Achieving precision in machining parting surfaces is critical for mold design success. These surfaces must be meticulously crafted to ensure seamless assembly and functionality of the final product.
Enhancing machining accuracy for parting surfaces involves selecting high-precision CNC machining centers, using appropriate tools like carbide cutters, optimizing cutting parameters, and employing advanced techniques such as high-speed cutting and EDM.
While understanding these core principles provides a solid foundation, delving deeper into each aspect can uncover valuable insights that are essential for mastering precision in mold design. Let’s explore the details further to enhance your manufacturing processes.
CNC machines can achieve ± 0.005mm accuracy.True
High-end CNC machines offer this precision, reducing dimensional errors.
EDM is unsuitable for high-hardness materials.False
EDM accurately processes high-hardness materials, ensuring shape and size precision.
What Role Does Machining Equipment Play in Accuracy?
In the world of manufacturing, precision is key. Machining equipment plays a pivotal role in ensuring accuracy during production.
Machining equipment ensures accuracy by using high-precision CNC machines, appropriate tool selection, and advanced technologies like high-speed cutting. These elements reduce dimensional errors and improve part quality.
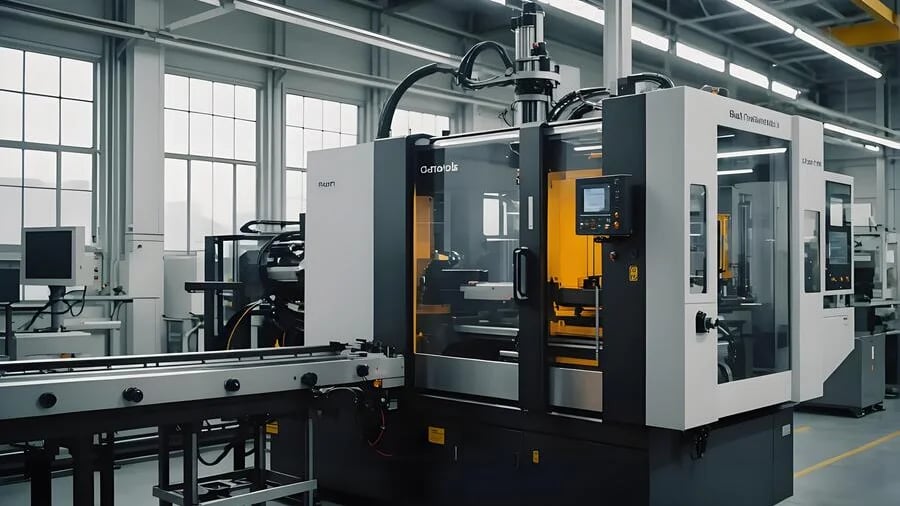
High-Precision Machining Equipment
High-precision machining equipment, such as CNC machining centers, are crucial for maintaining accuracy. These machines offer exceptional positioning accuracy, often up to ± 0.005mm, which is critical for reducing dimensional errors on parting surfaces. They also feature online measurement systems that allow real-time monitoring and adjustment of machining parameters to maintain accuracy.
Appropriate Tool Selection
The selection of appropriate tools is another essential factor in achieving machining accuracy. For complex curved surfaces, using a ball end milling cutter helps fit the shape better and reduces processing residue. Tools made of carbide are preferred for their high hardness and wear resistance, making them ideal under high-speed cutting conditions. Ensuring the correct parameters for cutting edge length and diameter is vital to prevent tool deformation and maintain surface accuracy.
Optimization of Cutting Parameters
Optimizing cutting parameters such as speed, feed, and depth of cut is crucial. These parameters can be determined through cutting tests and simulations to ensure the best results. For instance, when machining steel molds, speeds between 100 – 300m/min and a feed rate of 0.05 – 0.2mm/z are typical to enhance accuracy and surface quality. The depth of cut should be adjusted according to the material’s residual state.
Advanced Processing Technologies
Advanced technologies like high-speed cutting (HSC) can significantly enhance machining accuracy. HSC minimizes cutting force and vibration, improving surface quality and dimensional accuracy. The cutting speed in HSC can be 3 – 10 times faster than normal methods, completing tasks swiftly while maintaining precision. Precision electric discharge machining (EDM) is also effective for high-precision tasks, especially with complex shapes or hard materials like molds1.
Precise Inspection Means
Inspection is vital for ensuring machining accuracy. High-precision equipment such as coordinate measuring machines (CMM) can measure the size, shape, and position of parting surfaces with an accuracy of ± 0.001mm. This allows for detailed comparisons with design models to verify compliance with specifications.
Timely Corrective Measures
Finally, corrective measures based on inspection results are essential. Techniques such as hand grinding or EDM can adjust surfaces that don’t meet accuracy standards. For example, a plane grinder can correct flatness errors while slope correction functions in EDM can address angular deviations in molds2.
CNC machines have positioning accuracy of ± 0.005mm.True
High-end CNC machines achieve positioning accuracy of up to ± 0.005mm.
Ball end mills are unsuitable for complex surfaces.False
Ball end mills fit complex curved surfaces, reducing processing residue.
How Do Cutting Parameters Affect Machining Precision?
Precision in machining is a cornerstone of quality manufacturing. But how exactly do cutting parameters impact this precision?
Cutting parameters, including speed, feed rate, and depth of cut, significantly influence machining precision by affecting tool wear, surface finish, and dimensional accuracy. Optimizing these parameters through tests and simulations enhances the overall quality and accuracy of machined parts.
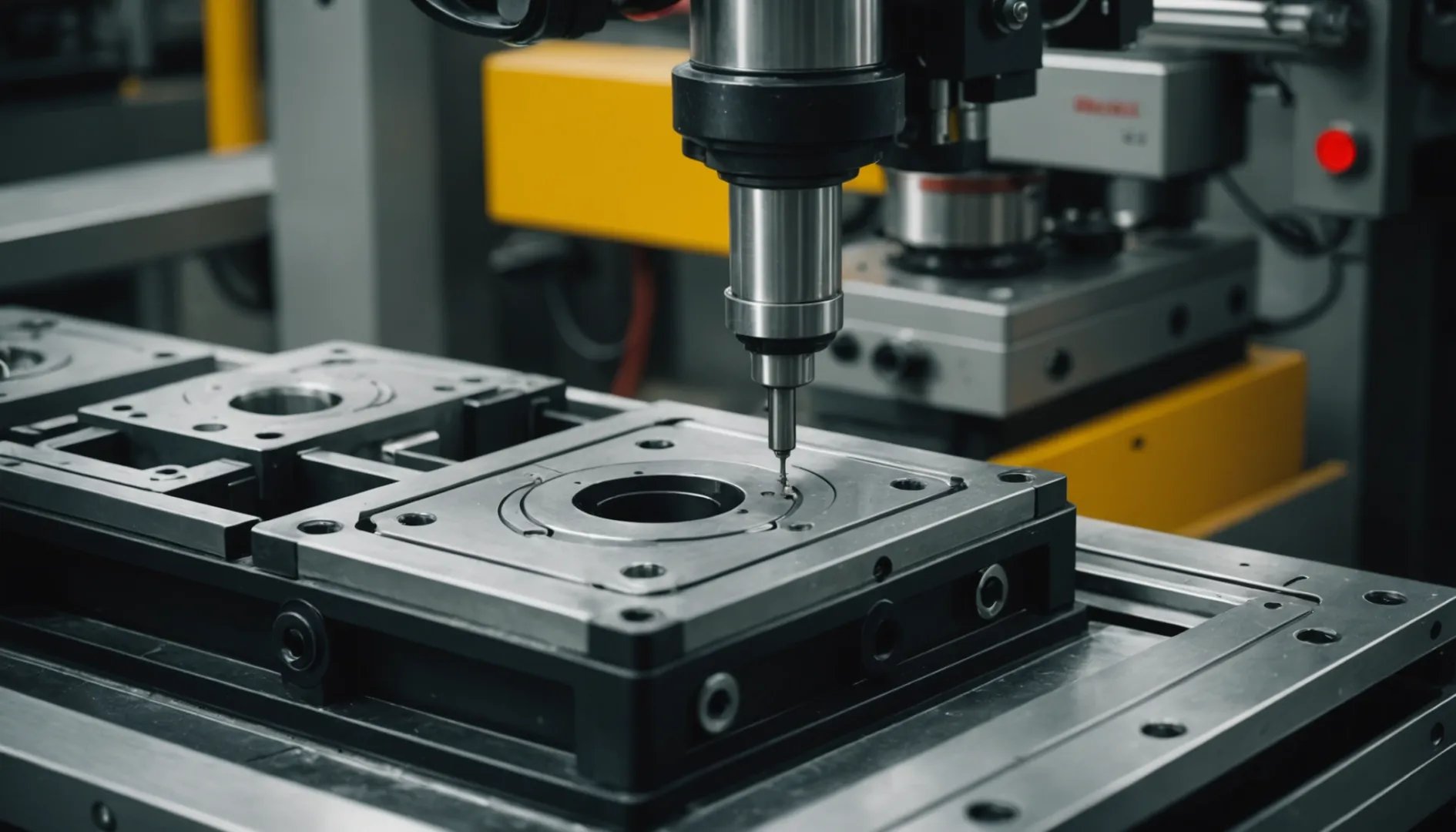
The Role of Cutting Speed
Cutting speed is a critical parameter that dictates the interaction between the tool and the material. Higher speeds can enhance the surface finish but may increase tool wear. Conversely, lower speeds reduce wear but can lead to poor finishes. High-speed cutting (HSC) technology minimizes cutting force and vibrations, improving surface quality and precision. For instance, when machining steel mold parting surfaces, selecting a cutting speed between 100-300m/min is recommended for optimal results cutting speed selection3.
Impact of Feed Rate on Precision
Feed rate determines the rate at which the tool advances into the material. A high feed rate can decrease machining time but may compromise surface quality and dimensional accuracy. An optimal feed rate is essential to balance productivity and precision. For steel molds, maintaining a feed rate between 0.05 – 0.2mm/z is advisable to ensure the best outcomes. feed rate optimization4 shows how to adjust based on material and tool specifications.
Depth of Cut Considerations
The depth of cut affects the amount of material removed in one pass. Deeper cuts can increase productivity but might lead to greater tool stress and possible deflection, affecting precision. Adjusting the depth according to residual material and desired surface quality ensures minimal impact on parting surface accuracy depth of cut strategies5.
Advanced Machining Techniques
Adopting advanced techniques like HSC or precision EDM can further refine machining accuracy. HSC allows for higher speeds with reduced forces, while EDM excels in shaping complex, high-hardness materials without mechanical stress. These technologies are pivotal in achieving superior precision in complex parting surfaces advanced machining methods6.
Importance of Equipment and Tool Selection
Selecting high-precision CNC machinery and appropriate tools is fundamental. Advanced CNC tools with positioning accuracy up to ±0.005mm significantly reduce dimensional errors. Carbide tools with suitable edge parameters are preferred for maintaining cutting performance under high-speed conditions tool and equipment selection7. Utilizing online measurement systems for real-time adjustments further enhances machining precision.
High-speed cutting reduces machining force.True
High-speed cutting decreases the cutting force, enhancing surface quality.
CNC machines have positioning accuracy of ±0.1mm.False
Advanced CNC machines have positioning accuracy up to ±0.005mm.
Why Are Advanced Processing Techniques Important?
Unlocking the potential of advanced processing techniques can revolutionize manufacturing, enhancing precision, efficiency, and quality.
Advanced processing techniques are crucial in manufacturing for achieving high precision, reducing errors, and improving efficiency. By utilizing sophisticated machining equipment and optimizing cutting parameters, manufacturers can produce high-quality components with minimal waste. These techniques are vital for maintaining competitiveness in various industries.
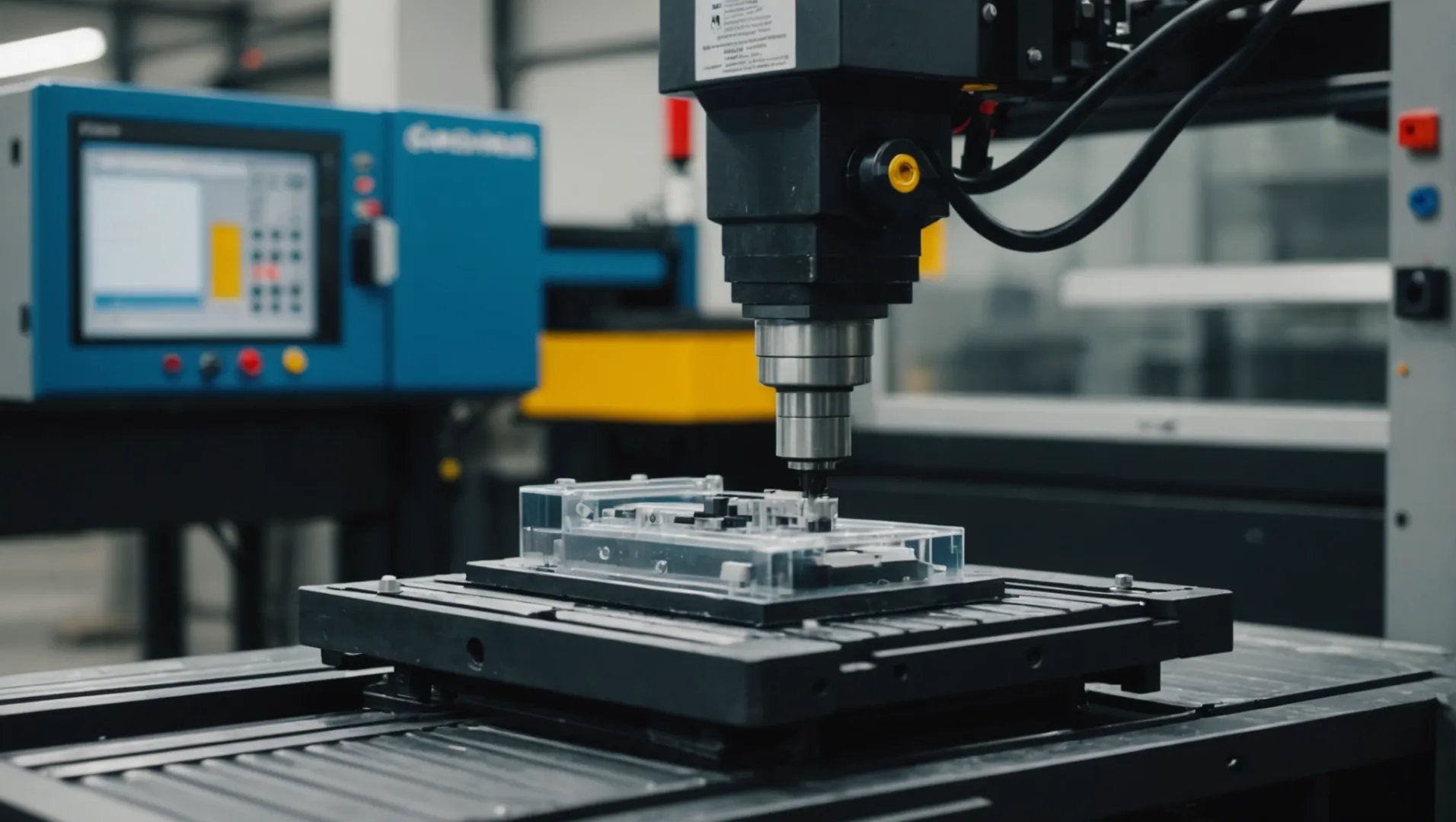
Precision and Accuracy in Manufacturing
Advanced processing techniques play a pivotal role in enhancing the precision and accuracy8 of manufactured products. For instance, the use of high-precision CNC machining centers allows for incredibly accurate parting surfaces. These machines provide positioning accuracy that can be as fine as ±0.005mm, crucial for reducing dimensional errors. This level of precision is essential in sectors like aerospace and automotive where exact specifications are critical.
Optimizing Machining Processes
The selection of appropriate tools is another facet where advanced techniques excel. Using the right tool based on the shape and material of the parting surface ensures reduced processing residue. For example, ball end milling cutters are ideal for complex curved surfaces. The optimization of cutting parameters through simulations is also crucial. By determining optimal cutting speeds and feeds, manufacturers can minimize the impact of cutting forces on surface quality.
High-Speed and Specialized Cutting
High-speed cutting (HSC) technology is a breakthrough in machining processes. It significantly reduces machining time while maintaining high surface quality. The cutting speed in HSC can reach three to ten times that of normal cutting, which drastically enhances productivity without compromising accuracy. Technologies like precision electric discharge machining (EDM) further extend the capabilities of processing complex shapes with micro-fine structures.
Quality Control and Inspection
Ensuring the quality of machined parts involves precise inspection using tools like Coordinate Measuring Machines (CMMs). These machines offer measurement accuracy up to ±0.001mm, allowing for rigorous quality checks against design models. Any deviations detected can be corrected through hand grinding or EDM adjustments, ensuring that the final product meets all specifications.
Impacts Across Industries
The importance of advanced processing techniques extends beyond traditional manufacturing sectors. In food processing, these methods ensure consistency and safety in product outputs. Automation technologies leverage these techniques to improve efficiency and reduce human error, leading to enhanced productivity9 across various industries. This adaptability makes advanced processing techniques indispensable for modern industrial applications.
By implementing these cutting-edge approaches, industries not only improve their operational efficiencies but also maintain a competitive edge in a rapidly evolving market landscape.
CNC machines improve parting surface accuracy.True
CNC machines have high positioning accuracy, reducing dimensional errors.
High-speed cutting increases machining vibration.False
High-speed cutting reduces vibration, improving surface quality and accuracy.
What Are the Best Practices for Quality Inspection?
Quality inspection is vital in manufacturing to ensure products meet standards. But what are the best practices?
Best practices for quality inspection include using precise equipment like CMM, timely corrective measures, and optimizing machining processes.
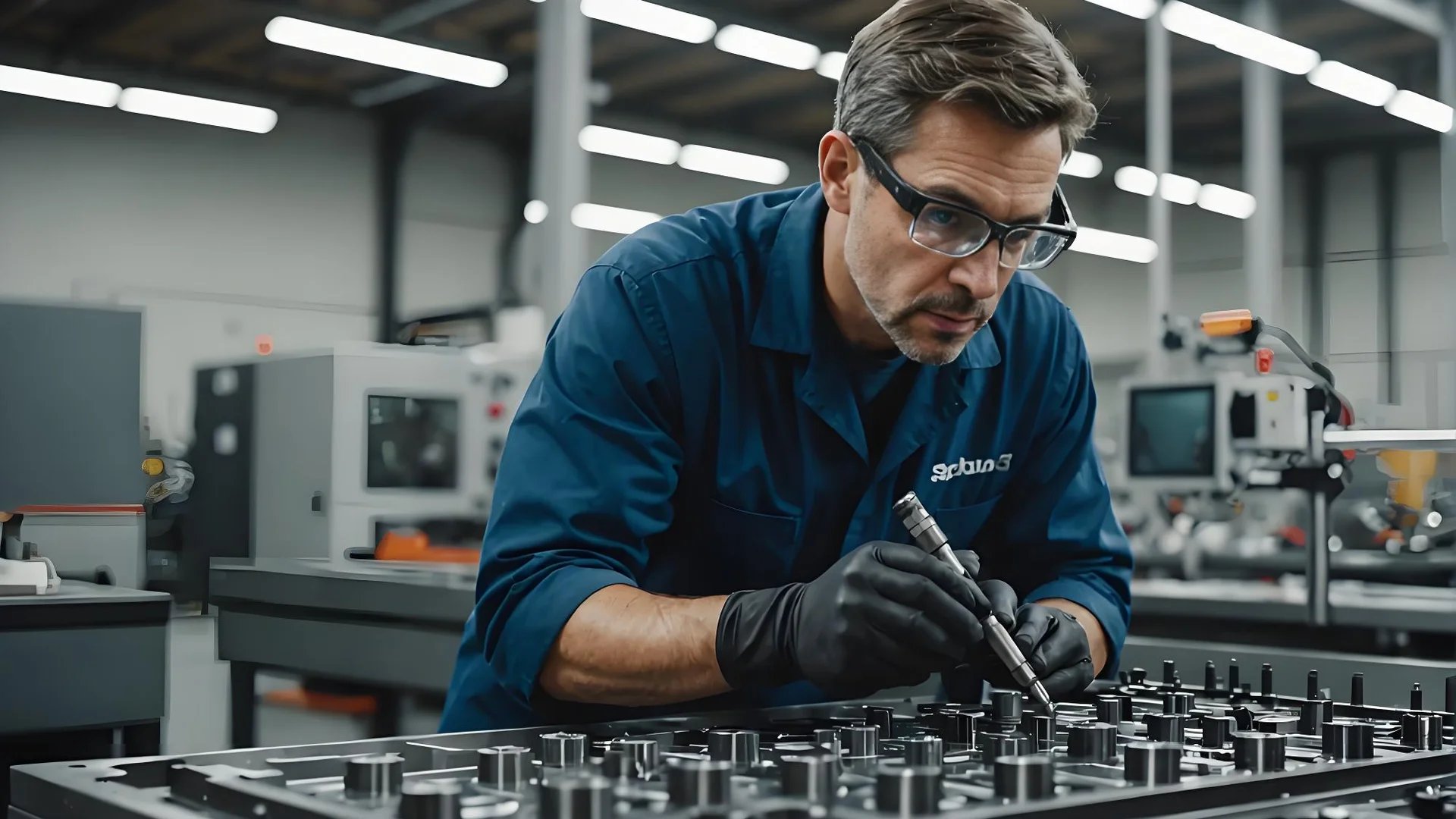
Precise Inspection Means
One of the foremost practices in quality inspection is employing high-precision inspection equipment. Tools such as Coordinate Measuring Machines (CMM) are essential in accurately measuring dimensions, shapes, and positional accuracy of components. For instance, a CMM‘s measurement accuracy can reach ± 0.001mm, allowing detailed detection of whether parting surfaces meet design specifications. During inspections, critical dimensions and points such as flatness, angles, and contours are measured and analyzed against the design model to ensure conformity10.
Timely Corrective Measures
Upon identifying discrepancies through inspection, implementing timely corrective actions is crucial. Adjustments can be made using techniques like hand grinding or Electric Discharge Machining (EDM) to correct deviations. For instance, if the flatness of a parting surface exceeds allowable limits, using a plane grinder can control flatness errors within design requirements. Similarly, correcting angular deviations can be achieved by setting adjustment blocks on molds or leveraging EDM‘s slope correction function to maintain accuracy11.
Machining Process Planning
Effective quality inspection begins with thoughtful machining process planning. Optimizing cutting parameters through tests and simulations enhances precision in parting surface machining. Selecting the optimal cutting speed, feed, and depth—such as 100-300m/min for steel molds—can reduce cutting force impacts on surface quality. Moreover, embracing advanced technologies like high-speed cutting (HSC) improves dimensional accuracy and surface quality due to reduced vibration and cutting force. This approach ensures that the machining process aligns with inspection12 standards.
Machining Equipment and Tool Selection
Choosing appropriate machining equipment and tools directly influences inspection success. High-precision CNC machining centers offer superior positioning accuracy, reducing dimensional errors. Tools like ball end milling cutters are suitable for complex curved surfaces, enhancing fit and reducing residue. Material selection is also critical; carbide tools provide high hardness and wear resistance, sustaining performance under high-speed conditions. These selections ensure the machining13 process meets rigorous inspection criteria.
CNC machines achieve positioning accuracy of ± 0.005mm.True
High-end CNC machines can reach a positioning accuracy of ± 0.005mm.
EDM is ineffective for high-precision parting surfaces.False
EDM is effective for complex, high-precision parting surfaces.
Conclusion
Enhancing machining accuracy for mold parting surfaces involves high-precision CNC equipment, appropriate tool selection, optimized cutting parameters, advanced techniques like HSC and EDM, and rigorous quality inspection.
-
Explore how high-speed cutting enhances mold precision and reduces errors. ↩
-
Learn about techniques to rectify machining errors in molds. ↩
-
Learn how to choose cutting speeds for different materials and tools. ↩
-
Discover strategies to balance feed rate for efficiency and precision. ↩
-
Explore techniques to optimize depth of cut for improved accuracy. ↩
-
Understand the advantages of HSC in enhancing machining precision. ↩
-
Find guidance on choosing machinery and tools for accurate results. ↩
-
Explore how precision impacts product quality in CNC machining. ↩
-
Discover how automation boosts efficiency and reduces errors. ↩
-
Understand how conformity ensures product meets design specifications. ↩
-
Learn how timely corrections enhance product precision. ↩
-
Explore standards that ensure high-quality machining results. ↩
-
Discover how tool selection affects machining precision. ↩