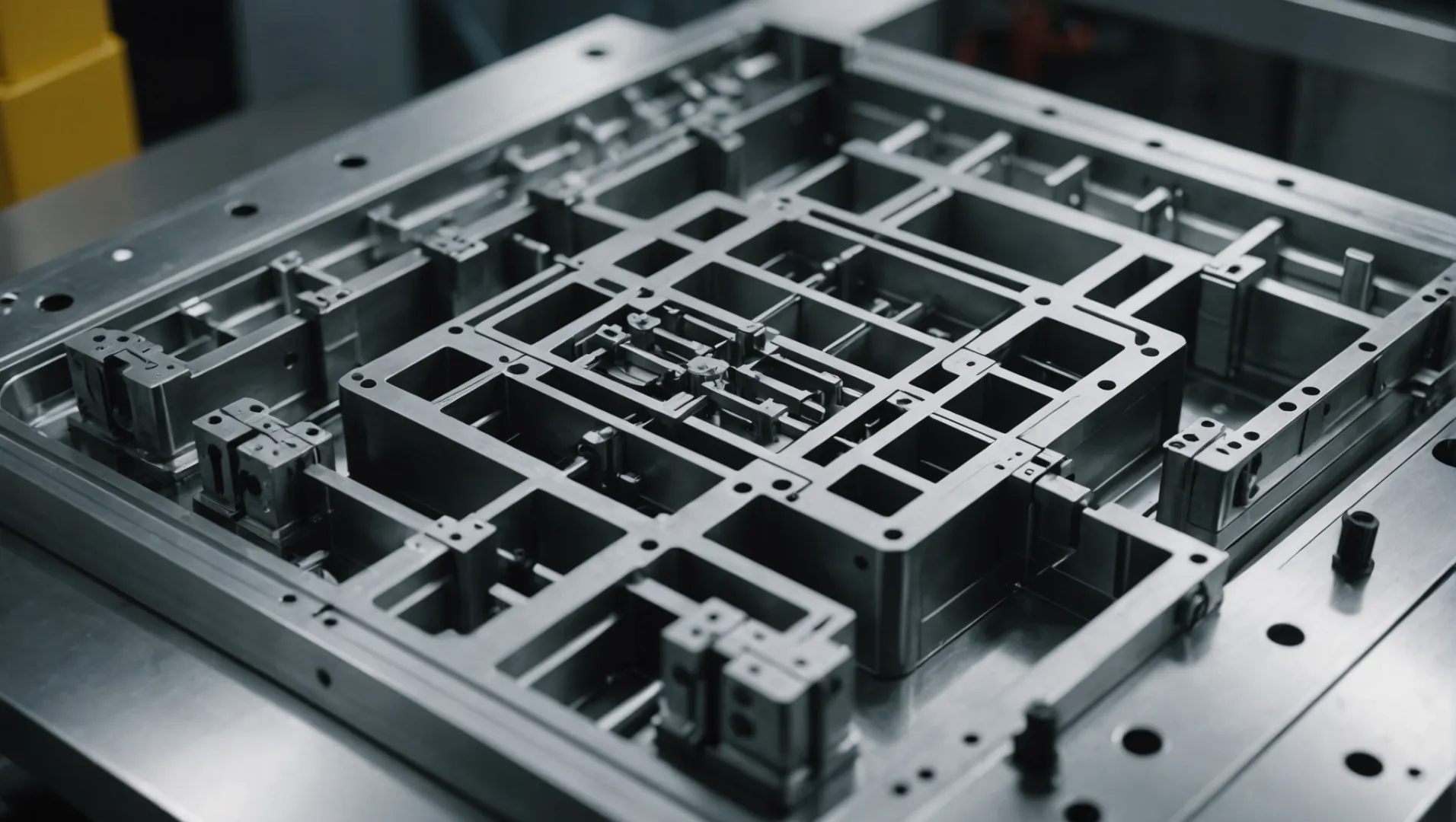
The Importance of Gate Design
One fundamental aspect of mold design is the positioning and size of the gate, which serves as the entry point for molten plastic. A well-designed gate ensures uniform filling, minimizing potential stress concentrations that could weaken the part. Optimal gate placement reduces flow paths and pressure drops, leading to more even material distribution.
- Gate Types: Different types of gates like edge, fan, or submarine gates can be used depending on the complexity and requirements of the part. For instance, a fan gate might be preferred for wide parts as it provides a broad entry, reducing flow marks.
Cooling System Efficiency
The mold’s cooling system is pivotal for controlling the solidification process, directly affecting crystallinity and mechanical properties. Enhanced cooling systems help in achieving uniform cooling across the part, which is vital for maintaining consistent strength and preventing warping or dimensional inaccuracies.
- Cooling Channels: Incorporating conformal cooling channels that match the part’s geometry can significantly improve cooling efficiency. This approach helps in maintaining uniform temperature, reducing cycle times while enhancing part strength.
Part Geometry Considerations
The geometry of the mold cavities profoundly influences how stress is distributed across the part. Designing with uniform wall thickness helps in reducing stress concentrations and potential weak points.
- Rib Design: Proper rib design can add structural support without compromising weight. Ribs should be strategically placed and adequately thick to balance between added strength and potential sink marks.
Material Flow Management
Ensuring a smooth material flow throughout the mold is essential to prevent defects such as air traps or weld lines that can weaken parts. Proper venting is necessary to allow trapped air to escape, ensuring full mold cavity fill.
- Flow Simulation: Utilizing computer-aided engineering tools for flow simulation can aid in predicting potential issues in material flow and allow designers to make informed adjustments before manufacturing.
In summary, mold design is a multifaceted process that involves careful consideration of multiple factors. Optimizing gate locations3, refining cooling systems, and ensuring adequate material flow are essential for producing strong, reliable injection molded parts. Each decision impacts the final product’s strength, highlighting the importance of precision in mold design.
Optimal gate placement reduces stress concentrations.True
Proper gate placement ensures uniform material flow, minimizing stress.
Cooling systems have no impact on part strength.False
Efficient cooling systems ensure uniform solidification, enhancing strength.
Conclusion
By strategically selecting materials, optimizing processes, and applying effective post-processing methods, you can significantly enhance polypropylene’s strength in injection molding. Implement these insights to elevate your manufacturing efficiency and product quality.
-
Discover essential principles for enhancing polypropylene’s strength through innovative mold design.: Plastic injection molding is where plastic materials (in this case, polypropylene) are melted and then injected under high pressure into molds. ↩
-
Explore diverse post-processing methods for stronger polypropylene parts.: This paper describes a new efficient method for the processing of post-consumer polypropylene (and other polyolefins) wastes into polar waxes that have … ↩
-
Explore how precise gate placement enhances part strength.: In injection molds with long and thin cores, the gate should be located far from the core to prevent deformation caused by material flow. You … ↩